DOI: 10.11817/j.issn.1672-7207.2016.12.017
用于星球表面岩石采样的超声波钻进取心器
全齐全,李贺,邓宗全,王鑫剑,姜生元
(哈尔滨工业大学 机器人技术与系统国家重点实验室,黑龙江 哈尔滨,150001)
摘要:基于超声波纵振原理提出一种可搭载在漫游车或机械臂末端的岩石钻进取心器。该装置利用高频纵向振动达到破碎岩石的目的,无需驱动钻具作回转运动。研究结果表明:所研制超声波钻进取心器具有较高的岩石钻进效率且断心取心可靠。
关键词:深空探测;采样机构;压电驱动;岩石取心
中图分类号:TP24 文献标志码:A 文章编号:1672-7207(2016)12-4081-09
An ultrasonic coring tool for rock-sampling on extraterrestrial planets
QUAN Qiquan, LI He, DENG Zongquan, WANG Xinjian, JIANG Shengyuan
(State Key Laboratory of Robotics and System, Harbin Institute of Technology, Harbin 150001, China)
Abstract: Based on ultrasonic longitudinal vibration theory, a kind of rock coring tool was proposed. This tool can be easily mounted on planetary rover or end effector of robotic arm. The coring tool can break rocks using high-frequency vibration, even when no rotary motion was provided. The results indicate that the tool has relative high drilling efficiency and high reliability of breaking and coring rocks.
Key words: deep space exploration; sampling device; piezoelectric drive; rock coring
由于地外天体的岩石内部蕴含着大量原始的地质和生物学信息,岩石样本的采集和就位分析已成为外星体探测任务的一个重要环节。为获取未经风化和侵蚀的岩石内部样本,通常采用回转冲击钻进的方式钻取具有一定直径和长度的岩心。回转冲击钻进装置一般安装在着陆器的工作平台或漫游车车载机械臂的末端。外星体表面岩石钻进过程不仅需要较大的能耗,而且需提供一定的轴向钻压力[1]。未来的深空探测采样任务中,多数探测目标距离地球更加遥远,探测器所能提供的有效载荷和能源有限。面对更苛刻的星体表面环境,回转冲击钻进这种传统的岩石样本采集方式将面临更严峻的挑战。回转冲击钻进装置的动力一般由电磁电机提供,而电磁电机在真空、高温环境下工作将面临着温升的问题,需采用特种材料和工业提高电机的耐温等级或采取温控措施,以保证电机正常工作。在真空环境下钻进装置运动副的润滑和密封变得更加困难,其传动部件容易发生失效[2]。在引力场比较小的星体(如小行星和彗星)表面开展岩石钻探采样,钻进装置钻进坚硬的岩石需要很大的轴向钻压力。过大的轴向力可能会导致着陆器或探测车发生倾覆。面向未来更加遥远星体的深空采样探测,受航天器载荷和能量限制,需对钻探采样装置进行小型化、轻量化和低功耗设计。近年来,由于智能作动器通常具有高能量密度、低功耗和较强的环境耐受能力,满足了空间探测技术的需求,引起了研究者的广泛兴趣[3]。作为一种新型的智能作动器,压电作动器实现了动力转换和运动传递的基本功能,已广泛应用于超声电机、超声清洗、超声辅助加工等诸多领域[4-5]。