Effect of Al addition on properties of TiNiFe shape memory alloys
XIAO Li(肖 莉), LIU Fu-shun(刘福顺), XU Hui-bin(徐惠彬)
School of Materials Science and Engineering, Beijing University of Aeronautics and Astronautics,
Beijing 100083, China
Received 20 April 2006; accepted 30 June 2006
Abstract: A little amount of aluminum substituting for Ni was added to Ti50Ni48Fe2 and Ti50Ni47.5Fe2.5 alloys to improve the mechanical properties, especially the yield stress of the TiNiFe alloys. The martensitic transformation temperature and mechanical properties of Ti50Ni48-xFe2Alx and Ti50Ni47.5-xFe2.5Alx (x=0, 0.5, 1) alloys were examined, and it was revealed that 0.5% and 1%(mole fraction) aluminum addition lead to about 10℃ and 60-80 ℃ martensitic transformation temperature (MS) decrease, respectively. 1%(mole fraction) aluminum addition enhances remarkably the yield stresses of Ti50Ni47Fe2Al1 and Ti50Ni46.5Fe2.5Al1 to 560 and 580 MPa, respectively. The systemic microstructure analysis indicates that the second phase Ti2Ni at the grain boundaries plays an important role in improving the mechanical properties of TiNiFe shape memory alloys.
Key words: shape memory alloy; yield strength; martensitic transformation temperature
1 Introduction
NiTi-based shape memory alloys combine good functional and structural properties, such as high strength, corrosion resistance, long fatigue life, stable configuration and elevated temperature stability[1-4]. Compared with Cu-based and Fe-based shape memory alloys, near-equiatomic TiNi alloys are the most important shape memory alloys (SMA) because of their superior shape memory effect (SME) and pseudoelasticity(PE). Up to now, NiTi based SMAs are applied in various fields as functional materials[5-7]. Extensive research was conducted on the transformation behaviors and mechanical properties of TiNi alloys. It was recognized that TiNi SMAs’ properties and transformation temperatures vary dramatically with their composition[8] as well as their thermal or mechanical experiences, such as rolling[9], aging[10] and thermal treatment[11]. During the past years, a great deal of attentions were paid to improve NiTi shape memory properties and mechanical properties by addition of ternary elements. TiNiFe[12-15] and TiNiNb[16] are the most popular ternary alloys applied for coupling or sealing, when an operating temperature is range from –50 ℃ to about 100 ℃. TiNiNb alloys with wide hysteresis are developed to avoid storing and installing at cryogenic temperature after deformation in the martensitic state
. However, the occurrence of strain-induced martensite in TiNiNb alloys could lead to softening of coupling at aircraft working ambient temperature. Since the cryogenic transformation temperature of TiNiFe alloys could be obtained and controlled readily by Fe additive, they became the first choice of pipefitting in aeroplane pipe couplings[15]. In this paper, the effects of aluminum added into TiNiFe alloys on the phase transformation temperature, the mechanical properties and microstructure were systemically discussed.
2 Experimental
Ti50Ni48-xFe2 and Ti50Ni47.5-xFe2.5 (x=0, 0.5, 1) alloys were melted six times in a high frequency induction vacuum furnace with levitation melting technique. The ingots were homogenized in a vacuum furnace at 850 ℃ for 24 h, and then hot-worked into approximately 1.5 mm thickness sheets followed by annealing at 450 ℃ for 30 min. The specimens for tensile tests were spark-cut with a gauge dimension of 30 mm×2 mm×1.5 mm. Tensile tests were performed using a MTS (model 880) at ambient temperature. Electrical resistance samples were spark-cut to be 15 mm×1 mm×1 mm. Phase transformation temperatures were determined by electrical resistivity measurement through heating and cooling the specimens between liquid nitrogen or helium temperature and 50℃. TEM samples were electro-polished in an electrolyte with 75% methanol and 25%(volume fraction) nitric acid at –15 ℃ and 12 V. TEM work was carried out on JEOL-2000 EX-II transmission electron microscopy.
