
Microstructural evolution of aluminum alloy 3003 during annealing
WU Wen-xiang(吴文祥)1, ZHANG Xin-ming(张新明)2, SUN De-qin(孙德勤)1,
HU Guo-qiang(胡国强)1, LIU Guo-jin(刘国金)1
1. Suzhou Institute for Nonferrous Metals Processing Technology, Suzhou 215026, China;
2. School of Materials Science and Engineering, Central South University, Changsha 410083, China
Received 28 July 2006; accepted 15 September 2006
Abstract: The microstructural evolution of cold-rolled aluminum alloy 3003 during annealing was investigated by means of micro-hardness measurement, electrical resistivity measurement, optical microscopy and transmission electron microscopy. The interaction of recrystallization and precipitation of aluminum alloy 3003 was also discussed. The results show that the recrystallized grain size of cold-rolled aluminum alloy 3003 is strongly affected by precipitation during annealing. When precipitation occurs prior to recrystallization at low temperature(300 ℃), the grain structure becomes coarse, and the precipitation process is affected by the presence of lattice defects, i.e. high cold reduction results in a large number of precipitates. When annealing at 500 ℃, however, for the recrystallization is prior to precipitation, the precipitation is independent of cold deformation reduction and a fine, equiaxed grain structure is obtained.
Key words: aluminum alloy 3003; microstructural evolution; recrystallization; precipitation; electrical resistivity
1 Introduction
Aluminum alloy 3003 foils are widely used as the cathode material of electrolytic capacitors, and their high specific capacitance is one of the properties that material scholars are busily engaged in seeking[1-4]. It is well established that second phase particles have a strong effect on the specific capacitance of the cathode foils of aluminum alloy 3003[5]. The solubility of Mn and Fe in aluminum matrix is very low at room temperature, and they are often precipitated in the form of (Mn, Fe)Al6. If dispersed (Mn, Fe)Al6 is homogeneously precipitated in the matrix, the etched surface of the foil can considerably increase in area, and as a result, the specific capacitance of the cathode foils is enhanced largely. Meanwhile, as a non-heat treatable alloy, the mechanical properties of aluminum alloy 3003 are influenced by grain size and dislocation density. Consequently a major concern during processing of aluminum alloy 3003 foils is the control of the second phase particle and grain size.
Previous investigations of 3003 cathode aluminum foils have focused on composition[6], homogenization[7], and cold rolling[8]. However, information about the recrystallization behavior and precipitation process during intermediate annealing is still lacked to date. This work is conducted to study the microstructural evolution of aluminum alloy 3003 during intermediate annealing. Specifically, the interaction between recrystallization and precipitation of aluminum alloy 3003 during intermediate annealing as well as its effect on the microstructures is investigated. Therefore, the purpose of this work is to provide information that enables optimization of intermediate annealing parameters for 3003 cathode aluminum foils.
2 Experimental
The materials used in this investigation were 3003 alloys with the following chemical compositions(all in mass fraction, %): Mn 1.19, Fe 0.56, Si 0.28, Cu 0.15 and balance Al. After homogenization at 610 ℃ for 36 h, aluminum alloy 3003 ingots were deformed by hot rolling to 3.5 and 1.7 mm, respectively. Then, the hot bands were cold rolled at room temperature to 0.5 mm with reduction of about 85% and 70%, respectively. To study the recrystallization and precipitation behavior of these samples, a series of isochronous annealing experiments were conducted at various temperatures between 250 and 600 ℃ for 30 min in a salt bath with temperature stability of ±3 ℃. The deformed samples with 85% cold rolling reduction in thickness were isothermally annealed at 300 and 500 ℃, respectively. During annealing samples were taken out of the salt bath after different holding time. The softening behavior of the annealed samples was quantified by measuring the change of the microhardness, as a function of holding time and temperature.
The microhardness was determined using 5 N load and 30 s loading time with a standardized Vickers indenter. Prior to anodizing using Barker’s reagent (50 mL HBF4 in 950 mL H2O), the samples were electropolished using a solution of 10 mL HClO4 in 90 mL C2H5OH to remove the deformation layer. The microstructures were examined using polarized optical microscopy. Electrical resistivity measurements were done to study the precipitation behavior during annealing. TEM samples were cut in the long-transverse(L-S)plane, mechanically polished and finally twin-jet polished using a solution of 30% HNO3 and 70% CH3OH at about -25 ℃. TEM observations were carried out on TECNAI G2 20 electron microscope.
