High-pressure sintering and magnetic properties of Fe86Zr11-xNbxB3(x=5.5, 6) amorphous alloys
LU Bin(卢 斌)1, YI Dan-qing(易丹青)1, YAN Biao(严 彪)2, YIN Jun-lin(殷俊林)2, LIU Yan(刘 岩)3,
LIU Hui-qun(刘会群)1, WU Wei(吴 炜)1, MA Rui(马 瑞)1
(1. School of Materials Science and Engineering, Central South University,Changsha 410083, China;
2. Institute of Materials Science and Engineering, Tongji University,Shanghai 200092, China;
3. Shanghai Institute of Ceramics, Chinese Academy of Sciences, Shanghai 200050, China)
Abstract: The thermal stability of milling Fe86Zr11-xNbxB3(x=5.5, 6) melt-spun strip powders and the influence of high-pressure sintering conditions on phase component and grain size of bulk alloys were investigated by X-ray diffractometry(XRD), differential scanning calorimetry(DSC) and scanning electron microscopy(SEM). The results show that milling melt-spun powder remains in the amorphous state, and the crystallization temperature of which is 480-530℃, the apparent activation energy Ep of crystallization process is 294.1-219.5kJ/mol. The increasing Nb content can increase crystallization temperature and decrease Ep. Under the sintering conditions of 5.5GPa/3min, when Pw is 1150W, single phase α-Fe nanocrystalline (20.6-26.7nm) bulk alloy with relative density higher than 99.0% can be obtained. Under the sintering conditions of 5.5GPa/1150W/3min, the magnetic properties of these nanocrystalline bulk alloys are Fe86Zr5.5Nb5.5B3 alloy, Bs=1.15T, Hc=5.08kA·m-1; Fe86Zr5Nb6B3 alloy, Bs=1.26T, Hc=4.27kA·m-1.
Key words: Fe-based alloy; amorphous alloy; thermal stability; high-pressure sintering; bulk alloy; nanocrystalline; magnetic properties CLC number: TG139.8; TF123.3
Document code: A
1 INTRODUCTION
Fe-based nanocrystalline soft magnetic alloys become the focus in the world because of their excellent soft magnetic properties and high saturation induction. In engineering applications, soft magnetic alloys are usually used in bulk form with complex shape. However, nanocrystalline soft magnetic alloys in engineering applications are prepared through the crystallization of amorphous alloy which is controlled by melt spinning, accordingly the shape and size of the alloys are restricted in a high degree. In order to enlarge the application range of this kind nanocrystalline alloy, it is necessary to prepare amorphous or nanocrystalline bulk alloys from these amorphous powder or thin ribbons. It was reported that amorphous or nanocrystalline soft magnetic bulk alloys were prepared by high-pressure solidification method[1-4], thermal extrusion method[5-7], explosion molding method[8, 9] and spark plasma sintering method (SPS)[10-12]. In these powder metallurgy methods, high sintering pressure can promote nucleation rate of crystallization and restrain grain growth significantly, so as to obtain nanocrystalline alloys[13], therefore high-pressure solidification method becomes a suitable method to prepare nanocrystalline bulk alloys. However special high-pressure equipment and bulk shape size become the constrained factors of development of this technique and its applications. At present, hexahedral crown fluid high-pressure equipment provides a technical basis for studying and preparing large size nanocrystalline soft magnetic bulk alloys because quite great progresses have been acquired at high pressure of synthesis cavity and large size.
In this paper, under the research basis of thermal stability of Fe86Zr11-xNbxB3(x=5.5, 6) amorphous alloys, the influence of high-pressure sintering conditions on phase component and grain size and magnetic properties were analyzed, which provided a theoretical basis for its engineering applications.
2 EXPERIMENTAL
Vacuum induction furnace was used to melt ingots of alloys with nominal composition Fe86-Zr11-xNbxB3(x=5.5, 6), and amorphous ribbons were prepared by single roller melt spinning in argon atmosphere. Amorphous ribbons were pulverized into 50-150μm powder by QM-1SP high energy milling machine. Graphite heating die (d20mm×10mm) filled with 10g powder assembled in phrophyllite cubic bulk composed the high pressure cavity, the sketch of which is shown in Fig.1. High pressure sintering experiment was performed on HTDS-032A hexahedral crown fluid pressure machine, and the sintering pressure (p) was 5.5GPa, heating power Pw was 530-1150W, heating time was 3min, holding time was 3min. Phase component was analyzed by Dmax-rA X-ray diffractometer, and Scherrer equation (D=0.91λ/(Bcosθ)) was used to evaluate average grain size value D of bulk alloys. Morphology of powder was observed by JSM-5600LV scanning electron microscope (SEM). The thermal stability analysis of samples was performed on STA449C differential scanning calorimeter (DSC), and the heating-up rate was 5-20℃/min. The microstructure of samples was analyzed by H-800 transmission electron microscope (TEM). Archimedes method was used to measure the density of samples. Measure of magnetic properties was performed on LDJ9600 vibrating sample magnetometer (VSM) with maximum magnetizing field Hmax=1.0×103kA·m-1.
