DOI: 10.11817/j.ysxb.1004.0609.2020-37517
液-固体积比对消失模铸造Al/Cu双金属界面组织性能的影响
管 峰,蒋文明,樊自田,李广宇,蒋海啸,朱俊文
(华中科技大学 材料成形与模具技术国家重点实验室,武汉 430074)
摘 要:研究液-固体积比对消失模铸造Al/Cu双金属界面组织和性能的影响,并对Al/Cu双金属界面的形成机理进行讨论。结果表明:液-固体积比为3:1时Al/Cu双金属材料无法形成有效的冶金结合,当液-固体积比超过5:1时,Al/Cu双金属材料连接区域部分位置开始发生冶金结合;在发生冶金反应的情况下,Al/Cu双金属界面面均由Al4Cu9层,AlCu层,Al2Cu层和共晶反应层4层组成;随液-固体积比增大,由于凝固时间延长和铜基体的溶解增加的共同作用,共晶反应层组织出现先粗大后细化的变化。Al/Cu界面层的硬度在140~190HV之间,未呈明显的规律性,随着液-固体积比的增大,Al/Cu双金属材料的剪切强度先增加后减小,并在在7:1时达到最大值(81 MPa),且均从金属间化合物(IMCs)层发生断裂。
关键词:消失模铸造;固-液复合;Al/Cu双金属材料;界面反应层;剪切强度
文章编号:1004-0609(2020)-02-0316-10 中图分类号:TB331 文献标志码:A
随着科学技术的不断发展,单一材料已经难以满足现代工业对于材料综合性能的要求。双金属材料可以结合两种不同材料的特点以获得更加优良的性 能[1],其研究受到越来越多的重视[2-5]。Al/Cu双金属材料能够结合铜的导电导热性好和Al的低密度的优点,从而在满足性能要求的同时达到减轻质量,降低成本的作用,在汽车、电力系统、铠装电缆、轭流线圈、换热和机械等领域具有广泛的应用前景。比如对于工业系统中的Al/Cu双金属过渡接头[6]。同时,在热交换器件上采用Al/Cu双金属材料,能够结合铜合金导热性好的铝合金散热能力强的优点,有效降低系统的质量,同时提高其换热效率[7]。因此,Al/Cu双金属材料的研究正受到越来越多的关注。
目前,Al/Cu双金属材料的制备方法主要可分为固-固复合法和固-液复合法。固-固复合法,常见的有轧制复合[8]、挤出复合[9]、扩散复合[10]以及搅拌摩擦焊[11]等,但是这些方法具有表面处理工艺复杂,工艺流程长和形状尺寸受到限制等不足。固-液复合法,比如结合砂型铸造、金属型铸造、消失模铸造和压铸等铸造方法的复合铸造法[12],通过将熔融的金属液浇铸到固体基材周围,实现两种材料的连接。由于复合铸造方法具有不受形状的限制,具有复合效率高和成本低等优点,在Al/Cu双金属材料的制备方面具有非常大的发展潜力,正越来越受到研究者们的关注。消失模铸造技术作为一种低成本,环保的近净成型铸造技术,具有无需砂芯,表面粗糙度较低,可成型复杂零件等特点。将消失模铸造和复合铸造相结合的消失模复合铸造工艺,与其他复合铸造方法相比具有其独特的优点[13-14]。例如,嵌体易于固定,同时,在浇注过程中,模样热解产生的还原性气氛可对铜嵌体表面起到保护作用。在消失模复合铸造过程中,液-固体积比是一个重要的参数,其改变会对双金属材料的界面状态产生重要的影响[12, 15]。目前通过消失模铸造技术制备Al/Cu双金属材料的研究较少,对于制备过程中的关键参数以及界面形成机制还有待进一步探索。
本文研究了液-固体积比这一重要参数对Al/Cu双金属材料的组织和性能的影响,为获得须知与性能优良的Al/Cu双金属铸件提供借鉴意义。