压电陶瓷材料具有宽广的耐温范围(比如锆钛酸铅陶瓷在300 ℃以上的高温下仍具有良好的压电性能[6]),对高低温环境具有较强适应能力。基于压电材料的作动器结构紧凑,轻质小巧,可适用于外星体表面采样探测任务。1999年,SHERRIT等[7]提出利用压电驱动技术开展星体表面就位采样探测的理念,并研制出世界上第1台超声波/声波钻探取心装置(ultrasonic/sonic driller/corer,USDC)。该装置结构简单、能耗低,在较小的钻压力下,便能刺入坚硬岩石。基于USDC技术,随后又陆续研制出超声打磨工具、超声囊地鼠和回转辅助超声钻探器等装置[8-10]。但研究主要集中在提高岩石的钻进取心效率上,而对纯冲击式的超声波钻进取心装置的断心和取心方式研究较少。自超声波/声波钻进技术问世以来,超声波钻进取心装置的研制备受关注。德国帕德博恩大学对超声波钻进取心装置的高低频振动转换过程开展了理论研究[11-12]。英国格拉斯哥大学利用可展卷管将钻进机构包裹,降低了钻具与岩壁间摩擦,提高了钻进取心装置的钻进效率[13]。欧空局(ESA)为支持ExoMars火星任务研制了一种超声波钻进取心装置并研究了其安装方式对钻进效果的影响[14]。俄罗斯比斯克超声技术中心和空间技术研究所对钻进工具的钻头开展了设计与研究工作,以实现月壤和粉状岩屑的采集[15-16]。除此之外,作为我国最早探索超声波钻进技术的机构,南京航空航天大学精密驱动研究所开展了超声波/声波钻探器的结构动力学、能量耦合机理等相关理论和试验研究[17-18]。针对未来对彗星、小行星等地外天体表面岩石的小样本就位探测,本文作者研制一种轻质小巧的超声波钻进取心器(ultrasonic coring tool,UCT)。它可方便安装在机械臂末端,并借助机械臂提供的动力实现对坚硬岩石的断心和取心功能。超声波钻探取心工具的研制可为我国未来对彗星、小行星等地外天体岩石钻探采样提供一种可行的技术手段。
1 超声波钻探取心器的研制
本文研制的超声波钻探取心器结构如图1所示。其主要包括3个组件:超声换能器、自由质量单元和取心钻具。由于压电材料的逆压电效应,超声换能器在超声频交流电激励下可产生高频机械振动。换能器振动频率一般在几千赫兹到几万赫兹之间。超声换能器输出的振动可驱动自由质量单元在超声换能器和取心钻具之间作往复碰撞运动。钻具受到自由质量单元的声频冲击,其内部将产生应力波并传递到钻具与岩石接触表面。当冲击应力超过岩石破碎应力,岩石发生破碎,取心器实现钻进和取心。为使超声波钻探取心工具具有良好的工作性能,需对这3个组件进行精确设计。
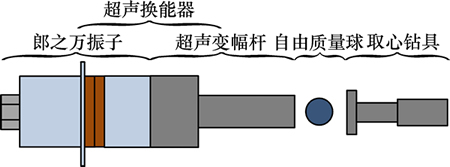
图1 超声波钻进取心器结构简图
Fig. 1 Schematic of UCT
1.1 超声换能器设计
超声换能器主要包括超声波振子和超声变幅杆2部分。超声波振子由前盖板、后盖板、压电陶瓷材料、预紧螺栓以及电极片等组成。振子利用压电陶瓷材料的逆压电效应将高频电信号转化为相应频率的机械振动,通过变幅杆截面面积变化将机械振动的质点位移或速度放大,并将能量集中在很小的面积上,以驱动自由质量单元的运动。超声换能器的性能决定了其对自由质量单元的驱动能力,继而直接影响自由质量单元作用在取心钻杆上的冲击力。其驱动特性与取心器的岩石破碎效果及钻进取心效率密切相关。因此,提高超声换能器的电声能量转换效率尤为重要。超声换能器最重要的2个参数是共振频率和变幅杆最大输出振幅。超声换能器的共振频率最初需由设计者设定。根据设计值和实际值之间的误差修改换能器设计参数,可使换能器工作频率与设计值相吻合。本文超声波钻探取心器共振频率的设计值为25 kHz,振子为半波长振子,变幅杆采用阶梯型,大端直径与小端直径之比为25/8。振子与变幅杆共同构成了一个全波长谐振系统。利用力电声类比的方法,可建立超声换能器等效阻抗网络模型(如图2所示),分析影响压电换能器特性的敏感结构参数[19]。图2中:li为超声换能器第i段结构的长度;vi为超声换能器第i段结构的振动速度;p为PZT压电陶瓷片数;C0为压电陶瓷静态截止电容;U和I分别为所施加外部电压和流经压电陶瓷的电流;N为机电耦合系数;ZLi和ZCi分别为第i段结构的阻抗,其表达式分别为
