
Leaching kinetics of bastnaesite concentrate in HCl solution
BIAN Xue, YIN Shao-hua, LUO Yao, WU Wen-yuan
School of Materials and Metallurgy, Northeastern University, Shenyang 110004, China
Received 30 October 2010; accepted 27 May 2011
Abstract: The leaching kinetics of bastnaesite concentrate in HCl solution was investigated with respect to the effects of HCl concentration by changing HCl concentration, leaching temperature, liquid to solid ratio, and particle size. A particle size of 25 μm was required to leach 89.6% RE2(CO3)3 and 1.5%REF3 at 90 °C for 90 min, when HCl concentration was 6 mol/L and liquid to solid ratio was 15:1. The leaching kinetics of bastnaesite concentrate is represented by shrinking core model with diffusion through a porous product layer. The activation energies for the dissolution reaction of RE2(CO3)3 and REF3 were calculated to be 59.39 kJ/mol and 66.13 kJ/mol respectively.
Key words: bastnaesite; RE2(CO3)3; REF3; leaching kinetics
1 Introduction
Bastnaesite is one of the important sources of rare earths which mainly distributes in Mianning, Sichuan, China and Mountain Pass, USA. The bastnaesite concentrate is produced by gravity and magnetic separation or by flotation. The formula of bastnaesite concentrate is REFCO3 [1-3]. Bastnaesite concentrate is calcined, and oxidizing cerium to a higher valency state can selectively separate cerium from the other rare earth oxide by acid leaching. This technology causes low-investment and low-cost. But the fluorine release as gas phase causes the problems of recovery of value elements and pollution [4-5].
Therefore, the green technology of bastnaesite treatment has been investigated by many researchers. The effect of thiourea on sulphuric acid leaching of bastnaesite shows that the leaching medium further improves the dissolution of the rare-earth elements in the roasted bastnaesite due to the reduction of cerium (IV) to cerium (III) by thiourea [6]. But the fluorine release is not resolved in the roasting process of this method. Another new method is non-thermal process for extracting rare earths from bastnaesite by means of mechanochemical treatment [7]. Milling of the mixture of bastnaesite and NaOH powders forms mechanochemically RE(OH)3 and Na compounds, and 90% rare earths are extracted by acid leaching. Roasting bastnaesite with RE2(CO3)3 at 400-1 000 °C was investigated by LAO et al [8], and the roasted product was leached by acid solution. In this process, Ce was separated from other rare earths elements, and the fluorine existed in the leaching slag.
2/3 of rare earths element exists as rare earth carbonate in bastnaesite. The unroasted bastnaesite concentrate leaching by industrial hydrochloric acid for dissolving RE2(CO3)3 in concentrate was investigated [9]. The leached slag of REF3 is decomposed by NaOH, and then rare earths in slag are extracted. The protection of equipments and environment is difficult in acidity of 9.8 mol/L, therefore this method is not applicable.
The advantage of unroasted bastnaesite leaching by acid is unwaste of fluorin and low-cost of energy. If the leaching ratio of RE2(CO3)3 is increased in concentrate at low acidity, and the REF3 will have a high-purity in leaching slag, and this slag can be used in rare earth electrolysis or Si-Fe alloy metallurgy directly [10-11]. In the present work, the leaching kinetics of bastnaesite concentrate in HCl solution and the effect of the parameters on leaching rate in HCl solution are investigated.
2 Experimental
2.1 Materials
Representative samples of bastnaesite concentrate taken from the Mianning, Sichuan deposit, were crushed to 6 mm. The chemical composition is given in Table 1.
Table 1 Chemical composition of bastnaesite (mass fraction, %)

2.2 Methods
The leaching experiments were performed in a 500 mL-glass reactor. A mechanical stirrer was used and a thermostat was employed to keep the reaction medium at constant temperature. In the leaching process, HCl solution was put into reactor. After the desired reaction temperature was reached, a specific amount of the sample was added to the solution and the stirring started. After a certain period of time, the solution was filtered. The particle sizes of bastnaesite concentrate prepared by ball milling were 25, 50, 99 and 220 μm, respectively.
2.3 Analysis
The amounts of rare earths and F in the leaching filtrate were analyzed by ICP spectrometer. The phase compositions were determined by the D/max 2400 diffraction instrument with the Cu Kα radiation.
The leaching ratio of REF3 was calculated by F concentration of leached slag, and according to this result, the leaching ratio of RE2(CO3)3 was calculated by RE of leached filtrate and F concentration of leaching slag.