3 Results and discussion
3.1 Phase transformation behavior
Fig.1(a) and (b) show the phase transformation temperatures of Ti50Ni48-xFe2Alx and Ti50Ni47.5-xFe2.5Alx (x=0, 0.5, 1) alloys between liquid nitrogen temperature and 50 ℃, where the top line corresponds to cooling process and bottom line represents heating one. From Fig.1(a) and (b), the R-phase and martensitic transformation temperatures (marked with a steep increase or decrease in resistance) of Ti50Ni48-xFe2Alx and Ti50Ni47.5-xFe2.5Alx (x=0, 0.5) alloys are decided, but it is difficult to obtain exact those of Ti50Ni47Fe2Al1 and Ti50Ni46.5Fe2.5Al1 alloys, because the temperature of the latter two alloys are near to liquid nitrogen temperature. The electrical resistivity vs temperature curves of Ti50Ni47Fe2Al1 and Ti50Ni46.5Fe2.5Al1 alloys with temperature between liquid helium temperature and 25 ℃ are tested to confirm the transformation temperature, as shown in Fig.1(c).
On cooling, the martensitic transformation start temperatures of Ti50Ni48Fe2 and Ti50Ni47.5Fe2Al0.5 and Ti50Ni47Fe2Al1 alloys are -88, -94 and -171 ℃, and those of Ti50Ni47.5Fe2.5, Ti50Ni47-Fe2.5Al0.5 and Ti50Ni46.5Fe2.5Al1 alloys are -118, -130 and -176 ℃, respectively. Relative to Ti50Ni48Fe2 and Ti50Ni47.5Fe2.5 alloys, the MS temperature decreases about 10 ℃ observed with 0.5% Al(mole fraction) addition, while at about 60-80 ℃ decreases with 1% Al additive. On heating, the reverse martensitic transformations begin at temperature As and finish at temperature Af. It can be seen that the martensitic transformations of alloys without and with 0.5% Al(mole fraction) exhibit a large temperature hysteresis, while almost no temperature hysteresis is found in the Ti50Ni47Fe2Al1 and Ti50Ni46.5Fe2.5Al1 alloys as demonstrated in Fig.1(c). Furthermore, the resistance-temperature curves of Ti50Ni47Fe2Al1 and Ti50Ni46.5Fe2.5Al1 specimens are not similar to those of other four alloys, which go with an abrupt resistance increasing at Rs and stop decreasing at Ms temperature. The reason for these phenomena needs a further investigation.
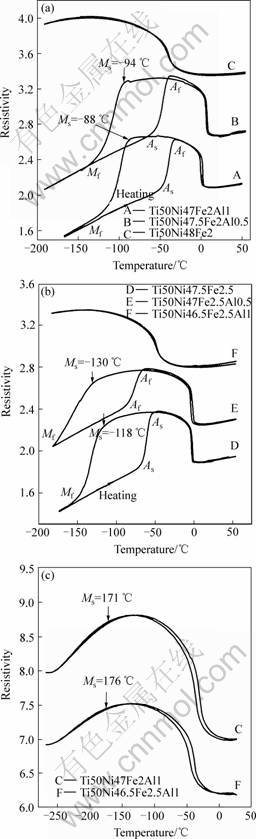
Fig.1 Electrical resistivity vs temperature curves between liquid nitrogen temperature and 50 ℃for Ti50Ni48-xFe2Alx(a), Ti50Ni47.5-xFe2.5Alx alloys(b) (x=0, 0.5, 1) and between liquid helium temperature and 25 ℃ for Ti50Ni47Fe2Al1 and Ti50Ni46.5Fe2.5Al1 alloys(c)
3.2 Mechanical properties
Stress-strain curves obtained from a MTS model 880 at room temperature are shown in Fig.2. From Fig.2, adding 0.5% Al(mole fraction) substituting Ni in Ti50Ni48Fe2 and Ti50Ni47.5Fe2.5 alloys almost does not change the yield strength of these alloys, but alloy ductility decreases a little. 0.2% yield stress peaks of Ti50Ni48Fe2 and Ti50Ni47.5Fe2Al0.5 alloys are 330 and 342 MPa, and those of Ti50Ni47.5Fe2.5and Ti50Ni47Fe2.5Al0.5 alloys are 336 and 345 MPa, respectively. Fracture strengths of Ti50Ni48Fe2 and Ti50Ni47.5Fe2Al0.5 alloys are both 680 MPa, and those of Ti50Ni47.5Fe2.5and Ti50Ni47Fe2.5Al0.5 are 655 and 688 MPa, respectively. However, with increase of Al content to 1.0%, the 0.2% yield strengths of Ti50Ni47Fe2Al1 and Ti50Ni46.5Fe2.5Al1 alloys increase dramatically to 561 MPa and 585 MPa, respectively, and associated fracture strengths are enha-
