Trans. Nonferrous Met. Soc. China 22(2012) s712-s716
Effective parameters on diameter of carbon nanotubes by plasma enhanced chemical vapor deposition
Kang Young JEONG1, Hyun Kyung JUNG2, Hyung Woo LEE1
1. National Core Research Center for Hybrid Materials Solution, Hybrid Graduate School, Pusan National University, Busan 609-735, Korea;
2. Department of Diagnostic Radiology, Inje University College of Medicine, Haeundae Paik Hospital, Busan 612-030, Korea
Received 21 May 2012; accepted 19 October 2012
Abstract: The effective parameters on the diameter of carbon nanotubes (CNTs) by plasma enhanced chemical vapor deposition (PECVD) were presented. Among lots of influential parameters, the effects of the catalytic film thickness and the pretreatment plasma power on the growth of CNTs were investigated. The results show that the size of catalytic islands increases by increasing the thickness of catalytic layer, but the density of CNTs decreases. The pretreatment duration time of 30 s is the optimal condition for growing CNTs with about 50 nm in diameter. By increasing the pretreatment plasma power, the diameter of CNTs decreases gradually. However, the diameter of CNTs does not change drastically from 80 to 120 W. The uniformly grown CNTs with the diameter of 50 nm are obtained at the pretreatment plasma power of 100 W.
Key words: carbon nanotubes; catalytic film thickness; pretreatment plasma power; plasma enhanced chemical vapor deposition
1 Introduction
Among a lot of carbon-based materials, carbon nanotube (CNT) is attracted by many researchers because of their unique electronic, mechanical, thermal, and chemical properties [1-3]. Due to these excellent characteristics, CNTs are known as a promising material for nano-scale sensors and devices such as chemical or biosensors, atomic force microscopy (AFM) tips, fuel cells, and field emitted display (FED) [4-8]. In the implementation of CNTs to the practical applications, the control of their diameters is one of the most important factors for the micro-, and nano-fabrication processes.
Among several methods, chemical vapor deposition (CVD) technique has been widely used for the CNTs growth [9-11]. In particular, the popular method to produce vertically-aligned CNTs having a good uniformity is plasma enhanced chemical vapor deposition (PECVD) [12-14]. CNTs can be synthesized on the substrates coated with a metal catalyst such as Ni, Co, and Fe using PECVD methods. In the CNTs growth by PECVD, there are a lot of influential parameters such as the gas mixing ratio, plasma condition, catalyst thickness, growing temperature [15,16]. Because they are coupled each other, however, it is not easy to control the specific parameter for obtaining well grown CNTs.
In this work, the effects of the catalytic film thickness, pretreatment duration time and pretreatment plasma power on the growth of CNTs were studied. The investigation of the effect of these parameters can give a clue to solve the issues caused in the implementation of CNTs into various CNTs applications.
2 Experimental
Because of several advantages such as low temperature process, high deposition rates and large area synthesis, the CVD process is a good technique for CNTs synthesis. In particular, PECVD can synthesize the CNTs at low temperatures compared to thermal CVD, and the vertically-aligned CNTs can grow by PECVD from the plasma guide. In this work, the hybrid vacuum machine combined the thermal CVD and the PECVD was used to synthesize the vertically aligned CNTs. Figure 1 shows the schematic diagram of the hybrid vacuum system.
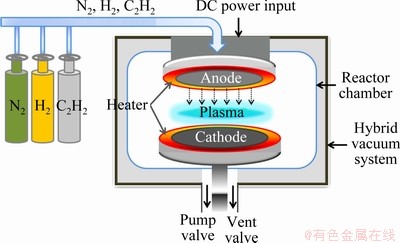
Fig. 1 Schematic diagram of hybrid vacuum system for synthesizing carbon nanotubes
The nickel deposited on SiO2/Si wafer by e-beam evaporator was used as a catalytic film. The 300 nm-thick SiO2 layer playing a role of the diffusion barrier grew on the p-type Si wafer by thermal oxidation in furnace. CNTs grew on the prepared substrates at the growing temperature of 750 °C and the chamber pressure of 600 Pa. For the hydrocarbon source gas, acetylene was used, and the gas mixture with V(NH3):V(C2H2)=4:1 was flushed during the growth process. Among lots of growing parameters, the effects of catalytic film thickness, pretreatment duration time, and pretreatment plasma power were investigated in this work. For various catalytic film thicknesses, 3 nm-, 5 nm- and 7 nm-thick Ni films were prepared. To investigate the effect of pretreatment duration time on the growth of CNTs,
the pretreatment was processed for 10, 20, and 30 s respectively. Through varying the pretreatment plasma power from 20 to 120 W, the effect of the plasma power on the growth of CNTs was investigated. The surface of catalytic film after the pretreatment and the diameters of CNTs were verified by a field emission scanning electron microscopy (FE-SEM, HITACHI S-4800).
