J. Cent. South Univ. (2017) 24: 353-359
DOI: 10.1007/s11171-017-3437-0

Performance comparison and analysis of a combined power and cooling system based on organic Rankine cycle
WANG Zhi-qi(王志奇), ZHOU Qi-yu(周奇遇), XIA Xiao-xia(夏小霞), LIU Bin(刘斌), ZHANG Xin(张欣)
Institute of Mechanical Engineering, Xiangtan University, Xiangtan 411105, China
Central South University Press and Springer-Verlag Berlin Heidelberg 2017
Abstract: A novel power and cooling system combined system which coupled organic Rankine cycle (ORC) with vapor compression refrigeration cycle (VCRC) was proposed. R245fa and butane were selected as the working fluid for the power and refrigeration cycle, respectively. A performance comparison and analysis for the combined system was presented. The results show that dual-pressure ORC-VCRC system can achieve an increase of 7.1% in thermal efficiency and 6.7% in exergy efficiency than that of basic ORC-VCRC. Intermediate pressure is a key parameter to both net power and exergy efficiency of dual-pressure ORC-VCRC system. Combined system can produce maximum net power and exergy efficiency at 0.85 MPa for intermediate pressure and 2.4 MPa for high pressure, respectively. However, superheated temperature at expander inlet has little impact on the two indicators. It can achieve higher overall COP, net power and exergy efficiency at smaller difference between condensation temperature and evaporation temperature of VCRC.
Key words: dual-pressure organic Rankine cycle; vapor compression refrigeration; waste heat; performance analysis
1 Introduction
Organic Rankine cycle (ORC) can convert low-grade waste heat into electricity effectively [1, 2]. During the past decades, many efforts have been made to improve the system performance, mainly focusing on working fluids selection, parameter optimization and the modification of cycle configuration.
Working fluid can significantly influence the cycle performance, and much research has been devoted to working fluid selection. The effect of dry, isentropic and wet fluids on thermal efficiency was investigated in Ref. [3], and isentropic fluids showed better performance. Besides, working fluids with high liquid specific heat, low latent heat and normal boiling point were recommended [4, 5]. On the other hand, some researchers have concentrated on parameter optimization of ORCs [6–8].
The modification of ORC configuration is an effective method to achieve higher energy conversion efficiency. MAGO et al [9] and XI et al [10] compared the regenerative ORC and basic ORC. It showed that regenerative ORC produces a higher efficiency than basic ORC. Additionally, using an inner heat exchanger or a recuperator can also improve thermal efficiency of ORCs [11, 12]. LI et al [13] and GUZOVIC et al [14] put forward a dual-pressure ORC (DPORC) to decrease the system irreversibility and generate more net power. Besides, the combined ORC with refrigeration cycle has drawn much attention in recent years because it showed a higher performance. The system combined ORC with vapor compression refrigeration cycle (VCRC) was presented in Ref. [15], which could provide both power and refrigeration capacity. LI et al [16] analyzed the performance of the combined system. It indicated that overall COP reaches 0.47 for combined system by using butane. Although, much research has been devoted to the system configuration of ORC, few references investigated the combined system which coupled the DPORC with VCRC.
In the present work, a power/refrigeration system coupled the DPORC with VCRC was put forward to improve the system performance. The combined-system was compared with a basic ORC(BORC)-VCRC. And the effects of different parameters on combined-system performance were discussed.
2 System description and thermodynamic analysis
2.1 System description
The schematic diagrams of DPORC-VCRC and BORC-VCRC are shown in Fig. 1.
