J. Cent. South Univ. Technol. (2010) 17: 1155-1162
DOI: 10.1007/s11771-010-0612-3
Microstructures and wear resistance of chromium coatings on P110 steel fabricated by pack cementation
LIN Nai-ming(林乃明)1, XIE Fa-qin(谢发勤)1, ZHOU Jun(周俊)1,
ZHONG Tao(钟涛)1, WU Xiang-qing(吴向清)1, TIAN Wei(田伟)1, 2
1. School of Aeronautics, Northwestern Polytechnical University, Xi’an 710072, China;
2. Tubular Goods Research Institute, China National Petroleum Corporation, Xi’an 710065, China
? Central South University Press and Springer-Verlag Berlin Heidelberg 2010
Abstract: In order to obtain a high-performance surface on P110 steel that can meet the requirements in oil/gas field environment, the chromium coatings were fabricated by pack cementation. The chromium coatings differed in with/without the addition of La2O3. Scanning electron microscope (SEM), energy dispersive X-ray spectrometer (EDS), X-ray diffractometer (XRD) and microhardness tester were employed to investigate the surface morphologies, surface element distributions, microstructures, phase constitutions and microhardness of the coatings. Friction-wear tests of the P110 steel substrate and the coatings were conducted in air at ambient temperature and humidity. The results show that uniform and continuous coatings are formed on P110 steel regardless of adding La2O3 or not. The chromium coatings consist of Cr23C6, Cr7C3, and (Cr, Fe)7C3. The La2O3-added chromium coating is more beneficial in terms of surface morphology, microstructure, thickness and microhardness as compared with the coating without adding La2O3. Chromizing treatment significantly improves the surface hardness and wear resistance of the P110 steel. The wear resistance of the tested samples can be sorted in the following sequence: La2O3-coating>no RE-coating>bare P110 steel.
Key words: chromium coating; P110 steel; pack cementation; La2O3; microstructure; wear resistance
1 Introduction
The petroleum tube is an important structural member of the oil/gas well, which spends one third of the cost in oil/gas well development, and the oil casing tube occupies 73%-76% of the entire petroleum tube consumption [1]. The oil casing tubes experience severe wear during their operations [2]. Normally, the wear of casing occurs in the course of drilling, including the drilling of extended-reach wells, long horizontal traverse wells, horizontal wells and deep wells or in the intervals with great dog-leg severity, as well as drilling the long open hole whose intermediate casings have been tripped in [3]. The wear of casing can lead to the reduction of collapsing strength and internal pressure strength of casing, which results in reducing the lifetime of oil/gas wells, and even the abandonment of a certain interval or the whole well [1]. In many situations, the prevention or reduction of wear is achieved by the use of surface engineering techniques. The surface engineering technique that can offer an attractive performance cost ratio is traditionally applied to overcoming the problems of corrosion, wearing, and high temperature oxidation of materials [4]. There are a lot of researches conducted to develop and/or apply the surface engineering in the view of industrial production and laboratory study. But the applications of surface engineering techniques on oil casing tube steel have not received enough attention. According to a short-term benefit-cost analysis, using oil casing tube that is made of plain carbon steel is a cost effective option [5]. Therefore, surface treatment is a convenient and effective method to enhance the surface properties of the oil casing tube that can be tailored to the demands for petroleum production.
Due to the excellent combination of wear resistance, corrosion resistance and high temperature oxidation resistance, chromium coatings were extensively employed to improve the surface properties of steel components [6]. LEE et al [7] improved corrosion resistance and interfacial contact resistance of 316L stainless steel used for proton exchange membrane fuel cell bipolar plates by chromizing. While WANG et al [8] reported the enhancements in wear and corrosion properties of a low carbon steel via chromizing treatment. However, to the best knowledge of the authors, there are less studies and applications of chromium coatings on oil casing tube steel. Among different techniques to form diffusion coatings (aluminum coating, chromium coating, and aluminum-chromium coating), the pack cementation process is an effective and inexpensive method, which is basically an in-situ, self-generated chemical vapor deposition (CVD) process [9-12]. Many researchers pointed out that the rare earth (RE) has positive influences on surface treatment, e.g. enlarging the thickness and hardness of the coatings, and the RE can greatly refine the microstructure, improving the toughness and the fatigue resistance of the coatings [13-14]. Therefore, the RE-surface engineering has become a hot issue in recent years [15-16].