3 Results and discussion
In this experiment, the effect of the catalytic film thickness on the growth of CNTs was investigated. Ni catalytic film was pretreated at 600 °C and 266.6 Pa to form the catalytic islands on the surface. Figure 2(a) shows the result of pretreatment with a 3 nm-thick Ni catalytic film. The small islands form on the whole area of the surface. By increasing the catalytic film thickness, the size of island gradually increases, and the density of catalytic islands is reduced, as shown in Figs. 2(b) and (c). It is understood that the Ni film forms into small islands due to the surface tension and the compressive stress caused by the mismatch of the thermal expansion coefficients of SiO2 and Ni. Figures 3(a)-(c) show the FE-SEM images of CNTs grown on Ni layers with different initial thicknesses at the gas mixing volume ratio of 4:1 (V(NH3):V(C2H2)). CNTs were synthesized at the growing temperature of 750 °C and the plasma power of 80 W for 5 min. As shown in Fig. 3(d), the diameter of CNTs increases by increasing Ni film thickness.
Figure 4 shows the results of growing CNTs on Ni thin film according to the pretreatment duration time.

Fig. 2 FE-SEM images of Ni catalytic films with thickness of 3 nm (a), 5 nm (b), and 7 nm (c) after pretreatment, and relationship between diameter of islands and Ni thickness (d)
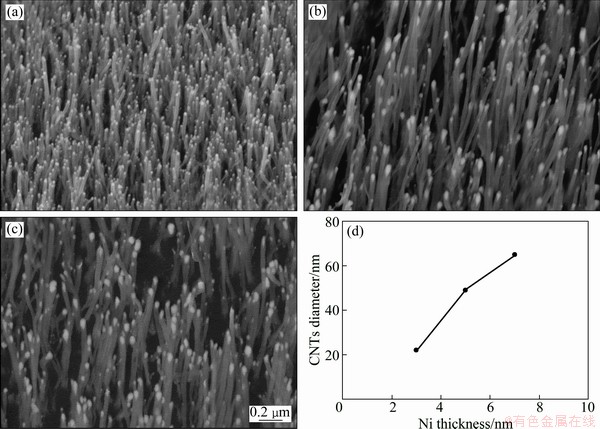
Fig. 3 CNTs grown on Ni layer with 3 nm (a), 5 nm (b), and 7 nm (c) by PECVD, and relationship between diameter of CNTs and Ni thickness (d)
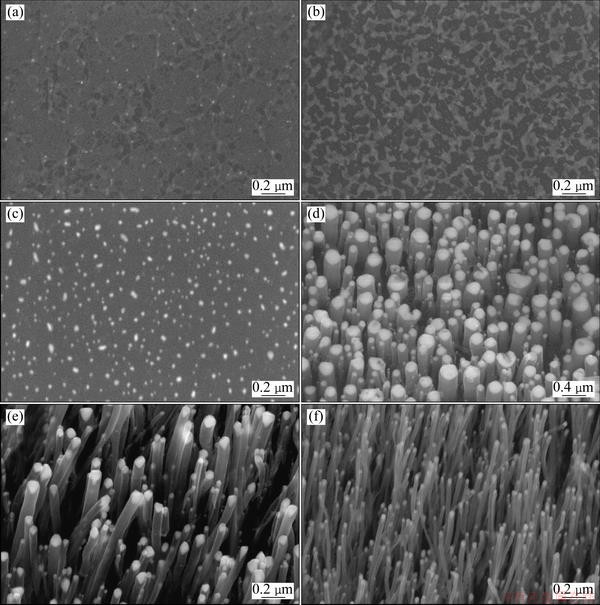
Fig. 4 FE-SEM images of Ni film at pretreatment duration time of 10 s (a), 20 s (b) and 30 s (c), and CNTs grown on pretreated Ni layer for 10 s (d), 20 s (e) and 30 s (f)
During the pretreatment process, the catalytic layer is etched and forms as small islands. By increasing the pretreatment time, the size of catalytic islands is reduced, as shown in Figs. 4(a)-(c). For verifying the effect of pretreatment duration time on the size of the etched catalytic islands, CNTs with the prepared samples were synthesized at the plasma power of 100 W and the growing temperature of 750 °C. Figure 4(d) shows the CNTs grown on the pretreated Ni film for 10 s. Because the pretreatment duration time of 10 s is too short to form small catalytic islands as shown in Fig. 4(a), CNTs with the diameter of over 100 nm were synthesized. For the pretreatment duration time of 30 s, the diameter of CNTs is around 50 nm. After the pretreatment for several minutes, however, CNTs are not synthesized because the catalytic layer is etched away by the long etching process.