nced to 878 and 940 MPa, respectively. As a result, the total fracture elongations of alloys decrease to 11% and 12%, respectively. The mechanical properties of TiNiFe alloys with different Al content are shown in Fig.3. Because
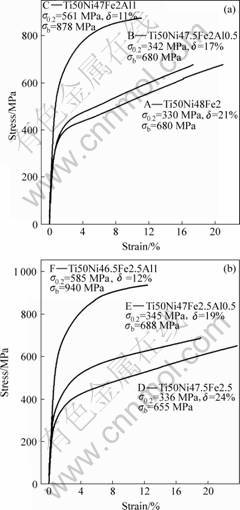
Fig.2 Stress—strain curves of Ti50Ni48-xFe2Alx(a) and Ti50Ni47.5-xFe2.5Alx (x=0, 0.5, 1.0) (b) alloys tested at room temperature
aluminum melting point is 933 K, which is far lower than points of titanium, nickel and iron, it is very easy to be volatilized during the melting process. The true aluminum contents of Ti50Ni47.5Fe2Al0.5 and Ti50Ni47Fe2.5Al0.5 alloys are likely much lower than nominal composition 0.5%(mole fraction), so a little amount solution strengthening and martensitic transformation temperature change (as discussed in section of phase transformation behavior) contributed to Al solution into TiNi matrix are obtained. When the aluminum content increases to 1%(mole fraction), the solution strengthening is one of the main reasons for the high yield strength and low fracture elongation strain.
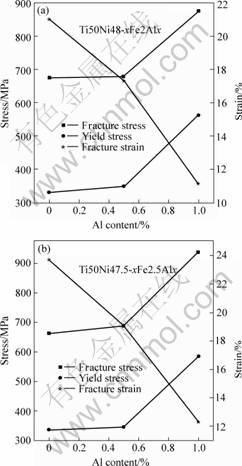
Fig.3 Mechanical properties of Ti50Ni48-xFe2Alx(a) and Ti50Ni47.5-xFe2.5Alx (x=0, 0.5, 1.0) (b) alloys with different Al contents
3.3 Microstructure analysis
In order to investigate the strengthening mechanism of alloys with different Al contents, the microstructures of Ti50Ni46.5Fe2.5Al1 alloy were studied. The SEM image of Ti50Ni46.5Fe2.5Al1 alloys is shown in Fig.4. It is found that there is a little amount of dispersed second phase in TiNi matrix. From TEM image and corresponding diffraction patterns, it is confirmed that the second phase is Ti2Ni, which always occurs at the grain boundaries or sub-boundaries with spherical or elliptical shape as demonstrated in Fig.5. It deduces that the yield strength increasing of Ti50Ni46.5Fe2.5Al1 alloys, as discussed in mechanical properties section, is a result of Ti2Ni phase strengthening matrix grain boundaries and hindering dislocation movement during plastic deformation. Furthermore, the phase without Al content in alloy indicates that Al addition entirely enters into TiNi matrix and Ti2Ni phase and strengthened TiNiFe alloy. In contrast to the Ni-rich alloys, the solubility limit on Ti-rich side of the binary TiNi alloy is almost vertical, precipitation of Ti2Ni phase appears only at grain boundaries and the precipitation behavior of Ti-rich alloys depends upon heat treatment temperature. KAWAMURA et al [17] found that Ti2Ni particles with random orientation in Ti-rich alloys will precipitate at the boundaries by heat- treatment at 720 K. In the present work, the specimens were annealed at 450 ℃ for 30 min, so it is possible to precipitate a little amount of Ti2Ni phase at the sub-boundaries. Another reason for the appearance of Ti2Ni is that additive Al prefers substituting Ti to Ni. As a result, the alloy with Al addition is easier to precipitate the Ti2Ni phase than TiNiFe alloys. Fe additive has strong preference for entering into Ni-site found by NAKATA et al[18], so there is no Ti2Ni phases were found in Ti50Ni47Fe3 alloys.
