文章编号: 1004-0609(2005)06-0946-06
纯铝及其合金的微等离子体氧化成膜特征
吴振东1, 2, 姜兆华1, 姚忠平1, 孙学通1, 张雪林1
(1. 哈尔滨工业大学 应用化学系, 哈尔滨 150001; 2. 白城师范学院 化学系, 白城 137000 )
摘 要: 研究了纯Al及其合金LC9、 LY12 在偏铝酸钠溶液中微等离子体氧化成膜的特点。 通过X射线衍射, SEM和EMPA等分析了陶瓷膜层的相组成及表面、 截面形貌和膜层截面的元素含量分布, 利用测厚仪测量了陶瓷膜层的厚度。 结果显示: Al膜层由α-Al2O3相组成, LC9膜层由γ-Al2O3相组成, LY12膜层由γ-Al2O3和α-Al2O3两相组成, 且膜层都由致密层和疏松层构成; 膜层的厚度随时间都近似呈线性变化; 在Al和LY12膜层中, 由内向外铝元素的含量逐渐增加; 在LC9膜层中, 铝元素的分布略呈两侧高中间低; 在LC9和LY12膜层中, 镁元素分布比较均匀; 在LC9膜层中, 含有很少量的锌元素, 而铜元素含量很不明显; 在LY12膜层中含有很少量的铜元素。
关键词: 纯铝; 铝合金; 微等离子体氧化; 陶瓷膜
中图分类号: TG174.453 文献标识码: A
Coating-forming characteristics of pure aluminum and aluminum alloy during micro-plasma oxidation
WU Zhen-dong1, 2, JIANG Zhao-hua1, YAO Zhong-ping1,
SUN Xue-tong1, ZHANG Xue-lin1
(1. Department of Applied Chemistry, Harbin Institute of Technology, Harbin 150001, China;
2. Department of Chemistry, Normal Institute of Baicheng, Baicheng 137000, China)
Abstract: The micro-plasma oxidation(MPO) coating-forming characteristics for different kinds of aluminum alloys (pure Al, LY12 and LC9) in NaAlO2 solution were study. Phase composition, section morphologies and the element distribution of the coating were analyzed by XRD, SEM and EPMA, respectively. The thickness of the coatings was measured by CTG-10 eddy current coating thickness gauge. The results show that the produced coating on pure Al is composed of α-Al2O3, the coating on LC9 is composed of γ-Al2O3 and the coating on LY12 is composed of α-Al2O3 and γ-Al2O3. The coating is composed of a compact layer and a loose layer. The thickness of the coatings on different substrate materials increases lineally with the MPO time increasing. For different substrate materials, Al in the coating all increases gradually from the inner layer to the outer layer. For LY12 and LC9, Mg in the coating distributes uniformly. For LC9, there is a little Zn in the coating and Cu does not exist apparently. For LY12, there is a little Cu on the coating.
