J. Cent. South Univ. Technol. (2010) 17: 954-958
DOI: 10.1007/s11771-010-0583-4

Comprehensive utilization of kaolin ore accompanying muscovite
YU Lian-xiang(喻连香)1, 2, WANG Hai-dong(王海东)1, QIU Guan-zhou(邱冠周)1, LIANG Dong-yun(梁冬云)2
1. School of Mineral Processing and Bioengineering, Central South University, Changsha 410083, China;
2. Mineral Processing Engineering Research Department, Guangzhou Research Institute of Non-ferrous Metals, Guangzhou 510651, China
? Central South University Press and Springer-Verlag Berlin Heidelberg 2010
Abstract: In light of the problems of low-quality and low degree of comprehensive utilization of Guangdong muscovite-type kaolin, the reasons affecting the quality of kaolin were found to be a small amount of maroon powdery goethite adhering to the surface of kaolin and minor muscovite affecting the firing whiteness of products. The ores were dealt with by using the new combined process of attritioning-classification-bleaching and flotation. The separation of kaolin from muscovite, quartz and feldspar can come true through the new process. The high-quality kaolin with the firing whiteness of 91% can be obtained, and the muscovite is comprehensively recovered by adopting the key technology of flotation. The content of high-purity muscovite produced is over 99%. The muscovite discarded by original process can be comprehensively recovered.
Key words: muscovite-type kaolin; flotation; goethite; desliming
1 Introduction
Kaolin, a very important nonmetallic material, is widely used in ceramics, chemical engineering, plastic, paint and fire-resistant materials industries for its excellent characteristics [1-4]. China is one of the largest producers of ceramics. There is a huge demand for kaolin as ceramic raw materials [5-6]. However, with the exploitation and utilization of kaolin resources, high-quality kaolin has reduced increasingly, while the quality of most kaolin from the newly-built kaolin material base cannot meet the requirement for high-quality products. Especially for the muscovite-type kaolin mine in Guangdong Province in China, the quality of kaolin is poor that it will turn into red during calcinations [7-10]. There remain such problems like insufficient comprehensive utilization of the muscovite, which causes huge waste of resources. It is significant to study the comprehensive utilization of kaolin accompanying muscovite aiming at solving the difficulty of separation of this type of low-quality raw materials and improving the quality of kaolin, meanwhile, aiming at comprehensively recovering of the muscovite. Considering the low level of comprehensive utilization of mineral resources of muscovite-type kaolin and low-quality products, the adoption of such a technique as attritioning-classification-bleaching and flotation was widely discussed in this work. At last, a mineral technology of comprehensive utilization for resources of muscovite-type kaolin was developed.
2 Properties of raw ore
Muscovite-type kaolin raw ore contains 18.78% (mass fraction) Al2O3, 71.69% SiO2, and 0.72% Fe2O3. The results of microscope observation present that the main clay minerals are halloysite (7 ?) and minor illite in the kaolin (Fig.1). The halloysite is of needle-like crystal structure that is made of extremely fine hollow tubes with diameter of 100-400 nm. The halloysite is distributed mainly in less than 0.043 mm size fraction. The products with size less than 2 μm are composed of halloysite and minor illite. Non-clay minerals are mainly fragment minerals such as quartz, mica, feldspar, and contain minor limonite.
From result of different size fractions for crude ore in Table 1, it is known that the valuable kaolin minerals are centralized in size fraction less than 0.043 mm with the yield of 39.88%, muscovite minerals are centralized in size fraction of 0.043-0.500 mm, quartz is centralized in size fraction larger than 0.500 mm.
