
Study of decomposing carbonyl slag
CHEN Ai-liang(陈爱良)1, SUN Pei-mei(孙培梅)2, ZHAO Zhong-wei(赵中伟)1,
LI Hong-gui(李洪桂)1, CHEN Xing-yu(陈星宇)1
1. School of Metallurgical Science and Engineering, Central South University, Changsha 410083, China;
2. School of Chemical Engineering and Technology, China University of Mining and Technology,
Beijing 100083, China
Received 23 May 2005; accepted 13 December 2005
Abstract: A new technology was put forward to deal with the carbonyl slag at low acidity and low oxygen pressure in the kettle. With the orthogonal experiments for analyzing the sequence of four factors and some single factor experiments for the best conditions. The best conditions are used for extracting nickel, cobalt and copper and enriching precious metals: the cupric ion concentration is 5 g/L; and pH=6; the sulfur coefficient is 1.4; the oxygen pressure is 0.08 MPa; the time bubbling oxygen is 20 min; the ratio of liquid to solid is 8:1; the leaching time is 2 h; the heating time is 2.5 h. The leaching rates of nickel and cobalt are more than 98% and that of copper is above 97%. Nickel and cobalt can be separated efficiently from copper and precious metals from the carbonyl slag. Moreover, its leaching liquor has less copper. Nickel and cobalt can be reclaimed only once. During the whole process, the leaching rates of Au and Ag are more than 99.9%, while other precious metals are still in the residue without any loss.
Key words: carbonyl slag; nickel; cobalt; copper; low oxygen pressure leaching; reclaiming efficiency; leaching rates
1 Introduction
Carbonyl slag is a kind of solid from the material with nickel by carbonylation. It usually contains Cu, Ni, Co, Fe, S, As, Sb, Au, Ag and platinum metals, and holds great recovery value. At present, with the development of the technology of super fines and nanometer nickel powder by carbonylation, it is applicable and economical to properly deal with the carbonyl slag.
Because of its particularity and difficulty when nickel is abstracted by carbonylation, few factories have used this technology in the world. At present, there are few reports on carbonyl slag at home. At abroad, there are some factories mainly in Canada and Russia[1]. Their technologies are different. NORILSK NICKEL of Russia mainly uses the technology of smelting— electrolysis[2-4]. During the process of smelting, nickel, cobalt and copper form an alloy to be electrolyzed. Copper can be separated from nickel, cobalt and iron. And the precious metals can be abstracted from anode mud[5-8]. Although the technology can separate sulfur and eliminate the bad effect on the subsequent steps by separating sulfur, the sulfur dioxide is exhausted into air to pollute environment. The reclaiming efficiency of nickel and cobalt is only 96%[9-13]. INCO company of Canada uses an aqueous method. It mainly uses pressure leaching. The technology is[13-15]: abstracting nickel, cobalt, copper, and then separating, electrolyzing and recovering copper. The precious metals are reclaimed from the second pressure leaching. It ensures the recovery of nickel, cobalt and copper and enriches the precious metals. But the recovery of main base metals is only 95%-97% and the long sheet is unavailable to separate nickel, cobalt and copper from the precious metals.
A new method of low oxygen pressure leaching was studied in this work. Nickel and cobalt are leached while other metals including copper are still in the residue. It is easy to separate nickel and cobalt from copper. Copper and the precious metals are reclaimed from the leaching residue by roasting and leaching. Then copper can be reclaimed and the precious metals are still in the residue for enrichment. The technology can ensure that the leaching rates of nickel and cobalt reach more than 98% and the precious metals can be enriched. The precious metals have no any loss in the whole process. While low oxygen pressure leaching is given emphasis to study for its vital role in the whole process.
2 Experimental
2.1 Raw materials
Chemical components of carbonyl slag are shown in Table 1.
Table 1 Chemical component of raw material(sample B)
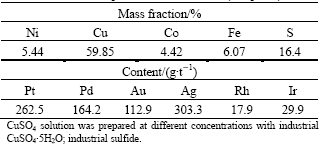
2.2 Methods of experiment
Carbonyl slag was put into a ball mill(QP—1SP type, Nanking University instrument factory) with water, grinded and then sieved. The material under 200 mesh, named B, was gotten and its chemical components are listed in Table 1. The material above 200 mesh, C, acted as revert for fire system. B was leached in high pressure kettle(FYX type, the fourth instrument plant in Dalian) with stirring for separating nickel, cobalt and copper. Then nickel and cobalt entered into the solution while copper still remained in the residue. The residue, called the first leaching residue, was sent to be roasted and then leached for extracting copper. The second leaching liquid can be used to produce electrolytic copper and bluestone. The second leaching residue was for the enrichment of the precious metals. The flow sheet of the treatment of carbonyl residue in the experiment is shown in Fig.1.
