稀有金属 2013,37(06),915-921
奥氏体不锈钢表面双辉等离子渗锆改性层的耐蚀性
蔡航伟 高原 马志康 王成磊
桂林电子科技大学材料科学与工程学院
摘 要:
利用双层辉光等离子渗金属技术, 在0Cr18Ni9Ti奥氏体不锈钢表面形成了一层均匀致密连续的渗锆合金层, 利用光学显微镜 (OM) 与扫描电子显微镜 (SEM) 分别观察了试样截面与表面的微观组织, 并对其表面的物相进行了X射线衍射分析;且对不锈钢基材与渗锆合金层分别进行电化学腐蚀性能测试。结果表明:渗锆改性层的组织为柱状晶, 渗锆改性层与基体有一明显分界线, 且与基体呈良好的固态冶金扩散结合, 渗锆改性层的物相主要为:ZrFe2, ZrC;在0.5 mol·L-1HCl溶液、3.5%NaCl溶液、0.5 mol·L-1NaOH溶液中, 不锈钢基材的相对腐蚀速度分别是渗Zr合金层的24.43倍、2.44倍、1.90倍;未处理的不锈钢表面腐蚀较为严重, 而渗Zr合金层表面只出现轻微的局部腐蚀, 可见经渗锆处理后, 不锈钢的耐蚀性有所提高。
关键词:
0Cr18Ni9Ti不锈钢;双辉等离子渗金属;渗锆合金层;耐蚀性;
中图分类号: TG156.8
作者简介:蔡航伟 (1985-) , 男, 河南漯河人, 硕士研究生;研究方向:材料表面改性;高原 (E-mail:gaoyuanguilin@126.com) ;
收稿日期:2013-03-26
基金:国家自然科学基金项目 (51264007) ;国家自然科学基金青年基金 (51201043);广西自然科学基金重点项目 (2010GXNSFD013008);广西科学研究与技术开发科技攻关计划项目 (桂科攻12118020-2-2-1);广西信息材料重点实验室项目 (桂科能1210908-10-Z) 资助;
Corrosion Resistance of Zr-Alloyed Layer on Austenite Stainless Steel by Double Glow Plasma Technique
Cai Hangwei Gao Yuan Ma Zhikang Wang Chenglei
School of Materials Science and Engineering, Guilin University of Electronic Technology
Abstract:
A continuous and compact zirconium modified surface alloying layer was prepared on 0Cr18Ni9Ti austenite stainless steel substrate by double-glow plasma surface alloying technology. The cross-section and surface microstructures of the samples were observed respectively by optical microscope ( OM) and scanning electronic