By process mineralogy research, the main reasons affecting whiteness of kaolin products in kaolin ore are found out. One of main reasons is that minor limonite is included in size fraction less than 0.043 mm and distributed on the surface of kaolin, which leads to kaolin to be brownish red. The other is that kaolin crude ores
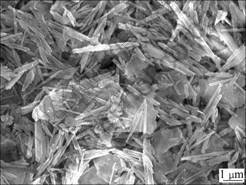
Fig.1 Needle-like halloysite and flake-like illite in less than 0.043 mm size fraction product
contain 10.97% muscovite, and minor fine muscovite particles are reported into kaolin product by traditional process of recovering kaolin, mono-mineral of muscovite contains 2.40% Fe2O3. Though part of Fe2O3 does not affect the natural whiteness of kaolin, the whiteness will be affected if muscovite lattice is destroyed and Fe in lattice is turned into Fe2O3 under the condition of high temperature (900 ℃). Therefore, in this work the ways of effective separation of muscovite and kaolin were investigated to improve the quality of kaolin products and realize the comprehensive utilization of muscovite in the purification of kaolin.
3 Results and discussion
3.1 Determination of way of comprehensive utilization of muscovite
Guangdong Muscovite-type Kaolin Mine originally adopts the mineral processing of attritioning- classification to mainly produce kaolin with size fraction less than 0.074 mm, so the quality of kaolin is affected by muscovite in kaolin. The natural whiteness of kaolin is about 65%, but the whiteness after calcination is decreased to approximately 50%. Such products are only used as low-rank products such as ceramic blank and rubber filler. The study of properties of raw ore shows that muscovite affecting the quality of kaolin is flake or layered aggregate distributed in kaolin with size fraction of 0.043-0.500 mm, and maroon powdery goethite is distributed in size fraction less than 0.043 mm. Therefore, the classified size is fixed at 0.043 mm. Majority of goethite is removed from kaolin after the classification by bleaching process, so the high-rank product of kaolin can be obtained. The screening size of muscovite, quartz and feldspar is fixed at 0.500 mm. After screening the muscovite products dealt by the key technology— flotation without fluorite are of high-quality. The method of the comprehensive utilization of muscovite-type kaolin is determined, as shown in Fig.2.
Table 1 Result of mineralogical content of crude ore in different particle fractions
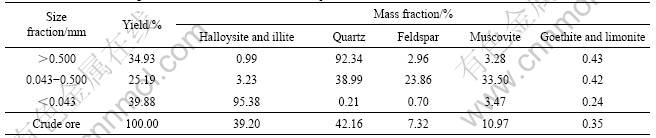
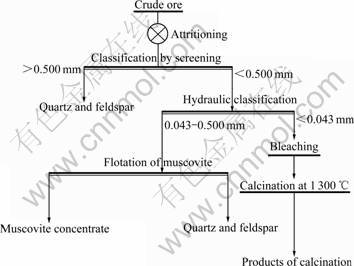
Fig.2 Method of comprehensive utilization of kaolin ore
3.2 Test of improving whiteness of kaolin
Kaolin with size fraction less than 0.043 mm from classification contains 35.17% Al2O3, 0.86% Fe2O3, and its natural whiteness is only 65.03%. Such low-rank products are used as ceramic blank, white cement, rubber and plastic filler and so on. To improve the rank of product quality, based on the requirement of market, the test for improving the whiteness of kaolin is carried out by classification.
There are many factors influencing bleaching such as temperature of bleaching, time of bleaching, pH of pulp, pulp density and reagent dosage [11-13]. The fact that the acidity of pulp and bleaching agent dosage have significant impact on the kaolin whitening is considered, so the dosages of sulfate and sodium hydrosulfite are mainly tested.
3.2.1 Effect of dosage of sulfuric acid on bleaching whiteness of kaolin
After sodium hydrosulfites react with iron oxide, Fe2+ generated can be stabilized only within a certain range of acidity. After cleaning and filtration the residual Fe2+ in kaolin will be oxidized to Fe3+ stained if kaolin is placed in air for a long time. For kaolin minerals, the phenomenon of “coloring” will appear. According to data in Refs.[14-15], the amount of oxalic acid and sulfuric acid used in appropriate conjunction can not only enhance the bleaching effect, but also prevent the bleaching product from appearing of the phenomenon of “coloring”. In addition to adjusting pH of pulp, oxalic acid can also participate in coordination reaction. Iron ions generated are of high water-soluble property. After cleaning and filtration, most of the iron-containing impurities can be washed away, even if there still exists Fe2+, because the chemical stability has oxalic acid iron complex, which is very difficult to be oxidized, resulting in a long-term maintenance of products without being colored again. Therefore, in this work 1 kg/t oxalic acid is added into sulfuric acid to carry out dosage test.
