J. Cent. South Univ. Technol. (2008) 15: 356-360
DOI: 10.1007/s11771-008-0067-y

Similar material simulation of time series system for induced caving of roof in continuous mining under backfill
GAO Feng(高 峰)1, 2, ZHOU Ke-ping(周科平)1, 2, DONG Wei-jun(董卫军)3, SU Jia-hong(苏家红)1
(1. School of Resources and Safety Engineering, Central South University, Changsha 410083, China;
2. Key Laboratory of Deep Mining and Disaster Control in Hunan Province,
Changsha 410083, China;
3. Beijing General Research Institute of Mining and Metallurgy, Beijing 100044, China)
Abstract: With the help of similar material simulation test, time series system for induced caving of roof in continuous mining under complex backfill in ore body No.92 of Tongkeng Tin Mine was studied. According to the similarity theory, a two-dimensional similar simulation test-bed was constructed. The stress and displacement that change along with the advance of mining were acquired and analyzed automatically by data system. The processes of continuous mining of ore-block in 5 intervals and artificial induced caving of roof were simulated. The results of the test show that ore body remained as safety roof in thickness of 15 m guarantees the safe advance of stoping work face. Caving of safety roof puts in practice at the first two mining intervals when the third interval of continuous mining is finished, and one interval as the safety distance should be kept all the time between stopping and caving. While mining in the last interval, pre-slotting should be implemented first of all, and the roof of the last two mining intervals is caved simultaneously. Only this kind of time series system can be an efficient and safe way for induced caving of roof in continuous mining.
Key words: continuous mining; induced caving; similar material simulation; safety roof; slotting
1 Introduction
After more than 20 years exploitation of Tongkeng Tin Mine, both upper veinlet belt type ore body and ore body No.91 have been exhausted, and ore body No.92 is the mainly productive object at present. Owing to the out-of-order exploitation of ore body No.91, the nether ore body No.92 is destroyed tremendously. Till now, its immediate roof is cemented or uncemented backfill in finished stopes, even some zones are unfilled open goaf[1]. Therefore, large-scale hidden dangerous mined-out areas have formed on the upper of ore body No.92. Now this slowly inclined large and thick ore body is mined using induced caving of roof technology based on continuous mining[2-4]. And the technology is an unconventional, high-efficient and safe method, which has been widely used in mining of inclined, gently inclined large-scale barren ore body and processing to mined stope[5-8].
Physical similar material model test is one of the most important techniques for the research of physical mechanical characteristics of rock mass. Compared with numerical simulation, it is also widely used in many complex engineering problems for its prominent advantages[9-13]. According to similarity theory, site practical problems can be analyzed and solved by observational study on the behavior of distortion, displacement and destruction in similar model. By using similar material simulation test[14], the time series system of artificial induced caving of safety roof which lies below the complex backfill during continuous mining in ore body No.92 was studied in this work.
2 Experimental
2.1 Conditions of test stope
The stope No.T112 of ore body No.92 was constructed as the test stope, and rock strata from bottom to top were wide strip limerock, ore body (40 m), marlite (4 m), backfill (30 m), and lenticular limerock. The physical mechanical parameters of rock strata are listed in Table 1. The dimensions of test stope were l×w×h= 80 m×50 m×40 m, where l is the length of stope, w is the width of stope, and h is the height of stope. The obliquity of the ore body is 15?-25?, and mining or caving interval is 16 m in length. The test emphasized geometrical similarity and stress similitude. The stresses in rock strata of stope were σ1=50 MPa, σ2=18 MPa, and σ3=γ×H, where σ3 is the vertical stress, γ is the bulk weight of rock strata, and H is the buried depth of ore body.
Table 1 Physical mechanical parameters of rock strata
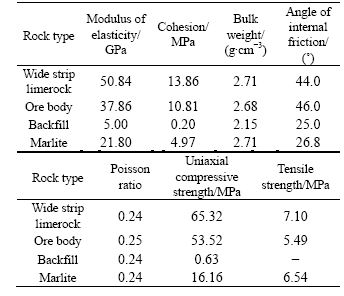
2.2 Design of similar material model
The upper terrane in overlapping region of ore bodies No.91 and No.92 is low intensity marlite with 4 m in average thickness. Because the overburden of marlite is backfill with extremely low intensity, one-slice full-dimension mining is impossible and ore body with determinate height remained as safety roof is needed. According to the results of theoretical and numerical analysis, safety roof with 15 m in height, 25 m in height of mining in ore body, and width in 16 m of mining interval were determined (Fig.1)[15].