microscope ( SEM) , and the phases of Zr-alloyed layer were analyzed by X-ray diffraction ( XRD) . The electrochemical corrosion experiments were carried out for stainless steel and Zr-alloyed layer respectively. The results showed that the microstructure of Zr-alloyed layer was columnar crystal, and there was an obvious boundary between alloying layer and the matrix. Zr-alloyed layer achieved good solid metallurgical bonding with the matrix, and the phases of Zralloyed layer were mainly ZrFe2, ZrC. The relative corrosion rates of stainless steel were 24. 43, 2. 44 and 1. 90 times of Zr-alloyed layer in 0. 5 mol·L- 1HCl solution, 3. 5% NaCl solution and 0. 5 mol·L- 1NaOH solution, respectively. The surface of unprocessed stainless steels were corroded seriously, but the surface of Zr-alloyed layers only existed slight local corrosion, which indicated that corrosion resistance could be improved after Zr-alloyed layer being formed on 0Cr18Ni9Ti stainless steel.
Keyword:
0Cr18Ni9Ti stainless steel; double-glow plasma surface alloying technology; Zr-alloyed layer; corrosion resistance;
Received: 2013-03-26
0Cr18Ni9Ti不锈钢具有优良的耐蚀性、焊接性及综合力学性能, 在航空航天、化工、原子能等行业中得到了广泛应用, 但其在特定的腐蚀环境中的耐蚀性能有待进一步提高[1]。双层辉光等离子渗金属技术与其他渗金属技术相比, 具有渗速快、渗层成分易于控制、渗层与基体结合强度高、节约合金元素、成本低、容易实现多元共渗、无环境污染等优点[2,3,4]。本文采用双辉等离子渗金属技术, 在0Cr18Ni9Ti不锈钢表面形成渗锆合金层, 利用Zr是强碳化物形成元素, 与C的亲和力强的特点, 在渗层中形成Zr C, 使渗层内的C含量降低, 减少Cr23C6的形成, 抑制因晶界贫Cr而引起的晶间腐蚀倾向, 改善不锈钢表面的耐蚀性。
