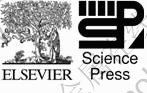
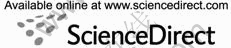
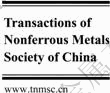
Trans. Nonferrous Met. Soc. China 22(2012) 2255-2260
Control method of chalcopyrite passivation in bioleaching
PAN Hao-dan1, YANG Hong-ying1, TONG Lin-lin1, ZHONG Cong-bin2, ZHAO Yu-shan3
1. School of Materials and Metallurgy, Northeastern University, Shenyang 110819, China;
2. College of Science, Northeastern University, Shenyang 110819, China;
3. College of Resource and Civil Engineering, Northeastern University, Shenyang 110819, China
Received 5 April 2012; accepted 26 June 2012
Abstract: Passivation is a common phenomenon on the surface of chalcopyrite in the process of bioleaching. The ordinary leaching and strengthening leaching by adding glass beads were carried out. The results show that the passivation of chalcopyrite was greatly weakened in strengthening leaching due to the change of leaching conditions. The copper leaching efficiency was increased from 50% to 89.8% through adding beads. The SEM and X-ray diffraction (XRD) analyses illustrate that there are few jarosite precipitates and weak passivation on the surface of chalcopyrite in strengthening leaching. In contrast, there are thick and compact jarosite precipitate and obvious passivation in ordinary leaching, which hinders further dissolution of chalcopyrite.
Key words: passivation; chalcopyrite; bioleaching; leaching; jarosite
1 Introduction
Chalcopyrite (CuFeS2) is one of the most wide-spread and refractory copper containing minerals. It occurs in various copper deposits [1-3]. Recently, the technique of copper bioleaching has been developed rapidly due to its advantages such as short flow, simple operation, low investment and friendly environment [4,5], which breaks a new way for green exploitation of copper ore. However, the bottlenecks of bioleaching, such as low leaching rate and efficiency, limit its development [6-9] because the insoluble passivation layer on the surface of the chalcopyrite significantly hiders the leaching efficiency [10-12]. Various leaching methods have been proposed from laboratory in order to accelerate the dissolution of chalcopyrite. There are different options to enhance chalcopyrite leaching. TODD et al [13] and WEN et al [14] retarded the speed of chalcopyrite passivation by lowering pH of the solution. But [H+] could reduce again due to the acid consumption of the gangue mineral and bacteria. It needs to keep the pH at a constant value by frequently changing the environment of the bacterial growth and mineral leaching, which will reduce the activity of the bacteria. Some researchers [15,16] attempted to increase the leaching efficiency of chalcopyrite through adjusting [Fe2+] and maintaining the potential at about 450 mV. It is difficult to prevent the formation of sulphate and jarosite layer on the surface of chalcopyrite. C?RDOBA et al [17] and XIA et al [18] leached the chalcopyrite with mesophiles and thermophiles. However, it can also be observed that strong jarosite precipitation on the surface of the mineral hindered the bacterial attack at high temperature [19-21].
In this work, the glass beads are used to strengthen stirring. The environment for the chalcopyrite leaching is greatly improved and the passivation of the chalcopyrite is weakened by a simple method. The copper leaching efficiency is increased significantly.
2 Experimental
2.1 Leaching bacteria
The mixed thermophilic leaching bacteria were provided by Biometallurgy Lab of Northeastern University. It has better antitoxic characteristics and oxidative abilities of sulphur and ferrous ions [22].
2.2 Ore samples
The chalcopyrite samples from Shandong Province of China were produced after flotation. The chemical compositions are listed in Table 1. The granularity distribution of the fine grinding ore is listed in Table 2. Above 60% chalcopyrite granularity is <37 μm. Figure 1 shows the X-ray diffraction (XRD) pattern of the chalcopyrite. It indicates that the main compositions of the ore are chalcopyrite and pyrite.
Table 1 Main elements and composition of chalcopyrite concentrate (mass fraction, %)

Table 2 Granularity distributions of chalcopyrite concentrate (mass fraction, %)

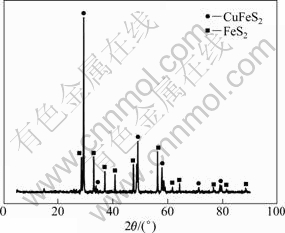
Fig. 1 XRD pattern of primary chalcopyrite ore
2.3 Microorganism culture
The culture medium of bacteria was the 9K medium [23]. The composition was as follows: 3.0 g/L (NH4)2SO4, 0.1 g/L KCl, 0.5 g/L K2HPO4, 0.5 g/L MgSO4?7H2O, 0.01 g/L Ca(NO3)2, 44.3 g/L FeSO4?7H2O. All chemical reagents used were of analytical grade.
