文章编号:1004-0609(2014)03-0787-06
电化学还原技术从废旧锂离子电池中浸出LiCoO2
常 伟,满瑞林,尹晓莹,张 建
(中南大学 化学化工学院,长沙 410083)
摘 要:基于电化学还原技术,提出在低酸度溶液中电解浸出废旧锂离子电池正极片(LiCoO2)的新方法。线性伏安扫描结果表明:LiCoO2的还原峰电位为0.30 V(vs SCE),验证了此方法的可行性。通过条件实验对影响钴和铝浸出率的各因素进行考察,得到电解浸出的最佳条件:电流密度15.6 mA/cm2、硫酸浓度40 g/L、柠檬酸浓度36 g/L、温度45 ℃、时间120 min。在此优化条件下,钴和铝的浸出率分别为90.8%和7.9%。电解浸出后,可直接回收铝箔,用扫描电子显微镜(SEM)对铝箔表面进行观察,结果表明:铝箔在浸出过程中的腐蚀深度远小于其表面原有点蚀坑的深度。
关键词:废旧锂离子电池;LiCoO2;电化学还原;电解浸出;阴极保护
中图分类号:X705 文献标志码:A
Leaching LiCoO2 from spent lithium-ion batteries by electrochemical reduction
CHANG Wei, MAN Rui-lin, YIN Xiao-ying, ZHANG Jian
(School of Chemistry and Chemical Engineering, Central South University, Changsha 410083, China)
Abstract: Based on the electrochemical reduction technique, a novel process was developed for leaching LiCoO2 in the low acidity medium by electrolysis from spent lithium-ion secondary batteries. The electrochemical deoxidizing of LiCoO2 was characterized by linear sweeping voltammetry. The results show that the cathodic peak potential of LiCoO2 is 0.30 V(vs SCE), which verifies the possibility of the process. The related factors on the leaching rates of Co and Al were investigated by single factor experimental method, and the optimal parameters are as follows: current density 15.6 mA/cm2, concentration of H2SO4 40 g/L, concentration of C6H8O7·H2O 36 g/L, reaction temperature 45 ℃, electrolysis time 120 min. Under the optimal conditions, the leaching rates of Co and Al are 90.8% and 7.9%, respectively. After leaching, the aluminum foil can be recovered in their metallic forms. The surface morphology of the aluminum foil was examined by scanning electron microscopy (SEM). The results indicate that the corrosion depth of aluminum foil under leaching conditions is much smaller than the corrosive pit depth of aluminum foil without leaching in the sulfuric acid solution.
