
Preparation of ZrO2 spherical nanometer powders by emulsion processing route
CHANG Ying(常 鹰), LI Xi-bin(李溪滨)
State Key Laboratory of Powder Metallurgy, Central South University, Changsha 410083, China
Received 10 April 2006; accepted 25 April 2006
Abstract: ZrO2 precursor powders containing 3% Y2O3 were prepared via a single emulsion processing route and a double emulsion processing route. In both routes xylol was used as the oil phase, span-80 as the surfactant, and an aqueous solution containing zirconium or ammonia as the water phase. The calcination of the precursor powders was performed at 600 ℃ for 2 h, leading to tetragonal phase ZrO2 nanometer powders. The ZrO2 powders and the precursor powders were analyzed and characterized by means of TGA-DTA, XRD, TEM, BET and laser particle size analyser. The results indicate that xylol-span-80-water phase system contain more water phase, which to a certain extent overcomes the disadvantages of low output by emulsion route in preparing powders. The best volume ratio Vxylol∶Vspan-80∶Vwater= 95∶5∶25 leads to the attaining of powders. The special tetragonal phase powders with less agglomeration were prepared via either the single emulsion processing route or the double emulsion processing route according with the ratio. But compared to the single emulsion processing route, the powders prepared via the double emulsion processing route display smaller particles with more even size distribution, the average size of around 15 nm.
Key words: zirconia; emulsion; spherical nanometer particles
1 Introduction
Zirconia powder is widely used in many advanced structural, high-temperature and electrical ceramic applications, because of its special properties, such as low-thermal conductivity, high mechanical strength, high fracture toughness, and relatively high thermal expansion coefficient. The effects of powder characteristics on the processing and the properties of the final ceramic products have been well known. Ceramic powders consisting of microparticles (from one tenth to several micrometers) with spherical morphology and narrow size distribution are required to produce materials with low sintering temperature, high packing density, and uniform microstructure. Nano-particles (less than 0.1 μm) can further enhance sinter ability at lower temperatures with smaller residual pores and grain sizes.
There is a variety of techniques available for producing ceramic particles, including conventional aqueous precipitation, hydrothermal processing, hydrolysis of alkoxide solution (sol-gel method), gas-phase reaction and precipitation in reverse emulsion. The preparation of nanoparticles is much more difficult than that of microparticles. Although the sol-gel method can be adopted in the preparation of spherical ceramic nanoparticles, the raw materials of metal-alkoxide of the process are too expensive to be used in a large-scale production. Among various techniques, precipitation of precursor particles from solution is still the most acceptable technique because of its simplicity, safety and low cost. However, the conventional aqueous precipitation method often produces irregular-shape particles with a wide size distribution. But for emulsion, the water droplets wrapped up in surfactant enveloped by oil phase can be used as nanosized reacants for the formation of nanoparticles. Therefore, spherical powder with uniform size distribution and good dispersibility can be obtained. All of these suit for the need of the preparation of ceramic materials, so there have been lots of papers about the preparation methods of ZrO2 nanoparticles from microemulsion[1-13]. However, the prices of raw materials and organic solvents such as cyclohexane and heptane are comparatively high, or the proportion of the aqueous phase as reactants in emulsion is too small. In order to obtain a small quantity of nanoparticle powders, a great deal of organic solvent is needed. All of these make the cost still comparatively high.
In this paper, a water/oil emulsion using low price xylol as oil phase, span-80 as surfactant was used to prepare ultrafine spherical zirconia nanoparticle powder; the content of aqueous phase in the system was high. At the same time, the nano-particle ZrO2 powders prepared via a single emulsion and a double emulsion processing route were compared and analyzed.
2 Experimental
2.1 Selection of emulsion
The emulsion used to prepare nanoparticle powders must possess the following qualities: 1) good stability which makes sure that droplets will not enlarge for their own instability when they react, or even when oil phase separates from aqueous phase; 2) good mobility which ensures that precipitation of emulsion can be fully reacted; 3) water/oil(w/o) emulsion(reversed micelles) in which irregular-shape particles produced by the direct contact reaction of reactants can be avoided; 4) After meeting the above requirements, in order to obtain high productivity, the aqueous ratio of emulsion must be high.