In order to weaken the stability of whole roof, slotting in certain height in roof was adopted in artificial induced caving of roof. At the same time, the induced slotting brought about free space without interrelated restriction, leading to easy collapse of the roof.
Based on similarity criteria, the strength parameters conversion relation between prototype and model, and the mechanical parameters of model were calculated[16]. According to the geological condition, the aggregates of
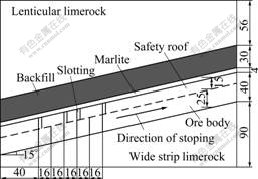
Fig.1 Sketch map of simulation test of induced caving of roof (unit: m)
the model were clean fine sand and sawdust, and the binder was gypsum. After ratio test on aggregate and binder, the feasible material ratios to the test can be ascertained, which are listed in Table 2.
Based on the actual site situation and test conditions, the results of similarity constants were calculated as follows: geometry similarity ratio 1?200, bulk weight similarity ratio 1?1.7, and stress similarity ratio 1?340. General dosage ratio of fine sand: gypsum: sawdust: water was 96?12?1?8. The dimensions of the test-bed were 1 600 mm×140 mm×1 200 mm. In order to make the process of test accord with the actual site situation and eliminate boundary effect and test error[17], a boundary of 40 m in length was set at the left of model. The average depth from simulation soleplate of ore body to the ground surface was 370 m, the obliquity of simulated ore body was 15?, and the test height of paving was 110 cm. The stress due to gravity was simulated by heavy metal bar with pressure.
2.3 Placement of measurement points
In the model, basic survey points were set in ore body and roof rock strata, so the stress and displacement of rock strata can be measured by high-sensitivity strain gauges. The test stope in model was divided into 5 ore- blocks, each of them was an interval with 8 cm in length. There were 4 survey points in ore body from the second mining interval ore-block to the fifth. In the middle of
Table 2 Mechanical parameters of rock strata of similar material model
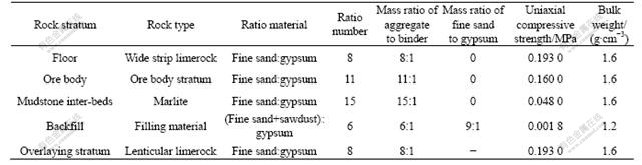
ore-block, the distance between each two points was 8 cm. In roof rock stratum, there were two rows survey points, each row had 5 survey points, which were located at the center of ore-block. Average distance between each two points was 8 cm. The distance between points in low level and boundary of roof, points in upper level and boundary of safety roof was 2 cm (Fig.2). The automatic collection, analysis and output of survey data were operated by 7V14 data system.
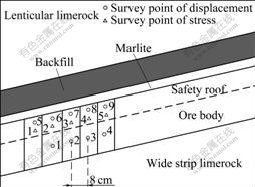
Fig.2 Sketch map of placement of survey points
3 Results and discussion
3.1 Process of simulation
Induced caving of roof was implemented after three intervals continuous mining in test, the distance of stoping was 48 m and caving of roof was 32 m. After mining of three intervals, cliff slotting was performed on safety roof from top to bottom in the starting mining region of ore body. The height of slotting should be perforated in the whole safety roof. Then the same operation was carried out at the end of the second mining interval. After perforation of induced slotting, both safety roof and marlite rock stratum over the first and second intervals ore-blocks broke down completely, while the safety roof over the third mining interval ore-block partly collapsed. Because of low intensity of backfill, nature caving of backfill due to gravity took place when the support of roof underlayer disappeared. The maximal height of collapse run through bottom to the top of backfill and a round arch structure formed finally (Figs.3(a) and (b)).
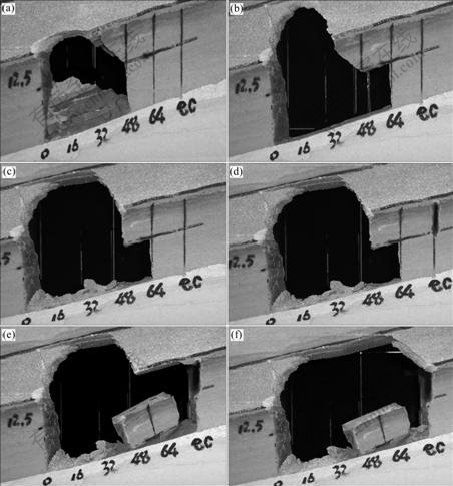
Fig.3 Images of simulation processes of time series in induced caving of roof: (a) Initial induced caving of roof in the first mining interval; (b) Final induced caving of roof in the first mining interval; (c) Induced caving of roof in the second mining interval; (d) Kerve in roof of induced caving in the last mining interval; (e) Initial induced caving of roof in the last mining interval; (f) Final induced caving of roof in the last mining interval
After the mining of the fourth interval was finished, slotting was cut in roof at the end of the third mining interval. Then the safety roof broke down wholly when the slotting interpenetrated in roof rock stratum, and that the marlite rock stratum collapsed subsequently together with backfill. The range of collapse was expanded from bottom to top of backfill (Fig.3(c)).
