由方铅矿精矿直接制备硫酸铅粉末材料的方法
覃文庆, 刘 辉, 孙 伟
(中南大学 资源加工与生物工程学院, 湖南 长沙, 410083)
摘要: 针对硫酸铅传统生产工艺存在工艺流程长, 能耗和成本高的缺点, 以方铅矿为研究对象, 通过三步法即三氯化铁浸出方铅矿精矿、选择性除杂和化学沉淀法,将硫化铅精矿直接转化为硫酸铅粉末材料。 研究结果表明: 产品转化率为97.39% , 纯度超过99%,平均晶粒粒度约为32 nm; 与传统生产工艺相比, 采用三步法不但可以简化工艺流程, 节约能耗, 降低生产成本, 而且在工艺过程中无铅蒸汽和二氧化硫等气体产生, 可以实现硫酸铅的清洁生产。
关键词: 硫酸铅; 方铅矿; 制备; 浸出
中图分类号:TF803.23 文献标识码:A 文章编号: 1672-7207(2005)03-0407-05
Method of direct preparation of lead sulfate
powders from galena concentrates
QIN Wen-qing, LIU Hui, SUN Wei
(School of Minerals Processing and Bioengineering, Central South University, Changsha 410083, China)
Abstract: In traditional process of lead sulfate there exists some disadvantages such as longer flow and higher energy-consumption. In order to explore a new process to produce PbSO4, the methods of three-step, including the leaching of galena concentrates in ferric chloride media, the selective purification and the method of chemical sedimentation, is developed to convert PbS concentrates into PbSO4. The results show that the conversion rate reaches 97.39%, and the purity of PbSO4 powder is above 99% with the calculated particle size of crystallites of 32 nm. In this process, the emission of lead vapour and SO2 cannot be produced. Compared with traditional process, the production process can be simplified and the energy consumption can be decreased, and cleaner production of PbSO4 can be realised.
Key words: lead sulfate; galena; preparation; leaching
硫酸铅作为一种重要的化工粉末材料,被广泛用于涂料和电池等行业[1,2]。 其传统生产工艺是将方铅矿精矿经火法冶炼得到粗铅, 将粗铅电解精炼得到电解铅, 再经高温熔融、 造粒、 磨粉、 氧化焙烧制取氧化铅, 最后通过氧化铅硫酸法制得[3,4]。 这一工艺流程长, 能耗高, 还会产生铅蒸汽、 二氧化硫和铅尘,因而对环境造成很大危害, 挥发出来的有毒物质不仅会危害工人身体健康, 而且会给当地的大气和水造成严重污染,为此,必须寻找生产硫酸铅的更有效的方法。 目前, 许多科研工作者对湿法炼铅工艺进行了大量研究[5-13], 然而, 由于技术本身存在不足或生产成本偏高等, 这些工艺至今仍仅停留在实验室或中小规模生产上,致使铅的湿法生产难以工业化。 这些研究主要是采取硫化铅精矿浸出及熔盐电解制铅的技术, 而很少采用湿化学法直接制备铅盐化工产品的方法。 在此, 作者采用湿化学法研究从方铅矿精矿直接制取硫酸铅粉末材料的可行性, 通过因素实验, 结合XRD和SEM产品表征和纯度分析, 对这一具体转化过程进行研究。
1 实 验
1.1 原 料
原料为方铅矿精矿,取自广东凡口铅锌矿, 其中, 粒度小于0.074 mm的方铅矿占85%(质量分数), 其化学成分见表1。
表 1 方铅矿精矿化学成分分析结果
Table 1 Chemical composition of galena
concentrates %

1.2 试剂及仪器
实验所用试剂均为化学纯物质, 包括1 mol/L的H2SO4, 1 mol/L的HCl,以及FeCl3·6H2O和NaCl。
实验仪器主要有: D60型电子搅拌器;pHS-3C型电位pH计; DK-8型恒温水浴槽和SHB-Ⅲ型循环水式真空泵等。 最终产品通过d/Max-Ra型X衍射仪(Cu靶, λ=0.154056 nm)和KYKY-2800型扫描电镜分别对方铅矿进行物相和表面形貌分析。
