
CO2 laser welding of 5A06 aluminum alloy plates with
different thicknesses
YU Shu-rong(余淑荣)1, 2, FAN Ding(樊 丁) 1, 2, XIONG Jin-hui(熊进辉)1, CHEN Jian-hong(陈剑虹)1, 2
1. State Key Laboratory of Gansu Advanced Non-ferrous Metal Materials,
Lanzhou University of Technology, Lanzhou 730050, China;
2. Key Laboratory of Non-ferrous Metal Alloys, The Ministry of Education,
Lanzhou University of Technology, Lanzhou 730050, China
Received 28 July 2006; accepted 15 September 2006
Abstract: CO2 laser beam welding of aluminum alloys with different thicknesses was carried out. The influences of laser power and travel speed on the weld width were analyzed. The mechanical characteristics of tailor-welded blanks (TWB) with unequal thickness were evaluated using tensile tests, and the fracture appearance was inspected after tensile tests. The microstructure of welded joints was analyzed by SEM. The results indicate that this alloy can be laser welded with full penetration. All the tensile specimens fracture on the base metal, far from the weld in the transverse direction. The tensile strength and yield strength of TWB are 89% and 91.2% compared with the base metal. The percentage of the thinner plate in the specimen has an important effect on the transverse elongation. The transverse elongation of TWB approaches that of the base metal when the thinner plate has a large percentage in TWB specimen. The weld microstructure shows extra-fine grains. Dendrite exists around weld fusion line and the equiaxed grains in the weld.
Key words: aluminum alloy; laser welding; tailor welded blanks
1 Introduction
In recent years, aluminum alloys are extensively used in transportation with increasing demand for light-mass structures. The main reason is wrought aluminum alloys provide a favorable combination of specific strength, ductility and enhanced formability [1-2]. So aluminum alloys are becoming a substitution for steel in transportation body components.
Tailored welded blank (TWB) is a new technology in the automotive industry. A tailored welded blank is welded metal plate different quality and/or thickness before stamping forming. The combination of sheets with different thickness and/or properties offers various advantages. It is possible to reduce the mass of a specific component, to lower the manufacturing costs and to lower tooling numbers and costs [3-4]. Tailored welded aluminum alloy blanks are in great demand.
Laser beam welding has several advantages over other welding processes. Some difficulties are encountered during laser welding of aluminum alloys owing to the high thermal conductivity and high surface reflectivity (about 96% for CO2)[5]. During the laser welding of aluminum alloys with different thickness, not only general issues of laser welded aluminum alloys such as low absorptivity, porosity and crack[6-7], but also serious issues such as difficult formation, high sensitivity of laser beam to gap and different thickness of the material exist.
Some of the researches on TWB have concentrated on developing welding procedures of aluminum alloys with the same thickness and quantifying the effects of the welding process on the formability of TWBs. VENKAT et al[8] and RAMASAMY et al[9] investigated aluminum alloys 5754-O and 6111-T4 which have the combination of being both weldable and formable. ZHAO and DEBROY[10] also investigated the weld metal composition change of aluminum alloys 5182 during conduction mode laser welding. Low alloy steel[11] was also studied through using of the OSU formability test, full dome height test and a uniaxial tensile test. In this study, 5A06 Al alloy was used. The focus of this research is to develop the welding procedures for CO2 laser beam welding of aluminum alloys with different thicknesses, and to investigate the influences of laser power and travel speed on the weld width and to evaluate the mechanical and microstructure characteristics of welded joints.
2 Experimental
The composition (mass fraction) of 5A06 aluminum alloy (in annealed state) used in this investigation is as follows: 5% Mg, 0.46% Mn, 0.20% Si, 0.16% Fe, 0.10% Cu, and <0.10% Ti. The starting stock for 5A06 was 1.0 mm and 2.0 mm in thickness. Specimens with dimensions of 270 mm×100 mm×1 mm and 270 mm× 100 mm×2 mm were machined from 5A06 sheet materials. The specimens were then ground for square-groove edge preparation, acetone washed and stainless steel wire brushed for surface preparation before welding.
Experiments were performed using a RF excited diffusively cooled CO2 laser with the maximum power output of 3 kW. All welds were made using a 190 mm focus length lens and a diameter of approximately 0.6 mm. During the welding, the lower surfaces were in the same flat and the laser beam leaned to the thicker plate. Argon shielding gas with purity of 99.99% was used for coaxial and back shielding.
The tensile testing was performed and three samples were tested at each parameter. The fracture appearance and microstructure of weld joints were characterized by SEM.
3 Results and discussion
3.1 Effect of welding conditions on weld width
Laser beam welding experiments were performed at different laser power, travel speed and defocused amount (in this study, zero defocused amount is on the upper surface of the thinner plate, positive defocused amount above the surface, negative defocused amount below the surface), respectively.