2.4 Experiment procedure
The biooxidation experiments were carried out in Erlenmeyer flasks, which were put into an constant temperature shaker incubator shaken with 185 r/min at 44 ℃. Ten conical flasks with the volume of 500 mL were divided into two groups for different samples. The first group was for ordinary leaching experiment. The mass concentration of pulp was 5%, and the initial pH was adjusted to 1.6 with H2SO4. The other group was for strengthening leaching experiment. The stirring was strengthened by adding 5 g glass beads with 5 mm of diameter into the pulp.
2.5 Measurement
The potential value was measured by PHS-25 pH meter. The reference electrodes were 213 platinum electrode and 217 saturated calomel electrode, respectively. Cu2+ concentration was measured by EDTA spectrophotometry with Optizen 2120UV ultraviolet photometer. Fe2+ concentration was measured by potassium dichromate titrimetric method. The granularity distribution of the chalcopyrite concentrate was measured by 2000E Malvern laser particle size analyzer.
The morphologies were observed by SSX-550 scanning electron microscope (SEM)/energy disperse spectroscope (EDS) produced by Japan Shimadzu Company. The phases of the ores were analyzed by D/MAX-RB X-ray diffractometer produced by Netherland.
3 Results and discussion
3.1 Potential and Fe2+ concentration
Figures 2 and 3 show the variation of potential and Fe2+ concentration ([Fe2+]) in the process of bioleaching, respectively. The potential is higher in the ordinary leaching than that in the strengthening leaching, while [Fe2+] is lower in the ordinary leaching than in the strengthening leaching. Taking ordinary leaching for example, the leaching process can be divided into three stages: the initial stage (0-9 d), the middle stage (9-18 d) and the later stage (18-30 d) shown in Fig. 2. In the initial stage, the potential of solution firstly decreases sharply and then increases slowly. It is because Fe preferentially dissolves from the ore, resulting in the increase of [Fe2+] to 8.32 g/L and the ratio of [Fe2+]/[Fe3+] increasing. The potential decreases from 509 mV to 419 mV after leaching for 3 d. As the time increases, [Fe2+] decreases from 8.32 g/L to 1.95 g/L due to its oxidation. The ratio of [Fe2+]/[Fe3+] is reduced and the potential rises to 458 mV. In the middle stage, Fe2+ is leached out from chalcopyrite and is oxidized to Fe3+. Since the speed of leaching is faster than the speed of oxidizing, the ratio of [Fe2+]/[Fe3+] also rises. The potential increases slowly from 458 mV on the 9th day to 527 mV on the 18th day. The leaching rate of Fe is extremely slow in the later stage. [Fe2+] is nearly reduced to zero after leaching for 24 d in ordinary leaching, while it takes 30 d in strengthening leaching. The potential ascends quickly to 696 mV after leaching for 30 d, when all Fe2+ is oxidized to Fe3+ in solution.
3.2 Copper leaching efficiency
The changes of copper leaching efficiency with bioleaching time in ordinary leaching and strengthening leaching are plotted in Fig. 4. It can be observed that the process of leaching can be divided into three stages: the initial stage (0-9 d), the middle stage (9-18 d) and the later stage (18-30 d) under both ordinary and strengthening leaching conditions. In the first stage, the activity of the bacteria is lower. Therefore, copper leaching efficiency increases slowly, which is approximately 9.11% in the ordinary leaching and 11.41% in strengthening leaching on the 9th day. As the time increases to the middle stage, the bacteria activity is enhanced after it get used to the environment. As a result, copper leaching efficiency rises sharply under the direct oxidation of bacteria to ore. However, the leaching efficiency is 83.51% in strengthening leaching, much higher than that (44.11%) in the ordinary leaching on the 18th day. In the later stage, copper leaching efficiency nearly ceases due to the decline of the bacteria activity. It reaches about 89.86% in strengthening leaching, while it is 50.14% in ordinary leaching after leaching for 30 d. It indicates that the passivation is enhanced as the activity decreases and potential increases (above 600 mV) in ordinary leaching. In contrast, copper leaching efficiency is higher in strengthening leaching; the passivation is probably suppressed due to the addition of glass beads. The result is consistent with the fact that the leaching efficiency is higher at lower potential [24,25].
