J. Cent. South Univ. Technol. (2007)06-0768-05
DOI: 10.1007/s11771-007-0146-5

Effect of electrolysis superheat degree on anticorrosion performance of 5Cu/(10NiO-NiFe2O4) cermet inert anode
WANG Jia-wei(王家伟)1,2, LAI Yan-qing(赖延清)1, TIAN Zhong-liang(田忠良)1, LIU Ye-xiang(刘业翔)1
(1. School of Metallurgical Science and Engineering, Central South University, Changsha 410083, China;
2. College of Materials Science and Metallurgy Engineering, Guizhou University, Guiyang 550003, China)
Abstracts: 5Cu/(10NiO-NiFe2O4) cermet inert anodes were prepared by cold-pressing and sintering process, and the effect of superheat degree of melting K3AlF6-Na3AlF6-AlF3 on their anticorrosion performance was studied under electrolysis conditions. The results show that, the fluctuation of cell becomes small with increasing of superheat degree, which is helpful to inhibit the formation of cathodic encrustation; the concentration of impurities from inert anode in bath goes up to certain degree, but it is far smaller than those in traditional high-temperature bath. Increasing the superheat degree of melting K3AlF6-Na3AlF6-AlF3 has unconspicuous effect on the contents of impurities in cathodic aluminum. The total mass fractions of Fe, Ni and Cu in aluminum are 15.38% and 15.09% respectively under superheat degree of 95 and 195 ℃. From micro-topography of anode used view, increasing the superheat degree can aggravate corrosion of metal Cu in inert anode, and has negative influence on electrical conductivity of electrode to some extent.
Key words: cermets; inert anode; aluminum electrolysis; electrolysis corrosion; superheat degree
1 Introduction
Since Hall-Héroult process for the industrial production of aluminum was born[1], despite obtaining much progress, there were still many shortcomings such as great energy consumption, serious environmental pollution and unstable production as well. Inert electrodes and their electrolysis techniques, which could solve these problems, attracted many people’s eyes and became research hotspots.
After many years’ study[2-4], the materials of inert anode for aluminum electrolysis were focused on alloy[5] and cermet[6-7]. Among them, NiFe2O4 based cermet is regarded as one of the potential materials because it has good electrical conductivity and ability to resist corrosion[7-8]. But the anticorrosion performance of NiFe2O4 based cermet still could not meet the requirement of inert anode for aluminum electrolysis. Therefore, in order to decrease corrosion rate of inert anode under electrolytic conditions, researchers set about from meliorating applied conditions and improving itself performance.
In recent years, low-temperature electrolysis has been paid much attention because it could provide friendly work condition and decrease corrosion rate of inert anodes[9-12]. Front-stage study on corrosive behavior of 5Cu/(10NiO-NiFe2O4) cermet at KF or K3AlF6 melting states has shown that cermet inert anode exhibits better anticorrosion performance at low- temperature than at traditional high-temperature[13]. However, low- temperature electrolysis has many disadvantages, mainly including unstable cell voltage, cathodic encrustation and alumina sedimentation at the cell bottom. Researchers believed that enhancing superheat degree can solve these problems[10-11].
In this paper, 5Cu/(10NiO-NiFe2O4) cermet inert anodes were prepared by cold-pressing and sintering process based on our previous work, and their electrolytic corrosion behavior in K3AlF6-Na3AlF6-AlF3 melts at various superheat degrees was studied. The effect of superheat degree on cell voltages, the contents of impurities in bath and cathodic aluminum, and the microstructure of inert anode were investigated.
2 Experimental
2.1 Preparation of cermet inert anode
Cu powder, NiO powder and Fe2O3 powder were all of reagent grade. NiFe2O4 based cermet inert anodes were prepared by cold-pressing and sintering process[14-16]. A proper amount of NiO and Fe2O3 was mixed using a ball milling and then calcined to obtain 10NiO-NiFe2O4 ceramic powder. The ceramic powder obtained was mixed with Cu powder by ball milling and dried again, and then pressed into some cylindrical green samples(d20 mm×40 mm). Finally,5Cu/(10NiO- NiFe2O4) cermet inert anodes were obtained by degreasing and sintering green samples under manipulative atmosphere, and their relative density are all 96.7% and electrical conductivity are listed in Table 1.
