
Synthesis kinetics of Mg2Sn in Mg-Sn powder mixture using non-isothermal differential scanning calorimetry
WU Yu-feng(吴玉锋)1, 2, DU Wen-bo(杜文博)2, ZUO Tie-yong(左铁镛)1, 2
1. Institute of Recycling Economy, Beijing University of Technology, Beijing 100124, China;
2. College of Materials Science and Engineering, Beijing University of Technology, Beijing 100124, China
Received 7 October 2008; accepted 15 June 2009
Abstract: The non-isothermal heating process of Mg-Sn powder mixture was studied by differential scanning calorimetry(DSC) technique and the synthesis kinetics of Mg2Sn was evaluated by the model-free and model-fitting methods. The activation energy and conversion function of Mg2Sn synthesis reaction are calculated to be 281.7 kJ/mol and g(α)=[-ln(1-α)]1/4, respectively. The reaction mechanism of 2Mg+Sn→Mg2Sn under non-isothermal condition is regarded as “nucleation and growth”. During the non-isothermal heating process, the phase transformation occurred in the Mg-Sn powder mixture was analyzed by XRD and the microstructure evolution of Mg2Sn was observed by optical microscopy, which is in good agreement with the reaction mechanism of 2Mg+Sn→Mg2Sn deduced from the kinetic evaluation.
Key words: magnesium alloy; Mg2Sn; synthesis kinetics; differential scanning calorimetry
1 Introduction
Magnesium alloys are regarded as promising structural materials in the 21st century because of their excellent properties such as low density, high specific strength and superior damping capacity[1-3]. The common Mg-Al alloys, such as AZ91, are unsuitable for using at temperatures above 393 K, because these alloys usually contain Mg+Mg17Al12 eutectic at grain boundaries and Mg17Al12 phase has low melting point ((711±1) K)[4] and poor thermal stability. In order to improve the creep resistance of Mg alloy, some alloying elements such as Si and Sn have been added into Mg matrix to form some thermally stable phases such as Mg2Si and Mg2Sn, which effectively resist the grain boundary sliding and dislocation motion[5-10]. The formation of Mg2Si in Mg alloy is usually realized by two methods. One is precipitating the Mg2Si phase in the solidification process of Mg alloy melt containing Si, and the other is synthesizing the Mg2Si phase by the powder metallurgy method. However, Mg2Sn, as a reinforcing phase in Mg alloy, is almost formed by the solidification method of Mg alloy melt containing Sn while the powder metallurgy method has not been reported. Because the Mg matrix and alloying element added can be refined by the powder metallurgy techniques and the mechanical properties of Mg alloy will be remarkably improved[9, 11], it is necessary to investigate the synthesis of Mg2Sn phase in Mg alloy by the powder metallurgy method systematically. In the present work, the non-isothermal heating process of Mg-Sn powder mixture is recorded by differential scanning calorimetry(DSC) technique and the synthesis kinetics of Mg2Sn is evaluated. The phase transformation occurring in Mg-Sn powder mixture and the microstructure evolution of Mg2Sn in the heating process are investigated.
2 Experimental
Pure magnesium powder (99.9%, 45 μm) and tin powder (99.9%, 45 μm) in mass ratio of 95?5 were mixed, and the typical sample mass was about 10 mg. The DSC measurements were carried out by using NETZSCH 449C equipment, in which Ar at 25 mL/min flow rate was used as analysis chamber gas. In non-isothermal heating process, the sample was heated from 373 K to 903 K at heating rates of 2.5, 5, 10 and 15 K/min, respectively. The exothermal curves as a function of temperature for the non-isothermal reaction were recorded. The powder mixture was pressed uniaxially in a hardened steel die with a pressure of 20 MPa to form a compact with diameter and thickness of 12 and 2 mm, respectively. According to the DSC curve at heating rate of 10 K/min, four compacts were heated to 798, 813, 828 and 843 K in Ar atmosphere and quenched, respectively. In order to clarify the phase transformation occurring in the Mg-Sn powder mixture and the microstructure evolution of Mg2Sn during the heating process, X-ray diffractometry(XRD) was applied to the samples quenched at 798 K and 828 K, and all samples were observed by optical microscopy.