1 实验
图1所示为消失模铸造固-液复合Al/Cu双金属材料的实验装置图。实验将T2铜棒预置在消失模模样中作为固态嵌体,其尺寸为d 10 mm×50 mm,并采用A356铝合金进行浇注。实验所用合金牌号及成分如表1所列。
表1 实验所用合金材料成分
Table 1 Chemical compositions of experimental alloys

为了获得可靠的Al/Cu双金属界面,嵌入泡沫模型的铜棒需要进行如下表面处理。首先铜棒需用2000号砂纸打磨并在丙酮溶液中超声清洗15 min。随后在常温下用30% H2SO4, 40% HNO3和4 g/L HCl的混合溶液酸洗40 s[16]。经过这一处理过程可去除铜棒表面的氧化层,获得清洁的且具有一定粗糙度的表面。处理完成的铜棒与泡沫模样进行组合,最终获得液固体积比分别为3:1,5:1,7:1和9:1的泡沫模样用于最终的浇注实验。浇注采用A356铝合金通过电阻炉进行熔炼,经过除气及精炼处理后,保温至800 ℃后,在真空度-0.03 MPa条件下,进行浇注。
获得的Al/Cu双金属铸件,从铜棒的中间位置切取试样进行显微组织观察及成分分析,并使用ZwickZ1000 万能实验机对Al/Cu双金属试样进行剪切性能测试。剪切强度(
)使用式(1)计算:
(1)
式中:F为实验过程中的最大载荷;S为铝基体和铜基体的接触面积。使用Zeiss Gemini 300场发射扫描电子显微镜观察Al/Cu双金属试样断口的组织形貌。对于剪切断裂的Al/Cu双金属材料,采用光学显微镜和X射线衍射仪(XRD)对断口进行观察分析。
2 结果与分析
2.1 液-固体积比对Al/Cu界面组织的影响
不同液-固体积比条件下通过消失模铸造固-液复合工艺制备的Al/Cu双金属材料的宏观形貌如图2和图3所示。从图2(a)中可以发现,在液-固体积比为3:1的条件下,Cu棒表面未发生明显熔化变形,且铝合金和铜棒交界处未产生明显的过渡区域。根据图2(b),(c),(d)所示结果可知,Cu棒表面少量区域出现细小的熔化坑,在此条件下Al/Cu之间的结合主要为机械结合的方式。所以在后续的实验分析中主要针对液-固体积比为5:1,7:1和9:1条件下制备的Al/Cu双金属材料进行分析。根据图3所示结果可以看出,随着液-固体积比的增大,铜棒表面开始发生熔化,并且在两基体连接处形成明显的过渡层,但在过渡层中存在较为明显的气孔缺陷,其中,当液-固体积比为9:1时,气孔缺陷最多。同时,随着液-固体积比的增大,Cu棒的熔化率及Al/Cu双金属材料的过渡层的平均厚度逐渐增大,结果如图4所示。
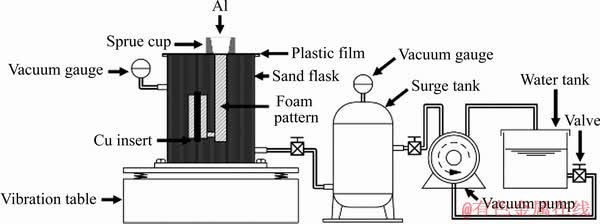
图1 消失模Al/Cu固-液复合实验装置示意图
Fig. 1 Schematic illustration of LFC liquid-solid compound process setup
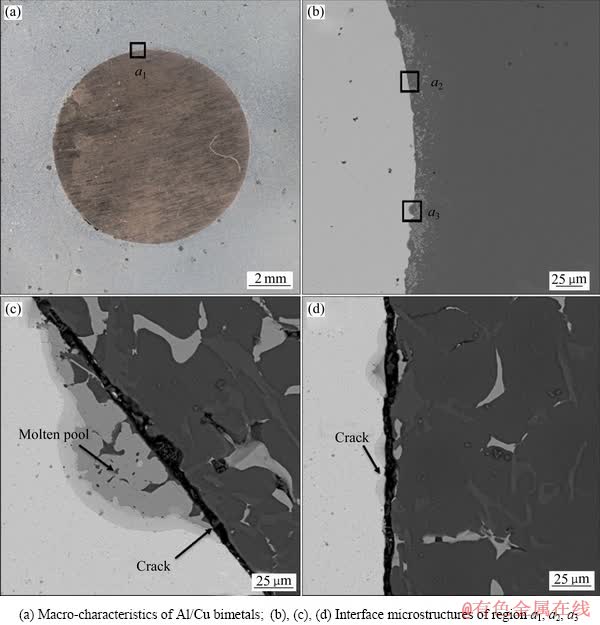
图2 液固体积比3:1时Al/Cu双金属试样界面形貌
Fig. 2 Interface morphologies of Al/Cu bimetal with melt-to-solid volume ratio of 3:1
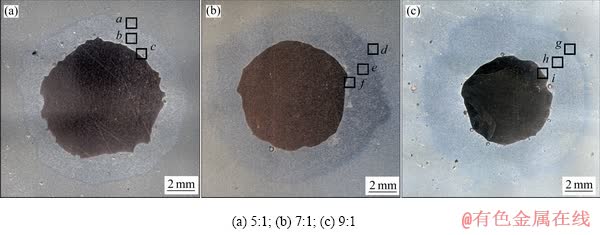
图3 不同液固体积比的Al/Cu双金属试样宏观形貌
