文章编号:1004-0609(2008)S1-0386-07
太阳能级多晶硅生产技术发展现状及展望
龙桂花,吴 彬,韩 松,丘克强
(中南大学 化学化工学院,长沙 410083)
摘 要:全面介绍了太阳能级多晶硅的生产技术现状及有代表性的新工艺、新技术的研究动态。太阳能级多晶硅生产技术主要包括西门子法、硅烷法和冶金法。冶金法因工艺简单、投资少、能耗低获得广泛的关注,但目前其产品达不到太阳能级硅的质量要求。展望未来,西门子法仍将是生产高纯度多晶硅的主流技术。
关键词:太阳能级多晶硅;西门子法;硅烷;硅
中图分类号:O 613.72 文献标识码:A
Development status and prospect of solar grade silicon production technology
LONG Gui-hua, WU Bin, HAN Song, QIU Ke-qiang
(School of Chemistry and Chemical Engineering, Central South University, Changsha 410083, China)
Abstract: The production status of solar grade silicon and development studies of its new representative processes and technologies were comprehensively introduced. The production technologies of solar grade silicon mostly include Simens process, silane process and metallurgical process. For simple process, lower investment and lower energy consumption, metallurgical process is given extensive attention, but the products cannot meet the quality requirements of solar grade silicon at present. Simens process will still be the mainstream process in the production field of the high purity silicon in the future.
Key words: solar grade silicon; Siemens process; silane; silicon
面对当前世界性传统能源枯竭和石油价格持续攀升的形势,太阳能作为可再生的洁净能源受到了世界各国的高度重视。世界光伏工业在20世纪末最后10年的平均增长率为20%,从1991年的55 MW增长到2000年的287 MW。而进入21世纪后,全球光伏组件的年均增长率更是高达30%以上,2003年全球的产量达到了742 MW,2004年全球光伏电池的生产首次突破1 000 MW。预计到2010年时,全球太阳能光伏装机容量累计量将增加到18 000 MW以上,这势必会给太阳能电池产业带来高速的发展。但是,当前高纯多晶硅的严重脱销和价格暴涨,制约了光伏发电产业的发展。此外,由于硅材料的成本约占太阳能电池总成本的50%,所以硅材料价格高也成为阻碍光伏产业发展的重要因素之一。在不影响效率的条件下,降低硅材料的成本是降低硅太阳能电池成本的关键。因此,为了满足光伏产业对于多晶硅原材料的强大需求,同时摆脱太阳能级硅材料对电子级硅材料的依附,世界各大多晶硅厂商及研究单位积极展开低成本生产太阳能级多晶硅的工艺技术研究。目前,大力发展针对太阳能用高纯多晶硅的低成本生产技术已成为了国际竞争的新领域。本文作者就目前太阳能级多晶硅生产技术现状及有代表性的新工艺、新技术的研究进展进行全面介绍。
1 西门子法及其新发展
