J. Cent. South Univ. Technol. (2008) 15: 136-140
DOI: 10.1007/s11771-008-0027-6

Application of neural network to prediction of plate finish cooling temperature
WANG Bing-xing(王丙兴), ZHANG Dian-hua(张殿华), WANG Jun(王 君),
YU Ming(于 明), ZHOU Na(周 娜), CAO Guang-ming(曹光明)
(State Key Laboratory of Rolling and Automation, Northeastern University, Shenyang 110004, China)
Abstract: To improve the deficiency of the control system of finish cooling temperature (FCT), a new model developed from a combination of a multilayer perception neural network as the self-learning system and traditional mathematical model were brought forward to predict the plate FCT. The relationship between the self-learning factor of heat transfer coefficient and its influencing parameters such as plate thickness, start cooling temperature, was investigated. Simulative calculation indicates that the deficiency of FCT control system is overcome completely, the accuracy of FCT is obviously improved and the difference between the calculated and target FCT is controlled between -15 ℃ and 15 ℃.
Key words: plate; heat transfer coefficient; mathematical model; back propagation (BP) neural network
1 Introduction
One of the important technological parameters during plate cooling process is FCT(finish cooling temperature). Improving the controlled accuracy of FCT is a key problem to improve the mechanical properties of plate[1-4]. Provided with the advantages of the powerful cooling ability, good controllability, lower possibility of trouble, laminar cooling system is used widely as accelerated cooling system after plate hot rolling[5]. A laminar cooling system combined with feed-forward control and self-learning model is working on-line in the national plate steel works. However, laminar cooling is a complex nonlinear process with strongly dynamic randomness. The fluctuation of the system performance such as the precision of measure instrument or control valves, time-lag produced by communication and control system cannot be reflected by the on-line control system[6]. In this study, a method combining traditional mathematical model with BP neural network was introduced to provide cooling regulations and meet production technology request and achieve plate FCT within narrow tolerances.
2 Combination of BP neural network with mathematic model
BP neural network capable of reliably characterizing nonlinear functional relationships and estimating complex process behavior is widely used in the field of plate rolling[7-14]. However, the stability of control model cannot be guaranteed only by neural networks. Under this condition, a method combining traditional mathematical model with BP neural network is introduced to calculate convective heat transfer coefficient in the advanced control system[9].
2.1 Introduction of mathematic model
In order to know the plate temperature distribution at an arbitrary time, the finite difference equation is applied to calculating temperature field. Ignoring the thermal conductivity along with the length direction and translating the latent heat from phase transformation into specific heat, the equation of heat equilibrium along with the width and thickness direction without internal heat source can be established as follows:
(1)
where a(a=λ/(ρc)) is coefficient of temperature conductivity, T is plate temperature, λ is thermal conductivity, ρ is density, c is specific heat, τ is cooling time, x is coordinate of width direction, y is coordinate of thickness direction.
The initial condition of the heat equilibrium equation is represented as
Tx,y(τ)=T(x, y, τ) (τ=0, 0≤x≤w/2, 0≤y≤h/2) (2)
The boundary condition of the heat equilibrium equation is represented as
(3)
where α is the heat transfer coefficient, TW is the water temperature, w is the plate width, h is the plate thickness. And the heat transfer coefficient α is a key parameter to solve the above heat equilibrium equation. Only the most important influencing parameters, such as cooling water flux and plate surface temperature are included in the simplified mathematic model:
(4)
where KA is self-learning factor of heat transfer coefficient (shortened as the self-learning factor), Q is water flux, a1, a2 and a3 are regression coefficients.
2.2 Foundation of BP neural network model for self-learning factor
The influencing parameters such as start cooling temperature (SCT), run-out table speed, plate thickness, ambient temperature etc, and various unpredictable disturbance[10] are not expressed in Eqn.(4). To find the multidimensional dependencies between process parameters and heat transfer coefficient, a BP neural etwork with three layers structure of 9×15×1 is established to predict the self-learning factor.
(5)
The neural network with a back-propagation algorithm needs to be trained with training data in order to learn the non-linear and complex relationships between input and output data, so a steady-state original database was established. As shown in Table 1, 9 parameters including water temperature, water tank level and plate thickness etc, were chosen as the input neurons, and the output neuron is the self-learning factor. Because of the ANN learning under supervision, some necessary methods are used to deal with the original data: 1) picking out the data by manual operating; 2) picking out the data out of the permit range of production conditions; 3) the temperature measurement points are along with the centerline of plate. Each operating point was validated as good or bad with respect to the quality of the product and only good points are kept; 4) picking out the data satisfying the function |X-
|/(3R)>1, where X is relative error and R is standard error,
is mean value of X.
The following equation is adopted to normalize the input neurons:
(6)
where xp is sample data, xmin is minimal value of sample data, xmax is maximal value of sample data.
The activation function is style sigmoid.
(7)
The root mean square error of all output neurons E is used as the index to update weight.
