
Component modification of steel slag in air quenching process to improve grindability
ZONG Yan-bing(宗燕兵), CANG Da-qiang(苍大强), ZHEN Yun-pu(甄云璞),
LI Yu(李 宇), BAI Hao(白 皓)
Key Laboratory of Ecologic & Recycle Metallurgy, University of Science and Technology Beijing,
Beijing 100083, China
Received 10 August 2009; accepted 15 September 2009
Abstract: A new solution called component modification in-process was introduced to the difficult grinding of air quenching steel slag by a series of experiments. The results show that the fly ash added into the molten steel slag before air quenching can more effectively improve the slag’s grindability than milltailings, which is the other modification agent tested under the same conditions. The role of fly ash is strengthened as its proportion increases, although the degree of promotion is gradually reduced. As a result of the reaction between fly ash and steel slag at high temperature, some new mineral phases and vitreous bodies with fine grindability promote the slag grinding easily. This work is helpful to making a comprehensive utilization of steel slag and maximize its economic efficiency in China.
Key words: steel slag; component modification in-process; air quenching; grindability; particle distribution
1 Introduction
At present, processing technology of steel slag is developing to make slag granulate easily, to disappear free calcia as far as possible, to separate scrap from slag conveniently, and to make a comprehensive utilization of tailings to reach 100% in order to maximize the economic efficiency and environmental benefits[1-4]. The main chemical compositions of steel slag are CaO, Fe2O3, SiO2, some MgO and the main phases are C3S, C2S and periclase, etc. Because of its high alkalinity, it is difficult to form glassy phases in steel slag[5-6]. Air quenching of steel slag is a process to use high-pressure air to cool molten steel slag from high-temperature rapidly to form small slag particles. Due to small particle size uniformity, the following coarse crushing process cannot be adopted, which has a certain advantage to reduce energy consumption[7-8]. What’s more, the slag particle size can be controlled by adjusting parameters of air quenching process. β-C2S is the main calsil in air quenching steel slag with granular patterns or the flowers-like patterns. The patterns of C3S are like plate or strip[9]. There are a large number of aphanitic ferrite on the edge of interface and some well-developed monocalcium ferrite locally[9-11]. Based on the results of analysis of mineral phase, the existence of calsil in air quenching slag makes it hydraulic set. After air quenching treatment[12], there is a relatively small number free calcia with instability. It is a major problem faced in the application of steel slag that the hard slag is not easy to be crushed[13-15]. It is obvious that there are very few documents in which in-depth study on slag grindability is given, especially, using component modification to improve the grindability of slag in-process is difficult to be found in literatures. In this work, a new solution method to the slag grinding was introduced. The basic idea of the experiment is that adding modification agent to the molten slag before quenching can change the slag phase composition and improve its grindability.
2 Experimental
The capacity of the slag tundish used in air quenching slag production was about 3.5 t in Ma Steel Company in China where the hot tests were done. Before experiment a layer of modification agent (50 kg) was put at the bottom of the slag tundish. 1 t of high-temperature slag (about 1 650 ℃) was poured into the tundish from the slag ladle. This course lasted not more than 40 s. Because of the flow and scouring effect of slag in molten condition, the high-temperature slag and modification agent were mixed well with reaction developing. Air quenching was subsequently done to the mixed slag. When the air quenched slag was cool, several samples were taken out and crushed in a ball mill with the same parameters. The evaluation method of grindability in this work was that the more the proportion of fine-grained samples is, the better the grindability. In addition, SEM was used to analyze the samples. To compare the modification effect, a blank experiment without modification was also done each time. In order to make chemical components of each slag sample is almost the same before modification, all the experiments were done when the BOF was used to produce the same type of steel.
3 Results and discussion
3.1 Effect of two kinds of modification agent
Fly ash and milltailings are two kinds of component modification agents tested in this work. The chemical composition of modification agents is shown in Table 1. The component of slag without modification is also given. The samples after quenching were broken first by general crushing machine. 500 g crushed slag within 0.60-1.18 mm in diameter screened by standard sieves was gotten. The slag was put into the ball mill (Q M-SX5) where 3 kg small steel balls with 6 mm in diameter were loaded. The rotation speed was 140 r/min, the crushing time was 2 h, and the direction of rotation was single. Each sample was weighed after grinding, and the results are given in Table 2.
It can be seen from Table 2 that under the same milling conditions, for the particles of 300-600 μm and 600-1 180 μm in diameter, the proportion in air quenching slag without modification is more than that of the modified samples with 5% fly ash or milltailings added. For particle size of 150-300 μm, 75-150 μm and <75 μm in diameter, there is much larger proportion in both 5% fly ash samples and 5% milltailings samples than that in the original slag samples. The big proportion of fine-grained level shows the addition of fly ash and milltailings improves the grindability of the air quenching steel slag.