Table 1 Electrical conductivities of 5Cu/(10NiO-NiFe2O4) anodes

2.2 Electrolysis corrosion tests
The electrolyte was made up of reagent grade Al2O3, Na3AlF6 and K3AlF6 and technical grade AlF3, the molar ratio of K3AlF6 to Na3AlF6 was 1:1, CR([n(NaF)+ n(KF)]/ n(AlF3)) was 1.5, mass fraction of Al2O3 was 5%, they were dried for 10 h at 120 ℃ before test. The bath melting point was 605 ℃ by measuring. Electrolysis temperatures were 700 and 800 ℃ respectively, and electrolysis testing was lasted for 20 h.
Sketch of electrolysis test is shown in Fig.1. Simulative cell was a graphite crucible with corundum inner lining, there was a hole(d47 mm) at the bottom of graphite crucible to keep steady cathodic aluminum surface and a certain ratio of anode area to cathode area. Before testing, anode was suspended above melt and heated to electrolysis temperature with furnace. When the electrolyte melted adequately after retaining temperature for a while, inert anode was immersed into the bath(the depth was 2 cm), and electrolysis testing started after 15 min. During testing, bath with the original composition was added according to the change of bath level, and alumina was added once per hour based on current efficiency(85%). After testing, the anode was upgraded to leave melt, and cooled with furnace naturally.
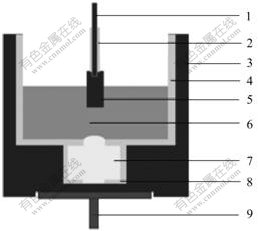
Fig.1 Sketch of electrolysis test
1-Stainless steel anode rod; 2-Corundum sleeve; 3-Graphite crucible; 4,8-Corundum crucible; 5-Inert anode; 6-Electrolyte; 7-Anode aluminum; 9-Stainless steel cathode rod
The contents of Fe, Ni and Cu in bath samples during testing and those in cathodic aluminum were analyzed by X-ray fluorescence analysis (PW2424, Philips), the microstructure of used anode was analyzed with electron microscope (XJP-6A, Reichert-POLYVAR MET), and the phases in bath were also analyzed with X-ray diffraction.
3 Results and discussion
3.1 Effect of electrolysis superheat degree on cell voltages
Fig.2 shows cell voltages as a function of time at various electrolysis superheat degrees. From Fig.2, it can be seen that with increasing of superheat degree, fluctuation of cell voltage becomes small. When the superheat degree is 95 ℃, in the first 5 h, cell voltages are between 5.96 and 19.60 V, their average value is 8.87 V, during 5-20 h, they stay at about 15 V. When the superheat degree is 195 ℃, cell voltages fluctuate from 4.27 to 9.62 V, and their average value is 5.17 V. The cell voltages are high but reposeful in the later stage when the superheat degree is 95 ℃. The reason for this is the formation of cathodic encrustation, which is in good agreement with the fact that bath level decreases obviously in the same time(considering the effect of bath volatilization). The cell voltages change within a small, range when the superheat degree is 195 ℃, but the cathodic encrustation still exists after cell being split only there is less effect on cell running. The reasons for this are that, melting points of bath change violently with the variation of bath compositions during low temperature phase, as a result, cathodic encrustation emerges easily, quantity of heat could not offset the melt cathodic encrustation under low superheat degree, but it
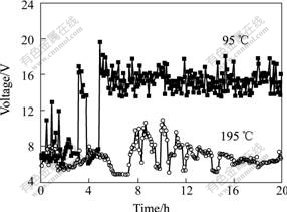
Fig.2 Cell voltages as function of time
could be partially under high superheat degree. Therefore, the quantity of cathodic encrustation under low superheat degree is far more than that under high superheat degree, and the fluctuation of cell voltages in the former is more serious than that of the latter. Cells were split after test, and the cathodic encrustation was taken out and analyzed with XRD. The results are shown in Fig.3.
