
Effect of heat diffusion on properties of zinc-aluminum coating on AZ91D magnesium alloys
LI Zhao-feng(李兆峰), HUANG Wei-jiu(黄伟九), LIU Ming(刘 明)
School of Material Science and Engineering, Chongqing Institute of Technology, Chongqing 400050, China
Received 28 July 2006; accepted 15 September 2006
Abstract: A protecting zinc and aluminum coating on the surface of AZ91D magnesium alloys was obtained by thermal spraying to improve the corrosion and wear resistance performances. In order to enhance the combination between magnesium alloy matrix and zinc and aluminum coating, the sample was heat-treated at 300 ℃ for 2 h, then, the cross-section patterns, XRD pattern, micro-hardness, wear and corrosion resistance abilities were researched. The results indicate that the interface between the coating and substrate is metallurgical bond, and a transitional fusion layer is formed by diffusion. The micro-scale abrasion test and polarization test in 3% NaCl solution show that the diffusion-treated specimen has better wear and corrosion resistance performances in comparison with the undiffusion-treated and substrate magnesium alloys; in addition, it has relatively higher micro-hardness than the undiffusion-treated magnesium alloys.
Key words: magnesium alloy; zinc-aluminum coating; heat diffusion; wear; corrosion
1 Introduction
Magnesium alloy is the lightest metal structural material; it has the advantages of low density, high specific strength and specific rigidity, good damping characteristic, machinability and castability, good electric and thermal conductivity[1,2]. Therefore, magnesium alloy is widely applied in automobile, aerospace and electronic industry. However magnesium is a very active metal, and its standard electrode voltage is negative (about -2.36 V). The oxidative films on the surface of magnesium alloy don’t have effective protective function because they are loose and porous[3,4]. Therefore, in practical applications, many surface treatment technologies are applied to improve the corrosion and wear resistance of magnesium alloys, such as electroplating, electroless plating, chemical transformation, anodic oxidation, laser surface alloying, organic coatings and micro-arc oxidation[5-11]. Each has its own advantages and disadvantages, and the simpler and cheaper coating technologies with low environmental pollution remain to be developed.
With the simple techniques and equipment, and no limit in workpiece shape, thermal spraying methods were widely applied to the synthesis of surface coatings, but the problems such as low hardness and poor integrated strength for coating were also existed for the technology. The formation of metallurgic layer between the substrate and coating by diffusion treatment may be an effective method to solve above problems. ZHANG et al[12] and LIANG et al[13] studied the thermal sprayed aluminum coating on the surface of AZ91D magnesium alloys, and found that the capability of corrosion resistance of magnesium alloys was improved by diffusion treatment. Because the melting points of aluminum and magnesium are near, and magnesium is easy to burn, the fusion and diffusion between aluminum and magnesium is difficult, and the integrated strength is also low.
In this work, thermal spraying technology was applied to prepare zinc and aluminum coating on the surface of AZ91D magnesium alloys. The zinc layer was used as a transition layer to decrease the diffusion temperature, and enhance the integrated strength between magnesium alloy matrix and zinc and aluminum coating. The sample was heat-treated at different temperatures and for holding time, and the effects of heat diffusion on the microstructure, microhardness, tribological proper ties and corrosion resistance of the coatings were also evaluated.
2 Experimental
A conventional AZ91D die casting magnesium alloy was utilized as test material. The chemical compositions are as follows (mass fraction, %): Al 9.1, Zn 0.85, Mn 0.27, Mg balance. The zinc and aluminum coating on the surfaces of the specimens was formed by flame wire spray after pretreatment. Processing parameters were optimized as follows: oxygen pressure 0.4-0.6 MPa, ethyne pressure 0. 07-0.1 MPa, air pressure 0.5-0.6 MPa, spray distance 110-140 mm, and angle 60?-90?. The thickness of zinc layer is 30-50 μm, and aluminum layer is 150-200 μm.
The samples sprayed with zinc and aluminum coating were heat-treated at (300±5) ℃ for 2 h and cooled down to room temperature in an electric resistance furnace. The microstructure of diffusion-treated specimens was observed with JSM-6460LV model scanning electron microscope (SEM), and a composition analysis was carried out using energy dispersive spectrum (EDS) attached to SEM. The phase composition of coating was analyzed by BDX3300 X-ray diffractometer (XRD). The tribological properties were studied using a Phoenix Tribology TE66 Micro-Scale Abrasion Tester. The testing rig is based on ball-cratering geometry: a GCr15 bearing steel sphere (R=12.7 mm) rotates against the specimen under investigation (sliding speed: 150 r/min, revolution: 3 000 r). Corrosion properties were studied in 3% NaCl solution by using electrochemical polarization testing. The electrochemical polarization tests were carried out in a closed three-electrode cell, with a sweep rate of 1 mV/s
using a 273 A electrochemical measuring system. In addition, microhardness of the diffusion layer and the matrix was measured using HVS-1000 digital microhardness tester under a load of 0.5 N(dwelling time is 15 s).