Fig. 3 Macro-characteristics of Al/Cu bimetals with different melt-to-solid volume ratios
根据图3所示结果,选择图中字母所示的区域对Al/Cu双金属材料的微观组织进行观察,其结果如图5所示。结果表明,Al/Cu双金属界面由为共晶反应层和金属间化合物(IMCs)层两部分组成。图6所示为不同液固体积比条件下Al/Cu双金属界面区域IMCs层EDS分析结果,并对EDS点分析结果汇总,结果如表2所列。根据EDS分析结果可知,在液固体积比分别为5:1、7:1、9:1条件下,IMCs层均由3层衬度不同的相组成且其成分不随液固体积比的变化而改变,分别是Al4Cu9相、AlCu相和Al2Cu相。而共晶反应层主要由α(Al)、Al2Cu和Si相组成。所以按照从Cu基体到Al基体方向,Al/Cu双金属界面可被分为Layer Ⅰ(Al4Cu9相层),Layer Ⅱ(AlCu相层),Layer Ⅲ(Al2Cu相层)和Layer Ⅳ(共晶反应层)。

图4 不同液固体积比的Al/Cu双金属材料冶金反应层的平均厚度及铜基体熔化率
Fig. 4 Changes of melt-to-solid volume ratio versus thickness of transition zone and the melting rate of Cu matrix
图5(c),(f),(i)所示为不同液-固体积比条件下IMCs层区域的SEM像,可以看出IMCs层的形态随着液-固体积比的增大而发生变化。当液-固体积比为5:1时,Layer Ⅲ呈现出一种不规则的形态,且在部分区域可观察到细小的枝晶状凸起,具有小平面生长的特点,如图5(c)所示。当液-固体积比为7:1时,Layer Ⅲ呈胞状生长形态,如图5(f)所示。其原因可能是因为随着液-固体积比的增大,铜元素扩散更加充分,减小了铜基体表面处的成分过冷度,抑制了Al2Cu相的枝晶生长。而当液-固体积比增大至9:1由于凝固时间延长,使得Layer Ⅲ相厚度增加,如图5(i)所示。
对于Al/Cu界面的共晶反应层即Layer Ⅳ,随着,液-固体积比的增大这一区域的组织没有产生明显的规律性的变化。图5(a), (b)和(d),(e)所示分别为液-固体积比为5:1和7:1时,Layer Ⅳ的微观组织图像,当液-固体积比从5:1增大至7:1时,Al2Cu-α(Al)共晶组织更加粗大,凝固时间的延长可能是导致这一变化的主要因素。但是,当液-固体积比继续增大至9:1时,如图5(h)所示,相比液-固体积比7:1时,Al2Cu-α(Al) 共晶组织出现细化,其原因可能在于,液-固体积比为9:1时,铜元素熔解和扩散更加充分,共晶反应层成分更接近Al/Cu共晶反应成分,促进了共晶反应的发生,使得共晶间距减小。
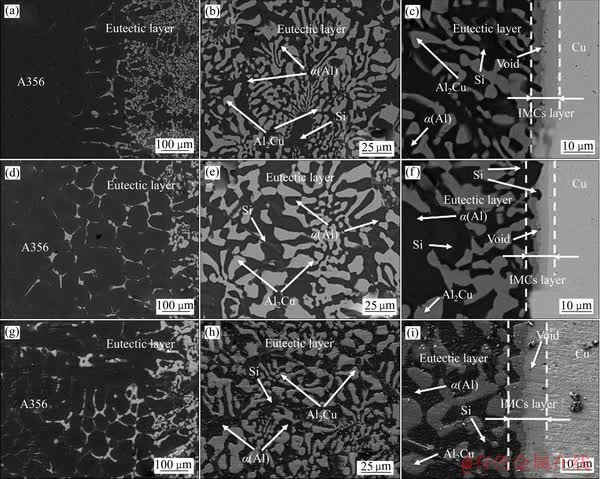
图5 不同液-固体积比条件下Al/Cu双金属界面区域的SEM像
Fig. 5 SEM interfacial images in three characteristic regions with different melt-to-solid volume ratios corresponding to Fig. 3 (a)-(c) 5:1; (d)-(f) 7:1; (g)-(i) 9:1
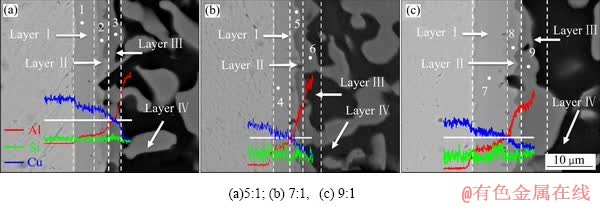