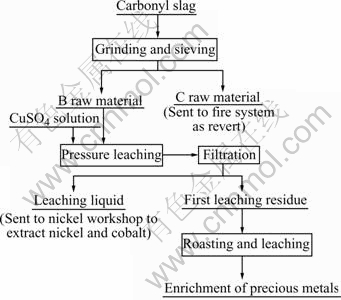
Fig.1 Flow sheet of treatment of carbonyl slag
In Fig.1, the leaching liquid from pressure leaching was sent to the nickel workshop to extract nickel and cobalt, which mainly contains Ni 5.74 g/L, copper 0.004 g/L, Co 4.83 g/L. The first leached residue contains Ni 0.084%, Cu 61.58%, Co 0.072%, Au 0.13%, Pt 0.26%,Pd 0.17%,Ag 0.3%,Rh 0.018%,Ir 0.021%. After the first leaching residue is roasted and leached, the enrichment of the precious metals was gotten and it contains Au 1.25%,Pt 2.91%,Pd 1.82%,Ag 1.98%,Rh 0.22%,Ir 0.33%.
In this paper, the process of low oxygen pressure leaching was especially discussed for the optimum technology.
2.3 Equilibrium calculation of main base metals and precious metals
During the process, there are two main working procedures: low oxygen pressure leaching, roasting and leaching. The main base metals discussed in the work are Ni, Co, Cu and the precious metals are Pt, Pd, Au, Ag, Rh, Ir. 100g raw materials were used and their equilibrium calculation of metals is shown in Table 2.
From Table 2, the loss quantity of Ni,Co and Cu is 0.005-0.01 g and their leaching rates are higher than 99.8%. The loss quantities of Au and Ag are 1-2 μg and their leaching rates are higher than 99.9%. But other precious metals are still in the residue without any loss.
3 Results and discussion
3.1 Sequence of factors
Due to the high effect of oxygen leaching time, oxygen pressure and pH on the leaching rates of nickel, cobalt and copper, it is necessary to study the sequence of these factors. Moreover, the ratio of liquid to solid may affect the concentration of nickel and cobalt in the leaching solution. At the same time, the copper concentration in the solution is directly concerned to the separation of nickel and cobalt from copper. Therefore, the leaching rate of copper is regarded as an aim value and the orthogonal experiments are studied which is based on the four factors. The orthogonal design table and its experiment results are shown in Tables 3 and 4, respectively.
From Tables 3 and 4, we can see R(the value of the max. minus the min.) of pH is the largest. R of the time of bubbling oxygen and the ratio of liquid to solid are the lowest while the former is less than the latter. pH and oxygen pressure have greater effects on copper content in solution than the other two. The time of bubbling oxygen has the least effects. The lower copper concentration in the solution is, the better the experiments’ results are. The best leaching condition is carried through under the conditions: the oxygen pressure is 0.08 MPa, pH=6, the oxygen leaching time is 20 min and the ratio of liquid to solid is 8:1 at 398 K.
Table 2 Metals equilibrium
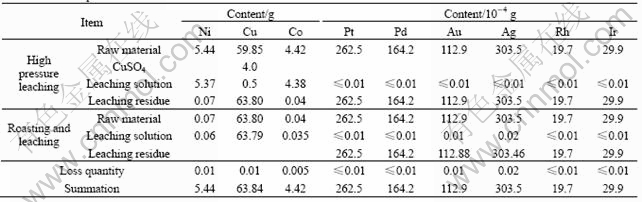
Table 3 Orthogonal design table
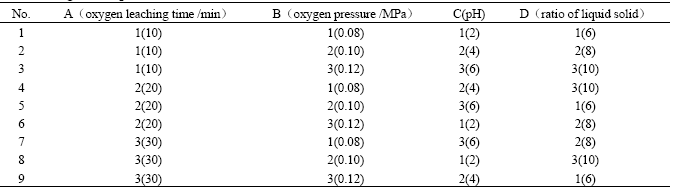
Table 4 Residual analysis of orthogonal experiment

3.2 Optimization of experiments
In the experiment, there are many influence factors, such as oxygen pressure p(O2), coefficient of sulfur (the ratio of practical sulfur dosage to its theory dosage)ФS. All the experiments are studied on 50 g raw materials at pH 6 and at the stirring rate of 300 r/min when the ratio of liquid to solid is 8:1 at 125 ℃.
