
Preparation of Ni-Cr/BN self-lubricating composites by active sintering process
YU Kun(余 琨), YANG Zhen(阳 震), WANG Ri-chu(王日初), TAN Ying-guo(谭映国)
School of Materials Science and Engineering, Central South University, Changsha 410086, China
Received 15 July 2007; accepted 10 September 2007
Abstract: A Ni-Cr/BN composite was produced by a active sintering process. The powder of nickel carbonyl,Cr2O3 and C were used as the original materials,and a hexagonal BN(h-BN) powder was added as a solid lubricant. The influence of sintering temperature,heating rate and holding time on the properties of Ni-Cr/BN were studied. The composition and microstructure of Ni-Cr/BN were analysed by X-ray diffraction(XRD) and the optical microscopy(OM). The frictional behavior and hardness were measured with ring-block friction testing machine and Brinell hardness tester respectively. The results show that Ni-Cr is the matrix and a low-melting eutectic compound is the bonding phase in the composite. The porosity reaches 48% and the value of hardness reaches HB18 when the composite is fabricated at 1 100 ℃ for 1 h. Its wear rate is 7.44×10-5 g/min, and the average friction coefficient is 0.266. These properties make such composite suitable for use as self-lubricating material.
Key words:activated sintering; Ni-Cr/BN; composite; solid lubrication material
1 Introduction
In modern machinery manufacturing engineering, in order to develop thermal power machine and other advanced equipment, it is necessary to develop high temperature self-lubricating composite materials[1]. Such materials are typically used at high temperatures without lubricants. And it also requires a high-temperature oxidation resistance and mechanical properties of stability, and nickel alloy will be combined with the solid lubricant to a system of material to achieve the required conditions[2]. Ni-base alloy with high working temperature (<1 100℃), organizational stability, less harmful phase, anti- oxidation, anti-heat-corrosion and other advantages, can replace certain high temperature refractory metal produced self-lubricating materials[3]. Therefore, the nickel-base superalloy self-lubricating composite materials research has very important significance.
The solid lubricant h-BN is white, with a similar structure as graphite, called “white graphite”[4]. It has a high melting point (sublimation temperature of 3 000 ℃[5]), will be oxidized under high temperature (900-1 200℃)[6]. h-BN with good wear performance and lubrication properties, widely used in high temperature wear sealing materials of aerospace engine in recent years[7], is the high-temperature self-lubricating materials excellent additive. Currently, the research on the nickel-based self-lubricating composite materials has been developing in many years. Products used in industrial production has been successfully developed both at home and abroad, but that on h-BN as a solid lubricant is less. At Ni-Cr/BN solid-phase sintering, h-BN hinder Ni-Cr alloy powder sintering process, when the BN content of 15%, materials cannot sinter[8]. PM active sintering uses physical or chemical means to enhance sintering activity. The Ni-Cr/BN of BN content 11%-15% can be prepared by active sintering method, which provides a new approach to the preparation of low hardness, high porosity wear sealing materials.
2 Experimental
The carbonyl Ni powder(≤3 ?m), Cr2O3 (analytically pure), metallurgical carbon black (C) (20 ?m) and h-BN (10 μm, oxygen content ≤0.5%) were used as starting materials. First, Cr2O3, C and h-BN were mixed in a certain proportion, Cr/BN composite powder was synthesized in a vacuum sintering furnace, after passing 120-mesh(0.125 mm) screener, mixed with Ni powder in a relative density of 58%-60% of the billet. Finally, certain proportion. Then, the mixture used 240-300 MPa axial pressure, at room temperature one-way shape to a relative density of 58%-60% of the billet. Finally, it was sintered in a tube type resistance furnace, using H2 as shielding gas. Warming up to the setting sintering temperature in different speed, and different insulation time, cooling to room temperature in 20 ℃/min.
The material phase was analysed in the D-MAX2000 Rigaku X-ray diffraction instument, using Cu target for 40 kV voltage, operating current of 200 mA. The material microstructure was observed and analysed in the POLYVER-MET OM. The friction test was carried out in the M-2000 ring-block sliding friction tester, using GCr40 steel as pair, with load of 60 N, speed of 400 r/min(0.42 m/s), without any lubrication conditions. The Brinell hardness of materials were measured in HW187:5 Brinell hardness tester, using steel ball of 5 mm in diameter, with experimental load 612.9 N and hold time 60 s.