图6 不同液固体积比条件下铜基体表面区域SEM像及Al/Cu双金属界面EDS分析图像
Fig. 6 SEM interfacial microstructures and result of EDS near Cu substrate with different melt-to-solid volume ratio
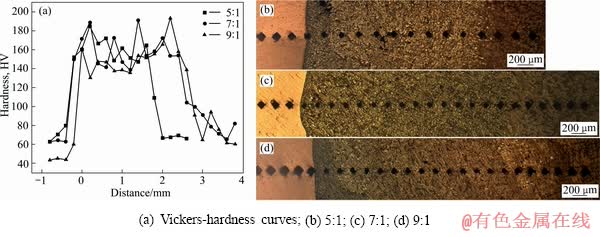
图7 不同液-固体积比条件下Al/Cu界面层的维氏硬度曲线和压痕图像
Fig. 7 Vickers-hardness curves and indentation images with different melt-to-solid volume ratio
表2 Al/Cu双金属材料界面区域EDS分析结果
Table 2 EDS results of Al/Cu bimetals
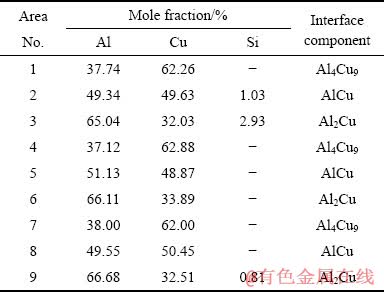
2.2 显微硬度和剪切强度
本实验对不同液-固体积比条件下的Al/Cu双金属材料的维氏硬度和剪切强度进行了测试。在液-固体积比分别为5:1,7:1和9:1条件下,Al/Cu双金属界面的维氏硬度曲线及对应的维氏硬度压痕图像如图7所示。从中可以发现,Al/Cu共晶反应层维氏硬度在140~190HV之间,由于存在大量脆硬的金属间化合物相,硬度较铝、铜基体硬度有大幅度的增加,这一结果与之前的研究结果较为吻合[15]。随着,液-固体积比的增大,共晶反应层的整体硬度未观察到明显的变化。
图8所示为不同液-固体积比条件下Al/Cu双金属材料的剪切强度图像。结果表明液-固体积比为5:1时,Al/Cu双金属材料剪切强度最低,在28 MPa左右。液-固体积比为7:1时,Al/Cu双金属材料剪切强度约为80 MPa,相比液-固体积比为5:1时有大幅的提高。然而当液-固体积比继续增大至9:1时,Al/Cu双金属材料剪切强度出现下降,约为52 MPa。
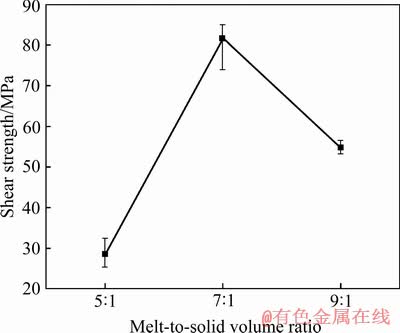
图8 液-固体积比分别5:1、7:1和9:1条件下Al/Cu双金属试样剪切强度
Fig. 8 Average shear strengths of Al/Cu bimetals with different melt-to-solid volume ratio
为了对Al/Cu双金属材料的断裂行为进一步进行分析,用金相显微镜对产生剪切断裂后的Al/Cu双金属材料铜侧断口进行观察,结果如图9所示。从图9中可以在Cu基体上观察到残留的IMCs层,且IMCs层上可观察到明显的裂纹扩展情况,这一观察结果表明Al/Cu双金属材料的剪切断裂发生在IMCs层。通过XRD对液-固体积比为7:1条件下Al/Cu双金属材料剪切断裂断口进行分析可知,Al基体侧断口处的组织主要由α(Al)、Al2Cu、Si和Al4Cu9相组成,而Cu基体侧断口的组织主要由α(Al)、Al2Cu、Si、AlCu和Al4Cu9相组成,结果如图10所示。这一结果进一步证明Al/Cu双金属材料的剪切断的位置在IMCs层位置而不是共晶层。其他液-固体积比条件下的Al/Cu双金属材料的XRD测试也表现出相似的结果。