1 实验
1.1 实验材料
双辉等离子渗锆所用的源极为锆板, 其几何尺寸为:100 mm×50 mm×5 mm (长×宽×厚) , 纯度为99.99%, 试验前将源极打磨清理干净。试样基材为0Cr18Ni9Ti奥氏体不锈钢, 尺寸为35 mm×10 mm×3 mm (长×宽×厚) 。试样化学成分 (%, 质量分数) 为:Cr 17.00~19.00, C≤0.07, Ni 8.00~11.00, Ti 0.05~0.07, Mn≤2.00, Si≤1.00, P≤0.035, S≤0.030, 其余为Fe。装炉前, 需将试样依次经不同型号的水砂纸打磨, 并用抛光机抛光, 再用超声波清洗干净并烘干。
1.2 实验方法
采用DGLT-15型多功能离子化学热处理炉进行渗锆处理, 工艺参数为:极间距25~30 mm, 氩气工作气压30~35 Pa, 保温温度1060℃, 源极与阴极之间的电压差300 V, 保温时间5 h。渗Zr的工作温度通过WDL-31型光电温度计进行测试。渗锆后, 将试样随炉缓冷至室温。采用Carl Zeiss Axio Scope A1型光学显微镜观察渗层金相组织, 用JEOL/JSM-5610LV型扫描电镜观察试样表面形貌, 用Bruker-axs-D8型X射线衍射仪检测渗层物相结构。
采用恒电位法和PS-268A型电化学测量仪进行电化学腐蚀试验, 将试样依次用丙酮、蒸馏水冲洗干净, 试样工作面积为1 cm2, 其余非工作面均用石蜡密封。然后将试样浸入腐蚀液中, 以饱和甘汞电极 (SCE) 作为参比电极, 铂电极作为辅助电极, 参比电极和研究电极之间用盐桥连接, 鲁金毛细管距研究电极1~2 mm, 待稳定10 min后进行阴极和阳极极化, 电位扫描速度为60 m V·min-1, 采用塔菲尔直线外推法, 测定金属的腐蚀电流icorr, 根据法拉第定律计算腐蚀速度, 即v=3.73×10-4M·icorr/n (单位:g·m-2·h-1) , 其中v为腐蚀速度, M为金属原子量, n为金属原子价, icorr为腐蚀电流。
2 结果与分析
2.1 渗Zr合金层的组织形貌及物相
图1为未处理的不锈钢基材的表面形貌, 不锈钢基材经渗Zr处理后的表面形貌与截面金相照片分别如图2与3所示, 由图3可知, 渗层组织为柱状晶, 且与基体间有一明显的界面, 渗层的组织致密、分布连续、无明显的孔隙和裂纹。图4为渗锆合金层的XRD衍射图谱, 可以看出, 渗锆处理后在不锈钢表面形成了Zr C和Zr Fe2的改性层, 这是由于Zr是强碳化物形成元素, 锆的碳化物比铬的碳化物更稳定, 在渗锆过程中Zr可以从铬的碳化物中置换出Cr, 而与C作用形成Zr C。试样表面与渗层的组织致密、分布连续、无明显的孔隙和裂纹。
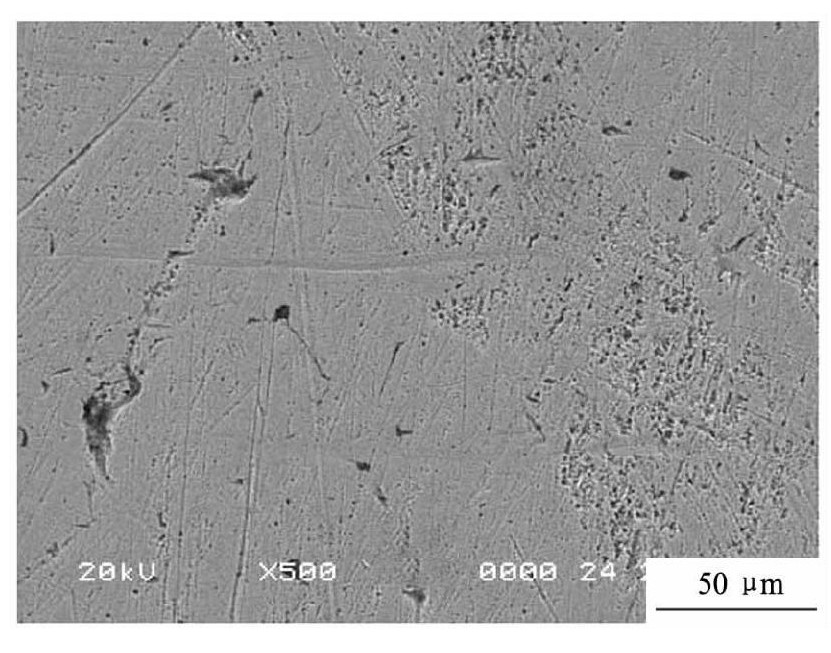
