
Preparation of fine nickel powders via reduction of nickel hydrazine complex precursors
HUANG Guo-yong(黄国勇)1, XU Sheng-ming(徐盛明)1, XU Gang(徐 刚)1,
LI Lin-yan(李林艳)1,ZHANG Li-feng(张立峰)2
1. Institute of Nuclear and New Energy Technology, Tsinghua University, Beijing 100084, China;
2. Department of Materials Science and Engineering, Missouri University of Science and Technology,
223 McNutt Hall, Rolla, MO 65409, USA
Received 14 January 2008; accepted 15 December 2008
Abstract: Fine nickel(Ni) powders with controllable particle sizes were synthesized via the reduction of nickel hydrazine complex precursors of pure [Ni(N2H4)2]Cl2 and a mixture of [Ni(N2H4)2]Cl2 and [Ni(N2H4)3]Cl2 in aqueous solution. The mechanism of the formation of metallic Ni powders experiences the reduction of nickel hydroxide by hydrazine released from the ligand exchange reaction between nickel hydrazine complex and NaOH. In comparison with the method of preparing Ni powders from nickel salts, the method of making Ni powders via the reduction of nickel hydrazine complex precursors shows the advantages of using half dosage of hydrazine for complete reduction of nickel ions in solution, and the obtained Ni particles show less agglomeration and better dispersibility. Moreover, the average particle size of nickel powders can be controlled from 180 to 260 nm by adjusting the reaction molar ratio and concentration.
Key words: multilayer ceramic capacitors; chemical reduction; nickel hydrazine complex; nickel powders; precursor
1 Introduction
Conductive metal powders such as nickel, copper, silver, are useful for forming internal electrodes in multilayer ceramic capacitors(MLCCs), and in particular, the increasing of internal metal electrode has led to the replacement of Pd or Pd/Ag by Ni as an electrode material due to its lower cost and lower resistivity[1]. Additionally, the MLCC with Ni electrodes is one of the most widely used passive components for highly- integrated electronic and telecommunication devices. The key concept is the large capacitance in a small volume, which is realized by the alternate stacking of BaTiO3-based dielectrics and Ni-based electrode layers up to several hundred layers[2]. The continuing development of advanced electronic devices for high performance with miniaturized dimensions has led to the improvement of MLCCs with larger capacitance in smaller volume. For the downsizing of MLCCs and achieving an ultra high capacitance, the thickness of Ni-based electrode layer reduces to the sub-micron scale, and it is required that Ni powders have a particle size of less than 1 ?m[3]. Therefore, the synthesis of a well- defined Ni powders with small size and narrow size distribution becomes increasingly important.
There have been developed kinds of synthetic methods, such as vapor phase method[4-5], spray pyrolysis[6], micro-emulsion[7], polyol process[8-9], and electrochemical reduction for the preparation of Ni powders. Among these methods, the chemical reduction method in aqueous has been investigated intensively due to its better capabilities for controlling composition, size and shape of Ni powders and the simple procedure [10-14]. In this method, hydrazine has widely been used as reducing agent for the preparation of metal particles, because pH and temperature dependent reducing ability of hydrazine makes the reduction rate easily controllable. But it was found that during the reduction of Ni2+ by N2H4 as
2Ni2++N2H4+4OH-→2Ni+N2+4H2O (1)
two side reactions take place, and the decomposition of hydrazine is catalyzed by the formed nickel particles as
N2H4→N2+2H2 (2)
3N2H4→N2+4NH3 (3)
so the consumption of hydrazine can be greatly increased.
Recently, it was reported that nickel hydrazine complex is attractive starting material for the preparation of fine nickel powders by chemical reduction method [15]. In this work, we report the preparation of fine nickel powders from nickel salt and nickel hydrazine complex. The effect of nickel hydrazine complexes, reaction molar ratio and reaction concentration on the phase composition, and morphology of nickel powders are also investigated.
2 Experimental
2.1 Materials
The NiCl2?6H2O, 85% N2H4?H2O, and NaOH (all were analytical pure) were used as the source materials.
