Effect of welding temperature and duration on properties of 7075 Al to AZ31B Mg diffusion bonded joint
Abdolhamid AZIZI1, Hossein ALIMARDAN2
1. Department of Engineering, Ilam University, Ilam 69315-516, Iran;
2. Department of Engineering, Kermanshah Branch, Islamic Azad University, Kermanshah 6718997551, Iran
Received 1 February 2015; accepted 20 July 2015
Abstract: 7075 Al alloy and AZ31B Mg alloy were joined by diffusion welding technique at pressure 29 MPa with various welding temperatures and durations. Scanning electron microscopy examination, shear tests and microhardness evaluation were conducted on the samples interface to find out the effect of welding temperatures and durations on the weldability. The results demonstrate that the AZ31B Mg/7075 Al composite plates are bonded well and the intermetallic phases such as Al12Mg17 and Al3Mg2 within the joint zone form. It is found that due to the grain coarsening and the formation of brittle compounds, high welding temperatures and long welding durations result in a decrease of shear strength and increase of interfacial welding hardness. The minimum shear strength of 15 MPa along with the maximum microhardness of HV 176 are obtained for the diffusion couple processed at 450 °C for 120 min. It is revealed that enhancing the temperature and choosing appropriate holding time makes a remarkable increase of interfacial welding thickness. Increasing the welding temperature from 430 to 450 °C along with long welding duration (120 min) results in the increase of interfacial welding thickness by 26% where this value is 6% at the welding performed for 60 min.
Key words: Al alloy; Mg alloy; diffusion welding; welding temperature; welding duration
1 Introduction
Diffusion welding (DFW) is a joining process wherein the principal mechanism for joining is solid-state diffusion. The coalescence of faying surface is accomplished through the application of pressure at elevated temperature ranging from 0.5Tm to 0.8Tm (where Tm is the absolute melting temperature). No melting and only limited macroscopic deformation or relative motion of parts occurs during welding [1-3]. The process has an important effect on the design and manufacturing of the workpieces, since it is a great advantage to bond similar or dissimilar materials [4]. By diffusion bonding, it is possible to bond all the materials whose chemical and metallurgical properties are different [5-7]. Dissimilar metal joining offers the potential to utilize the advantages of different materials. The main reasons for dissimilar joining are due to the combination of good mechanical properties of one material and either low density or good corrosion resistance or good electrical properties of the second material. Consequently, joining processes for dissimilar materials have received noticeable attention in recent years. Much of this activity has focused on the transportation industries such as aerospace, aviation, shipbuilding and railway. This is especially in the automotive industry due to the potential weight reduction of both vehicle components and structures [8]. The neediness to expand the use of lightweight structures in the automotive industry has increased interests in the use of both Al and Mg as structural materials. Dissimilar welding of Mg and Al alloys would achieve weight reduction and high efficiency of production by substituting Mg and Al alloys for steels [9]. The principal difficulty when joining Mg and Al lies in the formation of oxide films and brittle intermetallics in the bond region. However, diffusion bonding can be used to join these alloys without much difficulty [10]. So the diffusion bonding method is used to join these alloys to achieve a reliable bonding between them [11]. The outstanding process parameters promoting microscopic atomic movement to ensure complete metallurgical bond in diffusion bonding are bonding temperature, bonding pressure, holding time and surface roughness of the alloys to be joined [12,13]. The purpose of this research was to investigate the effects of holding time and welding temperature on the mechanical and metallurgical properties of the dissimilar joints of 7075 Al alloy and AZ31B Mg alloy fabricated by diffusion bonding processes. The holding time of 60 and 120 min were applied at the temperature range of 430-450 °C. Single lap joint configuration was performed in vacuum furnace to join the dissimilar materials which allowed bonding diffusion. The hardness and shear strength of the transition zone joints were evaluated at room temperature. Additionally, the morphologies of interface were examined by optical microscopy and scanning electron microscopy (SEM), and the elements content was analyzed with an energy dispersive spectrometer (EDS).