(1)
(2)
式中:ρi,ci和Si分别为换能器第i段结构的密度、波速和横截面积;f为换能器谐振频率。

图2 超声换能器等效阻抗网络模型
Fig. 2 Equivalent circuit network of ultrasonic transducer
由等效网络模型可知,影响谐振频率最主要的因素为前盖板、后盖板、变幅杆的轴向尺寸及换能器两端输入阻抗。图3所示为超声换能器结构尺寸参数及原理样机。换能器的后盖板材料采用软钢(20号钢),前盖板和变幅杆材料采用声阻抗小的钛合金(TC-4),压电陶瓷材料为机械品质因数较高的PZT-4,预紧螺栓材料为A2级稳固性不锈钢。
借助阻抗分析仪对所设计的超声换能器进行测试,获得其第1阶谐振频率为24 460 Hz。测试结果与理论值的相对误差为2.16%。利用激光测振仪测试超声波换能器变幅杆底端输出振幅和节面(换能器法兰处)振幅,试验数据如图4所示。由图4可知:变幅杆端面输出稳定的正弦振动,振动峰峰值约为47 mm,振幅约为23.5 mm;换能器节面为小振幅类正弦振动,振动峰峰值约为3.5 mm。变幅杆端面振幅较大,具有一定驱动能力;节面振幅很小,可作为机械接口的安装面。
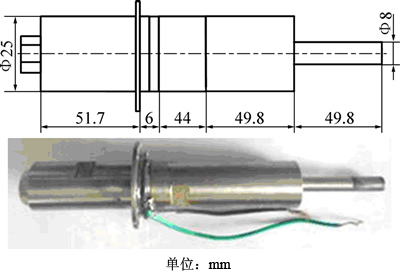
图3 超声换能器结构尺寸及原理样机
Fig. 3 Ultrasonic transducer prototype and its structural Dimensions
1.2 自由质量单元的构型及质量选择
超声波钻探取心器工作过程中,变幅杆底端的振动是动力输入,钻杆的运动是动力输出,自由质量单元起动力传递的作用。超声换能器的变幅杆输出的振动一般为超声频小振幅振动,振幅一般为微米级(几微米至几十微米)。在变幅杆激励下,自由质量单元在变幅杆底端和钻杆顶端作声频范围的大振幅振动。自由质量单元的振动频率一般为几百赫兹至几千赫兹,振幅一般为毫米级。由于自由质量单元对取心钻杆的冲击效果对装置钻探取心能力具有很大影响,因此,减少自由质量单元在动力传递过程中能量损耗,提高动力传递效率,是提高超声波钻探取心器钻探效率的关键。前期研究中,为便于观察自由质量单元运动状态,开展自由质量单元非线性动力学行为的研究,采用了环形自由质量单元,如图5(a)所示。由于钻具中心杆与自由质量单元的环形中心孔之间存在滑动摩擦,限制了自由质量单元的运动空间,使其在高频振动过程中,圆孔接触面摩擦严重,降低了自由质量单元动量传递效率。中心杆在钻具上表面应力集中效应明显,易引起疲劳断裂。本文采用球形自由质量单元,通过钻具内壁限制其运动空间。如图5(b)所示,封闭式导向设计使自由质量单元的振动不易受到外界影响,振动状态较稳定。自由质量单元与钻具内壁之间为滑滚摩擦,摩擦损耗低。冲击面近似点接触,冲量传递稳定,但需保证自由质量球和钻杆上表面的接触刚度。

图4 超声换能器幅测试曲线
Fig. 4 Amplitude of ultrasonic transducer
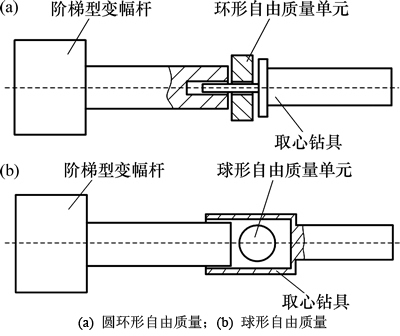
图5 环形和球形自由质量单元的结构形式
Fig. 6 Structure of ring-shaped and spherical free masses
对于变幅杆、自由质量单元和钻具三者构成的碰撞振动系统,碰撞后的系统状态既取决于碰撞前的初始运动状态,又与碰撞接触过程中的能量耗散、摩擦、非线性干扰等因素有关。试验中发现,自由质量单元在变幅杆底端和钻具顶端的碰撞振动是高度非线性的,很难找到一种准确的数学模型描述其动力学行为。影响自由质量单元对钻具冲击效果的主要因素是自由质量单元的质量和其与钻具接触时的瞬时速度[20]。自由质量单元规格如表1所示。本文将借助试验手段,从一系列不同质量的球形自由质量单元中选出最优质量规格。
表1 自由质量单元规格
Table 1 A series of free masses
