
Localized corrosion of LY12CZ under stress in chloride media
RAO Si-xian(饶思贤), ZHANG Zheng(张 峥), ZHU Li-qun(朱立群), ZHONG Qun-peng(钟群鹏)
School of Material Science and Engineering, Beijing University of Aeronautics and Astronautics,
Beijing 100083, China
Received 28 July 2006; accepted 15 September 2006
Abstract: Electrochemical methods were applied to investigate the corrosion behaviour of LY12CZ under applied stress in 3% sodium chloride aqueous solution. The experimental results indicate that LY12CZ shows two breakdown potentials on its polarization curve: one is related to the dissolution of the intermetallic particles and the other is related to the cracking of oxidation film and the dissolution of the matrix. When the stress is applied, it varies both breakdown potentials and makes the intermetallic particles and matrix dissolute at lower potentials. The relationship between the variation of the two breakdown potentials and applied stress was summarized. At the same time the influence of stress on the pitting and intergranular corrosion sensitivity of LY12CZ was also investigated. From the results it can be concluded that the stress can significantly affect the localized corrosion behaviour of LY12CZ in 3% NaCl solution.
Key words: LY12CZ; localized corrosion; intermetallic; applied stress; mechanochemical effect
1 Introduction
Because of the characteristics of high mechanical performance, high corrosion resistance, low density and low cost, LY12CZ gets its wide applications in aircraft and automotive industries. Nevertheless aluminum alloys are easily affected by different kinds of corrosion such as pitting corrosion, intergranular corrosion and stress corrosion cracking. When the stress is applied on the structures made of LY12CZ, the interactions between stress and environment will furthermore enhance its sensitivity to the corrosions above (commonly we called this interaction of stress and environment as mechanochemical effect[1]). It is necessary to uncover how much the stress can affect the corrosion behaviour of LY12CZ. The effect of applied stress on the corrosion behaviour of various metals or alloys have been carried out by many researchers[2-10], BONORA et al[4] and BEN-HAMU et al[5] made investigations in this interaction of Mg alloys and got the correlation between the mechanochemical behaviour and strain hardening stages during plastic deformation. GUTMAN et al[3] measured the mechanochemical effect on static loading mode for type 316L stainless steel and found that both passive and transpassive current densities reach a maximum during plastic strain growth. It is generally accepted that there exists an interaction between stress and environment and this mechanochemical effect has an accelerating effect on the corrosion behaviour of metals.
In this paper, the effect of stress on the pitting corrosion behaviour of LY12CZ is investigated in the media of 3% NaCl solution. The purpose is to uncover the effect of stress on the corrosion behaviour of LY12CZ. Specific attention is given to the variation of breakdown potentials and the susceptibility to pitting corrosion and intergranular corrosion under stress.
2 Experimental
The material selected in the experiments is 2 mm thick LY12CZ plate. The shape of the coupons is shown in Fig.1, and the working face is in the center. Firstly 10% NaOH was used to remove the plymetal on the coupons (the remained thickness is 1.7 mm), then the specimens were mechanically polished to 4000 grit SiC paper and then further polished with 1 μm diamond paste and rinsed with distilled water, finally neoprene is used to seal the non-working face. Before experiments the specimens were installed in the electrolytic cell. The loading equipment is shown in Fig.2.
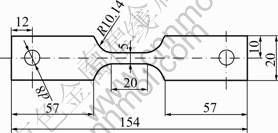
Fig.1 Dimension of specimen (mm)
All the electrochemical measurements were carried out at room temperature in naturally aerated 3% NaCl solution (pH=6). A saturated calomel electrode was was used as the reference electrode and a platinum electrode used as the counter electrode. Before electrochemical experiments the stress—strain curve of LY12CZ was measured, as shown in Fig.3.