3 Results and discussion
3.1 DSC measurements of Mg2Sn synthesis
Fig.1 shows the DSC curves for the non-isothermal synthesis of Mg2Sn at the heating rates of 2.5, 5, 10 and 15 K/min. Each DSC curve contains an exothermal peak and an endothermal peak in the temperature range of 720-870 K. The exothermal peak at about 803 K indicates the synthesis reaction of Mg2Sn. The onset temperatures of the synthesis reaction of Mg2Sn decrease with decrease in heating rate. Generally, the reactants in a solid-state reaction need to be activated during inoculation period. Under a lower heating rate, it is longer for the reactants to be inoculated. Therefore, the onset temperature of reaction 2Mg+Sn→Mg2Sn has the lowest value (771.5 K) at the lowest heating rate (2.5 K/min). The endothermal peak indicates the eutectic reaction of Mg(s)+Mg2Sn(s)→Liquid according to the Mg-Sn phase diagram[12]. This implies that if the powder mixture is heated at a higher heating rate, for example, 15 K/min, the synthesis reaction will end at a higher temperature and lead to the formation of the Mg+Mg2Sn eutectic phase. Therefore, a lower heating rate is recommended to synthesize the Mg2Sn particulate in Mg-Sn powder mixture.
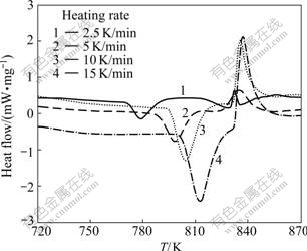
Fig.1 DSC curves for non-isothermal synthesis of Mg2Sn at different heating rates
3.2 Non-isothermal synthesis kinetics of Mg2Sn
3.2.1 Activation energy of Mg2Sn synthesis
The equation of a reaction rate under non- isothermal condition is usually written in the form[13]:
(1)
where α, A, β, Ea, R, T and f(α) are the degree of conversion, pre-exponential factor, heating rate, reaction activation energy, gas constant, temperature and conversion function, respectively.
The model-fitting and model-free approaches are commonly used in the reaction kinetics evaluation. In the model-fitting approach, the reaction activation energy is obtained by fitting experimental data to the assumed conversion function. However, the model-free method is more convenient to evaluate the reaction activation energy without knowing the conversion function[14]. The Ozawa method and KAS method are the famous model-free approaches, in which Ea can be calculated as a function of α[15]. The reaction mechanism can be obtained according to the dependence of Ea on α. The Ozawa equation and KAS equation are given in Eq.(2) and Eq.(3), respectively:
(2)
(3)
where g(α) is the integral representation of f(α). According to the Ozawa equation and KAS equations, the reaction activation energy for the synthesis of Mg2Sn corresponding to different degrees of conversion can be obtained by
and d[β/(T2)]/ d[1/(RT)], respectively. The calculated results are listed in Table 1. The average values of activation energy calculated by the two methods are 275.5 kJ/mol and 269.6 kJ/mol, respectively. Their derivation is only 2.2%, which implies the calculated results are credible [14]. In addition, for each method, the values of reaction activation energy keep almost constant corresponding to the different degrees of conversion, which reflects that the reaction mechanism in the whole process of Mg2Sn synthesis is invariant. In order to clarify the reaction mechanism, it is necessary to obtain the expression of conversion function, f(α) or g(α).
Table 1 Activation energies of synthesis of Mg2Sn calculated by model-free methods
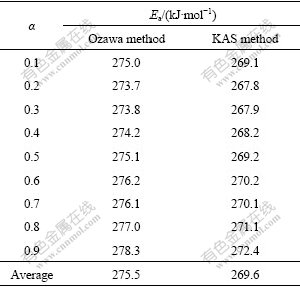
3.2.2 Conversion function of Mg2Sn synthesis
The Coats-Redfren equation[15] written in the Eq.(4) is a typical model-fitting method to investigate the reaction kinetics:
(4)
The activation energy can be calculated from the slope of the plot of ln[g(α)/T2] vs 1/T for the different α values, when the conversion function, g(α), is selected. The possible conversion functions (41 different forms) have been introduced in Refs.[16-17]. Every conversion function is applied to Eq.(4) and the calculated activation energy is compared with the value obtained by Eq.(2) and Eq.(3). If the values of the activation energy evaluated by Eq.(4) is the nearest to the results calculated from the model-free methods (the Ozawa method and KAS method), the selected conversion function is proved to be incredible[15]. When the conversion function, g(α) is selected as [-ln(1-α)]1/4, the values of activation energy at different heating rates are calculated and shown in Table 2. The derivation of Ea at different heating rates is so small that it can be neglected, which implies the reaction mechanism of Mg2Sn synthesis is independent of the heating rate. Moreover, in the 41 conversion functions, g(α)=[-ln(1-α)]1/4 is proved to be a preferable conversion function, making the relative derivation of activation energy calculated by the model-free method and model-fitting method reach the lowest value (about 5%). The conversion function, g(α)= [-ln(1-α)]1/4 indicates that the synthesis mechanism of Mg2Sn in Mg-Sn powder mixture is “nucleation and growth”[16-17]. It is suggested that the average value (281.7 kJ/mol) of activation energy calculated by Eq.(2), Eq.(3) and Eq.(4) can be regarded as the ultimate Ea of Mg2Sn synthesis.
