
Production of super-high strength aluminum alloy billets by low frequency electromagnetic casting
ZHANG Hai-tao, CUI Jian-zhong
Key Laboratory of Electromagnetic Processing of Materials of Ministry of Education,Northeastern University, Shenyang 110004, China
Received 20 November 2010; accepted 19 May 2011
Abstract: The effects of low frequency electromagnetic field on the macro-physical fields in the semi-continuous casting process of aluminum alloys and the microstructure and crack in the billets were studied and analyzed by the numerical and experimental methods. Comparison of the results for the macro-physical fields in the low frequency electromagnetic casting (LFEC) process with the conventional DC casting process indicates the following characters due to the application of electromagnetic field: an entirely changed direction and remarkably increased velocity of melt flow; a uniform distribution and a decreased gradient of temperature; elevated isothermal lines; a reduced sump depth; decreased stress and plastic deformation. Further, the microstructure of the billets is refined remarkably and the crack in the billets is eliminated in LFEC process because of modification of the macro-physical fields induced by the application of low frequency electromagnetic field.
Key words: super-high strength aluminum alloy; low frequency electromagnetic casting; DC casting; macro-physical field; crack; microstructure
1 Introduction
Super-high strength aluminum alloys are important materials for the aerospace industries, due to their low density, high strength, and good hot work ability. Demand in the aerospace industry for higher strength, higher toughness, and higher corrosion resistance motivates continuing research on these alloys [1-4]. In general, increasing alloying element content will increase strength, but increased alloying element content makes it more difficult to cast the alloy because the crack susceptibility is also increased remarkably. Therefore, the crack is a key problem in the production of super-high strength aluminum alloys billets. BOENDER and BURGHARDT [5] studied on the fracture mechanics to the DC casting of high-strength aluminum alloys and their results showed that it is more dangerous during the final stage of a cast to generate crack. NAGAUMI et al [6-8] investigated the effect of alloy element on the crack sensitivity of high strength aluminum alloys and it is shown that iron element increases the crack sensitivity. SUYITNO et al [9] and ESKIN et al [10-11] evaluated various hot tearing criteria and it is found that the RDG criterion shows the greatest potential in the regard when used on a qualitative base.
However, when the zinc content in the aluminum alloy is more than 8%, it is very difficult to obtain billets without crack defects by the conventional method. Therefore, in order to obtain the billets without crack defects, some special methods are used, such as spray forming process and low frequency electromagnetic casting (LFEC). LFEC process is the attracted one among these methods because this process is based on the conventional DC casting. LFEC was developed by CUI and his colleagues [12-13], in which the low skin effect of low frequency electromagnetic field is used to control the macro-physical fields in the casting process. In addition, there are not literatures reported about producing high strength aluminum alloys with zinc content more than 8% by the conventional DC casting. In this research, the low frequency electromagnetic casting process is used to produce the super-high strength Al-10Zn-2.3Mg-2.4Cu-Zr aluminum alloys and the macro-physical fields, the crack occurring in casting process and the microstructure of billets are studied by the numerical and experimental methods.
2 Numerical modeling and experiments
2.1 Numerical modelling
In this work, a coupled model was used to describe the interaction of the multiple macro-physical fields- electromagnetic field, fluid flow, temperature field, solidification and stress-strain field in the conventional DC and LFEC processes of the billets with 200 mm in diameter and the casting process parameters are listed in Table 1. Moreover, this detailed model can be found in Refs. [14-15].
In order to model the interaction of the multiple physical fields in the two processes, the model used in this work was implemented by the commercial software package Ansys and Fluent. Further, this modeling procedure of the DC casting and LFEC processes is as follows: firstly, the electromagnetic field is calculated by Ansys and the Lorentz force is obtained simultaneously; then, the Lorentz force is added to the conservation equation of momentum as the momentum source term during solving flow field which is coupled with temperature field and solidification, and these physical fields are calculated by Fluent software; lastly, the calculated temperature is inputted into Ansys software to calculate the stress-strain field which is carried out by Ansys software.
