文章编号:1004-0609(2007)02-0193-07
固溶处理对铸造Al-Si-Cu-Mg合金组织与性能的影响
李润霞1,李荣德1,吕 伟2,曲迎东1,李晨曦1
(1. 沈阳工业大学 材料学院,沈阳 110023;2. 沈阳航空工业学院 材料系,沈阳 110034)
摘 要:对固溶处理过程中铸造Al-Si-Cu-Mg合金析出相溶解过程进行了研究。结果表明:在固溶处理初期,组织中θ相的数量逐渐减少,但在(FeMn)3SiAl12相中还有一定的Cu含量;而固溶后期,富铁相中的Cu含量也明显降低,且难溶的Al3Ti针状相也发生钝化,但部分Q相尚存在;随着固溶时间的延长,合金基体中Cu和Mg的含量逐渐增多,且富Mn和富Ti相也在合金基体中略有溶解;合金的固溶强化作用主要来源于富Cu相的溶解。在Al-Si-Cu-Mg固溶处理过程中,合金力学性能的提高主要来源于共晶硅相形貌的改善、析出相溶解引起的固溶强化及组织的均匀化。
关键词:铸造Al-Si-Cu-Mg合金; 热处理; 析出相; 溶解; 固溶强化
中图分类号:TG 146.2 文献标识码:A
Effects of solution heat treatment on microstructures and
properties of Al-Si-Cu-Mg cast alloys
LI Run-xia1, LI Rong-de1, L? Wei2, QU Ying-dong1, LI Chen-xi1
(1. School of Materials Science and Engineering,
Shenyang University of Technology, Shenyang 110023, China;
2. Department of Material, Shenyang Institute of Aeronautical Engineering, Shenyang 110034, China)
Abstract: The dissolution of the intermetallic phases was studied and the function of solution strengthening in Al-Si-Cu-Mg casting alloys during solution heat treatment was analyzed. The results show that the θ phase (Al2Cu) dissolves gradually in the initial stage of solution, but still exists around (FeMn)3SiAl12 particles until holding time prolongs. In the final stage of solution the needle-like Al3Ti phases blunt but Q phases (Cu2Mg8Si5Al4) still exist. With the solution time prolonging, the amounts of Cu and Mg atoms in matrix increase, and Mn and Ti intermetallics dissolve partly. However, the function of solution strengthening mainly originates from Cu atoms. The increase of mechanical properties of alloy during solution heat treatment are due to the combined effect of dissolution of the intermetallic phases, uniformity of structure and spheroidization of silicon particles.
Key words: Al-Si-Cu-Mg cast alloy; heat treatment; intermetallic phases; dissolution; solution strengthening