The afore-mentioned requirements do not exist independently but influence mutually. For example, the stability parameter of emulsion mainly depends on the variety of surfactant on the one hand and the ratio of oil, aqueous and surfactant on the other hand. Especially the variety of surfactant influences the type of emulsion. To w/o emulsion, it requires the hydrophile-lipophile balance(HLB) of surfactant between 3 and 6. With the increase of surfactant content, the particle size containing water for agglomeration during precipitation reaction decreases, which will gradually increase the stability of scattered system. On the other hand, if the content of surfactant is too high, it will be easy to contain micro-droplets of water; and because the viscosity of surfactant is generally high, it is difficult to eliminate the micro-droplets of water, and the average particle size of powder will become large. Thereby, considering the four requirements and according to the principle of reducing preparation cost, xylol was used as oil phase, span-80 as surfactant and aqueous solution of Zr(NO3)4 or NH3 as aqueous phase. After lots of experiments, the best volume ratio Voil∶Vsurfactant∶Vaqueous=95∶5∶25 of reactants were obtained.
2.2 Experimental procedures
At room temperature, Zr(NO3)4?2H2O(analytical grade) and Y(NO3)3.6H2O (analytical grade) were confected into a precursor solution in which the molar fraction of yuria was 3%. Then the solution was added into the oxlyl solution containing surfactant according to the best volume ratio of reactants. During the period of adding, a magnetic stirrer was kept stirring. After being supersonic dispersed for 20 min, the mixed solution was divided into emulsion A and emulsion B for using. Ammonia solution was titrated into emulsion A to directly precipitate. Emulsion B was mixed with the ammonia emulsion prepared by the same method as emulsion. During the period of titrating and mixing, a magnetic stirrer was kept stirring to make each droplet become gel, so gel A and gel B were obtained. Then the gels were carried out an azeotropic distillation, and most of the water and oil were removed when the temperature increased to near the boiling point of oxlyl, which is 144 ℃. The two distilled gels were filtered, and then repeatedly washed with deionized water to remove the residual surfactants and oil phase. At last, the deionized water in gels was removed through washing with ethyl-alcohol, then dried under vacuum at 80 ℃ for 24 h. Finally, white ZrO2 powders sample A and sample B were obtained by calcining the amorphous precursors at 600 ℃ for 2 h to form a tetragonal structure.
2.3 Indicator of product
The mass loss and reaction evolution of powders were determined with DT-40 thermal analyzer. The samples for TGA/DTA measurement were heated from room temperature to 1 050 ℃ at a heating rate of 10 ℃/min in a static air atmosphere. The BET specific surface areas of the calcined powders were obtained by monosorb N2 adsorption-desorption with multiple points method, and particle diameter was calculated. TecnaiG2 20 TEM was employed to study the particle size of the ZrO2 nanoparticle powders and the morphology of resultant zirconia particles. The crystal structures of the two samples were determined by Max2500VB+ X-ray diffractometer. The average zirconia crystallite size was calculated from the Debye-Scherrer equation based on the (111) face for t-ZrO2. Particle size and particle size distribution of the calcined zirconia powders were analyzed by using Micro-plus laser particle size analyser.
3 Results and discussion
3.1 Characterization of dried precursors and products after calcinations
The dried gel B (Zr(OH)4) prepared by double emulsion method was used to measure DTA-TGA curves, and the results are shown in Fig.1. There is an apparent endothermal peak at about 180 ℃, which corresponds to the removing process of the bonded water. The rapid mass loss during this process indicates that the coalescent water is not removed at lower temperature, such as the drying temperature (about 80 ℃). The organic matters in Zr(OH)4 gel decompose and give out some energy, which results in an exothermal peak at 310 ℃, as shown in the curve. Furthermore, there is a sharp exothermal peak at 480 ℃, which indicates that zirconia powders are crystallized during the calcinations. At the same time, it can be seen from the XRD pattern(Fig.2) that the sharp diffraction peaks at 600 ℃ indicate that

Fig.1 DTA-TGA curves of gel B (Zr(OH) 4) at heating rate of 10 ℃/min
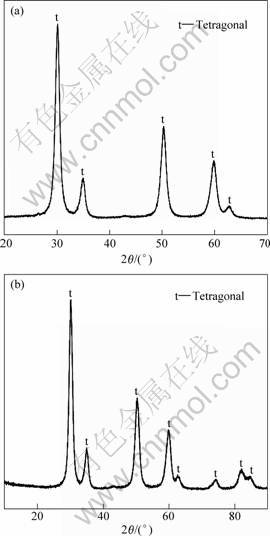
Fig.2 X-ray patterns of ZrO2 powders samples A (a) and B (b)
crystallization is finished and 100% tetragonal phase is obtained. But the breadth of XRD peaks is comparatively broad, and the overall broadening of XRD peaks comprises two effects: one arising from the small coherent grain size and the other arising from the atomic level microstrain. Because the peak width resulting from a small grain size effect alone can be described by the Scherrer equation[14], and the mean dimension of the grains dXRD can be obtained.