3 Results and discussion
3.1 Microstructure
Linear scanning analysis result along the cross section on undiffusion-treated specimen is shown in Fig.1. It shows that the elemental distribution has an abrupt change at the interface between the substrate and coating (or between aluminum layer and zinc layer), which indicates that the interface between the coating and substrate is mechanical bond.
After heat diffusion at 300 ℃ for 2 h, the interdiffusion between the substrate and coating (or between different coatings) took place. As shown in Fig.2, the change of elemental distribution of aluminum and zinc are continuous and gradual along the cross section direction. The morphology and microstructure of the Zn-Mg interdiffusion layer is shown in Fig.3. The compositions of the intermetallic compounds and transition zone were analyzed using EDS, and the analytic results are listed in Table 1. The results show that the three elements of magnesium, aluminum and zinc all exist in interface zone, and the composition analyses also reveal that point 1 and 2 have higher zinc content, and the magnesium and aluminum contents of the former are lower than those of the latter. The magnesium content in zone 3 goes up and is close to zinc content, which indicates that the zinc content gradually decreases from the zinc layer to magnesium alloy matrix. Fig.4 shows the X-ray diffraction pattern of Zn-Mg interface of diffusion-treated specimen. It is found that the diffusion layer consists of MgZn, MgZn2, Mg2Zn11 and AlMg4Zn11 intermetallic compounds. All these results indicate that the interface between the coating and substrate (or between aluminum layer and zinc layer) was metallurgical bond, and a transitional layer was formed by diffusion.
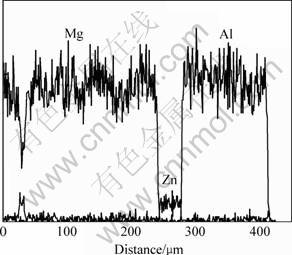
Fig.1 Elements distribution along cross-sectional direction for undiffusion specimen
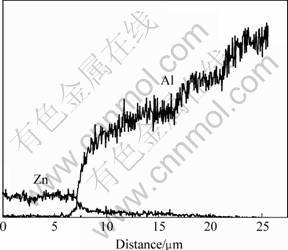
Fig.2 Linear scanning of zinc-aluminum interface for diffusiontreated specimen at 300 ℃ for 2 h
Table 1 Results of EDS analysis of Zn-Mg interface(mass fraction, %)

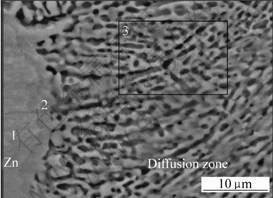
Fig.3 Microstructure of Zn-Mg interface
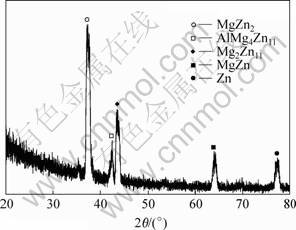
Fig.4 X-ray diffraction pattern of Zn-Mg interface
3.2 Hardness and wear tests
The microhardness distribution along the depth direction for the diffusion-treated specimen and undiffusion-treated specimen is shown in Fig.5. The microhardness of diffusion-treated specimen gradually increased with the depth, and then decreased to steady value, which corresponded to the microhardness of magnesium alloy matrix. The highest microhardness of diffusion-treated specimen is HV145, which is higher than that of undiffusion-treated specimen (HV85). The improvement of microhardness of diffusion-treated specimen is attributed to the formation of Mg-Al-Zn intermetallic compound.
Fig.6 shows the variation of wear volume with load for undiffusion-treated and diffusion-treated specimens. The results indicated that the increase of wear volume was slow with an increase of load for diffusion-treated specimen, however the wear volume increased quickly with load for undiffusion-treated specimen. Moreover the wear volume of diffusion-treated specimen was much less than that of unheated-treated specimen at higher load.
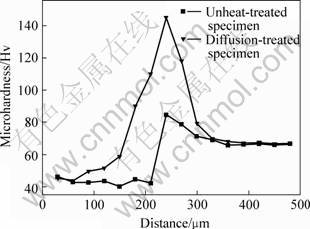
Fig.5 Distribution of hardness along depth direction of coating
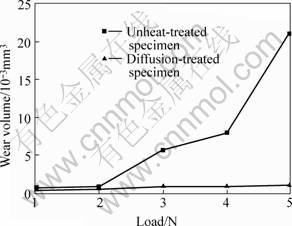
Fig.6 Variation of wear volume with load
3.3 Corrosion tests
Typical polarization curves of the three kinds of specimen in 3% NaCl solution are shown in Fig.7. It can be seen that the open-circuit potential (OCP) of AZ91D magnesium alloy is about -1.47 V(SCE). For undiffusion-treated specimen and diffusion-treated specimen, the OCP increases to -1.16 V and -0.95 V (SCE), respectively. Apparently, the OCP of the diffusion- treated specimen is higher than that of both undiffusion- treated specimen and naked magnesium alloy. On the other hand, the diffusion-treated specimen showed lower corrosion current than the others. Therefore, the formation of the diffusion fusion layer makes the diffusion-treated specimen have better corrosion resistance than the untreated specimen and bare AZ91D magnesium alloy.