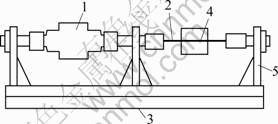
Fig.2 Sketch of tensile testing machine: 1 Tension sensor; 2 Specimen; 3 Base; 4 Glass electrolytic cell; 5 Stiffener
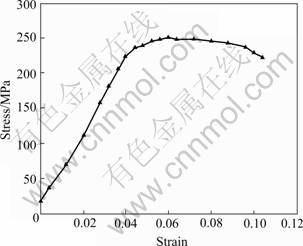
Fig.3 Stress—strain curve of LY12CZ aluminum aqueous solution
3 Result and discussion
3.1 Microstructure of LY12CZ
Commonly the susceptibility of aluminum alloys to pitting, intergranular corrosion and other corrosion types depends on the alloy microstructure. The main harding phases of LY12CZ are S phase (Al2CuMg) and Al2Cu phase. Optical and SEM observations in the experiments show the presence of uniform distribution of coarse intermetallic particles(Fig.4), of which the size can reach 20μm. EDS analysis of LY12CZ shows that there are two types of precipitates that can be distinguished. The black spherical-dot-shaped one is Al-Cu-Mg particle, and the grey irregular-shaped one is Al-Cu-Mn-Fe particles. Such observations have already been carried out by other authors. Commonly the black Al-Cu-Mn particles are assigned to Al2CuMg (S phase), and the grey Al-Cu-Mn- Fe particle is assigned to be different chemical phases: Al6(Cu, Fe, Mn), Al7Fe2Cu and (Al,Cu)6Mn. It has been found that a kind of dispersoid Al20Mn3Cu2 also exists in the matrix, which is uniformly distributed in the matrix. It has also been discovered that the S phase particles are surrounded by dispersoid-free zones. In S phase, the content of copper is 38% (mass fraction), but in dispersoid the content of copper is 15%, so around every Al-Cu-Mg particle or dispersoid there is a copper- depleting zone, and the copper-depleting zone around S phase is stronger than that around the dispersoid.
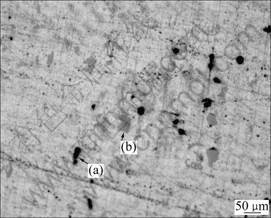
Fig.4 Intermetallic particles in LY12CZ alloys (in 3%NaCl): (a) Al-Cu-Mg contained particle; (b) Al-Cu-Mn-Fe contained particles
3.2 Breakdown potential of LY12CZ in sodium chloride solution and effect of applied stress on variation of breakdown potential
In alloys containing more than one phase, different breakdown potential may indicate the breakdown of different phases due to the heterogeneous microstructure of LY12CZ. We can deduce that there will not be only one breakdown potential in LY12CZ. Investigations carried out by GUILLAUMIN et al [9-13] have observed two breakdown potentials in the anodic polarization curve of 2024T351 aluminum alloy in deaerated 1 mol/L NaCl solution and approved this fact. In LY12CZ the first breakdown potential(φb1) around 720 mV corresponds to the breakdown of the Al-Cu-Mg rich particle(S phase). When the potential is kept below φb1, the matrix, the Al-Cu-Mn-Fe particle and S phase remain unattacked. Only the zone around S phase is likely to dissolve lightly at potential below φb1(due to the low content of copper around S phase, and S phase and the rest of the matrix both show cathodic behaviour in comparison to the copper-depleting zone around S phase). When the potential reaches φb1, S phase begins to dissolve. As no other phase is found to be attacked between φb1 and φb2, the dissolution of S phase is responsible for the anodic current rise on the polarization curve. Only after φb2 is reached, the grain boundary begins to be attacked and large pits begin to develop. So φb2 around 620 mV is responsible for the breakdown of the oxidation film and dissolution of the matrix, which is directly associated with pitting corrosion and inter- granular corrosion of LY12CZ.
In experiments the polarization of LY12CZ in NaCl solution under various stresses is measured, and the polarization curves are shown in Fig.5. When the stress is applied, two breakdown potentials and free corrosion potential show removals to lower potential. In Fig.5 two sharp increasing zones of current density can be seen on the polarization curves at 720 mV and 620 mV respectively. The amounts of removal of both breakdown potentials depend on the stress, as shown in Fig.6. From Fig.6 we can get the rough relationship between the removal extent of potential and applied stress. When the stress level is low, the Δφ is nearly proportional to the stress, and the proportion is about 6 mV/100 MPa for φb1 and 3.5 mV/100 MPa for φb2 respectively. But when the stress exceeds around half the yield stress of LY12CZ, there seemed to be a sharper decrease rate of two breakdown potentials. When the stress reaches 235.2 MPa, the max variations of two breakdown potentials are around 20 mV and 12 mV respectively. The stress applied on LY12CZ enhances the chemical potential of alloys and destroys the integrity of the oxidation film on the matrix. The decreases of breakdown potential and stress concentration in the defect lead by applied stress can significantly affect the pitting and intergranular corrosion behaviour of LY12CZ.