3.2 Particle characterization of ZrO2 powders
Fig.3 shows the particle size distribution of the calcined ZrO2 powders at 600 ℃ for 2 h. Samples A and B were respectively prepared via a single emulsion and a double emulsion processing routes. The average particle size of sample A is almost twice as large as that of sample B. What’s more, the particle size distribution of the former covers a wide size range from 40 nm up to 2 um. In contrast, the particle size of sample B, which ranges from 10 nm up to 900 nm, is smaller than that of sample A. As to the reason for particle size distribution difference, it is likely that the single emulsion processing route leads to local high consistency during titration process, and thus causes the local big particle size.
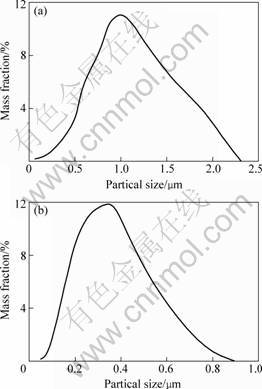
Fig.3 Particle size distribution of ZrO2 powders samples A (a) and B (b)
According to the results of BET, the average particle size dBET was obtained from the following equation and shown in Table 1.
d=6/(S?ρ) (1)
where S is the specific surface area of the sample (m2/g), ρ is the theoretical density of the sample (g/cm3), and d is the average particle size of the sample (nm). The particles are assumed to be spheres. Similarly, according to the results of XRD, the particle size of powders dXRD was obtained from Scherrer relationship, shown in Table 1 too.
Table 1 Mean particle size and specific surface area of ZrO2 (Y2O3) powder

It can be seen from Table 1 that the mean particle size calculated from BET is bigger than that measured from TEM and calculated from XRD with Scherrer formula. The reason is that with the particle size of powders achieving nanometer grade, the specific surface area and surface energy increase, and the surface force between particles strengthens, which leads to micro-agglomeration of powders. Therefore, N2 is not able to fully wrap particles, thus the measured values of specific area are smaller than the real values because N2 absorbed by particles surface is fewer. As a result, the particles size calculated from Eqn.(1) is bigger, but the difference of the three diameters is small from Table 1, which is a good indication of the low degree of agglomeration [15]. Furthermore, it indicates the obvious effect for the emulsion method to prevent the agglomeration between particles. But as shown in Fig.4, the particles agglomeration occurs in both the zirconia powders, and sample B exhibits a lower degree of particles agglomeration than sample A, which matches to Table 1, where dB is smaller than dA. The lower degree of particles agglomeration in sample B indicates the character of powders with the double emulsion processing route is better than that with the single emulsion processing route. The difference in these two zirconoa powders’ particle sizes can be accounted as follows: in the single emulsion processing route, titrating ammonia solution into the micro-emulsion containing Zr(NO3)4 leads to an apparent increase in the overall aqueous phase content of emulsion, then the overall size of aqueous droplets enlarges. The size of aqueous droplets as reactants finally determines the particle size of nanometer powders. In the double emulsion processing route however, combining the two emulsions containing the same amount of aqueous phase does not result in an increase in the overall content of aqueous phase in the mixed emulsion, therefore, the oxalate precursor formed of sample B is smaller than that of sample A, so the particle sizes of sample A are bigger than those of sample B. Especially to sample B, the reactants Zr(NO3)4 and NH3.H2O have to respectively cross the block of the oil phase before contact and subsequent reaction, so the reaction velocity is relative slow. The reaction becomes more even, and leads to the particle size distribution more uniform. At the same time, the spherical degree of sample B is better than that of sample A.