2.2 Experiments
Two new 7××× aluminum alloy billets with diameter of 200 mm were respectively cast by LFEC process and conventional DC casting process at melt temperature of 730 °C, and casting speed of 85 mm/min. The electromagnetic field was applied by a 80 t water-cooling copper coil surrounding the mold made of stainless steel. The current frequency in the coil was fixed at 25 Hz and the current was 120 A in the LFEC process.
3 Results and discussion
3.1 Effect of electromagnetic field on macro-physical fields
Figure 1 shows the temperature profiles and velocity vectors and velocity contours in the presence of the electromagnetic field and in the absence of electromagnetic field in three separate plots. The left part in the three plots is the predicted results in the absence of the electromagnetic field and the right part is the predicted results in the presence of the electromagnetic field.
Both the velocity vectors and profiles are entirely modified because of the presence of the electromagnetic field, as observed from the velocity vectors and patterns in Figs. 1(b) and (c). When the electromagnetic field is applied to the semi-continuous casting process, the flow direction in the melt pool is reversed and a small circulation is produced near the solidification front at the center of the billet. In addition, compared with that in the convection DC casting, the maximum velocity is increased by about five times and its location is moved from the inlet region to the contact position between the melt and the mold. The phenomena are commonly explained by the forced convection resulting from the rotational component of the electromagnetic force. This fluid flow must result in the temperature profiles in Fig. 1(a). As seen from the temperature profiles in Fig. 1(a), the distribution of the temperature field has been markedly modified. Firstly, it is observed that the temperature contours in the right part are shifted upwards relative to the left part, which must result in the sump shape being entirely modified and the sump depth being remarkably reduced. In addition, compared with that in the absence of the electromagnetic field, the temperature in the bulk liquid is lower and more uniform in the presence of the electromagnetic field. The reason for the great modification of the temperature field is the vigorous forced convection induced by the electromagnetic stirring and the increased heat flux along the longitudinal direction due to the vigorous forced convection in the solidification front. As explained the reason in detail, in the conventional DC casting, the melt with a high temperature reaches firstly the solidification front after the melt is poured into the melt pool from the inlet region, and then the contact region between the melt and the mold due to the thermal buoyancy, therefore, the sump depth is increased. In addition, because the flow velocity in the sump pool is very small, the heat transfer of the melt within the sump depends mainly on the conductive heat transfer, which results in uneven temperature distribution in the melt pool. However, in the LFEC process, due to the electromagnetic field action, the melt with high temperature reaches firstly the contact region between the melt and the mold along the free surface and its temperature is decreased as soon as it is poured into the melt pool, and then the melt cooled by the mold reaches the solidification front, which must result in the temperature at the solidification front being decreased and the sump depth becoming very shallower. In addition, the heat transfer manner in the melt pool is mainly the conductive and convective heat transfer due to the vigorous forced convection induced by the electromagnetic stirring, therefore, the uniform temperature distribution within the sump occurs (Fig. 1(a)).
Table 1 Casting process parameters in DC casting and LFEC processes

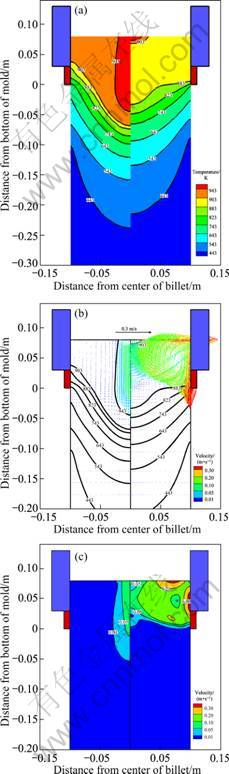
Fig. 1 Comparison of calculated results in conventional DC casting and LFEC processes: (a) Temperature profiles; (b) Velocity vectors with temperature profiles; (c) Velocity patterns
Figure 2 shows the stress and strain profiles in the billets in DC casting and LFEC processes, respectively. It is found that the stress and strain generated in the DC casting process are larger than those in LFEC process, which results from the temperature field modified by applying electromagnetic field. Further, when electromagnetic field is applied to casting process, the temperature contours shift upwards and the temperature difference is induced, which results in the cast stress and plastic strain induced remarkably in the casting process.