The effect of dosage of sulfuric acid on bleaching whiteness is shown in Fig.3. It is shown that with the increase of sulfuric acid dosage, the bleaching whiteness is upgraded. When the dosage of sulfuric acid is increased from 2 to 8 kg/t, the increasing range of bleaching whiteness is wide. When the dosage of sulfuric acid is over 8 kg/t, there is no additional effect on bleaching whiteness. This suggests that the suitable dosage of sulfuric acid is 8 kg/t for the kaolin. Under the suitable dosage, the bleaching whiteness of kaolin is up to 82.78%.
3.2.2 Effect of dosage of sodium hyposulfite on bleaching whiteness of kaolin
Under the fixed condition of pulp density of 15%, attritioning time of 15 min and oxalic acid dosage of 1 kg/t, the contrast test is conducted. The effect of the dosage of sodium hyposulfite on the bleaching whiteness of kaolin is shown in Fig.4. It is seen that with the increase of sodium hyposulfite dosage, the bleaching whiteness is upgraded. When the dosage of sodium hyposulfite is increased to 16 kg/t, the bleaching whiteness of kaolin is up to 82.73%. But when the dosage of sodium hyposulfite is over 16 kg/t, the bleaching whiteness is reduced. Because too much sodium hyposulfite will be quickly decomposed into sodium thiosulfate and sodium bisulfite in water, it not only fails to improve whiteness, but also results in waste of agents. Therefore, the appropriate amount of sodium hyposulfite is about 16 kg/t.
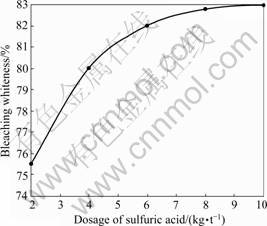
Fig.3 Effect of dosage of sulfuric acid on bleaching whiteness of kaolin

Fig.4 Effect of dosage of sodium hyposulfite on bleaching whiteness of kaolin
Under the best condition of bleaching, the bleaching whiteness of kaolin product with size fraction less than 0.043 mm through bleaching is upgraded from 65% to 83%. The calcining whiteness is upgraded from 83% to 91% and the content of Fe2O3 is decreased from 0.86% to 0.45%. The quality of kaolin with size fraction less than 0.043 mm through classification can be upgraded in a wide range. Thus, the high-quality kaolin may be used to produce ceramics.
3.3 Comprehensive utilization of muscovite
Gravity separation process of shaking table is usually adopted for comprehensive utilization of muscovite. But the purify and recovery of muscovite are often in a low level by shaking table. The muscovite is easy to be floated because of its major existence in the easy-floating size fraction of 0.043-0.500 mm. So, in this work the key technology-flotation is adopted to directly treat the product with size fraction of 0.043- 0.500 mm without additional grinding process. By exploring economic and reasonable process of effectively recovering the muscovite, the relatively pure muscovite concentrates are got and the separation of valuable minerals-muscovite and quartz, feldspar is achieved.
4 Flotation of kaolin
4.1 Batch test for roughing flotation
Sulfuric acid and mixed-amine are respectively used as regulator and collector in the muscovite flotation process. Its appropriate dosage is determined by the technological process of one roughing and one scavenging.
The tests on the dosage of sulfuric acid in roughing process are carried out when the mixed-amine dosage in roughing and scavenging process is respectively 100 and 80 g/t. When the dosage of sulfuric acid is respectively 200, 400, 600, and 800 g/t, the results show that the more the sulfuric acid added, the higher the yield of muscovite roughing, and the higher the content of muscovite in the rough concentrate, which indicates that it is beneficial to muscovite flotation to increase the dosage of sulfuric acid in a certain range of acidity. But when the dosage of sulfuric acid is more than 600 g/t, the content of muscovite is lower, which shows that the appropriate dosage of sulfuric acid is 600 g/t. Meanwhile, the content of muscovite is 95.48%.