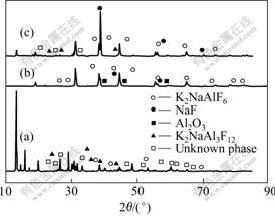
Fig.3 XRD patterns of cathodic encrustation from various baths
(a) Basal bath; (b) Cathodic encrustation at superheat degree of 95 ℃; (c) Cathodic encrustation at superheat degree of 195 ℃
From Fig.3, there are differences between basal bath and cathodic encrustations(under different superheat degrees). There are K2NaAlF6, K2NaAl3F12 and unknown phase in basal bath, K2NaAlF6, NaF and Al2O3 in cathodic encrustation obtained under superheat degree of 95 ℃, and K2NaAlF6, K2NaAl3F12, NaF and unknown phase in cathodic encrustation obtained under superheat degree of 195 ℃. It is found that with the increasing of superheat degree, the phases in cathodic encrustation are more similar to those in basal bath. The main difference between cathodic encrustation and basal bath is NaF, this is because there is little amount of Al3+ and large amount of Na+ on the bath/cathodic aluminum surface. At the same time, there is not Al2O3 in the cathodic encrustation obtained under superheat degree of 195 ℃. The reason for this is that solubility of alumina is improved with increasing the electrolysis temperature.
In a word, with augmenting of electrolysis superheat degree the fluctuation of cell voltages decelerates gradually, cell runs smoothly, and the phases in bath near cathode(cathodic encrustation) match those in basal bath to a great extent. So, increasing superheat degree has an inhibitory effect on the formation of cathodic encrustation.
3.2 Variation of mass fractions of impurities in bath
Fig.4 shows the mass fraction of Fe, Ni, Cu and their total as functions of time during electrolysis. Results illustrate that the change trends of mass fraction of impurities as the function of time are consistent under different electrolytic superheat degrees. At the beginning of about 2 h, there is a sharp rise of mass fraction of impurities, due to the enrichment of impurities. In subsequent 4-6 h the mass fraction of impurities decreases rapidly, the cause is that impurities begin to move from bath to cathodic aluminum. The detail reasons have been discussed [13]. And then Ni can keep dynamic balance within a short time, but Cu and Fe can not because the ratio of the transition rates of Fe, Cu and Ni from anode to bath to those from bath to liquid aluminum are 140, 274 and 60, respectively[17].
With increasing of superheat degree, there is an ascendant tendency of the mass fraction of impurities in bath. For example, at the moment of 4 h under the superheat degrees of 95 ℃ and 195 ℃, the mass fractions of Fe are 56.5×0-6 and 95.2×10-6, Cu 24.4×10-6 and 34.3×10-6, and Ni 38.2×10-6 and 40×10-6 , respectively. At the moment of 12 h, the mass fraction of Fe is 51.6×10-6 and 70.7×10-6, Cu 19.9×10-6 and 23.6×10-6, respectively. The reason is that high electrolysis temperature accelerates the transmission of ions.
It is also found that the mass fractions of impurities(Fe, Ni, Cu or the total of three) at the electrolysis temperature of 800 ℃(superheat degree is 195 ℃) are far lower than those in traditional sodium cryolite system(950 ℃) [13], the total of three impurities is 112.3×10-6 after testing at 800 ℃for 20 h, and that is 511×10-6 using same composition anode in traditional sodium cryolite system(CR=2.3, w(Al2O3)=5%).
In conclusion, decreasing electrolysis temperature is helpful to increase the anticorrosion performance of inert anodes in view of the mass fraction of impurities in bath.
3.3 Variation of mass fraction of impurities in cathodic aluminum
Table 2 shows the changes of mass fractions of Fe, Ni and Cu in cathodic aluminum before and after test. From it, it can be seen that when the superheat degree increases from 95 to 195 ℃, total of impurities decreases from 1 538.25×10-6 and 1 509×10-6, respectively. At the same time, as far as the changes of mass fractions of three impurities in cathodic aluminum before and after test are concerned, mass fraction of Fe changes remarkably, Ni and Cu can be neglected. For example, at 700 ℃, the changes of mass fractions of Fe, Ni and Cu are 129.5×10-6, 2×10-6 and 1.25×10-6, respectively. The cause is that among the transmitting rates from bath to liquid aluminum, the transmitting rate of Fe is larger than those of Ni and Cu[17].