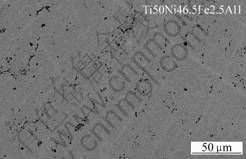
Fig. 4 SEM image of Ti50Ni46.5Fe2.5Al1 alloy
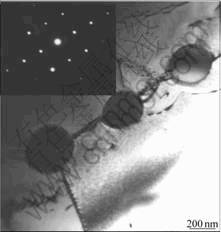
Fig. 5 TEM image of Ti50Ni46.5Fe2.5Al1 alloy
In Ti-Ni and TiNiFe alloys, martensites always prefer nucleation at the grain boundaries[19]. In Ti50Ni46.5Fe2.5Al1 alloy, Ti2Ni phase at grain boundaries will suppress martensitic nucleation and growth. So, it deduces that Ti2Ni phases play an important role on temperature hysteresis and martensitic transformation temperature.
References
[1] HORNBOGEN E. Shape memory alloys [J]. Proc Int Semin Adv Struct Funct Mater, 1991: 133-163.
[2] MIYAZAKI S, KOHL M. Recent development in TiNi-based shape memory alloys [J]. Proc SPIE Int Soc Opt Eng. 1998, 3324: 2-13.
[3] VAN HUMBEEK J. Non-medical applications of shape memory alloys[J]. Mat Sci Eng, 1999, A273-275: 134-148.
[4] DERIG T, PELTON A, STOECKEL D. An overview of nitinol medical applications[J]. Mat Sci Eng, 1999, A273-275: 149-160.
[5] HORIKAWA H, SUZUKI Y. Ni-Ti-Nb shape memory alloy pipe couplings[J]. Furukawa Rev, 1992, 10: 9-14.
[6] ZHAO L C, CAI W. Deformation-induced martensitic transformation and its reversibility in TiNiNb wide hysteresis shape memory alloys[J]. Acta Met Sinica, 1997, 33: 90-98.
[7] YANG J H, SIMPSON J W. Stress-induced transformation and super-elasticity in TiNiNb alloys [J]. J Phys IV: JP 1995, 5: c8-771.
[8] HWANG C M, WAYMAN C M. Phase transformation in TiNiFe TiNiAl and TiNi alloys[J]. Scri Metall, 1983, 17: 1345-1350.
[9] DAVID A M, DIMITRITS C L. Influence of cold work and heat treatment on the shape memory effect and plastic strain development of NiTi[J] Mater Sci Eng A, 2001, 308: 161-175.
[10] HARA T, OHBA T, OKUNISHI E, OTSUKA K. Structural study of R-phase in Ti50.23 at.%Ni and Ti47.75 at.%Ni1.5at.%Fe alloys[J]. Mater Trans JIM, 1997, 38: 11-17.
[11] MATSUMOTO H. Transformation behavior of TiNi in relation to thermal cycling and deformation[J]. Physica B, 1993, 190: 115-120.
[12] MOBERLY W J, PROFT J L, DUERIG J W, SINCLAIR R. Deformation, twining and thermal-mechanical strengthening of Ti50Ni47Fe3[J]. Acta Met Mater, 1990, 38: 2601-2612.
[13] MARQUINA M L, JIMENEZ M. Structural transitions in a TiNiFe shape memory alloy[J]. Mater Charact, 1994, 32: 189-193.
[14] XU H B, JIANG C B, GONG S K. Phase transformation and hysteresis of TiNiFe shape memory alloys[J]. Mater Sci Eng A, 2000, 218: 234-238.
[15] JIANG C B, XU H B. Effect of pre-deformation on gysteresis in TiNiFe shape memory alloy[J]. Mater Sci Forum, 2000, 327-328: 111-114.
[16] ZHANG C S, ZHAO L C, DUERIG T W, WAYMAN C M. Effects of deformation on the transformation hysteresis and shape memory effect in Ni47Ti44Nb9 alloy[J]. Scripta Metall Mater, 1990, 24: 1807-1812.
[17] KAWAMURA Y, GYOBU A, SABURI T, ASAI M. Structure of sputter-deposited Ti-rich TiNi alloys films[J]. Mater Sci Forum, 2000, 327-328: 303-306.
[18] NAKATA Y, TADAKI T, SHIMIZU K. Experimental and statistic-thermodynamical study on occupancy site of the third elements and their effects on the martentisitic transformations[J]. Proceeding of the 1996 International Conference on Displacive Phase, Transformations and Their Applications in Materials Engineering. 1998: 187-196.
[19] HWANG C M, WAYMAN C M, SALAMON M B, et al. Transformation behavior of a Ti50Ni47Fe3 alloy III martensitic transformation[J]. Phil Mag A, 1983, 47: 177-191.
(Edited by LI Yan-hong)
Corresponding author: XIAO Li; Tel: +86- 10-82317117; E-mail: liufs@huaa.edu.cn