
Properties of plasma sprayed NiCrAlY+ZrO2 coating on TiAl alloy surface
ZHOU Hai(周 海), CHEN Fei(陈 飞), L? Xiao-jing(吕晓静)
College of Mechanical Engineering, Beijing Institute of Petrochemical Technology, Beijing 102617, China
Received 15 July 2007; accepted 10 September 2007
Abstract: The NiCrAlY+ZrO2 thermal barrier coating was prepared on the surface of TiAl alloy by plasma spraying technique. The microstructure and phase structure were analyzed using scanning electron microscopy (SEM) and X-ray diffractometry (XRD). The high temperature oxidation resistance of the plasma sprayed samples at 850℃ was investigated. The results show that the bonding between thermal barrier coating and substrate is very good. Surface hardness of TiAl alloy is improved too. The microhardness of the coating surface is about HV 900 after the oxidation test at 850 ℃. The oxidation resistance of the samples is improved remarkably.
Key words: TiAl alloy; plasma spraying; NiCrAlY+ZrO2 thermal barrier coating; oxidation resistance
1 Introduction
Intermetallic compounds of TiAl are important materials for a wide variety of applications such as advanced automobile and aircraft engine components because of their low density, high melting temperature and good high temperature strength retention. However, one of the key problems in the practical use of these compounds is their poor high temperature oxidation resistance.
Thermal barrier coatings(TBCs) are widely used in the aerospace and automotive industries for increased operation temperature of important thermal components of systems such as the turbine engine and diesel engine in order to increase the efficiency, performance and durability of the engine[1-4].
ZrO2 coating is capable of high temperature resistance, heat insulation, oxidation resistance and anti-corrosion, so it becomes the most widely applied coating material. However, if it is directly sprayed on TiAl alloy basal body surface, the linear expansion coefficient of high temperature alloy is usually (18-20)×10-6/℃ and that of ZrO2 is (8-10)×10-6/℃ for a larger difference between thermal expansion coefficient of basal body and ZrO2 coating. Temperature variations make a high thermal stress in the coating, which can lead to breaking or stripping of coatings. Because coatings are difficult to ensure their quality under the higher temperature, MCrAlY coating, a heat resistant alloy coating, is selected as an intermediate coating. MCrAlY coating is to prevent basal body from oxidation and corrosion under a high temperature, realize the transition between thermal expansion factors of ceramic coating and basal body, and provide rough surfaces for the ceramic coating. Typical heat resistant alloys are CoCrAlY and NiCrAlY, of which micro-added Y can improve antistripping capacity of protective oxide coatings effectively. CoCrAlY has better heat and oxidation resistances than NiCrAlY, but the former has worse plasticity than the latter in ductile-brittle transition temperature of coating and minimum elongation in its brittle areas[5-11].
In this work, the NiCrAlY+ZrO2 thermal barrier coating was prepared on the surface of TiAl alloy by plasma spraying technique for improving the property of the oxidation resistance.
2 Experimental
TiAl alloy rods was cut into patterns of 10 mm×10 mm×1 mm with a wire cutting machine. Their surfaces were polished with sand paper before spraying coatings to remove oil spots and rust stains on them, and then a blast sanding treatment was made to form certain surface roughness convenient for cleaning with a ultrasonic washer and acetone. After drying the surfaces, patterns were fixed on a revolving table, and table was revolved to make it rotate at a speed of 180 r/s. The distance between each pattern and spray gun is 1 40 mm.
NiCrAlY powder was poured into a powder feeder, a plasma spraying device was started to let in an appropriate amount of argon gas and hydrogen, and increase mains current from 450 A to 530 A. After the plasma jet was created, NiCrAlY powder was melted through the spray gun muzzle, spayed onto pattern surfaces in colloidal state, and then formed coatings gradually. Synchronous feeding of argon gas and hydrogen is mainly used as protective atmosphere to reduce oxidations in course of forming coatings by the greatest extent and maintain their densities.
Procedures for spraying ZrO2 coatings are the same as those for spraying NiCrAlY powder coatings, but the distance between each pattern and spray gun is 120 mm.
3 Results and discussion
3.1 Microstructure and hardness distribution
Fig.1 shows the metallic phase microstructure of the pattern coating cross-section after plasma spraying, in which a row of black spot is impress produced by a microhardness tester. As shown in Fig.1, the entire coating consists of the outer ZrO2 thermal barrier coating (top coating) and intermediate NiCrAlY coating (bottom coating), in which the thickness of the top coating is about 100 μm, and the bottom coating is about 320 μm.
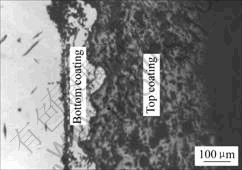
Fig.1 Microstructures of coating cross-section
Coating surface microhardness after plasma spraying is shown in Fig.2, and it increases remarkably. The hardness tends to decrease from surface to basal body, in which the surface hardness reaches up to HV 900, but that of basal body is only HV 300.