Table 2 also shows that mass fraction of impurities in aluminum has a negative growth trend but Cu under the superheat degree of 195 ℃, the same phenomenon also was found during low-temperature electrolysis in potassium cryolite system[13]. It has not been reported while testing in traditional sodium cryolite system. It is found that impurities centralize in the bath/liquid aluminum surface(cathodic encrustation), the bath in this region is gray and darker in color than basal bath, the mass fraction of impurities in this region is higher apparently than that of basal bath. For instance, when superheat degree is 95 ℃, the mass fractions of Fe, Ni and Cu in basal bath are 46.77×10-6, 36.74×10-6 and 19.85×10-6, while in cathodic encrustation those are 208.52×10-6, 51.85×10-6 and 27.86×10-6. The reasonable explanation needs to be proved by further study.
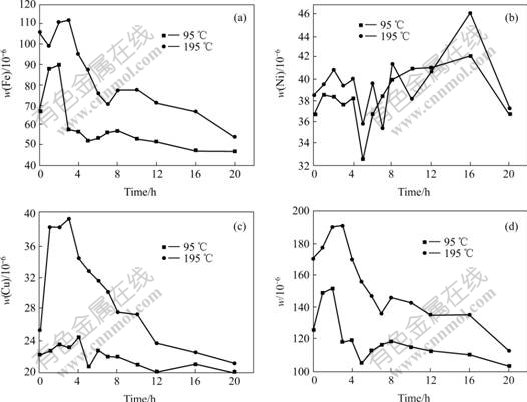
Fig.4 Mass fractions of impurities in electrolytes as function of time during electrolysis at different superheat degree
(a) Fe; (b) Ni; (c) Cu; (d) Total
Table 2 Mass fraction of impurities in aluminum after electrolysis at different temperatures w/10-6

In short, to low-temperature electrolyte, the increasing of superheat degree has little effect on impurities in aluminum, and the mass fractions of impurities in aluminum after low-temperature electrolysis are much lower than those of traditional high-temperature electrolysis. After testing for 20 h, mass fractions of impurities in aluminum are 1 538× 10-6, 1 509×10-6 and 2 549.3×10-6 under superheat degree 95 and 195 ℃ and traditional bath(950 ℃).
3.4 Variation of anode microstructure
From the microstructure(Fig.5), increasing superheat degree has slight effect on anticorrosion performance of basal material. When superheat degree is 95 ℃, the preferential corrosion of Cu(the highest contrast) on the surface layer is slight, while the corrosion degree is exacerbated when the superheat degree is 195 ℃, metal phase about 200 μm thick from anode surface was corroded. This is because with increasing electrolysis temperature, the multiform corrosion of metal Cu from anode is augmented. It is also found that these results differ from those in Refs.[13-14]. WANG et al[13] and LI[14] believed that anode was corroded at stoichiometric ratio and peeled off layer by layer. That is to say, Cu is corroded in company with ceramic body. While in this work there exists preferential corrosion of Cu. By comparative analysis, the electrolyte was Na3AlF6 based, but electrolyte of this work was K3AlF6-Na3AlF6-AlF3 system, different experimental conditions lead to various corrosion mechanisms of anode.
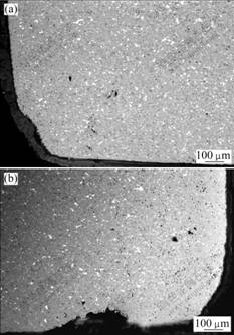
Fig. 5 SEM images of anodes at different superheat degrees
(a) 95 ℃; (b) 195 ℃
4 Conclusions
1) With increasing of superheat degree the fluctuation of cell voltage becomes weak and it is helpful to inhibit the formation of cathodic encrustation, but the mass fraction of impurities from inert anode in bath goes up. When superheat degree increases from 95 and 195 ℃ at 4 h, the mass fraction of Fe is from 56.5×10-6 to 95.2×10-6, that of Cu from 24.4×10-6 to 34.3×10-6 and that of Ni from 38.2×10-6 to 40×10-6, which are far smaller than those in traditional high-temperature bath. So it might contribute to increasing anticorrosion performance of cermet inert anode.
2) Increasing the superheat degree of melting K3AlF6-Na3AlF6-AlF3 has little effect on the mass fractions of impurities in cathodic aluminum, and the impurities excessively enrich near cathodic bath layer. The total mass fractions of Fe, Ni and Cu in aluminum are 1 538×10-6 and 1 509×10-6 under superheat degree 95 and 195 ℃, which are less than those in initial aluminum.
