Article ID: 1003-6326(2005)05-1021-05
Influence of Cr or Co doping on electrode properties of V2.1TiNi0.5Hf0.05 hydrogen storage alloy
CHEN Li-xin(陈立新), GUO Rui(郭 蕊),
LI Lu(李 露), LEI Yong-quan(雷永泉)
(College of Materials Science and Chemical Engineering, Zhejiang University, Hangzhou 310027, China)
Abstract: The microstructures and electrode properties of Cr or Co-doped V2.1TiNi0.5Hf0.05M0.113 (M=Cr, Co) hydrogen storage alloys were investigated. It is found that all alloys consist of a main phase of V-based solid solution with b.c.c. structure and a secondary phase of C14-type Laves phase with a three-dimensional network structure. After the doping of Cr or Co into V2.1TiNi0.5Hf0.05, the abundance and unit cell volume of the main phase decrease, and those of the secondary phase increase. The electrochemical measurements show that the discharge capacities of Cr-doped V2.1TiNi0.5Hf0.05Cr0.113 alloy and Co-doped V2.1TiNi0.5Hf0.05Co0.113 alloy are less than that of V2.1TiNi0.5-Hf0.05 alloy, but their cycle stability and high-rate dischargeability are improved markedly. The results show that Cr or Co doping into V2.1TiNi0.5Hf0.05 alloy is significantly beneficial for the cycling stability.
Key words: V-based hydrogen storage alloys; Cr doping; Co doping; electrode properties; microstructure CLC number: TG139.7
Document code: A
1 INTRODUCTION
Vanadium-based solid solution electrode alloys have attracted the attention of scientists since the V3TiNi0.56 alloy with high electrochemical discharge capacity was reported[1]. These alloys characteristically consist of two phases: a vanadium-based solid solution as main phase and a secondary phase, which work as a hydrogen storage phase and a micro-current collector, respectively. However, the poor cycling stability of these alloys in KOH electrolyte keeps them from the industrialization for Ni-MH batteries. The influence of various additive elements to V3TiNi0.56 alloy was investigated for improving the electrode properties, especially the cycling stability[2-7]. The results show that multi-component alloying is an effective method for improving the overall properties of the hydrogen storage electrode alloys[8-12]. In our previous works, V2.1TiNi0.5Hf0.05 was found to have a high discharge capacity of 444mA·h/g and a poor cycling capacity retention of 27.66% after 30 cycles[13]. In this paper, Cr and Co were chosen as the added alloying elements into V2.1TiNi0.5Hf0.05 for improving its cycling stability, and the microstructure and electrode properties of V2.1TiNi0.5-Hf0.05M0.113 (M=Cr, Co) hydrogen storage alloys were investigated systematically.
2 EXPERIMENTAL
The alloy samples were prepared by vacuum induction melting under argon atmosphere and each batch was remelted three times to ensure high homogeneity. The metallographic microstructures were examined by using a scanning electron microscope(SEM). The chemical compositions of the overall alloys and the contents of alloy elements in the KOH electrolyte after charging-discharging cycles were confirmed by using an inductively coupled plasma technique(ICP), and the chemical compositions of micro-area for each phase were determined with an energy dispersive X-ray spectrometer(EDS). The crystal structures and lattice parameters were determined by X-ray powder diffraction(XRD) using CuKα radiation.
The samples were pulverized first by hydriding and then crushed mechanically into particles below 50μm in size after dehydriding. Each test electrode was prepared by mixing alloy powders with copper powders in the mass ratio of 1∶2 and then the mixture was cold-pressed into a pellet. The electrochemical properties of these negative electrodes were measured in a tri-electrode open cell at 298K with a sintered Ni(OH)2/NiOOH positive counter electrode and a Hg/HgO reference electrode. The negative electrodes were charged at 100mA/g for 6.5h and discharged at 25-500mA/g to the cutoff potential of -0.70V vs Hg/HgO. The electrochemical hydrogen desorption P-C isotherms at 298K were plotted by using the pulse charge/discharge method at 25mA/g, and the hydrogen desorption equilibrium pressure(peq) was calculated from the measured equilibrium electrode potential(Eeq) according to the Nernst equation[14]:
Eeq(V vs Hg/HgO) =
-0.93045-0.029547log(peq)
The exchange current density Io of the alloys was calculated from the slopes of micro-polarization curves, which were determined by scanning the electrode potential at 0.1mV/s from -5mV to 5mV (vs open circuit potential) with a Solartron SI 1287 potentiostat.
