J. Cent. South Univ. (2012) 19: 835-841
DOI: 10.1007/s11771-012-1080-8
Utilization of municipal solid waste incineration fly ash in
lightweight aggregates
TAN Wen-fa(谭文发)1,WANG Li-ao(王里奥)1, HUANG Chuang(黄川)1,
LIU Yuan-yuan(刘元元)2, J. E. Green3, D. Newport3, T. Green4
1. State Key Laboratory for Coal Mine Disaster Dynamics and Control,
Resource and Environmental Science College, Chongqing University, Chongqing 400044, China;
2. Faculty of Urban Construction and Environmental Engineering, Chongqing University, Chongqing 400044, China;
3. Sustainability Research Institute, University of East London, 4-6 University Way, London, E16 2RD, UK;
4. RTAL (H.K.) Limited, Hong Kong, China
? Central South University Press and Springer-Verlag Berlin Heidelberg 2012
Abstract: Washing pre-treatment of municipal solid waste incineration (MSWI) fly ash blended with shale and sludge was utilized in the manufacture of light-weight aggregates and processed to form ceramic pellets. A formula uniform design was performed to arrange the mixture ratio of the materials. The optimal mixture ratio of the materials was determined by measuring the bulk density, granule strength, and 1 h water absorption of the pellets. It is shown that the optimal mixture ratios of materials, MSWI fly ash, shale, and sludge, are 23.16%, 62.58%, and 14.25% (mass fraction), respectively. The performance testing indicators of light-weight aggregates are obtained under the optimum mixture ratio: bulk density of 613 kg/m3, granule strength of 821N, and 1 h water absorption of 11.6%, meeting 700 grade light-aggregate of GB/T 17431.2—1998 standard. The results suggest that utilization of MSWI fly ash in light-weight aggregates is an effective method and a potential means to create much more values.
Key words: MSWI fly ash; pre-treatment; trefoil rotary kiln; heavy metal; light-weight aggregates
1 Introduction
Municipal solid waste incineration (MSWI) fly ash is a residue after incineration, which is classified as a hazardous waste in China, owing to its heavy metals and, in some cases, toxic chlorinated organics. Handling and disposal of municipal solid waste incineration (MSWI) fly ash have received substantial attention all over the world [1], principally because this material contains high concentrations of leachable heavy metals. Therefore, MSWI fly ash needs careful management and its disposal requires either high protection level landfills or treatment before landfill so as to reduce contaminants release into the environment [2].
Various technologies have been investigated in order to reduce the hazardous characteristics of MSWI fly ash, including solidification with cement-based materials, chemical stabilization with EDTA, sodium sulfide [3] and thiourea, hydrometallurgical extraction by dissolution in acidic or alkaline medium [4], and vitrification [5] or sintering [6] for reuse as construction materials. Except the last thermal method, it is difficult to remove dioxins from MSWI fly ash. Hence, thermal treatment is among the most promising methods to handle fly ash safely. Recent work in China demonstrated that MSWI fly ash can be vitrified by melting below 1 000 °C, and by adding borax, B2O3 and CaF2 [7]. However, leaching toxicity and specification of heavy metals as well as performance of the vitrification product are difficult to meet the requirements of relevant standards, which limits its use and development.
The un-pretreated MSWI fly ash was directly mixed with red ceramic clay in making ceramic brick [8]. However, it ignored highly toxic organic chloride by-products such as polychlorinated dibenzofurans and dibenzop-dioxins (PCDD/Fs) during the sintering process. The prerequisite for generating PCDD/Fs [9] is the existence of organic or inorganic chlorine, regardless of high temperature gas phase formation, de novo synthesis or precursor synthesis. MSWI fly ash contains about 20% (mass fraction) of chlorine. If not removed first, sintering and the cooling process would generate a lot of PCDD/Fs, which would cause serious environmental impact, especially, on industrial production. In addition, there is a need to find alternative material to replace clay in production of ceramic products due to shortages occurring worldwide [10].