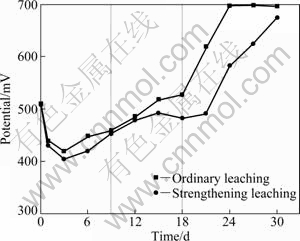
Fig. 2 Potential changes with bioleaching time
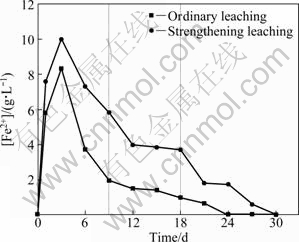
Fig. 3 [Fe2+] changes with bioleaching time
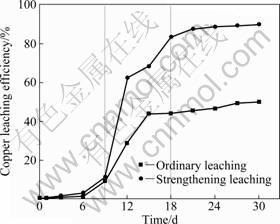
Fig. 4 Copper leaching efficiency changes with bioleaching time
3.3 Analysis of leaching residue
3.3.1 XRD pattern
Figure 5 presents the XRD patterns of the residues after leaching for 5 d (the initial stage), 10 d (the middle stage) and 25 d (the later stage) in ordinary and strengthening leaching, respectively. It can be observed that the main composition of the residue is chalcopyrite, pyrite and sulfur after leaching for 5 d (Fig. 5(a)). They are the same in ordinary leaching and strengthening leaching. The sulfur is probably formed by reaction (1) [26-28]. After leaching for 10 d, the main composition of the residue in ordinary leaching is also the same as that in strengthening leaching. Compared with the residue 5 d ago, jarosite appears as a new component (Fig. 5(b)). The jarosite is presumably formed by ferric ion hydrolysis according to reaction (2). As the leaching time increases to the 25th day, the compositions of the residue maintains the same in ordinary and strengthening leaching (Fig. 5(c)), which are chalcopyrite, pyrite and jarosite. Moreover, the XRD results show that the composition after 25 d remains the same as that after 10 d. It indicates that the residue does not change with increasing the leaching time.
CuFeS2+4Fe3+→Cu2++5Fe2++2S0 (1)
K++3Fe3++2SO42-+6H2O→KFe3(SO4)2(OH)6+6H+ (2)
3.3.2 SEM morphology
Figure 6 shows the morphologies of the residues after ordinary and strengthening leaching of 5 d (the initial stage). It can be observed that some cracks occur on the surface of chalcopyrite due to the bacterial oxidation. The mineral particles are in irregular polygonal shape with a few deposits on its surface. The granularity of the particles is similar to the original chalcopyrite, which is <37 μm counting for 62% approximately. In contrast, the share of <37 μm increases to 78% in strengthening leaching. The granularity of the ore particles is reduced resulting from the grinding of the glass beads. In this stage, the copper leaching efficiency is 1.25% in ordinary leaching and 2.98% in strengthening leaching (Fig. 4).
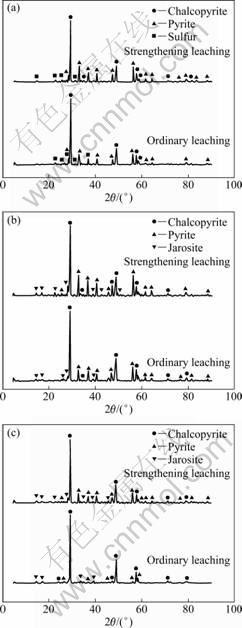
Fig. 5 XRD patterns of leaching residue after ordinary and strengthening leaching: (a) 5 d; (b) 10 d; (c) 25 d
Figure 7 displays the SEM morphologies of the leaching residue after 10 d of ordinary and strengthening leaching (the middle stage). More cracks are observed on the surface of chalcopyrite due to the further oxidation. Most surface areas of chalcopyrite are covered by the loose jarosite deposits in ordinary leaching (Fig. 7(a)). The share of ore particles with the size of <37 μm reduces from 62% to 60.1%, indicating the increase of granularity in ordinary leaching. In strengthening leaching, it is difficult for the jarosite to attach to the surface of chalcopyrite due to the grinding action of the glass beads (Fig. 7(b)). Thus the leaching area is more than that of the ordinary leaching, and the copper leaching efficiency is 24% higher than that of the ordinary leaching (Fig. 4).