3 RESULTS AND DISCUSSION
3.1 Microstructure
Fig.1 shows the XRD patterns of V2.1TiNi0.5-Hf0.05M0.113 (M=Cr, Co) alloys. All of three alloys consist of a main phase of V-based solid solution with b.c.c. structure and a secondary phase of C14-type Laves phase. The calculated unit cell volumes of each phase are shown in Table 1. It can be seen that the unit cell volume of the main phase decreases from 0.02873nm3 to 0.02866nm3 or 0.02847nm3 with adding Cr or Co into the V2.1TiNi0.5Hf0.05 alloy, and that of the secondary phase significantly increases from 0.17626nm3 to 0.17924nm3 or 0.17977nm3.
Fig.2 shows the SEM micrographs of V2.1TiNi0.5Hf0.05M0.113 (M=Cr, Co) alloys. It can be seen that the secondary phase all precipitates along the grain boundaries of the main phase in the form of a three-dimensional network. The phase abundance of the main and secondary phases are calculated[15] and shown in Table 1. The amount of the main phase decreases and the amount of the secondary phase increases after adding Cr or Co into the V2.1TiNi0.5Hf0.05 alloy.
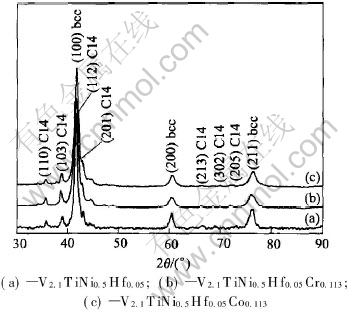
Fig.1 XRD patterns of alloy samples
3.2 Electrochemical characteristics
The activation cycle numbers and maximum discharge capacities of V2.1TiNi0.5Hf0.05M0.113 (M=Cr, Co) alloys are shown in Table 2. It can be seen that the activation cycle number increases from 1 to 2 after the doping of Cr or Co. V2.1TiNi0.5Hf0.05 has the highest discharge capacity of 444mA·h/g, much higher than that of V2.1TiNi0.5-Hf0.05Cr0.113 (392mA·h/g) and V2.1TiNi0.5Hf0.05-Co0.113 (386mA·h/g). The electrochemical P-C desorption isotherms of the alloys are shown in Fig.3. The results indicate that the plateau pressure rises and the width of pressure plateau reduces after adding Cr or Co into the V2.1TiNi0.5Hf0.05 alloy. The decrease of the discharge capacity due to the doping of Cr or Co could be ascribed to the decrease of the phase abundance and the unit cell volumes of the main phase. The later could be mainly responsible for the decrease, because comparing with V2.1TiNi0.5Hf0.05, the equilibrium hydrogen pressure of V2.1TiNi0.5Hf0.05Cr0.113 or V2.1TiNi0.5Hf0.05Co0.113 is almost the same or distinctly high er, respectively, while a smaller cell volume generally leads to a higher equilibrium pressure[16].
Table 1 Micro-structural characteristics of alloy samples
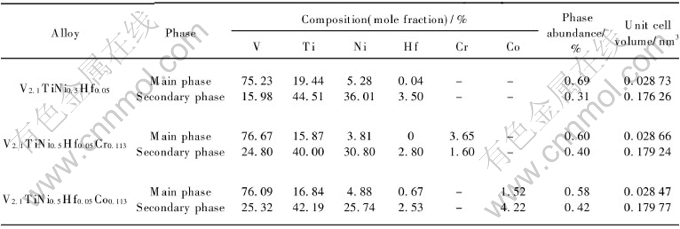
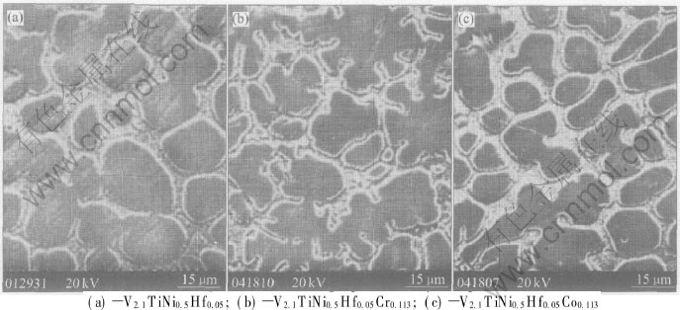
Fig.2 SEM micrographs of alloy samples
Table 2 Electrochemical properties of alloy samples
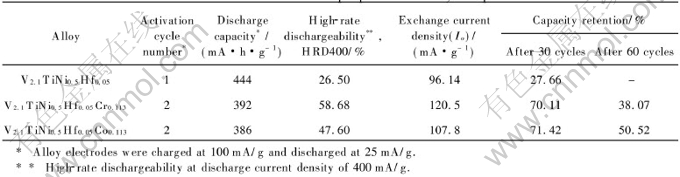
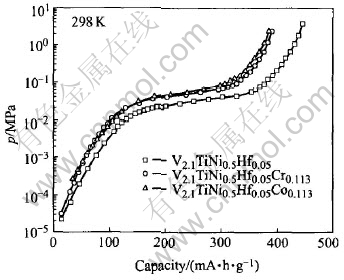
Fig.3 Electrochemical P-C desorption isotherms of alloy samples
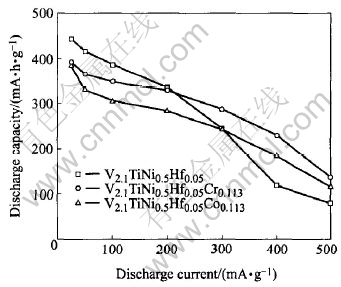
Fig.4 Relation between discharge capacity and discharge current density for alloy samples