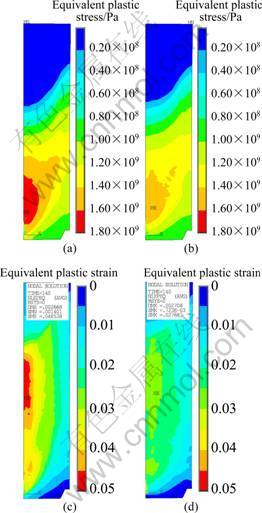
Fig. 2 Equivalent plastic stress (a, b) and strain (c, d) profile in billets in DC casting (a, c) and LFEC (b, d) processes
3.2 Effect of electromagnetic field on microstructure
Figures 3(a) and (b) show the microstructures of the billets cast by the conventional DC casting and LFEC processes, respectively. It is observed that the microstructure of the billets cast by the conventional DC casting process is usually coarse dendritic structure in the absence of the master alloy, but that in the LFEC process is very fine equiaxed grain structure. From the present investigation, the reasons of generating the fine equiaxed grain structure are as follows.
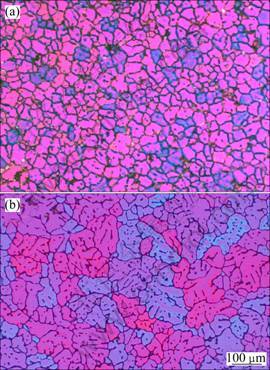
Fig. 3 Microstructures of LFEC and DC billets: (a) LFEC, d200 mm billet; (b) DC, d200 mm billet
1) As shown in Fig. 1(a), the temperature in the sump pool is very uniform and is lower than the liquidus temperature in the presence of electromagnetic field, which must result in the high undercooling and low temperature gradient. As seen from the temperature profile in Fig. 1(a), the whole melt within the sump keeps the large undercooling state, which must increase the nucleation rate and number. Therefore, such uniform temperature field generated by the electromagnetic stirring is one of the main reasons for obtaining the fine equiaxed structure of the billet cast in the LFEC process.
2) As given in Fig. 1(b), due to the vigorous forced convection caused by the electromagnetic stirring, the dendrite fragments are detached from the solidification front, the mold and the free surface of the melt. The causes of the dendrite detachment include dendrite arm fracture due to shearing action, dissolution of dendrite arms and the separated grain from the mold and the free surface of the melt. When these fragments are detached into the sump and move within the sump with the melt flow, each of them will all become a crystal nucleus. It is reason for such phenomenon that these fragments will survive and not be remelted due to the melt as the large undercooling state and the low thermal gradient when they move freely in the melt pool, and then they are captured by the high viscous melt or the dendritic net at the solidification front and form a new nucleus when they sedimentate at the solidification front, which cannot be observed in the conventional DC casing process. Therefore, the vigorous forced convection induced by the electromagnetic field can promote the formation of the fine equiaxed grain structure of the billet.
3.3 Effect of electromagnetic field on crack
The photographs of DC and LFEC billets are shown in Fig. 4. It is found that the crack is formed in DC casting process; however, the billet without crack defects is obtained in LFEC process. In order to study the crack, the numerical method was used in this work. Firstly, a criterion for crack occurring must be built. In this work, a cracking damage index (CDI) is as follows:
(1)
where, εe and εf are the equivalent plastic strain and fracture strain at the different temperatures, respectively. The crack can occur when CDI is more than 1, contrariwise, the crack cannot occur.
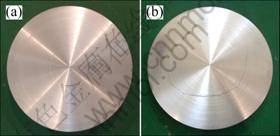
Fig. 4 Photographs of DC and LFEC billets: (a) LFEC, d200 mm billet; (b) DC, d200 mm billet
The coordinate, temperature and equivalent plastic strain when the maximum CDI (CDI, Max) generates in the DC casting and LFEC processes, are listed in Table 2. Corresponding time and location are called as the dangerous time and node, respectively.
It is found that the crack occurs in DC casting process but in LFEC process based on the criterion used above. Further, the reasons why applying the electromagnetic field can retrain the crack occurring are as follows.