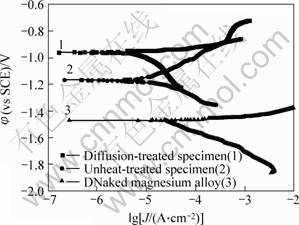
Fig.7 Potentiodynamic polarization curves of different specimens
4 Conclusions
1) A diffusion fusion layer was formed between the substrate and the coating when the sample was heat-treated at 300 ℃ for 2 h; and the diffusion fusion layer consisted of MgZn, MgZn2, Mg2Zn11 and AlMg4Zn11 intermetallic compounds.
2) The microhardness and antiwear properties of the diffusion-treated specimen are higher than those of untreated specimen.
3) Compared with the undiffusion-treated specimen, the diffusion-treated specimen has better corrosion resistance ability. The existence of the diffusion fusion layer enhances the surface corrosion potential and decreases the corrosion rate of the coating.
References
[1] DONG Qing, XIAO Liang-tao, LUO Qin. Preparation of ceramic membrane by micro arc oxidation on Mg alloy[J]. Materials Science Forum, 2005, 488-489: 677-680.
[2] HU Yong, DU Nan, ZHAO Qing, ZHOU Ya, MENG Ling-gang. Phosphoric conversion coating and chromic conversion coating for die-cast magnesium alloy ZM5[J]. Materials Science Forum, 2005, 488-489: 831-834.
[3] CHEN Zhen-hua, YAN Hong-ge, CHEN Ji-hua, QUAN Ya-jie, WANG Hui-min, CHEN Ding. Magnesium Alloys[M]. Beijing: Chemical Industry Press, 2004.
[4] ZENG Rong-chang, KE Wei, XU Rong-bo, HAN En-hou, ZHU Zi-rong. Recent development and application of magnesium alloys[J]. Acta Metallurgica Sinica, 2001, 37(7): 673-685.
[5] TONG Zhen-song, ZHANG Wei, LI Jiu-qing, GAO Jin, HE Ji-quan, ZHOU Ji. Galvanic corrosion behavior of die cast AZ91D magnesium alloy in chloride solution[J]. Journal of University of Science and Technology Beijing, 2004, 11(2): 127-132.
[6] BAGHNI I M, WU Yin-shun, LI Jiu-qing, ZHANG Wei. Corrosion behavior of magnesium and magnesium alloys[J]. Trans Nonferrous Met Soc China, 2004, 14(1): 1-10.
[7] MA You-ping, XU Ke-wei, WEN Wei-xin, HE Xi-peng, LIU Peng-fei. The effect of solid diffusion surface alloying on properties of ZM5 magnesium alloy[J]. Surface & Coatings Technology, 2005, 190: 165-170.
[8] GUO Hong-fei, AN Mao-zhong, XU Shen,HUO Hui-bin. Microarc oxidation of corrosion resistant ceramic coating on a magnesium alloy[J]. Materials Letters, 2006, 60(12): 1538-1541.
[9] GRAY J E, LUAN B. Protective coatings on magnesium and its alloys-a critical review[J]. Journal of Alloys & Compounds, 2002, 336(1-2): 88-113.
[10] ZHU Li-qun, LIU Hui-cong, LI Wei-ping, SONG Guang-ling. Zinc alloyed coating on AZ91D magnesium alloys[J]. Journal of Beijing University of Aeronautics and Astronautics, 2005, 31(1): 8-12.
[11] ABBAS G, LI Lin, GHAZANFAR U, LIU Zhu. Effect of high power diode laser surface melting on wear resistance of magnesium alloys[J]. Wear, 2006, 260: 175-180.
[12] ZHANG Jin, SUN Zhi-fu. Research on magnesium alloy AZ91D surface coating by metallizing aluminum[J]. China Mechanical Engineering, 2002, 13(23): 2057-2058.
[13] LIANG Yong-zheng, HAO Yuan, YANG Gui-rong, LI Yuan-dong. AZ91D magnesium alloy surface coating by electro-arc spraying aluminum[J]. Materials for Mechanical Engineering, 2005, 29(3): 29-31.
(Edited by LONG Huai-zhong)
Foundation item: Projects(2005BB4079, 2004BA4002) supported by the Natural Science Foundation of Chongqing City,China
Corresponding author: HUANG Wei-jiu; Tel: +86-23-68667300; E-mail: huangweijiu@cqit.edu.cn