
Deformation behavior of TC1 titanium alloy sheet under double-sided pressure
WANG Zhong-jin(王忠金), SONG Hui(宋 辉),WANG Zhe(王 哲)
School of Materials Science and Engineering, Harbin Institute of Technology, Harbin 150001, China
Received 27 February 2007; accepted 19 June 2007
Abstract: In order to investigate the influence of normal stress through thickness on the formability of sheet metal, the viscous pressure bulge(VPB) tests of an annealed TC1 titanium alloy sheet were carried out under two different conditions: double-sided pressure bulging and conventional single-sided pressure bulging. The automated strain analysis, measurement environment (ASAME) and scanning electron microscope(SEM) were used to study the strain distributions and the fracture morphology of bulged specimens. It is found that thickness strain is increased for double-sided pressure bulging specimens, and the limiting dome height(LDH) of double-sided pressure bulging specimens is increased by 31.8% compared with conventional single-sided pressure bulging specimens. The dimples in fracture surface for double-sided pressure bulging specimens are larger and deeper than those for conventional single-sided pressure bulging specimens. The results indicate that normal stress through thickness is helpful in improving the formability of titanium alloy sheet metal.
Key words: titanium alloy TC1; sheet; bulging; double-sided pressure; formability
1 Introduction
The decrease in aircraft’s mass can not only enhance its flexibility, but also reduce launching costs, therefore, titanium alloys with lightmass and high specific strength are widely used in aeronautics and astronautics applications[1-3], but the titanium alloy sheet usually exhibits limited ductility at room temperature[4]. Although the formability can be improved at elevated temperatures, a manufacturing process at room temperature is always desired for the cost-effective reason. There is a urgent need to seek a method to improve the formability of titanium alloy sheet.
MASANORI et al[5] have described that the formability of double-layer pure aluminum sheet is increased by overlapping. MASASHI et al[6] have studied the formability of pure aluminum-brass clad sheets, in which a pure aluminum sheet and brass sheet are stuck to each other by a binding agent, and find that the formability of the clad sheets is better than that of pure aluminum sheet or brass sheet. MORI and KURIMOTO[7] and FUSAHITO and RYUTAROH[8] have indicated that forming limit of the sandwich sheet can also be improved. It is demonstrated both by experiment and theory analysis that the normal stress through thickness has a significant effect on the formability of sheet metal[9-11]. However, these researches involve in a few materials, for example, pure aluminum, stainless steel, aluminum alloy and brass, and reports about exploring the effect of the normal stress through thickness on stamping formability of titanium alloy sheet are hard to find.
So, it is the objective of our investigation to assess the possibility of improving titanium alloy sheet formability at room temperature by normal stress through thickness, which is provided by the viscous pressure bulging(VPB)[12-15] of TC1 sheet with stainless steel overlapped outside, so as to make it possible that the titanium alloy sheets can be fabricated by cold-forming operations.
2 Experimental
Titanium alloy sheet TC1 (thickness of 1.0 mm) in the annealed state was used as the experimental material for this work, and its normal chemical compositions are listed in Table 1. The dimension of blank for bulging was 180 mm×180 mm. To determine the plastic strain in a deformed specimen, the blanks were first printed with circular grids that would be deformed into ellipses after bulging. The initial diameter of a circle grid was d 3.0 mm, and its diameter accuracy was less than 2%.
Table 1 Chemical compositions of TC1 titanium alloy sheet (mass fraction, %)
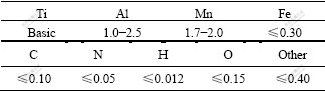
The VPB tests (Fig.1) were performed on viscous pressure forming(VPF) installed in the 4 000 kN press. During the VPB tests, the piston pushes the viscous medium, a semisolid polymer with molecular mass of 500 kg/mol, into the die chamber and pressure was generated within the medium to bulge titanium alloy sheet. In order to produce normal stress through thickness, a overlapped sheet (1Cr18Ni9Ti, 180 mm×180 mm) was laid between titanium sheet and die so that the titanium sheet was formed under double-sided pressure. The VPB tests of TC1 titanium alloy sheet without stainless steel were also carried out in the same setup in order to compare the influence of normal stress through thickness on sheet metal deformation behavior. Each VPB test was repeated three times under the same conditions.