Table 2 Activation energies of synthesis of Mg2Sn calculated by model-fitting method
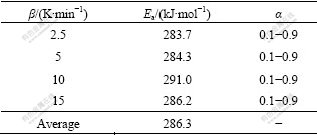
3.3 Microstructure evolution of Mg2Sn in heating process
The optical microscopy photographs of the four samples quenched at 798, 813, 828 and 843 K, respectively, are shown in Fig.2. The XRD patterns of these samples quenched at 798 and 828 K are shown in Fig.3. Fig.2(a) indicates that most Mg powders still keep in sphere shape and the Sn powders are melted and come into the interval of Mg powders when the powder mixture is heated to 798 K. Some small particles appear in Sn liquid, especially on the interface of Mg powder and Sn liquid. It can be seen from Fig.3(a) that the diffraction peaks of Mg2Sn appear when the powder mixture is heated to 798 K. These small particles can be identified as Mg2Sn. Even though a small amount of Sn power is added into a large amount of Mg powder, a Sn-rich region is formed in the local position of Sn distribution. According to the phase diagram of Sn-rich corner in Mg-Sn binary system[12], it can be found that Mg will be dissolved into liquid phase after the temperature exceeds the melting point of Sn. With the temperature increasing, more and more Mg will be dissolved into liquid Sn. Once the solubility of Mg in liquid Sn exceeds the ultimate value in the heating process, Mg2Sn will nucleate. Obviously, it is on the interface between Mg powder and liquid Sn where the solubility of Mg reaches the ultimate value firstly. Hence, the Mg2Sn particulates nucleated on the interface are much more than those inside the liquid Sn (Fig.2(a)). When the powder mixture is heated to 813 K, the block of Mg2Sn is formed in the liquid Sn (Fig.2(b)). This indicates that the Mg2Sn particulates come to cluster and grow with the heating temperature increasing continuously. When the heating temperature reaches 828 K, it can be seen from Fig.2(c) that the surplus liquid Sn reacts with Mg powder completely, which agrees with the result of XRD shown in Fig.3(b). The latter indicates that the diffraction peaks of Sn disappear when the heating temperature reaches 828 K. When the heating temperature increases from 798 K to 828 K, it is found that the “nucleation and growth” reaction mechanism controls the whole process of Mg2Sn synthesis. When the heating temperature arrives at 843 K, the synthesized Mg2Sn particulates develop into the eutectic phase composed of Mg+Mg2Sn (Fig.2(d)). After all of liquid Sn react with Mg powder, the reaction system transforms from Mg+Sn+Mg2Sn into Mg+Mg2Sn. In the Mg-rich corner of Mg-Sn phase diagram[12], there is an eutectic reaction (α-Mg+Mg2Sn→Liquid) at about 834 K. This eutectic reaction is also proved by the endothermal peak in the temperature range of 828-853 K on DSC curves (Fig.1). From the above discussion, it can be found that the synthesis mechanism of Mg2Sn deduced from the kinetic theory based on DSC is further confirmed by the evolution of Mg2Sn in the Mg-Sn powder mixture. The reaction mechanism of 2Mg+Sn→Mg2Sn under non- isothermal condition is regarded as “nucleation and growth”.
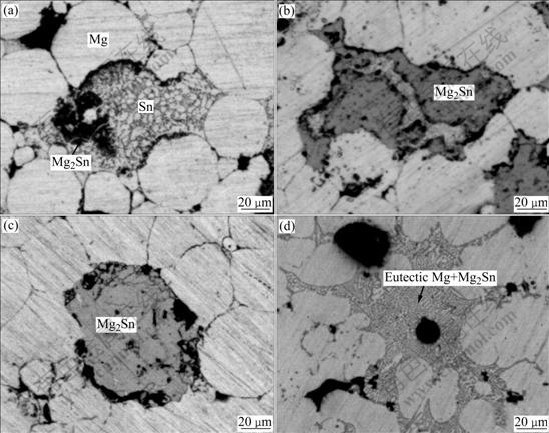
Fig.2 Microstructures of samples quenched at different temperatures: (a) 798 K; (b) 813 K; (c) 828 K; (d) 843 K
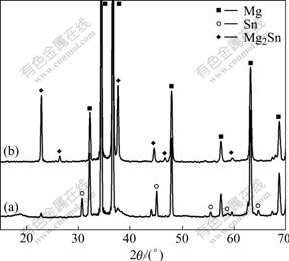
Fig.3 X-ray diffraction patterns of samples quenched at different temperatures: (a) 798 K; (b) 813 K
4 Conclusions
1) The non-isothermal heating process of Mg-Sn powder mixture was studied by DSC technique and the synthesis kinetics of Mg2Sn was evaluated by the model-free and model-fitting methods. The activation energy and conversion function of Mg2Sn synthesis reaction are calculated to be 281.7 kJ/mol and g(α)=[-ln(1-α)]1/4, respectively. The reaction mechanism of 2Mg+Sn→Mg2Sn under non-isothermal condition is regarded as “nucleation and growth”.