The results of the volume under 150 μm sieve for the 3 kinds of samples are shown in Fig.1. As can be seen from Fig.1, under the same milling conditions, the sample with 5% fly ash added has more particles whose size is less than 150 μm than the other two kinds of samples. More fine particles mean better milling effect. So it can be also drawn that the order of grindability from low to high for the 3 samples is as follows: the air quenching slag without modification, the sample with 5% milltailings added, the slag sample with 5% fly ash. That is, the promotion of fly ash can effectively improve the grindability of air quenching slag.
When the addition of fly ash was adjusted to 9%, a similar experiment was also completed. The particle size distribution of the slag modified by 9% fly ash and the original slag is given in Fig.2.
It can be seen from Fig.2 that in the region of fine particle size, such as particle size less than 30 μm, the volume of each size in the modified slag is significantly greater than that of the original slag. On the contrary, in the coarse particle region, for example, larger than 50 μm, the content of each size in modified sample is less than that of the original slag.
Table 1 Composition of modification agent and slag without modification (mass fraction, %)

Table 2 Particle size distribution of air quenching slag with different component modification agents
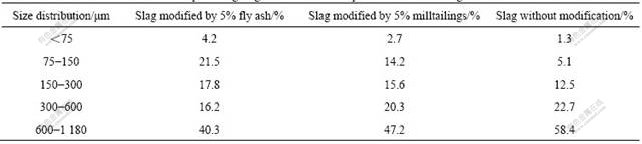
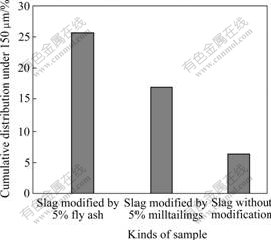
Fig.1 Grindability contrast of air quenching steel slag with different additives under 150 μm sieve
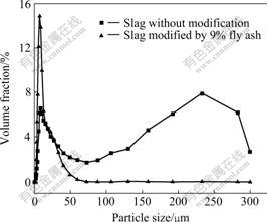
Fig.2 Particle volume fraction of slag modified by 9% fly ash and original slag
3.2 Effects of the addition ratio of fly ash
In order to obtain the effect of the amount of fly ash addition on the grindability of steel slag, a series of experiments were carried out in laboratory. The course of the experiment is shown in Fig.3.
Experimental analysis indicates that the more the amount of fly ash is added, the more easily the samples are
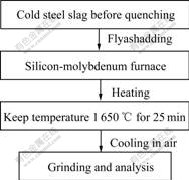
Fig.3 Flowchart of experiments in laboratory
ground. This was mainly because the reaction between steel slag and fly ash is promoted by the great amount of mixing of fly ash, thus the grindability is improved greatly. Fig.4 gives the cumulative undersize distribution of steel slag with different ratios of fly ash added.
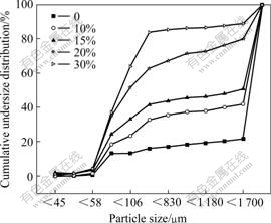
Fig.4 Cumulative undersize distribution of steel slag with different ratios of fly ash
As can be seen from Fig.4, under the same grinding conditions, the proportion of fine particles (less than 75 μm) of original steel slag is 13.3%. After 20% fly ash is added, the value is 35.21%, and it turns to 36.9% while the proportion of additive is 30%. For the particles less than 250 μm, the percentage share of the accumulated slag is from 16.1% to 83.8% when the amount of fly ash changes from 0 to 30%. All this indicates that with the increase of fly ash, the proportion of fine-grained powder of steel slag grows. Therefore, it can be concluded that, the fly ash can improve the grindability of steel slag greatly. Simultaneously this role is strengthened as the proportion of fly ash increases.
For the particle size of less than 75 μm and 106 μm, Fig.5 shows the relevant cumulative percentage under different ratios of fly ash added. When the ratio of fly ash changes from 20% to 30%, the increasing trend of the percentage of particles less than 75 μm is gentle. In sharp contrast, the increasing trend of the percentage of particles less than 106 μm is obvious. This shows that, with the increase of fly ash, the slag’s grindability improves, but the degree of promotion is gradually reduced. Taking into account of the restrictions on the amount of fly ash, the proposed ratio of fly ash is about 10%.