When the dosage of sulfuric acid is fixed as 600 g/t, the tests are carried out at different dosages of mixed- amine (100, 125, 150, and 175 g/t). The results show that the yield of muscovite roughing is improved significantly and the recovery is also increased from 80.79% to 90.29% with the increase of dosage of mixed-amine in the absence of the content obvious decline in muscovite. When the dosage of mixed-amine is increased to 175 g/t, though the yield of rough concentrate is increased continuously, the content of muscovite is decreased quickly from about 95% to 90% with no improvement of the rough recovery. This indicates that the collection effect of mixed-amine is too strong to selectively collect efficiently. When the dosage is too high many gangue minerals such as quartz and feldspar will float. So, the dosage of mixed-amine is determined as 150 g/t.
4.2 Desliming test before flotation
It is discovered in the cleaning process that pure muscovite cannot be obtained even though the muscovite of roughing is cleaned repeatedly, but its grade is only 96%. The microscopic analysis shows that the rough concentrate containing a little kaolinite, which is a finely dispersed mineral, is the main factor affecting the separation of concentrates. The granular kaolinite and illite are easy to be broken and scattered into more fine grains. These finely dispersed clay minerals absorb agent easily, which makes the cleaning froth sticky and carries quartz, feldspar and other particles, which has a poor effect on muscovite cleaning. The process of flotation after desliming is adopted with the flow sheet shown in Fig.5. It can be observed from the test that the concentrate froth becomes crisp and thick in the flotation process after desliming. Pure muscovite with the content higher than 99% can be obtained when the rough concentrate is cleaned five times and the recovery basically remains invariable. So, the desliming flotation has a good result.
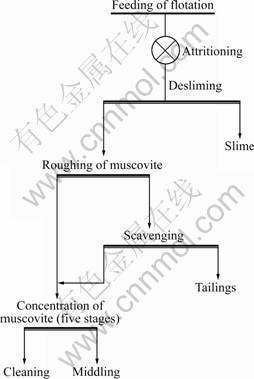
Fig.5 Flowsheet of desliming-flotation
4.3 Full flowsheet test on comprehensive utilization of muscovite
From the above test, the best test conditions are fixed, which are the roughing dosage of sulfuric acid as 600 g/t, the roughing dosage of mixed-amine as 150 g/t, the scavenging dosage of mixed-amine as 50 g/t, five- stage cleaning, and the cleaning dosage of mixed-amine as 30 g/t. The full flowsheet test on comprehensive utilization of muscovite is shown in Fig.5. The high-purity muscovite concentrate with the content over 99% is got after five-stage cleaning. The operation recovery of flotation is 71.74% in open circuit test.
5 Conclusions
(1) The primary clay minerals are halloysite (7 ?) and a spot of illite in the Guangdong muscovite-type kaolin deposit, and non-clay minerals are mainly detrital minerals such as quartz, mica, feldspar, which contain minor limonite. The halloysite is acicular crystals. The halloysite and illite are mainly centralized in the size fraction less than 0.043 mm, the natural whiteness of this size fraction is only 65.03% and the calcined whiteness is about 50%. The main influencing factor of the kaolin whiteness is that the surface of kaolin is adhered by a spot of maroon powdered goethite, and the secondary factor is that there is a spot of fine muscovite in the kaolin products, which has effect on the whiteness if muscovite lattice is destroyed and Fe2+ in lattice turns into iron brown Fe2O3 when it is calcined.
(2) The bleaching whiteness of kaolin product with size fraction less than 0.043 mm is upgraded from 65% to 83% after bleaching, the calcining whiteness is upgraded from 83% to 91%, and the content of Fe2O3 is downgraded from 0.86% to 0.45% after calcination. So the whiteness of the kaolin products can be greatly improved, meanwhile the high-quality kaolin can be got. The products can be used as ceramic glazes, refractory materials, paper filler and petroleum catalysts.