铸造Al-Si系合金具有高强度、低热膨胀系数、良好的铸造性能及耐磨性,广泛应用于制造活塞、汽缸体、汽缸盖和曲轴箱等铸件[1-2]。研究表明,铸造Al-Si-Cu-Mg合金的相组成比较复杂,在非平衡凝固时,合金的组织中有Mg2Si、Al2Cu和Si相。在铸造大型铸件时,局部凝固缓慢,则出现少量W相[3-4]。
在Al-Si系合金的固溶处理过程中,合金组织由于高温扩散会发生显著变化。早期的实验就已发现热处理可以使共晶Si粒状化[1, 5], 无论变质与否,硅相颗粒在固溶处理时均会经历钝化熔断、粒状化和粗化的过程,如当固溶处理时间过长或温度过高时,则硅相可能出现明显的粗化现象[1]。
合金铸态组织中的析出相在固溶处理过程中发生溶解[6-8],使Cu和Mg等合金元素充分固溶于α基体中,为随后的时效处理做好了准备。Narayanan发现,长时间固溶保温甚至可以使富Fe相发生溶解[9]。固溶处理过程同时使组织均匀化,减小在凝固过程中形成的溶质元素偏析[10-11],为时效处理时弥散强化相的析出创造了一个良好的条件。因此,铝合金T6处理的第一阶段—固溶处理被看成是决定时效后弥散强化相显微组织和最终合金的力学性能的关键阶段[12-14]。
以往,对Al-Si系合金固溶处理过程中Si相形貌变化的研究已经较多[1, 5],但对析出相的溶解过程和固溶强化作用的研究还不多见。本文作者通过力学性能测试、扫描电镜(SEM)观察和能谱分析等方法,对合金热处理过程中析出相的溶解过程及其产生的固溶强化作用进行全面的分析与探讨。
1 实验
纯Al和Al-10Cu、Al-28Si、Al-10Mn、Al-4Ti(质量分数,%)中间合金在720 ℃加热熔清后,加入纯Mg,六氯乙烷除气,三元钠盐变质处理后,在金属模中浇注成d 12 mm×60 mm的试棒,实验用合金的化学成分见表1。试样在氮气保护高温炉中(525±5)℃固溶处理0~24 h,60~80 ℃水淬,淬火持续时间小于10 s。淬火处理后的部分试样在台式干燥箱中175 ℃时效处理6 h。
表1 合金的化学成分
Table 1 Chemical composition of samples (mass fraction, %)

布氏硬度试样的尺寸为d 12 mm×5 mm,每个硬度值为6个测点的平均。依据标准GB145—59制备拉伸试样(d 5 mm×25 mm),试样经(525±5)℃、12 h固溶, 175 ℃、6 h时效处理后,在WE-10A万能实验机上测试抗拉强度和伸长率,拉伸速度为0.1 mm/s,每个值取3个实验的平均值。在配有能谱分析系统(Energy Disperse System)的JSM-6301F型冷场发射扫描电子显微镜上观察合金组织形态和拉伸断口。在透射电子显微镜PHILIPS EM400上观察合金的显微组织。
2 结果与分析
2.1 固溶处理对合金力学性能的影响
固溶处理的决定性因素为固溶温度,Al-Si-Cu-Mg合金的固溶处理温度由其凝固时所发生的共晶反应温度共同决定(见表2)[12-13]。为了加速固溶过程,在保证不过烧的前提下,应尽可能使固溶温度接近共晶温度,一般固溶温度低于共晶温度5~10 ℃。Al2Cu溶解缓慢,保温时间不够时不能充分固溶于基体,而Mg2Si只在较高温度下才能够迅速溶解[8]。
表2 Al-Si-Cu-Mg合金凝固的共晶反应
Table 2 Eutectic reaction of Al-Si-Cu-Mg alloy
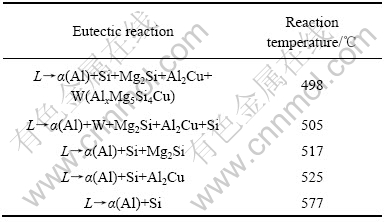
图1(a)所示为525 ℃固溶处理对合金T6和T4态硬度的影响,图1(b)所示为固溶时间对合金T6态抗拉强度和伸长率的影响。合金的硬度、抗拉强度和伸长率均随固溶时间的延长而逐渐增大,在固溶10~12 h达到了峰值,继续延长固溶时间,合金的力学性能有所下降,尤其是强度和硬度的降低比较明显。图2所示为合金分别在铸态、固溶10 h和14 h(T6态)后的拉伸断口形貌。可以看出,铸态合金的断口组织呈脆性沿晶断裂的冰糖状形貌(图2(a));固溶10 h合金的断口则转变为等轴韧窝状,韧窝深而细小(图2(b)),韧性和强度大幅度提高;继续延长固溶时间,可以看出韧窝逐渐变大变浅(图2(c))。
2.2 析出相的溶解
固溶处理的主要目的是使析出相重新溶解形成过饱和固溶体,为合金的时效处理做准备。图3所示为合金铸态组织的SEM形貌。变质处理不但使板片状的共晶Si相变为细小的珊瑚状,而且也使其他析出相细化,见图3(a)和(b)。这些析出相主要分布在共晶Si相的末梢和相界处,造成合金的塑性和韧性比较差。