Key words: spent lithium-ion battery; LiCoO2; electrochemical reduction; electrolysis leaching; cathodic protection
目前,环境和资源问题日益突出,而大量废弃的锂离子电池对环境和资源所产生的压力均不可估量[1]。如何高效低能耗地回收废旧电池中的有价金属成为面临的重要课题。目前已经有较多文献对废旧锂离子电池的回收进行报道[2-5],但未充分考虑工艺技术与生产成本之间的矛盾平衡,导致工业化进程长期停滞不前。对废旧锂离子电池进行回收,其关键在于正极片的处理工艺。铝箔与正极粉用粘接剂牢牢粘结在一起,常规剥离十分困难,其典型分离工艺为直接酸浸[2]和碱煮-酸浸工艺[3-4],但其浸出液中成分复杂、净化过程压力较大,且回收的氢氧化铝价值偏低。后来用有机溶剂溶解[5]分离活性物质和集流体的方法,可以回收完整的铝箔,但有机溶剂成本高、毒性大,且存在有机溶剂的循环利用问题。所以,低成本处理正极片LiCoO2兼顾回收铝箔成为技术难题之一。另一方面,在湿法回收工艺中,浸出过程是整个工艺流程的核心,大多以酸浸为主,而H2SO4-H2O2法[3-4]在浸出体系中长期占据重要位置。高浓度强酸作为浸出剂,且加入H2O2等还原剂,从价格而言不具有优势。
为此,本文作者利用电化学还原法,直接以钴酸锂极片为电解池阴极,在低酸度溶液体系中,一步完成LiCoO2的选择性浸出以及正极粉与铝箔的分离。由外加电源提供电子,不仅可取代双氧水,而且可对铝箔施以阴极保护,使其剥离后以单质的形式回收。该工艺流程简单,可控性强,且能有效避免引起二次污染,是一种绿色环保工艺[6]。
1 实验
1.1 实验材料及试剂
实验所用废旧锂离子电池来自湖南某回收公司。先对其进行放电处理,之后手工拆解金属外壳,再将电池芯剥离,即可得到电池正极。电池正极片的主要化学成分见表1。实验所用化学试剂包括浓硫酸、浓盐酸、无水硫酸钠和柠檬酸,均为分析纯。
表1 废旧锂离子电池正极片的化学成分
Table 1 Chemical composition of positive plate for spent lithium ion batteries (mass fraction, %)

1.2 实验方法
实验中使用300 mL烧杯作为电解池,截取2.5 cm×10 cm的正极片经压平后作为电解池阴极,以0.5 cm×0.5 cm的铂片为对电极,进行恒电流电解,电解液中硫酸钠作为支持电解质,它与硫酸的浓度之和固定为0.5 mol/L。电解浸出后,经蒸馏水冲洗即可回收完整的铝箔,残渣则用体积比为1:1的HCl溶解。其中,钴浸出率η(Co)和铝浸出率η(Al) 分别按下式计算:
(1)
(2)
式中:c0为电解浸出液中的Co2+浓度,g/L;c1为渣浸出液中的Co2+浓度,g/L;c2为电解浸出液中的Al3+浓度,g/L;V0为电解浸出液体积,L;V1为渣浸出液体积,L;m为回收铝箔质量,g。
1.3 分析方法及仪器
采用亚硝基R盐分光光度法测定钴含量;采用铬天青S分光光度法测定铝含量;采用PS-2真空型ICP-AES对试样进行全元素分析;使用RST5000电化学工作站测试线性扫描伏安曲线,其中工作电极表观面积为1 cm2,辅助电极为大片铂电极,参比电极为饱和甘汞电极,扫描速率为5 mV/s;采用荷兰 Quanta-200型扫描电子显微镜分析铝箔表面形貌。
2 结果与讨论
2.1 电化学还原工艺原理
将失效钴酸锂粉末、乙炔黑和聚偏氟乙烯(PVDF)按质量比8:1:1研磨混匀,以N-甲基吡咯烷酮(NMP)为溶剂,将其均匀地涂覆在铂片电极上,烘干后置于30 g/L H2SO4 +28.9 g/L Na2SO4溶液中进行线性伏安扫描,结果如图1所示。