In this work, two chromium coatings with/without the addition of La2O3 were prepared on P110 oil casing tube steel (P110 steel) by means of pack cementation. The surface morphologies and element distributions, cross-sectional microstructures, phase structures as well as microhardness of the two chromium coatings were systemically studied. The friction-wear behaviors of the P110 steel and the coatings in dry sliding were investigated. The mass loss for each specimen was used to assess the wear resistance of the tested samples, and the wear mechanism for each sample was discussed.
2 Experimental
2.1 Materials
The rectangular specimens were cut from a P110 steel oil casing tube by an electric discharge wire-cutting machining in the size of 25 m×20 m×3 m. The chemical composition (mass fraction, %) of the P110 steel was listed as follows: C 0.26; Si 0.19; Mn 1.37; P 0.009; S 0.004; Cr 0.148; Ni 0.028; Mo 0.013; Cu 0.019; Nb 0.06; V 0.006; Ti 0.011; and Fe balance. Each specimen was manually ground using SiC abrasive paper and then polished. Prior to being chromized, all the specimens were ultrasonically cleaned in acetone bath and distilled water.
2.2 Preparation of chromium coatings
The pack mixture was composed of 45% (mass fraction) chromium powder (99.99% purity, 75 μm), 45% (mass fraction) Al2O3 (hard-burned) used as inert filler, 3% (mass fraction) NH4Cl (activator) and 7% (mass fraction) La2O3. This mixing ratio was obtained after orthogonal tests. A pack without La2O3 was prepared as a comparison. All the pack mixtures were weighed and then mixed by tumbling in a ball mill sufficiently. The specimens and pack mixtures were placed in an alumina crucible. Each of the alumina crucibles was closed with an alumina lid; thereafter the crucibles were sealed with the mixture of seat clay and soluble silicate. An electric tube furnace was employed in pack cementation process: (1) the sealed crucibles were put into the furnace, which was heated to 150 ℃ and held at this temperature for 3 h to remove the moisture from the pack; (2) the furnace was raised up to and kept at the desired temperature of 1 000 ℃ for 8 h; and (3) the crucibles were taken out and cooled down to room temperature in air. Fig.1 displays the schematic diagram of the pack cementation [10].
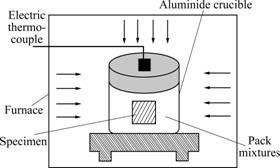
Fig.1 Schematic diagram of pack cementation device
2.3 Friction and wear tests
Friction and wear tests were carried out on the HT-1000 friction-wear testing machine by a ball-on-disc type tribometer under dry sliding in air at room temperature. The corundum balls with the diameter of 4.75 mm were chosen as the counterparts. All the tests were conducted at a gyration radius of 4 mm, a normal load of 10 N and a sliding velocity of 224 r/min for 1 h.
2.4 Characterization
Scanning electron microscope (SEM) was used to assess the surface morphologies, microstructures of the coatings and morphologies of the worn surface generated in the tests of the samples. The surface element distributions were examined by energy dispersive X-ray spectrometer (EDS). The obtained phases were identified by X-ray diffractometer (XRD) using Co Kα radiation (λ= 0.178 9 nm). An HV-1000 microhardness tester was used to measure the microhardness of the chromium coatings using a Knoop indenter at a load of 0.49 N and loading time of 20 s. The wear resistance of the specimens was evaluated via mass loss during sliding. An analytical balance (accuracy 0.1 mg) was employed to weigh the samples before and after friction and wear.
3 Results and discussion
3.1 Microstructural characterization
The chromium coatings were fabricated under the same process parameters, whose surface morphologies are shown in Figs.2 (no RE-coating) and 3 (La2O3- coating) in the back-scatter electron imaging (BEI) mode. The BEI mode makes it possible to detect any variation in chemical composition of the surface [14]. Tables 1 and 2 identify the surface element distributions of the two coatings.