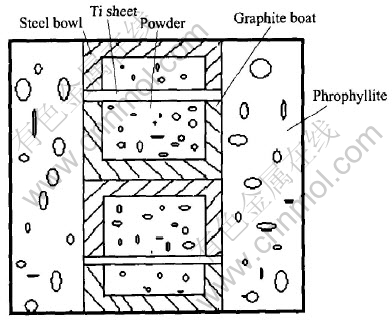
Fig.1 Sketch of structure of high pressure cavity
3 RESULTS AND ANALYSIS
3.1 Milling melt-spun powder
SEM observation shows that after milling Fe86-Zr11-xNbxB3(x=5.5, 6) melt-spun amorphous ribbons the morphology of powder is near lamella, and XRD analysis shows that these milling powders still remain in the amorphous state (see Fig.2(a)).
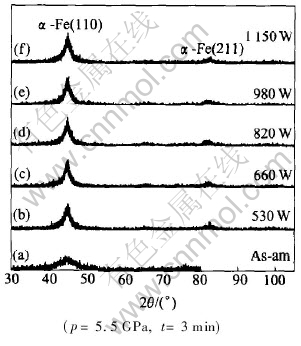
Fig.2 XRD patterns of melting-spun powder and sintering samples under different Pw
Fig.3 shows the DSC curves of Fe86Zr11-x-NbxB3(x=5.5, 6) amorphous powder. It can be seen that two exothermal peaks appear in every DSC curve, in which, the first peak temperature value of Fe86Zr5.5Nb5.5B3 alloy is 480-510℃, the other peak temperature value is 760-793℃; the first peak temperature value of Fe86Zr5Nb6B3 alloy is 500-530℃, the other is 770-800℃. In addition, two peak temperature values of two alloys increase with the increasing heating-up rate, however, the first peak temperature value of Fe86Zr5.5Nb5.5B3 alloy is lower than that of Fe86Zr5Nb6B3 alloy, the second peak temperature value of two alloys is the same. It is known that the first exothermal peak is induced by the precipitation of α-Fe phase from amorphous matrix, the second one is due to the decomposition of residual amorphous phase at high temperature[6]. According to the relationship between heating-up rate and peak temperature[14], apparent reaction activation energy of amorphous crystallization is evaluated as follows:

where is heating-up rate (K/min), Tp is peak temperature (K), Ep is reaction activation energy (J/mol), R is mole gas constant (8.314J/mol·K). Relationship between ln(φ/T2p) and (1/Tp) of two alloys is shown in Fig.4. It can be seen that ln(φ/T2p) and (1/Tp) have good linear relationship, the apparent reaction activation energy of alloys calculated by slope rate are: for Fe86Zr5.5Nb5.5B3 alloy Ep=294.1kJ/mol, for Fe86Zr5Nb6B3 alloy Ep=219.5kJ/mol.
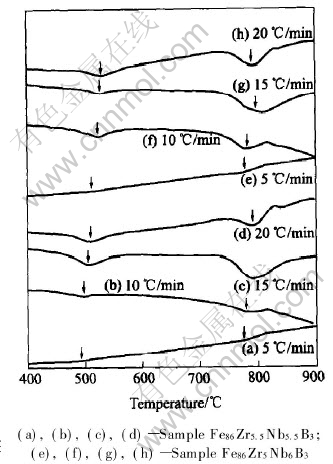
Fig.3 DSC curves of amorphous powders under different heating-up rates
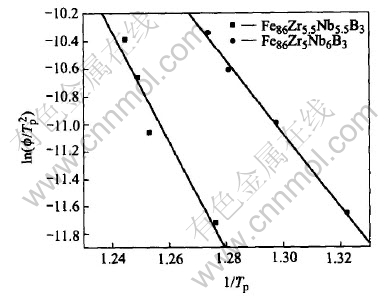
Fig.4 Relationship between ln(φ/T2p) and (1/Tp) of amorphous powder
From the analyses mentioned above, for Fe86Zr11-x-NbxB3(x=5.5, 6) amorphous alloys, with the increasing x(Nb) content, the crystallization temperature of alloys increase and the crystallization reaction activation energy decrease significantly, however it doesnt affect the phase decomposition of residual amorphous phase at high temperature. Thermal stability analysis shows that in order to obtain α-Fe phase nanocrystalline alloy, it is feasible that high-pressure sintering temperature is selected at 500-770℃.