The relation between discharge capacity and discharge current density for V2.1TiNi0.5Hf0.05-M0.113 (M=Cr, Co) alloys is shown in Fig.4. At larger discharge current densities (400-500 mA/g), the discharge capacities of V2.1TiNi0.5Hf0.05-Cr0.113 and V2.1TiNi0.5Hf0.05Co0.113 are much higher than that of V2.1TiNi0.5Hf0.05. The high-rate dischargeability (HRD400=C400/C25(100%) of these alloys at the discharge current density of 400mA/g is shown in Table 2. It can be seen that V2.1TiNi0.5Hf0.05Cr0.113 has the best high-rate dischargeability (HRD400 of 58.68%) among the studied alloys. These results are also supported by the magnitude of the exchange current densities Io (Table 2) calculated from the slopes of the micro-polarization curves of these alloys as shown in Fig.5.
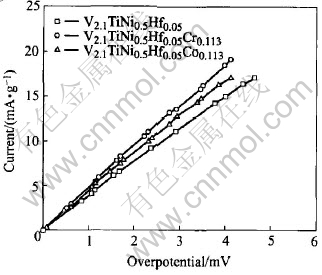
Fig.5 Micro-polarization curves of alloy electrodes
Fig.6 shows the cycling capacity degradation curves of the V2.1TiNi0.5Hf0.05M0.113 (M=Cr, Co) alloys. All of the alloys were activated within two charging-discharging cycles. The discharge capacity of V2.1TiNi0.5Hf0.05 reduces rapidly and its capacity retention after 30 cycles is only 27.66%. However, the degradation of V2.1TiNi0.5Hf0.05-Cr0.113 or V2.1TiNi0.5Hf0.05Co0.113 is slow comparatively. As shown in Table 2, the capacity retention of V2.1TiNi0.5Hf0.05Cr0.113 is 70.11% after 30 cycles and 38.07% after 60 cycles, and the capacity retention of V2.1TiNi0.5Hf0.05Co0.113 is 71.42% after 30 cycles and 50.52% after 60 cycles, much better than that of V2.1TiNi0.5Hf0.05. These indicate that the doping of Cr or Co is very helpful in improving the cycling stability of the V2.1TiNi0.5Hf0.05 alloy. Table 3 shows the content of alloy elements in the KOH electrolyte after 30 charging-discharging cycles. It can be seen that the dissolution of vanadium in the alloy into KOH electrolyte is faster than other elements, and the vanadium content in the electrolyte solution decreases markedly after the doping of Cr or Co into the V2.1TiNi0.5Hf0.05 alloy. This result indicates that Cr and Co can restrict the dissolution of vanadium and improve the corrosion resistance of this series alloys in KOH electrolyte solution noticeably[17, 18].
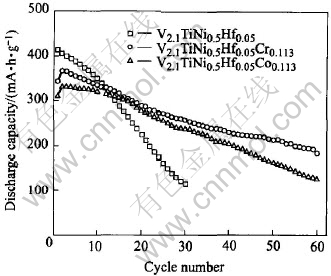
Fig.6 Cycling capacity degradation curves of alloy samples charged at 100mA/g and discharged at 50mA/g
Table 3 Content of alloy elements in KOH electrolyte after 30 charging-discharging cycles
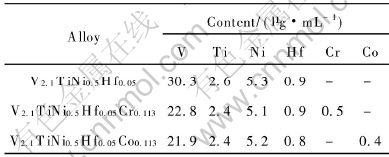
4 CONCLUSIONS
All V2.1TiNi0.5Hf0.05M0.113 (M=Cr, Co) alloys consist of a main phase of V-based solid solution with b.c.c. structure and a secondary phase of C14-type Laves phase with a three-dimensional network structure. After the doping of Cr or Co into V2.1TiNi0.5Hf0.05, the abundance and unit cell volume of the main phase decrease, and those of the secondary phase increase. The maximum discharge capacities of the Cr-doped and Co-doped alloys are less than that of the V2.1TiNi0.5Hf0.05 alloy. However, the doping of Cr or Co into the V2.1TiNi0.5-Hf0.05 alloy is significantly beneficial for the cycling stability and high-rate dischargeability.