图3(c)和(d)所示为铸态组织中各析出相的SEM形貌,对应的能谱定量分析结果见表3。合金的铸态组织中除了α (Al)基体和共晶Si相外,还存在着圆粒状的θ(Al2Cu)相(见图3(c)中的“A”)和含少量Mg的网状θ相和Q 相(Cu2Mg8Si5Al4)的混合组织(见图3(d)中的“E”);合金中Ti的加入是为了细化晶粒,而部分Ti 在合金中形成了针状的Al3Ti相(见图3(c)和(d)中的“B”);Mn与合金中的有害杂质Fe形成了块状的(FeMn)3SiAl12相(见图3(c)和(d)中的“C”);Mg主要以边界模糊的片状Q相(Cu2Mg8Si5Al4)方式存在(见图3(c)中的“D”),数量较少。

图1 固溶时间对Al-Si-Cu-Mg合金力学性能的影响
Fig.1 Mechanical properties of Al-Si-Cu-Mg alloy as function of solution time at 525 ℃: (a) Hardness; (b) UTS and Elongation
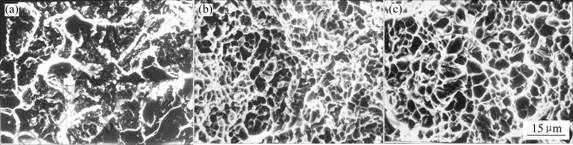
图2 不同固溶时间时Al-Si-Cu-Mg合金的拉伸断口形貌
Fig.2 SEM images of Al-Si-Cu-Mg alloy solutioned at 525 ℃ for various times: (a) As-cast; (b) 10 h; (c) 14 h
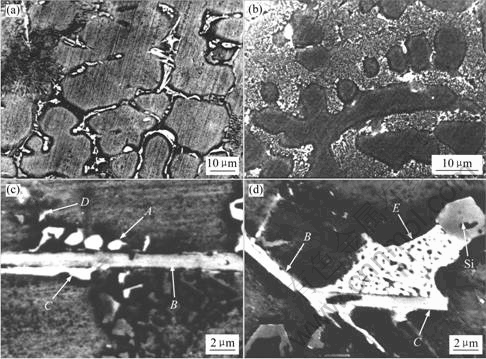
图3 合金的铸态组织
Fig.3 SEM images of as-cast alloy: (a) Unmodified, (b) Modified; (c), (d) Magnified images of (b)
在525℃固溶处理过程中,合金中的析出相逐渐发生溶解消失在基体中。固溶2~6 h后合金中细小的点状和网状θ相的数量随固溶时间的延长大幅度减少,使得合金的伸长率在固溶初期提高较快。但难溶的Al3Ti针状相和块状的(FeMn)3SiAl12基本没有变化(见图4(a)和(b))。
固溶10 h后(见图4(c)),在合金基体中基本上已难以发现θ相。但在块状的(FeMn)3SiAl12相中还有一定的Cu含量(约为3.79%),能谱分析见图5(a)。观察放大后的组织,可以看出有少量的θ相仍然依附在(FeMn)3SiAl12相上(见图4(d))。
表3 铸态组织中各相的能谱定量分析结果
Table 3 Results of EDS analysis of phases shown in Fig.3 (mass fraction,%)
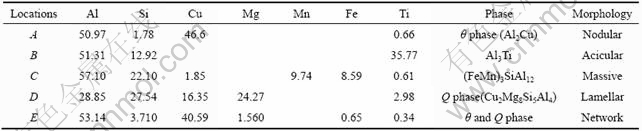
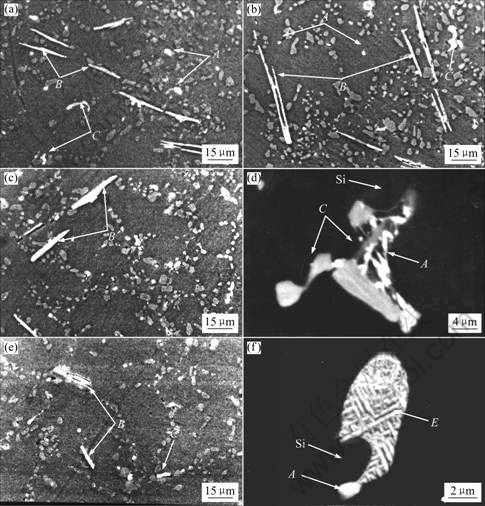
图4 525 ℃固溶处理过程中析出相的溶解
Fig.4 Dissolving process of precipitated phases of alloy solution treated at 525 ℃ for different time: (a) 2 h; (b) 6 h; (c), (d) 10 h; (e), (f) 14 h

图5 固溶不同时间后合金中含Fe相的能谱分析
Fig.5 EDS analysis of Fe-rich phase arrowed as “C” in Fig.4 (c) and (e): (a) 10 h; (b) 14 h
固溶14 h后(见图4(e)),(FeMn)3SiAl12相中的含Cu量明显降低(约为1.85%),能谱分析结果见图5(b)。由图可见,依附在(FeMn)3SiAl12相上的θ相也已经溶解。与此同时,由于固溶温度高,原子易于扩散,合金中难溶的Al3Ti针状相也发生了钝化,从而降低了合金中的应力集中,使固溶处理后期合金的伸长率得到进一步的提高,合金基体中Ti含量随固溶时间的延长而略有升高也证明了这一点(见表4)。但同时还发现部分网状的四元Q相仍然存在,见图4(f)。
2.3 固溶强化
表4所列为525 ℃固溶不同时间合金基体中各元素的能谱分析结果。可以看出,随着固溶处理的进行,合金中的析出相发生溶解,基体中溶质原子数量逐渐增多,Cu、Mg、Si、Mn和Ti都随着固溶时间的延长逐渐增多。