图1 不锈钢基材表面SEM图Fig.1Surface SEM image of stainless steel
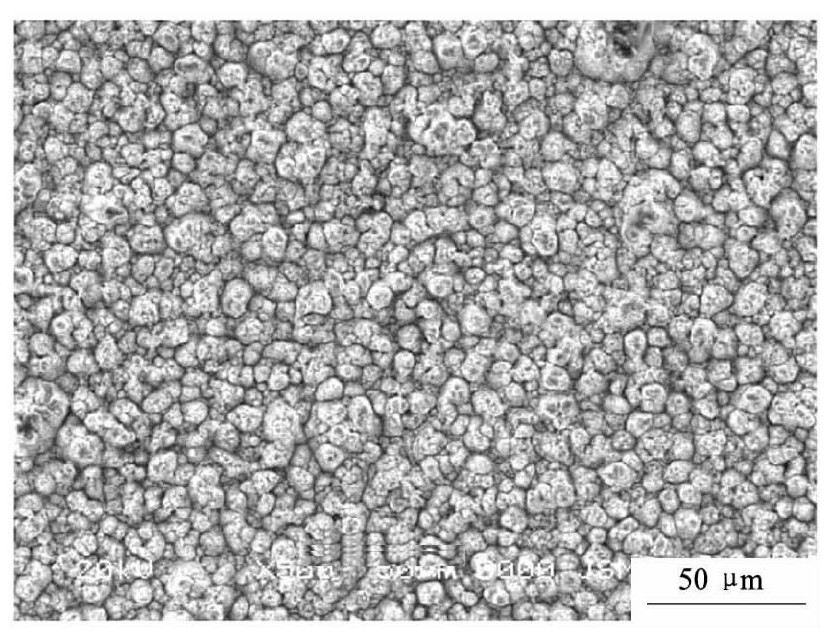
图2 渗锆后表面SEM图Fig.2 Surface SEM image of Zr surface alloying

图3 渗锆合金层金相组织图Fig.3 Microstructure of Zr-alloyed layer
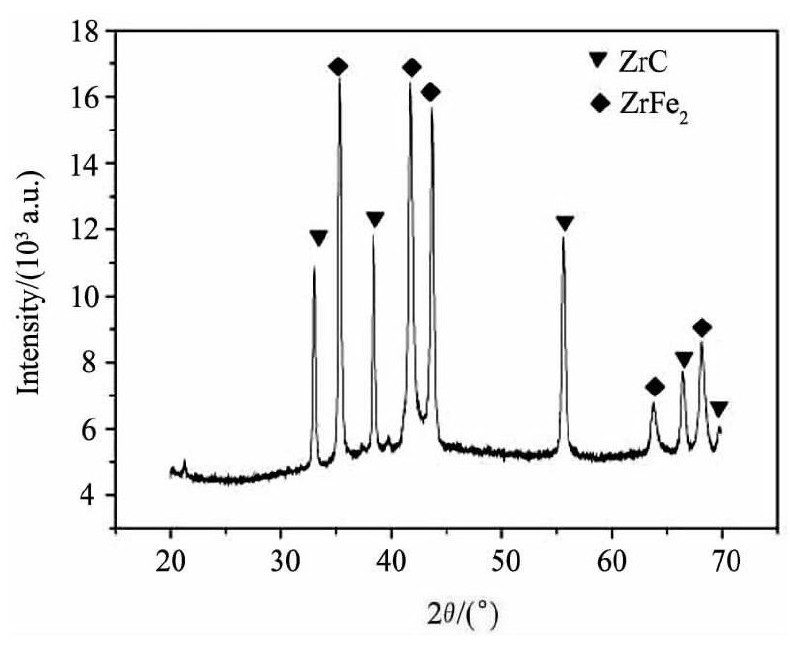
图4 渗锆合金层XRD物相图谱Fig.4 XRD pattern of Zr-alloyed layer
2.2 在0.5 mol·L-1HCl溶液中的腐蚀结果及分析
图5为基材与渗Zr合金层试样在0.5 mol·L-1HCl溶液中的极化曲线, 其自腐蚀电流密度icorr、腐蚀速度及相对腐蚀速度等的计算结果如表1所示。该过程为阴、阳极混合控制的析氢腐蚀。由图5与表1可知, 在阴极极化过程中, 电位升高, 基材的电流密度随之逐渐减少, 当电位升至其自腐蚀电位Ek=-86 m V时进入阳极极化, 之后随着电位升高, 电流密度开始增大。而对于渗Zr试样, 在阴极极化过程中, 渗锆合金层的极化电流密度明显小于不锈钢基材, 且在此过程中随着电位的升高, 其电流密度也逐渐减小。当电位升至自腐蚀电位Ek=-19 m V时, 进入阳极极化, 其自腐蚀电位较基材提高了67 m V, 从热力学角度说明渗Zr试样比基材难发生腐蚀, 之后电位升高, 电流密度随之增大, 出现钝化现象;且渗Zr试样的腐蚀电流密度和腐蚀速度较基体都有所降低, 基材与渗Zr试样的腐蚀速度分别为0.329356, 0.013483g·m-2·h-1, 基材的相对腐蚀速度是渗Zr试样的24.43倍, 从动力学角度分析, 可见渗锆后, 使表面钝化膜变得稳定且致密, 使表面不易发生点蚀与晶间腐蚀, 进一步提高了其耐蚀性。
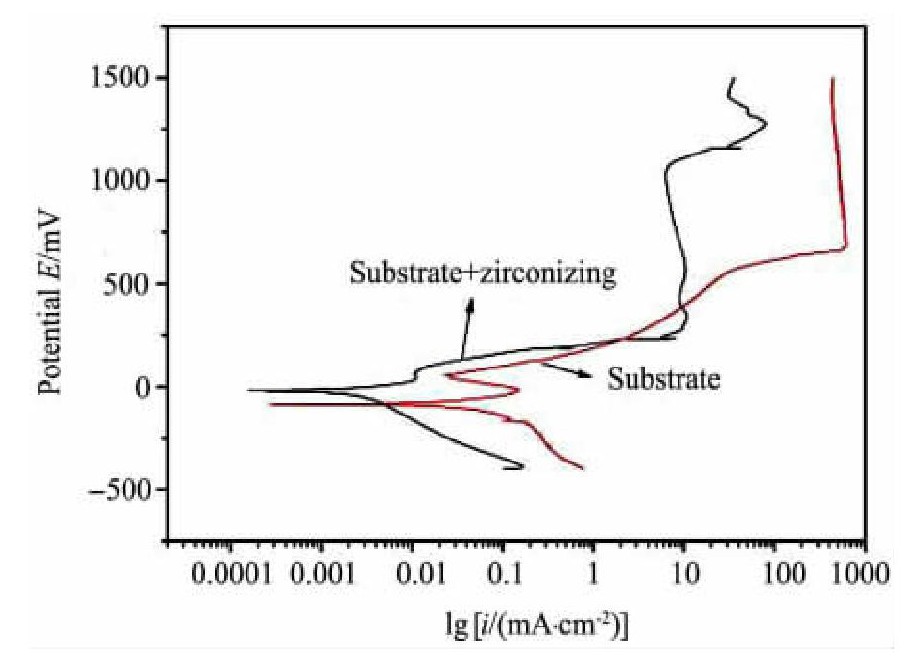
图5 在0.5 mol·L-1HCl溶液中的极化曲线Fig.5Cyclic polarization curves in 0.5 mol·L-1HCl solution
表1 在0.5 mol·L-1HCl溶液中的电化学腐蚀测试结果Table 1Electrochemical measuring results in 0.5 mol·L-1HCl solution 下载原图

表1 在0.5 mol·L-1HCl溶液中的电化学腐蚀测试结果Table 1Electrochemical measuring results in 0.5 mol·L-1HCl solution
图6为未处理的基材与渗锆合金层在0.5 mol·L-1的HCl中的腐蚀形貌, 可见, 由图6 (a) 可以看出, 经HCl腐蚀后, 未处理的基材的腐蚀形式为点蚀和晶间腐蚀;而由图6 (b) 可以看出, 渗锆合金层表面除出现较为细小的点蚀外, 整个表面较为平整, 无太大变化。这是由于不锈钢表面经过渗锆后, 渗锆合金层中合金元素呈梯度分布, 这种分布方式提高了渗锆合金层的耐蚀性;而且由于锆元素的渗入, 当腐蚀时在表面形成了一层致密的氧化锆钝化膜, 也使渗锆合金层的耐HCl腐蚀性较未处理的基材有所提高。
