Trans. Nonferrous Met. Soc. China 22(2012) s389-s394
Deformation behavior of 5A06 aluminum alloy sheet for rapid gas forming at elevated temperature
FAN Xiao-bo, HE Zhu-bin, YUAN Shi-jian
National Key Laboratory for Precision Hot Processing of Metals, Harbin Institute of Technology, Harbin 150001, China
Received 28 August 2012; accepted 25 October 2012
Abstract: The aim of this work is to investigate the deformation behavior of commercial 5A06 aluminum alloy sheet for rapid gas forming at elevated temperature. So-called cup-shaped workpieces were formed under different conditions. The temperatures ranged from 325 °C to 500 °C. The gas pressure was 2.5 MPa and 4.0 MPa, with different duration time from 8 s to 120 s. The profiles, corner radius and thickness distribution of the formed specimens were measured and analyzed. The results show that the formability of the sheet is improved by increasing the testing temperature, duration time and gas pressure. Corner radius changes obviously before the temperature attains to 450 °C or within 30 s, and then trends to the minimum value (about 2.0 mm) gently. Higher forming gas pressure can be used to reduce the duration time at the appropriate temperature ranging from 400 °C to 500 °C. However, the sheet needs enough deformation time to conform final corner filling when the gas pressure is 4.0 MPa. The minimum wall thickness appears at the transition zone between corner and bottom.
Key words: 5A06 Al alloy sheet; quick plastic forming; rapid gas forming; formability; deformation behavior; thickness distribution
1 Introduction
Along with the expansion of the energy consumption pressure, weight reduction becomes the urgent matter, which can be realized by optimized structural design and usage of light materials, such as aluminum and magnesium alloys. In recent years, the demand for aluminum alloys has increased in response to a growing need for lightweight structural metals, which can be found to gain more and more applications in aerospace and automobile industry [1-3]. However, complex shaped components, particularly those made from light-weight alloy sheet like aluminum and magnesium, are extremely difficult to form by traditional cold forming due to its poor formability at room temperature, which often acts as the main obstacle for the wide application of these materials.
Efforts have been made to improve the formability of these materials by forming at elevated temperature. Loading force decreases and formability increases with forming temperature increasing. The deformation behaviors of many light-weight alloy sheets have been analyzed and reported at elevated temperature [4-8]. Mechanical characteristics of Al5052 and Al6061 sheets were characterized using both tensile and bulge testing methods at temperature levels up to 300 °C [9]. The forming behavior of a commercial sheet of AZ31B magnesium alloy at elevated temperatures is investigated by free bulging test and analyzing the ability of the sheet in filling a closed die by SORGENTE et al [10].
Nowadays, special attention has been paid on the forming of light-weight materials with high strain rate at elevated temperature. The commercial application of high strain rate superplasticity (HSRS) has started to achieve medium or even large volume production, such as quick plastic forming (QPF). General Motors developed the QPF process as a hot (sheet) blow forming technology to enable complex aluminum shapes to be manufactured at automotive volumes of up to 100000 per year, which has been successfully implemented for automotive lift-gates and deck-lids with complex shapes [11,12]. Mass savings of 5.1 kg for front door and 4.7 kg for rear door were obtained in the prototype aluminum doors relative to their steel counterparts by SCHROTH et al [13].
However, the development of a suitable material and the subsequent characterization of this material under the proper conditions are critical to the success of the HSRS technology. Material preparation is much more restrictive: controlled microstructures with very small mean grain size are generally required [14]. The cost of material becomes more important as the production volume increases. Therefore, efforts have been made to investigate the feasibility of forming commercial materials at high strain rate. The newly proposed process was called rapid gas forming (RGF) [15].
The basic idea of this novel process is to heat quickly the metal by hot mold to the appropriate temperature, at which its formability is expected to be the most optimal, hereafter to form by using high hyperbaric gas within several seconds. The provided materials are often used directly without special requirement or treatment on microstructure. Therefore, the deformation behaviors at elevated temperature of these materials at high strain rate are different from those in HSRS process. However, few research works and results have been reported about how to choose the process parameters, such as forming temperature, duration time and gas pressure. In this work, the effect of temperature, duration time and gas pressure on the deformation behavior of 5A06 sheet will be investigated in a set of forming of round cup tests. The profiles, corner radius and thickness distribution will be measured and analyzed to illustrate directly the deformation behavior of sheet under different conditions.
2 Experimental
As mentioned above, the deformation behaviour of sheet for rapid gas forming would be investigated by forming of round cup test at elevated temperatures, therefore, special set-up was designed and manufactured, and experimental procedure was formulated under different conditions.