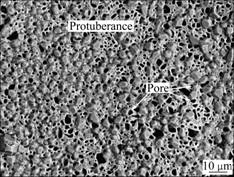
Fig.2 Surface morphology of no RE-coating
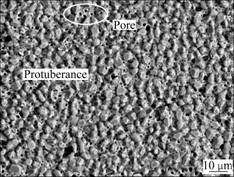
Fig.3 Surface morphology of La2O3-coating
Table 1 Surface element distributions of no RE-coating (mass fraction, %)
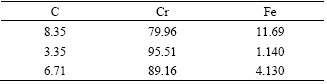
Table 2 Surface element distributions of La2O3-coating (mass fraction, %)
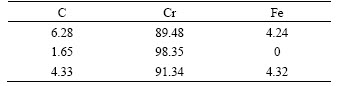
As shown in Fig.2, some homogenous protuberances with many pores distribute on the no RE-coating surface.
It is well known that the chromium is a carbide- forming element, so C and Cr are detected (Table 1). According to the EDS analysis results, the protuberances can be presumed to be the particles of chromium carbide.
With respect to the La2O3-coating, as shown in Fig.3, there are still homogenous protuberances distributing on the surface; but the surface seems smooth and more compact.
The pores located on the surfaces of the two coatings may be a result that vacancy migration, diffusion of chromium atoms into the P110 steel substrate and gas atoms decomposed from the activator (NH4Cl in the pack) act together [17].
Surface element distributions of the La2O3-coating are summarized in Table 2, which exhibits the contents of C and Cr, as well as Fe at the selected points.
For microstructural observations, each of the chromized samples was transversely cut, thereafter the coated samples were polished using standard metallographic procedure and chemically etched in a nital solution. Figs.4 (no RE-coating) and 5 (La2O3- coating) represent the cross-sectional SEM images of the two coatings in BEI mode.
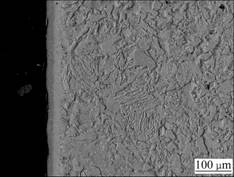
Fig.4 Cross-sectional SEM image of no RE-coating
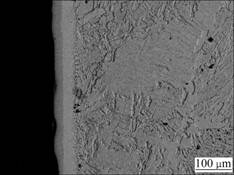
Fig.5 Cross-sectional SEM image of La2O3-coating
It is evident that the chromium coatings on the P110 steel are obtained using the pack cementation process whether adding La2O3 or not. The no RE-coating has a thickness of 30 μm in accordance with the survey scale. Compared with the no RE-coating in Fig.4, the La2O3- coating is much thicker and reaches a thickness of 50 μm according to the measuring scale as shown in Fig.5. In respect of Figs.4 and 5, the two coatings are continuous and compact; each coating consists of two distinct layers of different colors: an external layer and an internal layer. The external layer belongs to the compound layer (chromium-rich), and the internal layer corresponds to the chromium-diffusion zone. It is believed that the distribution characteristic of the coatings has a beneficial effect on the bond strength between the coating and the matrix [4, 11-12].
The mechanisms leading to the formation of the chromium coatings were widely and systematically discussed by different authors [4, 6-12]. The pack cementation process consists of a series of chemical reactions, which result in the formation of the chromium coatings:
2NH4Cl=2HCl(g)+2NH3 (1)
2NH3=N2+3H2 (2)
Cr+2HCl=CrCl2+H2 (3)
CrCl2+Fe=FeCl2+[Cr] (4)
CrCl2+H2=2HCl(g)+2[Cr] (5)
where [Cr] represents the active chromium atom. As described above the two chromium coatings are synthesized under the same parameters of test temperature and soaking time except adding La2O3 or without adding La2O3, and the chromium coating with addition of La2O3 is much thicker than that of no RE-coating. However, adding minor amount of La2O3 does not change the formation mechanism of chromium coatings, but facilitates the chromizing process [13-14]. It is reported that as the atom radius of RE is bigger than that of iron, in the early stage of chromizing, RE atoms segregate at grain boundary and defects (e.g. vacancy and dislocation) of the material, which can increase the diffusion pathway in numbers. As the RE is a surface-active element, it reacts with foreign elements, e.g. O, S, and P on the surface of test material and can clean the surface. As a result, chromium atoms are easily absorbed and solidified, their diffusion velocity is quickened, the chromizing process is speeded up, and the microstructure of the chromium coating is improved [15-16]. There are two diffusion courses in the chromizing process: one is the diffusion of chromium atoms into the P110 steel substrate, the other is inverse diffusion of the carbon atoms to the near surface of the P110 steel [4]. The chromium carbides are created by the two diffusion courses. Adding a small amount of La2O3 can promote the diffusion of chromium atoms into the P110 steel, meanwhile the inverse migration of carbon atoms is accelerated. And consequently, there are more protuberances (chromium carbides) and fewer pores on the La2O3-coating surface in comparison to the no RE-coating.