3 Results and analysis
3.1 Powder synthesis and composite materials before and after sintering phase analysis
Fig.1 shows the XRD patterns of the Cr/BN composite powder before and after synthesis. Fig.1(a) shows the presence of the three-phase, i.e. Cr2O3, BN and C. Fig.1(b) shows the two-phase characteristics, respectively Cr2B and BN. This shows that Cr2O3, BN and C joint in a chemical reaction, the reaction product is Cr/BN composite powder and its main ingredient is BN.
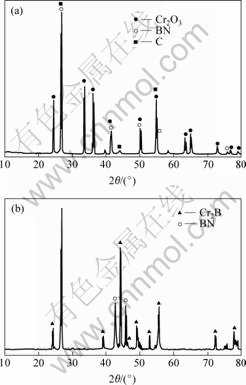
Fig.1 XRD patterns of Cr/BN composite powder before(a) and after(b) synthesis
Fig.2 shows the XRD patterns of Ni-Cr/BN before and after sintering. It can be seen that the characteristic peaks of Ni and BN phase exist. The difference is in the characteristic peaks of Cr2B in Fig.2(a) being replaced by Ni3B in Fig.2(b). This is because in the process of sintering, the products are Ni3B and (Ni, Cr) solution from reaction of Ni and Cr2B(Fig.2(b)).
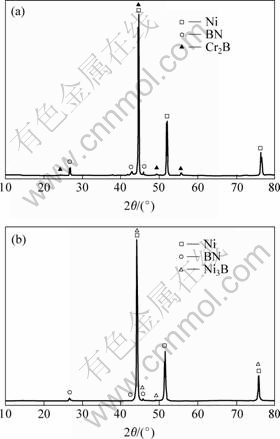
Fig.2 XRD patterns of Ni-Cr/BN before(a) and after(b) sintering
3.2 Sintered materials (sintered) analysis
Fig.3 shows Ni-Cr/BN after sintering at 1 050 ℃, 1 100℃ and 1 150 ℃ for 1 h, in which the bright region is the metal matrix, during which the distribution of a large number of pores (black region). Fig.3(a) shows material is sintered by metal particles linked mutually through sintered neck, only the presence of small amounts of the massive organization(liquid parcels solid particles from condensation). Fig.3(b) shows material composite of the massive organization, porosity relatively small. Fig.3(c) shows material have a great deal of pores, allow a small number of massive organizations as skeleton. Although during sintering process liquid phase appears, but active sintering is different from the liquid-phase sintering and solid-phase sintering. Strengthening sintering includes active sintering, transient liquid-phase sintering and liquid-phase sintering three ways[9]. The rapid channels of three sintering method is carried out through the second phase (solid or liquid) separating out in the powder interface[10]. Ni-Cr/BN active sintering kinetics is between solid-phase and liquid-phase sintering, similar dissolution and precipitation of liquid-phase sintering process. But the liquid of liquid-phase sintering reaches generally 13%-35% of sintered body volume, when the liquid is less than 13% sintered body will residue part of the liquid-unfilled holes, and the direct contact solid particles will be unduly raised. The active sintering requires liquid is not more than 10%, so sintered body have a lot of liquid-filled pores. As pressure sintering embryos before the relative low density, sintering, and the expansion of the initial volume of sintering neck BN formation and inhibit the growth[11], only allows a limited number of solid metal particles have direct contact with is not conducive to the densification of the material. BN content with the continuous enhancement of their role in impeding the right sintering has been continuously increasing, due to liquid phase sintering activation as a binder when BN content of 15% can be achieved sintering.
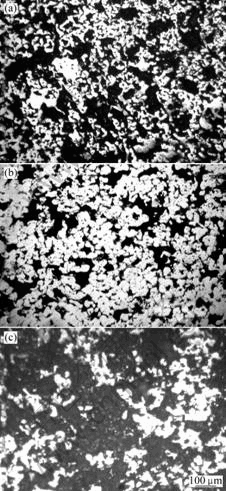
Fig.3 Microscopic structures of Ni-Cr/BN after sintering: (a) At 1 050 ℃ for 1 h; (b) At 1 100 ℃ for 1 h; (c) At 1 150 ℃ for 1 h
3.3 Sintered materials properties analysis
Table 1 lists sintered material’s properties. Similar foreign material properties are as follows: hardness ≤HB20, the average coefficient of friction is 0.439, and the wear rate is 4.1×10-4 g/min. By comparison, it can be seen that the material properties are very close or more than foreign material properties. As wear sealing materials, in addition to the friction properties, hardness of materials is also very important. Because the pair material is made generally of precious metal, the smaller hardness of materials, the smaller pairs wear, so it is not to cause greater damage.