2.1 Experiment set-up
Figure 1 shows the schematic diagram of round cup test. Forming of cup-shaped workpiece was adopted to investigate the effect of process parameters on deformation behaviour. The sheet was placed in the dies and sealed by plate compressed in the platform with load of 5 t. The mould was heated by the externally surrounded heating plate. When the mould was heated to a target temperature, it can act as a heat maintainer to conformed fluctuation of temperature during testing, and the temperature was PID controlled. Good result is that the sheet has the same temperature as mould, which reduces the troubles caused by direct measurement on the temperature of sheet used. The inner diameter of the die was 52.0 mm. The height of the cup was 15.0 mm.
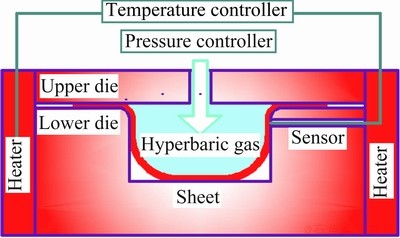
Fig. 1 Schematic diagram of round cup test
2.2 Experiment procedure
As is known that the sheet is formed for QPF at a temperature ranging from about 400 °C to 500 °C within several minutes [12], RGF aims at lager mass production realized for commercial aluminum alloy. Deformation behavior of 5A06 sheet affected by three key process parameters (forming temperature, duration time and gas pressure) would be investigated to provide the foundation of lager mass production by a set of forming of round cup tests. The experimental scheme is given in Table 1. The sheet specimen tested was 100 mm in length, 100 mm in width, and 1.0 mm in thickness.
Table 1 Experimental scheme for round cup tests
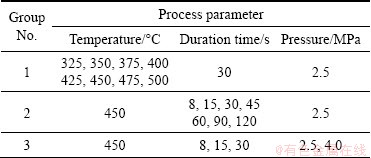
3 Results and discussion
Figure 2 shows the cup-shaped workpieces obtained under different conditions. Profile, corner radius, and thickness distribution were measured to describe quantitatively the deformation behavior, as shown in Fig. 3.
3.1 Profile and corner radius
Figure 4 shows the profile and corner radius of the cup-shaped workpieces under different temperatures and duration time. The sheet busted freely from 325 °C to 375 °C, while the forming pressure was 2.5 MPa and duration time was 30 s, as shown in Fig. 4(a). With temperature increasing, the sheet started to contact with the bottom of the die firstly and then expanded to the surrounding to realize small corner filling. Smaller corner radius can be achieved with temperature increasing. The smallest corner radius was just about 2.0 mm at 500 °C.
The effect of duration time is given in Fig. 4(b). The similar observation is made for increasing duration time. When the given forming temperature was 450 °C and pressure was 2.5 MPa, about 3.0 mm corner radius can be achieved within 60 s. However, the corner radius did not decrease obviously with the duration time increasing. It can be seen clearly that some duration time is necessary to make sure final corner filling. The sheet needs enough deformation time to fill die cavity perfectly.
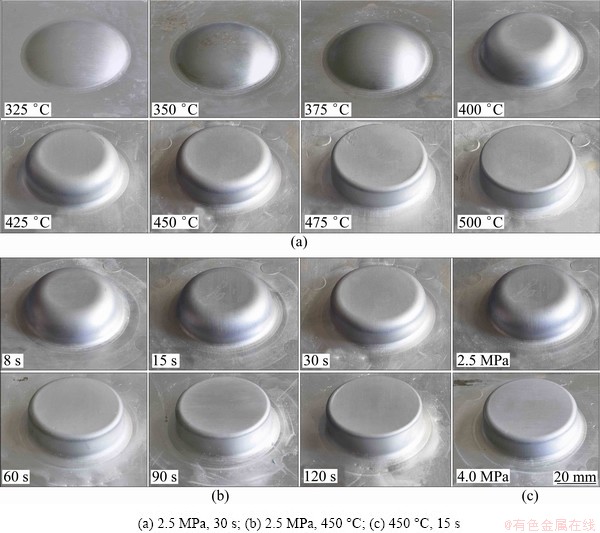
Fig. 2 Cup-shaped workpieces obtained under different conditions
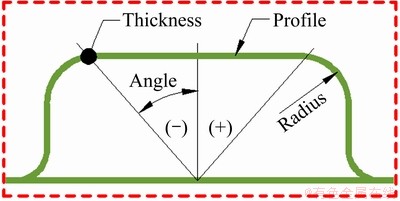
Fig. 3 Illustration of radius and thickness measuring
In fact, the three process parameters determine mutually the deformation behavior of sheet under RGF process, as shown in Fig. 5. It is clear that corner radius is also very sensitive to the forming pressure, especially with shorter duration time and at relatively lower temperature. It is illustrated from Fig. 5(a) that effect of gas pressure on die cavity filling ability decreases with temperature increasing. At high temperature, like 475 °C or 500 °C, same corner radius can be got while the gas pressure is different. In order to reduce the duration time at appropriate temperatures ranging from about 400 °C to 500 °C, higher forming gas pressure could be used. Similarly, effect of duration time decreases with gas pressure increasing, as shown in Fig. 5(b). When the forming gas pressure was 2.5 MPa and duration time was 30 s, the corner radius was about 6 mm. While the forming gas pressure was 4.0 MPa and duration time was 8 s, the corner radius was just 5 mm. Therefore, sheet can be formed into the die cavity completely within a shorter duration time with a larger gas pressure. However, enough duration time about 30 s is usually needed, especially when formed at relatively low temperature.