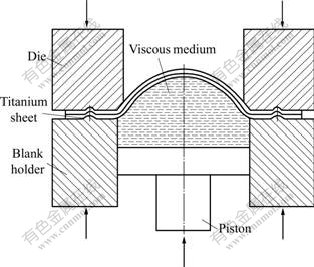
Fig.1 Schematic of tooling used in VPB test
The Automated Strain Analysis and Measurement Environment (ASAME, CamSys Inc., US) (see Fig.2) was used to analysis the strain distribution of bulged specimens with the limiting dome height(LDH). The accuracy of the strain measurement is less than 2%.
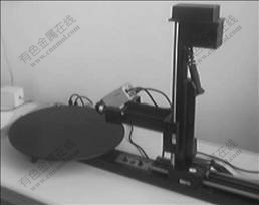
Fig.2 Automated strain analysis and measurement environment
To explore the mechanism of the increase in formability limit of titanium alloy sheet under double-sided pressure, the fractured surfaces of the bulged specimens were observed by SEM. The samples for SEM analysis were cut from the region close to the origin of the fracture.
3 Results
3.1 Limiting dome height(LDH)
Fig.3 shows the specimens after bulging. The LDH of conventional single-sided and double-sided pressure bulging specimens are 23.9 mm and 31.5 mm, respectively. The LDH of double-sided pressure bulging specimens is increased by 31.8% compared with that of conventional single-sided pressure bulging specimens here. This indicates that the formability of titanium alloy sheet is increased under double-sided pressure.

Fig.3 Specimens after bulging: (a) Conventional single-sided pressure bulging; (b) Double-sided pressure bulging
3.2 Strain distribution
The strain distribution curves of different bulged specimens are shown in Figs.4 and 5. The absolute value of thickness strain for double-sided pressure bulging is higher than that for conventional single-sided pressure bulging. In addition, the major strain and minor strain in dome center for double-sided pressure bulging are higher than those for conventional single-sided pressure bulging. This indicates that normal stress through thickness restrains the growth and conjunction of voids, consequently delays failure of titanium alloy sheet during deformation and increases its forming limit.
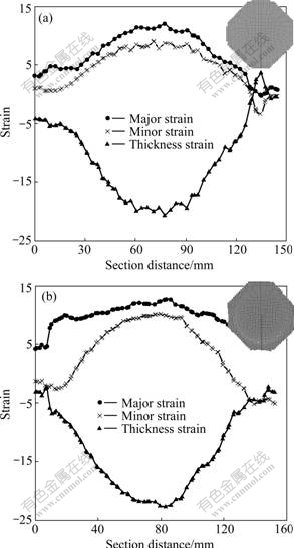
Fig.4 Strain distributions along parallel rolling direction: (a) Single-sided pressure bulging; (b) Double-sided pressure bulging
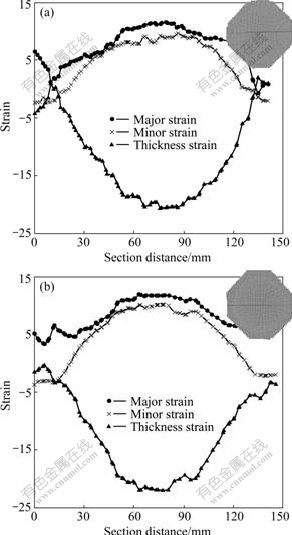
Fig.5 Strain distributions along vertical rolling direction: (a) Single-sided pressure bulging; (b) Double-sided pressure bulging
3.3 Fractography
The fractography indicates that all of the TC1 bulged specimens fracture with the fracture surface characterized by dimples (see Figs.6 and 7). There are longer and narrower furrows (see Fig.6(a)) on the fracture surface of conventional single-sided pressure bulging specimens, and the dimples are shallower and smaller (see Fig.6(b)). The fracture surface of double-sided pressure bulging specimens is much smoother (see Fig.7(a)) with lager and deeper dimples (see Fig.7(b)) observed. The analysis of fractography shows that the crack propagation is faster without intensively plastic deformation during conventional single-sided pressure bulging processes, and each dimple undergoes heavily plastic deformation under double- sided pressure.