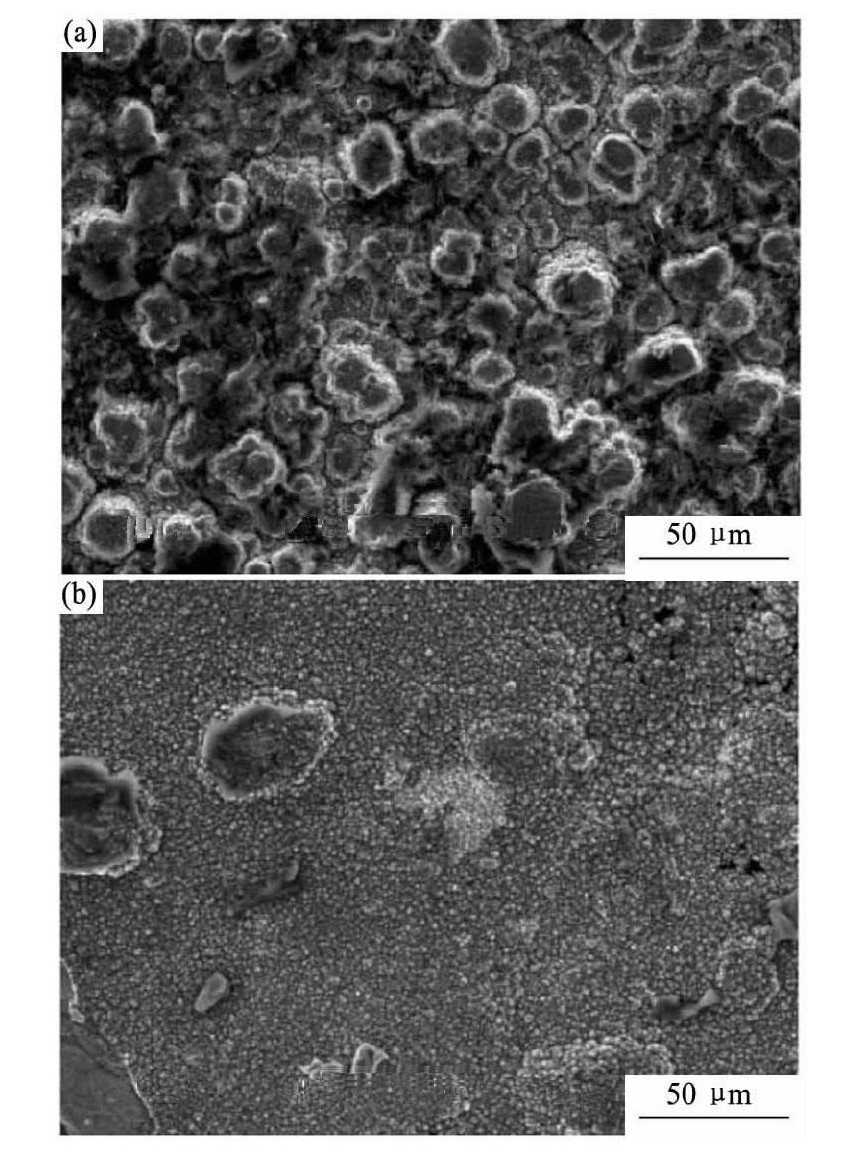
图6 在0.5 mol·L-1HCl中的腐蚀形貌Fig.6 Corrosion morphology in 0.5 mol·L-1HCl solution
(a) Substrate; (b) Zr-alloyed layer
2.3 在3.5%Na Cl溶液中的腐蚀结果及分析
图7为基材与渗Zr合金层试样在3.5%Na Cl溶液中的极化曲线, 其自腐蚀电流密度icorr、腐蚀速度及相对腐蚀速度的计算结果如表2所示。由图7与表2可知, 在阴极极化过程中, 电位升高, 基材的电流密度逐渐降低, 当电位升至其自腐蚀电位Ek=-277 m V时进入阳极极化, 随着电位升高, 电流密度开始增大, 进入活化-钝化过渡区。当电位升至253 m V时, 电流密度增速平缓, 出现钝化现象, 进入稳定钝化区, 表明其具有一定的耐蚀性。
而对于渗Zr试样, 在阴极极化过程中, 随着电位的升高, 其电流密度也逐渐减小。当电位升到自腐蚀电位Ek=-196 m V时, 进入阳极极化, 其自腐蚀电位较基材提高了81 m V, 从热力学角度说明渗Zr试样比基材难发生腐蚀, 之后电位升高, 电流密度随之增大, 进入活化-钝化过渡区。当电位升至214 m V后, 电流几乎保持不变, 出现钝化现象;且渗Zr试样的腐蚀电流密度和腐蚀速度较基体都有所降低, 基材与渗Zr试样的腐蚀速度分别为0.005218, 0.002135 g·m-2·h-1, 基材的相对腐蚀速度是渗Zr试样的2.44倍。从动力学角度分析, 说明锆元素的渗入提高了0Cr18Ni9Ti不锈钢在Na Cl溶液中的耐蚀性。
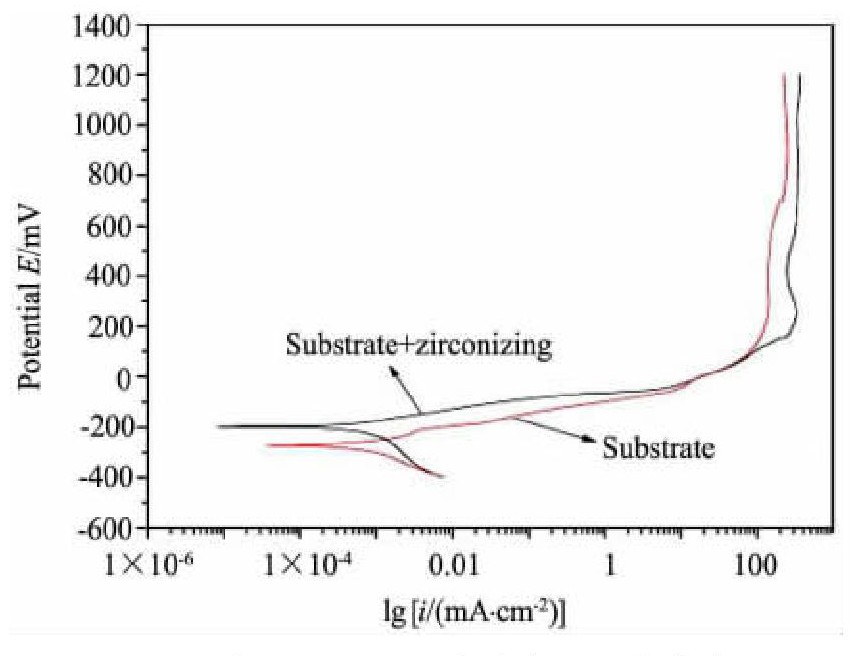
图7 在3.5%Na Cl溶液中的极化曲线Fig.7 Cyclic polarization curves in 3.5%Na Cl solution
表2 在3.5%Na Cl溶液中的电化学腐蚀测试结果Table 2Electrochemical measuring results in 3.5%Na Cl solution 下载原图

表2 在3.5%Na Cl溶液中的电化学腐蚀测试结果Table 2Electrochemical measuring results in 3.5%Na Cl solution
图8为未处理的基材与渗锆合金层在3.5%Na Cl溶液中的腐蚀形貌。由图8 (a) 可以看出, 在3.5%Na Cl溶液中, 未处理的基材腐蚀严重, 不仅有面腐蚀而且存在着小孔腐蚀, 这是由于在Na Cl溶液中存在着半径较小的Cl-。