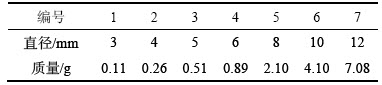
针对同一款钻进驱动装置及钻具,采用不同质量的自由质量单元,在砂岩上钻探5 min,观察不同质量的自由质量单元对钻探取心器钻探深度的影响。自由质量单元质量与钻深关系曲线如图6所示。

图6 自由质量单元质量与钻深关系曲线
Fig. 6 Relation between mass of free masses and drilling depth
由图6可知:超声波钻探取心器受输入功率的限制,无法使6号和7号的球形自由质量单元起振。在可驱动自由质量范围内,采用5号自由质量单元时,钻探取心器钻探效率最高。试验观察发现,由于球形自由质量单元与变幅杆和钻具的接触为高副接触,冲击力大,导致变幅杆和钻具与自由质量单元接触表面产生塑性变形,造成能量耗散,影响动量传递效果。设计时,应尽可能提高自由质量单元和钻具接触表面的接触刚度。综合以上分析及试验结果,研制出超声波钻进取心器原理样机,如图7所示。
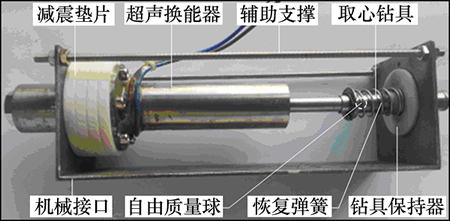
图7 超声波钻进取心器原理样机
Fig. 7 Prototype of UCT
整个装置设计成开放式结构以便于零部件更换与研究。为降低取心器振动对机架的影响,在超声换能器与机械接口连接处添加减震垫片。为提高装置的轴向刚度,增设辅助支撑。取心器原理样机主要技术参数如表2所示。
表2 原理样机主要技术参数
Table 2 Parameters of prototype of UCT

2 超声波钻进取心方式
外星体表面的岩石钻探采样可分为3个过程:钻进、断心和取心。取心钻具是超声波钻探取心器进行岩石钻进取心的执行部件。针对特定采样任务,选择合理的取心方式,开展钻具取心特性的研究,关系着采样任务的成败。
2.1 取心方案
根据未来深空探测采样任务中可能面临的实际工作状况及可达预期目标,在借鉴地质钻探取心原理的基础上提出三种取心钻具断心方案,如图8所示。
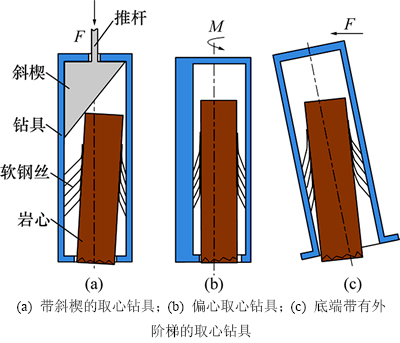
图8 3种不同原理的取心方案
Fig. 8 Schematic of three kinds of coring concepts
图8(a)所示为一种带斜楔的取心钻具(方案a)。斜楔固连在贯穿整个取心器的推杆末端。当取心器钻进至一定深度时,通过施加在推杆顶端的冲击力推动斜楔,使斜楔对取心钻具内的岩心产生弯矩。当岩石根部的应力达到其抗拉(压)强度时,岩心发生断裂。为提高斜楔断心的可靠性,该方案需由额外动力源提供自上而下的瞬时冲击力。但是,为放大变幅杆输出振动的幅值,变幅杆截面放大倍数通常比较大,变幅杆小端直径较小,给推杆的贯穿布置造成困难。
图8(b)所示为偏心取心钻具(方案b)。与传统双管式回转取心钻具原理类似,钻具回转轴线与所取岩心轴线偏置。当外部回转动力源驱动钻具回转时,钻具会对岩心产生剪切力。剪力值超过岩心剪切强度,岩心产生断裂。断心过程中,外部回转动力源提供给偏心钻具的回转力矩需克服岩心剪切力以及钻具与岩壁间的摩擦力。此方案中,大功率回转动力源是偏心钻具可靠断心的关键。回转动力一般由回转电机产生,而添加回转驱动装置会增加取心装置体积、重量及系统复杂性。
图8(c)所示为底端带有外阶梯的取心钻具(方案c)。其动力来源简单,只需机械臂对钻探取心器本体施加侧向推力将岩心折断。断心过程中,钻具外阶梯端面与岩壁的接触点可作为钻具活动支点;钻具外圆与岩孔内壁、钻具内圆与岩心之间的间隙可为断心过程提供充分的活动空间。
以上3种取心方式所采用的钻具内部均布置有一定长度和倾角的软钢丝。它们将折断后的岩石样心保持在钻具内部,可将岩心从岩孔中取出。
综合考虑3种取心方式,方案(a)和(b)均需要外部动力源,动力源的安置既增加了系统质量和体积,又增加了系统复杂性。第3种取心方案无需外部动力源,由机械臂辅助动作就能实现。只要钻具折断岩石所需活动空间足够大,就能实现可靠断心。本文拟选择取心方式简单可靠的第3种方案。