REFERENCES
[1]Tsukahara M, Takahashi K, Mishima T, et al. Phase structure of V-based solid solutions containing Ti and Ni and their hydrogen absorption-desorption properties [J]. J Alloys and Compounds, 1995, 224 (1): 162-167.
[2]Tsukahara M, Takahashi K, Mishima T, et al. Metal hydride electrodes based on solid solution type alloy TiV3Nix (0≤x≤0.75) [J]. J Alloys and Compounds, 1995, 226 (1-2): 203-207.
[3]Tsukahara M, Takahashi K, Mishima T, et al. Influence of various additives in vanadium-based alloys V3TiNi0.56 on secondary phase formation, hydrogen storage properties and electrode properties [J], J Alloys and Compounds, 1996, 245(1-2): 59-65.
[4]Tsukahara M, Takahashi K, Isomura A, et al. Improvement of the cycle stability of vanadium-based alloy for nickel-metal hydride (Ni-MH) battery [J]. J Alloys and Compounds, 1999, 287(1-2): 215-220.
[5]YU X B, WU Z, XIA B J, et al. A Ti-V-based bcc phase alloy for use as metal hydride electrode with high discharge capacity [J]. J of Chemical Physics, 2004, 121(2): 987-990.
[6]YU X B, WU Z, XIA B J, et al. Electrochemical performance of ball-milled Ti-V-based electrode alloy [J]. Int J Hydrogen Energy, 2005, 30(3): 273-277.
[7]CHEN Li-xin, DAI Fa-bang, LIU Jian, et al. Influence of ball-milling with Cu powder on the electrochemical properties of V-based solid solution type hydrogen storage alloys [J]. The Chinese Journal of Nonferrous Metals, 2005, 15(4): 661-666. (in Chinese)
[8]ZHANG Q A, LEI Y Q, YANG X G, et al. Influence of Mn on phase structures and electrochemical properties of V3TiNi0.56Hf0.24 alloy [J]. Int J Hydrogen Energy, 2000, 25(7): 657-661.
[9]ZHANG Q A, LEI Y Q, YANG X G, et al. Phase structures and electrochemical properties of V3TiNi0.56-Hf0.24Cox alloy [J]. J Alloys and Compounds, 2000, 296(1-2): 87-91.
[10]ZHANG Q A, LEI Y Q, YANG X G, et al. Phase structures and electrochemical properties of Cr-added V3TiNi0.56Hf0.24Mn0.15 alloys [J]. Int J Hydrogen Energy, 2000, 25(10): 977-981.
[11]ZHANG Y, LI S Q, CHEN L X, et al. Corrosion mechanism of mechanically alloyed Mg50Ni50 and Mg45Cu5Ni50 alloys [J]. Trans Nonferrous Metals Soc China, 2002, 12(2): 238-241.
[12]CHEN X L, LEI Y Q, LIAO B, et al. Effects of annealing treatment on microstructure and electrochemical performances of Co-free MlNi4.0Al0.3Si0.1Fe0.6 hydrogen storage alloy [J]. The Chinese Journal of Nonferrous Metals, 2004, 14(11): 1862-1868. (in Chinese)
[13]GUO R, CHEN L X, LEI Y Q, et al. The effect of Hf content on the phase structures and electrochemical properties of V2.1TiNi0.5Hfx (x=0-0.25) hydrogen storage alloys [J]. J Alloys and Compounds, 2003, 352(1-2): 270-274.
[14]Balej J. Determination of the oxygen and hydrogen overvoltage in concentrated alkali hydroxide solutions [J]. Int J Hydrogen Energy, 1985, 10(6): 365-374.
[15]Tsukahara M, Takahashi K, Mishima T, et al. V-based solid solution alloys with Laves phase network: hydrogen absorption properties and microstructure [J]. J Alloys and Compounds, 1996, 236(1-2): 151-155.
[16]Reilly J J, Adzic G D, Johnson J R, et al. The correlation between composition and electrochemical properties of metal hydride electrodes [J]. J Alloys and Compounds, 1999, 293-295: 569-582.
[17]Ovshinsky S R, Fetcenko M A, Ross J. A nickel metal hydride battery for electric vehicles [J]. Science, 1993, 260: 176-181.
[18]Tsukahara M, Takahashi K, Mishima T, et al. Vanadium-based solid solution alloys with three-dimensional network structure for high capacity metal hydride electrodes [J]. J Alloys and Compounds, 1997, 253-254: 583-586.
Foundation item: Project(50271064) supported by the National Natural Science Foundation of China; Project(2003AA515021) supported by the Hi-Tech Research and Development Program of China
Received date: 2005-02-08; Accepted date:2005-07-01
Correspondence: CHEN Li-xin, Associate professor, PhD; Tel: +86-571-87951152; E-mail: lxchen@zju.edu.cn
(Edited by LI Xiang-qun)