3 Results and discussion
3.1 Softening behavior
The softening behavior of the cold-rolled aluminium alloy 3003 during annealing was investigated by microhardness measurements. Fig.1 shows the microhardness evolution at 300 and 500 ℃ for various holding time. In theory, the microhardness evolution should include the contributions from both softening process and precipitation. But as for a non-heat treatable alloy the microhardness of aluminum alloy 3003 is not sensitive to the precipitation process. Therefore the microhardness measurement can be considered only with the softening behavior.
Assuming that the microhardness for the onset and end of recrystallization is essentially independent of processing history and annealing temperature, the fraction recrystallized, changing in annealing process, can be obtained from the microhardness measurement as:
(1)
where Frex is the fraction recrystallized, Hdef the microhardness of the sample in the as-deformed state, Hrex the microhardness of completely recrystallized sample, Ht the instantaneous microhardness after annealing time
, i.e. ranging from Hdef to Hrex. Using Eqn.(1), the fraction recrystallized can be calculated, as shown in Fig.1. It can be seen that the recrystallization softening behavior is strongly affected by annealing temperature. The time required for complete recrystallization is approximately 2 s at 500 ℃ as compared to approximately 2 000 s at 300 ℃.
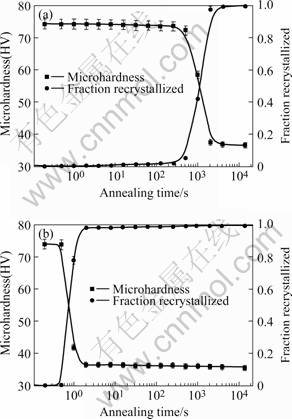
Fig.1 Microhardness as function of holding time during annealing at 300 ℃(a) and 500 ℃(b) in samples with 85% cold rolling reduction
3.2 Microstructural evolution during annealing
To study the precipitation process, electrical resistivity measurements were conducted on aluminum alloy 3003 at various time during isothermal annealing after 85% cold rolling reduction. Electrical resistivity measurements have often been used as an indirect evidence of changes in the solid solution level of the alloy[9-10]. However, there can also be an inneglectable contribution to resistivity in aluminum alloys from dislocation. It is, thus, necessary to carefully distinguish these two effects in order to provide insight into the changes in solute level during annealing. Fig.2 shows the change of the resistance variation ratio as a function of annealing time at 300 and 500 ℃, respectively. As shown in Fig.2, there is a large decrease in the resistivity of aluminum alloy 3003 during annealing, which consists of the decrease due to the precipitation of dispersoids such as Al(Fe,Mn)Si, (Fe, Mn)Al6 and that due to the annihilation of lattice defects introduced by cold rolling deformation. The differentiated curve dρ/d(lnt) is plotted to make the reaction steps more evident. Fig.2 indicates that for the samples with 85% reduction followed by annealing at low temperature(300 ℃), only one maximum is measured; while for the samples annealed at high temperature(500 ℃), two maxima are found. According to HOLM and HORNBOGEN[11], these processes can be explained by the interaction of recrystallization and precipitation at different temperatures. At low temperature the precipitation of Mn atoms and recrystallization process occur simultaneously, so that only one maximum appears. At high temperature, however, little Mn can be precipitated during recrystallization. Therefore a second maximum occurs after the recrystallization is completely finished, due to the precipitation by homogeneous nucleation in the recrystallization matrix. The change of electrical resistivity is of two-step reaction with increasing holding time at 500 ℃ as compared with one-step reaction at 300 ℃. The time at which recrystallization or precipitation starts according to the microhardness and electrical resistivity measurements, is marked on the resistivity curves in Fig.2.
