DOI: 10.11817/j.issn.1672-7207.2018.06.025
含硫尾砂充填体长期强度性能及其影响因素
姜关照1, 2,吴爱祥1, 2,李红1, 2,王贻明1, 2,王洪江1, 2
(1. 北京科技大学 金属矿山高效开采与安全教育部重点实验室,北京,100083;
2. 北京科技大学 土木与资源工程学院,北京,100083)
摘要:针对含硫尾砂胶结充填体经常出现的后期强度劣化现象,进行含硫和无硫尾砂充填体强度对比试验,研究灰砂比和料浆对含硫尾砂充填体长期强度性能的影响,并采用XRD和SEM对含硫尾砂充填体中水化产物进行分析。研究结果表明:尾砂含硫量(质量分数)为6.1%,主要硫化物为黄铁矿时,充填体120 d强度下降达到47.4%。灰砂比为1:8时,充填体各龄期强度显著增加,后期强度劣化得到改善。灰砂比为1:16时,充填体长期强度稳定在0.85 MPa左右。充填料浆质量分数对充填体强度影响也较为显著,质量分数为74%~76%时,充填体后期强度下降幅度最小。当充填体内部结构较疏松时,次生石膏可以填充水化产物之间的空隙,在一定程度上改善充填体长期强度性能。充填体结构较为致密时,次生石膏会破坏其微观结构,降低充填体后期强度。
关键词:含硫尾砂;灰砂比;料浆质量分数;强度性能;硫酸盐侵蚀
中图分类号:TD853 文献标志码:A 文章编号:1672-7207(2018)06-1504-07
Long-term strength performance of sulfur tailings filling and its affecting factors
JIANG Guanzhao1, 2, WU Aixiang1, 2, LI Hong1, 2, WANG Yiming1, 2, WANG Hongjiang1, 2
(1. Key Laboratory of High-Efficient Mining and Safety of Metal Mines, Ministry of Education,
University of Science and Technology Beijing, Beijing 100083, China;
2. School of Civil and Resource Engineering,
University of Science and Technology Beijing, Beijing 100083, China)
Abstract: Aimed at the common later strength failure phenomenon in cemented sulfur tailings backfill, sulfur and non sulfur tailings backfill strength tests were carried out, and the effect of cement sand ratio and slurry concentration on the cemented sulfur tailings backfill long-term strength property was studied, XRD and SEM were used to analyze the hydration products in sulfur tailings backfill. The results show that the sulfur content of tailings is 6.1%, the main sulfide is pyrite, the 120 d strength of the filling body drops to 47.4%. When the cement sand ratio is 1:8, the strength of the filling body increases significantly at different ages, and the strength degradation at later stage is improved. Cement sand ratio is 1:16, and the long-term strength of the filling body is maintained at about 0.85 MPa. The influence of the filling slurry concentration on the strength of the filling body is also significant. When the concentration is 74%-76%, the decrease of backfill strength is the smallest. The secondary gypsum can fill the voids between the hydration products when the filling structure is loose, which can improve the filling body long-term strength property to some extent. When the filling body structure is dense, the secondary gypsum will destroy its microstructure and reduces the later strength of the filling body.