进一步对Al/Cu双金属材料的剪切试验结果进行分析。根据图3(b)所示图像,在液-固体积比为5:1的条件下,Al/Cu双金属材料只在部分区域形成了冶金结合,仍有较多的机械结合区域,从而导致这一参数下的Al/Cu双金属材料的剪切强度极差,仅有28 MPa左右。而液固体积比增大至7:1后,Al/Cu双金属材料的机械结合区域大幅减小,如图3(c)所示。所以在液-固体积比7:1条件下,Al/Cu双金属材料的剪切性能得到的大幅度的提高达到81 MPa。随着,液-固体积比的进一步增大,Al/Cu双金属材料的剪切性能之所以产生了明显的下降,其原因可能是由于,随着液-固体积比的增大,脆硬的IMCs层的厚度增大,过厚IMCs层使得其力学性能大幅的降低,导致Al/Cu双金材料的剪切强度下降。同时,过渡区域中Cu基体附近气孔缺陷的增多,也是其剪切强度大幅减小的重要因素。
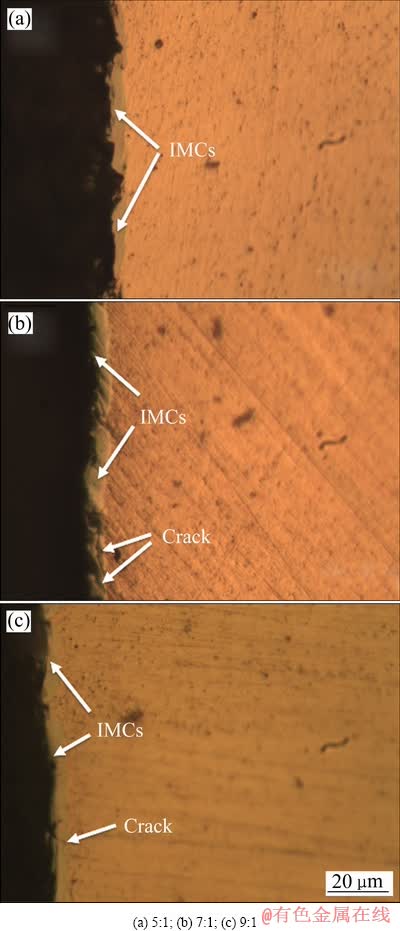
图9 Al/Cu双金属材料Cu基体侧剪切断口形貌
Fig. 9 Optical images of shear-fractured Al/Cu bimetals with different melt-to-solid volume ratio
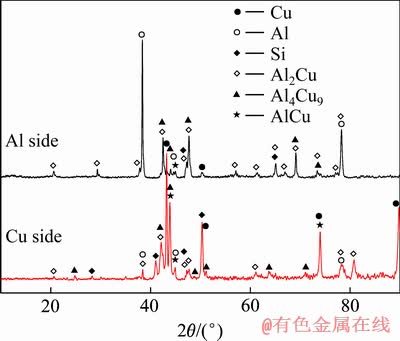
图10 液-固体积比7:1条件下Al/Cu双金属试样剪切断裂断口XRD分析结果
Fig. 10 XRD pattern of fractured Al/Cu bimetal with melt-to-solid volume ratio of 7:1
3 讨论
Al/Cu双金属界面由IMCs层和共晶反应层两部分组成。当熔融的铝液与铜棒相接触,由于Al/Cu之间的相互扩散,在铜棒表面形成低熔点区域,促进了铜棒表面的熔化。在表面形成了铜元素富集区域,在冷却过程中逐渐扩散形成具有铜的浓度梯度的扩散层,最终凝固形成共晶反应层。在凝固过程中由于硅元素具有较高的熔点,凝固初期会有少量初生Si相形成,如图5(b),(e),(h)所示,随后在远离铜基体的铜元素浓度较低区域,α(Al)枝晶首先析出。随着温度继续下降,扩散层中产生共晶反应,形成由α(Al)、Al2Cu和Si相组成的共晶组织。最终形成共晶反应层。
如前所述,在不同液-固体积比条件下IMCs层主要由Al2Cu、AlCu和Al4Cu9层组成。同时,从图5(f)中可知在IMCs层中存在少量的初生Si相,且部分初生Si相同时穿过Al2Cu、AlCu和Al4Cu9层。这一现象表明,在IMCs层的形成的初期,首先在Cu基体表面形核和生长。结合对Al/Cu双金属界面区域EDS分析的结果可以初步判断,Al2Cu相为IMCs层的先析出相。同时,根据图5(c)、(f)和(i),在Al2Cu、AlCu和Al4Cu9层接触的位置可观察到明显的Kirkendall空 洞[17]。这一现象表明AlCu和Al4Cu9层的形成是由于Al2Cu和铜基体之间的铝、铜原子相互扩散导致的。为进一步证实IMCs相的形成次序,采用PROTORIUS等[18]提出有效生成热模型(Effective of heat formation, EHF)对先析出相进行判断并结合吉布斯自由能计算来确定IMCs相的生成次序。根据EHF模型,IMCs相的有效生成热可表示为
(2)
式中:
为IMCs相的生成热;ce为体系中“限制元素”在界面处的有效浓度,一般取体系中最低共晶点温度所对应的“限制元素”的浓度;c0为“限制元素”在IMCs相中的浓度。经计算获得的IMCs相形成的有效生成热图如图11所示,相应得数值如表3所列。结合图11和表3所示结果,可以判断AlCu和Al4Cu9相的生成顺序为,AlCu相先形成,随后Al4Cu9相形成。根据ZENG等[17]和KIM等[19]的研究可知,Kirkendall空洞的存在会抑制金属间相的生长,由于AlCu相界面处存在较多的Kirkendall空洞,如图5(c)、(f)和(i)所示,使得Layer Ⅱ的生长受到抑制,厚度较薄。
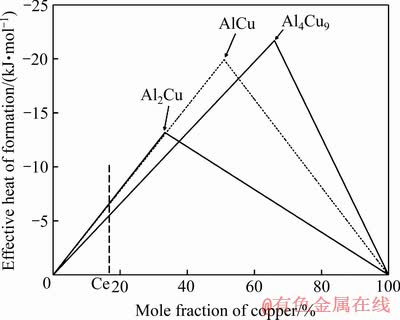
图11 Al/Cu双金属界面区域IMCs相形成的有效生成热图
Fig. 11 Effective heat of formation diagram for IMCs formation
表3 Al/Cu双金属界面区域的IMCs相的成分及其所对应的有效生成热
Table 3 Standard heat of formation ΔH0 and corresponding effective heat of formation ΔH for IMCs
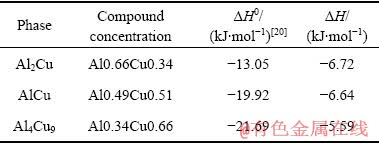
图12所示为消失模铸造Al/Cu双金属材料的界面形成过程示意图,其形成过程可分为如下几个阶段:a) 高温下Al/Cu元素发生相互扩散,铜基体表面形成低熔点成分区域;b) 铜基体表面熔化并形成铜元素富集区;c) 液相中的铜元素进一步扩散,形成一层具有铜的浓度梯度的扩散层;d) 扩散层中初生Si相析出,并在铜元素浓度较低区域析出α(Al)相;e) 铜基体上Al2Cu相开始析出和生长,同时α(Al)枝晶逐渐长大;f) Al2Cu和Cu基体之间Al/Cu原子相互扩散,产生固态相变形成先后形成AlCu和Al4Cu9相。

图12 Al/Cu双金属界面形成过程示意图
Fig. 12 Schematic illustration of formation process of Al/Cu interface
4 结论
1) 液-固体积比为3:1时Al/Cu双金属材料无法形成有效的冶金结合,增大至5:1时,Al/Cu双金属材料连接区域部分位置开始发生冶金结合,若继续增大,Al/Cu双金属材料连接区域全部发生了冶金结合,且界面层的平均厚度逐渐增加。
2) Al/Cu双金属界面可分为IMCs层和共晶反应层两部分。IMCs层主要包括Layer Ⅰ(Al4Cu9相层),Layer Ⅱ(AlCu相层)和Layer Ⅲ(Al2Cu相层)。而Layer Ⅳ(共晶层)主要由α(Al)、Al2Cu和Si相组成。当液-固体积比从5:1增大至7:1,Layer Ⅲ的枝晶生长受到抑制,其形态更接近胞状生长,且共晶反应层中共晶组织更加粗大。液-固体积比继续增大至9:1,共晶反应层中α(Al)-Al2Cu共晶间距减小。
3) Al/Cu双金属材料界面区域,维氏硬度在140~190HV之间,较铝、铜基体部分大幅增加。当Al/Cu双金属材料发生剪切断裂时,断裂首先发生在IMCs层而非共晶反应层,且在液-固体积比7:1的条件下,Al/Cu双金属材料具有81 MPa的最高剪切强度。
4) IMCs层中Al2Cu相首先在铜基体表面形核生长,随后由于Al/Cu元素间的相互扩散,AlCu相和Al4Cu9相先后形成,而共晶反应层则由具有铜元素浓度梯度的扩散层凝固所形成。
REFERENCES
[1] 张红安, 陈 刚. 铜/铝复合材料的固-液复合法制备及其界面结合机理[J]. 中国有色金属学报, 2008, 18(3): 41-47.