The results show the welds have full penetration using proper laser welding process. The micro- photographs of welded joints are shown in Figs.1 and 2. The adopted welding conditions were basically as follows: a laser power (p) 1.5 kW, travel speed (v) 1.2 m/min and defocusing distance (fd) -0.9 mm. It can be seen that the weld surfaces are uniform and smooth, and the formation of weld is fine.
Fig.3 shows the effects of laser power on the weld width. Other processing parameters are held constant as follows: v=1.2 m/min; fd=-0.9 mm. Laser output power has an important effect on the formation of the weld. If laser power is too low, splashing and lens contamination will occur owing to high surface reflectivity of aluminum alloys. If laser power is too high, the collapse of the weld will occur owing to high heat input. The weld width increases with increasing laser power.
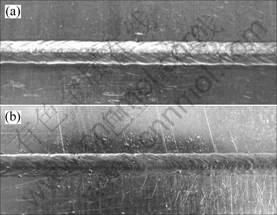
Fig.1 Weld appearances of 5A06 alloy: (a) Face of weld; (b) Back of weld
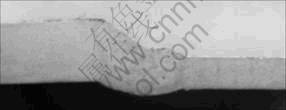
Fig.2 Cross-section image of 5A06 alloy
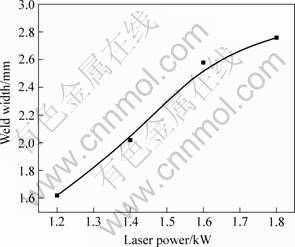
Fig.3 Effects of laser power on weld width
The effect of the travel speed on weld width is shown in Fig.4. For a given laser power, with increasing travel speed, heat input decreases, so the weld width and the area of weld pool decrease. The travel speed affects the weld pool shape and welding quality. The temperature gradient at center and edge of the welding pool, the elimination of heat of liquid aluminum alloys, the width and depth of the molten zone, and the welding pool shape are different at different travel speeds.
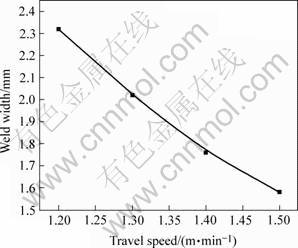
Fig.4 Effects of travel speed on weld width
3.2 Mechanical properties of welds
At present, there is no standard about the shape and size of tensile test specimen of TWB. The one-way tensile experiments at different positions of the weld on TWB were performed in this investigation. The tensile specimens are listed in Table 1.
Table 1 Tensile specimen
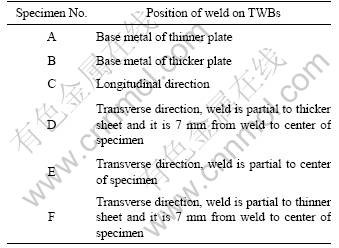
The mechanical properties of the joints with p=1.5 kW, v=1.2 m/min and fd=-0.9 mm are shown in Fig.5. It can be seen that tensile and yield strengths decrease in the longitudinal direction for laser TWB. The tensile strength and yield strength of TWB are 89% and 91.2% of the base metal, respectively. The total elongation of TWB has an evident decrease, and it is about 36.5% that of the base metal.
All the fractures of the specimen occur in the thinner plate and are far from the weld in the transverse direction. The percentage of the thinner plate in the specimen has an important effect on the tensile properties. The tensile properties of TWB approach those of the base metal when the thinner plate has a large percentage in TWB. The transverse elongation of TWB is 61.8% compared to the base metal. When the weld was in the center of TWB, or the thicker plate has a large percentage, the transverse elongations of TWB have a significant decrease (48.1% and 40.8%, respectively).
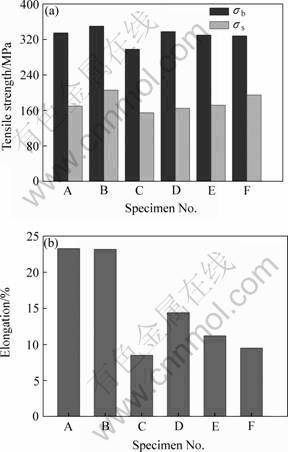
Fig.5 Tensile properties of base metal and TWBs: (a) Tensile strength; (b) Total elongation
3.3 Fracture surface
The result of the fractographic observations of the tensile specimen is shown in Fig.6. The fracture surface displays numerous cup-like depressions. This is indicative of a fracture mode commonly called “dimple rupture” and the mechanism of fracture known as microvoid coalescence[8]. At the bottom of some dimples, many fine particles are observed, and the fracture exhibited a ductile type of failure.