Key words: sulfur tailings; cement sand ratio; slurry mass fraction; strength property; sulfate attack
矿石选冶过程中会产生大量尾砂,为了实现采空区治理和尾砂固废利用的目的,往往需要将尾砂回填进入采空区。近年来,胶结充填已经成为主要的充填采矿方式,其具有可以减轻尾矿中潜在的有害物质对环境影响的优点[1-2]。研究表明,金属矿山尾矿中常含有多种硫化物和硫酸盐,含硫尾砂会对胶结充填体的稳定性和强度产生较大影响[3-5]。AYORA等[6]发现当尾砂中含有磁黄铁矿时,充填体内部会生成过量的次生石膏和钙矾石等膨胀相,造成块体开裂破坏,强度失效。KESIMAL等[7]进一步研究发现、尾砂中硫化物易氧化为硫酸盐,并与水泥水化产物反应生成钙矾石、次生石膏等膨胀相产物,从而对充填体产生硫酸盐侵蚀。由于这些产物具有很强的膨胀性,在充填体内部产生较高的内部压力,从而破坏充填体的强度。刘允秋等[8]认为:新桥矿尾砂含硫量为2.5%时,尾砂充填体强度最佳。闻奎武等[9]开展高硫极细尾砂充填料强度配比试验研究,发现灰砂比和料浆质量分数对充填体强度影响较大。王怀勇等[10]研究表明:提高充填体灰砂比至1:4时,可以降低硫化物氧化反应生成的硫酸盐对水泥的侵蚀作用。虽然国内外学者对含硫尾砂充填体强度性能研究已经取得了一定成果,但尾砂含硫量大多在10%以上,且对充填体长期强度性能影响因素研究依然不够深入。本文作者对含硫量较低的尾砂充填体强度性能进行研究,分析胶结剂添加量和料浆质量分数对充填体长期强度和稳定性的影响,为含硫尾砂充填体长期强度发展规律研究奠定理论基础。
1 试验材料
1.1 全尾砂
全尾砂Ⅰ来自安徽某硫铁矿选厂,其化学成分如表1所示,物相分析和粒度分析结果分别如图1和图2所示。全尾砂II取自甘肃某铅锌矿选厂,S质量分数为1.25%(含硫量较低,看作无硫尾砂),作为对照组。
由表1和图1可知:尾砂I中硫质量分数为6.1%,主要以黄铁矿(FeS2)的形式存在。由图2可知:尾砂I中粒度<20 μm的极细颗粒占60%以上,其粒径d50为4.3 μm。因此,全尾砂I属于含硫量相对较低(相对于含硫量10%以上尾砂)的细粒级尾砂[11]。
表1 全尾砂I化学成分(质量分数)
Table 1 Chemical component of tailings I %

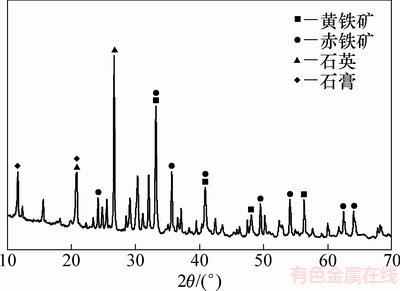
图1 全尾砂I XRD图谱
Fig. 1 XRD patterns of tailings I
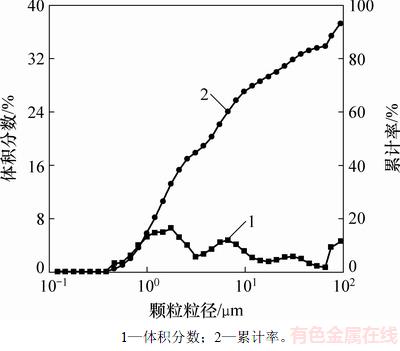
图2 全尾砂I粒径分析图
Fig. 2 Particle size of tailings I
1.2 胶凝剂
本试验胶凝剂选用425普通硅酸盐水泥,具有来源广,价格合理的优点。胶凝剂主要成分组成为48.3% C3S,21.0% C2S,10.0% C3A,8.7% C4AF,其中C3A和C4AF是钙矾石的主要物相来源。
2 试验方法
首先进行含硫尾砂充填体长期强度演变规律研究,然后开展不同灰砂比和料浆质量分数对充填体强度性能影响试验,最后通过分析充填体物相组成和微观结构,揭示含硫尾砂充填体强度形成规律和劣化调控机理。