2.2 断心力学模型
为保证岩石断心的可靠性,需预估岩心发生折断所需侧向推力。通过理论建模和试验验证手段,对底端带有外阶梯的取心钻具的断心力进行测试,为钻具结构尺寸和机械臂动力输出的确定提供依据。
在断心过程中,钻具底端外阶梯为机械臂侧推动作创造移动空间及断心支点,阶梯外径及高度分别决定钻具断心移动位移和支点位置。
机械臂作用下钻具与岩石相互作用模型如图9所示,假设钻具绕A点旋转,钻具与岩心及岩壁间隙很小但不可忽略。对钻具进行力学分析可得平衡方程
(3)
式中:P为机械臂施加在钻具上的推力;L为侧推力作用点与钻具底面的垂直距离;d为钻具外阶梯高度;Ff为钻具内壁受岩心的摩擦力;D1为钻具内径;D2为钻具外阶梯外径;u为岩心与钻具内径间单侧间隙;r为岩心半径;T为钻具受岩心的正压力;h为岩心高度;μ为岩心与钻具摩擦因数。岩心在E点所受正压力TE=T,所受摩擦力FfE=Ff。
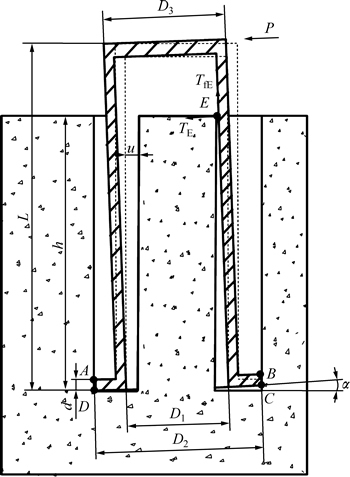
图9 机械臂作用下钻具与岩石相互作用模型
Fig. 9 Interaction model between coring tool and rock
由图9可知,A点与C点之间的直线距离LAC应满足
(4)
式中:u0为钻具阶梯外径与岩孔内壁的间隙。若LAC不满足上式,在不破坏岩孔内壁的条件下,钻具将无法绕A点旋转。
钻具内壁与岩石E点接触时的几何关系图如图10所示。为实现可靠断心,钻具内壁应与岩心E点接触。外阶梯钻具钻进岩石深度和钻具与岩心间的间隙需满足一定的几何关系。
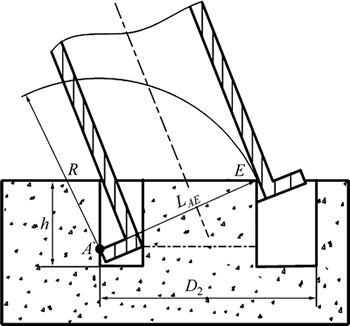
图10 钻具内壁与岩石E点接触时的几何关系图
Fig. 10 Geometric diagram when the inner wall of coring tool touches E point on rock core
(5)
式中:LAE为钻具A点距岩心顶端E点距离。只有当满足R<LAE时,钻具内壁才能与岩心E点接触,否则将无法实现断心。若要提高断心可靠性,则R应远小于LAE。设岩心顶部到折断位置轴向距离为L0,通常情况下,
(6)
否则,L0≈h,即岩石从根部断裂。
岩心根部所受最大拉应力σT和压应力σS分别为
(7)
根据式(3)和式(7)可得岩心受拉(压)断裂所需推力的表达式为
(8)
其中,
。
由式(8)可知,岩心折断力与钻具外阶梯尺寸、岩心尺寸、岩石的极限抗拉(压)强度等因素有关。 针对同一种岩石,在所获得岩心尺寸一定的条件下,影响折断力的主要参数是钻具与岩心单侧间隙u、钻具外阶梯高度d以及钻具阶梯外径D2。经计算分析,钻具阶梯外径D2对岩心折断力影响较小,钻具外阶梯高度d对折断力影响较大。
2.3 岩心与岩孔尺寸偏差分析
为确定岩心与钻具取心孔之间的间隙u以及岩孔与钻具外阶梯之间的间隙u0,需对同一钻具在相同钻探条件下的获得岩心和岩孔尺寸的一致性开展试验研究。试验拟采用的外阶梯型钻具尺寸如图11所示。
在同一块砂岩不同位置进行岩石钻探采样,从中随机选取10个岩石样本。对所获得岩心外径和岩孔内径进行测量,测量结果如图12所示。
岩心和岩孔直径波动分析数据如表3所示,岩心外径和岩孔内径均存在波动。岩心外径的偏差约为0.123 mm;岩孔内径的偏差约为0.472 mm。岩心外径和岩孔内径的波动率在5%以内,尺寸一致性比较好。将数据代入断心力模型进行计算,计算结果表明岩石样本尺寸和间隙均满足断心几何约束条件,可实现可靠断心。
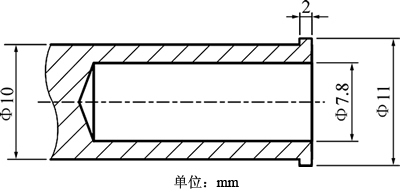
图11 测试钻具结构尺寸
Fig. 11 Dimension of tested coring tool

图12 岩心外径和岩孔内径尺寸
Fig. 12 Outer diameters of rock cores and inner diameters of holes
表3 岩心外径与岩孔内径波动分析结果
