DOI: 10.11817/j.ysxb.1004.0609.2020-37704
3CaO·2SiO2高温固相反应生成机理及稳定性
裴健男1, 2,潘晓林1, 2,崔维学2,于海燕1, 2,涂赣峰1, 2
(1. 东北大学 多金属共生矿生态化冶金教育部重点实验室,沈阳 110819;
2. 东北大学 冶金学院,沈阳 110819)
摘 要:为了降低烧结法生产氧化铝配钙量和提高生成硅酸钙稳定性,系统研究3CaO·2SiO2 (C3S2)在高温烧结过程中的生成动力学、转变机理以及在铝酸钠溶液中的稳定性。研究表明:在CaO-SiO2二元体系中,CaO和SiO2摩尔比(C/S)为1.5:1时物料的非等温烧结过程主要分为CaO·SiO2 (CS)和2CaO·SiO2 (C2S)的生成与转化、CS和C2S转化成C3S2以及C3S2分解为C2S.和CS三个阶段;在1460 ℃保温1 h时,烧结产物中C3S2含量达到最大,为75.6%;延长保温时间促进C3S2的生成,并降低C3S2的生成温度。C3S2的生成反应控制步骤为二级化学反应控制,其活化能为339.67 kJ/mol,指前因子为1.31×109 s-1。烧结产物在铝酸钠溶液中的稳定性随着C3S2含量的升高而增强,硅酸钙化合物的稳定性顺序为:C3S2>C2S>CS。
关键词:硅酸钙;固相反应;动力学;稳定性;烧结法
文章编号:1004-0609(2020)-12-2963-08 中图分类号:TF821 文献标志码:A
硅酸钙是重要的无机非金属材料,广泛应用于水泥[1-2]、陶瓷[3-4]、保温材料[5]和生物材料[6-7]等行业。其二元化合物包括CaO·SiO2 (CS)、2CaO·SiO2 (C2S)、3CaO·SiO2 (C3S)和3CaO·2SiO2 (C3S2),其中C2S和C3S是硅酸盐水泥的主要成分,可用于水泥基复合材料;CS在体液中具有生物活性,在其表面能够诱导骨磷灰石形成,可作为潜在的骨组织工程生物材料的基体;C3S2中掺杂Eu2+和Ce3+等稀土离子后,可用作红色荧光材料。硅酸钙的制备方法较多,一般包括高温固相合成法[8]、溶胶-凝胶法[9]、共沉淀法[10]和水热合成法[11]等,其中高温固相合成法由于其应用范围广、工艺简单、易于工业化,是合成硅酸钙的主要方法。
硅酸二钙(C2S)是烧结法生产氧化铝工艺中二氧化硅的目标物相,其在熟料浸出过程中能够发生一定程度的二次反应,从而导致氧化钠和氧化铝的损失。许多学者对不同晶型C2S的生成机理及其在碱液中的稳定性开展了研究。李小斌等[12]研究了烧结法生产氧化铝熟料溶出过程中SiO2的行为,结果表明β-C2S在3种碱性溶液中的热力学稳定性次序为NaOH>NaAl(OH)4>Na2CO3;王波等[13]在不同降温速度下合成了C2S,研究表明提高降温速度能够使γ-C2S的稳定性降低;SUN等[14]研究发现,熟料中γ-C2S的反应率随着浸出时间的延长和碳酸钠浓度的增加而上升,主要二次反应产物为水化石榴石和钠硅渣的混合物;作者研究发现Na2O的存在和矿石中的B、P等杂质均能阻止β-C2S向γ-C2S的转变,降低C2S的稳定性[15-17]。
烧结法是目前处理低品位铝资源工业应用的主要方法,在此过程中通常会加入过量的石灰,使SiO2形成较稳定的2CaO·SiO2,实现铝硅分离,但是,加入过量石灰会造成赤泥的含量增加,进而给赤泥后续的处理增加难度;同时2CaO·SiO2在浸出、分离过程中与浸出液会形成较难溶的含氧化铝和碱的硅渣,造成氧化铝和苛性碱的损失,因此降低烧结法配钙量、生成稳定的硅酸钙一直是烧结法改进的主要方向。