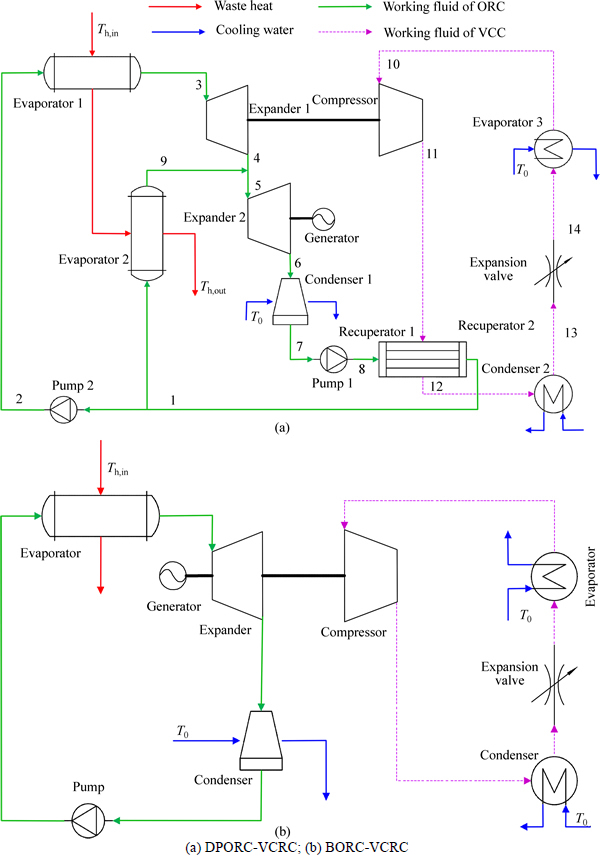
Fig. 1 Schematic diagrams of combined system:
In the DPORC, working fluid from the condenser 1 (state 7) is pressurized to intermediate pressure via the pump 1. Then, it recovers heat in the recuperator 1 and is split into two streams. A part of intermediate pressure fluid flows into the evaporator 2 and absorbs heat to generate vapor (state 9). Another part of fluid is pumped by the pump 2 and becomes high-pressure vapor after absorbing heat (state 3). It passes through the expander 1 to drive the compressor. The spent vapor (state 4) mixes with the vapor from evaporator 2 and flows into the expander 2 to produce power. Vapor comes from the exit of expander 2 (state 6) is cooled in the condenser 1 by water.
In the VCRC, the high-temperature vapor (state 11) becomes saturated liquid (state 13) after rejecting heat in the recuperator 1 and condenser 2. Then, it passes through the expansion valve to decrease the pressure. At the outlet of evaporator 3, refrigerant becomes saturated vapor (state 10) which is compressed by the compressor. During the process, refrigeration capacity is provided.
The configuration of BORC-VCRC is similar with that of DPORC-VCRC. The major difference between them is that there are two sets of evaporator and expander in DPORC, while only one in the former. Besides, the DPORC-VCRC has one recuperator which recovers the heat of working fluid in VCRC.
2.2 Thermodynamic analysis
Based on the first and second laws of thermodynamics, a thermodynamic model of the combined-system is developed. To simplify the thermodynamic calculation, the following is assumed: The system operates under steady condition. In addition, heat loss and pressure loss in heat exchangers and pipelines are neglected. Working fluid at the exit of evaporators is saturated vapor, and that at the outlet of condensers is saturated liquid.
R245fa can give higher net power for temperature greater than 160 °C [17]. Thus, R245fa is selected as the working fluid for DPORC, and its condensation temperature is set to be 303.15 K. Butane is recommended for refrigeration cycle in Ref. [15]. Its evaporation temperature and condensation temperature are set to be 278.15 K and 333.15 K, respectively [15, 16]. Besides, the input data of DPORC for thermodynamic analysis is listed in Table 1.
Table 1 Input data of combined-system
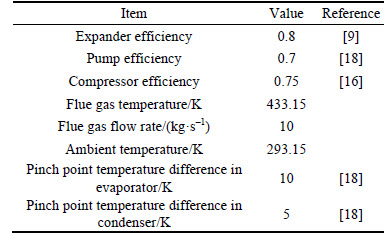
According to the state point of DPORC-VCRC in Fig. 1(a), thermal efficiency is defined as
(1)
The net power of two combined-systems can be calculated by
(2)
(3)
The refrigeration capacity and coefficient of performance (C) of VCRC can be written as
(4)
(5)
Heat transfer rate in two evaporators of DPORC is

(6)
Power generated by the turbines can be expressed as
(7)
(8)
Consumed work by the pumps and compressor is
(9)
(10)
(11)
The overall COP of combined-system can be written as
(12)
The exergy efficiency of DPORC-VCRC is defined as
(13)
(14)
(15)
3 Results and discussion
3.1 Compassion of configurations
In order to compare the performance of DPORC- VCRC and BORC-VCRC, the net power of both configurations is assumed to be equal. When the ratio of high pressure to intermediate pressure in DPORC is set to be 0.3, the influence of turbine inlet pressure (expander 1) on system performance is shown in Fig. 2.
