
Hot deformation behavior of medium carbon V-N microalloyed steel
XU Lei(许 磊)1, 2, WANG Cheng-yang(王承阳)2, LIU Guo-quan(刘国权)2, BAI Bing-zhe(白秉哲)1
1. Department of Materials Science and Engineering, Tsinghua University, Beijing 100084, China;
2. School of Materials Science and Engineering, University of Science and Technology Beijing, Beijing 100083, China
Received 10 August 2009; accepted 15 September 2009
Abstract: Processing maps for a medium carbon V-N microalloyed steel(designated as VN steel) and a medium carbon V-N bared steel(designated as Non-VN steel) were developed to study the hot deformation behavior and the influence of vanadium and nitrogen, in the temperature range of 750-1 100 ℃ and strain rate range of 0.005-30 s-1. Experimental results show that the processing map for the VN steel exhibits two dynamic recrystallization and three instability domains, while that for the Non-VN steel has one dynamic recrystallization and three instability domains. The instability domains of VN steel are larger than those of the Non-VN steel, and the VN steel is easier to be unstable when being hot deformed at high temperature and high stain rate. The addition and precipitation of vanadium and nitrogen can hinder the dynamic recrystallization. Compared with the Non-VN steel, the VN steel has higher dynamic recrystallization critical strain and the corresponding stress.
Key words: medium carbon V-N microalloyed steel; hot deformation; processing map; dynamic recrystallization
1 Introduction
Medium carbon vanadium microalloyed steels have been studied and used widely, such as application in oil, auto as well as engine. But compared with the quenched and tempered steels, they have the problem of mismatch between toughness and strength[1-4]. In order to solve this problem, Ti has been added and the amount of N has also been increased, which can enhance the properties of this kind of steel. But precipitation behavior of the alloying elements in the steel becomes more complex and the choice of hot deformation parameters is more difficult due to the mixed addition of titanium, vanadium and nitrogen.
Now, processing map invented by PRASAD et al[5] on the basis of dynamic material model has been successfully applied in more than 200 kinds of alloys[6], and has been proved to be effective for the study of hot deformation behavior of alloys. But few reports introduce its usage in medium carbon V-N microalloyed steel, especially the influence of vanadium and nitrogen on the hot deformation behavior of this kind of steel. In this work, processing maps of a medium carbon V-N microalloyed steel(designated as VN steel) and a medium carbon V-N bared steel(designated as Non-VN steel) were developed. Hot deformation behavior and the influence of vanadium and nitrogen on the behavior of these two kinds of steels were also investigated.
2 Experimental
The chemical composition of the steels used in the experiment can be seen in Table 1. The 40 kg ingot was preheated at 1 200 ℃, then forged in the temperature range of 1 100-1 000 ℃ and air cooled.
Table 1 Chemical compositions of experimental steels (mass fraction, %)

In order to obtain true stress―true strain curves, hot compression tests at constant true strain rate were carried out on a Gleeble 1500 thermal simulator, over a temperature range varying from 750 to 1 100 ℃ at 50 ℃ intervals and at different true strain rates ranging from 0.005 to 30 s-1. Cylindrical specimens of 8 mm in diameter and 20 mm in length were used. Prior to the hot compression, the specimens were austenitized at 1 200 ℃ for 10 min, and then cooled down to the compression temperature at an average rate of 6.7 ℃/s and thermally retarded for 30 s. The compressed specimens were water quenched to room temperature.
In order to observe the evolution of microstructure during compression tests, the compression-tested specimens were sectioned in parallel to the stress axis, and the samples were obtained for optical microscopy.
3 Rationale of processing map
On the basis of dynamic material model[7], the workpiece hot deformed is considered to be the only part of the total processing system to dissipate energy, and the instantaneous power P absorbed by the workpiece is dissipated through a temperature rise (G content) and a microstructural change (J co-content), shown as follows:
(1)
where σ is true stress and
is strain rate. The G and J are complementary functions, determined by strain rate sensitivity parameter(m) given by
(2)
For an ideal linear dissipator, m=1 and J=Jmax=
and (?J/?P)max=(?J/?P)line=1/2. Then, the efficiency of power dissipation(η) of a non-linear dissipater can be expressed as a dimensionless parameter[7-10]:
(3)
The variation of η with temperature and strain rate constitutes the processing map, which exhibits various domains that may be correlated with specific microstructural mechanisms.
The continuum instability criterion for identifying the domains of flow instabilities has been developed on the basis of the extremum principles of irreversible thermodynamics as applied to large plastic flow and given by another dimensionless parameter[11]:
(4)
The three-dimensional variation of the instability parameter as a function of temperature and strain rate represents an instability map. In this map, the temperature and strain rate regimes where ξ is negative represent microstructural instability. The processing map is constituted by the superimposition of power dissipation map and instability map.