含硫尾砂充填体试验配比如表2所示。根据表2将不同配比的水泥、全尾砂和水倒入砂浆搅拌锅内,按GB/T 50080—2002搅拌一定时间后测定充填料浆坍落度,然后将搅拌均匀的料浆注入长×宽×高为70.7 mm×70.7 mm×70.7 mm标准三联试模中振捣刮平,脱模后放入养护箱进行标准养护(温度(20±1) ℃,湿度≥90%),测定试块7,14,28,56,90和120 d单轴抗压强度。坍落度测定按照GB/T 50080—2002“普通混凝土拌和物性能试验方法标准”进行,抗压强度的测定按照GB/T 17671—1999“水泥胶砂强度检验方法”进行。
表2 含硫尾砂充填体试验配比
Table 2 Experimental ratio of sulfur tailings backfill

充填体试块测定90 d强度后,进行乙醇处理以终止水泥继续水化。将烘干后的试样磨细成粉并通过孔径80 μm的方孔筛,得到X线衍射(XRD)试验样品,采用D/max-rB大功率旋转阳极X线衍射仪进行试验。将部分试样切成小块采用FEI Quanta250扫描电子显微镜(SEM)分析试样微观形貌试样,并利用能谱仪(EDS)辅助识别矿物成分。
3 试验结果与分析
3.1 含硫尾砂充填体强度性能
2种尾砂充填体强度随固化时间变化如图3所示。由图3可知:固化时间超过28 d后,含硫尾砂充填体强度明显下降,90 d后下降趋势减缓,固化时间为120 d时,充填体强度下降47.4%。相反,无硫尾砂(全尾砂II)充填体强度随固化时间增加而上升,90 d后强度增加逐渐趋于平稳。这说明当尾砂中硫化物质量分数为6.1%时,会对充填体形成硫酸盐侵蚀,造成其后期强度劣化,这和BELLMANN等[12-13]的研究结果一致。
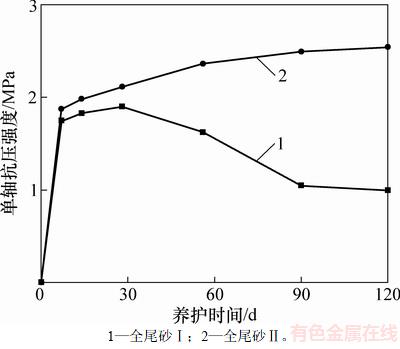
图3 2种尾砂充填体强度随固化时间变化
Fig. 3 Strength of two tailings filling bodies changing with curing time
3.2 灰砂比对充填体强度影响
尾砂充填体各龄期强度随灰砂比变化如图4所示。由图4可知:随着灰砂比的增大,充填体强度明显增加。当灰砂比为1:8时,充填体7 d强度达到5.0 MPa,但随着养护时间的增加强度迅速下降,28 d时强度为3.6 MPa,下降28.1%;当养护时间大于28 d后,充填体强度逐渐增加,长期强度(养护时间大于56 d)在4.0 MPa以上,120 d时强度损失率减小至16.2%。灰砂比为1:10时,充填体强度在14 d后出现下降,120 d时强度损失率为27.4%;当灰砂比降至1:12时,充填体120 d强度损失率为47.4%;当灰砂比为1:16时,充填体强度未出现明显劣化,随着养护时间的增加,强度稳定在0.85 MPa左右。

图4 尾砂充填体各龄期强度随灰砂比变化
Fig. 4 Strength of tailings filling in each age changing with cement sand ratio
