
Effect of Ce-rich misch metal addition on squeeze cast microstructure and mechanical properties of AZ81 alloy
LIAO Hui-min(廖慧敏)1, LONG Si-yuan(龙思远)1, 2, GUO Cun-bao(郭存宝)1, ZHU Zhi-bing(朱志兵)1
1. College of Mechanical Engineering, Chongqing University, Chongqing 400030, China;
2. National Engineering Research Center for Magnesium Alloys, Chongqing 400030, China
Received 12 June 2008; accepted 5 September 2008
Abstract: The effect of cerium-rich misch metal addition on the microstructure and properties of squeeze cast magnesium alloys AZ81 was empirically investigated. The results indicate that the addition of cerium-rich misch metal modifies the microstructure gradually. With the increase of the RE addition, the amount of Mg17Al12 decreases while that of Al11(RE)3 increases, accompanied by grain refinement. When the addition reaches 1.5%, the grain refinement becomes obvious. However, when the addition exceeds 2.0%, Al11(RE)3 phase coarsens into rod shape and the grain size increases. The tensile properties of the AZ81 at both room temperature and 150℃ increase with the addition, and reach their optimal values with the addition of 1.5%. Further increase of the addition to above 2.0% decreases the tensile properties considerably. The tensile fracture of the alloy is characterized by the cleavage of the brittle second phases and ductile dimples of the matrix.
Key words: cerium-rich misch metal; AZ81 alloy; microstructure; mechanical properties
1 Introduction
As the lightest commercial alloy, Mg alloy plays a more and more important role in automobile industry for its low density, high specific strength, outstanding damping capability and specific stiffness, good casting capability and machinability, and reasonable heat conductivity[1-2]. Mg alloys have already found many applications in power train, instrument panels, seat framework, steering wheels, steering columns, etc[3]. At present, a lot of research effort has been devoted to the development of high strength cast Mg alloys, but no alloys suitable to squeeze casting in mass production scale are commercially available. For instance, AE and AS series alloys have moderate high temperature strength, but are prone to oxide and adhere to metallic mould and, therefore, not suitable for squeeze casting. QE, ZE and WE series have outstanding high temperature mechanical properties, but they are expensive and have very poor squeeze casting capability. Therefore, they are only suitable for low pressure casting, such as sand mould gravity casting. Currently, the poor strength at elevated temperature, cost and processing capability remain to be the main bottlenecks to civil application of the Mg alloys, especially such applications as wheels, crankshaft, and transmission house, where their service temperature is just slightly above 120 ℃.
As far as their cost, processing capability, mechanical performance are concerned, further improvement of the mechanical properties of AZ series cast alloys for both room temperature and elevated temperature applications attracts attention of Mg research community in recent years[4].
RE is a group of alloying elements with the most acknowledged strengthening potential for elevated temperature applications. The research on the effect of RE addition on the strength of most commercial AZ series Mg alloys at both room and elevated temperatures has been carried out worldwide[5]. The results obtained show that β phase of low melting temperature forms preferentially on the grain boundaries, leading to a decreased strengthening effect[6-7]. Furthermore, the excessive reduction of Al content will reduce the casting capability of the alloy. However, how the RE addition affects microstructure and tensile properties remains not quantified. The aim of the present study is, therefore, to have an quantified insight into the effect of the Ce-rich misch RE addition on the microstructure and tensile properties of AZ81 in industrial condition.
2 Experimental
The raw materials used are AZ91D, pure Mg, pure Zn and Ce-rich misch RE metal with chemical composition of 65% Ce, 27%-29% La, 6%-8% Nd and a small percentage of Pr. The RE metal was cut into small pieces with an approximate size of 150 mm2×10 mm. N2+0.2% SF6 gas mixture was used to prevent the melt from oxidation and ignition during alloy preparation. A 120 kg capacity electric resistant furnace was used for melting, and a 160 t cold-chamber die-casting machine was used to net-shape cast dog-bone tensile specimens with a guage length of 25 mm and a diameter of 5 mm. The geometry of the specimens was in compliance with Chinese National Standard GB/T228—2002.
During alloy preparation, a designed mass of AZ91D was put into the crucible, and pure Mg and pure Zn were added after the AZ91D ingots were completely melted and the melt bath temperature reached 720 ℃ in order to adjust melt chemistry to the composition compliant with AZ81. To ensure a uniform melt chemistry, the Ce-rich misch metal blocks were slowly merged into and hanged in the middle of the melt bath, followed by gentle stirring until they were completely dissolved. Then, the temperature of melt bath was held at 690 ℃ for 15 min. The die preheating temperature was 220℃. During squeeze casting, the melt was poured into the injection chamber and cast with a speed of 1 m/s, followed by squeeze pressurization under 100 MPa.