Aiming to reduce the generation of PCDD/Fs from the source, chloride in MSWI fly ash was decreased through preliminary washing treatment with water. Besides, in this work, MSWI fly ash was used in the blending sintering in the trefoil rotary kiln which makes up for the shortages of slow heating rate and uneven heating of traditional muffle furnace. It not only significantly shortens the sintering time and lowers energy consumption, but also improves the properties of light-weight aggregates. Instead of only emphasizing the treatment of fly ash, this work emphasizes on the utilization of fly ash as a raw material to form light-weight aggregates, rather than a hazardous waste which possesses great commercial value.
This work provides a solution to two modern day dilemmas which confront both disposers of waste and users of natural aggregates. MSWI fly ash came from Chongqing Tongxing Waste Plant and other raw materials, shale and sludge, were utilized in the manufacture of light-weight aggregates and processed to form bonded pellets. Firstly, the chemical composition of MSWI fly ash was analyzed by the instrument like XRF. Secondly, the microstructure was studied by specific surface area and pore diameter measurement, and SEM. Thirdly, the leaching toxicity of heavy metals in the ceramic pellet was tested by AAS. This work seeks to find a way possible to use fly ash in making ceramic pellet to reach the standard of light-weight aggregate on one hand and stabilize heavy metals on the other hand.
2 Experimental
2.1 Main experimental apparatus
The trefoil rotary kiln shown in Fig. 1 mimics the rock formation of the natural volcanic eruption process. The inner cylinder of the kiln indicated in Fig. 2 has a corrugated design, so it can rapidly heat and cool
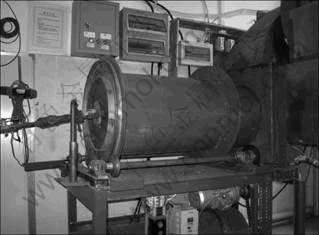
Fig. 1 Trefoil rotary kiln
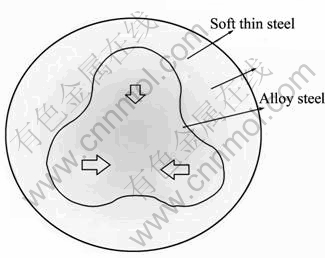
Fig. 2 Cross-section of trefoil rotary kiln
light-weight aggregates and melt toxic substances effectively, reducing the generation of volatile toxic gases significantly.
Compared with the traditional rotary kiln which consists of a thick steel drum lined with heavy manually laid fire bricks, trefoil rotary kiln has a higher thermal efficiency. Aerospace alloy steel was used as inwall, and soft thin steel as the outer wall. A ceramic fibre insulation was compressed between a thin steel alloy hot face and a tensioned thin mild steel cold face to form a cartridge with a triple-lobed cross section, forming a box-shaped cross section. The specific functions embodied in the kiln are:
1) There is significant insulation effect (when the inner temperature of kiln is 1 200 °C, and the outer wall temperature is only about 60 °C).
2) Due to its smaller and lighter structure, it does not require expensive repair or overhaul, and is easier to manufacture, transport, install, move and replace.
3) It possesses a higher heat transfer efficiency, much faster heating and cooling (faster than the traditional kiln by about 50 times), which significantly shortens the sintering time, thereby reducing the energy consumption.
4) It has higher load (twice that of the traditional rotary kiln) conducive to reduce the thermal gradient, improve the sintering stability, and eventually create more industrial and economic value.
2.2 Analysis methods of raw materials
1) Specific surface area and pore size analysis
By ASAP 2020M-type adsorption measurement, and N2 adsorption capacity method, the temperature was -195.996 °C; BET equation and BJH method of fly ash samples (dry basis) were selected to determine the specific surface area and pore size distribution.
2) X-ray fluorescence analyzer (XRF)
The Shimadzu XRF-1800 was used. The testing conditions were: Rh target, 40 kV, 95 mA, 20 (°)/min.
3) Microscopic analysis
TESCAN VEGA II LMU scanning electron microscopy (SEM) was used. The testing conditions were high vacuum (SE), 3.0 nm, and 30 kV.