ARLYUK[18]通过研究C/S为1时CaO-SiO2二元系烧结过程时发现,C2S总是最先生成,只有按C2S+S→CS才有可能生成CS,生成C3S和C3S2的可能性很小;LIU等[19]在C/S为1和2时分别在1200 ℃和1400 ℃合成了CS和β-C2S,结果表明CS在烧碱和纯碱溶液中的稳定性均高于β-C2S;张明等[20]研究了烧结法处理我国高铁中等品位矿石的工艺条件时发现,C/S为1.5时烧结产物中存在C3S2物相;刘伟[21]通过CaO与铝硅酸钠反应研究C3S2的反应行为,表明C3S2反应的动力学过程符合Jander模型,反应过程受固体反应物向反应界面的扩散控制。C3S2的C/S只有1.5,如果能够代替C/S为2的C2S作为二氧化硅的目标矿相,能够大幅度降低烧结法的配钙量和渣量,同时在熟料浸出过程中若C3S2能够发生较少的二次反应,可大大降低氧化钠和氧化铝的损失。目前,对C3S2的生成转化机理和稳定性研究还很缺乏,在CaO-SiO2二元系中C3S2的生成行为还鲜有研究。本文基于CaO-SiO2二元系,研究了C/S=1.5时C3S2在高温加热和烧结过程中的生成动力学、转变机理及其在铝酸钠溶液中的稳定性,为低钙比烧结法生产氧化铝的工艺创新提供理论基础。
1 实验
首先采用分析纯CaCO3和SiO2为原料,按照C/S=1.5进行配料,并在聚乙烯混料罐中混合2 h,然后压制成直径为2 cm的圆柱,装进石墨坩埚内并置入1700X型高温炉进行烧结。其中烧结过程分为两种形式,一种是升温至预定温度后不保温,直接取出在空气中冷却;另一种是升至预定温度后,保温1 h,然后取出在空气中冷却。冷却至室温后,研究其反应机理。
烧结产物稳定性试验步骤为首先将三口烧瓶放入恒温水浴锅中,安装好搅拌器及冷凝器,然后按照试验所需的液固比将烧结产物和铝酸钠溶液缓慢倒入三口烧瓶中并打开搅拌装置,待反应结束后,用布氏漏斗进行液固分离。溶液中SiO2浓度的测定采用硅钼兰比色法测定。
XRD分析检测采用荷兰Philips X′Pert PW3040-60型X射线衍射分析仪,在烧结产物中混入10% MgO(质量分数)作为内标,根据XRD软件半定量分析[22],计算烧结产物的各物相含量,计算公式如下:
(1)
式中:Ii、Ri、wi分别为物相i的特征峰强度、RIR值、质量分数;IMgO、RMgO、wMgO为MgO的特征峰强度、RIR值、质量分数。
2 结果与讨论
2.1 C3S2的生成热力学
由CaO-SiO2二元相图可知硅酸钙类化合物主要有C3S、C2S、C3S2和CS四种,当C/S=1.5时,由氧化物生成上述硅酸钙的反应如下:
SiO2+CaO=CaO·SiO2 (2)
SiO2+(3/2)CaO=(3/4)(2CaO·SiO2)+(1/4)SiO2 (3)
SiO2+3/2CaO= (1/2)(3CaO·SiO2)+(1/2)SiO2 (4)
SiO2+(3/2)CaO= (1/2)(3CaO·2SiO2) (5)
图1所示为硅酸钙生成反应的
关系图,由图1可知,四种硅酸钙生成反应的
均为负,理论上说明四种硅酸钙的生成反应是可以发生的。根据不同硅酸钙
的绝对值大小,可以得到生成这些化合物的热力学稳定性大小。根据计算,在小于1600 K时,稳定性顺序由大到小依次是:C3S2、C2S、CS、C3S,在高于1600 K时,C3S的稳定性逐渐超过CS,最稳定的硅酸钙化合物仍然是C3S2。
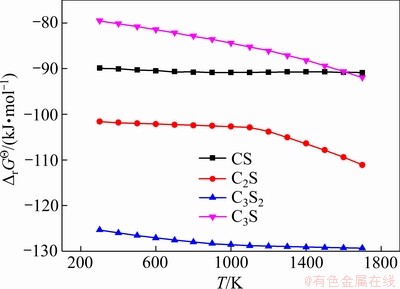
图1 硅酸钙生成反应的
关系图
Fig. 1 Gibbs free energy for formation reactions of calcium silicate compounds
2.2 C3S2的物相转变行为
