
Effect of CaC2 particulates concentration on microstructure and tensile properties of elemental magnesium
MA Yu-tao(马玉涛)1, ZHANG Xing-guo(张兴国)1, 2, HAO Hai(郝 海)1, 2
1. School of Materials Science and Engineering, Dalian University of Technology, Dalian 116023, China;
2. State Key Laboratory of Materials Modification by Laser, Ion and Electron Beams, Dalian 116023, China
Received 12 June 2008; accepted 5 September 2008
Abstract: CaC2 particulates reinforced magnesium materials were synthesized using a new technique— electromagnetic suspension casting(ESC). The microstructure and composition of magnesium alloys were investigated and the mechanical properties of alloys were tested. The tensile fracture surfaces were also studied by scanning electron microscopy. And the grain refinement effect of alloys was also examined. The results indicate that proper additions of CaC2 particulates are found to be efficient in refining the microstructure of magnesium materials. The tensile properties of alloys are consistent with the grain sizes. 0.26% (mass fraction) of CaC2 addition reduces the mean grain size of pure magnesium from more than 2 mm to 125 μm, and the ultimate tensile strength of pure magnesium at room temperature decreases from 77 to 148 MPa.
Key words: electromagnetic suspension casting; microstructure; grain refinement; tensile properties
1 Introduction
In the age of limited fossil energy recourses, the demand for lightweight construction material is growing in order to reduce energy consumption and lower environmental impact. In this regard, magnesium is highly available and possesses positive technological properties such as a low density together with high strength[1]. Achievement of a fine grain size is important for the further development of magnesium alloy[2]. It is an essential and fundamental approach since grain size significantly influences the mechanical properties of the casting, and the grain size is usually determined at an early stage of solidification by nucleation of the dendrites[3].
There are several grain-refining techniques for magnesium alloys, including superheating treatment[4], addition of ferric chloride[4-5], carbon inoculation[4, 6-8], melt stirring[9], grain refiner alloying elements addition and so on[3]. It has been long recognized that carbon inoculation is the major industrial grain refinement technique for magnesium alloys. It was investigated that aluminum carbide Al4C3 or Al2CO particles was formed in alloys and they both can be the nucleus for magnesium grains[3]. There have been some reports in the literature that the addition of certain calcium element can refine microstructure of alloys and improve the mechanical properties of magnesium alloys at room or high temperature[10-11]. Recent work has suggested that this effect in terms of the growth restriction factor[12] is relatively large for Ca compared with that of other solutes. Therefore, the compound CaC2 of Ca and C is an ideal reinforcement to improve the properties of magnesium.
Electromagnetic suspension casting (ESC) is a new technology, which combines the virtues of the electromagnetic stirring and the suspension casting. Nano or micro particulates as the suspension concentration were poured with the jets of argon gas orientated normally into the magnesium alloys melt which was held in the electromagnetic system, then solidified.
In the present study, by employing the new forming technique—electromagnetic suspension casting, we focused on the effect of CaC2 particulates concentration reinforcing on the microstructure and mechanical properties of elemental magnesium.
2 Experimental
The chemical compositions of studied alloys are listed in Table 1. A commercial pure elemental Mg (99.7%) was melted in an electrical furnace using a mild steel crucible under an argon atmosphere. The melt was homogenized with argon bubbling before pouring. When the temperature reached 710 ℃, the molten metal was poured into steel crucible which was held in the electromagnetic system at 710 ℃. CaC2 particulates were poured with the jet of argon gas orientated normal to the melt stream. The molten metal was stirred by electromagnetic stirred for about 2 min and then poured into steel molds with a size of d 50 mm×170 mm at approximately 200 ℃. A mixture of dry air/0.5%SF6 was used as protective gas when moulding.
Table 1 Chemical compositions of alloys (mass fraction, %)
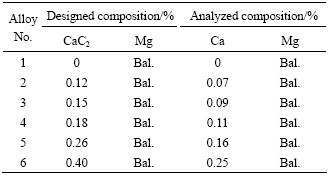
Chemical compositions of alloys were examined using XRF-1800 X-ray fluorescence spectrometer. Microstructure characterization of the grain size and qualitative analysis were conducted on selected specimens using a MEF4M optical microscope (OM) and a JSM-5600LV scanning electron microscope (SEM) with an energy dispersive spectroscope (EDS). The mean linear intercept method was used to measure the average grain size. The phase compositions of magnesium alloys were investigated using XRD-6000 X-ray diffractometer, and Ca element area distribution analysis was studied by EPMA-1600 electron probe micro analyzer. Tensile testing was carried out using WD-1OA universal testing machine at a crosshead speed of 1 mm/min. The fractography was observed on the tensile fractured samples using JSM-5600 LV scanning electron microscope (SEM).