目前,太阳能用多晶硅的主要来源是西门子法生产半导体工业硅材料中的边角料,即直拉单晶硅头尾料、电子级多晶硅的等外品。西门子法,即采用H2还原SiHCl3生产高纯多晶硅的方法,由德国Siemens公司发明并于1954年申请了专利,1965年左右实现了工业化,从而实现了超纯硅制备道路上的第二次大变革。
经过几十年的应用和发展,西门子法不断完善,先后出现了第一代、第二代和第三代技术,而第三代西门子多晶硅生产工艺就是目前常说的“改良西门子法”[1],它在第二代的基础上增加了还原尾气干法回收系统、SiCl4氢化工艺,实现了完全闭环生产,是西门子法生产高纯多晶硅技术的最新版本。
改良西门子法主要包括五个环节:SiHCl3的合成、精馏提纯SiHCl3、SiHCl3的氢还原、尾气回收和SiCl4的氢化分离,具体流程如图1所示。SiHCl3的合成在沸腾炉中进行,生成的SiHCl3含量在85%左右,同时产物中还伴随有SiCl4及杂质氯化物,利用各种氯化物挥发性的差别,精馏制得高纯SiHCl3。最后将高纯SiHCl3和高纯H2按一定的比例导入钟罩型还原炉内(见图2),在1 100 ℃的硅芯发热体上还原沉积得硅多晶棒。国外设备规模已达到5~6 t/炉[2]。

图1 改良西门子工艺流程图
Fig.1 Flow chart of Siemens process
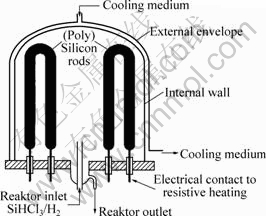
图2 钟罩型还原炉示意图[3]
Fig.2 Schematic diagram of bell jar reactor
改良西门子法是目前占绝对优势的主要方法, 产量占当今世界总量的70%~80%,其工艺成熟,经验丰富,产品质量高,国外用该法生产的多晶硅纯度为9~11N,直接电耗可降到60~70 kW?h/kg,但其具有工艺流程长、投资大、三氯氢硅还原率低、生产成本高、技术操作难度大等缺点。
半导体市场疲软时期,西方国家利用闲置的西门子法设备,通过“放宽”控制条件,以降低太阳能级多晶硅生产电耗和提高生产率。显然,上述对策对于降低硅生产成本是很有限的。1999年以后,世界经济复苏,半导体工业进入新一轮高速增长时期,闲置的西门子法设备“归队”,上述对策从而失去意义。为了更有效地降低生产成本,世界各大多晶硅厂商都在现有成熟固定床技术的基础上,用流态化技术改造传统的西门子法反应器。Wacker公司研究的流化床反应器如图3所示,其反应效率为65%,电耗为40 kW?h/kg,该公司已有2台50 t/a的炉子,并计划在德国Burghausen建立650 t/a的工厂,预计2008年底完工[4]。流化床反应器因大大增加了反应面积,使得反应速率明显提高,从而降低硅生产能耗和成本。该法的产品纯度比钟罩型还原炉技术的低,但完全可以满足太阳能级硅质量要求。
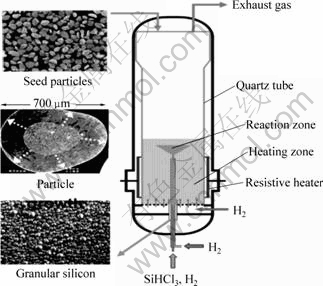
图3 流化床反应器内SiHCl3氢还原示意图[5]
Fig.3 Hydrogen reduction of SiHCl3 in Fludized Bed reactor
西门子法另一个值得重视的派生技术是日本Tokuyama公司研发的气液沉积法(VLD法),其主要工艺如图4所示:将石墨管升温至1 500 ℃,SiHCl3和H2气体从石墨管上部注入,并在管内壁1 500 ℃处反应生成液体硅和SiCl4,其中液体Si滴入反应器底部,固化生成粒状多晶硅。
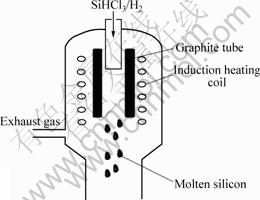
图4 VLD法生产多晶硅示意图[6]
Fig.4 Schematic diagram of polycrystalline silicon production by VLD
VLD法采用石墨管状炉将反应温度提高到Si熔点以上,比固定床工艺温度提高了约400℃,不仅有效地提高了SiHCl3的还原率,也大大提高了Si的沉积速率(约为经典西门子工艺的10倍[4]);其次,硅以液体形式出现,既避免了流化床技术中出现的粉尘问题,又可实现连续操作。由此可见,VLD法是一种具有重要优点的新技术。但是该法所得产品中碳和重金属的含量较高,碳原子含量约为0.01%、重金属原子含量约为0.000 01%,用该产品制备的太阳能电池的效率为15.6%[4]。VLD法已建成年产200 t的中试线[7]。