3 Results and discussion
3.1 Reactions of leaching process
Figure 1 shows the XRD patterns of bastnaesite concentrate and leaching slag. The peaks of bastnaesite concentrate disappear, and the peaks of CeF3 appear for the leached slag. Therefore, the leaching obeys the following reactions:
RE2(CO3)3+6HCl=2RECl3+3H2O+3CO2 (1)
REF3+3HCl=RECl3+3HF (2)
3.2 Kinetics of leaching process
The leaching process of bastnaesite concentrate could be explained by a shrinking core model [12]. If the reaction rate is controlled by diffusion through a product layer, the kinetics equation is as follows [13]:
(3)
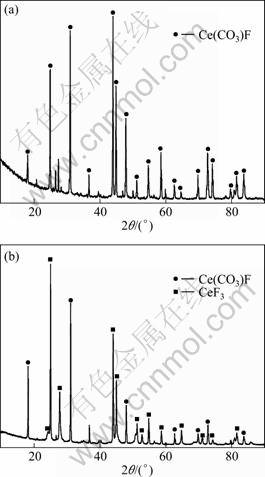
Fig. 1 XRD patterns of bastnaesite concentrate (a) and leached slag (b)
If the reaction is controlled by a surface reaction, the kinetics equation is [14]
(4)
where x is the fraction reacted; kc is the kinetic constant; MB is the molecular mass of the solid; cA is the concentration of the dissolved lixiviant A in the bulk of the solution; a is the stoichiometric coefficient of the coefficient of the reagent in the leaching reaction; r0 is the initial radius of the solid particle; t is the reaction time; D is the diffusion coefficient in the porous product layer; ρB is the density of the solid; kd and kr are the rate constants, respectively.
Eq. (3) or Eq. (4) reveals that if the diffusion through the product layer controls or the surface reaction controls the leaching rate, there must be a linear relationship between the left side of equation and time. The slope of the line is the apparent rate constant kd or kr, which is directly proportional to 1/r02 or 1/r0.
The effects of temperature on the leaching ratio of RE2(CO3)3 and REF3 are given in Fig. 2 and Fig. 3 respectively, under conditions of HCl concentration of 6 mol/L, liquid/solid ratio of 15:1, stirring speed of 300 r/min, and particle size of 25 μm. The results show that the leaching ratio of RE2(CO3)3 and REF3 are 89.6% and 1.5% respectively, after leaching for 90 min.
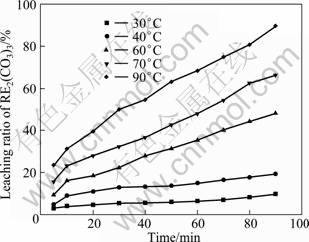
Fig. 2 Relationship between leaching ratio of RE2(CO3)3 and time
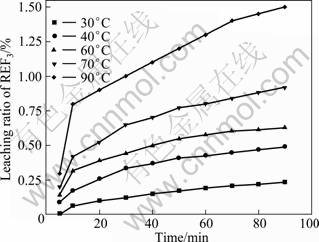
Fig. 3 Relationship between leaching ratio of REF3 and time
The apparent rate constants (kr, kd) are obtained for both equations and the correlation coefficients are calculated from the plots at each temperature, as shown in Fig. 2 and Fig. 3. The results obtained by the application of Eq. (3) to the values given in Fig. 2 and Fig. 3 are shown in Fig. 4 and Fig. 5.
Using the apparent rate constants (kd) obtained by Eq. (3), the Arrhenius plot is obtained (Fig. 6). The activation energy is calculated to be 59.39 kJ/mol and 66.13 kJ/mol, respectively. This value clearly confirms that this process is controlled by diffusion through a product layer [15]. The activation energy of RE2(CO3)3 leaching process is lower than that of REF3 leaching process, showing that RE2(CO3)3 of bastnaesite concentrate is leached easily.
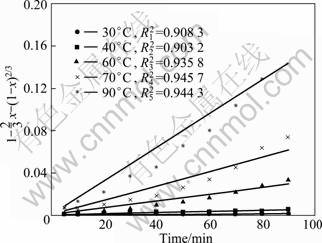
Fig. 4 Leaching kinetic curves of RE2(CO3)3
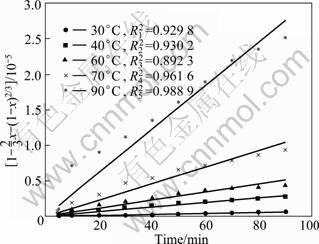
Fig. 5 Leaching kinetic curves of REF3
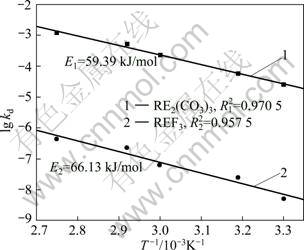
Fig. 6 Relationship between lg k and 1/T in leaching process
3.3 Effect of parameters on leaching rate
3.3.1 Effect of temperature on leaching rate
The effect of temperature on leaching rate is given in Fig. 7. The results show that the leaching rate of RE2(CO3)3 is higher than that of REF3. The leaching rate of RE2(CO3)3 and REF3 increases by 10.9 times and 5.4 times respectively when leaching temperature increases from 30 °C to 90 °C.