1) Effect of oxygen pressure p(O2) on leaching rate
Oxygen pressure p(O2) is changed, while other conditions are unchanged as follows: with cupric ion concentration 5 g/L; sulfur coefficient 1.4; leaching temperature 125 ℃; the leaching and heating time 2 h. The results are shown in Fig.2.
From Fig.2, the leaching rate of nickel and cobalt has greatly risen at the oxygen pressure from 0.06 MPa to 0.08 MPa. When the pressure is above 0.08 MPa, the leaching rates of nickel and cobalt reach the highest. This shows that nickel, cobalt and its sulfides are reacted in oxygen pressure as follows[17]:
NiS+2O2=NiSO4 (1)
CoS+2O2=CoSO4 (2)
S+H2O+(3/2)O2=H2SO4 (3)
Ni+H2SO4+(1/2)O2=NiSO4+H2O (4)
Co+H2SO4+(1/2)O2=CoSO4+H2O (5)
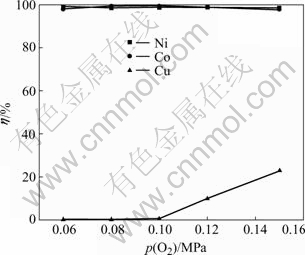
Fig.2 Influences of oxygen pressure on leaching rates of Ni, Co and Cu
While in Fig.2 the leaching rate of copper is very low at the oxygen pressure from 0.06 MPa to 0.10 MPa, at that time copper is not leached at all. However, when oxygen pressure is above 0.10 MPa, its leaching rate is obviously increased, then CuS, Cu, Cu2S are turned into CuSO4 as follows:
CuS+2O2=CuSO4 (6)
Cu+H2SO4+(1/2)O2=CuSO4+H2O (7)
Cu2S+H2SO4+(1/2)O2=CuSO4+H2O+CuS (8)
For the sake of the cost, the lower the oxygen pressure under the condition of higher leaching rate of nickel and cobalt, the lower its leaching rate of copper is. So, the oxygen pressure 0.08 MPa is regarded as the optimum.
2) Effect of sulfur coefficient ФS
Sulfur coefficient ФS is changed, while other conditions are unchanged as follows: with cupric ion concentration 5 g/L; oxygen pressure 0.08 MPa; leaching temperature 125 ℃ and the leaching and heating time 2 h. The results are shown in Fig 3.
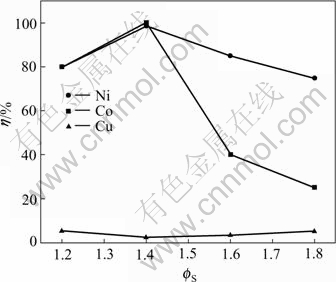
Fig.3 Influences of sulfur coefficient on leaching rates of Ni, Co and Cu
From Fig.3, the leaching rates of nickel and cobalt are greatly increasing. When it is 1.4, the leaching rate reaches the optimum. At that time, reactions (4) and (5) take place. When sulfur coefficients go on increasing, Cu and its sulfide are leached by H2SO4 of formula (3) at certain oxygen pressure. While the leaching rates of nickel and cobalt are decreasing, it may be for the reason that the ions of nickel and cobalt in the solution were exchanged into its sulfide deposition combining with sulfur after oxygen is used up.
3) Effect of [Cu2+]
Cupric ion concentration, CCu, is changed, while other conditions are unchanged as follows: sulfur coefficient 1.4; oxygen pressure 0.08 MPa; leaching temperature 125 ℃; the leaching and heating time 2 h. The results are shown in Fig.4.
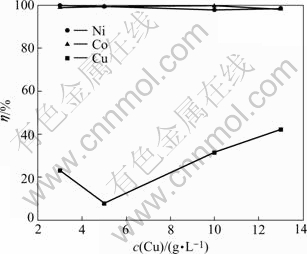
Fig.4 Influences of Cu2+ concentration on leaching rates of Ni, Co and Cu
From Fig 4, after cupric ion is added, the leaching efficiencies of nickel and cobalt are increasing. Because the solubility constant of CuS (Ksp in Table 5) is far smaller than those of NiS and CoS. CuSO4 takes re-exchanges with NiS and CoS and then produces more stable deposition of CuS.
CuSO4+NiS=NiSO4+CuS (9)
CuSO4+CoS=CoSO4+CuS (10)
Table 5 Solubility product constant (Ksp ) of CuS, CoS and NiS
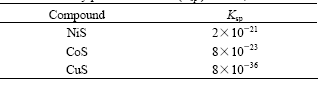
At cupric ion concentration of 5 g/L, the leaching rate of copper reaches at the lowest because copper has completely re-exchange reactions of (9) and (10). With the enhancement of cupric ion concentration, the leaching rates of nickel and cobalt are almost unchanged, but that of copper increases, which is not favorable to the separation of nickel and cobalt from copper.