3) Increasing the superheat degree aggravates corrosion of metal Cu in inert anode, and maybe has negative influence on electrical conductivity of electrode to some extent.
References
[1] GRJOTHEIM K, KROHN C, MALINOVSKY M, et al. Aluminium Electrolysis[M]. Dusseldorf: Aluminium-Verlag, 1982.
[2] KENIRY J. The economics of inert anodes and wettable cathodes for aluminum reducation cells[J]. JOM, 2001, 53(5), 43-37.
[3] de NORA V. Aluminium electrowinning-The future[J]. Aluminium, 2000, 76(12): 998-999.
[4] KVANDEK H. Inert electrodes in aluminium electrolysis cells[C]// ECKERT C E. Light Metals 1999. California: TMS, 1999: 369-376.
[5] HRYN J N, SADOWAY D R. Cell testing of metal anodes for the aluminium electrolysis[C]// DAS S K. Light Metals 1993. Colorado: TMS, 1993: 475-483.
[6] YANG Jian-hong, LIU Ye-xiang, WANG Hua-zhang. The behaviour and improvement of SnO2-based inert anodes in aluminium electrolysis[C]// DAS S K. Light Metals 1993. Colorado: TMS, 1993: 493-495.
[7] OLSEN E, ThONSTAD J. Nickel ferrite as inert anodes in aluminium electrolysis: part Ⅰ. Material fabrication and preliminary testing[J]. Journal of Applied Electrochemistry, 1999, 29: 293-299.
[8] LAI Yan-qing, TIAN Zhong-liang, QIN Qing-wei, et al. Solubility of complex oxide ceramic in Na3AlF6-Al2O3 melt[J]. Journal of Central South University: Nature Science, 2003, 34(3): 245-248. (in Chinese)
[9] THONSTAD J, SOLHEIM A. The use of strongly acid low melting bath in aluminium electrolysis[J]. Aluminium, 1986, 62(12): 938-941.
[10] SLEPPY W C, COCHRAN C N. Bench scale electrolysis of aluminium in sodium fluoride–aluminium fluride melts below 900 ℃[C]// WARREN S, PETERSON. Light Metals 1979. Louisiana: TMS, 1979: 385-395.
[11] GRJOTHEIM K, KVAND H. Physico-chemical properties of low-melting baths in aluminium electrolysis[J]. Metall, 1985, 39(6): 510-512.
[12] BROWN C W. Laboratory experiments with low-temperature slurry-electrolyte alumina reduction cells[C]// PETERSON R D. Light Metals 2000. Tennessee: TMS, 2000: 391-395.
[13] WANG Jia-wei, LAI Yan-qing, TIAN Zhong-liang, et al. Investigation of 5Cu-(10NiO-NiFe2O4) inert anode corrosion during low-temperature aluminum electrolysis[C]// SORLIE M. Light Metals 2007. Florida: TMS, 2007: 525-530.
[14] LI Xi-zheng. Study on the sintering properties, electrical conductivity and corrosion resistance of XM/(10NiO-NiFe2O4) cermet[D]. Changsha: Central South University, 2006. (in Chinese)
[15] TIAN Zhong-liang, LAI Yan-qing, ZHANG Gang, et al. Preparation of NiFe2O4-Cu based cermet inert anodes in aluminium electrolysis[J]. The Chinese Journal of Nonferrous Metals, 2003, 13(6): 1540-1545. (in Chinese)
[16] ZHANG Gang, LAI Yan-qing, TIAN Zhong-liang, et al. Preparation of nickel ferrite based cermets for aluminum electrolysis[J]. Journal of Material Science and Engineering, 2003, 21(4): 44-47. (in Chinese)
[17] PIETRZYK S, OBLAKOWSKI R. Investigation of the concentration of the inert anodes in the bath and metal during aluminum electrolysis[C]// ECKERT C E. Light Metals 1999. California: TMS, 1999: 407-411.
(Edited by YANG Hua)
Foundation item: Project (2005CB623703) supported by the Major State Basic Research and Development Program of China
Received date: 2007-06-05; Accepted date: 2007-08-10
Corresponding author: WANG Jia-wei, Doctoral candidate; Tel: +86-731-8876454; E-mail: mm.jwwang@gzu.edu.cn