3.2 Thickness distribution
Thickness was measured and reported to quantify the effects of the three key process parameters on the deformation behavior of the cup-shape workpieces. Note that for thickness measurements, the cup-shape workpieces were cut into two halves from the center line, and the thickness of one half was measured using a micrometer attached with conical shape tips at several locations along the radial directions. The results are shown in Fig. 6.
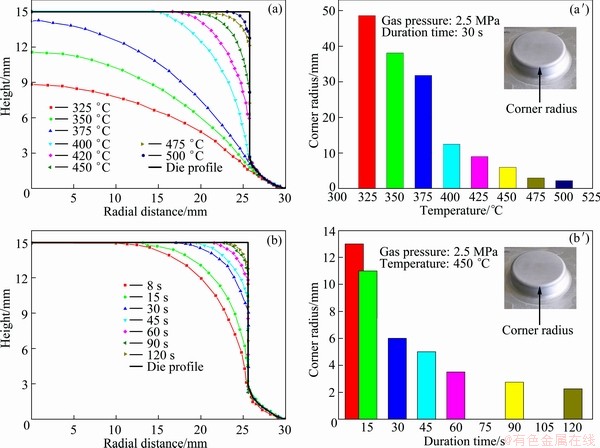
Fig. 4 Effects on profile and corner radius by temperature (a), (a′) and duration time (b), (b′)
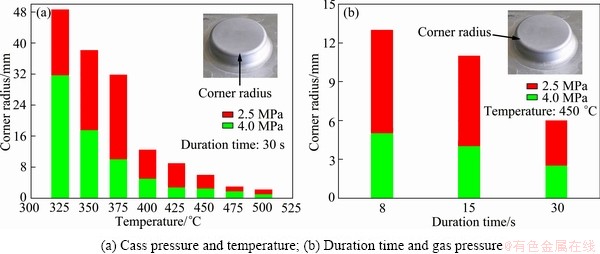
Fig. 5 Effect on radius by three process parameters mutually
On one hand, the highest thinning occurred at the center region of the workpiece before the sheet has been in touch with die, which is a free bulging process. On the other hand, the minimum wall thickness appeared at the transition zone of the workpiece between radius and bottom after the sheet has been in touch with die. Meanwhile, thickness of the center region is just about right at a value of 0.7 mm because of friction. This conforms that the alloy sheet is bugled freely, and then formed into the die cavity along the radial direction with formability increasing. Finally, the effects of temperature, duration time and pressure are as expected: increasing gas pressure, duration time and temperature leads to increasing thinning in general.

Fig. 6 Effect of key parameters on thickness distribution
4 Conclusions
1) The formability of the tested 5A06 sheet can be improved by increasing the forming temperature, duration time and gas pressure in general. Corner radius changes obviously at relatively a low temperature (<450 °C) or within a short duration time (<30 s), and then trends to the minimum value (about 2.0 mm) gently.
2) Temperature, duration time and gas pressure mutually determine the deformation behavior of sheet in RGF process. The smallest corner radius is about 2.0 mm. In practice, higher forming gas pressure can be used to reduce the duration time at an appropriate temperature ranging from about 400 °C to 500 °C. However, enough deformation time 15-30 s is required to achieve sound die cavity filling when the gas pressure is 4.0 MPa.
3) The minimum wall thickness appears at the transition zone of the workpiece between corner and bottom after the sheet contacts the die cavity. The thickness in the center region is almost the same value of 0.7 mm.