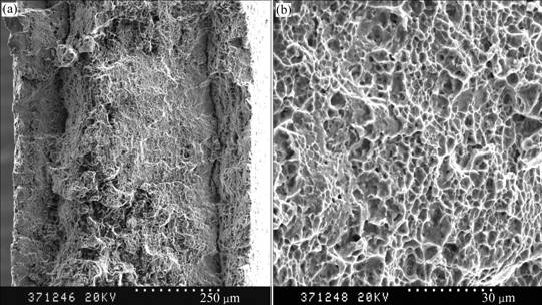
Fig.6 Fracture surfaces of conventional single-sided pressure bulging specimens
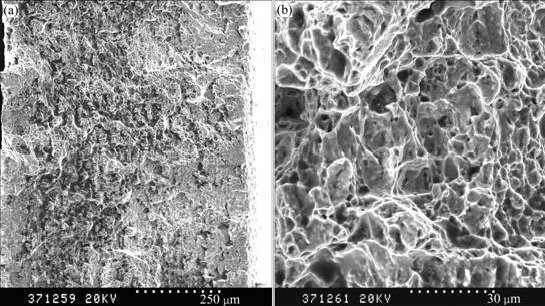
Fig.7 Fracture surfaces of double-sided pressure bulging specimens
4 Discussion
The main reason for improving formability of sheet metal by hydrostatic pressure is attributed to restrained microcrack from propagating[16] and necking[10].
Many defects, such as microcrack, cavity and void can always be produced in TC1 sheets during the plastic deformation processes. Because the magnitude and direction of the microcracks are random, there must be some microcracks that propagate easily under biaxial tensile stress conditions. For conventional single-sided pressure bulging, these easily propagated microcracks deepen and connect each other with increase in the plastic deformation, so as to result in fractured. In double-pressure bulging process, because hydrostatic pressure can restrain the microcracks from propagation, the degree of developing of micro-cracks is comparatively mild, which avoids faster propagation of some micro-cracks, so the plasticity of titanium alloy sheet can be improved. It is consistent with the results of bulging test and strain analysis.
Above mechanism is confirmed by the SEM morphology of the fracture surface. The reason for the presence of longer and narrower furrows on the fracture surface is the faster growth and linkage of some microcracks under conventional single-sided pressure bulging (Fig.6(a)). On the contrary, the fracture surface of double-pressure bulging is very smooth (Fig.7(a)).
Furthermore, it is well known that the fracture in metals often initiates at material or geometric inhomogeneities that are subject to tensile load conditions. The introduction of compressive normal stress components tends to reduce the tensile loads acting on locations with material or geometric inhomogeneities. Therefore, the compressive hydrostatic component σ3 of the stress field can restrain necking in sheet metal, accordingly increasing the forming limit strains. It can be expressed as[10]

where n is the strain hardening coefficient used in the power law hardening rule; β is the ratio of in-plane minor strain to in-plane major strain; γ is the ratio of σ3 to σ1 (σ3 must be less than or equal to zero); α is the ratio of in-plane minor stress to in-plane major stress. According to this expression, the forming limit strains increases with increasing σ3.
The macroscopic expression of the normal stress through thickness restraining necking in sheet metal shows that the LDH and absolute value of thickness strain increases.