The plasma power is one of the most effective parameters to synthesize CNTs using PECVD. The effect of pretreatment plasma power on the growth of CNTs was investigated in this work. Figure 5 shows the CNTs grown at pretreatment plasma powers of 20, 60, 80, 100 and 120 W. At the plasma power of 20 W, the diameter of CNTs is around 110 nm as shown in Fig. 5. It may be caused by the weak plasma power that may lead to the formation of the large sized catalytic islands. CNTs were synthesized under the same plasma power as the pretreatment plasma power. By increasing the plasma power, as shown in Figs. 5(a)-(c), the diameters of CNTs decrease. At the plasma power of 80 W, CNTs with the diameter of 50 nm grow. By increasing the plasma power from 80 to 120 W, however, the diameters of CNTs do not change drastically, as shown in Fig. 5(f). At the plasma powers of 80 and 120 W, the CNTs are kinked because of a little weak and a little strong power respectively as shown in Figs. 5(c) and (e). At the plasma power of 100 W, the vertically aligned CNTs with the diameter of 50 nm and good straightness are obtained.
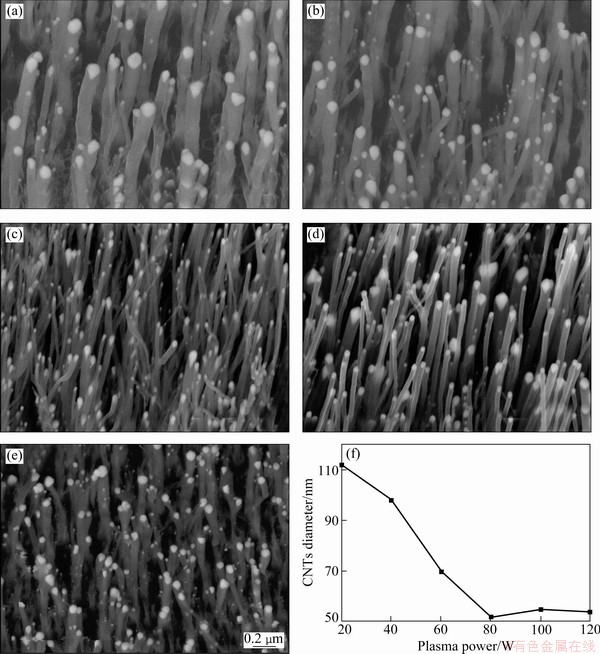
Fig. 5 CNTs grown at pretreatment plasma powers of 20 W (a), 60 W (b), 80 W (c), 100 W (d) and 120 W (e), and relationship between diameter of CNTs and pretreatment plasma power (f)
4 Conclusions
1) The effects of the catalytic film thickness and the pretreatment plasma power on the growth of CNTs were investigated by PECVD. Ni catalytic films with thickness of 3, 5 and 7 nm were pretreated at 600 °C to form the catalytic islands.
2) By increasing the thickness of catalytic layer, the size of island increases gradually, and the density of catalytic islands decreases.
3) For verifying the effect of the pretreatment duration time on the diameter, CNTs grow at the plasma power of 100 W and pretreatment duration time 10, 20 s, and 30 s. 10 s is too short to form small size catalytic islands, and the duration time of 30 s is proper to synthesize the well grown CNTs with the diameter of 50 nm. By increasing the pretreatment plasma power up to 80 W, the diameter of CNTs decreases gradually. However, the diameter of CNTs does not change drastically at pretreatment plasma power from 80 to 120 W. The uniformly grown CNTs with the diameter of 50 nm are obtained at 100 W.
References
[1] DALTON A B, COLLINS S, RAZAL J, MUNOZ E, EBRON V H, KIM B G, COLEMAN J N, FERRARIS J P, BAUGHMAN R H. Continuous carbon nanotube composite fibers: Properties, potential applications, and problems [J]. Journal of Materials Chemistry, 2004, 14(1): 1-3.