2 硅烷热分解法及其新发展
硅烷热分解法,即利用甲硅烷(SiH4)的热分解反应制取高纯硅,因硅烷制备方法不同有日本Komatsu发明的硅化镁法、美国Union Carbide发明的歧化法、美国MEMC采用的NaAlH4与SiF4反应方法。
硅化镁法是用Mg2Si与NH4Cl 在液氨中反应生成硅烷。该法由于原料消耗量大,成本高,危险性大,而没有推广,目前只有日本Komatsu使用此法。
现代硅烷的制备采用歧化法,即以冶金级硅与SiCl4为原料合成硅烷,首先用SiCl4、Si 和H2反应生成SiHCl3,然后SiHCl3歧化反应生成SiH2Cl2,最后由SiH2Cl2进行催化歧化反应生成SiH4,即:
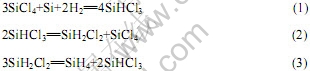
由于上述每一步的转换效率都比较低,所以物料需要多次循环,整个过程要反复加热和冷却,使得能耗比较高。制得的硅烷经精馏提纯后,通入类似西门子法固定床反应器,在800 ℃下进行热分解,反应如下:

硅烷热分解法与西门子法相比,其优点主要在于硅烷较易提纯,含硅量较高(87.5%),分解速度快,分解率高(达99%),分解温度较低,生成的多晶硅的能耗仅为40 kW?h/kg,且产品纯度高。但是缺点也突出:硅烷不但制造成本较高,而且易燃、易爆、安全性差,国外曾发生过硅烷工厂强烈爆炸的事故。因此,工业生产中,硅烷热分解法的应用不及西门子法。
与西门子方法相似,为了降低生产成本,流化床技术也被引入硅烷的热分解过程,如图5所示。流化床分解炉与固定床分解炉在操作上的最大差异在于其无须以大量冷却水降温,因此能耗可大幅度降低;其次,流化床分解炉可大大提高SiH4的分解速率和Si的沉积速率。但是所得产品的纯度不及固定床分解炉技术,但完全可以满足太阳能级硅质量要求,另外硅烷的安全性问题依然存在。
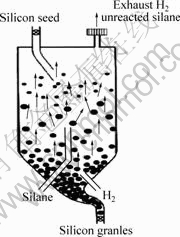
图5 流化床示意图[5]
Fig.5 Schematic diagram of Fludized bed
美国MEMC公司采用流化床技术实现了批量生产,其以NaAlH4与SiF4为原料制备硅烷,反应式如下:

硅烷经纯化后在流化床式分解炉中进行分解,反应温度为730 ℃左右,制得尺寸为1 000 μm的粒状多晶硅。该法能耗低,粒状多晶硅生产分解电耗为12 kW?h/kg左右,约为改良西门子法的1/10,且一次转化率高达98%[8],但是产物中存在大量微米尺度内的粉尘,且粒状多晶硅表面积大,易被污染,产品含氢量高,须进行脱氢处理。目前,MEMC公司Pasadena工厂产能2 700 t[8],其产量占硅生产总量的5.7%[4]。
REC公司则是在歧化法中引入流化床式分解炉,先在沸腾床内生成SiHCl3,后通过歧化反应制得硅烷,硅烷经纯化后在流化床分解炉内进行热分解生成粒状多晶硅。REC已于2006年8月采用流化床分解炉筹建第三座多晶硅生产工厂,厂址位于美国华盛顿州Moses Lake市,投资6亿美元,预定于2008年底完工,产能6 500 t[9]。
3 冶金法制备太阳能级硅
冶金法即是采用冶金行业中常用的冶炼或精炼方法制备太阳能级硅,可分为冶金级硅精炼法、硅石碳热还原法和熔盐电解法。
3.1 冶金级硅精炼工艺
冶金级硅精炼是利用Si与杂质元素物理与化学性质的差别,联合多种方法,如酸浸、真空精炼、等离子加热技术、定向凝固等制备太阳能级硅,并可分为全火法与火法和湿法联合两类工艺。
全火法工艺以日本JFE公司为代表,其工艺过程如图6所示。1) 真空下利用电子束将冶金级硅加热熔融除P,然后进行定向凝固;2) 在非真空的Ar气氛围下,采用等离子枪加热,并通入氧、水蒸气除B和C,然后进行第二次定向凝固。所得产品中P、B及金属杂质的含量均低于0.1 mg/L[9],符合太阳能级多晶硅的要求。
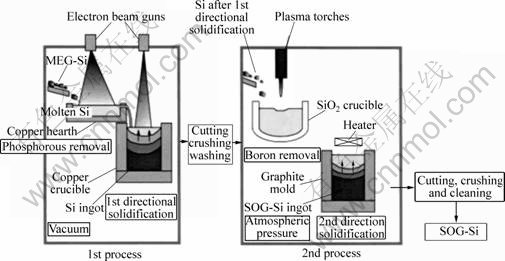
图6 JFE工艺流程示意图[10]
Fig.6 Flow chart of JFE process