Table 3 Analytical results of rock cores’ outer diameters and rock holes’ inner diameters
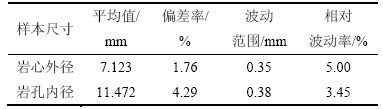
经分析,造成这种波动的主要原因有:1) 钻具与导向机构的配合间隙;2) 取心器本体的振动;3) 钻具与岩壁的摩擦。超声波钻进取心器在岩石钻进过程中,钻具与岩壁间摩擦既是影响岩心外径和岩孔内径的主要因素,也是造成冲击能量损失的主要原因之一。根据Bowden和Tabor提出的黏着摩擦理论[21],黏着摩擦因数为
(9)
式中:η为黏着摩擦因数;Afric为接触面积;τ为表面粘着剪切力;Fdirec为表面法向接触载荷.由式(9)可知,表面摩擦力与作用面积成正比。若增加钻具外阶梯高度,钻具外表面与岩壁接触面积增加,黏着摩擦因数增大,造成钻具冲击钻进过程中所受钻探阻力增大,同时影响岩心和岩孔直径一致性。因此,钻具外阶梯高度应在满足结构强度的条件下尽量在较小范围内进行选择。一般情况下,钻具外阶梯高度取2~4 mm。以本文所设计的取心钻具为对象,开展了侧推式断心的断心力测试试验。本次试验对象为砂岩,施力点为钻具最高点,开展12次岩石钻探采样并进行断心力测量,试验数据如图13所示。
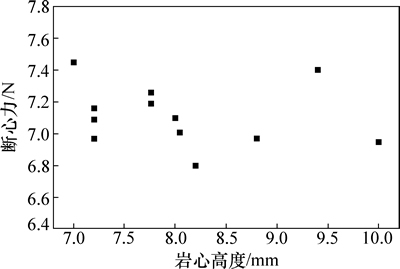
图13 断心力测试数据散点图
Fig. 13 Scatter plot of fracturing force data
数据显示,断心试验所选择的岩心高度分布在7~10 mm,断心力为6.8~7.45 N。
3 钻探取心试验
为测试取心器的钻进效率和岩石取心性能,开展结构参数优化和相关模型验证,搭建了超声波钻进取心器测试试验系统。该系统主要由钻进试验台、控制系统、信号发生器、压电陶瓷驱动器等组成。
钻进试验台的基本结构如图14所示。进尺电机通过齿轮齿条传动可带动取心器沿导轨向下钻进,砝码用于抵消取心装置自重。钻进过程中,控制系统可实时采集磁栅尺和压力传感器数据。
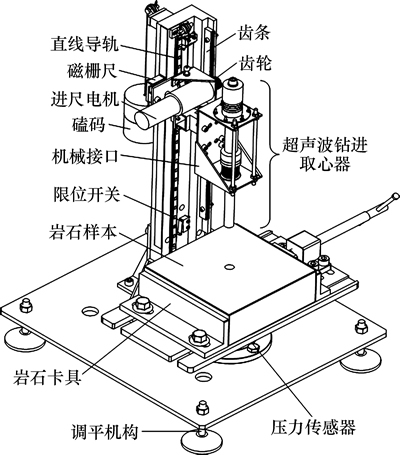
图14 钻进取心试验平台结构示意图
Fig. 14 Structure of test bed for UCT
3.1 轴向钻压力对钻进效率的影响分析
在超声波钻进取心器的动力参数中,施加给取心器的轴向静压力对钻进取心效果影响显著。轴向静压力可以改变自由质量单元的振动幅值和频率,从而影响超声换能器的负载阻抗。反之,负载阻抗的改变又影响超声换能器的输出特性。
钻进过程采用同一超声波钻进取心器;设定压电陶瓷驱动器输出电压100 V;钻进对象选择表面平整,质地均匀的同一种岩石(砂岩);钻进时间设定为5 min。为保证试验数据的客观性,进行多次钻进试验,记录试验数据,根据试验数据点绘制散点图。为找出最优轴向静压力的分布范围,对试验数据进行高斯拟合,获得轴向静压力与钻探效率之间的关系,如图15所示。
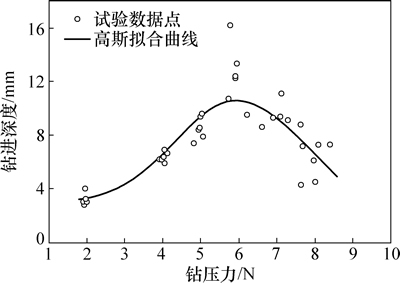
图15 轴向静压力与钻进深度关系曲线
Fig. 15 Relation between axial load and drilling depth
高斯拟合函数的表达式为
(10)
经计算,a=7.72,b=6.05,c=0.62,d=2.98。由高斯拟合结果可知,本文研制的超声波钻进取心器在当前钻进工况条件下对砂岩的最优轴向静压力约为6 N。
3.2 取心器排屑过程分析
超声波钻进取心器依靠钻具的高频冲击作用使岩石发生破碎。当钻进到一定深度时,排屑问题将是制约其钻进效率的主要因素。传统的排屑方式主要有2种:一种是在回转作用下借助钻具螺旋排屑;另一种是利用流体介质的冲刷作用排屑。超声波钻进取心器采用的是纯冲击钻进原理,无回转运动。在钻探任务所处的外星体表面环境下难以借助流体介质进行排屑。因此,传统的排屑方法难以应用于超声波钻进取心器。若要提高超声波钻进取心器的钻进效率,需要找到一种行之有效的排屑方式。试验中发现,当钻探深度较浅的时候,高频冲击破碎产生的岩屑可飞溅出来,岩屑堆积在钻具周围。观察发现,钻具底端及侧壁引起空气振动对岩屑排除起到一定作用。但当钻进到一定深度时,会出现破碎微小的岩屑吸附在钻具外表面并缓慢向上运移,岩屑运移到一定高度后停止向上运动并开始下落。利用该现象有望探索出超声波钻进取心器这类纯冲击钻进装置的排屑方法,提高其钻进效率。目前,还未找到对于该现象的合理解释,有待更深入的研究。