3.4 Microstructure of joints
The microstructures of base metal and the joints of TWB are shown in Fig. 7. The microstructure of the base metal shows β phase (Mg3Al2) dispersed in the grid α(Al) substrate. The microstructure of the weld is finer compared with that of the base metal. Equiaxed grains are observed in the center of the weld. Fig.7(c) shows the microstructure near the fusion line. The right of the fusion line is the microstructure of the heat affected zone, and the left is the microstructure of the weld. The columnar and dendritic microstructures can be observed near the fusion line, and the equiaxed grains can be observed in the center of the weld. All the dendritic microstructures are primary dendrites, and the dendrites become finer from the fusion line to the center of the weld.
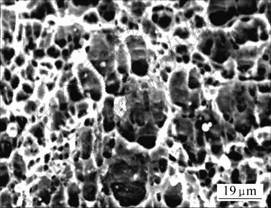
Fig. 6 Fracture surface of TWB tensile specimen (Laser power 1.5 kW and travel speed 1.2 m/min)
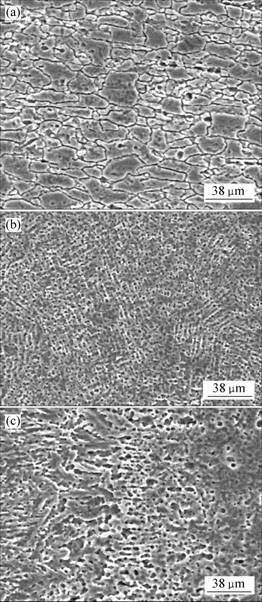
Fig.7 Microstructure of 5A06 and welded joint (Laser power 1.5 kW and travel speed 1.2 m/min): (a) Base metal; (b) Weld mental; (c) Zone near fusion line
4 Conclusions
1) TWB with full penetration and fine formation of 5A06 aluminum alloy with different thicknesses is obtained using the optimum CO2 laser welding process.
2) The tensile property of TWB reduces compared with the base metal, especially the longitudinal elongation has a significant decrease.
3) The tensile specimens of TWB all fractures in the thinner plate and are far away from the weld. The fracture exhibits a ductile type of failure. The transverse tensile deformability is dependant on the percentage of the thinner plate in TWB. The transverse elongation and the deformability of TWB decrease with reducing percentage of the thinner plate.
4) Microstructure of the weld is finer compared with the base metal. The dendrite was observed near the fusion line, and the equiaxed grains were observed in the center of the weld.
References
[1] STEVEN A. Steel cars face a weighty decision [J]. Mechanical Engineering, 1997, 119(2): 56-61.
[2] ROBERT K J. Aluminum Takes to the road [J]. Advanced Materials and Processes, 1994(1): 42-44.
[3] IRVING B. Welding tailored blanks is hot issue for automakers [J]. Weld, 1995, 74(2): 49-52.
[4] PALLETT R J, LARK R J. The use of tailored blanks in the manufacture of construction components[J]. Journal of Materials Processing Technology, 2001,117(1): 249-254.
[5] ZHAO H, WHITE D R, DEBROY T. Current issues and problems in laser welding of automotive aluminum alloys [J]. International Materials Reviews, 1999, 44(6): 238-266.
[6] KATAYAMA S, MATSUNA A, KOJIMA K. CO2 laser weldability of aluminum alloy(Report1): Effect of welding conditions on melting characteristics [J]. Welding International, 1998, 12(7): 14-19.
[7] KATAYAMA S, MATSUNAWA A, KOJIMA K. CO2 laser weld ability of aluminum alloys (2nd Report): Defect formation conditions and cause [J]. Welding International, 1998, 12(10): 44-59.
[8] VENKAT B S, ALBRIGHT C E, RAMASAMY S, HURLEY J P. CO2 laser beam welding of aluminum 5754-O and 6111-T4 alloys [J]. Welding Journal, 1997, 76(7): 275-282.
[9] RAMASAMY S, ALBRIGHT C E. CO2 and Nd: YAG laser welding of 6111-T4 aluminum alloy for automotive applications [J]. Journal of Laser Applications, 2000, 12(3): 101-115.
[10] ZHAO H, DEBROY T. Weld metal composition change during conduction mode laser welding of aluminum alloy 5182 [J]. Metall Mater Trans B, 2001, B32: 163-172.
[11] Saunders F I, Wagoner R H. Forming of tailor-welded blanks [J]. Metall Mater Trans A, 1996, A27: 2605-2616.
(Edited by LONG Huai-zhong)
Foundation item: Project(3ZS041-A25-031) supported by the Natural Science Foundation of Gansu Province, China; Projects(Z2004-1-62008) supported by the “Chunhui Plan” of the Ministry of Education of China
Corresponding author: YU Shu-rong; Tel: +86-931-2976097; E-mail: yushur@lut.cn