那些溶入α(Al)基体形成过饱和固溶体的溶质原子对合金产生固溶强化。溶质原子与溶剂原子的尺寸差别越大,所引起的晶格畸变也越大,强化效果也越好[13-14]。表5所列为合金元素的原子直径,可以看出Cu原子尺寸与合金基体原子Al的尺寸差别很大。
在固溶初期,合金基体中Cu含量的增长比较快。合金的强度和硬度随溶质原子过饱和度的增大而逐渐提高。合金经525 ℃固溶12 h后,θ相已基本发生溶解,淬火后合金基体中过饱和Cu原子的数量多(约1.9%),对合金产生了良好的固溶强化作用,合金的强度和硬度也达到了峰值。
Mg和Mn原子对合金也有较好的固溶强化作用,但含Mg的Q (Cu2Mg8Si5Al4) 相在固溶处理时只能部分溶解,而富Mn的 ((FeMn)3SiAl12) 相更是难以溶解。因此,在525 ℃固溶12 h时合金基体中过饱和的Mg和Mn原子数量均较少(分别约为0.15%和0.08%),因而Mg和Mn对合金的固溶强化作用相对较小。
另外,合金经525 ℃固溶12 h后,铝基体中Si原子的含量达到1.58%,但由于Si原子的扩散速度很快,这就使得淬火后,合金中的过剩硅会以细小的硅相质点形式析出(见图6),大大降低了Si原子在基体中的固溶度[15-16],同时,Si原子与Al的尺寸差异较小。因而,Si对合金的固溶强化作用基本可以忽略。
表4 固溶过程中基体的能谱定量分析结果
Table 4 Results of EDS analysis of matrix solution treated at 525 ℃ for different time (mass fraction, %)
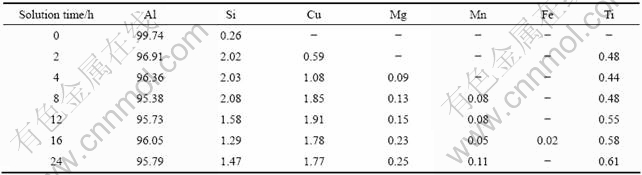
表5 几种主要合金元素的原子直径比较
Fig.5 Comparison of atom diameter of various alloying elements
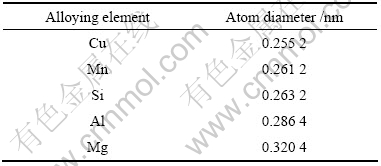
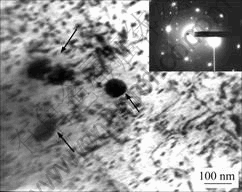
图6 固溶淬火后析出Si相质点的TEM形貌及选区衍射
Fig.6 TEM images and corresponding SADP of Si particles in matrix of alloy quenched
继续延长固溶时间,合金基体中Cu含量基本不变,而Mg含量却持续增多,Mn和Ti也在合金基体中略有溶解,固溶强化作用会略有增强。但是,少量Mg、Mn和Ti微小的固溶强化作用不能抵消固溶后期由于共晶硅相粗化而引起的力学性能的恶化,因此,12 h以后继续固溶处理时,合金的力学性能会呈现下降趋势。
由此可见,经525 ℃固溶12 h后合金强度和硬度的显著提高与富Cu相溶解产生的固溶强化密不可分。同时,固溶处理过程中析出相的溶解和共晶硅相的圆整化使合金的韧性提高[1, 5]。在Al-Si-Cu-Mg固溶处理过程中,合金力学性能的提高主要来源于共晶硅相形貌的改善、析出相溶解引起的的固溶强化以及组织的均匀化。
3 结论
1) 在合金变质后的铸态组织中,除了存在α(Al)基体和共晶Si相外,还存在着θ相(Al2Cu)、Al3Ti相、(FeMn)3SiAl12相以及Q相(Cu2Mg8Si5Al4)等。
2) 525 ℃固溶处理2~6 h时,组织中θ相的数量逐渐减少;固溶10 h后,θ相已基本溶解消失,但在 (FeMn)3SiAl12相中含有一定量的Cu;而固溶14 h后,富铁相中的Cu含量也明显降低,且难溶的Al3Ti针状相也发生了钝化,但部分Q相尚存在。
3) 随着固溶时间的延长,合金基体中Cu和Mg的含量逐渐增多,尤其是固溶初期,Cu含量的增长比较快。固溶12 h后,合金基体中Cu含量基本不变,而Mg含量却持续增多 ,且Mn和Ti也在合金基体中略有溶解。
4) 固溶处理后合金基体中Mg和Mn原子数量较少,且Si原子的固溶强化作用基本可忽略,合金的固溶强化作用主要来源于富Cu相的溶解。
REFERENCES
[1] LI Run-xia, LI Rong-de, ZHAO Yu-hua, et al. Effect of heat treatment on eutectic silicon morphology and mechanical property of Al-Si-Cu-Mg cast alloys [J]. Trans Nonferrous Met Soc China, 2004, 14(3): 496-500.