根据成相膜理论, Cl-通过以下两个方面来影响金属钝化现象:一方面, 当金属与合金尚处于活化态时, 位于电极表面的Cl-会与水分子及OH-等竞争吸附, 延缓甚至阻止钝化膜的形成[5,6,7];另一方面, 当金属步入钝化态在其表面形成固相的钝化膜时, 由于Cl-的易极化性质, 使其容易吸附在溶液与金属氧化物的界面上, 凭借着扩散与电场作用, 使其易穿过钝化膜内极小的孔隙[8,9], 成为钝化膜层内的杂质组分, 这种掺杂作用导致钝化膜层内的离子电导性与电子电导性显著改变, 产生强烈的感应离子导电, 使膜在特定点上保持较高的电流密度并导致阳离子不定向无序移动, 当膜/溶液界面的电场达到某一临界值时, 就会发生点蚀。
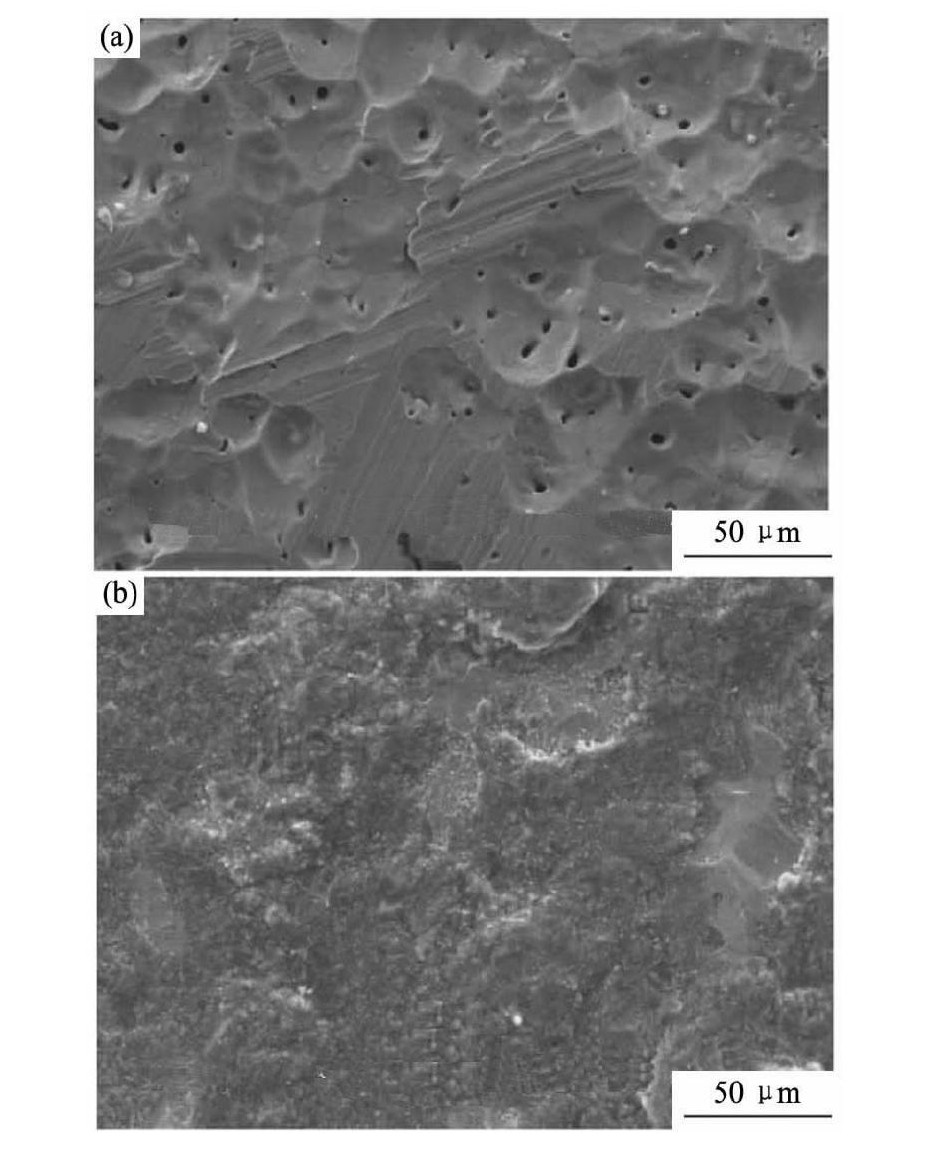
图8 在3.5%Na Cl中的腐蚀形貌 (a) 基材 (b) 渗锆合金层Fig.8Corrosion morphology in 3.5%Na Cl solution
(a) Substrate; (b) Zr-alloyed layer
针对点蚀机制, Mac Donald提出了一种点缺陷模型, 其中指出了在障碍层与外层的界面处存在着氧空位, Cl-容易在此氧空位上吸附, 使内部阳离子的空位浓度增大, 而阳离子空位会由障碍层与外层的界面处向金属与障碍层的界面处移动, 从而形成阳离子空位流。内部阳离子空位浓度增大, 会增强阳离子空位流。而金属氧化所形成的阳离子会占据在金属与障碍层的界面处形成的阳离子空位, 然而, 当其占据的速度小于阳离子空位移动的速度, 阳离子空位就会聚集在金属与氧化物的界面处, 当达到临界浓度时, 钝化膜就会破裂[10,11,12]。
而由图8 (b) 可以看出, 渗锆合金层表面仅为局部腐蚀, 表面较未处理基材平整。从动力学角度分析, 与不锈钢基材相比, 经渗锆处理后, 显著降低了试样表面钝化膜的载流子密度, 即显著降低了氧空位, 使Cl-难以吸附在表面, 使金属与氧化物的界面处的阳离子空位浓度大大降低, 使钝化膜溶解的速度减慢, 从而提高了钝化膜的致密性与稳定性, 抑制孔蚀的发生[13,14,15], 还可能是由于强碳化物形成元素Zr的渗入, 有效地降低了晶界的含碳量, 减少了Cr23C6的形成, 从而抑制了因晶界贫Cr而引起的晶间腐蚀倾向, 增强了不锈钢的耐点蚀和晶界腐蚀性能。
2.4 在0.5 mol·L-1Na OH溶液中的腐蚀结果及分析
图9为基材与渗Zr合金层试样在0.5 mol·L-1Na OH溶液中的极化曲线, 其自腐蚀电流密度icorr、腐蚀速度及相对腐蚀速度等的计算结果如表3所示。该过程为阴、阳极混合控制的析氢腐蚀。由图9与表3可知, 在阴极极化过程中, 随着电位的升高, 基材的电流密度逐渐减少, 当电位升至其自腐蚀电位Ek=-556 m V时进入阳极极化, 之后电流密度随着电位升高而开始增大, 在电流密度为2.511886 m A·cm-2时, 开始钝化, 钝化区间为-35m V。
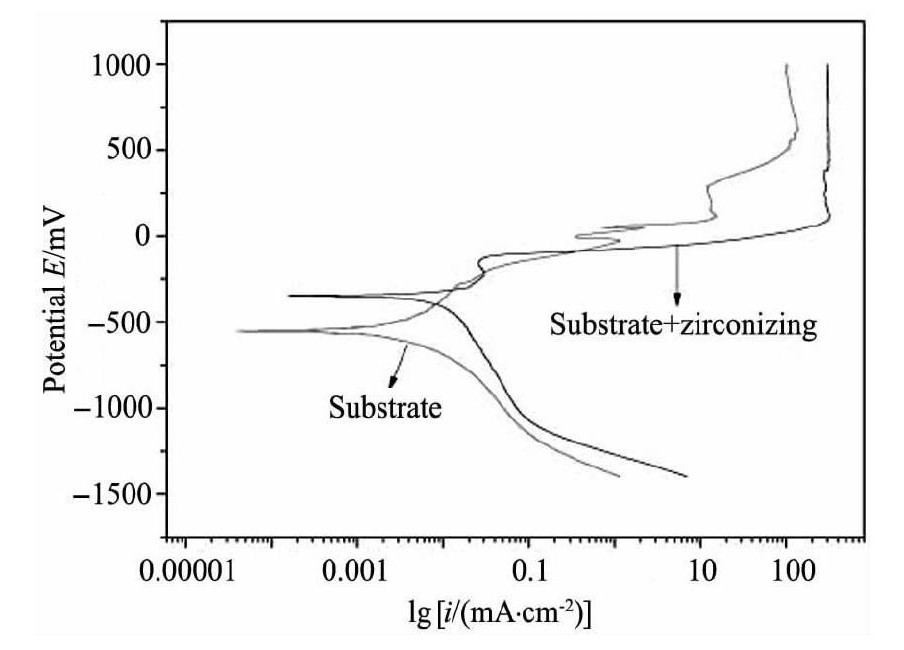
图9 在0.5 mol·L-1Na OH溶液中的极化曲线Fig.9 Cyclic polarization curves in 0.5 mol·L-1Na OH solution