3.2 Preparation of bulk alloys
During high-pressure sintering process, considering the relationship between heating temperature and heating power Pw, the range of Pw was 530-1150W. Under the sintering conditions of 5.5GPa/3min, the influence of Pw on relative density of Fe86Zr11-xNbxB3(x=5.5, 6) sintering samples is shown in Fig.5, from which it can be seen that with increasing Pw, when Pw≤820W, the relative density of samples increases significantly and then increases slowly; when Pw=1150W, the relative density of samples reaches 99%. Compared with that, the relative density of Fe86-Zr5Nb6B3 alloy increases quickly. All the samples have high densification, which is related to the decreasing viscosity and increasing plasticity happened during amorphous crystallization[6].
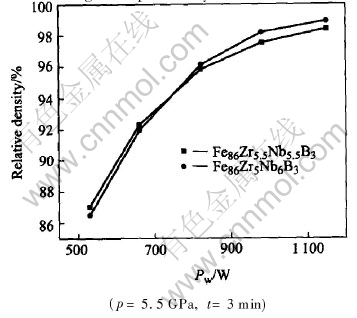
Fig.5 Influence of Pw on relative density of sintering samples
Figs.2(b)-(f) show the XRD patterns of Fe86Zr5.5Nb5.5B3 sintering samples under different Pw, the regularity of XRD patterns of Fe86Zr5Nb6B3 sintering samples is similar to that of Fe86Zr5.5Nb5.5B3 sintering samples. From XRD patterns it can be seen that, these samples are composed of single α-Fe phase, every diffraction peak shows the broadening characteristic. According to Scherrer equation, average grain size D values of α-Fe phase in Fe86Zr11-xNbxB3(x=5.5, 6) alloys are evaluated, and the results are given in Fig.6. With the increasing Pw, D values of all samples have the similar increasing tendency, while D values of Fe86Zr5Nb6B3 sintering samples are larger than those of Fe86Zr5.5Nb5.5B3 sintered samples. All the D values are 10.2-15.4nm.
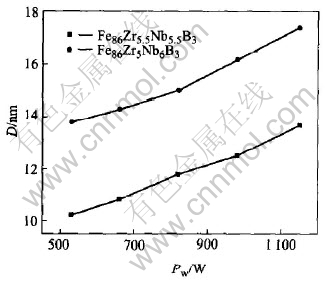
Fig.6 Effect of Pw on grain size of α-Fe phase of Fe86Zr11-xNbxB3(x=5.5,6) alloys
Fig.7 shows the typical TEM images and SAD patterns of Fe86Zr11-xNbxB3(x=5.5, 6) sintering samples under the sintering conditions of 5.5GPa/1150W/3min. From Figs.7(a) and (b) it can be known that in Fe86Zr5.5Nb5.5B3 bulk alloy nanocrystalline grains with homogeneous size precipitate in matrix, D value of which is 20.6nm. Diffusing diffraction ring appearing in the SAD patterns of this alloy shows that the matrix still remains in the amorphous state. The analysis shows that the diffraction rings from inner to exterior correspond to {110}, {200} and {211} plane diffraction of α-Fe solid solution phase precipitated from matrix. From Figs.7(c) and (d), it can be seen that micro-structure of Fe86Zr5Nb6B3 alloy is similar to that of Fe86Zr5.5Nb5.5B3 alloy, the difference is that D value 26.7nm of the former alloy is larger than that of the latter. It is observed that α-Fe nanocrystalline grains precipitating from amorphous matrix appear as elliptic morphology, which would affect the coercive force of bulk alloys. Comparing the results of Scherrer equation calculating with TEM images, it can be seen that calculation results of grains size are larger than that of quantified metallographic measured results of TEM images, the error range is 33-34%. From the description mentioned above it can be seen that, high sintering pressure can evidently promote the nucleation rate of amorphous crystallization process as well as restrain the growth of grains and is facilitated to obtain densified nanocrystalline bulk alloy, so hexahedral crown high-pressure technique is a simple method with high efficiency and low cost to prepare nanocrystalline bulk alloy.