2.2 Preparation of nickel powders from nickel salt
An appropriate amount of nickel chloride was dissolved in deionized water to form 50 mL solution, and an appropriate amount of hydrazine, mixed with an appropriate amount of NaOH, was slowly added dropwise into the solution with continuous stirring at a desired temperature. Then, the reduction was allowed to proceed for about 30 min. At the end, the resulting black products were separated from the solution, washed with deionized water and alcohol several times, and then dried in an oven at 80 ℃ for 12 h.
2.3 Synthesis of nickel hydrazine complex
An appropriate amount of nickel chloride was dissolved in deionized water to form 50 mL solution, and an appropriate amount of hydrazine was slowly added dropwise into the solution with continuous stirring at 25℃. During the addition, blue, violet, or pink precipitates depending on the reaction molar ratio of [N2H4]/[Ni2+] were formed, and the reduction proceeded for about 30 min. Then, the products were filtered, washed with deionized water several times, and dried in an oven at 30 ℃ for 12 h.
2.4 Preparation of nickel powders from nickel hydrazine complex
To a nickel hydrazine complex solution prepared by above procedure, an appropriate amount of NaOH was slowly added dropwise into the solution with continuous stirring at a desired temperature, and the reduction proceeded for about 30 min. At the end, the resulting black products were separated from the solution, washed with deionized water and alcohol several times, and then dried in an oven at 80 ℃ for 12 h.
2.5 Characterization
The products were characterized by X-ray diffraction (Rigaku, D/Max-2000) using Cu Kα radiation with graphite monochromator, and a scanning electron microscope (JEOL, JSM 4500) was used to image the size and morphology of the powders.
3 Results and discussion
3.1 Effect of molar ratio of [N2H4]/[Ni2+] on products prepared from nickel salts
Fig.1 shows the X-ray diffraction patterns of samples prepared from nickel salts with different molar ratios of [N2H4]/[Ni2+] from 1.0 to 6.0. The diffraction peaks marked with (◆) can be indexed as hexagonal phase of Ni(OH)2, and those with (▲) as face centered cubic metallic Ni phase. The molar ratio of [N2H4]/[Ni2+] equal 0.5 is needed to reduce the dissolved nickel ions according to Eq.(1). However, for the molar ratio of [N2H4]/[Ni2+]≤3.0, the amount of N2H4 is not enough to reduce Ni2+ to Ni; and the molar ratio of [N2H4]/[Ni2+]≥ 4.0 can ensure the complete reduction. A lot of hydrazine is catalytically decomposed by the formed nickel particles according to Eq.(2) and Eq.(3). Fig.2 shows the morphology of the Ni particles prepared by this method. It is found that these particles agglomerate easily with the van der Waals force and magnetic attractions.
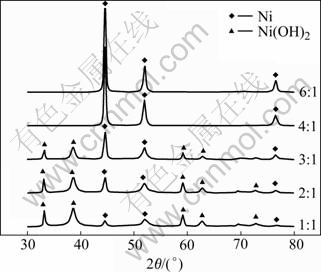
Fig.1 XRD patterns of samples prepared from nickel salts with different molar ratios of [N2H4]/[Ni2+]

Fig.2 SEM micrograph of nickel particles prepared from nickel salts under reaction condition of [Ni2+]=1.00 mol/L, [N2H4]/ [Ni2+]=4.0, [NaOH]/[Ni2+]=3.0, 60 ℃
3.2 Effect of molar ratio of [N2H4]/[Ni2+] on composi- tion of nickel hydrazine complex
It is known that the reaction between hydrazine and NiCl2 is[16-17]
NiCl2+nN2H4→[Ni(N2H4)n]Cl2, n=2, 3 (4)
The composition of nickel hydrazine complex is highly dependent on the reaction condition, such as the reaction temperature and the molar ratio of [N2H4]/[Ni2+]. The compositions of the products with molar ratio of [N2H4]/[Ni2+] of 1, 2, 3 and 4 in aqueous solution at 25 ℃ are determined by XRD (Fig.3). The XRD patterns show that when the reaction molar ratio of [N2H4]/[Ni2+] is 1 or 2, the nickel hydrazine complex of [Ni(N2H4)2]Cl2 is formed; when the reaction molar ratio of [N2H4]/[Ni2+] is 3 or 4, the mixture of [Ni(N2H4)3]Cl2 and [Ni(N2H4)2]Cl2, is generated. Additionally, it is found that the portion of [Ni(N2H4)2]Cl2 decreases while that of [Ni(N2H4)3]Cl2 increases as the molar ratio of [N2H4]/[Ni2+] is raised from 3 to 4. It is notable that the different products are formed under different reaction conditions. As the reduction reaction will proceed via these hydrazine complex precursors, the reduction potentials of them are possibly different.