4) The leaching toxicity analysis was performed by means of HJ/T 300—2007 (solid waste-extraction procedure for leaching toxicity-acetic acid buffer solution method): 17.25 mL reagent of glacial acetic acid was diluted to 1 L, using deionized water as the solvent and the ratio of liquid to solid was 20:1, then oscillating flip-style devices were vibrated for (18±2) h. In the last step, using AAS (AA6000), the leaching toxicity of heavy metals was analyzed according with GB/T 5085.3—2007 standard. The contents of Cd and Pb in the residue were analyzed by a sequential chemical extraction procedure [11] with HCl/HNO3/ HF/HClO4 and Hg with HCl/H2O2/HNO3.
2.3 Raw materials for making light-weight aggregates
The fly ash used in this work was sampled from Tongxing MSW Incineration Plant, Chongqing, China, which was firstly dried at 105 °C for 24 h to constant mass, then washed with distilled water at a liquid-to-solid ratio (L/S) of 10:1. Finally, the residues were dried and stored for sintering. Shale was used to increase the proportion of aluminosilicate came from a suburb of Chongqing and sludge was used as an expanding agent from the Jiguanshi wastewater treatment plant, Chongqing, China. The specific processes are as follows.
1) Washed fly ash together with ground shale and sludge were mixed with water, and the moisture content of mixture was controlled to approximately 30%.
2) The mixture was used in the manufacture of pellets in a granulator, as shown in Fig. 3, followed by oven drying for 5 h at 105 °C.
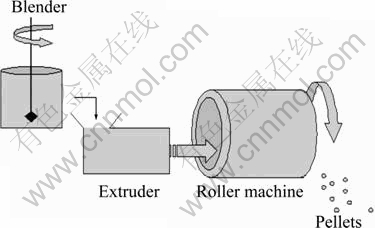
Fig. 3 Diagrammatic representation of granulation process
3) The baked pellets were put into the trefoil rotary kiln at 500 °C. The speed of rotation of the kiln was controlled at 7-10 r/min. The pellets were sintered for approximately 20 min until the temperature rose to 1 130 °C, it was maintained for 2-6 min at that temperature, and then the heating was stopped. When the kiln was cooled to 1 000 °C, the ceramic pellets were removed and allowed to cool to room temperature before testing the parameters of the ceramic pellets.
2.4 Mixture uniform design
Uniform design is a type of experiment designing program, called uniform design or uniform design experimental method, or space-filling design, in which the experimental formula is distributed uniformly in the test range. Compared with the orthogonal test, it can obtain the maximum information through the least amount of tests. In addition, the factors (levels) range of the uniform test can be much wider and more uniform. The design method is as follows:
1) Given s (factor number) and n (test times), select the appropriate uniform design table
or Un(ns-1), which is denoted by qki.
2) For each i, calculate Eqs. (1) and (2):
cki=(2qki-1)/2n, k=1, …, s-1 (1)
(2)
With the aim to incorporate as much MSWI fly ash as possible meanwhile ensuring the characterization of ceramic pellets meeting the relevant standards of light-weight aggregates, the ratio ranges of three types of raw materials (dry ratio) were controlled as follows:
Shale (X1): 0.6≤X1≤0.8,
Washed fly ash (X2): 0.15≤X2≤0.25,
Sludge (X3): 0.05≤X3≤0.15.
According to Eq. (2), there is
(3)
Calculate Eq. (3) and then select
as uniform design table to arrange experiment (Table 1).
3 Results and discussion
3.1 Characterization of MSWI fly ash
3.1.1 Specific surface area, pore size and pore volume
The specific surface area and pore size listed in Table 2 indicate that the specific surface area (BET) and pore volume (BJH) of ??original fly ash sample were both very small, approximately 1 831 m2/kg and1.14×10-8 m3/kg, respectively, with an average pore size of 20.607 nm. Micro-porous structure was few and far between. Compared with raw fly ash, the specific surface area (BET) increased to 2 0037 m2/kg and pore volume (BJH) increased to 12.05×10-8 m3/kg. Both were significantly changed due to the particle separation which adsorbed on the surface of MSWI fly ash after water washing pretreatment.