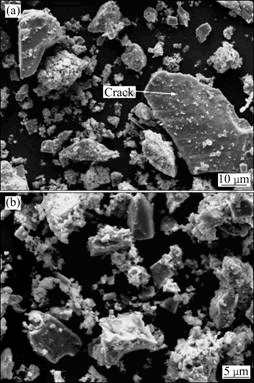
Fig. 6 Morphologies of leaching residue after 5 d of ordinary leaching (a) and strengthening leaching (b)
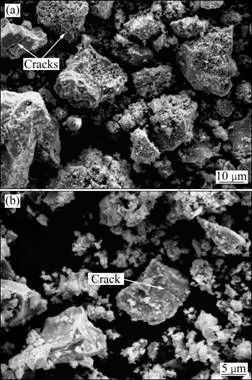
Fig. 7 Morphologies of leaching residue after 10 d of ordinary leaching (a) and strengthening leaching (b)
SEM micrographs collected from the bioleached residues after bioleaching for 25 d in two leaching conditions are shown in Fig. 8. In ordinary leaching, the arris of the ore particles disappear completely due to the cover of the jarosite deposits (Fig. 8(a)), which prevents transportation of both electrons and ion species between the mineral surface and the leaching medium. Therefore, the copper leaching efficiency nearly ceases (Fig. 4). The granularity in the size of <37 μm reduces from 60.1% to 48.9% because of the deposits. In strengthening leaching, visible corrosion holes can be observed on the surface of naked ore particles (Fig. 8(b)). In this condition, jarosite deposits also occur, but they are broken by the impacting and grinding actions of the glass beads. The copper leaching efficiency is 88.5% in strengthening leaching, which is twice higher than that in ordinary leaching (46.6%) after the same leaching time.
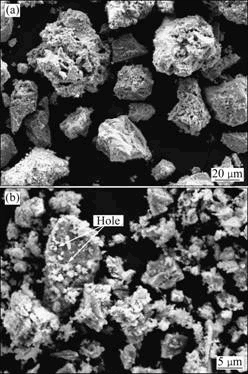
Fig. 8 Morphologies of leaching residue after 25 d of ordinary leaching (a) and strengthening leaching (b)
In order to further verify the inhibiting effects of the passivation film on the chalcopyrite surface, 5 g glass beads were added in the residue after leaching for 30 d and the shaking leaching was continued at constant temperature. The results show that compact jarosite film was formed on the surface of the ore particles after leaching for 30 d (Fig. 9(a)). However, it was broken in 30 min after adding 5 g glass beads, resulting in the exposure of fresh surface of the chalcopyrite (Fig. 9(b)). Moreover, the fraction of the particles in the size of <37 μm increased from 48.9% to 70.1%. The comparative results before and after adding glass beads indicate that the strengthening leaching conditions not only effectively inhibit the formation of the passive film, but also strengthen the leaching from the chalcopyrite with compact passivation film. The impact and friction peel the passivation film from the ore particles and promote the further leaching.
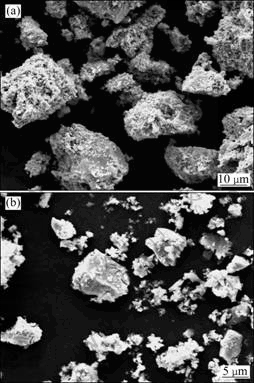
Fig. 9 SEM morphologies of residues: (a) After original leaching for 30 d; (b) Further strengthening leaching for 30 min after original leaching for 30 d
4 Conclusions
1) Potential was lower in the strengthening leaching, which is favored for the chalcopyrite leaching.
2) Jarosite can be observed in both the ordinary leaching and strengthening leaching. However, it was broken by the glass beads instead of attaching to the chalcopyrite. The surface of chalcopyrite with compact passivation film can be peeled from the ore particles in 30 min by strengthening leaching with the exposure of fresh surface of chalcopyrite.
3) The granularity of the ore particles was much smaller in strengthening leaching than in ordinary leaching resulting from the grinding of glass beads. It led to higher copper leaching efficiency due to the bigger specific surface area of the ore particle.
4) Ordinary shaking in chalcopyrite leaching was enhanced by adding the glass beads into the pulp. It significantly weakened the passivation of chalcopyrite. The copper leaching efficiency was increased from 50% to 89.8% obviously after leaching for 30 d.
References
[1] DREISINGER D, ABED N. A fundamental study of the reductive leaching of chalcopyrite using metallic iron (Part I): Kinetic analysis [J]. Hydrometallurgy, 2002, 66: 37-57.
[2] DUTRIZAC J E. The kinetics of dissolution of chalcopyrite in ferric ion media [J]. Metallurgical Transactions B, 1978, 9: 431-439.