Table 2 Calculated results of maximum cracking damage index

1) The maximum equivalent plastic strain is reduced by applying electromagnetic field. Figure 5 shows the equivalent plastic strain and temperature profile on the cross-section including the dangerous node at the dangerous time in DC casting and LFEC processes. It is observed in Figs. 5(c) and (d) that the dangerous node moves toward the border of the billet because of applying the electromagnetic field. In addition, the maximum equivalent plastic strain (0.031 3) in DC casting process is larger than that (0.022 4) in LFEC process because the temperature difference between the inner and outer of billet, which is because of the elevated isothermal line in the center of billet induced by applying electromagnetic field. As shown in Figs. 5(a) and (b), the temperature differences between the inner and outer of billet are 298.616 2 K and 256.802 2 K, respectively. Therefore, applying electromagnetic field in the casting process can reduce the casting stress and the driver force for the crack occurring remarkably.
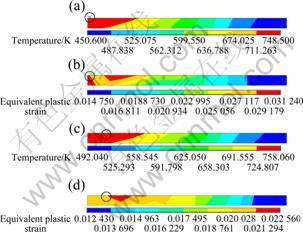
Fig. 5 Calculated results on cross-sections including dangerous position: (a) Temperature profile in DC process; (b) Equivalent plastic strain in DC process; (c) Temperature profile in LFEC process; (d) Equivalent plastic strain in LFEC process
2) The stress state at the dangerous node is modified by applying electromagnetic field. The calculated results of principle stress on the cross-sections including the dangerous node are shown in Figs. 6(a) and (b). It is found that the maximum principle stress direction in DC casing process is circumferential but that in LFEC process is radial, which results from the difference of the contraction and contractive restriction in three directions in the casing process induced by the modified temperature field after applying electromagnetic field. Moreover, Figs. 6(c) and (d) show the principle stress status on the dangerous nodes in DC casting and LFEC process. It is found that the principle stress status in DC casting process is the tensile stress in three directions but that in LFEC is the tensile in two directions and the compression stress in one direction. It is known that the crack occurring is easier for the tensile in three directions than in two directions. Therefore, the crack occurring is restrained remarkably by applying electromagnetic field.
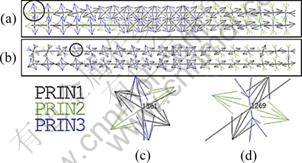
Fig. 6 Calculated results of principle stress on cross-section including dangerous position in DC (a) and LFEC (b) processes, principle stress status on dangerous position in DC (c) and LFEC (d) process: PRIN1—The first principle stress; PRIN2—The second principle stress; PRIN3—The third principle stress
4 Conclusions
1) Compared with the absence of electromagnetic field, the flow patterns in the sump pool were remarkably modified and the vigorous forced convection was produced in the presence of electromagnetic field. That is, the inverse flow direction and the higher flow velocity were found during the LFEC process.
2) The uniform temperature field and the low temperature gradient in the sump pool were observed during the LFEC process. In addition, it was found that the isothermal lines were shifted upward and the sump depth was remarkably reduced.
3) The stress and plastic deformation generated in LFEC process were much smaller than those in the conventional DC casting.
4) The microstructure of the billet was refined remarkably and the crack in the billets was eliminated in LFEC process because of modification of the macro-physical fields induced by the application of low frequency electromagnetic field. Therefore, LFEC process is an effective approach for producing the super-high strength Al-10Zn-2.3Mg-2.4Cu-Zr aluminum alloy.
References
[1] IMMARIGEON J P, HOLT R T, KOUL A K, ZHAO L, WALLACE W, BEDDOES J C. Lightweight materials for aircraft applications [J]. Materials Characterization, 1995, 35(1): 41-67.
[2] HEINZ A, HASZLER A, KEIDEL C, MOLDENHAUER S, BENEDICTUS R, MILLER W S. Recent development in aluminium alloys for aerospace applications [J]. Materials Science Engineering A, 2000, 280(1): 102-107.
[3] WILLIAMS J C, STARKE E A Jr. Progress in structural materials for aerospace systems [J]. Acta Materialia, 2003, 51(19): 5775-5799.
[4] WANG Tao, YIN Zhi-min. Research status and development trend of ultra-high strength aluminum alloys [J]. Journal of Rare Metals, 2006, 30(2): 197-202.