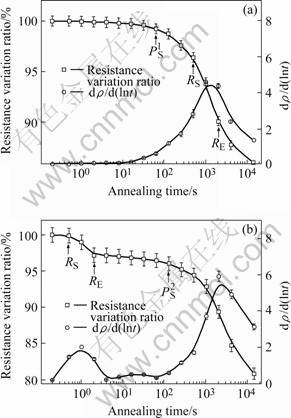
Fig.2 Variation of electrical resistivity of aluminum alloy 3003 with 85% reduction during isothermal annealing at 300 ℃ (a) and 500 ℃ (b) (RS and RE: onset and end of recrystallization;
and
: onset of precipitation before and after complete recrystallization)
The evolution of the recrystallized grain structure for aluminum alloy 3003 with annealing at various temperatures was studied by optical metallography. Fig.3 shows the different grain structures obtained from annealing at low and high temperatures((a) 300 ℃ and (b) 500 ℃, respectively) for 30 min. At low temperature(300 ℃), recrystallization is complete and a coarse grain structure is obtained. The average recrystallized grain size is 40-50 μm. At high temperature(500 ℃), however, the recrystallized samples have a fine equiaxed grain structure with an average grain size of 10-20 μm. The recrystallized grain size in the sample annealed at 500 ℃ is much finer than that in the sample annealed at 300 ℃. This difference is due to the interaction between precipitation and recrystallization.
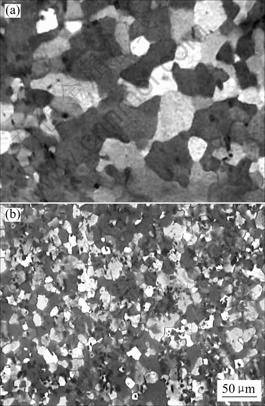
Fig.3 Grain structures of 3003 alloy after 85% cold rolling followed by annealing at 300 ℃ (a) and 500 ℃ (b) for 30 min
There is a large number of precipitates on subgrain boundaries prior to recrystallization when annealing at 300 ℃, which prevents the movement of dislocations during recovery and subsequent nucleation of recrystallization, and finally, results in a coarse grain structure, as shown in Fig.3(a).
When annealing at 500 ℃, however, precipitation takes place after complete recrystallization, and the fine particles formed in the recrystallized matrix pin grain boundaries, and prevent growth of recrystallized grain, leading to a fine equiaxed grain structure(Fig.3(b)).
Precipitation is a thermally activated process, including nucleation and growth of a second phase. The effect of deformation on precipitation kinetics often attributes to the increase of dislocation density, which increases both the nucleation site density and diffusivities of precipitation-forming elements in the material.
Fig.4 shows the change of electrical resistivity in aluminum alloy 3003 after 70% and 85% reduction, respectively, followed by isochronal annealing at various temperatures. According to the previous experiment, the electrical resistivity change due to annealing is very small compared with that due to precipitation, so the changes of the solid solution level of aluminum alloy 3003 are the major process leading to a large decrease in electrical resistivity. It is determined from Fig.4 that the precipitation is accelerated by cold deformation at low temperatures and the acceleration is marked at 300 ℃. Consequently, two minima appear in the isochronal resistivity curves of the deformed samples. Increasing cold reduction results in stronger precipitation process at 300 ℃. The precipitation process taking place at 300 ℃ strongly depends on cold rolling reduction, and it is assumed to be governed by pipe diffusion of alloying atoms and nucleation of particles at lattice defects, such as dislocations and subgrain boundaries. A second precipitation occurs at 500 ℃, however, it seems to be independent of the previous deformation, taking place in the recrystallized matrix by volume diffusion and heterogeneous nucleation. Above 500 ℃ the dissolution of alloying elements is the dominating process.
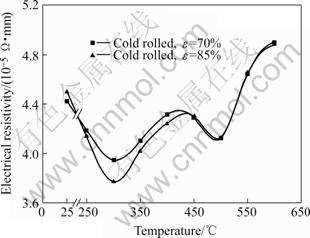
Fig.4 Isochronal annealing curves of electrical resistivity in aluminum alloy 3003 with different cold rolling reductions
It is observed by TEM that there are some very fine dispersoids with size of about several nanometers in aluminum alloy 3003 when it is annealed at 300 ℃. This result agrees with the electrical resistivity curve. The morphology of the dispersoids precipitated during annealing at 300 ℃ for 30 min is shown in Fig.5. It can be seen that most of the dispersoids are in globular shape and are located within subboundaries or on dislocations, which indicates that the subboundaries or dislocations act as nucleation sites for the dispersoids. Based on the above analyses, when the sample is annealed at 300 ℃, it can be characterized by pipe diffusion of dissolved atoms and their precipitation at dislocations and subgrain boundaries. So the precipitation process during annealing at 300 ℃ is affected by the presence of lattice defects, and thus, is strongly correlated with the cold rolling reduction prior to annealing, i.e. high cold reduction results in a large number of precipitates. With increasing cold rolling reduction, the density of dislocations increases rapidly, and then the nucleation sites for the dispersoids increase, which are in favor of the precipitation of the second phase, resulting in a lower electrical resistivity.