2 Experimental
Square shaped specimens (13 mm × 13 mm) with 5 mm in thickness were machined from Mg (AZ31B) and Al (7075) alloys. The chemical compositions of the base metals are shown in Table 1. To create the surface roughness, sandpapers with number 600 grit for Mg and number 1500 grit for Al were used. The average surface roughness for Al and Mg were 24.7 and 59.9 nm, respectively. To remove the surface contamination, before testing, the samples were ultrasonically cleaned in an acetone bath for 15 min and then rinsed by 96% ethanol, and immediately dried by the flowing of warm air. The polished and chemically treated specimens were stacked in a die and the entire diffusion bonding setup, as shown in Fig. 1, was inserted into a vacuum chamber (the vacuum pressure of 0.133 Pa was maintained). The specimens were heated up to the bonding temperature using induction furnace at a heating rate of 10 °C/min, simultaneously, the required pressure was applied. Selecting low bonding temperature causes no bonding occurrence between Mg and Al alloys due to the insufficient temperature to cause diffusion of atoms, while selecting high bonding temperature causes the bonding pressure to decrease automatically after a few minutes because of the melting of Mg alloy due to high temperature [8]. So, the bonding temperatures were held near to the eutectic temperature (430, 440 and 450 °C) and the sufficient bonding time was conducted for 60 and 120 min. If the bonding pressure is low, no bonding will occur due to less number of contacting points (between surface asperities) through which the diffusion of atoms generally should occur. Moreover, under high pressure, the plates are going to deform plastically and this causes a reduction in thickness and a bulge in the outer edges [8]. Regarding to above considerations and experimental findings, the practical pressure of 29 MPa, which causes the best bonding results, was selected.
Table 1 Chemical compositions of base metals (mass fraction/%)
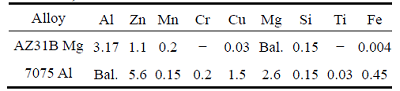
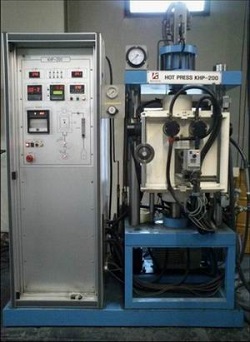
Fig. 1 Diffusion bonding apparatus
After completing the bonding, the samples were cooled down to room temperature before removing from the chamber. Microstructure analysis was carried out using a scanning electron microscope (SEM) equipped with EDS/EPMA chemical analysis (model VEGA// TESCAN-LMU) to check the formation of diffusion layer at the interface. The Mg side was etched by immersing in the solution of 0.25 mL acetic acid (CH3COOH), 0.6 g picric acid (C6H3N3O7), 10 mL ethanol (C2H6O) and distilled water (H2O) for 15 s. Whereas, the Al side was etched with Keller’s solution. The standard of ASTM: D1002-10 was used to measure the shear strength of the bonds. The 10 mm × 10 mm cross section lap shear tensile specimens, as shown in Fig. 2, were prepared from the Mg/Al diffusion bonded joints by a line cutting machine (electric spark cutting). The tests were carried out using SANTAM universal testing machine with a loading rate of 0.1 mm/min. Moreover, micro-hardness tests were performed by Vickers micro-hardness tester with a load of 0.49 N for 20 s along a perpendicular axis to the interface and a interspacing distances of 50 mm.
3 Results and discussion
3.1 Microstructure
Figure 3 illustrates the SEM images of the joints in the temperature range of 430-450 °C during welding for 60 and 120 min. As can be seen that due to sufficient temperature and time for atoms diffusing and bonding between two alloys, a complete joint happens and also a diffusing area forms in the contact area. In the interface, the reaction layer continuously forms and has a uniform thickness. The area between the base alloys of Mg and Al is called interfacial transition zone (ITZ).