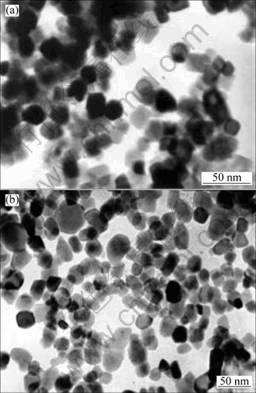
Fig.4 TEM images of ZrO2 powders samples A (a) and B (b)
4 Conclusions
1) The higher productivity tetragonal phase ZrO2 nanometer powders are obtained by using xylol as oil phase, span-80 as surfactant and an aqueous solution containing zirconia or ammonia as water phase, and the best volume ratio is Voil∶Vsurfactant∶Vaqueous=95∶5∶25. According this ratio, ZrO2 powders with average size of 15 nm are obtained.
2) The spherical powders with less agglomeration can be prepared via either the single emulsion processing route or the double emulsion processing route. But compared with the single emulsion processing rout, the powders prepared via the double emulsion processing route display smaller particles and more even size distribution.
References
[1] CAVALLI R, MARENGO E, CAPUTO O, UGAZIO E, GASCO M R. Effect of alcohols with different structures on the formation of warm o/w microemulsions[J]. Journal of Dispersion Science and Technology, 1996, 17: 717-734.
[2] LEE M H, TAI C Y, LU C H. Synthesis of spherical zirconia by precipitation between two water/oil emulsions[J]. Journal of the European Ceramic Society, 1999, 19: 2593-2603.
[3] WANG J, EE L S, NG S C, CHEW C H, GAN L M. Reduced crystallization temperature in a microemulsion-derived zirconia precursor[J]. Material Letters, 1997, 30: 119-124.
[4] JOO J, YU T, KIM Y Y, PARK H M, WU F, ZHANG J Z, HYEON T. Multigrain scale synthesis and characterization of monodisperse tetragonal zirconia noancrystal[J]. J Chem Soc, 2003, 125: 6553- 6557.
[5] ZHAN Zi-li, SONG Wen-hui, JIANG Deng-gao. Preparation of nanometer-sized In2O3 particles by a reverse microemulsion method[J]. Colloid and Interface Science, 2004, 271(2): 366-371.
[6] HUSEIN M M, RODIL E, VERA J H. A novel method for the preparation of silver chloride nanoparticles starting from their solid powder using microemulsions[J]. Colloid and Interface Science, 2005, 288(2): 457-467.
[7] PILENI M P. Reverse micelles as microreactors[J]. J Phys Chem, 1993, 97: 6961-6973.
[8] KAWAI T, FUJINO A, KON-NO K. Synthesis of monodispersed ZrO2 particles in polyoxethylated nonionic reverse micelles[J]. Colloids Surf A, 1996, 109: 245-253.
[9] LEE M H, TAI C Y, WU Y C. Control of zorconia participle size by using two-emulsion precipitation technique[J]. Chem Eng Sci, 2001, 56: 2389-2389.
[10] HUANG Yong, MA Tian, YANG Jin-long. Preparation of spherical ultrafine zirconia powder in microemulsion system and its dispersibility[J]. Ceramics International, 2004, 30(5): 675-681.
[11] TAI C Y, HSIAO B Y, CHIU H Y. Preparation of spherical hydrous-zirconia nanoparticles by low temperature hydrolysis in a reverse microemulsion[J]. Colloids and Surfaces A: Physicochemical and Engineering Aspects, 2004, 237(1-3): 105-111.
[12] GUO Yi-ming, ZHAO Jing-zhe, YANG Shao-feng. Preparation and characterization of monoclinic sulfur nanoparticles by water-in-oil microemulsions technique[J]. Powder Technology, 2006, 162(2): 83-86.
[13] XING De-song, SHI Jian-xin, GONG Meng-lian. Uperfine Sr2CeO4 powder with blue-emission prepared by microemulsion method[J]. Materials Letters, 2005, 59(8-9): 948-952.
[14] LIMA R S, KUCUK A, BERNDT C C. Integrity of nanostructured partially stabilized zirconia after plasma spray processing[J]. J Mater Sci and Eng A, 2001, A313: 75-82.
[15] KLEIN S, WINTERER M, HAHN H. Reduced pressure chemical vapor synthesis of nano-crystalline silicon carbide powders[J]. J Chem Vap Deposition, 1998, 4(4): 143-149.
(Edited by CHEN Wei-ping)
Corresponding author: CHANG Ying; Tel: +86-731-8876566; Fax: +86-731-8830161; E-mail: wlcy@mail.csu.edu.cn