Table 1 Parameters of sample for BP neural network training and testing
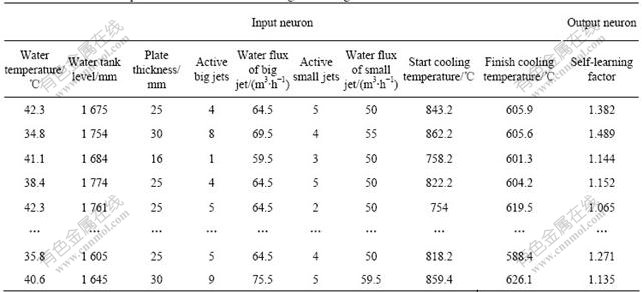
(8)
where
are actual outputs,
are target outputs, m is number of training sample group, q is output layer.
After testing times without number, the parameters of the BP neural network in Table 2 is validated to be with the best performance.
Table 2 Performance parameters of BP neural network

3 Analysis of prediction result and influencing parameters 3.1 Result analysis
1 000 groups of samples were used for BP network training and 150 groups for testing. Apparently, most of the calculated self-learning factors match the practical ones as shown in Fig.1.
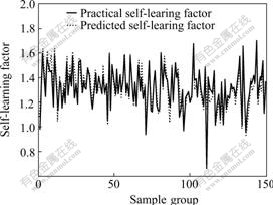
Fig.1 Comparison of predicted value and practical value of self- learning factor
Analyzing the cooling reports after day-to-day rolling operation, the result is satisfactory that about 90% of difference between target and practical FCT changes between -20 ℃ and 20 ℃. However, the out-of- tolerance of practical FCT is still observed regularly. Fig.2 demonstrates that: 1) as soon as the plate specification is changed, the difference between the practical and the target FCT (600 ℃) of the following several plates become comparatively large; 2) the poor abilities of anti-interference, fault-tolerance and stability of the on-line system are observed. Once the cooling condition is changed such as the measurement accuracy of pyrometer losing, bed point for measuring temperature chosen, water temperature or water tank level beyond the safe range, the controlled accuracy of the following several plates FCT will fluctuate. The reason is that in the traditional model, the self-learning coefficient is influenced strongly by the former so that several following plates are necessary to be used to modify the unreasonable self-learning coefficient.
Corresponding to practical FCT, the difference of predicted FCT obtained from off-line simulation system is relatively small. The results indicate that the new method developed from the mathematic model and neural network overcomes the deficiency of on-line system, avoids the violent fluctuation of FCT and improves controlled accuracy of laminar cooling system. The majority of FCT is between –15 ℃ and 15 ℃.
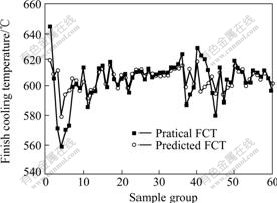
Fig.2 Comparison of predicted value and practical value of FCT
3.2 Effect of influencing parameters on self-learning factor
Based on the powerful data-mining ability of artificial neural network, the neural network model of the self-learning factor was used to investigate the effect of input parameters on heat transfer coefficient. By changing only one influencing parameter, the variation of the self-learning factor due to the change of this parameter can be obtained.
3.2.1 Tanks of active headers and water flux
The water flux and the arrangement of tanks of active headers, which not only determine the efficiency of cooling water but also influence the ultimate microstructure and mechanical properties of the rolling plates, are essence parts of control strategy of laminar cooling system[11]. As illustrated in Figs.3(a) and (b), the self-learning factor is not obviously changed along with the water flux. However, the effect of arrangement of active tanks has not been reflected yet. As shown in Fig.3(c), the self-learning factor is larger if only smaller tanks are activated. With the number of active tanks increasing, the self-learning factor deceases obviously. When active tanks are enough, the self-learning maintains a smaller value nearly to 0.6. This phenomenon reflects that the cooling water efficiency of the isolated or alternative active tanks is higher than the continuous ones.
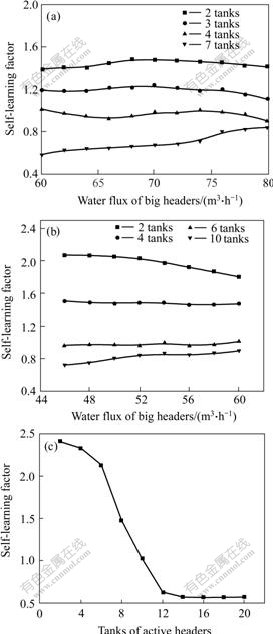
Fig.3 Self-learning factor changing with water flux and number of tanks of active headers: (a) Water flux of big headers; (b) Water flux of small headers; (c) Active headers
3.2.2 Start cooling temperature (SCT) and finish cooling temperature (FCT)
The heat transfer is caused by the temperature difference between plate surface and the cooling water so the plate surface temperature is one of the important parameters during heat transfer process. As shown in Fig.4(a), due to the larger temperature difference between metal surface and the water coolant, the self-learning factor increases obviously along with start cooling temperature. But along with finish cooling temperature increasing, the self-learning factor fluctuates surrounding the constant 1.0(Fig.4(b)).