4 Results and discussion
True strain and true stress data corresponding to different strain rates and deformation temperatures were obtained through hot compression tests. Fig.1 shows the true strain―true stress curves of the experimental steels corresponding to different strain rates at 800 ℃. It is indicated that the flow softening appears at higher strain rates and true strains. The flow stress increases with increase of strain rate at the same deforming temperature. At different strain rates, peak flow stress values appear with increasing the true strain, and the strain corresponding to the peak stress increases with increase of the strain rate, that is, raising strain rate can increase the dynamic recrystallization critical strain.
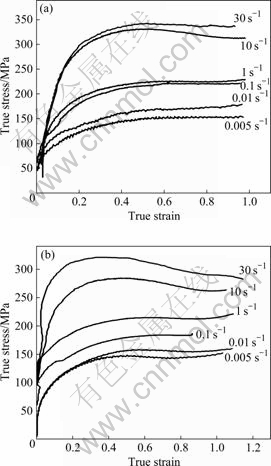
Fig.1 True strain―true stress curves of VN steel (a) and Non-VN steel (b) corresponding to different strain rates at 800 ℃
Fig.2 shows the true strain―true stress curves of the experimental steels at 850 ℃ and 30 s-1. Experimental results show that for the VN steel, the dynamic recrystallization critical strain is 0.59, and the corresponding critical stress is 314 MPa. Both of them are higher than those of the Non-VN steel, which indicates that the addition of vanadium and nitrogen can increase the critical strain and stress.
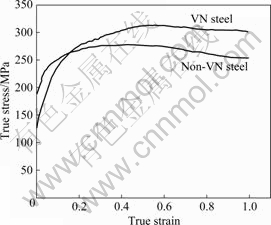
Fig.2 True strain―true stress curves of VN steel and Non-VN steel at 850 ℃ and 30 s-1
It can also be concluded that the flow softening characteristic of the Non-VN steel is more obvious than that of the VN steel, which indicates that the two steels have different hardening and softening factors. It is considered that the VN steel has high amount of nitrogen, which can enhance the precipitation of vanadium at austenite grain boundary and thus hinder the dynamic recrystallization.
According to the true strain and true stress data, processing maps of the experimental steels were developed. The contour numbers represent the power dissipation efficiency and the shaded regions exhibit the flow instability domains. Fig.3 shows the processing maps at strain of 0.9. It can be learned that there are two peak efficiency domains in the power dissipation map of the VN steel (see Fig.3(a)): domain peakⅠ(peak efficiency 31%, the temperature range 925-1 100 ℃ and the strain rate range 0.1-5.6 s-1), and domain peak Ⅱ (peak efficiency 24.5%, the temperature range 825-875 ℃ and the strain rate range 6-30 s-1). But there is only one peak efficiency domain in the power dissipation map of Non-VN steel, with a peak efficiency of 29% in the temperature range of 900-1 100 ℃ and the strain rate range of 0.08-1.6 s-1.
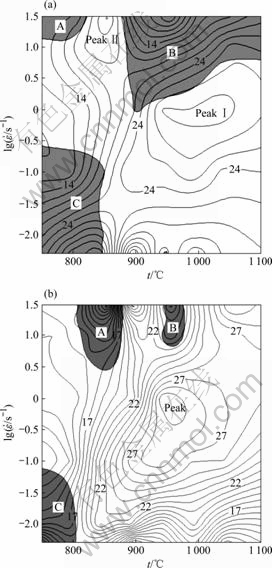
Fig.3 Processing maps for experimental steels: (a) VN steel; (b) Non-VN steel
Microstructure morphology was investigated to explain the peak efficiency domains of the experimental steel. Fig.4 shows the micrographs of the experimental steels, corresponding to the peak efficiency domains. It is revealed that the microstructures of the two steels have the similar characteristic. The austenite grains become equiaxed with homogeneous size. In addition, the grain boundary is wavy and the deformed microstructure has completely disappeared, which agrees with the dynamic recrystallized grain feature. Thus, the peak efficiency domains must correspond to full dynamic recrystallization of the two steels. By comparing the microstructure in domain peak Ⅰ with that in domain peak Ⅱ of the VN steel, it can be found it is easier to obtain finer microstructure at lower temperature and higher strain rate.