[2] 谭建波, 邢书明, 李立新, 等. 半固态A356合金微观组织特征对充型能力的影响[J].中国有色金属学报, 2004, 2006, 16(4): 612-617.
TAN Jian-bo, XIN G Shu-ming, LI Li-xin, et al. Influences of microstructure characteristics of semi-solid A356 alloy on filling ability[J]. The Chinese Journal of Nonferrous Metals, 2006, 16(4): 612-617.
[3] Li R X, Li R D, Zhao Y H, et al. Age-hardening behavior of cast Al-Si base alloy [J]. Mater Lett, 2004, 58(15): 2096-2101.
[4] Samuel F H. Incipient melting of Al5Mg8Si6Cu2 and Al2Cu intermetallics in unmodified and strontium-modified Al-Si-Cu-Mg (319) alloys during solution heat treatment [J]. J Mater Sci, 1998, 33: 2283-2297.
[5] 戴洪尚, 刘志勇, 王明星, 等. 固溶处理对电解制备的A356合金硅颗粒的影响 [J]. 中国有色金属学报, 2004, 14(7): 1201-1205.
DAI Hong-shang, LIU Zhi-yong, WANG Ming-xing, et al. Influence of solution treatment on eutectic silicon of A356 alloy made of electrolysis aluminum [J]. The Chinese Journal of Nonferrous Metals, 2004, 14(7): 1201-1205.
[6] Samuel A M, Gauthier L, Samuel F H. Microstructural aspects of the dissolution and melting of Al2Cu phase in Al-Si alloys during solution heat treatment [J]. Metall Mater Trans A, 1996, A27(7): 1785-1798.
[7] Sokolowski J H, Sun X C. The removal of copper-phase segregation and the subsequent improvement in mechanical properties of cast 319 aluminum alloys by two-stage solution heat treatment [J]. J Mater Processing Technol, 1995, 53: 385-392.
[8] Lasa L, Rodriguez-Ibabe J M. Characterization of the dissolution of the Al2Cu phase in two Al-Si-Cu-Mg castings using calorimetry [J]. Materials Characterization, 2002, 48: 371-378.
[9] Narayanan A L, Samuel F F, Gruzleski L E. Dissolution of iron intermetallic in Al-Si alloys through nonequilibrium heat treatment [J]. Metall Mater Trans A, 1995, A26 (8): 2161-2174.
[10] 刘小涛, 董 杰, 崔建中, 等. 高强铝合金均匀化热处理 [J]. 中国有色金属学报, 2003, 13(4): 909-913.
LIU Xiao-tao, DONG Jie, CUI Jian-zhong, et al. Homogenizing treatment high strength aluminum alloy cast under electric magnetic field [J] . The Chinese Journal of Nonferrous Metal, 2003, 13(4): 909-913.
[11] Crowell N, Shivkumar S. Solution treatment effects in cast Al-Si-Cu alloys [J]. AFS Trans, 1995, 107: 721-726.
[12] WANG Gui-qing, BIAN Xiu-fang, WANG Wei-min, et al. Influence of Cu and minor elements on solution treatment of Al-Si-Cu-Mg cast alloys [J]. Materials Letters, 2003, 4480: 1-5.
[13] Gauthier J, Samuel F H. Tensile properties and fracture behavior of solution-heat-treated 319.2 Al automotive alloy [J]. AFS Trans, 1995, 114: 849-856.
[14] Riontino G, Abis S, Mengucci P. DSC investigation of natural ageing in high-copper AlCuMg alloys [J]. Mater Sci Forum, 2000, 331/337: 1025-1030.
[15] Zhang D L. Precipitation of excess silicon during heat treatment of cast Al-7w%Si-0.4wt%Mg alloy [J]. Mater Sci Forum, 1996, 217/222: 771-776.
[16] Kaczorowski M. The role of excess silicon in the process of precipitation hardening of AlSiMg alloy (Ⅰ) [J]. Aluminium, 1985, 10: 756-762.
收稿日期:2006-07-20;修订日期:2006-11-29
通讯作者:李润霞,博士;电话:024-25691310;E-mail: runxiali@163.com
(编辑 何学锋)