[3] BRIERLEY J A. Acidophilic thermophilic archaebacteria: Potential application for metals recovery [J]. FEMS Microbiology Letters, 1990, 75(2-3): 287-291.
[4] YANG Hong-ying, YANG Li. Bacterial metallurgy [M]. Beijing: Chemical Industry Press, 2006: 10-18. (in Chinese)
[5] SMITH R W, MISRA M, DUBEL J. Mineral bioprocessing and the future [J]. Minerals Engineering, 1991, 4(7-11): 1127-1141.
[6] STOTT M B, WATLING H R, FRANZMANN P D, SUTTON D. The role of iron-hydroxy precipitates in the passivation of chalcopyrite during bioleaching [J]. Minerals Engineering, 2000, 13(10-11): 1117-1127.
[7] BEVILAQUA D, LEITE A L L C, GARC?A O, TUOVINEN O H. Oxidation of chalcopyrite by acidithiobacillus ferrooxidans and acidithiobacillus thiooxidans in shake flasks [J]. Process Biochemistry, 2002, 38(4): 587-592.
[8] DEVECI H, AKCIL A, ALP I. Bioleaching of complex zinc sulphide using mesophilic and thermophilic bacteria: Comparative importance of pH and iron [J]. Hydrometallurgy, 2004, 73(3-4): 293-303.
[9] PAN Hao-dan, YANG Hong-ying, CHEN Shi-dong, LI Wei-tao. Study of passivation phenomenon on chalcopyrite surface under different conditions [C]//Memoir of the 8th Annual Conference of Transactions of Nonferrous Metals Society of China. Beijing: The Nonferrous Metals Society of China, 2010: 146-151. (in Chinese)
[10] XIA Le-xian, TANG Lu, XIA Jin-lan, YIN Chu, CAI Li-yuan, ZHAO Xiao-juan, NIE Zhen-yuan, LIU Jian-she, QIU Guan-zhou. Relationships among bioleaching performance, additional elemental sulfur, microbial population dynamics and its energy metabolism in bioleaching of chalcopyrite [J]. Transactions of Nonferrous Metals Society of China, 2012, 22(1): 192-198.
[11] ZHANG Yan-sheng, QIN Wen-qing, WANG Jun, ZHEN Shi-jie, YANG Cong-ren, ZHANG Jian-wen, NAI Shao-shi, QIU Guan-zhou. Bioleaching of chalcopyrite by pure and mixed culture [J]. Transactions of Nonferrous Metals Society of China, 2008, 18(6): 1491-1496.
[12] YANG Hong-ying, PAN Hao-dan, TONG Lin-lin, LIU Yuan-yuan. Formation process of biological oxide film on chalcopyrite crystal surface [J]. Acta Metallurgica Sinica, 2012(9): 1145-1152. (in Chinese)
[13] TODD E C D, SHERMAN M, PURTON J A. Surface oxidation of chalcopyrite (CuFeS2) under ambient atmospheric and aqueous (pH 2-10) conditions: Cu, Fe L- and O K-edge X-ray spectroscopy [J]. Geochimica et Cosmochimica Acta, 2003, 67(12): 2137-2146.
[14] WEN Jian-kang, YAO Guo-cheng, CHEN Bo-wei, WU Biao, LIU Xue, HUANG Song-tao. Effect of pH on activities of mineral-bioleaching microorganisms and bioleaching rate [J]. Chinese Journal of Rare Metals, 2009, 33(1): 80-83. (in Chinese)
[15] VILC?EZ J, SUTO K, INOUE C. Bioleaching of chalcopyrite with thermopiles: Temperature–pH–ORP dependence [J]. International Journal of Mineral Processing, 2008, 88(1-2): 37-44.
[16] SANDSTR?M ?, PAUL J. XPS characterization of chalcopyrite chemically and bio-leached at high and low redox potential [J]. Minerals Engineering, 2005, 18(5): 505-515.
[17] C?RDOBA E M, MU?OZ J A, BL?ZQUEZ M L, GONZ?LEZ F, BALLESTER A. Leaching of chalcopyrite with ferric ion (Part IV): The role of redox potential in the presence of mesophilic and thermophilic bacteria [J]. Hydrometallury, 2008, 93(3-4): 106-115.
[18] XIA Jin-lan, YANG Yi, HE Huan, LIANG Chang-li, ZHAO Xiao-juan, ZHENG Lei, MA Chen-yan, ZHAO Yi-dong, NIE Zhen-yuan, QIU Guan-zhou. Investigation of the sulfur speciation during chalcopyrite leaching by moderate thermophile Sulfobacillus thermosulfidooxidans [J]. International Journal of Mineral Processing, 2010, 94(1-2): 52-57.