3 Results and discussion
3.1 Microstructure
Fig.1 shows the influence of CaC2 concentration on grain refinement of element magnesium. The average grain size decreases with increasing quantity of CaC2 added. The grain size of the alloy decreases from 2 mm to 125 μm when the quantity of CaC2 added increases to 0.26% and the Ca content of No.5 alloy is 0.16%.
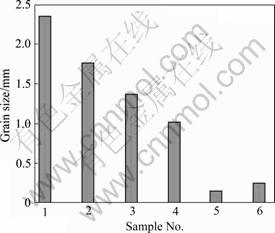
Fig.1 Grain size versus CaC2 addition sample No.
The optical microstructures of alloys with different CaC2 content are presented in Figs.2(a)-(f). The microstructure shown in Fig.2(a) is that of No.1 without CaC2 and Figs.2(b)-(e) show those of specimens No.2 to No.6 respectively. In Fig.2(a), only some grain boundaries are clearly observed and the crystal grains are seen to be very large. In contrast, lots of crystal grains are clearly observed in the specimens with CaC2 addition, as shown in Figs.2(b)-(f).
Microstructural characterization of alloys with CaC2 addition reveals that: 1) CaC2 particulates have capability as reinforcement to nucleate magnesium grains during crystallization in ESC; 2) CaC2 particulars have capability of restricting growth of crystallized magnesium grains[13-14]. The results also reveal that grain refinement of magnesium matrix is enhanced till the addition of 0.26% of CaC2 particulates (0.16% of Ca contents). However, beyond that relatively higher tendency of clustering of particulates might have no further incremental effect.
The SEM micrograph of No.5 alloy is shown in Fig.3. It also can be seen that the alloys consist of α-Mg solid solution and a little particles. EDS analysis reveals that the compositions of the particle are 97.44% Mg and 2.56% Ca. The Ca element distributes along the grain boundaries.
The X-ray diffraction patterns of No.4, No.5 and No.6 alloys are illustrated in Fig.4. The main phases in the alloys are α-Mg. No other peaks are found. The most likely reason is that content of Ca is very little and Ca solid solution in Mg is negligible.
EPMA area analysis was performed to trace the Ca element distribution in ESC casting pure magnesium alloy after the addition of 0.26% CaC2 (No.5 alloy). The results are shown in Fig.5. The Ca concentration is found on grain boundary. The results indicate that Ca possesses strong segregation ability in melt and an intensive constitutional undercooling is formed in a diffusion layer ahead of the advancing solid/liquid interface, which restricts grain growth and promotes nucleation in the melt.
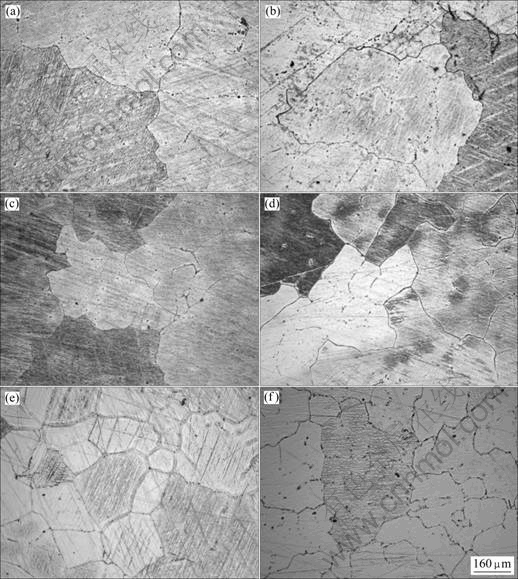
Fig.2 Microstructures of pure magnesium specimen with different CaC2 addition: (a) No.1; (b) No.2; (c) No.3; (d) No. 4; (e) No.5; (f) No.6
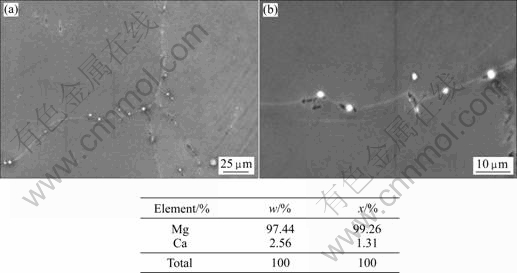
Fig.3 SEM micrographs of No.5 alloy (0.26% CaC2 addition) and corresponding EDS analysis results
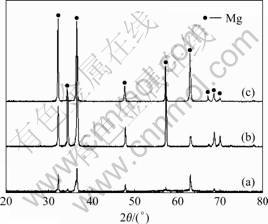
Fig.4 XRD patterns of samples: (a) No.4; (b) No.5; (c) No.6
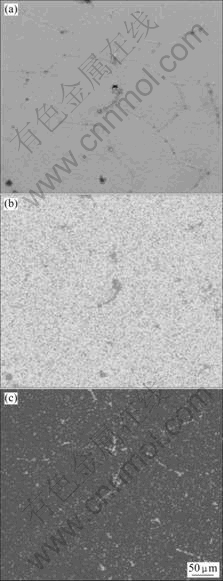
Fig.5 EPMA surface composition analysis of No.5 alloy (0.26% CaC2 addition): (a) Morphology; (b) Mg; (c) Ca
3.2 Tensile properties