4) Temperature effect
Leaching temperature(t) is changed, while other conditions are unchanged as follows: with cupric ion concentration 5 g/L, sulfur coefficient 1.4, oxygen pressure 0.08 MPa, the leaching and heating time 2 h. The results are shown in Fig.5.
From Fig.5, when the leaching temperature was added up to 125 ℃ from 110 ℃, an increase gave a corresponding increase at the leaching rate of nickel and cobalt, which reach 99.3% from 97.2% and 98.4% from 96.0%, respectively. In the temperature range of 125-160 ℃, the rates remain above 98.4%, It is shown that cupric ion concentration has little effect on the leaching rate of Ni and Co at the temperature more than 125 ℃. While the leaching rate of copper increases by 9.23% from zero with temperature increasing, which is not expected. So, at the temperature lower than 125 ℃, it not only ensures oxygenation of nickel and cobalt, but also makes less copper remaining in the solution.
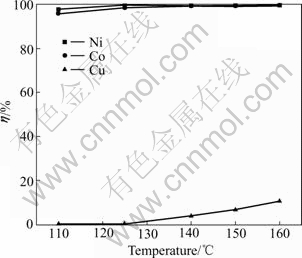
Fig.5 Influences of leaching temperature on leaching rate of Ni, Co and Cu
5) Leaching time effect
Leaching time(tl) is changed, while other conditions are unchanged as follows: with cupric ion concentration 5 g/L, sulfur coefficient 1.4, oxygen pressure 0.08 MPa, the heating time 2h. The results are shown in Fig.6.
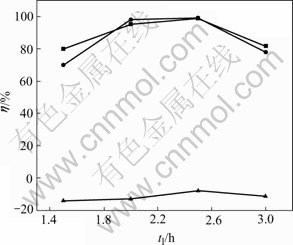
Fig.6 Influences of leaching time on leaching rate of Ni, Co and Cu
From Fig.6, at the beginning of leaching, the leaching rate of nickel is higher than that of cobalt, which shows that nickel is leached more quickly. Going on leaching, the leaching rates of them reach the highest and then begin to decrease. While that of copper firstly remains unchanged and then decrease after it increases. It is shown that copper is leached after nickel and cobalt. When time ≥2 h, copper and its sulfide are about to be leached. When time ≥2.5 h, reactions (9) and (10) take place at the same time . NiS and CoS will react with Cu2+ in the solution to form CuS. So, the cupric ion concentration decreases in the solution. It’s shown that the leaching rates of nickel and cobalt reach the highest while that of copper is the lowest when the leaching time is 2 h.
6) Effect of heating time
Heating time(th) is changed while other conditions are unchanged as follows: with cupric ion concentration 5 g/L, sulfur coefficient 1.4, oxygen pressure 0.08 MPa, the leaching time 2 h at 125 ℃. The results are shown in Fig.7.
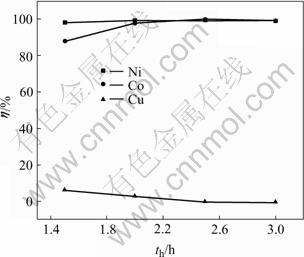
Fig.7 Influences of heating time on leaching rate of Ni, Co and Cu
From Fig.7, when the heating time prolongs, the leaching rates of nickel and cobalt increase until 2.0 h. When the time increases from 1.0 h to 2.0 h, the rates of nickel increase from 98.0% to 98.5%, while that of cobalt increases from 88.0% to 98.3%. After 2 h, the leaching rates of nickel and cobalt reach the highest. Then reactions (9) and (10) take place. NiS and CoS will react with Cu2+ in the solution and change into CuS. When the time is above 2.5 h, the leaching rates of nickel and cobalt have no change. Cupric in the solution fully deposits and the leaching rate of copper reaches the lowest as expected.
4 Conclusions
1) The technology doesn’t need high acidity and high pressure, so, it avoids corrupting the pressure kettle by high acidity and prolongs its life, which greatly reduces the cost.
2) The orthogonal experiments show the sequence of the four factors: pH>oxygen pressure>oxygen time>ratio of liquid to solid. The best leaching condition is A2 B1 C3 D2. That is 0.08 MPa, pH=6, 20 min of oxygen time and 8:1 of ratio of liquid to solid.
3) The best conditions are used for extracting nickel, cobalt, copper and the enrichment of the precious metals: cupric ion concentration is 5 g/L, pH=6, sulphur coefficient is 1.4, oxygen pressure is 0.08 MPa, the time bubbling oxygen is 20 min, the ratio of liquid to solid is 8:1, the leaching time is 2 h, and the heating time is 2.5 h.