Fig.5 TEM image of 85% cold rolled aluminum alloy 3003 annealed at 300 ℃ for 30 min
When annealing at 500℃, however, since recrystallization is completely finished in about 2 s, the dislocations formed during cold-rolling deformation are eliminated before the precipitation starts. The precipitation process takes place in the recrystallized matrix by volume diffusion and heterogeneous nucleation. Therefore, with increasing temperature, cold rolling reduction has little effect on the precipitation kinetics, and the precipitation is independent of cold deformation reduction, resulting in a similar change of electrical resistivity, as shown in Fig.4.
4 Conclusions
1) When annealing at 300 ℃, precipitation process in aluminum alloy 3003 is affected by the presence of lattice defects, i.e. high cold reduction results in a large amount of precipitates, and the grains become coarse for the precipitation prior to recrystallization.
2) When annealing at 500 ℃, however, for the recrystallization prior to precipitation, the precipitation is independent of cold deformation reduction and a fine, equiaxed grain structure is obtained.
References
[1] ALUMINUM S. Aluminum Alloy Foil for Cathode of Electrolytic Capacitor [P]. JP88106A-KoKai. Japan, 1988.
[2] Sumitomo Light Metals. Manufacturing Aluminum Foil for Ele- ctrolytic Capacitor Cathode [P]. JP88137505A-KoKai. Japan, 1988.
[3] WU Wen-xiang, ZHANG Xin-ming, TANG Jian-guo, JIAN Xiong, LIU Sheng-dan. Microstructures evolution of 3003 aluminum alloy foil during preparing process[J]. Heat Treatment of Metals, 2006, 31(3): 36-39.(in Chinese)
[4] ZHANG Hong-mei, MIAO Qun, LI Yong, LI Sheng-ying, FU Zhong-guo. Factors of affecting specific capacitance of 3003-3 aluminum alloy foil for negative electrode[J]. Process Technology of Light Alloy, 2005, 33(11): 27-29. (in Chinese)
[5] ZHANG Xin-ming, JIN Li, XIAO Ya-qing, JIAN Xiong. Effect of microstructure on specific capacitance of AA3003 aluminum alloy[J]. Trans Nonferrous Met Soc China, 2003, 13(5) : 1030-1034.
[6] VAN ALPHEN L, NAUWEN P, SLAKHORST J. Relation between the composition, the structure parameters and the etchability of alloyed Al-cathode foils for electrolytic capacitors [J]. Z Metallkde, 1979, 70(3): 158-167.
[7] JIAN Xiong, ZHANG Xin-ming, TANG Jian-guo, LI Hui-zhong, WU Wen-xiang, ZHOU Zhuo-ping. Effect of different homogeniza- tion treatment on specific capacitance of 3003 aluminum alloy[J]. Trans Mater and Heat Treatment, 2005, 26(2): 39-42. (in Chinese)
[8] ZHANG Xin-ming, JIAN Xiong. Effects of cold deformation before and after intermediate annealing on specific capacitance of cathode foils of 3003 aluminum alloy[J]. The Chinese Journal of Nonferrous Metals, 2005, 15(3): 334-337. (in Chinese)
[9] LI Y J, ARNBERG L. Precipitation of dispersoids in DC-cast 3003 alloy[J]. Materials Science Forum, 2002, 396/402: 875-880.
[10] SJOLSTAD K, ENGLER O, TANGEN S, MARTHINSEN K, ERIK N. Texture evolution of an AA3XXX alloy after different homogenization treatments[J]. Materials Science Forum, 2002, 396/402: 463-468.
[11] HOLM K, HORNBOGEN E. Annealing of supersaturated and deformed Al-0.042wt%Fe solid solutions[J]. J Mater Sci, 1970, 5(8): 655-662.
(Edited by YANG Bing)
Foundation item: Project(2006KJA08) supported by the Science and Technology Development Foundation of CHALCO
Corresponding author: WU Wen-xiang; Tel: +86-512-62585625; E-mail: wwx985@163.com