4 结论
1) 基于超声波/声波钻进技术,研制出可方便搭载在漫游车或机械臂上的超声波钻进取心器。提出了一种新型的取心钻具和断心取心方式,并对该钻具的断心和取心特性开展了研究。分析了轴向静压力对取心器钻进效率的影响规律和高频冲击作用下取心器的排屑特性。
2) 所研制的超声波钻进取心器具有较高的钻进取心效率和较为可靠的断心取心性能,可为彗星、小行星等弱引力场星体的岩石钻探采样提供参考。
参考文献:
[1] ZACNY K, BAR-COHEN Y, BRENNAN M, et al. Drilling systems for extraterrestrial subsurface exploration[J]. Astrobiology, 2008, 8(3): 665-706.
[2] 翁立军, 刘维民, 孙嘉奕, 等. 空间摩擦学的机遇和挑战[J]. 摩擦学报, 2005, 25(1): 92-95.
WENG Lijun, LIU Weimin, SUN Jiayi, et al. Opportunities and challenges to space tribology[J]. Tribology, 2005, 25(1): 92-95.
[3] FRECKER M I. Recent advances in optimization of smart structures and actuators[J]. Journal of Intelligent Material Systems and Structures, 2003, 14(4/5): 207-216.
[4] UCHINO K. Piezoelectric actuators and ultrasonic motors[M]. Bremen: Springer, 1997: 100-324.
[5] UCHINO K. Recent trend of piezoelectric actuator developments[C]//Proceedings of International Symposium on Micromechatronics and Human Science. Nagoya, Japan: 1999: 23-26.
[6] FETT T, THUN G. Determination of room-temperature tensile creep of PZT[J]. Journal of Materials Science Letters, 1998, 17(22): 1929-1931.
[7] SHERRIT S, BAO X, CHANG Z, et al. Modeling of the ultrasonic/sonic driller/corer[C]//IEEE Ultrasonics Symposium. San Juan, Puerto Rico: IEEE, 2000: 691-694.
[8] BAR-COHEN Y, SHERRIT S, DOLGIN B P, et al. Ultrasonic/sonic drilling/coring (USDC) for in-situ planetary applications[C]//SPIE’s 7th Annual International Symposium on Smart Structures and Materials. San Jose, CA, USA: 2000: 661-668.