Key words: pure Al; aluminum alloy; micro-plasma oxidation; ceramic coatings
微等离子体氧化又称微弧氧化或阳极火花沉积, 是基于阀金属在电解质溶液中引起阳极上微等离子体击穿(火花放电或微弧)原位生长陶瓷膜的表面改性技术。 20世纪30年代初期, Gunterschulze和Betz首次发现了在高压电场下浸在某种电解液中的金属表面发生火花放电现象, 认为高压放电对金属表面具有破坏作用。 后来进一步研究发现, 高压放电可以在金属表面生长出氧化膜[1]。 20世纪70年代末期, 苏联、 美国、 德国等国家开始加快此项技术的研究。 我国20世纪90年代中期以后才开始微等离子体氧化的研究。 影响微等离子体氧化的因素主要为电源, 电解液和基体材料3部分。 电源和电解液对金属微等离子体氧化形成陶瓷膜的组成、 结构、 性能等的影响研究比较多, 也比较深入[2-4], 基体的化学成分对陶瓷膜层的影响研究相对较少。 本文作者选取纯Al、 LC9、 LY12在偏铝酸钠溶液中进行微等离子体氧化处理, 并研究了其成膜特点, 以便深入认识纯铝及其合金微等离子体氧化间的差别和实际应用。
1 实验
实验材料为纯Al、 LC9及LY12合金, 试样尺寸为15.0mm×15.0mm×1.5mm, 铝及其合金表面粗细砂纸打磨掉氧化膜及包铝层, 磨细磨亮。 自制2kW双向脉冲电源, Al及其合金为阳极, 不锈钢电解液槽为阴极。 保持正负相电流密度均恒定为8A/dm2, 正负相占空比均为45%, 频率为50Hz, 0.1mol/LNaAlO2水溶液, 搅拌循环水冷却, 温度不高于35℃。 反应时间分别为30、 60、 90、 120和150min。
利用S-4500型扫描电镜, 用电子探针观察陶瓷膜表面与截面的形貌和陶瓷膜层中各主要元素的含量分布, 用日本理光D/max-rB自动X射线衍射仪(铜靶, Kα射线)研究陶瓷膜层的相组成, 用时代公司生产的CTG-10电涡流测厚仪测量陶瓷膜层厚度。
2 结果与分析
2.1 槽电压随时间变化
微等离子体氧化按槽压—时间曲线可分为无火花阶段(又称普通阳极化阶段)、 火花阶段、 微弧阶段和弧阶段[5]。 图1和2所示分别为正、 负相槽压与时间的关系。 由图1和2可知, 正负相槽压-时间曲线变化大致趋势相同, 其中LY12的正负相槽压时间曲线变化比较均匀。 无火花阶段: 氧化开始时, 表面都有气泡产生, 随电压上升都产生辉光放电现象(产生辉光时的电压称辉光电压)[6], 金属表面逐渐变亮, 辉光放电持续时间比较短(辉光放电时, Al通体暗略呈黄色, LC9通体呈暗红色, LY12 通体呈亮黄色)。
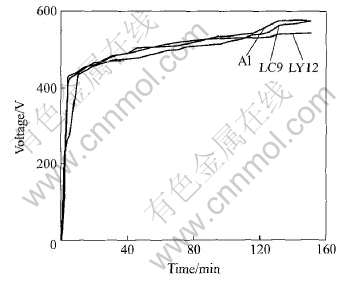
图1 正相槽压—时间曲线
Fig.1 Curves for voltage and time of anode pulse

图2 负相槽压—时间曲线图
Fig.2 Curves for voltage and time of cathode pulse
表1所示为合金表面的放电电压。 由表1可知, 正相起始辉光电压按Al>LC9>LY12依次减小, 负相起始辉光电压按LC9>Al>LY12依次减小。 火花阶段: 表面开始出现第一个火花, 火花很小, 随反应的进行, 火花迅速增多, 快速游动, 密集, 出现噪声, 并随着微等离子体氧化反应进入微弧及弧阶段后, 噪声变得更大。 Al火花颜色最浅, 较明亮; LC9 火花呈现的淡紫色, 较LY12 略微深一些。 正相起始火花电压按Al>LC9>LY12依次减小, 且Al的正相起始火花电压和LC9的接近; 负相火花电压按LC9>Al>LY12依次减小。 微弧阶段: 火花体积增加, 持续时间较长, 在火花放电之后, 便产生了更强烈的放电, 有许多微小的电弧在阳极表面上扫描, 伴随有弧光和声音的产生, 火花均匀, 电压上升的速率减小, 它们在这一阶段差别小。 弧阶段: 火花体积继续增大、 数量减少, 扫描速度减弱, 停留时间变长, 电压上升缓慢。 Al的几个大火花和一些小火花共存, 分布不均匀; LC9和LY12 表面只有几个大火花, 颜色变深, 在最后阶段, 它们的火花颜色都趋向橘黄色。 造成上述差别是由于铝及其合金元素不同, 在LC9和LY12基体内, Cu和Mg等元素的存在有利于微弧氧化[7], 而在LC9基体内含大量锌元素, 对成膜有比较大的破坏作用所致[8]。
2.2 膜层形貌与元素分布
Al、 LC9和LY12微等离子体氧化反应30min 时, 膜层表面都很均匀细腻, 且随反应时间的延长, 膜层表面粗糙度逐渐变大。 图3所示为微等离子体氧化120min时, 陶瓷膜层的表面和截面形貌