图2所示为C/S为1.5、不保温的条件下,不同烧结温度下烧结产物的XRD谱。由图2可知,在该温度段内存在的主要物相分别是C3S2、CS、β-C2S和未反应的SiO2、CaO。其中,C3S2的PDF卡片是22-0539,属于双岛状硅酸钙,是P21/a(14)空间群组,晶体学参数为:a=10.614,b=8.914,c=7.847 nm;β=119.6°。CS的PDF卡片是31-0300,属于环状硅酸钙,是P-1(2)空间群组,晶体学参数为:a=6.820,b=6.820,c=19.650 nm;α=β=90.4°,γ=119.3°。β-C2S的PDF卡片是33-0302,属于斜硅钙石,是P21/n(14)空间群组,晶体学参数为:a=9.310,b=6.756,c=5.506 nm;α=γ=90.0°,β=94.46°。
对烧结产物中各物相进行半定量分析,表1所列为烧结产物中未反应的SiO2和CaO含量,图3所示为生成的CS、C2S和C3S2含量变化。结合图2、图3和表1可知,随着温度的提高,CaO、SiO2的峰强逐渐降低,反应程度进行更为彻底,说明温度的升高有利于固相反应的进行。当加热温度为1350 ℃时,烧结产物中主要物相为CS和C2S,以及少量未反应的CaO和SiO2,这是由于温度较低时不利于物料扩散,反应进行比较缓慢,反应不完全。当温度升高到1400 ℃时,CS和C2S的峰强逐渐增强,CS含量由36.3%升高到45.5%,C2S含量由46.4%升高到50.8%,CaO和SiO2含量分别降到1.1%和1.5%,反应程度逐渐增强,反应接近完全,说明升高温度有利于固态反应期间的元素扩散,加快烧结反应的进程,促进反应发生。当加热温度升高到1460 ℃时,CS和C2S含量降低,并出现C3S2相,表明C3S2在该温度能够形成。继续升高温度到1480 ℃,C3S2的峰强降低,含量由39.2%下降到26%,C2S和CS的峰强增强,C2S含量由39.1%下降到31.7%,CS含量由21.6%升高到42.3%,这是由于随着温度的进一步升高,C3S2首先分解成C2S和SiO2,然后C2S和SiO2反应进一步生成CS。
根据图3中CS、C2S和C3S2的含量变化可以将反应过程分为三段,在1400 ℃以下温度范围内,主要发生CaO与SiO2反应生成CS、C2S及CS与C2S的相互转化;在1400~1460 ℃发生CS与C2S的反应生成C3S2;1460~1480 ℃发生的反应是C3S2分解为C2S、SiO2及C2S与SiO2的反应生成CS。因此,1400~1480 ℃是C3S2发生反应的主要温度段,在此温度段内,其含量在1460 ℃达到最大,为39.2%。
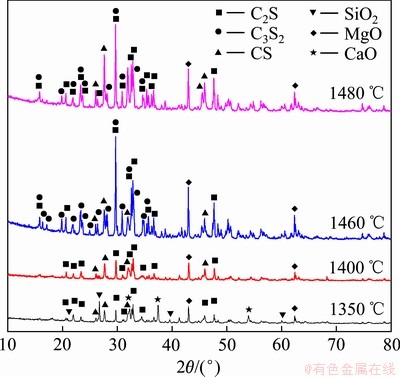
图2 不同烧结温度下未保温烧结产物XRD谱
Fig. 2 XRD patterns of sintered products at different temperatures without duration
表1 不同烧结温度下未保温烧结产物中SiO2和CaO含量
Table 1 Contents of SiO2 and CaO in sintered products at different temperatures without duration
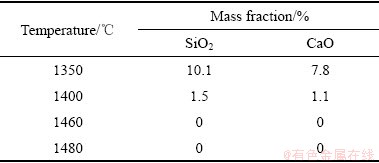
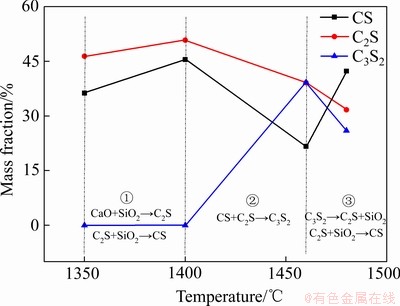
图3 不同烧结温度下未保温烧结产物中硅酸钙的含量变化
Fig. 3 Contents of calcium silicate compounds in sintered products at different temperatures without duration