5 Conclusions
1) Under double-sided pressure, the absolute value of thickness strain for bulged specimens of TC1 titanium alloy sheets increases and its distributions become uniform.
2) The mechanism of which double-sided pressure increases the plasticity of titanium alloy sheet at room temperature is that the hydrostatic pressure restrains the microcracks from propagation and reduces nonequilibrium developing for the microcracks, then delays the failure of titanium alloy sheet metal and increases its formability.
3) The double-sided pressure forming technique can improve the formability of TC1 titanium alloy sheet, and provides a new way to cold forming for titanium alloy sheet.
References
[1] HANSON B H, KEARNS M W. Properties and applications of titanium sheet [J]. Sheet Metal Industries, 1982, 59(12): 877-878.
[2] PEACOCK D K. Aerospace applications for titanium [J]. Sheet Metal Industries, 1988, 65(8): 406, 408.
[3] KOSAKA Y, STEPHEN P, FALLER K. Newly developed titanium alloy sheets for the exhaust systems of motorcycles and automobiles [J]. JOM, 2004, 56(11): 32-34.
[4] SONG Hui, WANG Zhong-jin, GAO Tie-jun. Effect of high density electropulsing treatment on formability of TC4 titanium alloy sheet [J]. Trans Nonferrous Met Soc China, 2007, 17(1): 87-92.
[5] MASANORI K, NOBUKAZU H, YASUSHI K. Improvement of pure stretch ability by overlapping sheet metals [J]. Journal of the JSTP, 2001, 42(43): 328-332.
[6] MASASHI H, KAZUYOSHI K. Press forming of clad sheets [J]. Journal of the JSTP, 1985, 26(291): 385-393.
[7] MORI T, KURIMOTO S. Press-formability of stainless steel and aluminum clad sheet [J]. Journal of Materials Processing Technology, 1996, 56: 242-253.
[8] FUSAHITO Y, RYUTARO H. Forming limit of stainless steel and clad aluminum sheet under plane stress condition [J]. Journal of Materials Processing Technology, 1997, 63: 66-71.
[9] ABDEL-RAHMAN M. Determination of workability curves using two mechanical tests [J]. Journal of Materials Processing Technology, 1995, 51: 50-63.
[10] SMITH L M, AVENRILLB R C, LUCASC J P. Influence of transverse normal stress on sheet metal formability [J]. International Journal of Plasticity, 2003, 19: 1567-1583.
[11] MATIN P H, SMITH L M. Practical limitations to the influence of through-thickness normal stress on sheet metal formability [J]. International Journal of Plasticity, 2005, 21(4): 671-690.
[12] WANG Xin-yun, WANG Zhong-jin, WANG Zhong-ren. Numerical simulation of aluminum alloy ladder parts with viscous pressure forming [J]. Trans Nonferrous Met Soc China, 2003, 13(2): 391-397.
[13] WANG Z J, LIU J G, WANG X Y. Viscous pressure forming(VPF): State-of-the-art and future trends [J]. Journal of Materials Processing Technology, 2004, 151: 80-87.
[14] GERHARD G, WU H C, GRACIUS N, ALTAN T. Determination of flow stress for sheet metal forming using the viscous pressure bulge(VPB) test [J]. Journal of Materials Processing Technology, 2004, 146: 1-7.
[15] MUSTAFA A, JIANG H, SRIKANTH K, ALTAN T. Hydroforming of sheet metal using viscous pressure forming(VPF) dome test [J]. Journal of Materials Processing Technology, 2004, 146: 97-107.
[16] HUANG Ke-qin, YANG Jie. The physical foundation of plastic deformation [M]. Beijing: Metallurgical Industry Press, 1989. (in Chinese)
Corresponding author: WANG Zhong-jin; Tel: +86-451-86418643; Fax: +86-451-86413786; E-mail: wangzj@hit.edu.cn
(Edited by LI Xiang-qun)