表1 Al、 LC9、 LY12表面放电情况
Table 1 Discharge voltages of alloys surfaces


图3 不同基体材料制备的陶瓷膜的表面、 截面形貌及截面的元素分布
Fig.3 Surfacial ((a), (b), (c)) and sectional((d), (e), (f)) morphologies and elements distributions((g), (h), (i)) of ceramic coatings with different based materials
及截面元素电子探针线分析。 从图3(a), (b)和(c)膜层表面形貌可看出, 都有大量的圆形堆积物, 具有明显的烧结熔融痕迹, 残留些类似火山喷发的小孔(见文献[9-11])。 Al 形成膜层表面的烧结颗粒大且较均匀, 存在裂纹, LC9和LY12膜层表面形貌差别不大, 颗粒、 裂纹大小接近, 不均匀。 由图3 (d), (e)和(f)可知, 陶瓷膜层都是由致密层和临近表面的疏松层构成, 与文献报道一致[12, 13], 而Al膜层和LC9膜层的致密层及疏松层都不如LY12明显。 Al膜层与基体结合略差, LY12膜层与基体结合略好, LC9膜层与基体结合好。 这可能是由于γ-Al2O3相转变为α-Al2O3相使体积收缩了14.3%, 从而使Al和LY12的膜层与基体结合略差所致。 沿着膜层横截面位置线扫描可知(见图3 (g), (h)和(i)), 在Al膜层中, 铝元素分布不均匀, 由内向外含量增加较快; 在LC9膜层中, 铝元素分布略呈现两侧高中间低; 在LY12膜层中, 铝元素分布比较均匀, 含量呈上升趋势。 这是由于铝酸钠溶液中的铝元素也参与了微等离子体氧化, 从溶液进入膜层, 使得Al和LY12膜层中的铝元素含量由内向外增加所致。 也可能是由于LC9基体中存在大量的锌元素, 抑制了LC9膜层内铝元素的扩散迁移, 使其在膜层中略微呈现两侧高中间低所致。 在LC9和LY12膜层中, 基体的镁元素含量明显高于膜外, 说明镁元素已进入膜层, 分布比较均匀。 在LC9膜层中, 基体的铜元素含量与膜外的相比较, 变化非常不明显, 而锌元素的含量略有变化, 说明有少量的锌元素进入膜层。 在LY12中, 基体的铜元素与膜外的比较略有变化, 说明有很少量的铜元素进入膜层。
2.3 膜层相组成
选取Al、 LC9和LY12微等离子体氧化120min制备的膜层, 进行X射线衍射膜层相组成分析, 结果如图4所示。 由图可知, Al、 LC9和LY12制备的膜层的相组成特点突出, Al膜层由α-Al2O3
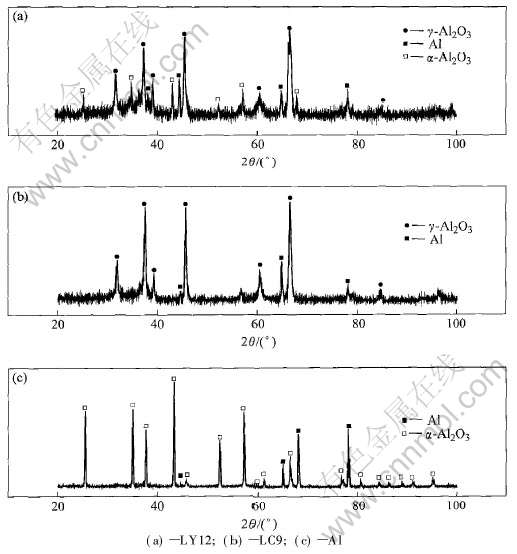
图4 铝及其合金反应120min时制备的陶瓷膜的X射线衍射谱
Fig.4 XRD patterns of coatings prepared by Al and Al alloy for 120min
组成, LC9膜层由γ-Al2O3组成, LY12膜层由大量γ-Al2O3和少量α-Al2O3相组成, 与文献[14-16]类似。 造成它们膜层相组成差别的主要是由于构成Al, LC9和LY12基体的化学成份和含量不同所致。 α-Al2O3是高温稳定相, γ-Al2O3为低温稳定相。 Al膜层由α-Al2O3相组成, 为弄清其微等离子体氧化初期是直接生成α-Al2O3相, 还是首先生成γ-Al2O3相, 然后转变为α-Al2O3相。 本文作者选取纯铝Al微等离子体氧化10min形成的膜层进行X射线衍射相组成分析, 结果如图5所示。 从图5可知, 在纯铝Al膜层中, 既有α-Al2O3相, 又有γ-Al2O3相。 由于γ-Al2O3形核自由能比α-Al2O3小, 因此, 首先生成了γ-Al2O3相, 但随着反应的进行, 微等离子体氧化温度升高, 发生了由γ-Al2O3相向α-Al2O3相的高温相变, 反应120min时, 全部转化为α-Al2O3相。 而在LY12中, 由于含有其它元素, 导致了由γ-Al2O3相向α-Al2O3相转变的速度减慢, 因而高温相α-Al2O3与低温相γ-Al2O3共存。 在LC9中, 可能是由于含有大量的锌元素, 抑制了由γ-Al2O3相向α-Al2O3相的转变, 从而只生成γ-Al2O3相所致。
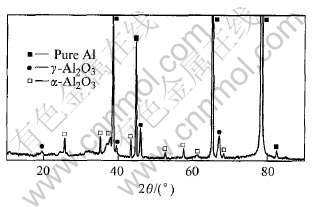
图5 纯铝基体反应10min时陶瓷膜的X射线衍射谱