ZHANG Hong-an, CHEN Gang. Fabrication of Cu/Al compound materials bysolid-liquid bonding method and interface bonding mechanism[J]. The Chinese Journal of Nonferrous Metals, 2008, 18(3): 41-47.
[2] 李 慧, 龙 萍, 牛永胜, 黄斐荣, 杨 斌. Al/Cu复合材料制备中理论与工艺研究进展[J]. 材料导报, 2016, 7(30): 148-153.
LI Hui, LONG Ping, NIU Yong-sheng, HUANG Fei-rong, YANG Bin. Fabrication of Al/Cu composite: Theoretical and technological progresses[J]. Materials Reports, 2016, 7(30): 148-153.
[3] HU Yuan, CHEN Yi-qing, LI Li, HU Huan-dong, ZHU Zi-ang. Microstructure and properties of Al/Cu bimetal in liquid-solid compound casting process[J]. Transactions of Nonferrous Metals Society of China, 2016, 26: 1555-1563.
[4] LI Xiao-bing, ZU Guo-yin, WANG Pin. Microstructural development and its effects on mechanical properties of Al/Cu laminated composite[J]. Transactions of Nonferrous Metals Society of China, 2015, 25(1): 36-45.
[5] ZHAO Jia-lei, JIE Jin-chuan, CHEN Fei, CHEN Hang, LI Tin-ju, CAO Zhi-qiang. Effect of immersion Ni plating on interface microstructure and mechanical properties of Al/Cu bimetal[J]. Transactions of Nonferrous Metals Society of China, 2014, 24(6): 1659-1665.
[6] 刘 腾, 刘 平, 王渠东. 铜铝双金属复合材料的研究进展[J]. 材料导报, 2013, 27(19): 1-5.
LIU Teng, LIU Ping, WANG Qu-dong. Research Progress on Copper/Aluminum Bimetal Composite[J]. Materials Reports, 2013, 27(19): 1–5.
[7] 汪 鸣, 赵学龙. 海水淡化热交换用铜合金管的应用前景[J]. 世界有色金属, 2009(5): 72-75.
WANG Ming, ZHAO Xue-long. Application prospects of copper alloy tubes for seawater desalination heat exchange[J]. World Nonferrous Metal, 2009(5): 72-75.
[8] SHABANI A, TOROGHINEJAD M R, SHAFYEI A. Effect of post-rolling annealing treatment and thickness of nickel coating on the bond strength of Al-Cu strips in cold roll bonding process[J]. Materials & Design, 2012, 40: 212-220.
[9] SAPANATHAN T, KHODDAM S, ZAHIRI S H. Spiral extrusion of aluminum/copper composite for future manufacturing of hybrid rods: A study of bond strength and interfacial characteristics[J]. Journal of Alloys and Compounds, 2013, 571: 85-92.
[10] ESLAMI P, KARIMI TAHERI A, ZEBARDAST M. A comparison between cold-welded and diffusion-bonded Al/Cu bimetallic rods produced by ECAE process[J]. Journal of Materials Engineering and Performance, 2013, 22(10): 3014-3023.
[11] LI X, ZHANG D, QIU C, ZHANG W. Microstructure and mechanical properties of dissimilar pure copper/1350 aluminum alloy butt joints by friction stir welding[J]. Transactions of Nonferrous Metals Society of China, 2012, 22(6): 1298-1306.