Fig.5 Effects of ratio of fly ash added into steel slag on cumulative undersize distribution of less than 75 μm and 106 μm
3.3 Effect of two adding ways of modification agent
There are two ways to add the fly ash into steel slag, one is called physical mix, and the other is chemical mix. Physical mix is remelting slag and fly ash alone first, then mixing the two air-cooled samples together to the certain proportion. Chemical mix is mixing the fly ash and slag to the certain proportion first, then remelting the mixture together. Comparison of these two ways can tell whether it is the chemical reaction resulting in the substantial increase of grindability for the mixture. It should be noted that all experiments done before are the so-called chemical mix here. Of course, the melting temperature and the proportion of additives are the same for the two ways, as well as the crushing process. In this work, the melting temperature is kept 1 650 ℃ for 25 min, and the cooling medium is air at room temperature. The particle size of the test fly ash is very small, which is mostly less than 75 μm. The ball mill (Q M-SX5) and its parameters are the same as those mentioned in this paper.
From the grinding results (as shown in Fig.6) of the two adding ways above, as to the chemical mix samples, the proportion of fine particles is much larger than that of the physical mix sample. This shows that the good grindability is due to the reaction between fly ash and steel slag taking place at a high temperature, not because fly ash owns fine grindability. In this test, for the modified slag by fly ash, the modification in molten state is not the same as the simple cold mix (physical mix mentioned before) in nature. Modification under high-temperature of the slag changes its composition and structure. This means that a qualitative variety is undergone in the slag.
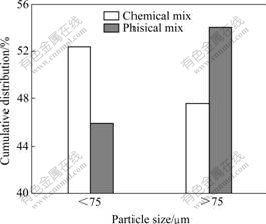
Fig.6 Effects of two mix methods on grindability
3.4 SEM analysis
The change in mineralogical structure before and after modification was analyzed by SEM. For SEM observation, the samples obtained in this work was consolidated with epoxy resin adhesive, and were polished to slices.
The microstructures of the slags are shown in Figs.7 and 8, Tables 3 and 4. For the steel slag samples modified by fly ash, there exist new minerals grammite (CaO?SiO2), a small amount of vitreous body and some metallic iron. A little of ferriferous oxide, monocalcium ferrite and C2S also occurs in the modified samples. The f-CaO is difficult to find basically. The emergence of new mineral phase and vitreous body with fine grindability promotes the slag grinding. The hardness of grammite (CaO?SiO2) is from 4.5 to 5.0, which is less than that of C3S and Fe2O3 (their hardness is 5-6). In addition, the increase of metallic iron in slag improves the magnetic properties, and the rate of magnetic separation in slag can be increased. That is to say, the recovery rate of iron increases, which is beneficial to both the conservation of resources and the use of follow-up products.
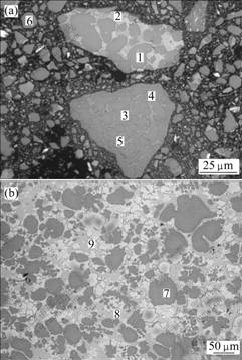
Fig.7 SEM images of slag without fly ash added: 1, 3, 6—3CaO?SiO2; 2, 4, 5—RO; 7—2CaO?SiO2; 8—Ca(FeO2)2; 9—f-CaO
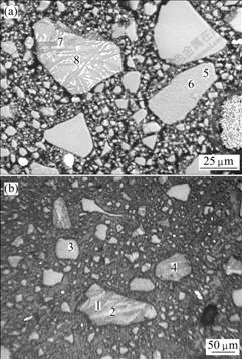
Fig.8 Micrographs of slag with 5% fly ash added: 1, 2, 3, 4—CaO·SiO2; 5, 7—2CaO?SiO2; 6—CaO?FeO?SiO2; 8—RO
Table 3 Mineral phases in steel slag without modification
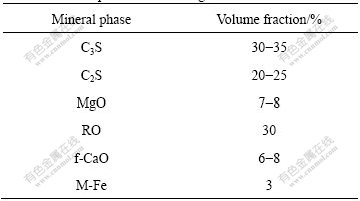
Table 4 Mineral phases in steel slag modified by 5% fly ash added
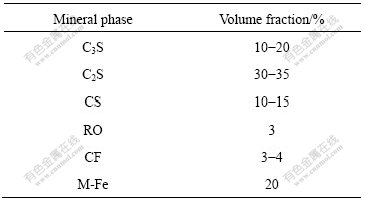
As the main components of fly ash are SiO2 and Al2O3 (as shown in Table 1), the following reaction can take place between fly ash and steel slag at high temperature[16]:
f-CaO +SiO2→CaO·SiO2
2f-CaO +Fe2O3→2CaO·Fe2O3
3f-CaO +Al2O3→3CaO·Al2O3
2f-CaO +SiO2→2CaO·SiO2
C+2Fe2O3→4FeO+CO2
C+2FeO→2Fe+CO2
These reactions change the slag mineral phases, produce the easy grinding phases, decrease the content of f-CaO, and overcome the shortcomings inherent in the performance.