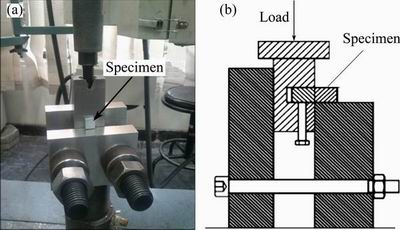
Fig. 2 Configuration of lap shear testing set up
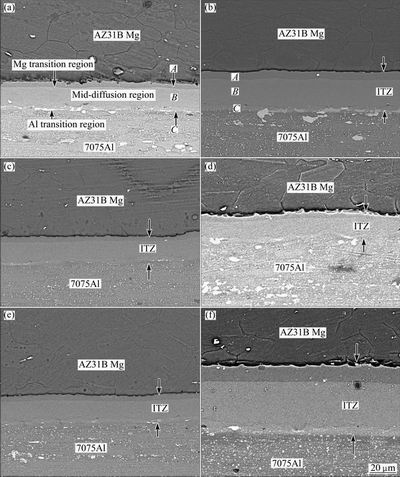
Fig. 3 SEM images of interface bonding at 430 °C for 60 min (a), 430 °C for 120 min (b), 440 °C for 60 min (c), 440 °C for 120 min (d), 450 °C for 60 min (e), and 450 °C for 120 min (f)
It is understood from the results that the thickness of the reaction layer increases gradually with increasing the heating temperature and holding time. Figure 4 shows that the diffusion zone thickness in the welding zone is different for the specimens welded at various temperatures and time. The ITZ thickness of the specimen diffusion welded at the lowest temperature and time (430 °C and 60 min) is measured to be around 21.26 mm. However, this value becomes more than 29.92 mm when the time increases to 120 min at the same temperature. Similarly, the ITZ thickness of the specimen diffusion welded at 450 °C for 60 min and 120 min are measured to be around 22.60 and 37.77 mm, respectively. It can be figured out that increasing the welding time from 60 to 120 min at 430 °C make an improvement of 40% in the ITZ thickness which increases up to 66% at 450°C. This findings show that increasing the temperature with the holding time of 120 min has a greater effect on the ITZ thickness than increasing the temperature with the holding time of 60 min. Therefore, the thickness of the ITZ layer increases remarkably with increasing the holding time. In spite of increasing the temperature, low holding time does not allow atoms to diffuse each other more and hence the diffusion layer thickness remains almost unchangeable. Increasing the holding time to upper level increases the grain boundary mobility (migration), and the grain boundary mobility measures how easy atoms transition from one grain to another [14]. This allows more atoms to diffuse on the other side. It leads to significant increase of diffusion layer thickness by increasing the temperature with elevated holding time.
The bonding temperature along with the holding time affects the atomic diffusion of the base alloys and influences the homogeneity of composition and interface microstructure of the bonded joints, so they are the dominant parameters in the diffusion bonding process [15,16]. According to Fig. 3, three layers between two alloys are observed from Mg side towards Al, including the Mg transition region (zone A), the middle diffusion region (zone B) and the Al transition region (zone C). It clearly exhibits a good bonding along the Mg/Al interface, which is free from discontinuities, and no evident compounds appear. In order to determine the elemental distribution across the joint interface, EDS (both line and point analyses) examinations were applied. The changes in the contents of Mg and Al along the interface of samples welded at 430 °C for 60 and 120 min are shown in Figs. 5-7. It is apparent from Fig. 5 that Mg and Al contents present a sharp gradient distribution in the regions A and C, which is the Mg-Al solid solution layer. Region B represented as the Mg-Al solid solution layer shows continuous gradient distributions of Mg and Al. Meanwhile, at the holding time of 120 min, the width of region B is thicker than that at the holding time of 60 min because of the more tendency of atomic diffusion with increasing the holding time.