Fig.5 XRD pattern of coatings for pure aluminum reacted for 10min
2.4 膜层厚度生长速率
Al、 LC9和LY12在微等离子体氧化过程中, 膜层的生长速率不同。 图6所示为合金的厚度与时间关系曲线。 由图6可知, Al、 LC9和LY12的膜厚都随反应时间的延长近似呈线性增加, 在微等离子体氧化反应时间相同时, 膜厚按Al〈LC9〈LY12的顺序依次增大。 斜率即膜层生长速率, 经最小二乘法拟合得方程:
Al: d=0.54t-5.73;
LC9: d=0.69t-2.71;
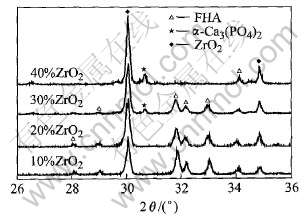
图6 合金的厚度与时间的关系
Fig.6 Relationship between thickness and time of alloys
LY12: d=0.73t+4.995
式中 d为厚度, μm; t为时间, min。
3 结论
1) 膜层都由致密层和疏松层构成。 Al膜层与基体结合略差, LC9膜层与基体结合较好, LY12膜层与基体结合略好。
2) 在Al和LY12膜层中, 由内向外铝元素的含量逐渐增加; 在LC9膜层中, 铝元素的分布略呈两侧高中间低; 在LC9和LY12膜层中, 镁元素分布比较均匀; 在LC9膜层中, 含有很少量的锌元素, 而铜元素含量很不明显; 在LY12膜层中含有很少量的铜元素。
3) 微等离子体氧化120min , Al所得的膜层完全由α-Al2O3相组成; LC9膜层完全由γ-Al2O3相组成; LY12膜层由大量γ-Al2O3相和少量α-Al2O3相组成。
4) 铝及其合金制备的膜层厚度都随时间近似呈线性变化, 膜厚按Al〈LC9〈LY12次序增加。
REFERENCES
[1]薛文彬, 邓志威, 来永春, 等. 有色金属表面微弧氧化技术评述[J]. 金属热处理, 2000(1): 1-3.
XUE Wen-bin, DENG Zhi-wei, LAI Yong-chun, et al. Review of micro-arc oxidation technique on surface of nonferrous metals[J]. Heat Treatment of Metals, 2000(1): 1-3.
[2]张欣宇, 方明, 吕江川, 等. 电解液参数对铝合金微弧氧化的影响[J]. 材料保护, 2002, 35(8): 39-41.
ZHANG Xin-yu, FANG Ming, LU Jiang-chuan, et al. Effect of electrolyte parameters on micro-arc oxidation of aluminum alloy[J]. Materials Protection, 2002, 35(8): 39-41.
[3]刘凤岭, 骆更新, 毛立信. 微弧氧化与材料表面陶瓷化[J]. 材料保护, 1998, 31(3): 22-24.
LU Feng-ling, LUO Geng-xin, MAO Li-xin. Micro-arc oxidation and ceramic process of material surface[J]. Materials Protection, 1998, 31(3): 22-24.
[4]顾伟超, 沈德久, 王玉林, 等. 铝及其合金微弧氧化技术的研究与进展[J]. 金属热处理, 2004, 29(1): 53-58.
GU Wei-chao, SHEN De-jiu, WANG Yu-lin, et al. Research and progress oxidation on aluminum and its alloys[J]. Transactions of Metals and Heat Treatment, 2004, 29(1): 53-58.
[5]姜兆华, 辛世刚, 王福平, 等. 铝合金在水玻璃KOH NaAlO2体系中的微等离子体氧化[J]. 中国有色金属学报, 2000, 10(4): 519-524.
JIANG Zhao-hua, XIN Shi-gang, WANG Fu-ping, et al. Micro-plasma oxidation of aluminium alloy in sodium silicate-KOH-NaAlO2[J]. The Chinese Journal of Nonferrous Metals, 2002, 10(4): 519-524.