Table 1 Proportioning scheme of light-weight aggregate
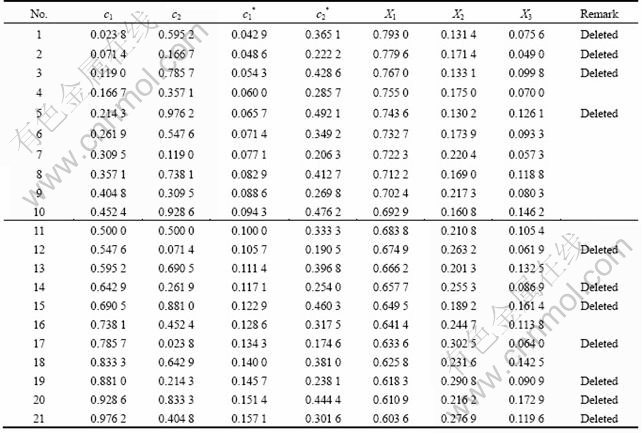
Table 2 Specific surface areas, pore size and pore volume of MSWI fly ash
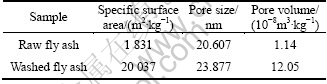
3.1.2 Chemical composition analysis
Major elements of original fly ash are shown in Table 3, including Ca, Si, Na, K, O and Cl. The compounds were presented in the form of CaO, SiO2, NaCl and KCl. Original fly ash contains nearly 21% of chlorine. If not removed first, sintering and cooling process would generate a lot of PCDD/Fs, which would have a serious environmental impact. After water washing pretreatment, the amounts of Na, K, Cl soluble-salts were significantly reduced, especially Cl which was reduced to only 1.4% compared with the original fly ash, leading to a reduction in the amount of dioxins generated during the combustion process. The contents of Si and Ca were doubled to 13.9% and 50.3%, respectively.
Table 3 Chemical composition of raw material (mass fraction, %)
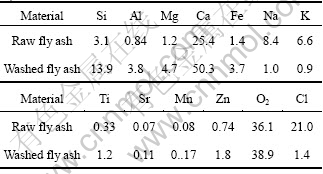
Four chemical forms include extractable acids which jeopardize human and environment most and other three speciations, iron oxide occluded, organically bounded and residues are relatively stable, especially residue less impacting on the environment. From Fig. 4, it can be seen that soluble Cd mainly existed in the acid extractable, Pb and Cu mainly in the acid soluble and iron oxide occluded, soluble Zn, Cr and Hg mainly in organically bounded and acid soluble phases, soluble Mn slightly more in organically bounded residue. Hence, acids could enhance leaching of the seven heavy metals, which is consistent with results of the leaching test. MSWI fly ash blended with shale and sludge was utilized in the manufacture of light-weight aggregates and processed to form ceramic pellets to minimize leaching toxicity of these heavy metals by reducing their existence in acid soluble, iron oxide occluded and organically bounded phases, as done in this work.
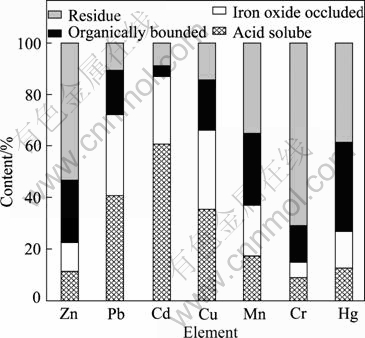
Fig. 4 Sequential chemical extraction results of sampled fly ash
3.1.3 Leaching toxicity of fly ash
The leaching test in Table 4 shows that heavy metals such as Cd, Cr, Hg, Cu, Pb, Zn and Hg are toxic which are explicitly described in “Identification standard of hazardous waste–identification of leaching toxicity (GB 5085.3—2007)”. Therefore, these seven heavy metals were the principal pollutants found in leachate and caused potential harm to the environment. The contents of Pb and Zn exceeded the limit described in GB 5085.3—2007, thus leading to severe influence on the environment. The remaining five heavy metals can meet the leaching limit value (GB 5085.3—2007).
Table 4 Heavy metals leaching toxicity of fly ash (10-3kg/m3)
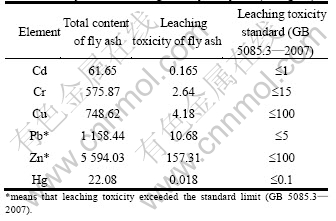
3.2. Mixture uniform design
According to the national standards (GB/T 17431. 1—1998, and GB/T 17431.2—1998), bulk density, granule strength and 1 h water absorption are important indicators to measure the performance of light-weight aggregate. Therefore, they were chosen as the assessment indicators in the formula uniform design. Experiment and test results are given in Table 5.