3.3 Magnetic property of bulk alloys
Fig.8 shows the hysteresis loops of Fe86Zr11-x- NbxB3(x=5.5, 6) sintering samples under the
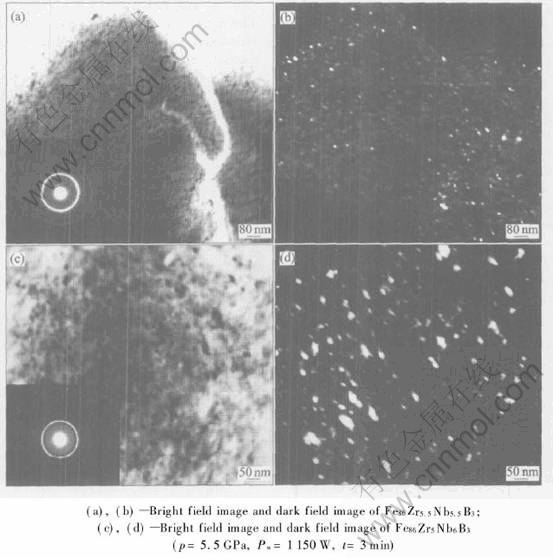
Fig.7 TEM images and SAD patterns of sintering samples
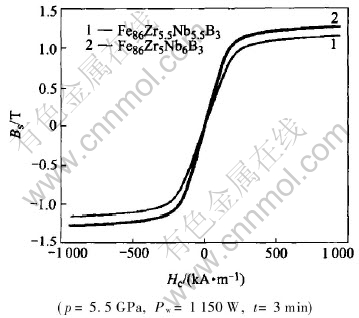
Fig.8 Hysteresis loop of sintering samples
sintering conditions of 5.5GPa/1150W/3min. From the curves saturation induction Bs and coercive force Hc were calculated as follows, Fe86Zr5.5-Nb5.5B3 alloy: Bs=1.15T, Hc=5.08kA·m-1; Fe86Zr5Nb6B3 alloy: Bs=1.26T, Hc=4.27kA·m-1. After Nb content was increased from 5.5% to 6.0%, the magnetic properties of sintering bulk alloys were improved evidently. Compared with the results reported by Kawamura et al[2] and Kojima et al[6], the Hc of as-received bulk alloys in this paper is several orders of magnitude higher. The microstructure of bulk alloys is composed of single phase α-Fe nanocrystalline. According to the theoretical analysis of nanocrystalline soft magnetic materials proposed by Herzer[15], these samples have low Hc. Herzer[15] considered that, in an exchanged relating characteristic length L0ex large amount of nanocrystalline soft magnetic grains should exist, and the magnetocrystalline anisotropy K of these grains can be averaged into a low value by enough exchange couple between these grains, so Hc of materials is decreased and good soft magnetic properties can be obtained. Simple statistic calculation shows that the average value of K is 〈K〉:

where D is grain size; exchange related length L0ex is determined by exchange stiffness A of nanocrystalline phases and anisotropy content K, L0ex=(A/K)1/2. Eqn.(2) shows that, when D〈L0ex, the average value of anisotropy content is proportional to hexagonal equation of grain size D. If spinning rotary model is valid, Hc can be described as follows:

where Pc and Pμare proportional constant, and Js is saturation magnetization.
Evidently, the decrease of grain size to a certain degree leads to small average or effective anisotropy of materials, so, Hc of materials is decreased. Microstructure sensitive property Hc is not only related to grain size, but also related to morphology of grains, crystal defect, and second phases. High Hc results in large moving resistance of magnetic domain wall. The existence of holes and reverse domain boundaries caused by incomplete densification of samples during sintering process induces hindrance of magnetic domain wall, therefore coercive force increases, and internal microstrain is introduced during high-pressure sintering process and oxidation of powders also affect Hc of sintering bulk alloy. In addition, α-Fe phase nanocrystalline grains with evident directivity and elliptic shape are disadvantage to decrease Hc. So, several reasons lead to the increase of Hc.
4 CONCLUSIONS
1) After milling powders are pulverized, Fe86-Zr11-xNbxB3(x=5.5, 6) melt-spun powders still remain in the amorphous state, their crystallization temperature and apparent activation energy are 480-530℃ and 294.1-219.4kJ/mol, respectively. The increasing Nb content improves the crystallization and decreases the crystallization apparent activation energy.