[19] D’HUGUES P, FOUCHER S, GALL?-CAVALLONI P, MORIN D. Continuous bioleaching of chalcopyrite using a novel extremely thermophilic mixed culture [J]. International Journal of Mineral Processing, 2002, 66(1-4): 107-119.
[20] GOMEZ E, BLAZQUEZ M L, BALLESTER A, GONZALEZ F. Study by SEM and EDS of chalcopyrite bioleaching using new thermophilic bacteria [J]. Minerals Engineering, 1996, 9(9): 985-999.
[21] TONG Lin-lin, YANG Hong-ying, ZHANG Yao, ZHANG Gu-ping. Effect of Acidithiobacillus ferrooxidans on leaching out chalcopyrite and pentlandite [J]. Journal of Northeastern University: Natural Science, 2010, 31(11): 1590-1593. (in Chinese)
[22] PAN Hao-dan, YANG Hong-ying, CHEN Shi-dong. Conditions for bio-sorption measuring on chalcopyrite surface [J]. Journal of Northeastern University: Natural Science, 2010, 31(7): 999-1002. (in Chinese)
[23] SILVERMAN M, LUNDGREN D. Studies on the chemoautotrophic iron bacterium Ferrobacillus ferrooxidans: I. An improved medium and a harvesting procedure for securing high cell yields [J]. Journal of Bacteriology, 1959, 77(5): 642-647.
[24] YU Run-lan, ZHONG Dai-li, MIAO Lei, WU Fa-deng, QIU Guan-zhou, GU Guo-hua. Relationship and effect of redox potential, jarosites and extracellular polymeric substances in bioleaching chalcopyrite by acidithiobacillus ferrooxidans [J]. Transactions of Nonferrous Metals Society of China, 2011, 21(7): 1634-1640.
[25] HIROYOSHI N, KITAGAWA H, TSUNEKAWA M. Effect of solution composition on the optimum redox potential for chalcopyrite leaching in sulfuric acid solutions [J]. Hydrometallurgy, 2008, 91(1-4): 144-149.
[26] DUTRIZAC J E. Elemental sulphur formation during the ferric sulphate leaching of chalcopyrite [J]. Canadian Metallurgical Quarterly, 1989, 28(4): 337-344.
[27] MAJIMA H, AWAKURA Y, HIRATO T, TANAKA T. The leaching of chalcopyrite in ferric chloride and ferric sulfate solutions [J]. Canadian Metallurgical Quarterly, 1985, 24(4): 283-291.
[28] MU?OZ P B, MILLER J D, WADSWORTH M E. Reaction mechanism for the acid ferric sulfate leaching of chalcopyrite [J]. Metallurgical Transaction B, 1979, 10: 149-158.
生物浸出过程中黄铜矿钝化的控制方法
潘颢丹1,杨洪英1,佟琳琳1,仲崇斌2,赵玉山3
1. 东北大学 材料与冶金学院,沈阳 110819;2. 东北大学 理学院,沈阳 110819;
3. 东北大学 资源与土木工程学院,沈阳 110819
摘 要:在细菌浸出黄铜矿的过程中,黄铜矿表面钝化是普遍现象,成为生物浸铜技术的瓶颈问题。对比研究了普通浸出与强化浸出(加入玻璃圆珠)对铜浸出的影响。结果表明,玻璃圆珠的加入改善了浸出条件,削弱了黄铜矿的钝化效应,使黄铜矿的Cu浸出率从50%提升至89.8%。扫描电镜(SEM)和X射线衍射(XRD)分析发现,添加玻璃圆珠的黄铜矿表面没有黄钾铁矾沉淀,钝化作用不明显;而不加玻璃圆珠的黄铜矿表面附着厚厚的结构致密的黄钾铁矾,钝化严重,从而阻碍了黄铜矿的溶解和浸出。
关键词:钝化;黄铜矿;细菌浸出;浸出;黄钾铁钒
(Edited by YUAN Sai-qian)
Foundation item: Projects (51174062, 51104036, 50874030) supported by the National Natural Science Foundation of China; Projects (2012AA061502) supported by the High-tech Research and Development Program of China; Projects (N100602007) supported by the Fundamental Research Funds for the Central Universities, China
Corresponding author: YANG Hong-ying; Tel: +86-24-83673932; E-mail: yanghy@smm.neu.edu.cn
DOI: 10.1016/S1003-6326(11)61457-X