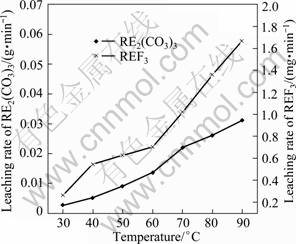
Fig. 7 Effect of temperature on leaching rate (HCl of 6 mol/L, liquid to solid ratio of 15:1, stirring speed of 300 r/min, particle size of 25 μm, time of 90 min)
3.3.2 Effect of HCl concentration on leaching rate
As shown in Fig. 8, the leaching rate of RE2(CO3)3 increases with increasing the HCl concentration. When HCl concentration increases to 6 mol/L, the leaching rate of RE2(CO3)3 increases by 2.4 times. But the leaching rate of REF3 does not obviously change.
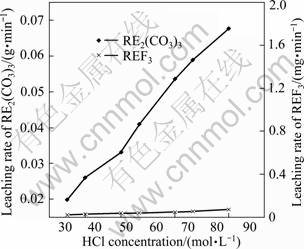
Fig. 8 Effect of HCl concentration on leaching rate (temperature of 90 °C, liquid to solid ratio of 15:1, stirring speed of 300 r/min, particle size of 25 μm, time of 90 min
3.3.3 Effect of liquid to solid ratio on leaching rate
The effect of liquid to solid ratio on leaching rate is shown in Fig. 9. The results show that increasing liquid to solid ratio can increase leaching rates of RE2(CO3)3 and REF3, and the leaching rate of RE2(CO3)3 is higher than that of REF3. When the liquid to solid ratio increases to 15:1, the leaching rate of RE2(CO3)3 increases slowly. Therefore, the liquid to solid ratio is selected as 15:1.

Fig. 9 Effect of liquid to solid ratio on leaching rate (HCl of 6 mol/L, temperature of 90 °C, stirring speed of 300 r/min, particle size of 25 μm, time of 90 min)
3.3.4 Effect of particle size on leaching rate
The effect of particle size on leaching rate was examined for four different size fractions (25, 50, 99, 220 μm), and the results are shown in Fig.10. From Fig. 10, it can be seen that leaching rate of RE2(CO3)3 increases with decreasing particle size. But the particle size has weak influence on leaching rate of REF3.
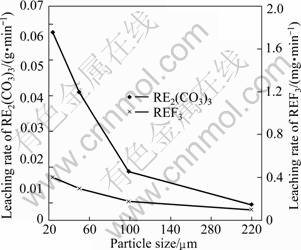
Fig. 10 Effect of particle size on leaching rate (HCl of 6 mol/L, temperature of 90 °C, liquid to solid ratio of 15:1, stirring speed of 300 r/min, time of 90 min)
3.4 Character of leaching process
The leached slag was obtained under the following conditions: stirring speed 300 r/min, 6 mol/L HCl, 90 °C and 90 min. SEM and EDS analyses of the slag are presented in Figs. 11. The EDS analysis shows that RE2(CO3)3 is dissolved, and the morphology implies that the bastnaesite concentrate leaching proceeds initially by the diffusion of lixiviant through the reaction product.

Fig. 11 SEM image (a) and EDS analysis (b) of leached slag (HCl of 6 mol/L, temperature of 90 °C, liquid to solid ratio of 15:1, stirring speed of 300 r/min, particle size of 25 μm, time of 90 min)
4 Conclusions
1) Leaching of the bastnaesite concentrate by hydrochloric acid at atmospheric pressure shows that 89.6% RE2(CO3)3 and 1.5% REF3 can be leached under the experimental conditions of 6 mol/L HCl, reaction temperature 90 °C, leaching time 5 min, particle size 25 μm, stirring speed 300 r/min and liquid to solid ratio 15:1.
2) The activation energies for RE2(CO3)3 and REF3 leaching from bastnaesite concentrate were determined to be 59.39 kJ/mol and 66.13 kJ/mol, respectively. The dissolution kinetics was found to fit well diffusion through a product layer as the rate controlling step.