图4所示为C/S为1.5、保温时间为1 h的条件下,不同烧结温度下烧结产物的XRD谱。同时对烧结产物中各物相进行半定量分析,表2所列为烧结产物中未反应SiO2和CaO的含量。图5所示为生成的CS、C2S和C3S2含量变化。结合图4、图5和表2可知,在1300 ℃时,烧结产物物相成分主要为CS和C2S,以及未参与反应的SiO2和CaO,说明烧结温度低,物料扩散缓慢,烧结原料未反应完全。当烧结温度升高到1400℃时,CS含量由31.9%下降到16.8%,C2S含量由55.6%下降到18.2%,并出现C3S2物相,而且含量达到58.6%,成为主要物相。当温度升高到1460 ℃时,C3S2含量达到最大值75.6%,CS和C2S含量进一步降低,C3S2的峰强随着温度的升高逐渐变强,说明随着温度升高,C3S2的结晶度越来越好,结晶趋于完善。因此,1300~1460 ℃是C3S2生成的主要温度段。继续升高温度到1480 ℃时,C3S2物相消失,CS和C2S含量分别升高到65.8%和31.4%,主要物相变为CS和C2S。因此,1460~1480 ℃是C3S2的分解温度段,而且分解速率很快。对比图3与图5不同烧结时间的烧结产物各物相含量可知,在相同温度下,随着时间的延长,C3S2的含量升高,这是由于保温时间较短时,物料扩散缓慢,烧结原料未反应完全,延长保温时间,可加快烧结反应进程,使烧结产物总体结晶度升高,有利于C3S2生成,促进反应的进行。
根据图5可知,CS、C2S和C3S2含量变化大致可以分为两段,即C3S2生成阶段和C3S2分解阶段,其中,1300~1460 ℃为C3S2生成阶段,1460~1480 ℃为C3S2分解阶段。C3S2的生成温度在保温1 h条件下比不保温时低,说明在相同的烧结温度下,延长保温时间有助于Ca2+扩散到SiO2界面和晶格中,加快烧结反应进程,促进固相反应的发生及C3S2的生成。因此,在相同温度条件下,保温1 h物料生成的C3S2含量较不保温物料中的高;相同烧结时间时,在C3S2的生成阶段,随着温度的升高,促进物料之间的扩散,加速反应进行,C3S2含量也随之升高。
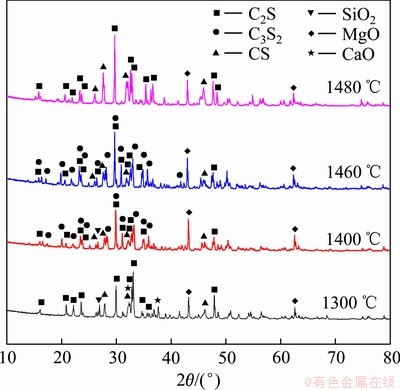
图4 不同烧结温度下保温1 h烧结产物XRD谱
Fig. 4 XRD patterns of sintered products at different temperatures for 1 h
表2 不同烧结温度下保温1 h烧结产物中SiO2和CaO含量
Table 2 Content of SiO2 and CaO insinteredproducts at different sintering temperatures for 1 h

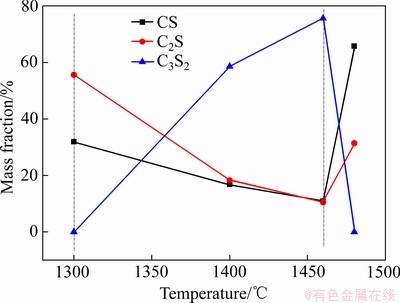
图5 不同烧结温度下保温1 h烧结产物中硅酸钙的含量变化
Fig. 5 Contents of calcium silicate compounds in sintered products at different temperatures for 1 h
2.3 C3S2的生成动力学
由图5中C3S2含量变化可知,在1300~1460 ℃是C3S2的生成阶段,因此以1300 ℃至1460 ℃阶段C3S2的含量变化分析C3S2的生成动力学。图6所示为C/S为1.5、保温时间为1 h、烧结温度为1340~1460 ℃条件下烧结产物的XRD谱。同时对烧结产物中各物相进行半定量分析,含量如图7所示。
本试验中采用Coats-Redfern法[23]来确定反应模型和相应的方程式,见式(6):
(6)
式中:
为反应模型的积分形式;A为指前因子,s-1;E为反应活化能,kJ/mol;R为摩尔气体常数,J/(℃·mol);T为反应温度,K;β为升温速度,K/s。
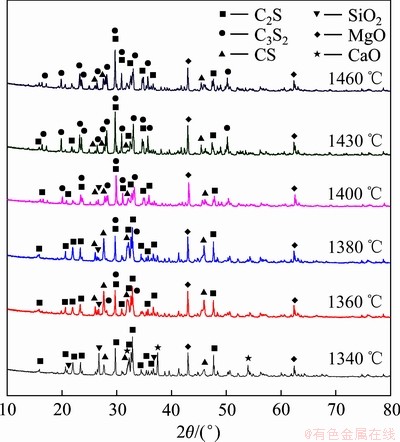
图6 不同烧结温度下保温1 h烧结产物XRD谱