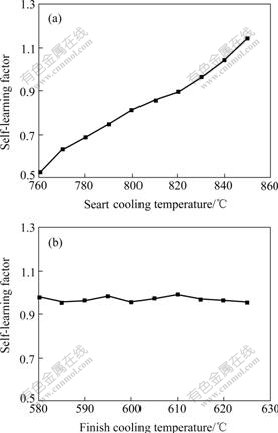
Fig.4 Self-learning factor changing with SCT and FCT: (a) Start cooling temperature; (b) Finish cooling temperature
3.2.3 Water tank level and water temperature
As expected, the self-learning factor increases appreciably with the increase of water tank level in the mass(Fig.5(a)). The reason is that the laminar water with higher pressure is more powerful to penetrate the water film remained on plate surface, so as to increase the efficiency of cooling water. On the other hand, the cooling water with higher temperature has lower cooling capacity. As a result, it is also reasonable that along with water temperature increasing[12], the self-learning factor decreases appreciably as illustrated in Fig.5(b).
Fig.5 Self-learning factor changing with water tank level and water temperature: (a) Water tank level; (b) Water temperature
4 Conclusions
1) To overcome the deficiency of laminar cooling system dug out from practical data, a new model developed from the combination of a BP neural network and traditional mathematical model is brought forward to predict the plate FCT.
2) Simulative calculation indicates that the defi- ciency is overcome completely. The accuracy of FCT is also obviously improved and the difference between the calculated and target FCT is controlled between -15 ℃ and 15 ℃. This method has an anticipant application on- line in the future.
3) The self-learning factor of heat transfer coeffic- ient changing along with influencing factors is investigated by the BP neural network model. The results indicate that the factors including water tank level, water temperature, number of active tanks and start cooling temperature, influence heat transfer strongly, but the effects of water flux of headers and finish cooling temperature are weaker.
References
[1] FIIIPOVIC J, VISKANTA R, INCROPERA F P, VESLOCKIT A. Cooling of a moving steel strip by an array of round jets[J]. Steel research, 1994, 65(12): 541-547.
[2] MUKHOPADHYAY A, SIKDAR S. Implementation of an on-line run-out table model in a hot strip mill[J]. Journal of Materials Processing Technology, 2005, 169: 164-172.
[3] SERAJZADEH S. Prediction of temperature variations and kinetics of austenite phase change on the run-out table[J]. Applied Mathematical Modelling, 2003, 27: 861-875.
[4] CHEN S J, TESENG A A. Spray and jet cooling in steel rolling[J]. Int J Heat and Fluid Flow, 1992, 13(4): 358-367.
[5] WEI Shi-zheng, WANG Zhao-dong, ZHAO De-wen, LIU Xiang-hua, WANG Guo-dong. Controlled cooling technology for medium plate[J]. Journal of Iron and Steel Research, 2002, 14(5): 67-72. (in Chinese)
[6] van DITZHUIJZEN G. Controlled cooling of hot rolled strip: A combination of physical modeling, control problems and practical adaption[J]. IEEE Transactions on Automatic Control, 1993, 38(7): 1060-1065.
[7] AIRKKA P. Advanced control methods for industrial process control[J]. IEE Computing & Control Engineering, 2004, 15(6/7): 18-23.
[8] BISSESSUR Y, MARTIN E B, MORRIS A J, KITSON P. Fault detection in hot steel rolling using neural networks and multivariate statistics[J]. IEE Control Theory Appl, 2000, 147(6): 633-640.
[9] SUN Xiao-guang. Application of synergetic artificial intelligence to the scheduling in the finishing train of hot strip mills[J]. Journal of Materials Processing Technology, 1996, 60(5): 405-408.
[10] GUO Ren-min. Heat transfer of laminar flow cooling strip acceleration on hot strip mill run-out tables[J]. Iron and Steel Maker: IGSM, 1993, 20(8): 49-59.
[11] AUZINGER D, PARZER F. Process optimization for laminar cooling[J]. Iron and Steel Engineer, 1998(8): 45-49.
[12] LIU Zheng-dong, SAMARASEKERA I V. Application of cooling water in controlled run-out table cooling on hot strip mill[J]. J Iron and Steel Res, 2004, 11(3): 15-23.
[13] ZHOU Fu-qiang, CAO Jian-guo, ZHANG Jie, YIN XIAO-qing, JIA Sheng-hui, ZENG Wei. Prediction model of rolling force for tandem cold rolling mill based on neural networks and mathematical models[J]. Journal of Central South University: Science and Technology, 2007, 37(6): 1155-1160. (in Chinese)
[14] ZHANG Cai, TAN Jian-ping. Strip flatness pattern recognition based on genetic algorithms-back propagation model[J]. Journal of Central South University: Science and Technology, 2006, 37(2): 294-299. (in Chinese)
(Edited by YANG Hua)
Foundation item: Projects(50634030) supported by the National Natural Science Foundation of China
Received date: 2007-04-02; Accepted date: 2007-07-18
Corresponding author: WANG Bing-xing, PhD; Tel: +86-24-83688547; E-mail: wbxang@126.com