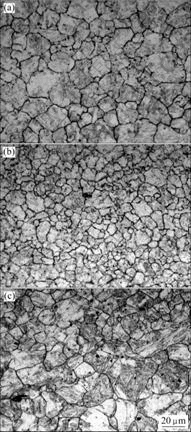
Fig.4 Micrographs of VN steel deformed at 1 000 ℃ and 1 s-1 (domain peakⅠ) (a), 850 ℃ and 30 s-1 (domain peak Ⅱ) (b), and Non-VN steel deformed at 950 ℃ and 1 s-1 (domain peak) (c)
Either of the processing maps for the experimental steels at strain of 0.9 has three instability regions, marked as shaded regions in Fig.3. For the VN steel, region A occurs at the temperature range of 750-825 ℃ and stain rate range of 12-30 s-1; region B occurs at 875-1 100 ℃ and 1-30 s-1; and region C occurs at 750-850 ℃ and 0.005-0.3 s-1. For the Non-VN steel, region A occurs at the temperature range of 810-880 ℃ and 3.2-30 s-1; region B occurs at 940-975 ℃ and 6.3-30 s-1; and region C occurs at 750-802 ℃ and 0.005-0.08 s-1.
The microstructure morphologies corresponding to these unstable regions are shown in Fig.5 and Fig.6. It is indicated that mixed grain structure is generated when the VN steel and Non-VN steel are deformed at 950 ℃ and 30 s-1, corresponding to region B of the two steels. And necklace type of structure with fine grains at the boundaries of elongated grains and the core showing no recrystallized grains is formed in the VN steel deformed at 800 ℃ and 0.1 s-1 or 750 ℃ and 30 s-1, corresponding to unstable regions A and C, respectively. The similar case occurs in the Non-VN steel deformed at 850 ℃ and 10 s-1 or 750 ℃ and 0.01 s-1, corresponding to regions A and C, respectively. It is inferred that the strength of the grain boundary is lower, resulting in deformation near the grain boundary preferring to that of the grain. Thus, huge amount of dislocation is generated, which induces the dynamic recrystallization near the boundary, and the formation of the necklace type of structure[12-15].
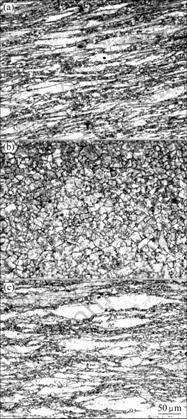
Fig.5 Microstructure morphologies of VN steel deformed at 750 ℃ and 30 s-1 (a), 950 ℃ and 30 s-1 (b), and 800 ℃ and 0.1 s-1 (c) corresponding to instability regions A, B and C, respectively (shaded regions in Fig. 3(a))
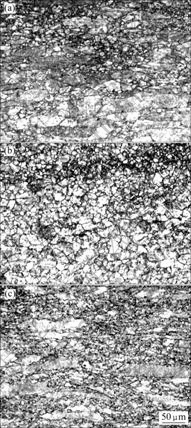
Fig.6 Microstructure morphologies of Non-VN steel deformed at 850 ℃ and 10 s-1 (a), 950 ℃ and 30 s-1 (b), and 750 ℃ and 0.01 s-1 (c) corresponding to instability regions A, B and C, respectively (shaded regions in Fig.3(b))
Experimental results show that the unstable regions in the processing map of VN steel are larger than those of the Non-VN steel; especially, unstable region B occurs at high temperature and strain rate with mixed grain structure. This indicates the addition of vanadium and nitrogen in the VN steel can lead to the precipitation of vanadium at grain boundaries at suitable temperature. But the vanadium precipitates can occupy not all but part of the grain boundaries, when the VN steel is deformed at high temperature and high strain rate. Therefore, the vanadium precipitates can only hinder dynamic recrystallization and regrowth of part of the austenite grains in the steel, and that is why large unstable region B appears in the processing map for the VN steel.
As discussed above, addition of vanadium and nitrogen can promote the properties of microalloyed steel through solid solution strengthening, precipitation strengthening and so on. Simultaneously, it also hinders the dynamic recrystallization and enlarges the unstable region. Consequently, unstable regions should be avoided and peak efficiency domains are optimum for choosing the parameters of hot deformation for the VN steel.
5 Conclusions
1) The processing map for the VN steel reveals two dynamic recrystallization domains in the following temperature and strain rate ranges: 925-1 100 ℃ and 0.1-5.6 s-1 with the peak efficiency of 31%; and 825-875 ℃ and 6-30 s-1 with the peak efficiency of 24.5%. It is also indicated that there are three unstable regions: region A and region C occur in the temperature range of 875-1 100 ℃ and strain rate range of 12-30 s-1, or in the temperature range of 750-850 ℃ and strain rate range of 0.005-0.3 s-1, with the generation of necklace type microstructure; region B occurs in the temperature range of 875-1 100 ℃ and strain rate range of 1-30 s-1, with the generation of mixed grain structure.