3) The morphology of the leaching slag implies that the bastnaesite concentrate leaching proceeds initially by the diffusion of lixiviant through the reaction product.
References
[1] ANDRESEN L. Occurrence and processing of rare earth mineral [J]. Natural Resources and Development, 1987, 25: 7-19.
[2] PRADIP D, FUERSTENAU W. The role of organic and inorganic reagents in the flotation separation of the rare earth ores [J]. International Journal of Mineral Processing, 1991, 32: 1-22.
[3] KANAZAWA Y, KAMITANI M. Rare earth minerals and resources in the world [J]. Journal of Alloys and Compounds, 2006, 408-412: 1339-1343.
[4] ZHANG Guo-cheng, HUANG Xiao-wei. Comment of bastnaesite smelting technology [J]. Rare Metals, 1997, 21(3): 193-199. (in Chinese)
[5] HUANG Xiao-wei, LI Hong-wei, WANG Cai-feng, WANG Guo-zhen, XUE Xiang-xin, ZHANG Guo-cheng. Development status and research progress in rare earth industry in China [J]. Chinese Journal of Rare Metals, 2007, 31(3): 279-288. (in Chinese)
[6] YORUKOGLU A, OBUT A, GIRGIN I. Effect of thiourea on sulphuric acid leaching of bastnaesite [J]. Hydrometallurgy, 2003, 68: 195-202.
[7] ZHANG Q W, SAITO F. Non-thermal process for extracting rare earths from bastnaesite by means of mechanochemical treatment [J]. Hydrometallurgy, 1998, 47: 231-241.
[8] LIAO Chun-sheng, ZHANG Bo, JIA Jiang-tao. A decomposition method of bastneasite: Chinese patent, CN 101186977A [P]. 2008. (in Chinese)
[9] KRUESI P R. Production of rare earth chloride from bastnasite [J]. Journal of Metals, 1965, 17(8): 847-849.
[10] LIU Ye-xiang. Current status and future proposals of fundamental research in nonferrous metallurgy [J]. The Chinese Journal of Nonferrous Metals, 2004, 15(S1): 21-24.(in Chinese)
[11] XU Guang-xian. Rare earths [M]. 2nd ed. Beijing: Metalllurgical Industry Press, 1995: 314-318. (in Chinese)
[12] LUO Wei, FENG Qi-ming, OU Le-ming, ZHANG Guo-fan, CHEN Yun. Kinetics of saprolitic laterite leaching by sulphuric acid at atmospheric pressure [J]. Minerals Engineering, 2010, 23(6): 458-462.
[13] QIU Ting-sheng, NIE Guang-hua, WANG Jun-feng, CUI Li-feng. Kinetic process of oxidative leaching of chalcopyrite under low oxygen pressure and low temperature [J]. Transactions of Nonferrous Metals Society of China, 2007, 17(2): 418-422.
[14] XIE Ke-qiang, YANG Xian-wan, WANG Ji-kun, YAN Jiang-feng, SHEN Qing-feng. Kinetic study on pressure leaching of high iron sphalerite concentrate [J]. Transactions of Nonferrous Metals Society of China, 2007, 17(1): 187-194.
[15] AYDOGAN S, UCAR G, CANBAZOGLU M. Dissolution kinetics of chalcopyrite in acidic potassium dichromate solution [J]. Hydrometallurgy, 2006, 81: 45-51.
氟碳铈矿盐酸浸出过程的动力学
边 雪, 尹少华, 罗 瑶, 吴文远
东北大学 材料与冶金学院,沈阳 110004
摘 要:考察盐酸浓度、浸出温度、液固比和矿物粒度对浸出速度的影响。结果表明:在盐酸浓度6 mol/L、浸出温度90 °C、液固比15?1、矿物粒度25 μm 的条件下浸出90 min后,氟碳铈矿中稀土碳酸盐的浸出率达到89.6%,而稀土氟化物的浸出率仅为1.5%。氟碳铈矿浸出过程符合产物层扩散模型,稀土碳酸盐和氟化物浸出过程的表观活化能分别为59.39 kJ/mol和66.13 kJ/mol。
关键词:氟碳铈矿;稀土碳酸盐;稀土氟化物;浸出动力学
(Edited by YANG Hua)
Foundation item: Project (50974042) supported by the National Natural Science Foundation of China; Project (20090042120015) supported by Scientific Research Special Foundation of Doctor Subject of Chinese Universities; Project (N090302007) supported by the Fundamental Research Funds for the Central Universities, China
Corresponding author: BIAN Xue; Tel: +86-24-83680527; E-mail: bxbx80_2003@yahoo.com.cn
DOI: 10.1016/S1003-6326(11)61012-1