而对于渗Zr试样, 在阴极极化过程中, 随着电位的升高, 其电流密度也逐渐减小。当电位升到自腐蚀电位Ek=-358 m V时, 进入阳极极化, 其自腐蚀电位较基材提高了198 m V, 从热力学角度说明渗Zr试样比基材难发生腐蚀, 之后电位升高, 电流密度随之增大, 在电流密度为0.02884 m A·cm-2时, 出现钝化现象, 钝化区间为-221 m V;且渗Zr试样的腐蚀电流密度和腐蚀速度较基体都有所降低, 基材与渗Zr试样的腐蚀速度分别为0.067250, 0.035464 g·m-2·h-1, 基材的相对腐蚀速度是渗Zr试样的1.90倍, 从动力学角度分析, 可见渗锆合金层使0Cr18Ni9Ti不锈钢在碱溶液中的耐蚀性有所提高。
图10为未处理的基材与渗锆合金层在0.5mol·L-1Na OH溶液中的腐蚀形貌。由图10 (a) 可以明显看出未处理的基材表面腐蚀严重, 出现块状剥落现象, 为典型的剥蚀。由图10 (b) 可以看出, 渗锆合金层腐蚀后表面较平整, 未出现腐蚀剥落现象, 且与未腐蚀前的状态相比, 变化不大。这是由于锆的存在, 钝化时表面形成致密、覆盖性好的氧化膜, 使基体与腐蚀环境隔开, 腐蚀速度降低, 从而使渗锆合金层在0.5 mol·L-1Na OH溶液中的耐腐蚀性能较未处理基材得到很大改善。
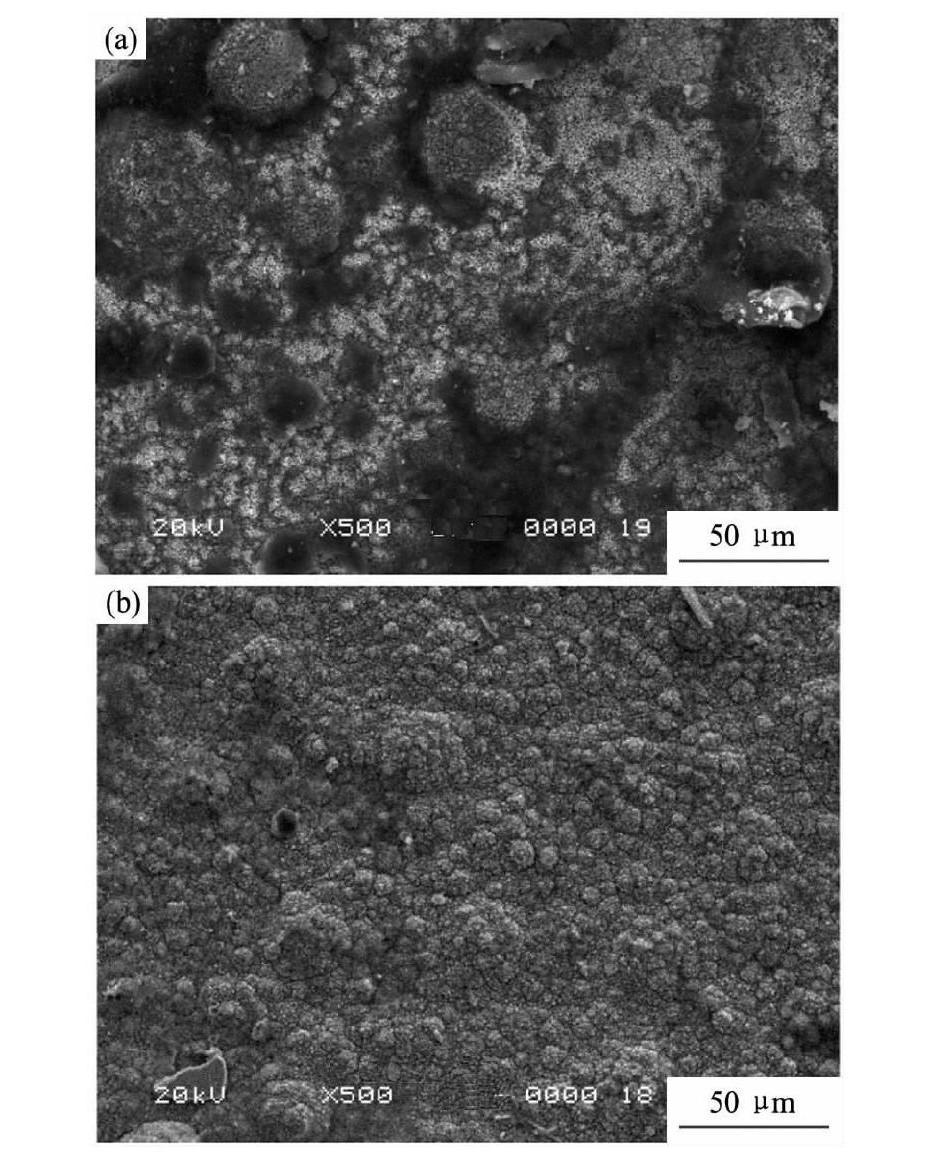
图1 0 在0.5 mol·L-1Na OH中的腐蚀形貌 (a) 基材 (b) 渗锆合金层Fig.10Corrosion morphology in 0.5 mol·L-1Na OH solution
(a) Substrate; (b) Zr-alloyed layer
3 结论
1.利用双辉等离子技术渗锆后, 在0Cr18Ni9Ti不锈钢表面形成厚约65μm、均匀致密连续的渗锆合金层。
表3 在0.5 mol·L-1Na OH溶液中的电化学腐蚀测试结果Table 3Electrochemical measuring results in 0.5 mol·L-1Na OH solution 下载原图

表3 在0.5 mol·L-1Na OH溶液中的电化学腐蚀测试结果Table 3Electrochemical measuring results in 0.5 mol·L-1Na OH solution
2.在0.5 mol·L-1HCl溶液、3.5%Na Cl溶液、0.5 mol·L-1Na OH溶液中, 不锈钢基材的相对腐蚀速度分别是渗Zr合金层的24.43倍、2.44倍、1.90倍;未处理的不锈钢表面腐蚀较为严重, 而渗Zr合金层表面只出现轻微的局部腐蚀, 可见经渗锆处理后, 不锈钢的耐蚀性有所提高。
参考文献
[1] Luo H, Gong M.On intergranular corrosion of austenitic stainless steel[J].Corrosion Science and Protection Technology, 2006, 18 (5) :357. (罗宏, 龚敏.奥氏体不锈钢的晶间腐蚀[J].腐蚀科学与防护技术, 2006, 18 (5) :357.)