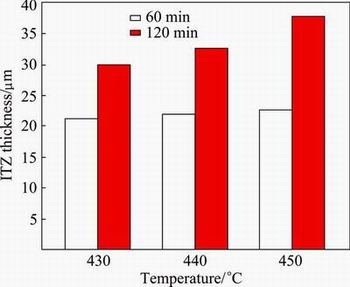
Fig. 4 Effect of welding temperature and holding time on ITZ thickness
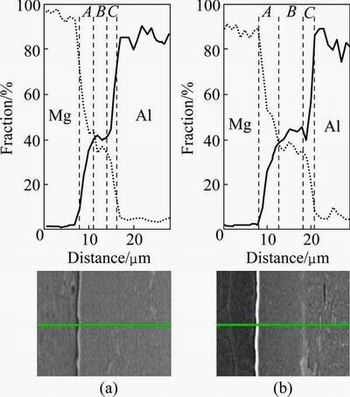
Fig. 5 EDS line scan across bonding interface as indicated by line for specimen welded at 430 °C for 60 min (a) and 430 °C for 120 min (b)
According to Figs. 6 and 7, when the interface area (area B) is examined, it is observed that almost 60% of the area B is composed of Al, and almost 36% of this area is composed of Mg. It is considered that the atomic radius can be considered for the reason why Al is heavily observed in the Mg side. It is given that the atomic radius for Al is 0.118 nm and that for Mg is 0.145 nm. Since, the atomic radius of Al is less than that of Mg, Al migrates faster towards the Mg side than Mg towards the Al side in the Al/Mg joints, hence, the intense diffusion of Al in the reaction layer is observed [17]. From the Al-Mg equilibrium diagram and the reported composition results in Figs. 6 and 7, the formation of γ(Al12Mg17) and β(Al3Mg2) intermetallic compounds in the bonding zone can be anticipated. Region A is composed of γ, which is considered Mg and Al solid solution. A mixture of γ and β and a mixture of γ and β with higher mass fraction of β are the formed layers in regions B and C, respectively.
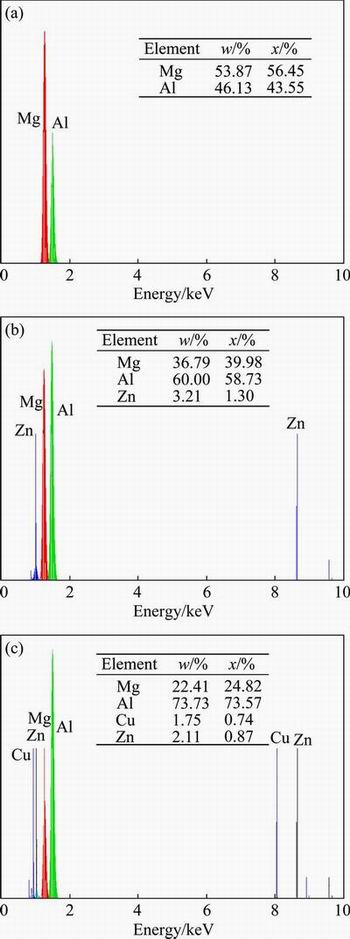
Fig. 6 EDS spectra of layers in zone A (a), zone B (b) and zone C (c) of specimen welded at 430 °C for 60 min
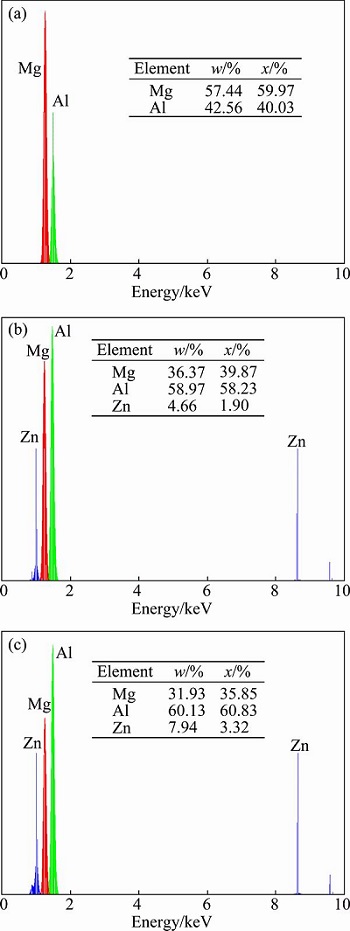
Fig. 7 EDS spectra of layers in zone A (a), zone B (b) and zone C (c) of specimen welded at 430 °C for 120 min
In Derby’s theoretical model [18-20], the possible diffusion bonding mechanisms are identified as: 1) the plastic deformation of surface asperities; 2) the power-law creep deformation of the surface; 3) the diffusion of matter from interfacial void surfaces to growing necks; 4) the diffusion of matter from bonded regions on the interface to growing necks. At the beginning of diffusion welding, Mg and Al atoms have a driving force to diffuse into the contact interface with different content gradients. After that, they diffuse to the irregular interface with much micro-interstice and the contents of Mg and Al increase. The reaction between Mg and Al atoms happens and a layer containing Mg and Al forms. Then, the concentrated Al at the Mg/MgAl interface begins to diffuse to the Mg side across the original boundary with the increase of temperature. After that, the reaction 17Mg+12Al→Al12Mg17 takes place and the Al12Mg17 phase forms. At the third stage, the concentrated Mg at the MgAl/Al interface also diffuses to the Al side. Then, the reaction 2Mg+3Al→Al3Mg2 occurs and the Al3Mg2 phase forms. Finally, with the continuous increase of heating temperature, Mg and Al atoms in the Mg/Al ITZ continuously diffuse into each other. However, the phases in the ITZ do not change any longer, in other words, only the thickness of the intermetallic layer increases gradually [21].