[5] BOENDER W, BURGHARDT A. Application of fracture mechanics to the DC casting of high-strength aluminium alloys [C]// HOWARD J. Proceedings of the 5th Decennial International Conference on Solidification Processing. Great Britain: University of Sheffield, 2007: 714-718.
[6] NAGAUMI H, UMEDA T. Study of crack sensitivity of 6××× and 7××× aluminum alloys [J]. Materials Science Forum, 2003, 426-432: 465-470.
[7] NAGAUMI H, SUZUKI S, OKANE T, UMEDA T. Effect of iron content on hot tearing of high-strength Al-Mg-Si alloy [J]. Materials Transaction, 2006, 47(11): 2821-2827.
[8] NAGAUMI H, SUVANCHAI P, OKANE T, UMEDA T. Mechanical properties of high strength Al-Mg-Si alloy during solidification [J]. Materials Transaction, 2006, 47(12): 2918-2924.
[9] SUYITNO W H, KOOL L, KATGERMAN L. Hot tearing criteria evaluation for direct-chill casting of an Al-4.5 pct Cu alloy [J]. Metallurgical and Materials Transactions A, 2005, 36(6): 1537-1546.
[10] ESKIN D G, KATGERMAN L. A quest for a new hot tearing criterion [J]. Metallurgical and Materials Transaction A, 2007, 38(7): 1511-1519.
[11] EKIN D G, SUYITNO W H, KATGERMAN L. Mechanical properties in the semi-solid state and hot tearing of aluminum alloys [J]. Progress in Materials Science, 2004, 49: 629-711.
[12] DONG Jie, CUI Jian-zhong, BAN Chun-yan, LIU Xiao-tao. Effect of low frequency electromagnetic casting on the castability, microstructure, and tensile properties of DC cast Al-Zn-Mg-Cu alloy [J]. Metallurgical and Materials Transactions A, 2004, 35(8): 2487-2494.
[13] DONG Jie, CUI Jian-zhong. Effect of low-frequency electromagnetic field on microstructures and macrosegregation of Φ270 mm DC billets of an Al-Zn-Mg-Cu-Zr alloy [J]. Materials Letters, 2005, 59: 1502-1506.
[14] ZHANG Hai-tao, NAGAUMI H, ZUO Yu-bo, CUI Jian-zhong. Coupled modeling of electromagnetic field, fluid flow, heat transfer and solidification during low frequency electromagnetic casting of 7xxx aluminum alloys: Part I. Development of a mathematical model and comparison with experimental results [J]. Materials Science and Engineering A, 2007, 448(3): 177-188.
[15] ZHANG Hai-tao, NAGAUMI H, CUI Jian-zhong. Coupled modeling of electromagnetic field, fluid flow, heat transfer and solidification during low frequency electromagnetic casting of 7xxx aluminum alloys: Part II. The effects of electromagnetic parameters on casting processes [J]. Materials Science and Engineering A, 2007, 448(3): 189-203.
低频电磁铸造超高强铝合金铸锭
张海涛,崔建忠
东北大学 材料电磁过程研究教育部重点实验室, 沈阳 110004
摘 要:通过使用数值模拟和实验相结合的方法,研究低频电磁场对铝合金半连续铸造过程中宏观物理场与铸锭的组织和裂纹的影响;比较低频电磁铸造和DC铸造过程的宏观物理场。结果表明:应用电磁场可以完全改变熔体的流动方向,加快流动速度,均匀熔池内熔体温度,降低温度梯度,提升等温线,减少液穴深度和铸造应力及塑性变形;低频电磁铸造还可以明显细化铸锭的微观组织和消除铸造裂纹,其原因是低频电磁场改变了宏观物理场。
关键词:超高强铝合金;低频电磁铸造;DC铸造;宏观物理场;裂纹;微观组织
(Edited by YANG Hua)
Foundation item: Project (2005CB623707) supported by National Basic Research Project of China
Corresponding author: ZHANG Hai-tao; Tel: +86-24-83681431; E-mail: haitao_zhang@epm.neu.edu.cn
DOI: 10.1016/S1003-6326(11)60985-0