The samples with 1.0%, 1.5%, 2.0%, 2.5% and 3.0% (mass fraction) of Ce-rich misch RE addition were cast under identical processing conditions. The chemical composition of the alloys is summarized in Table 1.
Specimens for microscopy were prepared from the grip sections of the net-shape cast tensile test bars. After mechanical cutting, grinding, polishing and etching with 3% natal (nitric-acid and alcohol), the microstructures of the alloys were analyzed by optical microscopy. The tensile tests were performed at both room temperature and 150 ℃ on a computerized WDW3100 universal material testing machine at a tensile speed of 1 mm/min. The temperature precision for the tests at 150 ℃ was controlled within ±2 ℃. The composition of the second phases and tensile fracture morphology were analyzed with SEM equipped with energy spectrometer.
3 Results and discussion
3.1 Effect of RE addition on solidification micro- structure of AZ81
The microstructures of the AZ81 with different RE addition are given in Fig.1. The microstructure of the alloys consists of α-Mg grains, with β-Mg17Al12 eutectics decorating on the grain boundaries. The Al11(RE)3 RE containing phase appears at the grain boundaries when the addition is below 1.0%, and then starts to precipitate within the matrix grains[8].
The Al11(RE)3 phase mainly possesses a refined granular morphology when the RE addition is below 1.5%, as shown in Figs.1(b), (c) and (d), and starts to coarsen with further increase of the RE addition. The β-Mg17Al12 eutectics are dispersed by Al11(RE)3 phase and grain refining effect of RE addition[9-10].
Refinement on the solidification microstructure is not notable when the RE addition is below 1.0%. When the RE addition is between 1.5%-2.0%, the refining effect becomes significant, leading to a reduction of average grain size from 30 mm in AZ81 to 12 mm in AZ81+1.5RE. However, the refining effect fades when the RE addition exceeds 2.0%. Considering the obvious appearance of Al11(RE)3 in eutectics on grain boundary, this observation indicates that the well dissolved Ce-rich misch metal does not promote nucleation in solidification of AZ81 melt[11].
The well refined microstructure in AZ81+1.5RE and AZ81+2.0RE can be attributed to the preferential partition behavior of rare earth elements in solidification of Mg melt. It is well-known that the solubility of Ce and La in α-Mg is very low[12]. When Ce-rich misch metal is dissolved in AZ81, Ce and La atoms are pushed forward by the solidified α-Mg growth front, leading to a progressive concentration of Ce and La in the liquid phase in front of the solid/liquid interface during solidification. The solute enrichment results in a pronounced constitutional supercooling at the growth front, leading to the formation of the fine solidification microstructure[13-14].
Table 1 Chemical composition of alloys (mass fraction, %)
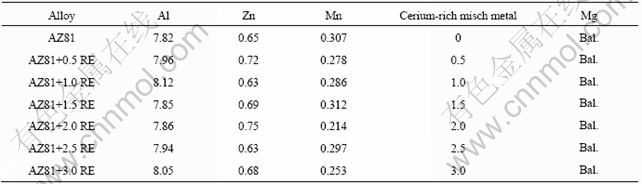
Fig.1 Microstructures of AZ81 with different rare earth addition: (a) AZ81; (b) AZ81+ 0.5RE; (c) AZ81+1.0RE; (d) AZ81+1.5RE; (e) AZ81+2.0RE; (f) AZ81+2.5RE; (g) AZ81 + 3.0RE
However, when the RE addition exceeds its maximum solubility in the melt in the solidifying temperature range, Al11(RE)3 starts to nucleate and grow along with or even prior to the primary α-Mg phase, leading to the appearance of coarse Al11(RE)3 embedded in α-Mg primary grain. The precipitation reduces the concentration of RE in the solidified liquid phase, as well as constitutional supercooling degree in the melt in growth front. Consequently, the microstructure refinement effect of the RE addition decreases as observed above[15].
3.2 Effect of Ce-rich misch metal addition on tensile properties of AZ81
The effects of RE addition on the tensile properties of AZ81 at both room temperature and 150 ℃ are summarized in Fig.2. The curves in Fig.2 show that the RE addition improves the tensile properties of the AZ81 dramatically.
As illustrated in Fig.2(a), with the increase of RE addition from 0 to 1.5%, the tensile strength and yield strength are gradually raised from 223 and 132 MPa to their maximum values of 272 and 153 MPa, respectively. Following the same trend, the elongation increases sharply from 7.6% to its maximum value of 11.5%, 53% higher than that of AZ81. Further increase of RE addition from 2.0% to 3.0% brings the decrease of the tensile strength, yield strength and elongation significantly.