2) Under the conditions of 5.5GPa/3min, when Pw=1150W, single phase α-Fe nanocrystalline (20.6-26.7nm) bulk alloys with relative density higher than 99.0% can be obtained.
3) Under the conditions of 5.5GPa/1150W/3min, the magnetic properties of as-received single phase α-Fe nanocrystalline bulk alloys are as follows: Fe86Zr5.5Nb5.5B3 alloy, Bs=1.15T, Hc=5.08kA·m-1; Fe86Zr5Nb6B3 alloy, Bs=1.26T, Hc=4.27kA·m-1.
REFERENCES
[1]Kawamura Y, Takagi M, Senoo M, et al. Preparation of bulk amorphous alloys by high temperature sintering under a high pressure[J]. Mater Sci Eng, 1988, 98: 415-418.
[2]Kawamura Y, Inoue A, Kojima A, et al. Consolidation of amorphous Fe-Zr-B powders by hot-pressing method[J]. Journal of the Japan Society of Powder and Powder Metallurgy,1995, 42(1): 40-46.
[3]LU Bin, YI Dan-qing, LIU Yan, et al. Formation of Fe73.5Cu1Nb3Si13.5B9 nanocrystalline soft magnetic bulk alloys in high pressure[J]. Journal of Inorganic Materials, 2004, 19(4): 269-273.
[4]LU Bin, YI Dan-qing, LIU Yan, et al. Preparation of Fe84Nb7B9 nanocrystalline soft magnetic bulk alloy under high-pressure[J]. The Chinese Journal of Nonferrous Metals, 2004, 14(2): 173-178.(in Chinese)
[5]Kawamura Y, Takagi M, Akai M. A newly developed warm extrusion technique for compacting amorphous alloy powders[J]. Mater Sci Eng, 1988, 98: 449-452.
[6]Kojima A, Horikiri H, Kawamura Y, et al. Production of nanocrystalline b.c.c. Fe-Nb-B bulk alloys by warm extrusion and their magnetic properties[J]. Mater Sci Eng, 1994, A179-A180: 511-515.
[7]Kojima A, Horikiri H, Makino A, et al. Soft-magnetic porerties of nanocrystalline bcc Fe-(Nb, Zr)-B bulk alloys consolidated by warm extrusion[J]. Mater Trans JIM, 1995, 36(7): 945-951.
[8]Sato T, Taniguchi T, Kondo K, et al. Effect of shock duration time on magnetic properties of dynamically compacted amorphous powder[J]. Journal of the Japan Society of Powder and Powder Metallurgy, 1988, 35(3): 96-100.
[9]QIU Jun, XIE Zi-zhang, YANG Rang, et al. The magnetic properties of the explsive consolidating amorphous powder[J]. Journal of University of Science and Technology Beijing, 1994, 16(4): 330-334.
[10]Kojima A, Mizushima T, Makino A, et al. Soft magnetic properties of bulk nanocrystalline Fe90Zr7B3 alloys consolidated by spark-plasma sintering[J]. Journal of the Japan Society of Powder and Powder Metallurgy, 1996, 43(5): 613-618.
[11]Shen B L, Kimura H, Inoue A A, et al. Consolidation of Fe-Co-Ga-P-C-B glassy powders by spark-plasma-sintering and their magnetic properties[J]. Journal of the Japan Society of Powder and Powder Metallurgy, 2001, 48(9): 858-862.
[12]LU Bin, YI Dan-qing, LIU Yan, et al. SPS sintering and magnetic properties of Fe70Cr8Mo2Si5B15 amorphous[J]. Journal of Functional Materials, 2004, 35: 698-699.
[13]LIU Xiao-min, YAO Bin, SU Wen-hui. A thermodynamic study on the crystallization processes of amorphous (Fe0.99Mo0.01)78Si9B13 alloy under high pressure[J]. Chinese Journal of High Pressure Physics, 1997, 11(4): 260-265.
[14]LU Chang-wei, XI Tong-geng. Thermal Analysis Mass Spectrography[M]. Shanghai: Shanghai Scientific and Technical Literature Press, 2002. 104-105.
[15]Herzer G. Nanocrystalline soft magnetic materials[J]. J Magn Magn Mater, 1992, 112: 258-262.
(Edited by LI Xiang-qun)
Foundation item: Project(0452NM086) supported by the Tackling Key Science and Technology Program of Shanghai, China
Received date: 2004-10-08; Accepted date:2005-01-24
Correspondence: LU Bin, Associate Professor, PhD; Tel: +86-731-8836319; E-mail: luoffice@mail.csu.edu.cn