4 Conclusions
1) The fly ash added into the steel slag before air quenching can more effectively improve the slag’s grindability than milltailings under the same conditions. The role of fly ash is strengthened as the proportion of fly ash increases, although the degree of promotion is gradually reduced.
2) The good grindability is a result of the reaction between fly ash and steel slag taking place at a high temperature, not because fly ash owns fine grindability. Modification under high-temperature of the slag changes its composition and structure.
3) In the steel slag samples modified by fly ash there exist new minerals grammite (CaO?SiO2), a small amount of vitreous body. The emergence of new mineral phase and vitreous body with fine grindability promotes the slag grinding easily.
References
[1] ZHANG Tong-sheng, LIU Fu-tian, WANG Jian-wei, LI Yi-kai, ZHOU Zong-hui, CHENG Xi. Recent development of steel slag stability and activating activity [J]. Bulletin of the Chinese Ceramic Society, 2007, 26(5): 980-984. (in Chinese)
[2] MOTZ H, GEISELER J. Products of steel slags an opportunity to save natural resources [J]. Waste Management, 2001, 21(3): 285-288.
[3] SHI Cai-jun. Characteristics and cementitious properties of ladle slag fines from steel production [J]. Cement and Concrete Research, 2002, 32(3): 459-462.
[4] JAIN A K, GUPTA V K, SUHAS B A. Utilization of industrial waste products as adsorbents for the removal of dyes [J]. Journal of Hazardous Materials, 2003, 101(1): 31-42.
[5] ALTUN I A, ISMAIL Y. Study on steel furnace slags with high MgO as additive in Portland cement [J]. Cement and Concrete Research, 2002, 32(8): 1247-1249.
[6] LU Lei, WEN Jin-bao, YAO Qiang. Study on mechano-chemical effect for steel slag [J]. Iron Steel Vanadium Titanium, 2005, 26(2): 39-43. (in Chinese)
[7] QIAN Guang-ren. Actions of alkali content sand pH in the solution on cement strength of steel-slag with lower alkali basicity and a few of clinker [J]. Journal of Southwest Institute of Technology, 1997, 12(4): 17-20. (in Chinese)
[8] WAN Yong-min, ZHANG Shao-ming. Increase the quantity of mineral admixturein cement by mechanochemistry [J]. Journal of Nanjing University of Chemical Technology, 1998, 20(2): 66-68. (in Chinese)
[9] LI Dong-xu, FU Xing-hua, WU Xue-quan. Influence of composite admixture on steel slag cement properties [J]. Journal of Nanjing University of Chemical Technology, 1994, 16(4): 68-72. (in Chinese)
[10] WEN Jin-bao, LU Lei. Influence of powder grinding fineness on steel-ore-slag no-clinker cement properties [J]. Journal of Shenyang Institute of Chemical Technology, 2002, 16(4): 276-279. (in Chinese)
[11] XIAO Qi-zhong. Expansion and its inhibition of steel slag [J]. Journal of the Chinese Ceramic Socity, 1996, 24(6): 635-640. (in Chinese)
[12] HU Dong-feng, WU Zeng-rui. Application of slag wind-crushing technique to 30-ton converter of Shijiazhuang iron and steel plant [J]. Hebei Metallurgy, 1997(1): 36-39. (in Chinese)
[13] DING Xin-bang, ZHAO San-yin, LI Zai-bo, ZHAO Xu-guang, ZHOU Xi-ya. Experimental studies on the grinding characteristic and cementitious activity of pyrolytic converter steel slag [J]. Cement Engineering, 2008(5): 16-18. (in Chinese)
[14] DIPPENAAR R. Industry uses of slag (the use and re-use of iron and steelmaking slags) [J]. Iron and Steelmaking, 2005, 32(1): 35-46.
[15] LIN Hui, WANG Ling, LI Yun-feng. State of the art on work ability and mechanical property of steel slag concrete [J]. Industrial Construction, 2008, 138(S): 867-869. (in Chinese)
[16] WU Shao-peng, XUE Yong-jie, YE Qun-shan. Utilization of steel slag as aggregates for stone mastic asphalt (SMA) mixtures [J]. Build Environment, 2007, 42(6): 2580-2585.
(Edited by CHEN Can-hua)
Foundation item: Project(IRT0708) supported by Program for Changjiang Scholars and Innovative Research Team in University of China (“PCSIRT”); Project(20070008031) supported by the Research Fund for the Dectoral Program of Higher Education of China
Corresponding author: ZONG Yan-bing; Tel: +86-01-62333893; E-mail: zybustb@126.com