[6]来永春, 邓志威, 宋红卫, 等. 耐磨性微弧氧化膜的特性[J]. 摩擦学学报, 2000, 20(4): 304-306.
LAI Yong-chun, DENG Zhi-wei, SONG Hong-wei, et al. Properties of micro arc oxidation films on aluminum alloy substrate[J]. Tribology, 2000, 20(4): 304-306.
[7]周海晖, 旷亚非, 侯朝辉, 等. LF4合金在磷酸盐-氢氧化钠溶液中的微弧氧化[J]. 湖南大学学报(自然科学版), 2001, 28(5): 67-71.
ZHOU Hai-hui, KUANG Ya-fei, HOU Zhao-hui, et al. Microarc oxidation of LF4 alloy in mixed phosphate electrolytes[J]. Journal of Hunan University (Natural Sciences Edition), 2001, 28(5): 67-71.
[8]张文华, 胡正前, 马晋. 俄罗斯微弧氧化技术进展[J]. 轻合金加工技术, 2004, 32(1): 25-29.
ZHANG Wen-hua, HU Zheng-qian, MA Jin.The development of research on micro-arc oxidation technology in russia[J]. The Technology of Nonferrous Metal, 2004, 32(1): 25-29.
[9]罗胜联, 周海晖, 陈金华, 等. ZL系列铸铝合金的微弧氧化[J]. 中国有色金属学报, 2002, 12(3): 491-495.
LUO Sheng-lian, ZHOU Hai-hui, CHEN Jin-hua, et al. Microarc oxidation of ZL cast aluminum alloys[J]. The Chinese Journal of Nonferrous Metals, 2002, 12(3): 491-495.
[10]王亚明, 蒋百灵, 郭立新, 等. 磷酸盐系溶液中钛合金微弧氧化涂层生长与组织结构[J]. 中国有色金属学报, 2004, 14(4): 548-553.
WANG Ya-ming, JIANG Bai-ling, GUO Li-xin, et al. Growth and microstructure of microarc oxidation coatings on titanium alloy insolution containing phosphate[J]. The Chinese Journal of Nonferrous Metals, 2004, 14(4): 548-553.
[11]蒋百灵, 白力静, 蒋永锋. LY12铝合金表面氧化铝陶瓷层的生长过程[J]. 中国有色金属学报, 2001, 11(2): 186-189.
JIANG Bai-ling, BAI Li-jing, JIANG Yong-feng. Growth of alumina ceramic coatings on aluminum matrix material surface[J]. The Chinese Journal of Nonferrous Metals, 2001, 11(2): 186-189.
[12]Dittrch K H, Krysmann W, Kurze P, et al. Structure and properties of ANOF layers[J]. Cryst Res Technol, 1984, 19(1): 93-99.
[13]薛文斌, 邓志威, 汪新福, 等. 铝合金微弧氧化陶瓷膜的形貌及相组成[J].北京师范大学学报, 1996(1): 67-70.
XUE Wen-bin, DENG Zhi-wei, WANG Xin-fu, et al. Analysis of morphology and phase composition of ceramic films formed by the micro arc oxidation of aluminum alloys[J]. Journal of Beijing Normal University (Science), 1996(1): 67-70.
[14]辛世刚, 姜兆华, 赵荣根, 等. 微等离子体氧化α-Al2O3陶瓷膜的组织结构与形成过程[J]. 无机化学学报, 2004, 20(6): 671-674.
XIN Shi-gang, JIANG Zhao-hua, ZHAO Rong-gen, et al. Microstructure and formation process of alluminia ceramic coatings by micro plasma oxidation[J]. Chin J Inor Chem, 2004(6): 671-674.
[15]Xue W, Wang D Z, Lai Y, et al. Analysis of phase distribution for ceramic coatings formed by microarc oxidation on aluminum alloy[J]. J Am Ceram Soc, 1998, 81(5): 1365-1368.
[16]Nie X, Leyland A, Song H W, et al. Thickness effects on the mechanical properties of micro-arc discharge oxide coatings on aluminium alloys[J]. Surf Coat Technol, 1999, 116-119: 1055-1060.
(编辑李艳红)
基金项目: 国家自然科学基金资助项目(50171026)
收稿日期: 2004-11-24; 修订日期: 2004-03-21
作者简介: 吴振东(1963-), 男, 博士研究生.
通讯作者: 姜兆华, 教授, 博士; 电话: 0451-86413707; E-mail: jiangzhaohua@hit.edu.cn