(3) The content of the mineral muscovite is about 10.97% in the ore body. The muscovite is flake or layered aggregate, which is mainly centralized in kaolin with size fraction of 0.043-0.500 mm. Study on comprehensive utilization of muscovite in kaolin with size fraction of 0.043-0.500 mm is directly adopted by flotation key technology under the condition of non-grinding. The kaolin entrained into the muscovite at classification can be removed cleanly by desliming, subsequently, the quartz and feldspar can be effectively separated by the flotation technology which adopts non-toxic flotation reagents such as mixed-amine and sulfuric acid, finally, the high-purity muscovite concentrate can be achieved and its content is more than 90%, at the same time the flotation recovery of the open-circuit test is 71.74%.
References
[1] GAO Hui-min, WANG Jin-ling, YUAN Ji-zu, ZHANG Ling-yan. Experimental research on benefication of Daoxian kaolinite ore [J]. Metal Mine, 2004(z1): 424-426. (in Chinese)
[2] ?MINOV A M, MASLENNIKOVA G N, ABDURAKHMANOV A K, KADYROVA Z R, BAIZHAOV I R. Kaolin from Sultan-Uvaiskoe deposit in ceramic production [J]. Glass and Ceramics, 2001, 58(9/10): 315-316.
[3] AKHTAR N A, WORRALL W E. Separation of kaolinite and illite in fireclays [J]. Transactions and Journal of the British Ceramic Society, 1975, 74(3): 105-111.
[4] SHARAD M. Kaolin flotation [J]. Journal of Colloid and Interface Science, 2002, 256(1): 153-158.
[5] GAO Hui-min, LEI Yun, YUAN Ji-zu, CHANG Ling-yan. Experimental research on ore dressing of kaolin in Chijiang [J]. China Ceramics, 2003, 9(5): 22-37, 54. (in Chinese)
[6] WU Tie-lun. Present situation and prospect of kaolin market in China [J]. Non-metallic Mines, 2004, 27(1): 1-4. (in Chinese)
[7] SATHY C, RAMASWAMY S. Influence of mineral impurities on the properties of kaolin and its thermally treated products [J]. Applied Clay Science, 2002, 21(3/4): 133-142.
[8] CAI Li-na, HU De-wen, LI Kai-qi, XI Shu-na. Progress of technology on iron removal from kaolin [J]. Mining and Metallurgy, 2008, 17(4): 51-54. (in Chinese)
[9] SULTANOVICH E A, KARMAZIN V I. Kaolin beneficiation in a high-gradient magnetic separator with a ball matrix [J]. Magnetic and Electrical Separation, 1993, 5(1): 1-15.
[10] PENG Shi-ying. Application of high gradient magnetic separation in kaolin industry in China [J]. Conservation and Utilization of Mineral Resources, 1994(3): 27-30. (in Chinese)
[11] VEGLIO F, PAGLIARINI A, TORO L. Factorial experiments for the development of a kaolin bleaching process [J]. International Journal of Mineral Processing, 1993, 39(1/2): 87-99.
[12] FYSH S A, CLARK P E. A Mossbauer study of the iron mineralogy of acid leached bauxite [J]. Hydrometallurgy, 1983, 10(3): 285-3031.
[13] HU Qing-fu, LIU Bao-shu, HU Xiao-xing, HU Xiao-bo. Practice of bleaching powder materials [J]. Industrial Minerals and Processing, 2004, 33(9): 14-15, 29. (in Chinese)
[14] VEGLIO F, PASSARIELLO B, TORO L, MARABINI A M. Development of a bleaching process for a kaolin of industrial interest by oxalic, ascorbic, and sulfuric acids: Preliminary study using statistical methods of experimental design [J]. Industrial and Engineering Chemistry Research, 1996, 35(5): 1680-1687.
[15] de MESQUITA L M S, RODRIGUES T, GOMES S S. Bleaching of Brazilian kaolins using organic acids and fermented medium [J]. Minerals Engineering, 1996, 9(9): 965-971.
(Edited by YANG You-ping)
Received date: 2010-01-07; Accepted date: 2010-04-26
Corresponding author: YU Lian-xiang, PhD, Senior engineer; Tel: +86-20-61086451; Fax: +86-20-37238535; E-mail: ylxgz2008@126.com