3.2 Mechanical strength
The microhardness profiles were measured out across the diffusion bonded joints in the temperature range of 430-450 °C during welding for 60 and 120 min. It can be seen from Fig. 8 that by increasing the bonding temperature, the hardness increases significantly in the reaction layer. The Al and Mg base materials have the average hardness values of HV 60 and HV 40, respectively. While in the reaction layer, some quite large microhardness values are noticeable, the largest value is HV 176, due to the formation of brittle intermetallic compounds at 450 °C with the holding time of 120 min. It reveals that by increasing the temperature, the amount of intermetallic compounds and solid solution in the diffusion bonding will increase too, which leads to the increase of microhardness values in the joint [5]. The influences of time on the microhardness were determined (Fig. 9). It can be seen that the diffusion welding at 430 °C for 60 min leads to the maximum hardness value of HV 70 in the interfacial layer, while it reaches
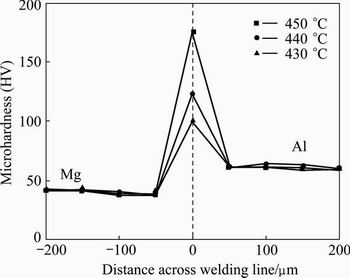
Fig. 8 Effect of temperature on microhardness across bonding line with holding time of 120 min
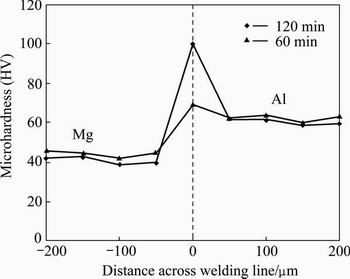
Fig. 9 Effect of holding time on microhardness across bonding line at 430 °C
HV 100 at the same temperature with the holding time of 120 min. The increase of hardness value due to the increase of holding time is attributed to the growth of the brittle intermetallic compounds Al3Mg2 and Al12Mg17 [17].
The effect of welding temperature on the shear strength is shown in Fig. 10. It is indicated that by increasing the welding temperature, the bonding strength reduces due to the enhanced volume fraction of brittle intermetallics. At the holding time of 60 min, the maximum amount of the shear strength at 430 °C is up to 24 MPa and that at 450 °C decreases to 15 MPa which is related to the bonded samples. At lower welding temperature, the plastic deformation of the bonding surface asperities causes close contact, which counterbalances the embrittlement because of the intermetallic compounds. Therefore, the shear bond strength obviously improves. It is observed that the thickness of brittle intermetallic compounds significantly increases at 450 °C and the embrittlement effect over- balances the positive effect obtained because of the improvement in coalescence of faying surfaces [7]. Therefore, the shear bonding strength drops. As illustrated in Fig. 11, a further drop in joining strength is observed by increasing the holding time. For longer bonding time (120 min), the most pronounced features such as composition homogenization and grain coarsening are observed at the interface. The brittle compounds (Al12Mg17 and Al3Mg2) and grain coarsening of the joint are the main reasons for impairing the joint shear strength with longer holding time [7].