Fig. 6 XRD patterns of sintered products at different temperatures for 1 h
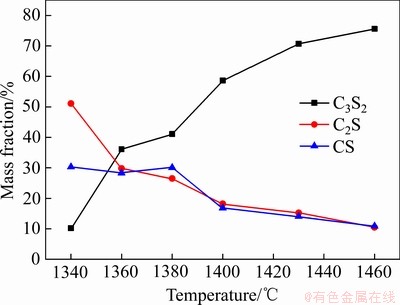
图7 不同烧结温度下保温1 h烧结产物中的各物相含量
Fig. 7 Content of calcium silicate compounds in sintered products at different sintering temperatures for 1 h
对一般的反应温区,E/(RT)﹥﹥1,1-2RT/E≈1,所以式(6)右端第一项可看作常数,以
对
作图能得到一条直线,根据斜率和截距求得反应活化能E和指前因子A,其中线性关系较好者确定为该固相反应的模型。
将C3S2的生成率
带入到表3的固相反应模型[24]中,并对曲线进行线性拟合,得到相关系数
,如表3所列。由表3可知,F2模型的线性相关系数最高。图8所示为根据F2模型得到的C3S2生成过程动力学函数数据线性回归结果。根据斜率与截距可求出活化能E与指前因子A分别为339.67 kJ/mol和1.31×109 s-1,在固-固相反应的指前因子的理论值1×106~ 1×1018 s-1范围内[25]。因此,C3S2的生成属于二级反应模型,此反应过程的控制环节是化学反应控制,C3S2的生成动力学方程为式:
(7)
2.4 C3S2的稳定性
将C/S为1.5、保温时间为1 h,不同温度条件下的烧结产物与铝酸钠溶液(NaOH浓度为69.5 g/L(以Na2O计),Na2CO3浓度为38.6 g/L(以Na2O计),Al2O3浓度为64.5 g/L)在反应温度80 ℃、反应时间30 min、液固比为10条件下进行反应,并计算出硅酸钙反应率,反应率计算式(η)见式(8)。


(8)
式中:η为硅酸钙的反应率,%;
为溶液中二氧化硅浓度,g/L;V为溶液总体积,mL;m为烧结产物质量,g;
、
和
分别为烧结产物中C3S2、C2S和CS的含量,%;
、
、
和
分别为C3S2、C2S、CS和SiO2相对分子质量。
表3 不同固相反应速率模型下C3S2生成的计算结果
Table 3 Calculated results of C3S2 formation with different reaction rate models
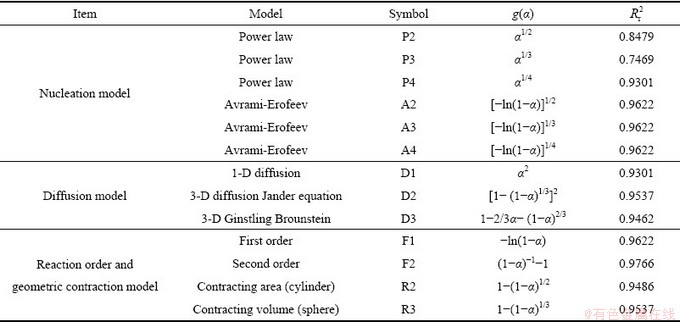

图8 C3S2生成过程动力学函数线性回归结果
Fig. 8 Linear relationship for formation of C3S2 according to F2 model
图9所示为不同烧结温度下烧结产物反应后溶液SiO2浓度及硅酸钙反应率。结合图9和图7可知,随着烧结温度的提高,烧结产物与铝酸钠溶液反应后SiO2浓度和硅酸钙的反应率总体趋势是降低的,C3S2的含量整体呈上升趋势,C2S和CS含量整体呈下降趋势,说明烧结产物在铝酸钠溶液中的稳定性随着C3S2含量的升高而增强,进一步说明C3S2的稳定性强于C2S和CS。在1360~1380 ℃温度段内,SiO2浓度和硅酸钙反应率略有上升,通过观察硅酸钙物相的含量变化,SiO2浓度和硅酸钙反应率的变化趋势与固相中CS含量的变化趋势一致,在1360~1380 ℃温度段内,部分C2S转化为CS,C2S含量降低,CS含量升高,同时反应液中的SiO2浓度升高,硅酸钙反应率变大,说明C2S的稳定性强于CS的。因此,硅酸钙化合物的稳定性顺序为:C3S2>C2S>CS,这与热力学分析结果相一致。
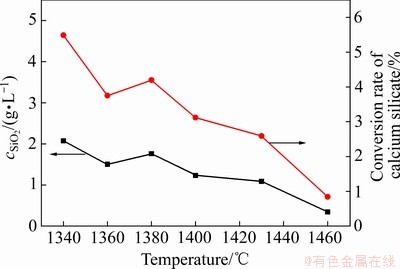
图9 不同烧结温度下烧结产物反应后SiO2浓度及硅酸钙反应率