2) The processing map for the Non-VN steel reveals one dynamic recrystallization domain in the temperature range of 900-1 100 ℃ and strain rate range of 0.08-1.6 s-1 with the peak efficiency of 29%. But three unstable regions occur in the following temperature and strain rate ranges: region A and C occur in 810-880 ℃ and 3.2-30 s-1 or 750-802 ℃ and 0.005-0.08 s-1 with the generation of necklace type microstructure; region B occurs in 940-975 ℃ and 6.3-3.0 s-1 with the generation of mixed grain structure.
3) The unstable domains of the VN steel are larger than those of the Non-VN steel, and unstable deformation is easier to occur at the strain rate higher than 10 s-1.
4) Addition of vanadium and nitrogen can hinder the dynamic recrystallization. Compared with the Non-VN steel, the critical strain and stress for dynamic recrystallization in the VN steel are higher.
Acknowledgement
The authors wish to thank the Vanadium International Technical Committee for their financial support, and China Iron and Steel Research Institute Group for the smelting and supply of the experimental steels.
References
[1] CAPDEVILA C, ANDR?S C G D, CABALLERO F G. Incubation time of isothermally transformed allotriomorphic ferrite in medium carbon steels [J]. Scripta Mater, 2001, 44: 129-134.
[2] BYUN J S, SHIM J H, SUH J Y, OH Y J, CHO Y W, SHIM J D, LEE D N. Inoculated acicular ferrite microstructure and mechanical properties[J]. Mater Sci Eng A, 2001, 319/321: 326-331.
[3] MADARIAGA I, GUTI?RREZ I, ANDR?S C G D, CAPDEVILA C. Acicular ferrite formation in a medium carbon steel with a two stage continuous cooling [J]. Scripta Mater, 1999, 41: 229-235.
[4] CAPDEVILA C, CABALLERO F G, ANDR?S C G D. Isothermal allotriomorphic ferrite formation kinetics in a medium carbon vanadium-titanium microalloyed steel [J]. Scripta Mater, 2001, 44: 593-600.
[5] PRASAD Y V R K, GEGEL H L, DORAIVELU S M, MALAS J C, MORGAN J T, LARK K A, BARKER D R. Modeling of dynamic material behavior in hot deformation: forging of Ti-6242 [J]. Metall Trans A, 1984, 15: 1883-1892.
[6] PRASAD Y V R K, SASIDHARA S. Hot working guide: a compendium of processing maps [M]. Materials Park, Ohio: ASM International, 1997.
[7] PRASAD Y V R K, SRSHACHARYULU T. Modelling of hot deformation for microstructural control [J]. International Materials Reviews, 1998, 43(6): 243-258.
[8] PRASAD Y V R K. Processing maps: A status report [J]. Journal of Materials Engineering and Performance, 2003, 12(6): 638-645.
[9] SOMANI M C, MURALEEDARAN K, PRASAD Y V R K, SINGH V. Mechanical processing and microstructural control in hot working of hot isostatically pressed P/M IN-100 superalloy [J]. Mater Sci Eng A, 1998, 245: 88-99.
[10] PRASAD Y V R K. Author’s reply: Dynamic materials model: basis and principles[J]. Metall Mater Trans A, 1996, 27A: 235-236.
[11] PRASAD Y V R K. Recent advances in the science of mechanical processing [J]. Indian J Tech, 1990, 28: 435-451.
[12] PONGE D, GOTTSTENIN G. Necklace formation during dynamic recrystallization: Mechanisms and impact on flow behavior [J]. Acta Mater, 1998, 46(1): 69-80.
[13] WANG Ling-yun, FAN Yong-ge, HUANG Guang-jie, HUANG Guang-sheng. Flow stress and softening behavior of wrought magnesium alloy AZ31B at elevated temperature [J]. Trans Nonferrous Met Soc, 2003, 13(2): 335-338.
[14] WANG Ling-yan, HUANG Guang-sheng, FAN Yong-ge, HUANG Guang-jie. Grain refinement of wrought AZ31 magnesium alloy [J]. The Chinese Journal of Nonferrous Metals, 2003, 13(3): 594-598. (in Chinese)
[15] CAHN R W. Materials science and technology: Processing of metals and alloys [M]. LEI Ting-quan. Beijing: Science Press, 1999: 408-415. (in Chinese)
Foundation item: Project supported by Vanadium International Technical Committee(VANITEC)
Corresponding author: XU Lei; Tel: +86-10-62772976; E-mail: xulei_80@yahoo.cn
DOI: 10.1016/S1003-6326(09)60038-8
(Edited by YANG Bing)