JFE工艺流程简单、污染少,过程中没有副产品生成。但因使用电子束、等离子焊枪等操作,生产成本较高。JFE公司已进行建厂,2007年年底投产,产能400 t[9]。
火湿联合工艺则以挪威Elkem公司火湿联合工艺为代表。Elkem是全球冶金级硅的主要生产商和供应商,因此其开发的硅精炼工艺特别强调与冶金级硅生产过程接轨:电炉炼出的冶金级硅直接进行火法精炼,即造渣精炼和定向凝固,如图7(a)所示;然后将多晶硅锭破碎后进行湿法酸浸除杂,如图7(b)所示。
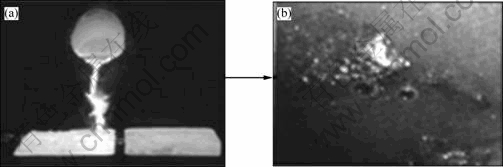
图7 Elkem火湿联合工艺示意图[11]
Fig.7 Schematic diagram of Elkem pyro-hydrometallurgy combination process: (a) Pyrometallurgical refining; (b) Hydrometallurgical refining
Elkem已于2005年完成中试工作,生产的硅按25%~100%与电子级硅混合使用所制备的太阳能电池转换效率为15%~16.5%[12]。该工艺流程简单、生产成本较低,能耗仅为西门子法的20%~25%[13],但是产品必须与电子级硅掺配才能用于制备太阳能电池。
3.2 硅石碳热还原法
硅石碳热还原法是冶金级硅的主要生产方法,其基本原理如下:SiO2+C=Si+CO2。
20世纪70年代起,德国Simens、挪威Elkem、Sintef等公司分别改良此法,研究采用高纯C还原高纯SiO2制备太阳能级硅。
Sintef公司研发的SOLSILC工艺如下:首先在等离子体回转炉中用碳还原SiO2得SiC,然后将SiC注入电弧炉中与SiO2反应制得液体硅(见图8)。经分析检测表明,液体硅除C外其他杂质含量较低。因此,其后的精炼主要是除C,即先控温冷却,使C与Si生成SiC沉降而与硅分离,再通入Ar/H2O气体使余C以CO气体形式挥发除去,最后进行定向结晶。所得硅中C的质量含量小于0.000 5%[14]。Sintef公司于2005年完成了中试工作,规模为20 kg/h[15]。
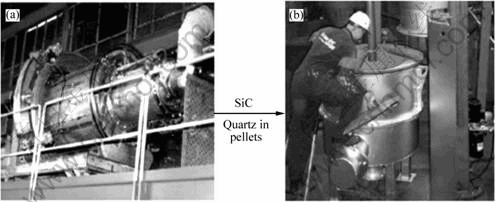
图8 SOLSILC工艺生产过程图[15]
Fig.8 Schematic diagram of SOLSILC process: (a) SiC production in plasma-furnace; (b) Si production in arc furnace
改良的硅石碳热还原法,由于采用高纯原料,可制得较高纯度的硅产品,但若想直接生产太阳能级多晶硅还比较困难,须结合其他提纯方法。Siemens和Elkem的工艺与Sintef类似,但是所得产品中B、P、C的含量较高。
3.3 电解法
熔盐电解法制取多晶硅已有150多年的历史。自20世纪80年代起,一些研究者开始研究采用此法制取太阳能级硅,研究内容按原料不同可分为硅石熔盐电解和粗硅的电解精炼。
3.3.1 硅石熔盐电解
20世纪90年代,Jan Relder Stubergh研究了在冰晶石熔体中电解硅酸盐制取高纯硅:采用碳阳极,电解温度为1 000 ℃,电流密度为0.5 A/cm2,阴极上沉积得Si,阳极上析出CO2。所得阴极产物先经酸浸进行富集提纯,后再熔融、铸锭,制得硅的纯度为99.999 7%,其中B、P含量分别为0.6 mg/L和1.0 mg/L[16]。冰晶石熔体能很好地溶解SiO2,且价格低廉,但是其腐蚀性强,高温时更严重,所以对电极材料的要求比较高。事实上只有碳电极能适用于此环境,但碳电极会污染电解质,污染产品,引入B、P杂质,致使所制备的硅纯度不高。
除冰晶石熔体外,其他电解质体系中电解SiO2的情况亦有研究报道,如BaO-BaF2熔盐体系[17]、CaCl2-CaO-SiO2体系[18]等。
2007年,日本京都大学报道了采用CaCl2熔盐电解太阳能级SiO2的情况,如图9所示。以石墨为阳极,采用特制阴极,将太阳能级SiO2置于两单晶硅板中,并用钼丝绑紧,电解时,钼丝不浸入电解质中,以避免污染产品,电解温度为1 123 K。
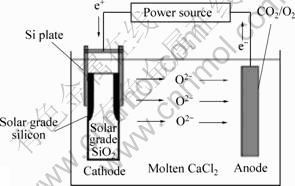