Fig. 9 Calcium silicate reaction ratio of sintered products and SiO2 concentration in leached solution at different sintering temperatures
3 结论
1) 在CaO-SiO2二元体系中,C/S为1.5物料的非等温烧结过程主要分为CS和C2S的生成与转化、CS和C2S转化成C3S2以及C3S2分解为C2S.和CS三个阶段;烧结温度为1460 ℃,保温1 h时,烧结产物中C3S2含量达到最高值75.6%;延长保温时间促进C3S2的生成。
2) C3S2的生成反应控制步骤为二级化学反应控制,其活化能为339.67 kJ/mol,指前因子为1.31×109 s-1,生成动力学方程为(1-α)-1-1=1.31×109× e-339670/(RT)×t。
3) 烧结产物在铝酸钠溶液中的稳定性随着C3S2含量的升高而增强,硅酸钙化合物的稳定性顺序为:C3S2>C2S>CS。
REFERENCES
[1] RICARDO S, FRANCO Z. Recycling of hydratiod cement pastes by synthesis of α′H-C2S[J]. Cement and Concrete Research, 2017, 100: 398-412.
[2] LARBI K, MARTIN C, PIERRE C. Synthesis of α′L-C2S cement from fly-ash using the hydrothermal method at low temperature and atmospheric pressure[J]. Journal of Hazardous Materials, 2010, 181: 593-601.
[3] CEKDAR V. Zeolite decoratiod highly porous acicular calcium silicate ceramics[J]. Ceramics International, 2014, 40(8): 11925-11932.
[4] LINK L, CHANG J, ZENG Y, QIAN W J. Preparation of macroporous calcium silicate ceramics[J]. Materials Letters, 2004, 58(15): 2109-2113.
[5] 郭曦尧, 马淑花, 吕松青, 郑诗礼, 邹 兴. 以脱铝赤泥-脱铝粉煤灰为原料制备硬硅钙石[J]. 中国有色金属学报, 2015, 25(2): 534-544.
GUO Xi-yao, MA Shu-hua, Lü Song-qing, ZHENG Shi-li, ZOU Xing. Preparation of xonotlite using red mud and fly ash after removal alumina as raw materials[J]. The Chinese Journal of Nonferrous Metals, 2015, 25(2): 534-544.
[6] LI H, CHANG J. Stimulation of proangiogenesis by calcium silicate bioactive ceramic[J]. Acta Biomaterialia, 2013, 9(2): 5379-5389.
[7] CHEN C C, HO C C, LIN S Y, DING S J. Green synthesis of calcium silicate bioceramicpowders[J]. Ceramics International, 2015, 41(4): 5445-5453.