It can be seen from Fig. 2 that DPORC-VCRC shows better performance than BORC-VCRC. As shown in Fig. 2(a), refrigeration capacity of DPORC-VCRC is obviously higher than that of BORC-VCRC, and the difference between two systems increases with the inlet pressure of expander 1. In addition, refrigeration capacity decreases with the increment of inlet pressure. It indicates that combined-system provides less power to produce refrigeration at higher inlet pressure. As results, the overall COP decreases with the expander1 inlet pressure increases, as shown in Fig. 2(b). The COP of DPORC-VCRC decreases from 0.23 to 0.08 as inlet
pressure increases from 1.0 MPa to 3.5 MPa.
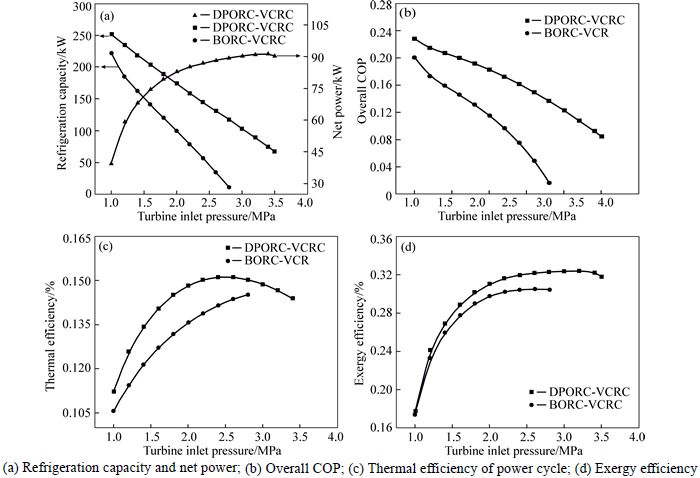
Fig. 2 Influence of expander 1 inlet pressure on system performance of DPPRC and BPRC:
Figure 2(c) shows that there is an optimal expander1 inlet pressure to achieve better thermal efficiency for DPORC-VCRC. When inlet pressure of expander1 is 2.4 MPa, the maximal thermal efficiency is 15.1% which is 7.1% higher than that of BORC-VCRC.
Since refrigeration capacity of DPORC-VCRC is larger than that of BORC-VCRC, the former has higher exergy efficiency as shown in Fig. 2(d). When inlet pressure is 2.4 MPa, exergy efficiency of DPORC- VCRC is 0.32, which increases by 5.1%. Figure 2(d) also shows that there is a very similar trend between net power and exergy efficiency. This demonstrates that net power is in the dominant position of exergy efficiency according to the Eq. (13). Besides, exergy efficiency of the novel combined-system at 2.4 MPa is 77.8% higher than that of 1.1 MPa. However, it only increases by 1.2% as inlet pressure ranging from 2.4 MPa to 3.4MPa. It indicates that DPORC-VCRC can keep good performance at 2.4 MPa.
3.2 Performance analysis of DPORC-VCRC
Using the same assumption in thermodynamic analysis for combined-system, the effects of expander inlet pressure on combined-system are shown in Fig. 3.
Figure 3(a) shows that the net power output increases rapidly at first and then decreases slowly with with the increase of intermediate pressure (p5). According to Eq. (2), net power of combined system is main determined by the output of expander 2. With the increase of p5, mass flow rate of working fluid decreases while enthalpy difference in expander 2 increases. Therefore, the maximum net power reaches 88 kW at 0.85 MPa. However, there is only 4.8% increase on net power as p3 increases from 1.9 MPa to 3.5 MPa. This indicates that intermediate pressure plays a more important role than high pressure on the net power.