XRD patterns of the chromium coatings are shown in Fig.6. It is demonstrated that the chromium coatings are composed of Cr23C6, Cr7C3, and (Cr, Fe)7C3. On the basis of the XRD results, the influence of adding La2O3 on phase constitution in the coatings is not significant because the diffraction peaks corresponding to the coatings are close to each other.
Based on the microhardness corresponding to the measuring points along the depth direction of the coatings, the microhardness curves of the two coatings were plotted, as given in Fig.7. It is noted that higher microhardness of the P110 steel samples is obtained after chromizing treatments. The hardness distributions of the two coated specimens decrease gradually from the near surface to the inside.
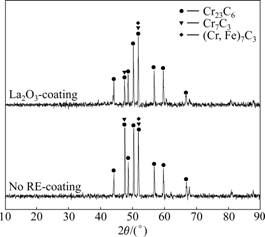
Fig.6 XRD patterns of chromium coatings
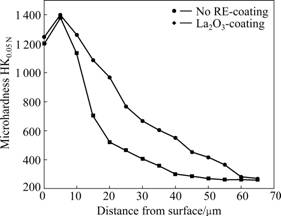
Fig.7 Microhardness profiles of two chromium coatings
Considerable enhancement of microhardness is connected with structural modi?cations on the near surface of the P110 steel, which is resulted from the formation of chromium carbides in the coatings, as shown in Fig.6. In general, the wear resistance is related to the surface hardness of the materials, therefore, the formation of chromium coatings on the P110 steel is also thought to be able to significantly improve their wear resistance [4].
3.2 Friction and wear behavior of samples
Fig.8 illuminates the friction coefficient-time curves of the P110 steel substrate and the coatings in dry sliding.
As shown in Fig.8(a), it is found that in the first 10 min, the friction coefficient belonging to the P110 steel substrate exhibits a sharp fluctuation characteristic, which indicates the existence of a running-in period during the initial state in sliding. Afterwards, the friction coefficient of the P110 steel substrate experiences a growth procedure lasting approximately 10 min and then keeps at a relative constant level [18]. The friction coefficient of the P110 steel maintains at around 0.4 until the test is completed.
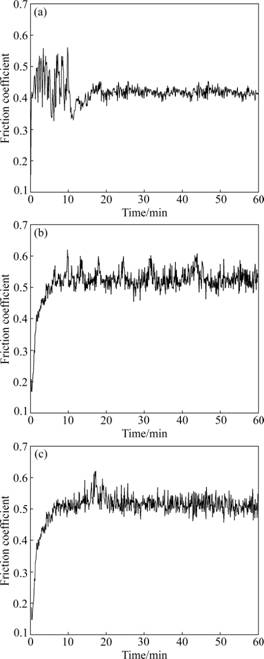
Fig.8 Friction coefficients of P110 steel (a), no RE-coating (b) and La2O3-coating (c) in dry sliding
Comparing the average friction coefficients in Fig.8, the P110 steel substrate has the smallest average friction coefficient, while the margin of friction coefficients between the two chromium coatings is narrow. Seen from Fig.8(b), it is noted that in the initial sliding stage the friction coefficient of no RE-coating continually increases for about 10 min and subsequently keeps on sharp fluctuation in the range of 0.50-0.60 in the remainder of the testing period. Fig.8(c) displays the variation of friction coefficient of the La2O3-coating with time. It can be found that the friction coefficient of the La2O3-coating oscillates slightly in the range of 0.50- 0.55 after reaching a peak and then decreases when the sliding is operated for about 20 min.
The distinction in friction coefficient among the tested samples can be explained from three aspects as follows: (1) the polished P110 steel is comparatively smooth, meanwhile the P110 steel is softer than the corundum ball, so the resistance to motion (friction force) between the P110 steel and the corundum ball is low; (2) as the previous investigations of surface morphologies (see Figs.2-3) suggest that chromium carbides (according to the EDS and XRD analysis) and pores distribute on the coated surfaces, which have an effect on the surface roughness, thus, the friction coefficients increase in sliding; and (3) the results of microhardness indicate that chromium carbides are of high hardness, hence, the plastic deformation occurs on the near surfaces of the coatings under the given load, which results in the increase of the friction force and the friction coefficient [19].