由图1中曲线1可知,铂电极在0.68~-0.26 V电位窗口内几乎不发生电极反应,最大电流为3 mA,相对于曲线2中最大电流(28 mA),可忽略。而电位由-0.26 V继续负移,H2开始析出,还原电流急剧增大。曲线2中,在电极电位为0.30 V左右出现了一个明显的还原峰,因为在本研究的电位范围内,考虑到溶液体系为强酸环境,LiCoO2只能被还原为Co2+,即此峰是LiCoO2还原为Co2+的特征峰,从而证明LiCoO2能够通过阴极电解进行浸出。

图1 不同工作电极的线性扫描伏安曲线
Fig. 1 Linear sweeping voltammetry curves of different working electrodes

图2 铝箔作工作电极的线性扫描伏安曲线
Fig. 2 Linear sweeping voltammetry curve of aluminum foil
铝箔作为正极片的一部分,在电解浸出过程中同样作为阴极,在外加电流作用下进行阴极极化,从而减缓在硫酸溶液中的溶解速率,简言之,铝箔是受阴极保护的[7-8]。将正极片的钴锂膜剥离,得到集流体铝箔,对其进行线性伏安扫描,结果如图2所示。
由图2可以看出,在电极电位0.48 V附近出现一个氧化峰,对应于铝阳极活性溶解过程。当扫描至-0.53 V时,腐蚀电流为0,铝箔得到了完全保护,此电位为铝箔最小保护电位。
综上可以得到电化学还原工艺的电极反应如下:
阴极,
LiCoO2 + 4H+ + e = Co2+ + Li+ + 2H2O (3)
2H++2e=H2 (4)
阳极,
2H2O-4e=O2+4H+ (5)
2.2 电化学还原工艺
2.2.1 电流密度对钴和铝浸出率的影响
在H2SO4浓度为40 g/L、C6H8O7.H2O浓度为36 g/L、反应温度为25 ℃和反应时间为120 min的条件下,考察电流密度对钴、铝浸出率的影响,结果如图3所示。
由图3可知,电流密度增加,Co2+浸出率先随之增加,当电流密度高于15.6 mA/cm2时,Co2+浸出率出现大幅下降,这主要是由LiCoO2和H+在阴极还原时相互竞争、此消彼长引起。电流密度偏低时,随电流密度的增加,LiCoO2的还原作用加强,因为LiCoO2比H+更容易得电子,其中LiCoO2/Co2+的标准电极电位为2.08 V,H+/H2的标准电极电位为0 V。当电流密度大于15.6 mA/cm2时,阴极极化严重,而LiCoO2的还原过电位更高,H+阴极放电的竞争优势加大。从图3中还可以看出,铝浸出率在电流密度为12.5~18.7 mA/cm2的范围内的变化趋缓。综上所述,电流密度的最佳值选为15.6 mA /cm2。

图3 电流密度对钴、铝浸出率的影响
Fig. 3 Effects of current density on leaching rates of Co and Al
2.2.2 硫酸浓度对钴、铝浸出率的影响
在电流密度为15.6 mA/cm2、C6H8O7·H2O浓度为36 g/L、反应温度为25 ℃和反应时间为120 min的条件下,研究硫酸浓度对钴、铝浸出率的影响,结果如图4所示。

图4 硫酸浓度对钴、铝浸出率的影响
Fig. 4 Effects of H2SO4 concentration on leaching rates of Co and Al
由图4可知,钴浸出率随硫酸浓度的增大先升高再降低,当硫酸浓度为40 g/L时,钴浸出率达到最大,为86.6%。维持一定的pH值,使LiCoO2直接还原为Co2+进入溶液,需要足够高的硫酸浓度,但当硫酸浓度过高时,H+阴极还原加剧。大量析氢造成铝箔表面局部碱化,破坏钴锂膜与铝箔的粘结作用[9],二者相互剥离;另一方面,析氢量较大,H2不能及时排出,使钴锂膜鼓破。最终,由于钴锂膜在溶液体系中不能有效转移电荷而使钴浸出率偏低。从图4中还可以看出,随硫酸浓度的增加,铝浸出率增加较快,但在硫酸浓度为40和50 g/L时出现持平。综合以上分析,最佳硫酸浓度确定为40 g/L。
2.2.3 柠檬酸浓度对钴、铝浸出率的影响