It can be seen in Fig. 3(b) that overall COP can achieve maximum value of 0.3 at 1.7 MPa for p3 and 0.25 MPa for p5, respectively. The main reason is that expander 1 can generate more power to drive the compressor in this condition. As a result, combined- system will provide more refrigeration capacity than that of net power at lower expander inlet pressure.
As shown in Fig. 3(c), thermal efficiency of power cycle is influenced by the intermediate pressure (p5) and high pressure (p3). The maximum thermal efficiency is 16.5% at 2.4 MPa and 1.1 MPa of p3 and p5, respectively. The exergy of VCRC is much smaller than that of DPORC, so variation of exergy efficiency with p5 and p3 is similar with that of net power, as shown in Fig. 3(d).
When p3 and p5 are 2.4 MPa and 0.85 MPa
respectively, the effect of superheated temperature of T3 and T5 on system performance is shown in Fig. 4.
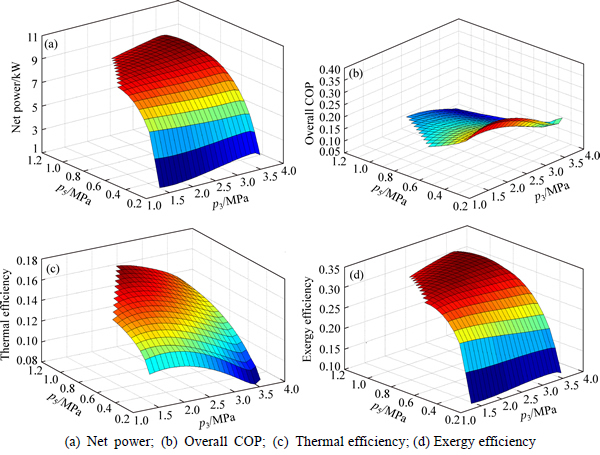
Fig. 3 Variation of combined-system performance with expander inlet pressure:
As shown in Fig. 4(a), superheated temperature has a small impact on the net power of combined system. Besides, variation of exergy efficiency with superheated temperature is similar with that of net power, as shown in Fig. 4(d). Difference between the maximum and minimum value of net power and exergy efficiency is less than 2.4% for superheated temperature ranging from 0 K to 30 K. The main reason is that the effect of superheated temperature on enthalpy difference and mass flow rate of working fluid is reverse.
Due to the increment of T3, mass flow rate of working fluid in expander1 decreases, which leads to the decrement of output. Consequently, the overall COP decreases with the rising of T3, as shown in Fig. 4(b). Although less heat is absorbed by evaporator 1 at a higher T3, the rejected heat is absorbed by evaporator 2. Thus, the total heat transfer rate in two evaporators increases with the rising of T3. The thermal efficiency and overall COP decreases by 8.1% and 17.9% for T3 ranging from 0 K to 30 K, respectively. However, T5 (superheated temperature of expander 2) leads to little variation of thermal efficiency and overall COP.
Figure 5 shows that the effect of evaporation temperature and condensation temperature in VCRC on system performance. In the analysis, working fluid at the exit of evaporators is assumed to be saturated vapor, and the inlet pressure of expander 1 and expander 2 is set to 2.4 MPa and 0.85 MPa, respectively.
With the decrease of difference between condensation temperature and evaporation temperature, mass flow rate of butane increases. The mass flow rate plays a dominant position in total heat transfer. Therefore, the overall COP can achieve the maximum value (0.31) at higher evaporation temperature and lower condensation temperature, as shown in Fig. 5(b). Meanwhile, work fluid in DPORC can recover more heat from VCRC. As a result, net power increases, shown in Fig. 5(a). Besides, the trend of net power is similar to that of overall COP. When condensation temperature and evaporation temperature are 318.15 K and 287.15 K, net power and overall COP are 101.2 kW and 0.31, respectively.
Figure 5(c) shows that evaporation temperature and condensation temperature of VCRC have a small impact on thermal efficiency. The difference of thermal efficiency rate between different conditions is less than 3.1%. According to Fig. 5(d), exergy efficiency decreases with the rising condensation temperature. When it increases from 318.15 K to 338.15 K, exergy efficiency decreases by 12.5%.