[2] CADEK M, COLEMAN J N, BARRON V, HEDICKE K, BLAU W J. Morphological and mechanical properties of carbon-nanotube- reinforced semicrystalline and amorphous polymer composites [J]. Applied Physics Letters, 2002, 81(27): 5123-5225.
[3] COLEMAN J N, KHAN U, BLAU W J, GUN’KO Y K. Small but strong: A review of the mechanical properties of carbon nanotube- polymer composites [J]. Carbon, 2006, 44(9): 1624-1652.
[4] RUEKES T, KIM K, JOSELEVICH E, TSENG G Y, CHEUNG C, LIEBER C M. Carbon nanotube based nonvolatile random access memory for molecular computing [J]. Science, 2000, 289(5496): 94-97.
[5] KONG J, FRANKLIN N R, ZHOU C, CHAPLINE M G, PENG S, CHO K, DAI H. Nanotube molecular wires as chemical sensors [J]. Science, 2000, 287(5453): 622-625.
[6] LEE H W, KIM S H, KWAK Y K, HAN C S. Nanoscale fabrication of a single multiwalled carbon nanotube attached atomic force microscope tip using an electric field [J]. Review of Scientific Instruments, 2005, 76: 046108.
[7] AKITA S, HISHIJIMA H, NAKAYAMA Y, TOKUMASU F, TAKEYASU K. Carbon nanotube tips for a scanning probe microscope: Their fabrication and properties [J]. Journal of Physics D: Applied Physics, 1999, 32(9): 1044-1049.
[8] BACHTOLD A, HADLEY P, NAKANISHI T, DEKKER C. Logic circuits with carbon nanotube transistors [J]. Science, 2001, 294(5545): 1317-1320.
[9] KONG J, CASSELL A M, DAI H. Chemical vapor deposition of methane for single-walled carbon nanotubes [J]. Chemical Physics Letters, 1998, 292(567): 567-574.
[10] PAN Z W, XIE S S, CHANG B H, SUN L F, ZHOU W Y, WANG G. Direct growth of aligned open carbon nanotubes by chemical vapor deposition [J]. Chemical Physics Letters, 1999, 299(1): 97-102.
[11] LEE C J, PARK J. Growth model of bamboo-shaped carbon nanotubes by thermal chemical vapor deposition [J]. Applied Physics Letters, 2000, 77(21): 3397-3399.
[12] MEYYAPPAN M. A review of plasma enhanced chemical vapour deposition of carbon nanotubes [J]. Journal of Physics D: Applied Physics, 2009, 42(21): 213001.
[13] BELL M S, TEO K B K, LACERDA R G, MILNE W I, HASH D B, MEYYAPPAN M. Carbon nanotubes by plasma-enhanced chemical vapor deposition [J]. Pure Applied Chemistry, 2006, 78(6): 1117-1125.
[14] QIN L C, ZHOU D, KRAUSS A R, GRUEN D M. Growing carbon nanotubes by microwave plasma-enhanced chemical vapor deposition [J]. Applied Physics Letters, 1998, 72(26): 3437-3439.
[15] CHOI Y C, SHIN Y M, LEE Y H, LEE B S, PARK G, CHOI W B, LEE N S, KIM J M. Controlling the diameter, growth rate, and density of vertically aligned carbon nanotubes synthesized by microwave plasma-enhanced chemical vapor deposition [J]. Applied Physics Letters, 2000, 76(17): 2367-2369.
[16] CHHOWALLA M, TEO K B K, DUCATI C, RUPESINGHE N L, AMARATUNGA A J, FERRARI A C, ROY D, ROBERTSON J, MILNE W I. Growth process conditions of vertically aligned carbon nanotubes using plasma enhanced chemical vapor deposition [J]. Journal of Applied Physics, 2001, 90(10): 5308-5317.
(Edited by CHEN Wei-ping)
Foundation item: Project supported by a 2-Year Research Grant of Pusan National University; Project (2011-0006257) supported by National Core Research Center (NCRC) Program through the National Research Foundation of Korea funded by the Ministry of Education, Science and Technology
Corresponding author: Hyung Woo LEE; Tel: +82-51-5103160; E-mail: LHW2010@pusan.ac.kr
DOI: 10.1016/S1003-6326(12)61792-0