添加柠檬酸是实验的关键技术之一,主要是为了避免电解浸出过程中溶液失稳而变得浑浊。分别配制3种不同溶液,测试铂电极在不同溶液体系中的线性扫描伏安曲线,以考察电解浸出中的阳极行为,结果如图5所示。
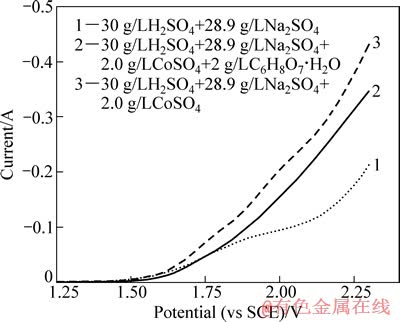
图5 铂电极在不同溶液体系中的线性扫描伏安曲线
Fig. 5 Linear sweeping voltammetry curves of platinum electrode in different solution
由图5中曲线2与3可看出,相同电位下,添加柠檬酸溶液体系的氧化电流明显减小。在电解过程中,LiCoO2还原为Co2+进入电解液,随Co2+浓度的升高,Co2+在阳极被氧化为Co3+的概率越来越大;而1 g/L的Co3+在pH>0.5时就会发生水解反应,生成Co(OH)3沉淀((Co(OH)3的溶度积为3×10-41)。同时需要强调的是,电解生成的Co3+的稳定时间为30 min左右[10],且其水解也是逐渐进行的,所以浑浊的电解液经抽滤澄清后静置一定时间还会变浑浊。基于以上分析,柠檬酸之所以可防止电解液浑浊,是因为它能抑制Co2+的阳极氧化,即使有少量Co3+生成,就会立即被还原成Co2+。
在电流密度为15.6 mA/cm2、硫酸浓度为40 g/L、反应温度为25 ℃和反应时间为120 min的条件下,柠檬酸浓度对钴、铝浸出率的影响如图6所示。

图6 柠檬酸浓度对钴、铝浸出率的影响
Fig. 6 Effects of C6H8O7·H2O concentration on leaching rates of Co and Al
由图6可知,当柠檬酸浓度为36 g/L时,钴浸出率较其他的略大。值得注意的是,当柠檬酸浓度在12~48 g/L的范围内时,随柠檬酸浓度的增加,铝浸出率逐渐降低。柠檬酸是三元有机酸,在铝表面的吸附能力极强,而且这种吸附能力与pH值无关[11],从而对铝箔腐蚀起到一定防护作用[12]。选取柠檬酸浓度36 g/L为最佳值。
2.2.4 温度对钴、铝浸出率的影响
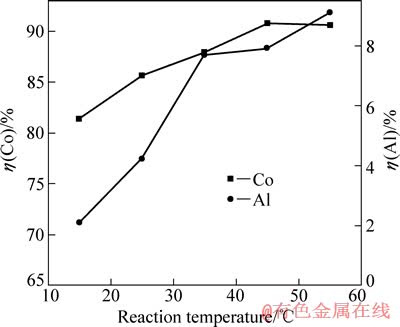
图7 反应温度对钴、铝浸出率的影响
Fig. 7 Effects of reaction temperature on leaching rates of Co and Al
在电流密度为15.6 mA/cm2、硫酸浓度为40 g/L、C6H8O7·H2O浓度为36 g/L、反应时间为120 min的条件下,反应温度对钴、铝浸出率的影响如图7所示。
由图7可知,15 ℃时钴浸出率较低,随温度的升高,钴浸出率逐渐增大,当温度达到45 ℃时出现最高峰后,钴浸出率随温度的变化不再明显。升高温度可明显促进LiCoO2的阴极还原。同时,铝浸出率随温度的升高增加比较明显。综合实验结果,取温度45 ℃为最佳值,此时钴浸出率达到90.8%,铝浸出率为7.9%。
2.2.5 电解时间对钴、铝浸出率的影响
在电流密度为15.6 mA/cm2、硫酸浓度为40 g/L、C6H8O7·H2O浓度为36 g/L、反应温度为45 ℃的条件下,研究电解时间对钴、铝浸出率的影响,结果如图8所示。
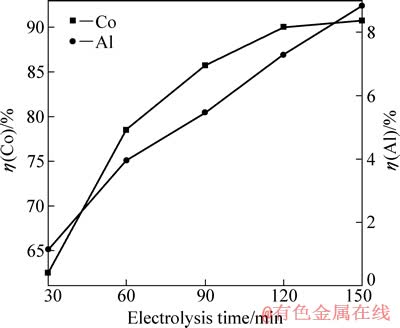
图8 电解时间对钴、铝浸出率的影响
Fig. 8 Effects of electrolysis time on leaching rates of Co and Al
由图8可知,钴浸出率随电解时间的延长明显增大,且增大的速率越来越慢,时间超过120 min后变化不明显。这主要是由于在电解过程中正极片的表面状态是变化的,从而影响其表面阴极反应。电解初期,电极粉颗粒间以面接触为主,有利于电子的传递,LiCoO2的还原占主导地位;但随着电解时间的延长,LiCoO2脱离钴锂膜,电子传递的通道受阻;至电解后期,钴锂膜与铝箔相剥离,由于活性物质的导电性远不如金属铝的[13],电荷转移受到阻滞,最终造成LiCoO2浸出阻力变大,析氢加剧。从图8还可以看出,铝浸出率随着电解时间的延长逐渐升高。综上可得出电解时间的最佳值为120 min。