Table 1 Properties of Ni-Cr/BN after sintering
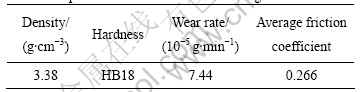
3.4 Sintered material impact on performance analysis
Factors affecting more material sintering properties, such as physical properties of powder, blank cold density, sintering atmosphere, the sintering temperature and so on. The activation sintering rapid proliferation of channels through the provision of enhanced sintering: lower sintering temperature, sintering shorten the time and improve the performance of sintered material[12]. Therefore, the entire process in the lower sintering temperatures will be completed smoothly[13-14]. When certain conditions outside, how good control of sintering temperature, velocity and temperature insulation time these three factors[15], sintering properties of the final plays a vital role.
3.4.1 Sintering temperature on relative density of materials
The phase diagram[15] shows that Ni and Ni3B eutectic temperature change is 1 093 ℃, and 1 093 ℃ embryos will be expected to produce liquid. With increasing temperature, liquid volume is increasing. For outstanding performance materials, we must have a sufficient number of solid particles liquid inclusions, the need to choose the appropriate sintering temperature. Fig.4 shows the sintering temperature of 1 050, 1 100 and 1 150 ℃, the embryo for 1 h insulation material changes in the relative density. It can be seen from Fig.4, billet relative density at 1 100 ℃ than that at 1 050 ℃. This is because, with the sintering temperature is going up, the liquid compound embryo growing in solid particles will be wrapped up at the same time filling more porous, so the relative density from 1 050-1 100 ℃ upward trend. However, as the sintering temperature further improved, but continues to decline relative density, 1 150 ℃ billet the relative density of 42%. Although sintering temperature higher liquid content more mobile but also a corresponding increase in gravity and other factors, the excess liquid will percolate billet surface, the loss of liquid, solid phase particles due to the involvement of external gas and formation porosity, resulting sintered density relative decline to large pores in the material existence. The main sample sintered density and density of the compact, the sintering temperature increases, and narrow pore of the ball, but the pore shape changes do not significantly improve the sintered density[16], the material is sintered density with temperature changes lesser degree.
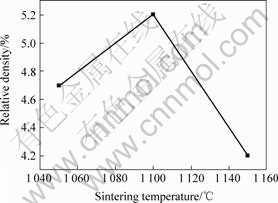
Fig.4 Influence of sintering temperature on relative density of Ni-Cr/BN
3.4.2 Holding time on relative density of materials
Sintering is the phenomenon and process brought out by the powder pressed compact at the right temperature and atmosphere conditions. The result of sintering is that the particles bond together each other, porosity decreases, the strength and density of sintered body increase. When a certain temperature, the longer the sintering time, the higher the properties of sintered body. But the effect of holding time is less than that of sintering temperature, only in the early stages of sintering, density changes rapidly with time. Therefore, the extension of sintering time alone is difficult to attain high dense, and reduces productivity, so to raise the temperature, and shorten the time taken to process as much as possible to ensure product performance. But in the sintering temperature certain circumstances, extend only through sintering time to ensure the performance of sintered. Fig.5 shows at the sintering temperature of 1 100 ℃ with warming rate of 14 ℃/min for different soaking time of the billet changes in the relative density. We can see that the insulation 0.5 h, the relative density of the sintered from 45% to 49%; A further 0.5 h, up to 52%; Continued extension of the time, the relative density did not change significantly.
3.4.3 Warming up speed on trelative density of materials
Fig.6 shows different heating rates on the impact of the relative density at sintering temperature 1 100 ℃ for 1 h. The embryo is not expected to BN particles with a sintered metal particles in the initial sintering distortion due to the release will happen volume expansion, while metal particle contact surface between the bond will happen to billet provide certain intensity, and not because of expansion in the collapse. If the rapid warming in the metal particle contact area has not been completely bonded circumstances result volumetric expansion further exacerbated, often sintered large deformation along the axial cracks, thereby seriously affecting the sintered density and size; If the temperature is too slow, in liquid form on the metal particles before linking, on the liquid distribution, but also a waste of energy. Overall, 10-14 ℃/min within the heating rate on the density of the sintered little impact on. When the heating rate of 20 ℃ or greater than, sintered body is easy to crack, if cracking, a product waste.
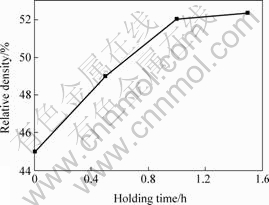
Fig.5 Influence of holding time on relative density of Ni-Cr/BN
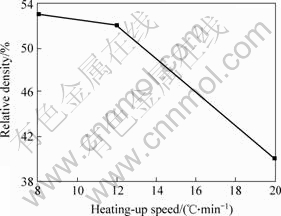
Fig.6 Influence of heating-up speed on relative density of Ni-Cr/BN
4 Conclusions
1) The porosity of Ni-Cr/BN prepared by active sintering process reaches 48%, hardness only HB18, wear rate 7.44×10-5 g/min, average friction coefficient 0.266. These satisfy fully use requirements of self- lubricating materials.