4) The leaching rates of nickel and cobalt are higher than 98% and that of copper is above 97%. Nickel and cobalt can be separated efficiently from copper and the precious metals can be enriched in the carbonyl slag.
5) The leaching rates of Au and Ag are higher than 99.9%, while other precious metals are still in the residue without any loss.
6) It can effectively reduce the copper concentration of its leaching solution. Nickel and cobalt are reclaimed only once.
References
[1] Tyroler p m. Nickel carbonyl corpus(No.1 underside)[C]. 1996. 77-85.(in Chinese).
[2] Zhou K L, Cao W M, Zhang Y, LIU M W. Structure and tribological properties of plasma-polymerized nickel carbonyl films[J]. Thin Solid Films, 1997, 303(1): 89-93.
[3] Della P R, Eliano D, Liugi G. Iron-nickel mixed metal clusters: synthesis, reactivity and vibrational spectroscopy of [FeNi5(CO)13]2-. Solid state structure of the anions [FeNi5(CO)13]2- and [Fe3Ni(CO)12]2-[J]. Inorganica Chimica Acta, 2003, 4(350): 107- 113.
[4] Moskalyk R R, Alfantazi A M. Nickel laterite processing and electrowinning practice[J]. Minerals engineering, 2002, 15(8): 593- 605.
[5] LI Fei, WANG chun-ming, HU Ke-ao. Optimization of non-aqueous nickel slips for manufacture of MCFC electrodes by tape casting method[J]. Materials Research Bulletin, 2002, 37(12): 1907-1921.
[6] Beattie James K, Masters Anthony F, Meyer Josephine T. Nickel carbonyl cluster complexes[J]. Polyhedron, 1995, 14(7): 829-868.
[7] Kunkelv Horst, Vogler Arnd. Absorption and emission spectrum of bis-(triphenylphosphine)-dicarbonylnickel(0)[J]. Inorganic Chemistry Communications, 2000, 3(3): 143-144.
[8] WANG Yong-qin, FENG ZHi-jie. Study of the technology of carbonyl residues[J]. Nonferrous Smelt, 1999(28): 55-58. (in Chinese)
[9] LIU Si-lin, CHEN Qu-shan, TENG Rong-hou. Enrichment of precious metals in the process of nickel carbonylization[J]. Nonferrous Metal, 1998, 50(3): 80-84.(in Chinese)
[10] LIU Si-lin, CHEN Qu-shan, TENG Rong-hou. Refine nickel by carbonyl and concentration and abstraction of noble metals[J]. Noble Mentals, 1998, 1(2): 20-25.(in Chinese)
[11] Akio Yamamoto. A reminiscence and a future prospect of transition metal-catalyzed cross-coupling processes[J]. Journal of Organometallic Chemistry, 2002, 653: 5-10.
[12] Moskalyk r r, Alfantazi a m. Nickel laterite processing and electrowinning practice[J]. Minerals Engineering, 2002, 15: 593-60.
[13] Femoni C, Iapalucci M C, Longoni g. The new enneanuclear nickel carbonyl anion [Ni9(CO)16]2- and its relationships with the [Ni12(CO)21]4- and [Ni6Rh3(CO)17]3-clusters[J]. Inorganica Chimica Acta, 2002, 33: 111-117.
[14] Labertv C, marquez-Alvarez C, Drouet C, ALPHONSE P, MIRDDATOS C. CO oxidation over nonstoichiometric nickel manganite spinels[J]. Journal of Catalysis, 2001, 198(2): 266-276.
[15] Brown D A, Clarkson G J, Fitzpatrick N J, GLASS W K, HUSSEIN A J, KEMP T J, MüLLER-BUNZ H. Complexation and proton transfer by hydroxamic acids in model inhibited metallohydrolases: formation of metal hydroxamate trimers[J]. Inorganic Chemistry Communications, 2004, 7(4): 495-498.
[16] SUN Pei-mei, CHEN Ai-liang, JIA Xi-jun. Reclaiming valuable metals from carbonyl residues by leaching under low oxygen pressure[J]. Mining and Metallurgical, 2004, 24(6): 48-50, 55.
[17] REN Hong-jiu, WANG Li-chuan. Abstraction Manual of Nonferrous Metallurgy (Nickel and Copper)[M]. Beijing: Metallurgical Industry Press, 2000.(in Chinese)
Corresponding author: CHEN Ai-liang; Tel: +86-731-8830476; E-mail: chenailiang@etang.com
(Edited by LI Xiang-qun)