2.3 铝箔的阴极腐蚀
铝箔电解浸出前后的SEM像如图9所示。由图9(a)可见,铝基体表面存在大量形状不规则的小孔,尺寸为3~8 μm。这是由于铝集流体在多次充放电循环后,出现了点蚀现象[14]。由图9(b)可见,铝基体表面分布有较多大小坑洞,大坑洞为电解浸出过程中产生的腐蚀坑,小坑洞为图9(a)所示点蚀坑的残余部分。值得注意的是,在某些大腐蚀坑中嵌套有小孔洞,这就证明了上面提出的结论。进一步可知,铝箔在浸出过程中受腐蚀的深度远小于其表面原有点蚀坑的深度,这就保证了铝的溶解率维持在8%以下。

图9 铝箔电解浸出前后的SEM像
Fig. 9 SEM images of aluminum foil before(a) and after(b) leaching
如前所述,铝箔在电解浸出过程中是受到阴极保护的,故H+直接腐蚀铝箔的可能性较小。其实,铝发生阴极腐蚀的原因很可能是OH-的生成,并参与铝的溶解反应。当铝处于阴极极化状态时,在金属/氧化物界面放电的H+得不到及时补充,使铝表面局部pH值升高,引起铝的碱性溶解[15]:
(6)
另一方面,Al(OH)4-只在碱性环境中稳定,随本体溶液中H+向铝箔表面扩散,界面pH值降低,Al(OH)4-会分解为Al3+[15-16];同时,局部区域过剩的OH-会溶解铝箔基体的氧化物层,或侵蚀界面的粘结剂,加之释放H2所产生的冲击,使得钴锂膜与铝箔产生分离,即实现了铝、钴分离。
3 结论
1) 线性扫描伏安曲线的分析结果表明,LiCoO2在0.30 V(vs SCE)左右发生阴极还原反应,控制电位低于0.53 V(vs SCE)则可对铝箔施以阴极保护。
2) 采用恒流电解法,通过抑制阴极析氢副反应的发生以及减缓钴锂膜剥离铝箔的速率,得到最优工艺条件如下:电流密度15.6 mA/cm2、硫酸浓度40 g/L、柠檬酸浓度36 g/L、45 ℃、120 min,此时,钴浸出率为90.8%、铝溶解率7.9%。
3) 在电解浸出过程中,铝箔受到阴极保护,其表面腐蚀程度较小,而铝发生腐蚀的原因是OH-的生成,OH-引起铝的碱性溶解。
REFERENCES
[1] 余海军, 袁 杰, 欧彦楠. 废锂离子电池的资源化利用及环境控制技术[J]. 中国环保产业, 2013, 7(1): 48-51.
YU Hai-jun, YUAN Jie, OU Yan-nan. Study on resource utilization and environmental control technology for spent lithium ion batteries[J]. China Environmental Protection Industry, 2013, 7(1): 48-51.
[2] 申勇峰. 从废锂离子电池中回收钴[J]. 有色金属, 2002, 54(4): 69-70.
SHEN Yong-feng. Recovery cobalt from discarded lithium ion cells[J]. Nonferrous Metals, 2002, 54(4): 69-70.
[3] 吴 芳. 从废旧锂离子二次电池中回收钴和锂[J]. 中国有色金属学报, 2004, 14(4): 697-701.
WU Fang. Recovery of cobalt and lithium from spent lithium-ion secondary batteries[J]. The Chinese Journal of Nonferrous Metals, 2004, 14(4): 697-701.
[4] FERREIRA D A, PRADOS L M Z, MAJUSTE D, MANSUR M B. Hydrometallurgical separation of aluminium, cobalt, copper and lithium from spent Li-ion batteries[J]. Journal of Power Sources, 2009, 187(1): 238-246.