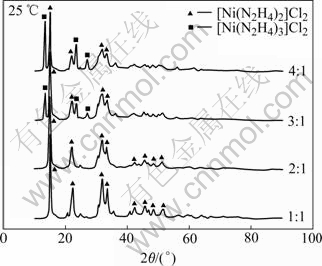
Fig.3 XRD patterns of nickel hydrazine complex prepared with different molar ratios of [N2H4]/[Ni2+]
3.3 Formation of Ni powders via nickel hydrazine complex
According to the experiments, when the NaOH is added into the nickel hydrazine complex solution, the color of the solution gradually changes to green due to the formation of nickel hydroxide by the ligand exchange of Cl- by OH- as follows:
[Ni(N2H4)n]Cl2+2NaOH→Ni(OH)2+nN2H4+2NaCl (5)
Then, the color changes to gray, and finally to black due to the subsequent reduction by hydrazine as following equation:
2Ni(OH)2+N2H4→2Ni+N2+4H2O (6)
Fig.4 shows the X-ray diffraction patterns of samples prepared from different compositions of nickel hydrazine complex with the molar ratios of [N2H4]/[Ni2+] from 1.0 to 4.0. The XRD results indicate that the products consist of Ni and Ni(OH)2 when the molar ratio of [N2H4]/[Ni2+] is 1.0, and the samples are pure Ni powders when the molar ratio of [N2H4]/[Ni2+] is more than 2.0. Compared with that for preparing nickel powders from nickel salts (Fig.1), the dosage of hydrazine, for completely reducing the nickel ion in the solution, decreases a half by this method.
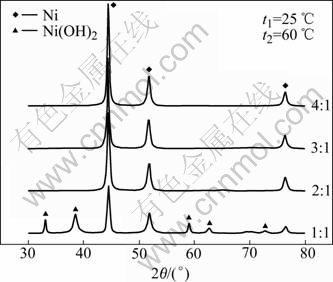
Fig.4 XRD patterns of nickel powders prepared from nickel hydrazine complex prepared with different molar ratios of [N2H4]/[Ni2+] (t1 is temperature of preparing precursor [Ni(N2H4)3]Cl2; t2 is temperature of preparing Ni powder with precursor)
Fig.5 shows that the morphology of Ni particles prepared from nickel hydrazine complex is less- agglomerated and better-spherical. In addition, the average particle size is about 235 nm with narrow size distribution (Fig.6). Comparing Fig.7 with Fig.2, it shows that the particles prepared from nickel hydrazine complex disperse better than those prepared from nickel salt.