灰砂比对含硫尾砂充填体强度影响试验结果表明,增大灰砂比可以提高充填体强度,但是灰砂比和充填体长期强度损失率之间并不存在反比关系。当灰砂比为1:8时,充填体获得较高的早期强度,提高其内部致密程度,随着膨胀相矿物的生成,充填体内部产生较高拉应力,从而引起内部微裂隙发展,充填体整体强度下降[14]。随着固化时间增加,C-S-H等水化产物进一步生成,逐渐填充充填体内部裂隙,使强度重新增加。这是因为C-S-H凝胶不仅可以在富铝相上生成保护层,减少钙矾石的生成,而且可以改善充填体微观结构,阻止黄铁矿氧化,降低充填体受到硫酸盐侵蚀的可能性[14-15]。当灰砂比为1:12~1:10时,虽然C-S-H凝胶生成量较少,充填体长期强度出现劣化,但是由于水化产物的填充作用,增加灰砂比可以显著改善充填体长期强度劣化现象。当采用1:16的低灰砂比时,充填体早期强度较低,长期强度无显著下降,推测此时充填体内部空隙和水化产物、膨胀相生成量达到平衡,即水化产物和部分膨胀相可以填充由于膨胀相增加引起的充填体内部空隙。
3.3 料浆质量分数对充填体强度影响
含硫尾砂充填体各龄期强度随料浆质量分数变化如图5所示。由图5可知:提高充填料浆质量分数对增大充填体早期强度作用明显。料浆质量分数为72%时,充填体长期强度小于0.7 MPa,强度损失率较大,达到60.9%。料浆质量分数为74%~76%时,充填体7 d强度显著增加,长期强度均大于1.0 MPa,120 d强度损失率为27.3%~47.4%。由表2可知:此时充填料浆塌落度为21.5~23.6 cm,表明充填料浆在该浓度区间可以达到理想膏体状态[16]。当料浆质量分数增加到78%时,充填体长期强度增加不显著,120 d强度损失率为50.2%。
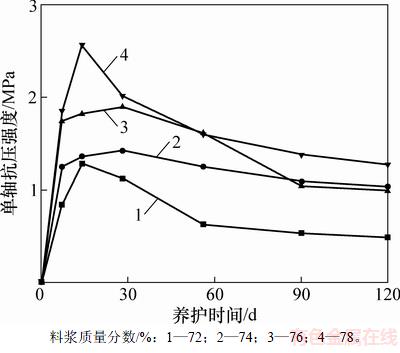
图5 含硫尾砂充填体各龄期强度随料浆质量分数变化
Fig. 5 Strength of tailings filling in each age changing with slurry concentration
料浆质量分数对含硫尾砂充填体强度影响试验结果表明,适当的料浆质量分数可以降低充填体强度损失系数。当料浆质量分数较高时,充填料浆中拌合水少,充填体内部结构密实,孔隙率低,C-S-H凝胶生成量不足以阻止膨胀相的破坏,造成充填体长期强度明显下降;当料浆质量分数较低时,充填体内部孔隙较多,有利于硫化物氧化,膨胀相矿物生成量增加,对充填体强度的破坏也加剧。当充填料浆质量分数为74%~76%时,充填体内部空隙率适中,强度损失率相对较低。因此,可以推测当充填料浆达到理想膏体状态时,充填体120 d强度损失系数最低。
3.4 充填体强度劣化调控机理分析
不同配比充填体90 d 时XRD图谱如图6所示。由图6可知:除含硫尾砂中含有的石英、黄铁矿、石膏、赤铁矿等矿物外,充填体水化产物中还含有次生石膏和钙矾石。充填体中钙矾石含量较低,且不同配比对其含量影响不大。
不同配比充填体SEM图谱如图7所示。由图7可知,不同配比充填体微观形貌明显不同,这是充填体强度演变规律不同的内在原因。

图6 不同配比充填体90 d 时XRD图谱
Fig. 6 XRD patterns of different ratios of 90 d filling body
由图6(a)可知:当料浆质量分数为76%,灰砂比为1:12时,充填体中生成较多的次生石膏。与图1相比,充填体中黄铁矿衍射峰强度下降,数量减少,说明其结晶度和含量降低。黄铁矿含量下降和次生石膏的生成,说明尾砂中硫化物会发生氧化,氧化过程[15, 17]如下:

图7 不同配比充填体SEM图谱
Fig. 7 SEM images of different ratios of filling body
(1)

(2)
(3)