[8] LONG L H, CHEN L D, BAI S Q, CHANG J, LIN K L. Preparation of dense β-CaSiO3 ceramic with high mechanical strength and HAp formation ability in simulated body fluid[J]. Journal of the European Ceramic Society, 2006, 26(9): 1701-1706.
[9] 朱宏扬, 尹光福, 吴 江, 陈显春. 溶胶-凝胶法制备硅酸钙及其体外生物活性的研究[J]. 生物医学工程研究, 2008, 27(1): 9-12.
ZHU Hong-yang, YIN Guang-fu, WU Jiang, CHEN Xian-chun. In vitro bioactivity of calcium silicate prepared by sol-gel process[J]. Biomedical Engineering Research, 2008, 27(1): 9-12.
[10] 刘孟彬, 李 蔚, 杨爱霞. 共沉淀法低温合成β-CaSiO3纳米粉体[J]. 华东理工大学学报(自然科学版), 2011, 37(3): 315-319.
LIU Meng-bin, LI Wei, YANG Ai-xia. Low temperature preparation of β-CaSiO3 nanopowder via coprecipitation process[J]. Journal of East China University of Science and Technology (Natural Science), 2011, 37(3): 315-319.
[11] 佟 钰, 王 朔, 马秀梅. 水化硅酸钙的晶型调控及其对吸/放湿性能的影响[J]. 硅酸盐通报, 2019, 38(1): 83-87.
TONG Yu, WANG Shuo, MA Xiu-mei. Crystallinity regulation of calcium silicate hydratio and its influence on moisture absorption/desorption properties[J]. Silicate Bulletin, 2019, 38(1): 83-87.
[12] 李小斌, 徐华军, 刘桂华, 彭志宏, 周秋生, 刘云峰. 氧化铝熟料溶出过程中SiO2的行为[J]. 过程工程学报, 2006, 6(3): 431-434.
LI Xiao-bin, XU Hua-jun, LIU Gui-hua, PENG Zhi-hong, ZHOU Qiu-sheng, LIU Yun-feng. Behavior of SiO2 during leaching process of alumina sinter[J]. Journal of Process Engineering, 2006, 6(3): 431-434.
[13] 王 波, 刘佳佳, 孙会兰, 马东东. 降温速度对γ-2CaO·SiO2分解性能和晶体结构的影响[J]. 中国有色金属学报, 2016, 26(8): 1817-1822.
WANG Bo, LIU Jia-jia, SUN Hui-lan, MA Dong-dong. Effect of cooling ratio on decomposition property and crystal structure of γ-2CaO·SiO2[J]. The Chinese Journal of Nonferrous Metals, 2016, 26(8): 1817-1822.
[14] SUN H L, WANG B, ZHANG J X, ZONG S F, LIU J J. Secondary reaction mechanism of leaching process of calcium aluminate slag[J]. Transactions of Nonferrous Metals Society of China, 2015, 25(4): 1334-1340.
[15] YU H Y, PAN X L, WANG B, ZHANG W, SUN H L, BI S W. Effect of Na2O on formation of calcium aluminates in CaO-Al2O3-SiO2 system[J]. Transactions of Nonferrous Metals Society of China, 2012, 22(12): 3108-3112.
[16] 潘晓林, 董凯伟, 侯宪林, 于海燕, 涂赣峰, 毕诗文. 含硼铝酸钙熟料的高温成矿机理及其浸出性能[J]. 中国有色金属学报, 2014, 24(6): 1663-1670.
PAN Xiao-lin, DONG Kai-wei, HOU Xian-lin, YU Hai-yan, TU Gan-feng, BI Shi-wen. High-temperature metallogenic mechanism and leaching property of calcium aluminate clinker with B2O3[J]. The Chinese Journal of Nonferrous Metals, 2014, 24(6): 1663-1670.
[17] YU H Y, PAN X L, DONG K W, WU Y. Effect of P addition on mineral transition of CaO-Al2O3-SiO2 system during high-temperature sintering[J]. Transactions of Nonferrous Metals Society of China, 2019, 29(3): 650-656.
[18] ARLYUK B I. Study of an effect of a nepheline raw material composition on process parameters of alumina production by the sintering methods[J]. Light Metals,1994: 59-66.
[19] LIU G H, LI X B, PENG Z H, ZHOU Q S. Behavior of calcium silicate in leaching process[J]. Transactions of Nonferrous Metals Society of China, 2003, 13(1): 213-216.