The tensile properties of the alloys with and without CaC2 addition are listed in Table 2. It can be inferred that the CaC2 suspension particulates has a significant influence on the strength properties of pure Mg. The tensile strength decreases with increasing CaC2 addition, and it consists of the change of grain size of alloys. When grain size is 125 μm, the tensile strength σb is 148 MPa and the elongation is 8.8%.
Table 2 Tensile properties of alloys
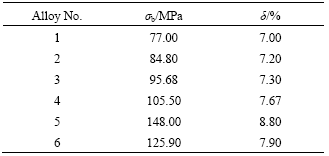
Fractographs of tensile fractured surface of No.1, No.3, and No.5 alloys are shown in Fig.6, revealing features of brittle fracture with cleavage and quasi- cleavage as the principal fracture modes.
3.3 Discussion
It is well known that according to the classic solidification theory, the grain size depends on three factors: the effective number of potential crystal nucleus in the melt, nucleation ratio and growth rate. Recent work[15-17] on the grain refinement of aluminum alloys has shown that grain refinement correlates with two factors. One is the solute elements present in the melt and the other is the number and potency of the nucleus particles.
The grain refinement of calcium addition by ESC may be introduced by the following factors. Firstly, CaC2 addition promotes the number of the nucleus particles in the melt alloy, increases the impediment effect of constitutional undercooling in a diffusion layer ahead of the advancing solid/liquid interface and lowers the extent of the eutectic reaction, which all are importance reasons to refine the alloys[18]. Secondly, CaC2 particulate concentration has capability of restricting growth of crystallized magnesium grains[13]. Thirdly, electromagnetic suspension casting is provided with the virtues of the electromagnetic stirring and the suspension casting. It can homogenize CaC2 particulates into the melt, disperse the particulates, distribute particles well, and refine the microstructures to improve the quality of alloy.
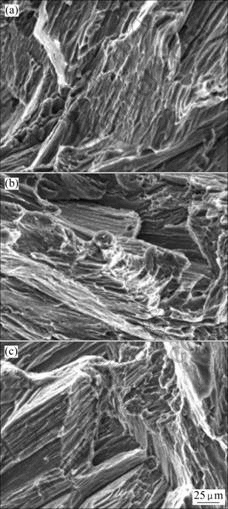
Fig.6 SEM images for surface of specimen failed in tensile test: (a) No.1 alloy; (b) No.3 alloy; (c) No.5 alloy
The Hall-Petch formula[19]: σs=σ0+Kd-1/2, describes the relationship between tensile properties and grain size, where d is grain size; K is a constant and σ is the tensile strength. The addition of CaC2 particulates makes the grain sizes much smaller to 125 μm, which increases the tensile strength to 148 MPa.
4 Conclusions
1) CaC2 particulate concentration in magnesium leads to very noticeable effect on the grain size and tensile properties of pure magnesium using electromagnetic suspension casting.
2) Microstructural characterization shows that CaC2 particulates concentration has significant grain refinement effect in magnesium. 0.26% CaC2 addition while the Ca content is 0.16% reduces the mean grain size of pure magnesium to 125 μm.
3) The results of tensile characterization reveal that 0.26% CaC2 addition while the Ca content is 0.16% produces quite improvement in tensile properties. The ultimate tensile strength and relative elongation of magnesium alloys increase to 148 MPa and 8.8%, respectively.