Table 5 Test results of light-weight aggregate formula
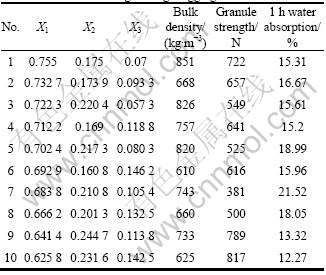
Group 10 appears to be the best ratio of raw materials. With a fly ash content of 23% (Table 5), it had the highest crushing strength with bulk density and water absorption also meeting standard requirements.
In accordance with the optimized material ratio, many granules (4 kg) were sintered using the trefoil rotary kiln to form light-weight aggregates. Sample appearances are shown in Figs. 6 and 7. The corresponding performance testing indicators of light- weight aggregates show the bulk density to be 613 kg/m3, granule strength to be 821 N, and 1 h water absorption to be 11.6%.
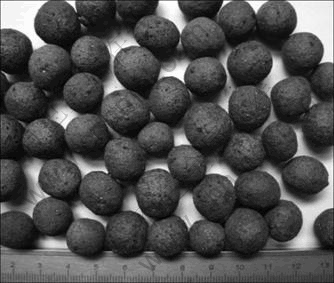
Fig. 6 Appearance of ceramic pellets
3.4. Microstructure of light-weight aggregates
Scanning electron microscopy utilizes secondary electron signal imaging to observe the morphology and microstructure of the samples. Samples should not have electrical conductivity and therefore need to be fully dried and metallized by spraying on surface before the SEM test. Morphology and microstructure of light-weight aggregates are shown in Fig. 8 and Fig. 9, respectively.
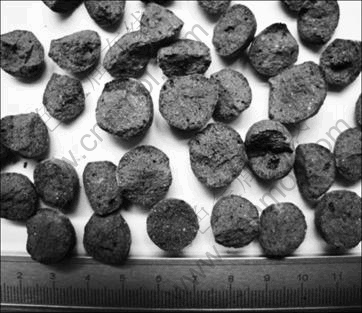
Fig. 7 Structure of ceramic pellets section
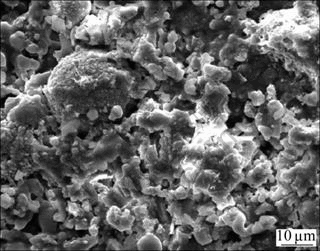
Fig. 8 SEM image of ceramic pellets surface
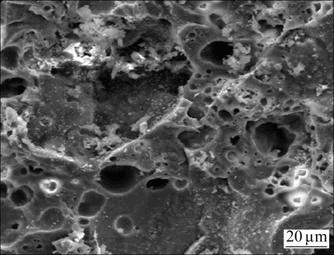
Fig. 9 SEM image of ceramic pellets section
From SEM images, micro-pore structure of light-weight aggregate surface is few and far between, and material in a glassy phase occupies most of the granule surface. Compared with the light-weight aggregate surface, the internal microstructure is completely different. Abundant micro-pore structure, most in the range of 10-20 μm, was uniformly distributed within the internal granule. The different micro-pore structure of the surface and interior formed a high strength, low water absorbing light-weight aggregate.
3.5 Extraction value of light-weight aggregates
Leaching results of heavy metals from sintered light-weight aggregates based on the optimal ratio of material are given in Table 8. The heavy metal extraction values of light-weight aggregates are all much lower than the standard described in “Identification standard of hazardous waste–identification of leaching toxicity (GB 5085.3—2007)” and the landfill standard (GB 16889—2008). Among them, the contents of Cr, Hg in the leach liquor cannot be detected and the contents of the other four heavy metals are Cu 0.15 mg/L, Pb 0.012 mg/L, Cd 0.05 mg/L and Zn 0.053 mg/L, respectively. Reasons can be simply divided into two categories: 1) The majority of the volatile heavy metals such as Hg and Pb are evaporated and the inactive part is difficult to extract; 2) Less volatile heavy metals such as Cr, Cu, Cd and Zn are stabilized by certain substances through a series of complex chemical reactions during the sintering process. Hence, utilization of MSWI fly ash to make glazed light-weight aggregates is an effective way to stabilize heavy metals.