Before the last step of mining the slotting had been cut at the end of roof in ore body (Fig.3(d)). After interpenetration of slotting in entire safety roof, the last interval of ore-block was mined (Fig.3(e)). When the mining of all ore-blocks was finished, the roof and marlite rock stratum above the final two intervals of ore body collapsed in sequence (Fig.3(f)).
3.2 Analysis of stress
Fig.4 shows the stress distribution in ore body during test. Before induced caving of roof, the changes of stress in ore body can be depicted as curves of survey points 1 and 2. It can be seen that snap stress appears in the third and fourth steps. In addition, the change of stress in ore body tends to be gentle along with the advance of work face after induced caving, and there is no mutation phenomenon of stress peak value. This indicates that after induced caving of roof, part of stress in ore body is released ahead of schedule and the releasing free space of internal stress is enlarged.
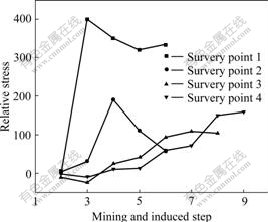
Fig.4 Stress curves of ore body
Fig.5 shows the stress distribution in roof during test. It is easy to see that after stoping the goaf with 48 m in length is formed. The stress will increase rapidly and reach the peak value instantly when the roof falls in the induced caving zone; when induced caving of roof in multi- intervals take place synchronously, the stress is high in the middle of collapse zone (survey point 6). However, the stress of the two sides is low (survey points 5 and 7), and the stress ratio of point 5 to point 7 is 2. The maximum stress in roof is quite equivalent to single interval and multi-intervals caving of roof, shown as survey points 8 and 9 in Fig.5. Because of the influence of slotting, part of stress in rock mass of roof is released by free space of slotting. Hence, the stress in rock mass of roof is reduced before reaching the maximum stress. But the stress away from the position of slotting is influenced hardly.
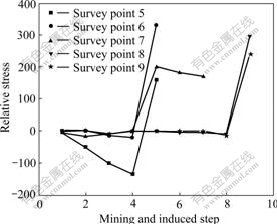
Fig.5 Stress curves of safety roof
The results show that with increasing accumulated energy in roof, stress concentration becomes more and more obvious. Roof rock strata in critical balance or slippage state will fail on the effect of outside perturbation. In order to prevent the failure of rock mass from bringing serious disaster to mining, an irreversible mechanical destabilization process in roof can be induced by activities of man-made intervention and control. It keeps the continuous mining going on and achieves the aim of mined-out areas process.
3.3 Analysis of displacement
From Fig.6, it can be seen that change tendency of displacement in safety roof is different. Before induced caving, the displacement change of roof accords with that of natural caving basically. Fig.6 shows that obvious
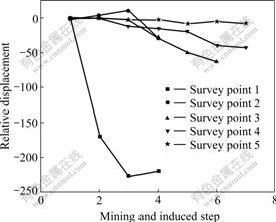
Fig.6 Uprightness displacement curves of roof
displacement occurs at the first step. Displacement in roof increases gradually in mining of other ore-blocks. After caving of roof in front zone is finished, two moving free faces in side and vertical direction are formed in next continuous stopping, which reduces the down-move displacement of above roof in mined stope. Because mined-out areas are formed after mining of ore-blocks, roof becomes cantilever beam which turns around the end of ore body and leads to a little up displacement in roof during the simulation test.
4 Conclusions
1) The simulation processes indicate that artificial induced caving is capable of controlling the roof dilapidation, and makes complete collapse of remained safety roof above rock strata and backfill. However, because of its high-strength and good integrity, overburden roof keeps integrated state and is hard to fall in one or two mining intervals. Furthermore, the test proves that ore body remained 15 m in thickness as the safety roof guarantees the safety advance of work face in mining.
2) Stoping, caving and slotting are basic processes of time series system of induced caving of roof in continuous mining. Slotting on both sides of induced area of ore-block produces free space on roof boundary and results in reduction in holistic strength.
3) Reasonable sequence of stoping and caving plays a very important role in the induced caving of roof. However, multi-project similar material simulation will be more effective than single test on study of time series of the technology.