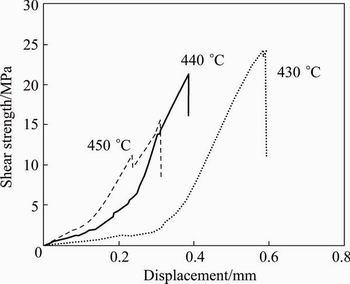
Fig. 10 Effect of temperature on shear strength of welded joints with holding time of 60 min
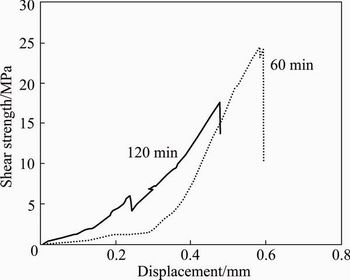
Fig. 11 Effect of holding time on shear strength of welded joints at 430 °C
4 Conclusions
1) 7075Al alloy and AZ31B Mg alloy were bonded successfully by diffusion bonding process. For holding time of 60 min, increasing the bonding temperature from 430 to 450 °C leads to more atoms diffusing across the interface, and the thickness of ITZ layer increases by 6%. But that increases by 26% for the holding time of 120 min. This finding shows that increasing temperature along with selecting the proper welding time can have a remarkable effect on the thickness of ITZ layer.
2) The EDS analysis of the joints shows that the formed layers in zones A, B, C from the Mg side towards the Al side are composed of γ(Al12Mg17), a mixture of γ and β(Al3Mg2), and a mixture of γ and β with higher mass fraction of β, respectively.
3) The shear strengths of the joints which were bonded at the temperature range of 430-450 °C for 60 and 120 min indicate that increasing both the temperature and holding time causes more intermetallic compounds. As a result, the shear strength has a considerable reduction. Moreover, due to the existence of different reaction products and brittle phases, the hardness of the joints in the interfacial transition zone is enhanced by increasing the temperature and holding time. The maximum hardness of HV 176 is achieved during the test conducted at 450 °C for 120 min.
References
[1] KEMAL A, YAKUP K, NIZAMETTIN K. Experimental study of diffusion welding/bonding of titanium to copper [J]. Materials and Design, 2012, 37: 356-368.
[2] RAVISANKAR B, KRISHNAMOORTHI J, RAMAKRISHNAN S S, ANGELO P C. Diffusion bonding of SU 263 [J]. Material Processing Technology, 2009, 209(4): 2135-2144.
[3] AYDIN M, GURLER R, TURKER M. The diffusion welding of 7075Al-3%SiC particles reinforced composites [J]. Physics of Metals and Metallography, 2009, 107(2): 206-210.
[4] WU G Q, LI Z F, LUO G X , LI H Y, HUANG Z. Dynamic simulation of solid-state diffusion bonding [J]. Materials Science and Engineering A, 2007, 452: 529-535.
[5] MAHENDRAN G, BALASUBRAMANIAN V, SENTHILVELAN T. Influences of diffusion bonding process parameters on bond characteristics of Mg-Cu dissimilar joints [J]. Transactions of Nonferrous Metals Society of China, 2010, 20(6): 997-1005.
[6] CHEN S D, SOH A K, KE F J. Molecular dynamics modeling of diffusion bonding [J]. Scripta Materialia, 2005, 52: 1135-1140.
[7] MAHENDRAN G, BABU S, BALASUBRAMANIAN V. Analyzing the effect of diffusion bonding process parameters on bond characteristics of Mg-Al dissimilar joints [J]. Journal of Materials Engineering and Performance, 2010, 19(5): 657-665.
[8] EMEL T, JERRY E, GOULD B, JOHN C L. Dissimilar friction welding of 6061-T6 aluminum and AISI 1018 steel: Properties and microstructural characterization [J]. Materials and Design, 2010, 31: 2305-2311.
[9] SOMEKAWA H, WATANABE H, MUKAI T, HIGASHI K. Low temperature diffusion bounding in a super plastic AZ31 magnesium alloy [J]. Scripta Materialia, 2003, 48(9): 1249-1254.
[10] FERNANDUS M J, SENTHILKUMAR T, BALASUBRAMANIAN V. Developing temperature–time and pressure–time diagrams for diffusion bonding AZ80 magnesium and AA6061 aluminum alloys [J]. Materials and Design, 2011, 32: 1651-1656.