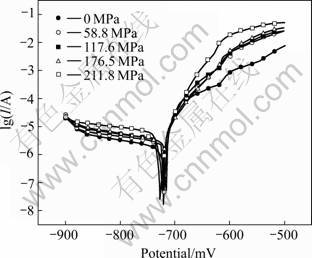
Fig.5 Polarization curves of LY12CZ under different stresses
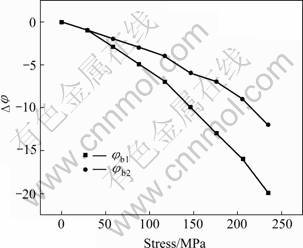
Fig.6 Variations of two breakdown potentials
3.3 Effect of stress on pitting corrosion and intergranular corrosion
To study the effect of stress on the pitting corrosion behaviour of LY12CZ, the potentiostatic tests at different potentials around two breakdown potentials (730, 710, 630 and 610 mV) under various stresses are performed. The I—t curves under various stresses are recorded, as shown in Fig.7. When the specimen is polarized to 730 mV without stress, the corrosion current remains at the order of 10-5A/cm2 (Fig.7, curve 0) and fluctuates between anodic and cathodic values. When the stress reaches 117.6 MPa, the holding potential (730 mV) is still lower than the first breakdown potential, and the current gets a rise to the order of 10-4A/cm2 (Fig.7, curve 1) in contrast to that with no stress, and the corrosion current is still fluctuant between anodic and cathodic values. Under such circumstances, no obvious pits are found on the surface on LY12CZ (Fig.8(a)). Only some light dissolution around the S phase particles is found (Fig.9). When the stress exceeds 117.6 MPa, the holding potential surpass φb1 and corrosion current starts to get an obvious rise. When stress reaches 235.2 MPa, the corrosion current has risen to around 3×10-3A/cm2 (Fig.7, curve 3), and obvious pits have initiated from the surface and developed quickly(Fig.8(c)). When the poitential keeps decreasing to 710 mV and 630 mV respectively (above φb1), the S phase particles start to dissolve under any stress. After immersion, some particles entirely dissolve or fall out, as shown in Fig.10. The pits develop quickly under the action of stress during the dissolution of S phase, and Mg dealloying from S phase is observed. EDS analysis shows that Mg selectively dissolves from S phase and leaves the Cu-rich remnant, as shown in Fig.11. Under the condition of equal time immersion, the stress can also affect the Mg dealloying (Fig.11). The greater the stress, the more severe the Mg dealloying is. Only after φb2 is reached can grain boundary be attacked and large pits will develop. Too great stress can break the oxidation film intergrity and prohibit the repassivation of the matrix. So under enough stress the grain boundaries can be attacked at much lower potential. The preferential dissolution of Cu-depleting zone along grain boundary happens and leads to intergranular corrosion.
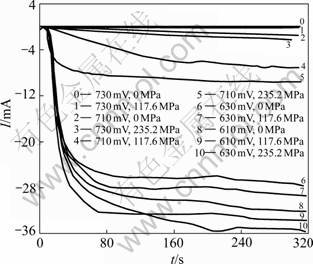
Fig.7 I—t curves under different stresses and holding potentials
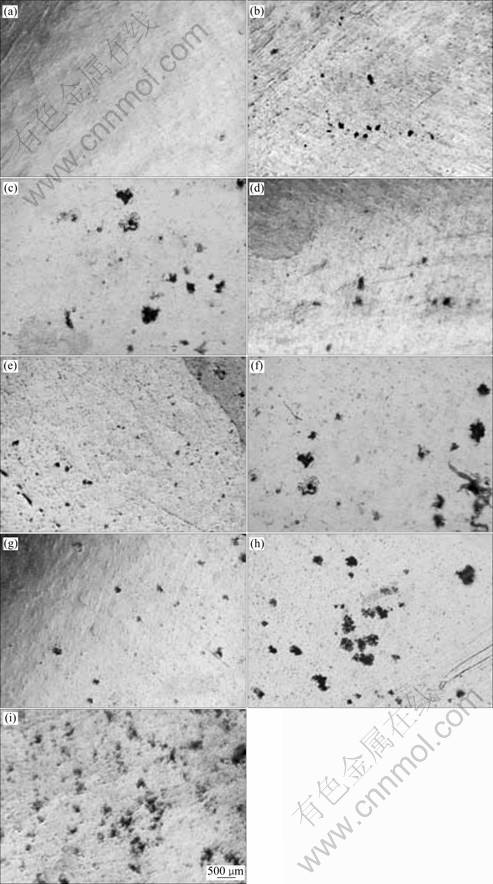
Fig.8 Surface topographies of LY12CZ after potentiostatic tests for 5 min immersion at different stresses and potentials: (a) 730 mV, 0 MPa; (b) 730 mV, 117.6 MPa; (c) 730 mV, 235.2 MPa; (d) 710 mV, 0 MPa; (e) 710 mV, 117.6 MPa; (f) 710 mV, 235.2 MPa; (g) 630 mV, 0 MPa; (h) 630 mV, 117.6 MPa; (i) 630 mV, 235.2 MPa
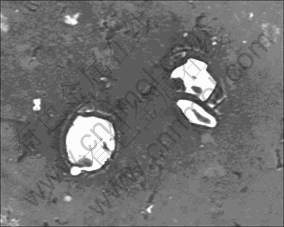
Fig.9 Al2CuMg particles after polarization to 730 mV without stress
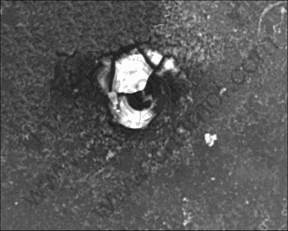
Fig.10 Al2CuMg particles dissolution after polarization to 710 mV without stress