References
[1] KAINER K U. Magnesium alloys and technologies [M]. Weinheim: WILEY-VCH, Verlag GmbH & Co, 2003.
[2] CAO P, QIAN M A, STJOHN D H. Native grain refinement of magnesium alloys [J]. Scripta Materialia, 2005, 53(7): 841-844.
[3] DAHLE A K, LEE Y C, NAVE M D, STJOHN D H. Development of the as-cast microstructure in magnesium-aluminium alloys [J]. Journal of Light Metals, 2001, 1: 61-72.
[4] NELSON C E. Grain size behavior in magnesium casting alloys [J]. AFS Trans, 1948, 56: 1-23.
[5] CAO P, QIAN M A, STJOHN D H. Effect of iron on grain refinement of high-purity Mg-Al alloys [J]. Scripta Materialia, 2004, 51(2): 125-129.
[6] LU L, DAHLE A K, STJOHN D H. Grain refinement efficiency and mechanism of aluminium carbide in Mg-Al alloys [J]. Scripta Materialia, 2005, 53(5): 517-522.
[7] LUO A. Development of matrix grain structure during the solidification of a Mg(AZ91)/SiCp composite [J]. Scripta Metall Mater, 1994, 31(9): 1253-1258.
[8] BROWN R E, KARLSEN D O, OYMO D, WESTENGEN H, PINFOLD P M D, STROMHAUG S I. Development of grain refiner for aluminium containing magnesium alloys [C]// Light Metals Processing and Applications. Canada: Canadian Institute of Mining, Metallurgy and Petroleum, 1993: 397-408.
[9] LI M, TAKUYA T, MIWA K. Controlling microstructures of AZ31 magnesium alloys by an electromagnetic vibration technique during solidification: From experimental observation to theoretical understanding [J]. Acta Materialia, 2007, 55(14): 4635-4643.
[10] LUO A, PEKGULERYUZ M O. Cast magnesium alloys for elevated temperature applications [J]. J Mater Sci, 1994, 29(20): 5259-5271.
[11] WANGQu-dong, CHENWen-zhou, ZENGXiao-qin, LUYi-zhen, DINGWen-jiang, ZHUYan-ping, XUXiao-ping, MABUCHI M. Effects of Ca addition on the microstructure and mechanical properties of AZ91 magnesium alloy [J]. J Mater Sci, 2000, 36(12): 3035-3040.
[12] LEE Y C, DAHLE A K, STJOHN D H. The role of solute in grain refinement of magnesium [J]. Mater Trans A, 2000, 31(11): 2895-2906.
[13] REED-HILL R E, ABBASCHIAN R. Physical metallurgy principles [M]. 2nd ed. New York: D Van Nostrand Company, 1973.
[14] HASSOLD G N, HOLM E A, SROLOVITZ D J. Effects of particle size on inhibited grain growth [J]. Scripta Metall Mater, 1990, 24(1): 101-106.
[15] HUTT J E C, STJOHN D H, HOGAN L, DAHLE A K. Equiaxed solidification of Al-Si alloys [J]. Mater Sci Technol, 1999, 15(5): 495-500.
[16] HUTT J E C, DAHLE A K, LEE Y C, STJOHN D H. The effects of growth restriction and effective nucleant potency on grain size and morphology in Al-Si and Al-Cu alloys [C]// ECKERT C E. Light Metals 1999, the Minerals, Metals and Materials Society (TMS). Warrendale, PA, USA, 1999: 685-692.
[17] EASTON M, STJOHN D H. Grain refinement of aluminum alloys. PartⅡ. Confirmation of, and a mechanism for, the solute paradigm [J]. Metall Mater Trans A, 1999, 30(6): 1625-1633.
[18] LIShuang-shou, TANG Bin, ZENGDa-ben. Effects and mechanism of Ca on refinement of AZ91D alloy [J]. Journal of Alloys and Compounds, 2007, 437(1/2): 317-321.
[19] KUBOTA K, MABUCHI M, HIGASHI K. Review processing and mechanical properties of fine-grained magnesium alloys[J]. Journal of Materials Science, 1999, 34(10): 4311-4320.
(Edited by YANG Hua)
Foundation item: Project(50475157) supported by the National Natural Science Foundation of China; Project(105052) supported by the Key Project of Ministry of Education of China
Corresponding author: ZHANG Xing-guo; Tel: +86-411-84706114; E-mail: zxgwj@dlut.edu.cn