2) During the non-isothermal heating process, the phase transformation occurring in the Mg-Sn powder mixture was analyzed by XRD and the microstructure evolution of Mg2Sn was observed by optical microscopy, which is in good agreement with the reaction mechanism of 2Mg+Sn→Mg2Sn deduced from the kinetic evaluation.
References
[1] YIN Dong-song, ZHANG Er-lin, ZENG Song-yan. Effects of Zn on mechanical property and corrosion property of extruded Mg-Zn-Mn alloy [J]. Trans Nonferrous Met Soc China, 2008, 18(4): 763-768.
[2] GUAN Shao-kang, WU Li-hong, WANG Li-guo. Flow stress and microstructure evolution of semi-continuous casting AZ70 Mg alloy during hot compression deformation [J]. Trans Nonferrous Met Soc China, 2008, 18(2): 315-320.
[3] ZHOU Hong-hui. Effects of microstructure on creep behavior of Mg-5%Zn-2%Al(-2%Y) alloy [J]. Trans Nonferrous Met Soc China, 2008, 18(3): 580-587.
[4] GULDBERG S, RYUM N. Microstructure and crystallographic orientation relationship in directionally solidified Mg-Mg17Al12 eutectic [J]. Mater Sci Eng A, 2000, 289: 143-150.
[5] KANG D H, PARK S S, KIM N J. Development of creep resistant die cast Mg-Sn-Al-Si alloy [J]. Mater Sci Eng A, 2005, 413/414: 555-560.
[6] SASAKIA T T, OH-ISHIB K, OHKUBOB T, HONO K. Enhanced age hardening response by the addition of Zn in Mg-Sn alloys [J]. Script Mater, 2006, 55(3): 251-254.
[7] MENDIS C L, BETTLES C J, GIBSON M A, HUTCHINSON C R. An enhanced age hardening response in Mg-Sn based alloys containing Zn [J]. Mater Sci Eng A, 2006, 435/436: 163-171.
[8] LIU H M, CHEN Y G, TANG Y B, WEI S H, NIU G. The microstructure, tensile properties, and creep behavior of as-cast Mg-(1-10)%Sn alloys [J]. J Alloys Comp, 2007, 444(1/2): 122-126.
[9] WANG L, QIN X Y. The effect of mechanical milling on the formation of nanocrystalline Mg2Si through solid-state reaction [J]. Script Mater, 2003, 49(3): 243-248.
[10] YUAN G Y, LIU Z L, WANG Q D, DING W J. Microstructure refinement of Mg-Al-Zn-Si alloys [J]. Mater Let, 2002, 56(1/2): 53-58.
[11] LU L, THONG K K, GUPTA M. Mg-based composite reinforced by Mg2Si [J]. Compos Sci Technol, 2003, 63: 627-632.
[12] NAYEB-HASHEMI A A, CLARK J B. The Mg-Sn (magnesium-tin) system [J]. Bull Alloy Phase Diagrams, 1984, 5(5): 467-476.
[13] HU Rong-zu, SHI Qi-zhen. Thermal analysis kinetics [M]. Beijing: Science Press, 2001: 1-3. (in Chinese)
[14] WAZOYKIN S, WIGHT C A. Isothermal and nonisothermal reaction kinetics in solids: In search of ways toward consensus [J]. Phys Chem A, 1997, 101: 8279-8284.
[15] LIN C M, TANG D H, TANG W J, PENG J H. Synthesis of MgNi2O3 and kinetics of thermal decomposition of the oxalate precursor [J]. Anal Appl Pyrolysis, 2006, 75: 240-244.
[16] HU Rong-zu, SHI Qi-zhen. Thermal analysis kinetics [M]. Beijing: Science Press, 2001: 127-135. (in Chinese)
[17] HU R Z, CHEN S P, GAO S L, ZHAO F Q, LUO Y, GAO H X, SHI Q Z, ZHAO H G, YAO P, LI J. Thermal decomposition kinetics of Pb0.25Ba0.75(TNR)·H2O complex [J]. J Hazard Mater A, 2005, 117: 103-110.
Foundation item: Project(2007CB613706) supported by the National Basic Research Program of China; Project(0330005412901) supported the Key Disciplines Development of Beijing Municipality (“Resources, Environment and Recycling Economy” Interdisciplinary), China; Project(X0104001200905) supported by the Scientific Research Foundation for the New Doctoral Teachers, Beijing University of Technology, China
Corresponding author: WU Yu-feng; Tel: +86-10-67396263; Fax: +86-10-67396234; E-mail: wuyufeng@bjut.edu.cn
DOI: 10.1016/S1003-6326(08)60428-8
(Edited by YANG Bing)