Fig.11 Mass fraction of Mg after polarization
4 Conclusions
1) Electrochemical tests show that there are two breakdown potentials in LY12CZ. The first active one around 720 mV is related to the dissolution of S phase, and the second breakdown potential around 620 mV is related to the breakdown of the oxidation film and dissolution of the matrix. Both breakdown potentials show removals to lower potential when being stressed. The removal extent depends on the stress. At low stress zone, there is a rough linear relationship between Δφ and stress.
2) When S phase dissolves, the Mg de-alloying in S phase can be found. Under the same potential and immersion time the de-alloying extent is directly related to the amount of stress intensity. If the stress is big enough to destroy the integrity of the oxidation film and to prohibit the repassivation of the matrix, LY12CZ aluminum alloy will corrode at lower potential and show more severe pitting corrosion and intergranular corrosion sensitivity.
References
[1] GUTMAN E M. Mechanochemistry and Corrosion Prevention of Metals [M]. Beijing: Science Press, 1989.
[2] MAGNIN T. Advances in Corrosion-Deformation Interactions [M]. 1996.
[3] GUTMAN E M, SOLOVIOFF G. The Mechanochemical behavior of type 316L stainless steel [J]. Corro Sci, 1996, 38: 1141-1145.
[4] BONORA P L, ANDREI M, ELIEZER A, GUTMAN E M. Corrosion behaviour of stressed magnesium alloys [J]. Corro Sci, 2002, 44: 729-749.
[5] BEN-HAMU G, ELIEZER A, GUTMAN E M. Electrochemical behavior of magnesium alloys strained in buffer solutions [J]. Electrochimica Acta, 2006, 152: 304-313.
[6] BEN-HAMU G, ELIEZER A, GUTMAN E M, UNIGOVSKI Y, HADDAD J. Mechanoelectrochemical behavior of magnesium alloys [J]. Materials Science and Engineering A, 2006, A420: 109-114.
[7] IWANAGA H, OKI T. Effect of applied stress on anodic polarization behaviour and pitting corrosion of stainless steel [J]. Journal of the Society of Materials Science, Japan/Zairyo, 1981, 30: 394-400.
[8] KUWANO S, OKI T. Effect of applied stress on SCC susceptibility and polarization behavior of SUS316 type stainless steel [J]. Journal of the Society of Materials Science, Japan/Zairyo, 1982, 31: 828-833.
[9] LIU Xiao-dong, FRANKEL G S. Effects of compressive stress on localized corrosion in AA2024-T3 [J]. Corro Sci, 2006. (in Press)
[10] LIU Xiao-dong, FRANKEL G S. Effect of applied tensile stress on intergranular corrosion of AA2024-T3 [J]. Corro Sci, 2004, 46: 405-425.
[11] BLANC C, LAVELLE B, MANKOWSKI G. The role of precipitates enriched with copper on the susceptibility to pitting corrosion of the 2024 aluminium alloy [J]. Corro Sci, 1997, 39: 495-510.
[12] GUILLAUMIN V, MANKOWSKI G. Localized corrosion of 2024T351 aluminum alloy in chloride media [J]. Corrosion Science, 1999, 41: 421-438.
[13] ZHANG Wei-long, FRANKEL G S. Localized corrosion growth kinetics in AA2024 alloys [J]. Journal of the Electrochemical Society, 2002, 149: B510-519.
(Edited by HE Xue-feng)
Foundation item: Project(G1999065010) supported by National Basic Research Program of China
Corresponding author: RAO Si-xian; Tel: +86-10-82317108; E-mail: raosixian@mse.buaa.edu.cn