As Fig.2(b) shows, the RE addition improves the tensile properties of AZ81 at 150 ℃ with the same trend under room temperature. The tensile properties reach their maximum values of σb=164 MPa, σ0.2=137 MPa and δ=13.4% with 1.5% of RE addition.
The above relationship between tensile properties and RE addition can be interpreted by the effect of RE on the solidification microstructure as follows[16]. When the RE addition is little, the RE is mainly consumed to purify the melt. The surplus RE in the melt crystallizes as Al11(RE)3 in the eutectic phases on the grain boundary, contributing to the improvement of tensile properties to a limited extent. With the increase of RE addition, more and more RE dissolves in the melt and refines the solidification microstructure via enhancement of crystal growth supercooling, leading to a enhanced tensile properties. However, further increase of RE addition leads to the appearance of coarse primary Al11(RE)3 in the microstructure, resulting in the decrease of tensile properties because of the reduced refining effect and the brittle nature of Al11(RE)3.
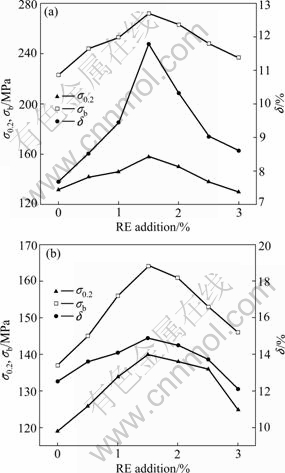
Fig.2 Relationship between tensile properties and RE addition in AZ81: (a) Room temperature; (b) 150 ℃
3.3 Effect of RE addition on tensile failure behavior of AZ81
SEM fractographs of the tensile specimens tested at room temperature are given in Fig.3. As these images show, the room temperature tensile fractures of the specimens with different RE additions are all characterized by the cleavage failure of the second phases and plastic dimples of Mg matrix phase. However, the AZ81+1.5RE specimen possesses fracture featured by a refined grain size, while the AZ81 alloy produces a fracture of coarser grain and the AZ81+3.0RE gives a fracture characterized by large brittle Al11(RE)3, consis-tent with the results of optical microscopy and tensile tests.
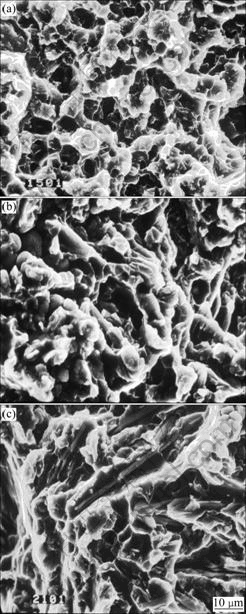
Fig.3 Tensile fracture morphologies of tensile specimens at room temperature: (a) AZ81; (b) AZ81+1.5RE; (c) AZ81+ 3.0RE
The SEM micrographs of the tensile fractures of AZ81, AZ81+1.5RE and AZ81+3.0RE alloys at 150 ℃ are shown in Fig.4. As these images show, except for the features caused by the variation of the grain size, all three specimens fail by Mg matrix plastic deformation, leading to fractures featured by ductile dimples of matrix along the grain boundaries. The lack of brittle cleavage of Al11(RE)3 on AZ81+3.0RE fracture not only indicates that, even with a considerable amount of Al11(RE)3 phase in the primary grain, the alloy still fails mainly via matrix plastic deformation, instead of brittle breakage of Al11(RE)3 under tensile loading, but also hints that Al11(RE)3 phase contributes little to the high temperature strengthening effect. Instead, the matrix refinement and purification play a more significant role in strengthening at 150 ℃.
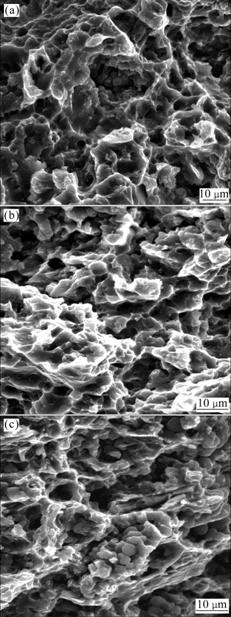
Fig.4 Tensile fracture morphologies of tensile specimens at 150 ℃: (a) AZ81; (b) AZ81+1.5RE; (c) AZ81+3.0RE
It is, therefore, concluded that the addition of 1.5% Ce-rich misch metal is beneficial to AZ81 in the light of solidification microstructure refinement and tensile properties improvement at both room temperature and 150 ℃.