图9 CaCl2熔盐中直接电解固体SiO2制备太阳能级Si示意图[19]
Fig.9 Schematic diagram of solar grade silicon production process by direct electrolytic reduction of solid SiO2 in molten CaCl2
电解后,将阴极置于1 772 K下进行真空处理,利用熔点差别,使沉积的Si与未电解的SiO2分离,所得Si的纯度约为99.80%[19],其中B、P的浓度较低,须结合其他方法除杂,如定向凝固。
3.3.2 硅的电解精炼
由于三层电解法制备高纯铝的成功,因此采用此法制备高纯硅也让人有所期待。该法的提纯原理是利用各元素在电解液中电极电位的差别,即电解过程中比Si更正电性的元素滞留在阳极合金中,而比Si负电性的元素因不能在阴极析出而进入电解液中。Sintef和NTNU对此开展了研究,所用的实验装置如图10所示。为了改善Si的导电性,下层采用密度较大的Si-Cu阳极合金,中层为由CaO-MgO-SiO2组成的精炼电解液,上层为所制备的高纯硅,电解温度为1 500 ℃。每层熔体之间都维持一定的密度差以保持它们在电解过程中处于稳定的状态。该法得到的Si有电解质夹杂等缺点,且由于电解质、电解槽壁等的污染,阴极硅很难符合太阳能级硅的质量要求,目前,实验室试验只能制得4N硅。
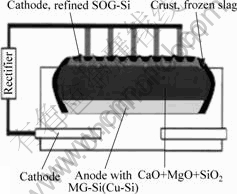
图10 1 500 ℃CaO-MgO-SiO2体系中Si电解精炼示意图[20]
Fig.10 Schematic diagram of Si electrorefining in molten CaO-MgO-SiO2 at 1 500 ℃
4 展望
能源紧缺和环境污染在我国都是极为严峻的问题,我国经济可持续发展急需开发可再生的清洁能源。因此,多晶硅太阳能电池可有所作为,甚至大有作为。在国内,目前多晶硅年需求3 000多t,今后还会逐年大量增加,到2010年估计需多晶硅14 000 t/a。但是目前国内年产能只有约300 t,2006年实际产量仅 180 t左右,光伏用硅几乎全部依赖进口。可见,由于我国至今没有形成规模的多晶硅材料制备产业,我国光伏工业面临的硅材料紧缺形势比西方国家更为严重。因此,无论是从国家的战略需要,还是从企业投资回报需求看,开展低成本多晶硅生产技术的研究具有重要的战略意义。但是如何发展中国多晶硅的制备技术,不但要决定于未来市场需求,也要考虑技术的可行性。
从国际的技术研究现状来看,冶金法技术虽然具有工艺简单、投资少和能耗低的吸引力,但是这一“远水”显然还救不了多晶硅需求量每年增长速率为35%以上的“近火”。尽管太阳电池用的硅对杂质含量的要求比半导体硅低,但是其纯度至少仍要达到7N以 上[4, 21]——即使是常见的有色金属要提纯到这样的纯度,也是一件很难的事情,何况对于熔点高、含杂质多并且含有用冶金法难以脱除的B和P的硅!国外对冶金法研究至少已有25年时间,但是至今还不能真正为光伏产业提供质量合格的硅材料,看来并非偶 然。因此,本文作者认为:试图用冶金精炼方法生产出满足太阳能电池质量要求的多晶硅不是近期可望达到的。
回顾高纯硅的生产技术的发展历史可知:50多年前,由于采用各种方法均无法从硅中彻底除掉硼和磷,才开发了西门子法技术;展望未来,可以肯定:西门子法作为生产高纯度多晶硅主流技术的战略地位在今后很长时期内是不会动摇的。因此,以西门子法等方法为背景的流化床技术和VLD法应该受到国人更多的关注。
REFERENCES
[1] 梁骏吾. 电子级多晶硅的生产工艺[J]. 中国工程科学, 2000, 2(12): 34-39.
LIANG Jun-wu. The production technology of electronic grade polycrystalline silicon[J]. Engineering Science, 2000, 2(12): 34-39.
[2] 蒋荣华, 肖顺珍. 国内外多晶硅发展现状[J]. 半导体技术, 2001, 26(11): 7-9.