Fig.9 compares the variation characteristics of the mass losses between the P110 steel and chromium coatings. It is notable that, under the same conditions, the mass losses of the chromium coatings are far lower than those of P110 steel, and La2O3-coating has the lowest mass loss. The reduction of mass loss in dry sliding can be attributed to the enhancement in surface hardness degree of the two coatings. Generally, the increase in hardness of the ordinary chromium coatings is achieved at the cost of toughness, which may have a negative effect on the wear resistance [20]. SHARMA et al [14] reported that the RE such as CeO2 and La2O3 can both enlarge the hardness and toughness besides improving the corrosion and oxidation resistance of the chromium coatings. Thus, the mass loss of the no RE-coating is higher than that of La2O3-coating in this work. From the above results, it is allowed to conclude that good anti-wear performances of the chromium coatings are not due to their anti-friction property, but lie in the excellent wear resistance. The wear resistance of the tested samples is sorted in the following sequence: La2O3- coating>no RE-coating>bare P110 steel.
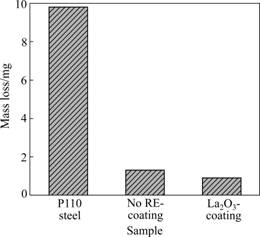
Fig.9 Mass losses of samples in dry sliding
Figs.10-12 illustrate the wearing morphologies of the P110 steel and chromium coatings at different scales in the secondary electron imaging (SEI) mode. The SEI mode can present the changes in surface morphologies of the tested samples [14].
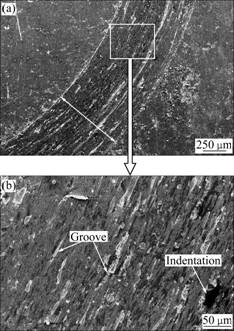
Fig.10 Secondary electron images of wear morphologies of P110 steel: (a) In lower magnification; (b) In higher magnifica- tion
As presented in Fig.10(a), the P110 steel is severely worn. The higher magni?cation image in Fig.10(b) highlights the signi?cant wear occurring during sliding. Grooves and indentation can be observed in the wear track. As the corundum ball is harder than P110 steel, plastic deformation takes place on P110 steel under the actions of load and friction force. There exists a dislocation pileup region on the near surface, which can induce the initiation of micro-cracks underneath the surface [21-22]. The cracks will gradually propagate with the development of plastic deformation when the cracks extend to the surface; and thin, long wear sheets will be formed and removed from the surface. The wear sheets will be engaged in the friction and ground into abrasive particles with small size. Thereby, the wear mechanism of P110 steel is a composite form of spalling crack and abrasive wear.
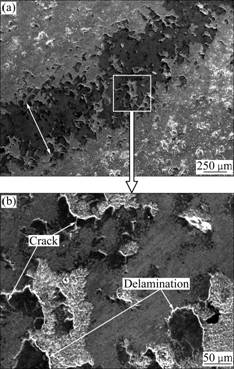
Fig.11 Secondary electron images of wear morphologies of no RE-coating: (a) In lower magnification; (b) In higher magnification
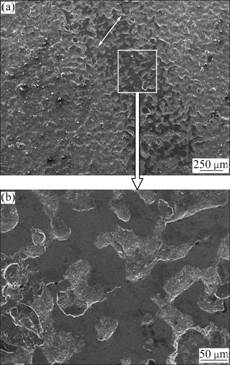
Fig.12 Secondary electron images of wear morphologies of La2O3-coating: (a) In lower magnification; (b) In higher magnification
However, the damage in wearing to the chromium coatings is relatively slight (see Figs.11-12). Seen from Fig.11(a), the wear scar of the no RE-coating is narrower than that of P110 steel. Some cracks and delaminations are evident in Fig.11(b). Studies show that the contact between the frictional pairs is discontinuous owing to the irregularities of the surface of material during the dry sliding [23]. Plastic deformation occurs and the fatigue cracks initiates at the contacted points under the impacts of cyclic loading and friction force. As the sliding proceeds, the propagation of the cracks will take place with the sustainable development of the plastic deformation. It is demonstrated that the no RE-coating has a porous surface (Fig.2) while the cracks preferentially propagate along the pores [24]. And the fractured and loosened pieces can be chipped off from the surface of the no RE-coating. Detailed observation in Fig.11(b) indicates that the worn surface is characterized by scale-like delamination, which is related to the wear mechanism. So the wear mechanism can be deduced as fatigue cracking and delamination wear.