在一定氧气和湿度的条件下,黄铁矿发生氧化,导致酸和硫酸盐的形成(式(1)),氧化产物会和进一步与C3A和Ca(OH)2发生反应形成钙矾石和次生石膏等膨胀相产物(式(2)和式(3)),其膨胀量分别为120%和140%[18-19]。酸的形成将降低水化产物存在环境的pH值,使C-S-H凝胶出现脱钙现象,导致已有水化产物减少,降低充填体力学性能[20]。
次生石膏多生成于水泥水化中后期(14 d以后),其生长膨胀会挤压周围已经形成的水化产物结构,使充填体内部产生较大的拉应力,当水化产物之间的黏聚力不足以抵抗拉应力时,会产生微裂隙(图7(a)),造成充填体后期强度降低[14, 21-22]。在实验室无外力约束条件下,微裂隙继续发展会造成充填体试块开裂、变形。由图7(d)可知:充填体中含有针状钙矾石,但含量较少,不会对充填体强度产生明显不利影响。
由图6(b)可知:当充填体灰砂比降低至1:16时,石膏衍射峰强度明显增强,说明其结晶度上升,含量也有所增加。由图7(b)可知:当灰砂比较低时,充填体内部结构疏松,空隙较多,部分空隙被疑似石膏的不规则短柱状晶体填充。对图7(e)中A处短柱状水化产物进行EDS分析,结果如图8所示。由图8可知:A处产物为晶体未发育完全的次生石膏。由于对充填体大量内部空隙具有填充作用,次生石膏对充填体的宏观强度有利,所以,当灰砂比为1:16时,充填体在受到膨胀相破坏时,强度未出现明显劣化。增大灰砂比一方面可以提高充填体强度,减少其内部空隙和膨胀相的生成,降低其渗透性;另一方面可以增加后期C-S-H凝胶生成量,在黄铁矿表面形成保护膜,阻止其进一步氧化,提高充填体后期强度。因此,增加灰砂比可以降低充填体劣化程度[15]。
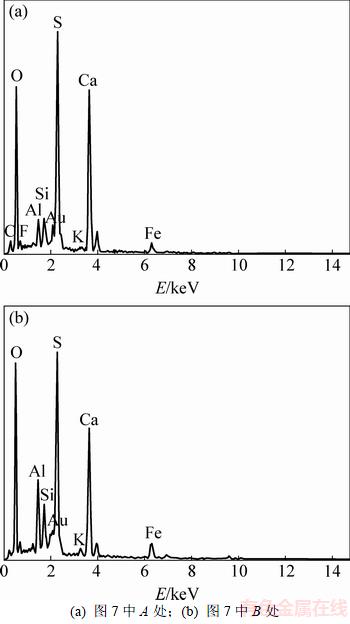
图8 部分水化产物EDS图谱
Fig. 8 EDS spectra of partial hydration product
由图6(c)可知:当充填料浆质量分数提高至78%时,充填体水化产物中石膏结晶度下降,含量也显著降低。由于充填料浆中拌合水含量较少,固结后的充填体结构致密,少量的次生石膏(图7(f)中B处)使充填体内部产生较强内应力,造成许多微裂隙形成,这是充填体早期强度明显下降的内在原因。同时,由于充填料浆灰砂比较低,后期C-S-H凝胶生成量较少,所以,当料浆质量分数为78%时,充填体后期强度持续下降。
4 结论
1) 含硫尾砂主要硫化物为黄铁矿,固化龄期内含硫尾砂充填体后期强度出现明显下降,无硫尾砂充填体强度逐渐增加,这说明黄铁矿对充填体强度演变影响显著。深入研究含硫尾砂充填体长期强度性能及影响因素,具有一定理论意义。
2) 虽然提高灰砂比可以增加C-S-H凝胶的生成量,改善充填体后期强度效果明显,但是会增加充填材料成本。当灰砂比降低至1:16时,充填体强度劣化现象不明显,这是因为充填体内部结构疏松,水化产物和部分膨胀相可以填充因为膨胀相引起的充填体内部空隙。
3) 料浆质量分数过高或过低都会对含硫尾砂充填体强度不利,本实验中充填料浆的适宜质量分数在74%~76%之间。适当的提高质量分数会降低充填体内部空隙,减少次生石膏的生成,同时充填体结构不会过于致密,内部应力保持在较低水平。
4) 灰砂比和料浆质量分数的增加均会减少次生石膏的生成量,提高充填体后期强度。考虑到经济成本,实际充填时应在较低灰砂比基础上,控制充填料浆质量分数,减小含硫尾砂对充填体强度产生的不利影响。
参考文献:
[1] 孟跃辉, 倪文, 张玉燕. 我国尾矿综合利用发展现状及前景[J]. 中国矿山工程, 2010, 39(5): 4-9.