JIANG Rong-hua, XIAO Shun-zhen. Development and trend of international and internal polycrystal Si material[J]. Semiconductor Technology, 2001, 26(11): 7-9.
[3] CECCAROLI B. Manufacturing of solar grade silicon[C]// Europv 2003. Granada, 2003.
[4] 梁骏吾. 光伏产业面临多晶硅瓶颈及对策[J]. 科技导报, 2006, 24(6): 5-7.
LIANG Jun-wu. Polycrystalline silicon bottleneck confronting photovoltaic industry and the countermeasures[J]. Science and Technology Review, 2006, 24(6): 5-7.
[5] HESSF K, SCHINDLBECK E. Feedstock for the photovoltaic industry[C]//The 2nd Solar Silicon Conference. Munich, 2005.
[6] HIROYUKI O. Tokuyama VLD at a glance[C]//The 3rd Solar Silicon Conference. Munich, 2006.
[7] 郭 瑾, 李积和. 国内外多晶硅工业现状[J]. 上海有色金属, 2007, 28(1): 20-25.
GUO Jing, LI Ji-he. Present status of polysilicon industries at home and abroad[J]. Shanghai Nonferrous Metals, 2007, 28(1): 20-25.
[8] 汤传斌. 粒状多晶硅生产概况[J]. 有色冶炼, 2001(3): 29-31.
TANG Chuan-bin. The production status of granular silicon[J]. Non-ferrous Smelting, 2001(3): 29-31.
[9] 黄齐刚. 台湾多晶硅评述[J]. 石油通讯, 2007(669): 26-29.
HUANG Ji-gang. The comment of polycrystalline silicon in Taiwan[J]. Petroleum Communication, 2007(669): 26-29.
[10] YUGE N, ABE M, HANAZAWA K, BABA H, NAKAMURA N, KATO Y, SAKAGUCHI Y, HIWASA S, ARATANI F. Purification of metallurgical-grade silicon up to solar grade[J]. Progress in Photovoltaics: Research and Applications, 2001(9): 203-209.
[11] DETHLOFF C. Elkem solar AS[C]//The 2nd Solar Silicon Conference. Munich, 2005.
[12] PETER K, ENEBAKK E, FRIESTAD K, TRONSTAD R, DETHLOFF C. Investigation of multicrystalline silicon solar cells from solar grade silicon feedstock[C]//EUPVSEC-20. Barcelona, 2005.
[13] GEERLIGS B, WYERS P, SANTEN S, WIERSMA B. New feedstock materials[EB/OL]. http://www.ecn.nl/docs/library/ report/2005/rx05022.pdf, 2005.
[14] GEERLIGS L J, WYERS G P, JENSEN R, RAANESS O, WAEMES A N, SANTEN S, REININK A, WIERSMA B. Solar grade silicon by a direct route based on carbothermic reduction of silica: requirements and production technology[EB/OL]. http:// www.ecn.nl/docs/library/report/2002/rx02042.pdf. 2002-08.
[15] WAERMES A N, OVRELID E J, RAANESS O S, PAUL B, GEERLIGS L J, WYERS G P, SANTEN S, WIERSMA B. The SOLSILC route to low-cost solar grade silicon[C]//The 2nd Solar Silicon Conference. Munich, 2005.
[16] STUBERGH J R. Process for preparing silicon and optionally aluminum and silumin (aluminum-silicon alloy). US 20040108218[P]. 2004-06-10.
[17] ELWELL D. Electrolytic production of silicon[J]. Applied Electrochemistry, 1988, 18(1): 15-22.
[18] OLSEN E. Electrolyte and method for manufacturing and/or refining of silicon[EB/OL]. http://www.freepatentsonline. com/20040238372.html, 2004-12-02.
[19] YASUDA K, NOHIRA T, HAGIWARA R, OGATA Y H. Direct electrolytic reduction of solid SiO2 in molten CaCl2 for the production of solar grade silicon[J]. Electrochimica Acta, 2007, 53(1): 106-110.
[20] OLSEN E, OSEN K S. Solar grade silicon through electrolysis[C]//The 3rd Solar Silicon conference. Munich, 2006.
[21] MORITA K, MIKI T. Thermodynamics of solar-grade-silicon refining[J]. Intermetallics, 2003, 11(11/12): 1111-1117.
基金项目:广东省教育部产学研结合专项资金资助项目(2006D90404001)
通讯作者:丘克强,教授,博士;电话:0731-8877364;E-mail: qiuwhs@sohu.com
(编辑 杨幼平)