[5] CONTESTABILE M, PANERO S, SCROSATI B. A laboratory-scale lithium-ion battery recycling process[J]. Journal of Power Sources, 2001, 92(1/2): 65-69.
[6] 刘美凤, 郭占成, 卢维昌. TiO2直接电解还原过程的研究[J]. 中国有色金属学报, 2004, 14(10): 1752-1757.
LIU Mei-feng, GUO Zhan-cheng, LU Wei-chang. Process of direct electrochemical reduction of TiO2[J]. The Chinese Journal of Nonferrous Metals, 2004, 14(10): 1752-1757.
[7] BAECHKMAN W V, SCHWENK W, PRINZ W. 阴极保护手册[M]. 胡士信,王向农, 译. 北京: 化学工业出版社, 2005: 33-47.
BAECHKMAN W V, SCHWENK W, PRINZ W. The theory and practice of electrochemical protection[M]. HU Shi-xin, WANG Xiang-nong, transl. Beijing: Chemical Industry Press, 2005: 33-47.
[8] CHOI Y S, KIM J G. Determination of cathodic protection potential criteria for thermally insulated pipeline in synthetic groundwater[J]. Corrosion, 2009, 62(2): 88-95.
[9] ROY D, SIMON G P, FORSYTH M. Towards a better understanding of the cathodic disbondment performance of polyethylene coatings on steel[J]. Advances in Polymer Technology, 2002, 21(1): 44-58.
[10] 徐泽民, 李 波. 石墨基二氧化铅阳极室温电生三价钴的研究[J]. 四川大学学报: 自然科学版, 2005, 42(3): 553-557.
XU Ze-ming, LI Bo. Study on electro-generation of trivalent cobalt ion with graphite-based lead dioxide anode at ambient temperature[J]. Journal of Sichuan University: Natural Science Edition, 2005, 42(3): 553-557.
[11] 李茂东. 钼酸盐对铝缓蚀性能的研究[J]. 材料保护, 1998, 31(11): 29-31.
LI Mao-dong. Corrosion inhibition of aluminum by molybdate[J]. Materials Protection, 1998, 31(11): 29-31.
[12]
B. Citric acid as corrosion inhibitor for aluminum pigment [J]. Corrosion Science, 2004, 46(1): 159-167.
[13] 胡建军, 刘侦德, 李宇明, 程建聪. 聚合物锂离子电池正极集流体材料的研制与应用[J]. 湖南有色金属, 2008, 24(5): 40-42.
HU Jian-jun, LIU Zhen-de, LI Yu-ming, CHENG Jian-cong. Research and application of material of positive pole current collectors of new polymer lithium-ion battery-preparation and application of pierced aluminum foils[J]. Hunan Nonferrous Metals, 2008, 24(5): 40-42.
[14] NIEDZICKI L, ZUKOWSKA G Z, BUKOWSKA M,
P, GRUGEON S, LARUELLEL S, ARMAND M, PANERO S, SCROSATI B, MARCINEK M, WIECZOREK W. New type of imidazole based salts designed specifically for lithium-ion batteries[J]. Electrochimica Acta, 2010, 55(4): 1450-1454.
[15] TERRYN H, VEREECKEN J, THENPSON J E. The electro-graining of aluminum in HCl. II: Formation of etch products[J]. Corrosion Science, 1991, 32(11): 1173-1177.
[16] 肖占文, 杨邦朝, 王豪才, 陈银富, 袁德明. 阴极析氢对铝箔交流腐蚀特性的影响[J]. 电子元件与材料, 1999, 18(4): 1-7.
XIAO Zhan-wen, YANG Bang-chao, WANG Hao-cai, CHEN Yin-fu, YUAN De-ming. Influence of cathodic hydrogen evolution on AC etching behavior of capacitor aluminum foil[J]. Electronic Components and Materials, 1999, 18(4): 1-7.
(编辑 陈卫萍)
基金项目:国家自然科学基金资助项目(21046007)
收稿日期:2013-04-16;修订日期:2013-11-26
通信作者:满瑞林,教授,博士;电话:0731-88836237;E-mail:rlman@mail.csu.edu.cn