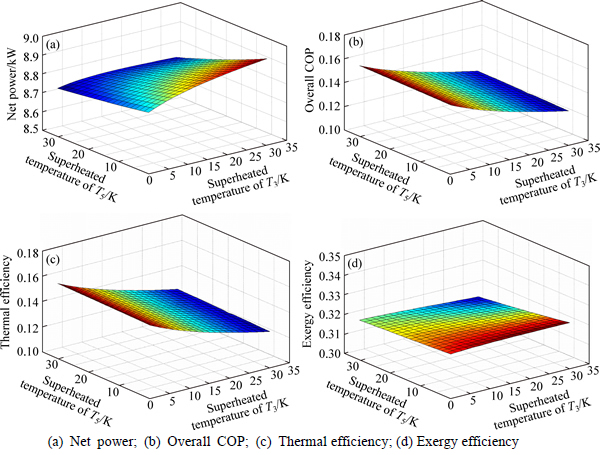
Fig. 4 Variation of combined-system performance with superheated temperature:
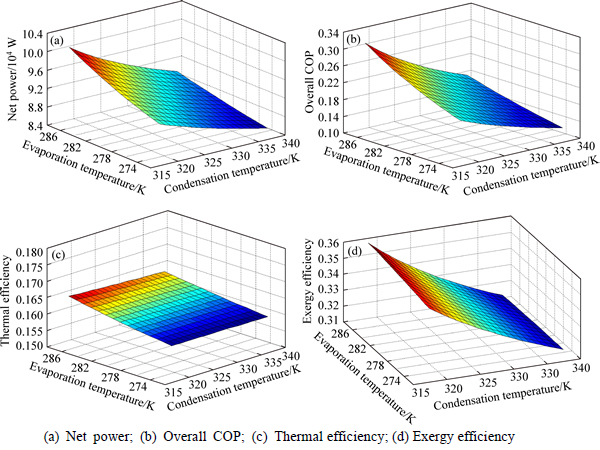
Fig. 5 Variation of combined-system performance with evaporation temperature and condensation temperature:
4 Conclusions
1) Compared with the BORC-VCRC, increases in thermal efficiency and exergy efficiency of 7.1% and 6.7% respectively are obtained for DPORC-VCRC.
2) Intermediate pressure is a key parameter to both net power and exergy efficiency. For the DPORC-VCRC, it can produce the maximum net power and exergy efficiency at 0.85 MPa for intermediate pressure and 2.4 MPa for high pressure, respectively.
3) Overall COP and thermal efficiency decrease with the increase of superheated temperature at expander 1 inlet, while superheated temperature at expander 2 inlet has little impact on different indexes.
4) Combined-system can achieve higher overall COP, net power and exergy efficiency at smaller difference between condensation temperature and evaporation temperature of VCRC. Exergy efficiency decreases with condensation temperature of VCRC.
Nomenclatures
W Power, kW
Q Heat flow rate, kW
m Mass flow rate, kg·s–1
c Specific heat, kJ·kg–1·K–1
h Specific enthalpy, kJ·kg–1
T Temperature, °C
η Efficiency, %
C Coefficient of performance
e Specific exergy, kJ
Subscripts
t Turbine
p Pump
net Net power
f Working fluid
g Exhaust gas
dp Dual-pressure ORC
bp Basic ORC
e Evaporator
h Heat source
com Compressor
s System
j Different component
References
[1] SCHUSTER A, KARELLAS S, SPLIETHOFF H. Energetic and economic investigation of organic Rankine cycle applications [J].
Applied Thermal Engineering, 2009, 29(8): 1809–1817.
[2] TCHANCHE B F, LAMBRINOS G, FRANGOUDAKIS A, PAPOADAKIS G. Low-grade heat conversion into power using organic Rankine cycles-A review of various applications [J]. Renewable and Sustainable Energy Reviews, 2011,15(8): 3963–3979.
[3] HUNG T C,WANG S K, KUO C H, PEI B S, TSAI K F. A study of organic working fluids on system efficiency of an ORC using low-grade energy sources [J]. Energy, 2010, 35(3): 1403–1411.