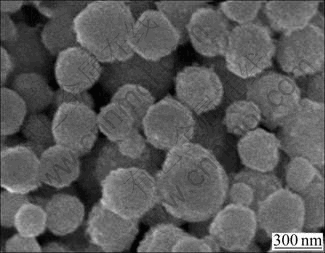
Fig.5 SEM micrograph of nickel particles prepared from nickel hydrazine complex under reaction condition of [Ni2+]=1.00 mol/L, [N2H4]/[Ni2+]=3.0, [NaOH]/[Ni2+]=3.0, t1=25 ℃, t2=60 ℃
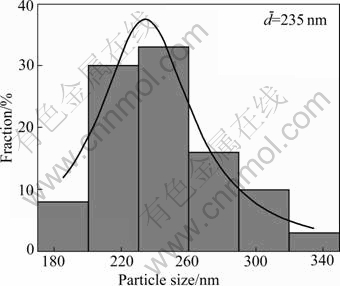
Fig.6 Particle size distribution of nickel particles in Fig.5
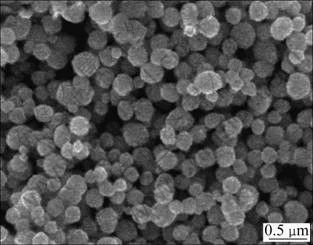
Fig.7 SEM micrograph of nickel particles prepared from nickel hydrazine complex under reaction condition of [Ni2+]=1.00 mol/L, [N2H4]/[Ni2+]=4.0, [NaOH]/[Ni2+]=3.0, t1=25 ℃, t2=60 ℃
These results can be explained by the Ni(OH)2 phase which is prepared not by simple precipitation but by the decomposition of nickel hydrazine complex, which results in the molecular-scale uniform distribution of the reducing agent (N2H4) throughout the Ni(OH)2 matrix. This would lead to uniform and homogenous nucleation of spherical Ni particles, and the precursory Ni(OH)2 network plays the role of a protective matrix against the coagulation of subsequently formed particles. So the well-defined and less-agglomerated Ni powders are prepared. In addition, the most nuclei are formed at the same time and grow at the same rate, so the size distribution of particles would be in the narrow range, and the amount of decomposed hydrazine, catalyzed by the formed nickel particles, would be reduced.
3.4 Effect of nickel hydrazine complex concentration on nickel powders
The effects of nickel hydrazine complex concentration on the formation of nickel powders were investigated. The reduction reactions were carried out with molar ratio of [Ni2+]:[N2H4]:[NaOH] at1:3:3. It is found that the average particles size increases from about 180 nm to 260 nm as the concentration of Ni2+ increases from 0.35 mol/L to 1.5 mol/L (Fig.8). The result could be explained by the reaction rate on the nucleation. With the increase of Ni2+ concentration, the nuclei concentration and nucleation rate increase. It would induce the growth of larger size particles.
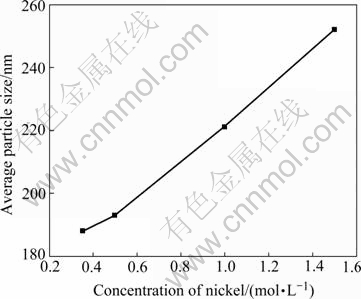
Fig.8 Average particle size of nickel powders from various nickel hydrazine complex concentration
4 Conclusions
Fine Ni powders with narrow size distribution were prepared via the reduction of nickel hydrazine complex precursors in aqueous solution. The composition of nickel hydrazine complex precursors was highly dependent on the synthetic conditions. The pure nickel hydrazine complex, [Ni(N2H4)2]Cl2 was prepared with the molar ratio of [N2H4]/[Ni2+] at 1.0 and 2.0, while a mixture of complexes, [Ni(N2H4)2]Cl2 and [Ni(N2H4)3]Cl2, was formed with [N2H4]/[Ni2+] at 3.0 and 4.0 at 25℃. The reduction of Ni2+ to metallic Ni powder proceeded via the formation of nickel hydroxide reduced by hydrazine released from the ligand exchange reaction between the nickel hydrazine complex and NaOH. Compared with that for preparing nickel powders from nickel salts, the dosage of hydrazine for completely reducing the nickel ion into Ni powder in solution is reduced a half with this method. So the well developed method may reduce the cost of producing Ni powders for various industrial applications. The Ni particles show less agglomeration and better dispersibility. Moreover, the average particle sizes of the nickel powders could be controlled from 180 to 260 nm by adjusting the reaction molar ratio and concentration.
References
[1] KISHI H, MIZUNO Y, CHAOZONO H. Base-metal electrode multilayer ceramic capacitors: Past, present, and future perspectives [J]. Appl Phys, 2003, 42: 1-15.