It is clear in Fig.12(a) that, the wear trace of the La2O3-coating is incomplete and discontinuous as the white arrow indicates. The protuberances on the La2O3-coating surface are worn down, but there is no groove, and indentation, delamination and crack can be found in the enlarged image (Fig.12(b)). The La2O3- coating is found to have considerable hardness values on the surface, and adding La2O3 into chromium coating can improve the toughness of the coating. This leads to excellent resistance to plastic deformation and material wastage [23-25]. In addition, the La2O3-coating has a denser and lower porosity surface compared with that of the no RE-coating, as shown in Fig.3, accordingly, it is unfavorable for the production and growth of fatigue cracks [18, 21]. Consequently, the promising micro- structural characteristics belonging to the La2O3-coating significantly protect itself from serious damage in dry sliding, and the La2O3-coating experiences mild wear. So the most involved wear mode of the La2O3-coating is micro-scratching. Combining the mass loss with the observation of wearing morphology, it is confirmed that the La2O3-coating exhibits the best wear resistance.
4 Conclusions
(1) Continuous chromium coatings are formed on P110 steel by pack cementation under the same process parameters with the addition of La2O3 or not. The coatings are composed of Cr23C6, Cr7C3, and (Cr, Fe)7C3. Higher surface hardness of P110 steel is obtained after chromizing treatment. The La2O3-coating is much thicker than the no RE-coating, and shows less pores and higher hardness on the surface.
(2) The chromium coatings have higher friction coefficients, but lower mass loss in comparison to the P110 steel. The mass loss results confirm that P110 steel obtains excellent wear resistance by means of chromizing, and the wear resistance of the La2O3-coating is superior to that of the no RE-coating.
(3) The P110 steel undergoes a transition from spalling crack to adhesive wear. The wear mechanism of the no RE-coating can be considered as a combination of fatigue cracking and delamination wear, while micro- abrasion is the main wear mechanism to the La2O3- coating.
References
[1] LI He-lin, ZHANG Ya-ping, HAN Li-hong. Development situation of OCTG and production localization of Hi-grade OCTG: Part ? [J]. Steel Pipe, 2007, 36(6): 1-6. (in Chinese)
[2] WU Xue-feng, LIN Yuan-hua, WU Cai-wen, SHI Tai-he, LI Run-fang, LIN Teng-jiao. Research development of the preventing wear measures of casing [J]. Journal of Southwest Petroleum Institute, 2004, 26(4): 65-70. (in Chinese)
[3] LIN Yuan-hua, FU Jian-hong, SHI Tai-he, YAN Ren-jun, HE Zhi-gang, DONG Wei, LI Run-fang. Research on casing wear mechanism and antiwear measures [J]. Natural Gas Industry, 2004, 7: 58-61. (in Chinese)
[4] CAO Xiao-ming, WEN Ming, DU An. Modern metal surface alloying technologies [M]. Beijing: Chemical Industrial Press, 2007: 1-2. (in Chinese)
[5] LI He-lin, ZHANG Ya-ping, HAN Li-hong. Development situation of OCTG and production localization of Hi-grade OCTG: PartⅡ [J]. Steel Pipe, 2008, 37(1): 1-6. (in Chinese)
[6] ZHOU Y B, CHEN H, ZHANG H, WANG Y. Preparation and oxidation of an Y2O3-dispersed chromizing coating by pack cementation at 800 ℃ [J]. Vacuum, 2008, 82: 748-753.
[7] LEE S B, CHO K H, LEE W G, JANG H. Improved corrosion resistance and interfacial contact resistance of 316L stainless-steel for proton exchange membrane fuel cell bipolar plates by chromizing surface treatment [J]. Journal of Power Sources, 2009, 187: 318-323.
[8] WANG Z B, LU J, LU K. Wear and corrosion properties of a low carbon steel processed by means of SMAT followed by lower temperature chromizing treatment [J]. Surface and Coatings Technology, 2006, 201: 2796-2801.
[9] VOURLIAS G, PISTOFIDIS N, CHALIAMPALIAS D, PAVLIDOU E, STERGIOUDIS G, POLYCHRONIADIS E K, TSIPAS D. Zinc deposition with pack cementation on low carbon steel substrates [J]. Journal of Alloys and Compounds, 2006, 416: 125-130.