[4] LIU B, CHEN K, WANG C. Effect of working fluids on organic Rankine cycle for waste heat recovery [J]. Energy, 2004, 29(8): 1207–1217.
[5] HE C, LIU C, ZHOU M T, XIE H, XU X X, WU S Y, LI Y R. A new selection principle of working fluids for subcritical organic Rankine cycle coupling with different heat sources [J]. Energy, 2014, 68 (15): 283–291.
[6] ROY J P, MISRA A. Parametric optimization and performance analysis of a regenerative organic Rankine cycle using R-123 for waste heat recovery [J]. Energy, 2012, 39(1): 227–235.
[7] WANG Z Q, ZHOU N J, GUO J. Fluid selection and parametric optimization of organic Rankine cycle using low temperature waste heat [J]. Energy, 2012, 40(1):107–115.
[8] IMRAN M, PARK B S, KIM H J. Thermo-economic optimization of Regenerative organic Rankine cycle for waste heat recovery applications [J]. Energy Conversion and Management, 2014, 87: 107–118.
[9] MAGO P J, CHAMRA L M, SRINIVASAN K, SOMAYAJI, C. An examination of regenerative organic Rankine cycles using dry fluids [J]. Applied Thermal Engineering, 2008, 28(8): 998–1007.
[10] XI H, LI M J, XU C, HE Y L. Parametric optimization of regenerative organic Rankine cycle (ORC) for low grade waste heat recovery using genetic algorithm [J]. Energy, 2013, 58: 473–82.
[11] DAI Y P, WANG J, GAO L. Parametric optimization and comparative study of organic Rankine cycle (ORC) for low grade waste heat recovery [J]. Energy Conversion and Management, 2009, 50(3): 576–582.
[12] YARI M. Exergetic analysis of various types of geothermal power plants [J]. Renewable Energy, 2010, 35(1): 112–121.
[13] LI T L, ZHU J L, HU K Y, KANG Z H, ZHANG W. Implementation of PDORC (parallel double-evaporator organic Rankine cycle) to enhance power output in oilfield [J]. Energy, 2014, 68(15): 680–687.
[14] GUZOVIC Z, RASKOVIC P, BLATARIC Z. The comparision of a basic and a dual-pressure ORC (Organic Rankine Cycle): Geothermal Power Plant Velika Ciglena case study [J]. Energy, 2014, 76(1): 175–186.
[15] LI Y R, WANG X Q, LI X P, WANG J N. Performance analysis of a novel power/refrigerating combined-system driven by the low-grade waste heat using different refrigerants [J]. Energy, 2014, 73(14): 543–553.
[16] LI H S, BU X B, WANG L B, LONG Z, LIAN Y W. Hydrocarbon working fluids for a Rankine cycle powered vapor compression refrigeration system using low-grade thermal energy [J]. Energy and Buildings, 2013, 65: 167–172.
[17] LAKEW A A, BOLLAND O. Working fluids for low-temperature heat source [J]. Applied Thermal Engineering, 2010, 30: 1262-1268.
[18] IBARRA M, ROVIRA A, ALARCON PADILLA D C. Performance of a 5 kWe Organic Rankine Cycle at part-load operation [J]. Applied Energy, 2014, 120(1): 147–158.
(Edited by YANG Bing)
Cite this article as: WANG Zhi-qi, ZHOU Qi-yu, XIA Xiao-xia, LIU Bin, ZHANG Xin, Performance comparison and analysis of a combined power and cooling system based on organic Rankine cycle [J]. Journal of Central South University, 2017, 24(2): 353-359. DOI: 10.1007/s11171-017-3437-0.
Foundation item: Project(12C0379) supported by the Scientific Research Fund of Hunan Province, China; Project(13QDZ04) supported by the Scientific Research Foundation for Doctors of Xiangtan University, China
Received date: 2015-07-16; Accepted date: 2015-12-16
Corresponding author: WANG Zhi-qi, Associate Professor, PhD; Tel: +86–731–58292215; E-mail: wangzhiqi@xtu.edu.cn