[11] JAFARIAN M, KHODABANDEH A, MANAFI S. Evaluation of diffusion welding of 6061 aluminum and AZ31 magnesium alloys without using an interlayer [J]. Materials and Design, 2015, 65: 160-164.
[12] FENG J C, ZHANG B G, QIAN Y Y, HE P. Microstructure and strength of diffusion bonded joints of TiAl base alloy to steel [J]. Materials Characterization, 2002, 48: 401-406.
[13] PETERSON K A, DUTTA I, CHEN M. Processing and characterization of diffusion bonded Al-Si interfaces [J]. Journal of Material Processing Technology, 2004, 145: 99-108.
[14] SCHONFELDER B, GOTTSTEIN G, SHVINDLERMAN L S. Comparative study of grain-boundary migration and grain-boundary self-diffusion of [001] twist-grain boundaries in copper by atomistic simulations [J]. Acta Materialia, 2005, 53: 1597-1609.
[15] JIAN Z H, QIANG S H, GUOGIANG L, MEIJURAN L, LIANMENG Z. Microstructure and bonding strength of diffusion welding of Mo/Cu joints with Ni interlayer [J]. Materials and Design, 2012, 39: 81-86.
[16] BARRENA M J, GOMEZ J M, MATESANZ L. Interfacial microstructure and mechanical strength of WC-Co/90MnCrV8 cold work tool steel diffusion bonded joint with Cu/Ni electroplated interlayer [J]. Materials and Design, 2010, 31: 3389-3394.
[17] MAHENDIRAN G, BALASUBRAMANIAN V, SETHILVELAN T. Mechanical and metallurgical properties of diffusion bonded AA2024 aluminum alloy and commercial grade copper [J]. Elixir Mechanical Engineering, 2011, 38: 4283-4289.
[18] DERBY B, WALLACH E R. Theoretical model for diffusion bonding [J]. Metal Science, 1982, 16: 49-56.
[19] DERBY B, WALLACH E R. Diffusion bonding: Development of theoretical model [J]. Metal Science, 1984, 18: 427-431.
[20] ELZEY D M, WADLEY H. Modeling the densification of metal matrix composite monotape [J]. Acta Metallurgica et Materialia, 1993, 41: 2297-2316.
[21] JUAN Wang, LI Ya-jiang, HUANG Wan-qun. Interface microstructure and diffusion kinetics in diffusion bonded Mg/Al joint [J]. Reaction Kinetics and Catalysis Letters, 2008, 95(1): 71-79.
焊接温度和焊接时间对7075铝合金和AZ31B镁合金扩散焊接头性能的影响
Abdolhamid AZIZI1, Hossein ALIMARDAN2
1. Department of Engineering, Ilam University, Ilam 69315-516, Iran;
2. Department of Engineering, Kermanshah Branch, Islamic Azad University, Kermanshah 6718997551, Iran
摘 要:在压力29 MPa、不同焊接温度和焊接时间下,采用扩散焊技术连接7075铝合金和AZ31B镁合金。对样品界面进行扫描电镜观察、剪切测试和显微硬度测试来研究焊接温度和焊接时间对可焊性的影响。结果表明: 7075铝合金/AZ31B镁合金复合板材被很好地连接在一起,且在焊合区形成金属间化合物如Al12Mg17 和 Al3Mg2。由于晶粒粗化和脆性化合物的形成,升高焊接温度和延长焊接时间会导致剪切强度降低和界面焊接硬度增加。在450 °C焊接120 min得到的扩焊接接头具有最小的剪切强度(15 MPa)和最大的显微硬度(HV 176)。提高焊接温度且选择合适的焊接时间能显著地提高焊接界面层厚度。将焊接温度从430 °C提高到450 °C,焊接时间为120 min时,焊接界面层厚度增加了26%,而当焊接时间为60 min时,界面层厚度增加了6%。
关键词:Al合金;Mg合金;扩散焊;焊接温度;焊接持续时间
(Edited by Mu-lan QIN)
Corresponding author: Abdolhamid AZIZI; Tel: +98-9124056441, Fax: +98-8412227026, E-mail: ah.azizi@ilam.ac.ir
DOI: 10.1016/S1003-6326(16)64091-8