[20] 张 明, 肖 伟, 彭志宏, 周秋生, 李小斌. 高铁一水硬铝石型铝土矿的低钙比烧结[J]. 中国有色金属学报, 2008, 18(10): 1903-1908.
ZHANG Ming, XIAO Wei, PENG Zhi-hong, ZHOU Qiu-sheng, LI Xiao-bin. Sintering process of diasporic bauxite with high iron content at low ratio of lime to silica for alumina production[J]. The Chinese Journal of Nonferrous Metals, 2008, 18(10): 1903-1908.
[21] 刘 伟. 氧化铝熟料制备的基础理论和工艺[D]. 长沙: 中南大学, 2011.
LIU Wei. Basic theory and technology of alumina clinker preparation[D]. Changsha: Central South University, 2011.
[22] ZHOU X, LIU D, BU H L, DENG L L, LIU H M, YUAN P, DU P X, SONG H Z. XRD-based quantitative analysis of clay minerals using reference intensity ratios, mineral intensity factors, Rietveld, and full pattern summation methods: A critical review[J]. Solid Earth Sciences, 2018, 3(1): 16-29.
[23] VYAZOVKIN S, WIGHT C A. Model-free and model-fitting approaches to kinetic analysis of isothermal and nonisothermaldata[J]. Thermochim Acta, 1999, 340(1): 53-68.
[24] 朱航宇, 李正邦, 王堇青. CaCO3与MoO3固相反应机理[J]. 过程工程学报, 2012, 12(2): 227-230.
ZHU Hang-yu, LI Zheng-bang, WANG Jin-qing. Mechanism of solid state reaction between CaCO3 and MoO3[J]. Journal of Process Engineering, 2012, 12(2): 227-230.
[25] TAZUDDIN, AIYER H N, CHATTERJEE A. Phase equilibria studies of CaO-SiO2-Al2O3-Fe2O3-MgO system using CALPHAD[J]. Calphad, 2018, 60: 116-125.
Formation mechanism and stability of 3CaO·2SiO2 during high-temperature solid-state reaction
PEI Jian-nan1, 2, PAN Xiao-lin1, 2, CUI Wei-xue2, YU Hai-yan1, 2, TU Gan-feng1, 2
(1. Key Laboratory for Ecological Metallurgy of Multimetallic Mineral, Ministry of Education, Northeastern University, Shenyang 110819, China;
2. School of Metallurgy, Northeastern University, Shenyang 110819, China)
Abstract: In order to reduce the lime addition and improve the stability of calcium silicates in alumina production by the sinter process, the formation kinetics, transformation mechanism and stability of 3CaO·2SiO2(C3S2) during high- temperature sintering process were investigated. The results show that the non-isothermal sintering process can be divided into three stages in the CaO-SiO2 binary system with the CaO to SiO2 molar ratio (C/S) of 1.5:1, the formation and transformation of CaO·SiO2 (CS) and 2CaO·SiO2 (C2S), the transformation of CS and C2S into C3S2, and the decomposition of C3S2 into C2S and CS. The content of C3S2 in the sintered product reaches the highest value of 75.6% when the sintering temperature is 1460 ℃ and the holding time is 1 h. The prolonging of holding time can promote the formation of C3S2 and reduce its generation temperature. The formation process of C3S2 follows the second-order chemical reaction model, and the corresponding apparent activation energy and the pre-exponential factor are 339.67 kJ/mol and 1.31×109 s-1, respectively. The stability of the sintered products in sodium aluminate solution increases with the increase of C3S2 content, and the stability order of calcium silicate compounds is C3S2>C2S>CS.
Key words: calcium silicate; solid state reaction; formation kinetics; stability; sinter process
Foundation item: Project(51674075) supported by the National Natural Science Foundation of China; Project (2018YFC1901903) supported by the National Key Research and Development Program of China
Received date: 2020-03-09; Accepted date: 2020-06-23
Corresponding author: PAN Xiao-lin; Tel: +86-24-83686460; E-mail: panxl@smm.neu.edu.cn
(编辑 王 超)
基金项目:国家自然科学基金资助项目(51674075);国家重点研发计划(2018YFC1901903)
收稿日期:2020-03-09;修订日期:2020-06-23
通信作者:潘晓林,副教授,博士;电话:024-83686460;E-mail:panxl@smm.neu.edu.cn