Table 8 Leaching toxicity test results of light-weight aggregate (10-3kg/m3)
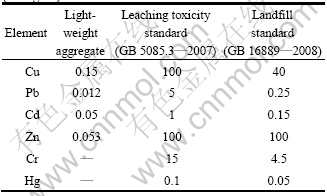
4 Conclusions
1) With the uniform design method, the optimum mixture ratios of raw materials-(MSWI) fly ash, shale, and sludge are 23.16%, 62.58%, and 14.25%, respectively. This method greatly reduces the number of experiments, thereby providing a fast and effective way to industrial manufacture.
2) Compared with traditional rotary kiln, the trefoil rotary kiln has a higher thermal efficiency leading to heating and cooling rates approximately 50 times faster, which can rapidly vitrify the surface of the granule. This means that it can significantly shorten the sintering time, thereby reducing the energy consumption.
3) The performance testing indicators of aggregates are obtained under the optimum mixture ratio: bulk density of 613 kg/m3, granule strength of 821 N, and 1 h absorption water of 11.6%. All of the parameters meet the 700 grade light-weight aggregate of GB/T 17431.2—1998 standard.
4) The results of leaching test are below the concentration limits of hazardous constituents of hazardous waste identification standard (GB/T 5085.3—2007) and landfill standard (GB 16889—2008), achieving the dual purpose of detoxification and utilization of fly ash.
References
[1] SUN Y, ZHENG J C, ZOU L Q. Reducing volatilization of heavy metals in phosphate-pretreated municipal solid waste incineration fly ash by forming pyromorphite-like minerals [J]. Waste Manage, 2011, 31: 325-330.
[2] WAN X, WANG W, YE T M, GUO Y W, GAO X B. A study on the chemical and mineralogical characterization of MSWI fly ash using a sequential extraction procedure. [J]. J Hazard Mater, 2006, 134: 197-201.
[3] ZHANG H J, YU Y, NI Y W. Stabilization of heavy metals in municipal solid waste incineration fly ash with the thiol collectors [J]. J Environ Sci, 2008, 28: 1899-1904.
[4] SREENIVASARAO K, WARREN G W, MCKINLEY M D, GAO G. Hydrometallurgical treatment of municipal solid waste fly ash for simultaneous detoxification and metal recovery [J]. J Environ Sci, 1997, 32: 1225-1245.
[5] ABANADES S, FLAMANT G. Fate of heavy metals during municipal solid waste incineration [J]. Waste Manage, 2002, 20: 55-68.
[6] MANGIALARDI T. Sintering of MSW fly ash for reuse as a concrete aggregate [J]. J Hazard Mater, 2001, 87, 225-239.
[7] CHEN D Z, ZHANG H S. Preliminary study on MSWI fly ash vitrification at lower temperature [J]. Shanghai Environ Sci, 2002, 21: 344-349.
[8] ZHANG H Y, ZHAO Y C. Utilization of municipal solid waste incineration (MSWI) fly ash in ceramic brick: Product characterization and environmental toxicity [J]. Waste Manage, 2010, 31: 331-341.
[9] CIEPLIK M K, de JONG, V, BOZOVIC J. Formation of dioxins from combustion micropollutants over MSWI Fly Ash [J]. Environ Sci Technol, 2006, 40: 1263-1269.
[10] ZHANG H Y, ZHAO Y C. Study on use of MSWI fly ash in ceramic tile [J]. Journal of Hazardous Materials, 2007, 141: 106-114.
[11] ABANADES S, FLAMANT G. Fate of heavy metals during municipal solid waste incineration [J]. Waste Manage, 2002, 20: 55-68.
(Edited by YANG Bing)
Foundation item: Project(CSTC.2011AC7065) supported by the Science & Technology Committee of Chongqing, China; Project(50808184) supported by the National Natural Science Foundation of China
Received date: 2011-07-26; Accepted date: 2011-11-14
Corresponding author: WANG Li-ao, Professor; Tel/Fax: +86-23-65111477; E-mail: wang65111477@yahoo.com.cn