[9] BAR-COHEN Y, SHERRIT S, DOLGIN B, et al. Ultrasonic/Sonic Driller/Corer (USDC) for planetary application[C]//SPIE’s 8th Annual International Symposium on Smart Structures and Materials. Sante Fe, NM, USA: 2001: 441-448.
[10] BADESCU M, BAR-COHEN Y, SHERRIT S, et al. Percussive augmenter of rotary drills (PARoD)[C]//SPIE Smart Structures and Materials Nondestructive Evaluation and Health Monitoring. San Diego: SPIE Press, 2012: J1-J8.
[11] NEUMANN N, SATTEL T. Set-oriented numerical analysis of a vibro-impact drilling system with several contact interfaces[J]. Journal of Sound and Vibration, 2007, 308(3/4/5): 831-844.
[12] POTTHAST C, TWIEFEL J, WALLASCHEK J. Modelling approaches for an ultrasonic percussion drill[J]. Journal of Sound and Vibration, 2007, 308(3): 405-417.
[13] HARKNESS P, LUCAS M, CARDONI A. Architectures for ultrasonic planetary sample retrieval tools[J]. Ultrasonics, 2011, 51(8): 1026-1035.
[14] THOMAS P N H. Magna Parva and ESA’s ultrasonic drill tool for planetary surface exploration[C]//12th Biennial International Conference on Engineering, Construction, and Operations in Challenging Environments. Honolulu, Hawaii, USA: 2010: 1235-1245.
[15] KHMELEV V N, NESTEROV V A, KHMELEV S S, et al. The development of experimental sample of ultrasonic equipment for the intake of lunar soil[C]//IEEE 13th International Conference and Seminar of Young Specialists on Micro/Nanotechnologies and Electron Devices (EDM). Novosibirsk, Russia: IEEE, 2012: 162-169.
[16] KHMELEV V N, GENNE D V, KHMELEV S S, et al. Studies of functional possibilities of model sample of the ultrasonic apparatus for drilling of the simulator of lunar soil[C]//14th International Conference on Micro/Nanotechnologies and Electron Devices (EDM). Altai, Erlagol, Russia, 2013: 123-127.
[17] 郭俊杰, 黄卫清, 李志荣. 一种新型的超声波/声波钻探器[J]. 压电与声光, 2008, 30(5): 579-581.
GUO Junjie, HUANG Weiqing, LI Zhirong. A new ultrasonic/sonic drilling device[J]. Piezoelectectrics & Acoustooptics, 2008, 30(5): 579-581.
[18] 杨康. 基于超声波/声波能量耦合机理的钻探器研究[D]. 南京: 南京航空航天大学航空宇航学院, 2012: 1-58.
YANG Kang. Research on drilling corer based on ultrasonic/acoustic energy coupling mechanism[D]. Nanjing: Nanjing University of Aeronautics & Astronautics. College of Aerospace Engineering, 2012: 1-58.
[19] SHERRIT S, LEARY S P, DOLGIN B P, et al. Comparison of the Mason and KLM equivalent circuits for piezoelectric resonators in the thickness mode[C]//1999 IEEE Ultrasonics Symposium. Caesars Tahoe, NV, USA: IEEE, 1999: 921-926.
[20] QUAN Qiquan, LI He, JIANG Shengyuan, et al. A piezoelectric-driven ultrasonic/sonic driller for planetary exploration[C]//2013 IEEE Robotics and Biomimetics (ROBIO). Shenzhen, China: IEEE, 2013: 2523-2528.
[21] 雷帆, 温彤, 于建明. 基于粘着摩擦理论的塑料微观摩擦特性研究[J]. 塑料工业, 2012, 40(8): 85-88.
LEI Fan, WEN Tong, YU Jianming, et al. Research on micro-tribological properties of plastic materials based on adhesive friction theory[J]. China Plastics Industry, 2012, 40(8): 85-88.
(编辑 赵俊)
收稿日期:2015-12-20;修回日期:2016-02-28
基金项目(Foundation item):国家自然科学基金资助项目(61403106);高等学校学科创新引智计划(B07018);中央高校基本科研业务费专项资金资助项目(HIT.NSRIF.2014051)(Project(61403106) supported by the National Natural Science Foundation of China;Project(B07018) supported by the Program of Introducing Talents of Discipline to Universities;Project(HIT.NSRIF.2014051) supported by the Fundamental Research Funds for the Central Universities)
通信作者:全齐全,博士,讲师,从事宇航空间机构与控制研究;E-mail:quanqiquan@hit.edu.cn