4 Conclusions
1) The RE addition modifies the solidification microstructure of AZ81 and results in the formation of Al11(RE)3 phase in AZ81. Optimal microstructure is featured by significantly refined grain size and Al11(RE)3 phase when RE addition is 1.5%.
2) With 1.5% RE addition, the tensile strength and yield strength of AZ81 at both room temperature and 150 ℃ are gradually raised to the maximum value.
3) AZ81 with different RE addition fails via plastic deformation of Mg matrix phase and brittle breakage of the second phase and Al11(RE)3 at room temperature, while fails at 150 ℃ mainly via plastic deformation of Mg matrix phase along the grain boundaries.
Acknowledgement
Sincere thanks are given to Chongqing Magnesium Science & Technology Co. Ltd. for its support in specimen manufacturing.
References
[1] POLMEAR I. Magnesium alloys and application [J]. Materials Science & Technology, 1994, 10(1): 1-16.
[2] IFEANYI A, YASUHIRO G, ATSUYA S, SHIGEHARU K, YO K, SUGURU T, TAKETOSHI I. Effect of substituting cerium-rich mischmetal with lanthanum on high temperature properties of die-cast Mg-Zn-Al-Ca-RE alloys [J]. Materials Science and Engineering, 2004, A380: 93.
[3] KIM J M, PARK B K, SHIN K, JUN J H, KIM K T, JUNG W J. Development of Mg-Al-Zn based diecasting alloys for elevated temperature applications [J]. Materials Science Forum, 2005, 475/479: 525-528.
[4] AGHION E, ELIEZER D. Magnesium alloys (science, technology and applications) [M]. Haifa: The Israeli Consortium for the Development of Magnesium Technology, 2004.
[5] BENEDY K, JOSEPH C. Magnesium advances in automotive applications [J]. Light Metal Age, 2005, 63(3): 36-38.
[6] MORDIKE B. Development of highly creep resistant magnesium alloys [J]. Journal of Materials Processing Technology, 2001, 117: 391-394.
[7] KIM J M, PARK B K, JUN J H, KIM K T, JUNG W J. Microstructure and properties of Mg-Al based casting alloys modified with minor alloying elements [J]. Materials Science Forum, 2005, 488/489: 147-150.
[8] YU Fan, WU Guo-hua, ZHAI Chun-quan. Influence of cerium on the microstructure, mechanical properties and corrosion resistance of magnesium alloy [J]. Materials Science and Engineering A, 2006, 433: 208-215.
[9] SHEPELEVA L, BAMBERGER M. Microstructure of high pressure die cast AZ91D modified with Ca and Ce [J]. Materials Science and Engineering A, 2006, 15(6): 312-317.
[10] WU An-ru, XIA Chang-qing, WANG Jie-wen. Distribution, evolution and the effects of rare earths Ce and Y on the mechanical properties of ZK60 alloys [J]. Journal of University of Science and Technology Beijing, 2006, 13(5): 424. (in Chinese)
[11] ZHENG Wei-chao, LI Shuang-shou, BIN TANG, ZENG Da-ben. Effects of mischmetal on microstructure and mechanical properties of AZ91D magnesium alloy [J]. Acta Metall Sinica, 2006, 42(8): 835-842. (in Chinese)
[12] ZHONG Yang, LI Jian-ping, LI Gao-hong, YANG Jue-ming. Effect of antimony and Ce-rich mischmetal additions on as-cast micro- structure and mechanical properties of AZ91 alloy [J]. Materials Science and Engineering, 2005, 488/489(1): 219-222.
[13] WANG Ming-xing, ZHOU Hong, WANG Lin. Effect of yttrium and cerium addition on microstructure and mechanical properties of AM50 magnesium alloy [J]. Journal of Rare Earths, 2007, 25: 233-237.
[14] CHEN Zhen-hua. Heat-resistant magnesium alloy [M]. Beijing: Chemical Industry Press, 2006. (in Chinese)
[15] KIM Y W. Microstructures and mechanical properties of rapidly solidified Mg-Al-Zn-MM alloys [J]. Journal of Materials Science and Technology, 2008, 24(1): 89-92.
[16] LIU Sheng-fa, HUANG Shang-yu, XU Ping. Influence of cerium addition on as-cast microstructure refinement of AZ91 magnesium alloy [J]. Acta Metall Sinica, 2006, 42(4): 443-448. (in Chinese)
(Edited by YANG Bing)
Foundation item: Project(2007CB613702) supported by the National Basic Research Program of China; Project(2006BA104B04-2) supported by Chongqing S&T Research Program, China
Corresponding author: LONG Si-yuan; Tel: +86-23-65112626; E-mail: siyuan_long@yahoo.com