2) The low melting point eutectic of Ni and Ni3B is made as bonding phase. When the temperature is more than 1 093 ℃, embryos will be expected to produce a small amount of liquid. During the sintering process, the liquid phase parcelling solid phase particles is conducive to the proliferation of atomic, it can promote sintering process. After solidification, liquid phase bonds matrix particles together and play the role of linking matrix.
3) Active sintering temperature must be more than the melting point of eutectic(1 100 ℃): Sintering temperature is too low, no liquid produced, too high, liquid spills caused uneven composition. Holding time must not exceed one hour: time is too short, the proliferation of insufficient density changed little,too long, unable to provide further density. Warming up speed for 10-14 ℃/min is suitable.
References
[1] MATSUO M. Solid manual lubrication[M]. FAN Yu, transls. Beijing:China Machine Press, 1986. (in Chinese)
[2] LIU Ru-tie, LI Xi-bin. Nickel-base high temperature self-lubricate material[J]. Powder Metallurgy Material and Engineering, 1997, 2(1): 32-38. (in Chinese)
[3] FU Xing-wang. Effects of solid lubricant MoS2 on the tribological behavior of hot pressed Ni/MoS2 Self-lubricating composites at elevated temperature[J]. Tribology Trans, 1996, 39(2): 392-397.
[4] HU Wan-ying. Study on a new process for synthesis of hexagonal boron nitride[J]. Advanced Ceramics, 2002, 2: 35-36. (in Chinese)
[5] GUO Zhi-meng, SONG Yue-qing. Superhard material and tool[M]. Beijing: Metallurgical Industry Press, 1996. (in Chinese)
[6] GUO Sheng-bo, WANG Wei-ming. Research progress of C/BN laminated composites with high properties[J]. Journal of Ceramics, 2005, 26(4): 285-289. (in Chinese)
[7] LI Fan, ZHANG Deng-jun, LI Bao-hou, LUO Shi-min, ZHAO Xiao-feng. A new chemical plating system for hexagonal boron nitride particles[J]. The Chinese Journal of Process Engineering, 2002, 10: 425-430.
[8] WEI Sheng-ming. WANG Ri-chu, LI Qin-yong, LI Wen-xian, HUANG Bai-yun. Effect of BN on sintering properties of Ni-based abradable seal alloy[J]. Rare Metal Material and Engineering, 2006, 35(1): 127-130. (in Chinese)
[9] LIU Yong, WEI Wei-feng, HUANG Bai-yun, ZHOU Ke-chao. Qualitative and quantitative theory of enhanced sintering in powder metallurgy[J]. Materials Review, 2003, 17(3): 1-4. (in Chinese)
[10] MUNIR Z A, GERMAN R M. A generalized model for the prediction of periodic trends in the activation of sintering of refractory[J]. High Temperature Science, 1977, 9: 275-283.
[11] GERMAN R M, MUNIR Z A. Activated sintering of refractory metal by transition metal additions[J]. Reviews Powder Metallurgy Physical Ceramic, 1982, 2(1): 9-13.
[12] DUAN L C, LIU X Y, MAO B S, YANG K H, TANG F L. Research on diamond enhanced tungsten carbide composite button bits[J]. Journal of Materials Processing Technology, 2002, 129(1/3): 395-398.
[13] SHAO G Q, DUAN X L, XIE J R, YU X H, ZHANG W F, YUAN R Z. Sintering of nanocrystalline WC-Co composite powder[J]. Reviews on Advanced Materials Science, 2003, 5(4): 281-286.
[14] HIRSCHHORN J S. Introduction to powder metallurgy[M]. New York: APMI,1969.
[15] PORTNOI1 K I,ROMASHOV1 V M, CHUBAROV1 V M, LEVINSKAYA M K, SALIBEKOV S E. Phase diagram of the system nickel-boron[J]. Powder Metallurgy and Metal Ceramics, 1967, 6(2): 99-103.
[16] MORDIKE B L, KACZMAR J, KIELBINSKI M, KAINER K U. Effect of tungster content on the properties and structure of cold extended Cu-W composite materials[J]. Powder Metallurgy International, 1991, 23(2): 91-95.
(Edited by YANG You-ping)
Corresponding author: YANG Zhen; Tel: +86-13786198841; E-mail: yangzhen82@163.com