MENG Yuehui, NI Wen, ZHANG Yuyan. Current state of ore tailings reusing and its future development in China[J]. China Mine Engineering, 2010, 39(5): 4-9.
[2] 姚振文. 浅析我国采矿技术的现状及发展趋势[J]. 科技创新与应用, 2016(35): 136.
YAO Zhenwen. Analysis on present situation and developing trend of mining technology in China[J]. Technology Innovation and Application, 2016(35): 136.
[3] 许毓海. 尾砂中硫化物对充填体质量影响研究[J]. 矿业研究与开发, 2009(5): 4-6.
XU Yuhai. Study on the effect of sulfide in tailings on filling body quality[J]. Mining Research and Development, 2009(5): 4-6.
[4] 常宝孟, 韩斌, 闫其盼,等. 高硫尾矿胶结充填长期强度演化规律及机理分析[J]. 现代矿业, 2016(5): 6-9.
CHANG Baomeng, HAN Bin, YAN Qipan, et al, Analysis of the long-term strength evolution regularity and mechanism of cemented filling with high sulphur tailings[J]. Modern Mining, 2016(5): 6-9.
[5] 田均兵, 陈昌礼, 邓晓轩, 等. 高硫尾砂胶结充填试验研究[J]. 中国矿业, 2016, 25(4): 103-107.
TIAN Junbing, CHEN Changli, DENG Xiaoxuan, et al. The experimental study of the cemented filling of high sulfur tailings[J]. China Mining, 2016, 25(4): 103-107.
[6] AYORA C, CHINCHON S, AGUADO A, et al. Weathering of iron sulfides and concrete alteration: thermodynamic model and observation in dams from Central Pyrenees, Spain[J]. Cement and Concrete Research, 1998, 28(4): 591-603.
[7] KESIMAL A, YILMAZ E, ERCIKDI B. Evaluation of paste backfill mixtures consisting of sulphide-rich mill tailings and varying cement contents [J]. Cement and Concrete Research, 2004, 34(10): 1817-1822.
[8] 刘允秋, 侯大德. 含硫尾砂充填体强度试验[J]. 现代矿业, 2013, 29(11): 195-196.
LIU Yunqiu, HOU Dade. Test of sulfur tailings backfill strength[J]. Modern Mining, 2013, 29(11): 195-196.
[9] 闻奎武, 彭亮, 康瑞海, 等. 高硫极细尾砂充填料强度配比试验研究[J]. 采矿技术, 2016(4): 40-42.
WEN Kiuwu, PENG Liang, KANG Ruihai, et al. Experimental study on high sulfur fine tailings filling strength ratio[J]. Mining Technology, 2016(4): 40-42.
[10] 王怀勇, 张爱民, 贺茂坤. 高硫极细全尾砂充填料配比及输送特性试验研究[J]. 中国矿山工程, 2014, 43(6): 1-4.
WANG Huaiyong, ZHANG Aimin, HE Maokun. Experimental study on unclassified tailing backfill materials proportion and pipeline transportation property with high sulphur and superfine particle[J]. China Mine Engineering, 2014, 43(6): 1-4.
[11] HUSTRULID W, BULLOCK R. Underground mining methods: engineering fundamentals and international case studies[M]. Colorado: Society Mining, Metallurgy and Exploration, 2001: 14-601.