[12] AKBARIFAR M, DIVANDARI M. On the interfacial characteristics of compound cast Al/Brass bimetals[J]. International Journal of Metalcasting, 2017, 11(3): 506-512.
[13] LI G, JIANG W, YANG W, JIANG Z, GUAN F, JIANG H, FAN Z. New insights into the characterization and formation of the interface of A356/AZ91D bimetallic composites fabricated by compound casting[J]. Metallurgical and Materials Transactions A, 2019, 50(2): 1076-1090.
[14] JIANG W, LI G, FAN Z, WANG L, LIU F. Investigation on the interface characteristics of Al/Mg bimetallic castings processed by lost foam casting[J]. Metallurgical and Materials Transactions A, 2016, 47(5): 2462-2470.
[15] LIU G, WANG Q, ZHANG L, YE B, JIANG H, DING W. Effects of melt-to-solid volume ratio and pouring temperature on microstructures and mechanical properties of Cu/Al bimetals in compound casting process[J]. Metallurgical and Materials Transactions A, 2019, 50(1): 401-404.
[16] LIU T, WANG Q, SUI Y, WANG Q, DING W. An investigation into interface formation and mechanical properties of aluminum–copper bimetal by squeeze casting[J]. Materials & Design, 2016, 89: 1137-1146.
[17] ZENG K, STIERMAN R, CHIU T C, EDWARDS D, ANO K, TU K N. Kirkendall void formation in eutectic SnPb solder joints on bare Cu and its effect on joint reliability[J]. Journal of Applied Physics, 2005, 97(2): 024508.
[18] PRETORIUS R, DEREUS R, VREDENBERG A.M, SARIS F.W. Use of the effective heat of formation rule for predicting phase formation sequence in Al-Ni systems[J]. Materials Letters, 1990, 9(12): 6-13.
[19] KIM J Y, YU J. Effects of residual impurities in electroplated Cu on the Kirkendall void formation during soldering[J]. Applied Physics Letters, 2008, 92(9): 092109.
[20] HAIR J, DOWNIE D B. Thermodynamic properties of the Cu-Al system: correlation with bonding mechanisms[C]// Faraday Symposia of the Chemical Society. Royal Society of Chemistry, 1973, 8: 56-63.
Effects of melt-to-solid volume ratio on microstructures and mechanical properties of Al/Cu bimetal interface in lost foam casting
GUAN Feng, JIANG Wen-ming, FAN Zi-tian, LI Guang-yu, JIANG Hai-xiao, ZHU Jun-wen
(State Key Laboratory of Material Processing and Die &Mould Technology, Huazhong University of Science and Technology, Wuhan 430074, China)
Abstract: The effects of the melt-to-solid volume ratio (VR) on microstructure and mechanical properties of the Al/Cu bimetal were studied, and the formation mechanism of the Al/Cu interface was discussed. The results show that the metallurgical bonding cannot be formed when the VR is 3:1. When the VR rises above5:1, the interface zone begins to form in part of the Cu substrate. The interfaces of the Al/Cu bimetals are composed of four different layers: Al4Cu9,AlCu, Al2Cu, and eutectic reaction layer. The hardness of the Al/Cu interface is between 140 and 190 HV. With the increase of the VR, the microstructure of the eutectic reaction layer first becomes coarse, followed by refinement, due to the combination of prolonged solidification time and the increased dissolution of Cu, and the shear strength of the Al/Cu bimetal increases first and then decreases. When the VR is 7:1, it reaches a maximum of 81 MPa, and both of them break from the intermetallic compounds(IMCs) layer.
Key words: lost foam casting; solid-liquid reactions; Al/Cu bimetal; interface; shear strength
Foundation item: Project(2018YFE0313300) supported by the National MCF Energy R&D Program, China; Project (51775204) supported by the National Natural Science Foundation of China; Project(2017CFB488) supported by the Natural Science Foundation of Hubei Province
Received date: 2019-03-13; Accepted date: 2019-09-02
Corresponding author: JIANG Wen-ming; Tel: +86-27-87540094; E-mail: wmjiang@hust.edu.cn
(编辑 王 超)
基金项目:国家磁约束核聚变能发展研究专项资助项目(2018YFE0313300);国家自然科学基金资助项目(51775204);湖北省自然科学基金资助项目(2017CFB488)
收稿日期:2019-03-13;修订日期:2019-09-02
通信作者:蒋文明,副教授,博士:电话:027-87540094;E-mail:wmjiang@hust.edu.cn