References
[1] TOROS S, OZTURK F, KACAR I. Review of warm forming of aluminum-magnesium alloys [J]. Journal of Materials Processing Technology, 2008, 207(1-3): 1-12.
[2] CUI Ji-rang, ROVEN H J. Recycling of automotive aluminum [J]. Transactions of Nonferrous Metals Society of China, 2010, 20(11): 2057-2063.
[3] YUAN Shi-jian, HE Zhu-bin, LIU Gang, WANG Xiao-song, HAN Cong. New developments in theory and processes of internal high pressure forming [J]. The Chinese Journal of Nonferrous Metals, 2011, 21(10): 2523-2533. (in Chinese)
[4] MULT E H, GEIGER M. Sheet and tube hydroforming at elevated temperatures [C]// International Conference on Hydroforming. Fellbach, Germany, 2003: 259-278.
[5] LIN Yan-li, HE Zhu-bin, YUAN Shi-jian, WU Jia. Formability determination of AZ31B tube for IHPF process at elevated temperature [J]. Transactions of Nonferrous Metals Society of China, 2011, 21(4): 851-856.
[6] JESWIET J, GEIGER M, ENGEL U. Metal forming progress since 2000 [J]. Journal of Manufacturing Science and Technology, 2008, 1(1): 2-17.
[7] KLEINER M, GEIGER M, KLAUS A. Manufacturing of lightweight components by metal forming [J]. CIRP Annals—Manufacturing Technology, 2003, 52(2): 521-542.
[8] WANG Hui, LUO Ying-bing, FRIEDMAN P, CHEN Ming-he, GAO Lin. Warm forming behavior of high strength aluminum alloy AA7075 [J]. Transactions of Nonferrous Metals Society of China, 2012, 22(1): 1-7.
[9] MAHABUNPHACHAI S, KOC M. Investigations on forming of aluminum 5052 and 6061 sheet alloys at warm temperatures [J]. Materials and Design, 2010, 31(5): 2422-2434.
[10] SORGENTE D, SCINTILLA L D, PALUMBO G. Blow forming of AZ31 magnesium alloy at elevated temperatures [J]. Journal of Material Forming, 2010, 3(1): 13-19.
[11] RASHID M S, KAM C, RYNTZ E F. Quick plastic forming of aluminum alloy sheet metal [R]. US 6253588 B1. Detroit, 2001.
[12] KRAJEWSKI P E, SCHROTH J G. Overview of quick plastic forming technology [J]. Materials Science Forum, 2007, 551-552: 3-12.
[13] SCHROTH J G, BRUEGGEMAN M H, GREWAL N P. Quick plastically formed aluminum doors: Design and performance [J]. Journal of Materials Engineering and Performance, 2007, 16(3): 339-348.
[14] RAJIV M. Processing commercial aluminum alloys for high strain rate superplasticity [J]. Journal of the Minerals, Metals and Materials Society, 2001, 53(3): 23-26.
[15] HE Zhu-bin, FAN Xiao-bo, XU Yong-chao, YUAN Shi-jian. Investigation on the formability of 5A06 sheet for rapid gas forming [J]. Rare Metal Materials and Engineering, 2011, 40(S3): 144-147. (in Chinese).
5A06铝合金板材热态快速气压胀形的变形形为
凡晓波,何祝斌,苑世剑
哈尔滨工业大学 金属精密热加工国家级重点实验室,哈尔滨 150001
摘 要:通过热态气压胀形实验测试5A06铝合金板材在不同温度、保压时间和气压下的成形性能。测量不同成形条件下(温度:325~500 °C;压力2.5,4.0 MPa;保压时间:8~120 s)圆底杯形件的轮廓、圆角半径和壁厚分布,分析各因素对板材热态气压胀形行为的影响。结果表明:温度越高,压力越大,保压时间越长,板材贴靠模具程度越大。圆底杯形件圆角半径最小仅为2.0 mm。最小壁厚值出现在圆角与底部过渡区域。在400~500 °C温度范围内,提高气体压力可以缩短保压时间,实现板材的快速气压成形。
关键词:5A06铝合金板材;快速塑性成形;快速气压成形;成形性能;变形行为;壁厚分布
(Edited by YANG Bing)
Foundation item: Project (NCET-11-0799) supported by the Program for New Century Excellent Talents in University of China; Project (HIT.BRETIII.201204) supported by Fundamental Research Funds for the Central Universities of China; Project (51175111) supported by the National Natural Science Foundation of China
Corresponding author: HE Zhu-bin; Tel: +86-451-86414751; E-mail: hithe@hit.edu.cn
DOI: 10.1016/S1003-6326(12)61736-1