[12] BELLMANN F, M
SER B, STARK J. Influence of sulfate solution concentration on the formation of gypsum in sulfate resistance test specimen[J]. Cement & Concrete Research, 2006, 36(2): 358-363.
[13] ARGANE R, BENZAAZOUA M, BOUAMRANE A, et al. Cement hydration and durability of low sulfide tailings-based renders: a case study in Moroccan constructions[J]. Minerals Engineering, 2015, 76(Pt7): 97-108.
[14] SONG Hui, CHEN Jiankang, JIANG Jinyang. An internal expansive stress model of concrete under sulfate attack[J]. Acta Mechanica Solida Sinica, 2016, 29(6): 610-619.
[15] ERCIKDI B, KESIMAL A, CIHANGIR F, et al. Cemented paste backfill of sulphide-rich tailings: importance of binder type and dosage[J]. Cement & Concrete Composites, 2009, 31(4): 268-274.
[16] 吴爱祥, 王洪江. 金属矿膏体充填理论与技术[M]. 北京: 科学出版社, 2015: 5-10.
WU Aixiang, WANG Hongjiang. Theory and technology of paste filling in metal mine[M]. Beijing: Science Press, 2015: 5-10.
[17] 李文臣. 硫酸盐对胶结充填体早期性能的影响及其机理研究[D]. 北京: 中国矿业大学(北京)资源与安全工程学院, 2016: 103-110.
LI Wenchen. Characteristics and mechanism of sulphate effect on the early age properties of cemented paste backfill[D]. Beijing: China University of Mining and Technology. College of Resources & Safety Engineering, 2016: 103-110.
[18] 杨建森. 混凝土中钙矾石作用的二重性及其发生条件[J]. 土木工程学报, 2003, 36(2): 100-103.
YANG Jiansen. Discussion on the action duality of ettringite and it's causing condition in concrete[J]. China Civil Engineering Journal, 2003, 36(2): 100-103.
[19] 肖佳, 邓德华, 张文恩, 等. 硫酸盐侵蚀下石膏形成引起的水泥净浆破坏[J]. 建筑材料学报, 2006, 9(1): 19-23.
XIAO Jia, DENG Dehua, ZHANG Wenen, et al. Formation of gypsum leading to the destruction of cement paste under the external sulfate attacking[J]. Journal of Building Materials, 2006, 9(1): 19-23.
[20] 何真, 王磊, 邵一心, 等. 脱钙对水泥浆体中C-S-H凝胶结构的影响[J]. 建筑材料学报, 2011, 14(3): 293-298.
HE Zhen, WANG Lei, SHAO Yixin, et al. Effect of decalcification on C-S-H gel microstructure in cement paste[J]. Journal of Building Materials 2011, 14(3): 293-298.
[21] 王宝, 张虎元, 董兴玲, 等. 硫化物氧化对充填体长期强度的影响[J]. 化工矿物与加工, 2007, 36(10): 29-31.
WANG Bao, ZHANG Huyuan, DONG Xingling, et al. Long-term deterioration of cemented paste backfill due to sulphide oxidation[J]. Industrial Minerals & Processing, 2007, 36(10): 29-31.
[22] BENZAAZOUA M, OUELLET J, SERVANT S, et al. Cementitious backfill with high sulfur content physical, chemical, and mineralogical characterization[J]. Cement & Concrete Research, 1999, 29(5): 719-725.
(编辑 赵俊)
收稿日期:2017-06-01;修回日期:2017-08-14
基金项目(Foundation item):国家自然科学基金资助项目(51374034);北京市科委项目(Z161100001216002)(Project(51374034) supported by the National Natural Science Foundation of China; Project(Z161100001216002) supported by Beijing Municipal Science & Technology Commission)
通信作者:吴爱祥,博士,教授,从事膏体充填采矿、矿山岩石力学、溶浸采矿等研究;E-mail:wuaixiang@126.com