[2] Xu Z, Zhang G H, Zhang P Z, Zhang Y M, Chi C Z, Yuan Q L.New development of double glow plasma surface metallurgy technology[J].Engineering Science, 2005, 7 (6) :73. (徐重, 张高会, 张平则, 张艳梅, 池成忠, 袁庆龙.双辉等离子表面冶金技术的新进展[J].中国工程科学, 2005, 7 (6) :73.)
[3] Cai H W, Gao Y, Ma Z K, Wang C L, Yuan L, Zhang W, Li B.Research on W-Mo-Y plasma surface alloying process and microstructure of alloying layer[J].Surface Technology, 2012, 41 (2) :16. (蔡航伟, 高原, 马志康, 王成磊, 袁琳, 张维, 李冰.钨钼钇等离子共渗工艺及渗层组织的研究[J].表面技术, 2012, 41 (2) :16.)
[4] Gao Y, Xu J Y, Gao Q, Cheng J, Xu Z.Analysis on characteristics of double glow discharge plasma surface alloying process[J].Hot Working Technology, 2006, 35 (6) :56. (高原, 徐晋勇, 高清, 成均, 徐重.双层辉光离子渗金属技术特点分析[J].热加工工艺, 2006, 35 (6) :56.)
[5] Szymura S, Bala H.Corrosion resistance of the (Fe40Co40Mn20) 98.2C0.4Si1.4magnet alloy[J].Materials Chemistry and Physics, 1989, 21 (4) :367.
[6] Deodeshmukh Vinay, Gleeson, Brian.Evaluation of the hot corrosion resistance of commercialβ-NiAl and developmentalγ'-Ni3Al+γ-Ni-based coatings[J].Surface and Coatings Technology, 2007, 202 (4-7) :643.
[7] Chen H M, Fan C Y, Liu Y Z, Wen Y X, Zhong X P. Effect of Ce on corrosion behaviors of aluminum in 3.5%NaCl solution[J].Chinese Journal of Rare Metals, 2011, 35 (5) :657. (陈红梅, 范常有, 柳玉柱, 文衍宣, 钟夏平.Ce含量对Al在3.5%NaCl溶液中腐蚀行为影响的研究[J].稀有金属, 2011, 35 (5) :657.)
[8] Her Shiuh-Chuan, Wu C L.Corrosion resistance of TiN coating on 304 steel[J].Applied Mechanics and Materials, 2012, 121-126:3779.
[9] Chao C Y, Lin L F, MacDonald D D.A point defect model for anodic passive film[J].J.Electrochem.Soc., 1981, 128:1191.
[10] Chen Y, Nie X, Northwood D O.Plasma electrolytic oxidation (PEO) coatings on a zirconium alloy for improved wear and corrosion resistance[J].WIT Transactions on Engineering Sciences, 2010, 66:183.
[11] Gurrappa I.Thermal barrier coatings for hot corrosion resistance of CM 247 LC superalloy[J].Journal of Materials Science Letters, 1998, 17 (15) :1267.
[12] Gao Y, Wang C L, Liu Y P, Xu J Y.Corrosion resistance of TiN layer prepared by double glow plasma surface alloying process[J].Transactions of Materials and Heat Treatment, 2011, 32 (6) :143. (高原, 王成磊, 刘燕萍, 徐晋勇.双层辉光等离子制备TiN渗镀层的耐蚀性能[J].材料热处理学报, 2011, 32 (6) :143.)
[13] Tian Z J, Gao X S, Huang Y H, Liu Z D, Shen L D, Wang D S.Study on hot corrosion behavior of plasmasprayed NiCoCrAl-Y2O3coating on TiAl alloy surface[J].Rare Metal Materials and Engineering, 2010, 39 (8) :1439. (田宗军, 高雪松, 黄因慧, 刘志东, 沈理达, 王东生.TiAl合金表面等离子喷涂MCrAlY涂层热腐蚀行为研究[J].稀有金属材料与工程, 2010, 39 (8) :1439.)
[14] Liu J F, Li R D, Song J, Bai Y H.Effects of Zr on electrochemical corrosion behavior of ZA35 alloy[J].Foundry, 2012, 61 (3) :308. (刘敬福, 李荣德, 宋建, 白彦华.Zr对ZA35合金电化学腐蚀行为的影响[J].铸造, 2012, 61 (3) :308.)
[15] Wever D J, Veldhuizen A G, De Vries J, Busscher H J, Uges D R A, van Horn J R.Electrochemical and surface characterization of a nickel-titanium alloy[J].Biomaterials, 1998, 19 (7/9) :761.