[10] PENG X M, XIA C Q, LIU Y Y, WANG J H. Surface molybdenizing on titanium by halide-activated pack cementation [J]. Surface and Coatings Technology, 2009, 203: 3306-3310.
[11] HOUNGNINOU C, CHEVALIER S, LARPIN J P. Synthesis and characterization of pack cemented aluminide coatings on metals [J]. Applied Surface Science, 2004, 236: 256-269.
[12] TSIPAS S A, OMAR H, PEREZ F H, TSIPAS D N. Boroaluminide coatings on ferritic-martensitic steel deposited by low-temperature pack cementation [J]. Surface and Coatings Technology, 2008, 202: 3263-3271.
[13] ZHANG Jin-zhu, YANG Zong-lun, WEI Ke-yuan. Study of the catalysis and diffusion mechanism by rare earth (RE) elements during the thermo-chemical treatment [J]. Materials Review, 2006, 20(5): 223-225. (in Chinese)
[14] SHARMA S P, DWIVEDI D K, JAIN P K. Effect of La2O3 addition on the microstructure, hardness and abrasive wear behavior of ?ame sprayed Ni based coatings [J].Wear, 2009, 267: 853-859.
[15] JI Ze-sheng. Effect of rare earth on B-Al permeating and computer kinetic simulation of permeation layer forming [J]. Transactions of Nonferrous Metals Society of China, 1999, 9(4): 791-795.
[16] HUANG Na-can, HU She-jun. Rare earth thermo-chemical treatment and rare earth material surface modification [J]. Chinese Rare Earths, 2003, 24(3): 59-63. (in Chinese)
[17] QI Tao, GUO Xi-ping. Structure formation of Si-Y2O3 co-deposition coatings on Nb-silicide-based alloy [J]. The Chinese Journal of Nonferrous Metals, 2009, 19(10): 1822-1828. (in Chinese)
[18] ZHANG Xiao-hua, LIU Dao-xin. Effect of TiN/Ti multilayer on fretting fatigue resistance of Ti-811 alloy at elevated temperature [J]. Transactions of Nonferrous Metals Society of China, 2009, 19(3): 557-562.
[19] ZHAO Guo-gang, ZHOU Yue-bo, ZHANG Hai-jun. Sliding wear behaviors of electrodeposited Ni composite coatings containing micrometer and nanometer Cr particles [J]. Transactions of Nonferrous Metals Society of China, 2009, 19(2): 319-323.
[20] SUCHANEK J, KUKLIK V. Influence of heat and thermochemical treatment on abrasion resistance of structural and tool steels [J]. Wear, 2009, 267: 2100-2108.
[21] YANG Jian-qun, LIU Yong, YE Zhu-yu, YANG De-zhuang, HE Shi-yu. Microstructure and tribological characteristics of nitrided layer on 2Cr13 steel in air and vacuum [J]. Surface and Coatings Technology, 2009, 204: 705-712.
[22] JIANG Jin-long, DAI Jian-feng, YANG Hua, WANG Qing. Wear behavior of Cu matrix composites reinforced with mixture of carbon and carbon nanotubes [J]. Journal of Wuhan University of Technology: Materials Science Edition, 2009, 24(2): 254-256.
[23] JONES L C, LLEWELLYN R J. Sliding abrasion resistance assessment of metallic materials for elevated temperature mineral processing conditions [J]. Wear, 2009, 267: 2010-2017.
[24] WAN Yi, XIONG Dang-sheng, LI Jian-liang. Cooperative effect of surface alloying and laser texturing on tribological performance of lubricated surfaces [J]. Journal of Central South University of Technology, 2010, 17(5): 906-910.
[25] CHENG Jiang-bo, LIANG Xiu-bing, XU Bin-shi, WU Yi-xiong. Microstructure and wear behavior of FeBSiNbCr metallic glass coatings [J]. Journal of Materials Science and Technology, 2009, 25(5): 687-690.
(Edited by CHEN Wei-ping)
Foundation item: Project(2007CB607603) supported by the National Basic Research Program of China
Received date: 2009-12-29; Accepted date: 2010-04-30
Corresponding author: XIE Fa-qin, PhD, Professor; Tel: +86-29-88494371; E-mail: fqxie@nwpu.edu.cn