References
[1] GAO Feng, ZHOU Ke-ping. Evaluation of the stability of stope roof based on extenics theory [J]. Mining Research and Development, 2005, 25(5): 76-79. (in Chinese)
[2] YU Jian, ZHANG Ai-lan. Study on new technique of rapidly following curtain filling [J]. Journal of Central South University of Technology, 2002, 9(2): 118-122.
[3] DENG Jian, GU De-sheng, LI Xi-bing, PENG Huai-sheng. Energy method and numerical simulation of critical backfill height in non-pillar continuous mining [J]. Transactions of Nonferrous Metals Society of China, 1999, 9(4): 847-851.
[4] WU Ai-xiang, HAN Bin, GU De-sheng, HU Hua. Progress in research on continuous mining technology of domestic and foreign underground metal mines [J]. Mining and Metallurgical Engineering, 2002, 22(3): 7-10. (in Chinese)
[5] BROWN E T. Block caving geomechanics [M]. Brisbane: Julius Kruttschnitt Mineral Research Centre, 2003: 3-12.
[6] GU De-sheng, LI Xi-bing. Modern mining science and technology for metal mineral resources [M]. Beijing: Metallurgical Industry Press, 2006: 68-70. (in Chinese)
[7] HU Jian-hua, ZHOU Ke-ping, LI Xi-bing, YANG Nian-ge, SU Jia-hong. Numerical analysis of application for induced caving roof [J]. Journal of Central South University of Technology, 2005, 12(S1): 146-149.
[8] HU Jian-hua, ZHOU Ke-ping, GU De-sheng, SU Jia-hong. Analysis of time-variation mechanical characteristics of induced roof caving based on continuous mining [J]. Mining Technology, 2006, 6(3): 157-160. (in Chinese)
[9] ALFARO M C, WONG R C K. Laboratory studies on fracturing of low-permeability soils [J]. Canadian Geotechnical Journal, 2001, 38(2): 303-315.
[10] LIU Chang-wu, GUO Yong-feng, YAO Jin-ming. The development and problems of mining similar simulation experiment technique— Meaning of developing three dimensional mining physical simulation experiment [J]. China Mining Magazine, 2003, 12(8): 6-8. (in Chinese)
[11] LI Zhong-kui, LIU Hui, DAI Rong. Application of numerical analysis principles and key technology for high fidelity simulation to 3-D physical model tests for underground caverns [J]. Tunneling and Underground Space Technology, 2005, 20(4): 390-399.
[12] LI Jun-ping, ZHOU Chuang-bing, LI Xiang-yang. Similarity simulation of disposal scheme for abandoned stope under the sunken topography [J]. Chinese Journal of Rock Mechanics and Engineering, 2005, 24(4): 581-586. (in Chinese)
[13] HAZZARD J F, YOUNG R P. Dynamic modeling of induced seismictiy [J]. International Journal of Rock Mechanics and Mining Sciences, 2004, 41(8): 1365-1376.
[14] WANG Jin-xue, WANG Jia-chen, DONG Wei-jun, CHEN Zhong-hui. Similar simulated experiment for continuous mining and roof dilapidation or ore body underground [J]. Journal of Liaoning Technical University, 2006, 25(4): 172-175. (in Chinese)
[15] ZHOU Ke-ping, SU Jia-hong, GU De-sheng, SHI Xiu-zhi, XIANG Ren-jun. The nonlinear forecasting method of the least security coping thickness when mining under complex backfill [J]. Journal of Central South University: Science and Technology, 2005, 36(6): 1094-1099. (in Chinese)
[16] DONG Wei-jun, SUN Zhong-ming, WANG Jia-chen, CHEN Zhong-hui. Study of similar material simulated experiment on natural caving of ore body [J]. Mining Technology, 2001, 1(3): 13-15. (in Chinese)
[17] CUI Xi-min, MIAO Xie-xing, SU De-guo, MA Wei-min. Error analysis in similar material simulation test of the movement of rock strata and surface [J]. Chinese Journal of Rock Mechanics and Engineering, 2002, 21(12): 1827-1830. (in Chinese)
(Edited by CHEN Wei-ping)
Foundation item: Project(50490274) supported by the National Natural Science Foundation of China; Project(20050533035) supported by the Specialized Research Fund for the Doctoral Program of Higher Education of China; Project(1343-77236) supported by the Doctor Degree Paper Innovation Engineering of Central South University, China
Received date: 2007-08-28; Accepted date: 2007-10-11
Corresponding author: GAO Feng, PhD; Tel: +86-731-8879965; E-mail: gf81412@126.com