3.2 SEM micrograph of coating surface
Fig.3 shows SEM micrograph of pattern coating
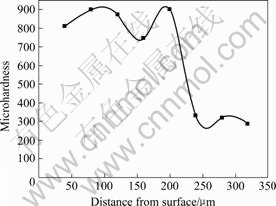
Fig.2 Microhardness of coating
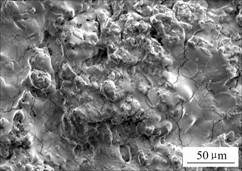
Fig.3 SEM micrograph of coating surface
surface, and ZrO2 coating is shown in the form of strip, joined and piled by molten particles in the form of strip or irregular particle, which has typical structure and basic features of plasma coating. Moreover, surface flattening area and particle enriching area exist in ZrO2 coating surface. Surface flattening area is formed by molten deformed ZrO2 particles, but more microcrack areas in plexiform exist in this area. Formation of microcracks is related to the shrinkage of molten particle size and process of coating cooling. Firstly, while spraying, settled particles in melding status shrink in the course of solidification and crystallization, which is hindered by settled parcels and basal bodies on cold conditions, so a tensile stress is produced inside the parcels; secondly, after spraying is completed, the high temperature coating begins to cool, and tensile stress is produced due to inconsistent volume shrinkages caused by different thermal expansion coefficients. When the stress exceeds the fracture strength of coating, microcracks will form in the coating.
3.3 Analysis of coating phase composition
Fig.4 shows XRD spectrum of patterns and their coating surfaces are mainly composed of ZrO2 and Ni3Al after plasma spraying.
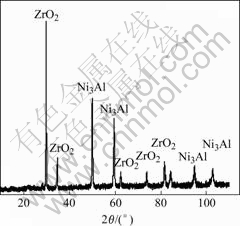
Fig.4 XRD patterns of coating
3.4 High temperature oxidation resistance of gradated coating
Fig.5 shows the oxidation kinetics curves of the gradated coating and original sample at 850 ℃. It is shown that after high temperature oxidation is started, mass gaining speed of the untreated original sample is very fast. Mass gain reaches 0.7 mg/cm2 after oxidation at 850 ℃ for 10 h, keeps on increasing with oxidation time, finally reaches 0.99 mg/cm2 after oxidation for 75 h, and maintains a rising trend. While for the spray-coated sample, in comparison with the untreated original sample, mass gaining speed is obviously slowed down. After oxidation for 75 h, mass gaining of the graduated coating is only 0.72 mg/cm2, and basically keeps unchanged during the period of 60-75 h. This indicates that high temperature oxidation resistance of the spray-coated sample is substantially improved. At earlier stage of the oxidation, the gradated coating is relative loose, and easy for oxygen molecules to enter. However, after certain time of oxidation, a uniform and dense oxidation film is formed on the surface of the coated sample to prevent it from being further oxidized.
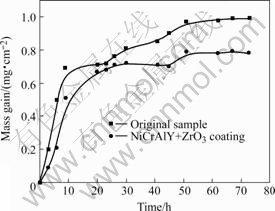
Fig.5 Oxidation kinetics curves of gradated coating and original sample at 850 ℃
4 Conclusions
1) The coating consists of NiCrAlY intermediate coating and ZrO2 ceramic heat barrier coating is prepared on the surface of refractory steel by plasma spraying technique.
2) The coating mainly consists of ZrO2 and Ni3Al. The microhardness of sprayed pattern surface is increased remarkably.
3) The dense oxidation film formed by the plasma sprayed gradated coating after high temperature oxidation can hinder infiltration of oxygen.
References
[1] BRINDLY W J, MILLER R A. Thermal barrier coating lige and thermal oxidation of low plasma-sprayed bond coat alloys[J]. Sur Coat Technol, 1990, 43: 446-457.
[2] MICHAELA Krauss. In-situ particle temperature, velocity and size measurements in the spray forming process[J]. Mate Sci Eng, 2002, 326:: 154-164.
[3] EVANS A G, HUTCHISON J W. On the mechanics of delamination and spalling in compressed films[J]. Int J Solids Structures, 1993, 74(2): 1321-1326.
[4] LELAIT L, ALPERIEN S, MEVREL R. Alumina scale growth at zirconia-MCrAlY interface: A microstructural study[J]. J Mater Sci, 1992, 27: 5-12.
[5] LUTHRA K L, BRAINT C L. Mechanism of adhesion of alumina on MCrAlY alloys[J]. Oxid Met, 1986, 26: 397-403.
[6] MARTIN F, CHRISTER P. Influence of particle in-flight characteristics on the microstructure of atmospheric plasma sprayed yttria stablized ZrO2[J]. Sur Coat Technol, 2001, 4: 115-127.
[7] MENDELSON M L. Graded thermal barrier coatings: evaluation[J]. Ceramic Engineering and Science Processing, 1994, 15(4): 555-562.
[8] KAWASAKI A, WATANABE R. Thermal fracture behavior of metal/ceramic functionally graded materials[J]. Engineering Fracture Mechanics, 2002, 69: 1713-1728.
[9] KHOR K A, Dong Z L. Plasma sprayed functionally graded thermal barrier coatings[J]. Materials Letters, 1999, 38(6): 437-444.
[10] WANG Ning, LU Chun-yan. Effect of NiCrAlY coatings on oxidation resistance of Ni-base superalloy K17[J]. Corrosion Science and Protection Technology, 2002, 14(1): 7-11. (in Chinese)
[11] CHEN Bing-yi. Thermal barrier coatings of speed development[J]. Engineering of Aviation Manufacture, 1994, 6: 25-26. (in Chinese)
(Edited by CHEN Can-hua)
Foundation item: Project(20061D0500500151) supported by Beijing Excellent Talent Nurture and Sponsor Project
Corresponding author: ZHOU Hai; Tel: +86-010-81292007; E-mail: zhouhai@bipt.edu.cn