[2] SATO S, NAKANO Y, SATO A, NOMURA T. Mechanism of improvement of resistance degradation in Y-doped BaTiO3 based MLCCs with Ni electrodes under highly accelerated life testing [J]. Eur Ceram Soc, 1999, 19: 1061-1066.
[3] LEE J Y, LEE J H, HONG S H, LEE Y K, CHOI J Y. Coating BaTiO3 nanolayers on spherical Ni powders for multilayer ceramic capacitor [J]. Adv Mater, 2003, 15: 1655-1662.
[4] HWANG J H, DRAVID V P, TENG M H, HOST J J, ELLIOTT B R, JOHNSO D L, MASON T O. Magnetic properties of graphically encapsulated nickel nano crystals [J]. J Mater Res, 1997, 12(4): 1076-1082.
[5] STOPIC S, LLIC I, USKOKOVIC D P. Preparation of nickel submicron powder by ultrasonic spray pyrolysis [J]. Int J Powder Metall, 1996, 32(1): 59-65.
[6] XIA B, LENGGORO I W, OKUYAMA K. The role of ammonia and ammonium bicarbonate in the preparation of nickel particles from nickel chloride [J]. Mater Res, 2000, 15(10): 2157-2166.
[7] NI X M, SU X B, YANG Z P. The preparation of nickel nanorods in water-in-oil micro emulsion [J]. J Crystal Growth, 2003, 252(4): 612-617.
[8] YU K N, KIM D J, CHUNG H S. Dispersed rodlike nickel powder synthesized by modified polyol process [J]. Mater Lett, 2003, 57: 3993-3997.
[9] VIAU V, FIEVET F. Nucleation and growth of bimetallic CoNi and FeNi monodisperse particles prepared in polyols [J]. Solid State Ionics, 1996, 84: 259-270.
[10] WANG F, ZHANG Z C, CHANG Z Q. Effects of magnetic field on the morphology of nickel nanocrystals prepared by gamma irradiation in aqueous solutions [J]. Mater Lett, 2002, 55: 27-29.
[11] GLAVEE G N, KLABUNDE K J, SORENSEN C M. Borohydride reduction of nickel and copper ions in aqueous and nonaqueous media-controllable chemistry leading to nanoscale metal and metal boride particles [J]. Langmuir, 1994, 10: 4726-4730.
[12] LI D Y, LI C W, WANG H R, LI L Q, QIAN Y T. Preparation of nickel ultrafine powder and crystalline film by chemical control reduction [J]. Mater Chem Phys, 1999, 59: 88-90.
[13] GUI Z, FAN R, MO W, CHEN X, YANG L, HU Y. Synthesis and characterization of reduced transition metal oxides and nanophase metals with hydrazine in aqueous solution [J]. Mater Res Bull, 2003, 38: 169-176.
[14] GAO J, GUAN F, ZHAN Y, YANG W, MA Y. Preparation of ultrafine nickel powder and its catalytic dehydration activity [J]. Mater Sci Commun, 2001, 71: 215-219.
[15] JUNG W P, EUN H C, SANG H K, SANG H K. Preparation of fine Ni powders form nickel hydrazine complex [J]. Mater Chem Phys, 2006, 97: 371-378.
[16] CHOI J Y, LEE Y K, YOON S M, LEE H C. A chemical route to large-scale preparation of spherical and monodisperse Ni powders [J]. J Am Ceram Soc, 2005, 88(11): 3020-3023.
[17] KIM K M, LEE J H, YOON S M, LEE H C. Preparation of mono-disperse Ni powders via the reduction of hydrazine complexes: The effect of source materials and impurities [J]. J Electroceram, 2006, 17: 339-343.
Foundation item: Projects(50674060, 50734005, 20601016) supported by the National Natural Science Foundation of China; Projects(2007CB613506, 2007CB613505) supported by the National Basic Research Program of China
Corresponding author: XU Sheng-ming; Tel: +86-10-89796082; E-mail: smxu@tsinghua.edu.cn
DOI: 10.1016/S1003-6326(08)60283-6
(Edited by YUAN Sai-qian)