1.3 实验原理及方法
1.3.1 浸出过程原理
由于硫化铅中的硫处于最低价态, 选用强氧化剂三氯化铁浸出, 加入适量的NaCl和盐酸, 可将不溶物硫化铅转化为可溶性的铅盐, 不但浸出反应速度快, 而且氯化铅在该体系中的溶解度较大。 在浸出过程中, 氯离子起了重要作用, 在饱和氯化钠溶液中, 它可与氯化铅迅速络合形成[PbCl4]2-, 使氯化铅的溶解度梯度增大,溶液体系电位降低, 从而促进浸出反应的发生。 另外, 加入少量盐酸, 维持溶液pH〈2, 其目的是避免铁离子和氯化铅发生水解反应。 浸出反应机理可看作是氧化溶解与非氧化溶解之间的竞争反应。
氧化机理为:
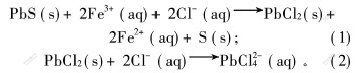
非氧化机理为:
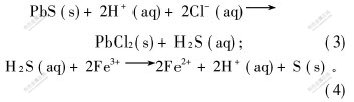
例如,在反应初期, Fe3+与H+的浓度比相对较高, Fe3+迅速与方铅矿发生(1)和(2)的反应, 浸出过程以氧化溶解为主, 因而反应前期几乎无H2S气体冒出。 而在反应后期, 由于溶液中Fe3+与H+的浓度比降低, 即H+的相对浓度提高, 浸出过程逐渐以非氧化溶解为主, 并伴随有少量的H2S气体生成。
1.3.2 浸出实验方法
首先, 取200 mL水置于500 mL的玻璃烧杯中, 加入一定量的HCl, 调溶液pH=0.5~1.0, 加入适量的NaCl和FeCl3·6H2O, 待反应温度达到给定值后, 立刻加入方铅矿精矿, 并启动搅拌器, 在预设的反应时间、 温度和搅拌强度下进行反应。 待反应结束, 趁热过滤, 分离出残渣, 并将浸取液静置于冰水混合物中约2 h, 促使反应(2)向逆方向进行, 使PbCl42-不断转化成PbCl2晶体析出, 过滤浸出液, 即可得到PbCl2晶体。
通过向滤液中添加少量的H2O2,可将大部分Fe2+转化为Fe3+,实现浸出剂的回收再利用。 另外, 对浸出过程中生成的少量硫化氢气体, 通入NaOH溶液, 将其转化为Na2S副产品。 浸出过程如图1所示。
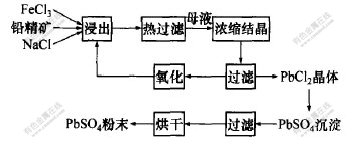
图 1 PbSO4产品转化流程图
Fig. 1 Flowchart of preparing PbSO4
products by PbS concentrates
1.3.3 化学沉淀法合成硫酸铅的原理及方法
在室温时, 往溶液中滴加1 mol/L H2SO4, 恒速搅拌, 下列反应即可发生:

反应式(5)是PbSO4的转化方程式。 其298 K时的反应吉布斯自由能为-3.89 kJ/mol, 而且PbSO4和PbCl2溶解度常数相差较大(分别为1.7×10-8和1.6×10-5), 因而, 从热力学上说, 该反应在常温下可以顺利进行。
通过控制合适的反应条件, 使PbCl2完全转化为PbSO4。 待反应结束后, 陈化2 h, 过滤, 并利用PbCl2在热水中溶解度增大的特点, 用热蒸馏水反复洗涤产品以除去残留在产品表面的PbCl2沉淀, 烘干, 即可得到硫酸铅粉末产品。
2 结果和讨论
2.1 因素实验
对浸出过程的几个主要影响因素包括搅拌速度、 反应时间、 反应温度和浸出液浓度对浸出反应速度的影响进行实验研究。 在实验中, 除另有规定外, 保持下列条件不变: pH=0.5~1.0, 液固比为20 m3/t, 方铅矿精矿质量为10 g。
不同的搅拌速度和反应时间对方铅矿浸出率的影响如图2所示。 可以看出, 搅拌速度对浸出率影响不大, 故选取搅拌速度为1600 r/min作为其他因素实验的条件。
![]()
70 ℃, 250 g/L NaCl, 65 g/L FeCl3·6H2O
转速/(r·min-1):1—1200; 2—1600; 3—1800
图 2 搅拌速度对方铅矿浸出率η的影响
Fig. 2 Effect of stirring velocity on leaching
rate of galena concentrate
反应时间和三氯化铁质量浓度对方铅矿浸出率的影响如图3和图4所示。 可见, 随着反应时间或三氯化铁质量浓度的增加, 方铅矿浸出率增加。
反应温度对方铅矿浸出率的影响如图5所示。 可见, 随着温度的升高, 方铅矿浸出率呈线性增加, 从节约能耗的角度出发, 选取80 ℃作为下一步反应的温度条件。
NaCl质量浓度对方铅矿浸出率的影响如图6所示。 可以看出, 当NaCl质量浓度低于250 g/L时,方铅矿浸出率明显增加; 高于250 g/L之后, 其值几乎保持不变。 说明此时的浸出体系为NaCl饱和溶液体系。
![]()
1600 r/min, 75 g/L FeCl3·6H2O, 250 g/L NaCl, 80 ℃
图 3 反应时间t对方铅矿浸出率η的影响
Fig. 3 Effect of reaction time on leaching
rate of galena
![]()
1600 r/min, 80 ℃, 40 min, 250 g/L NaCl
图 4 三氯化铁质量浓度ρ(FeCl3)对方铅矿浸出率η的影响
Fig. 4 Effect of ferric chloride concentration
on leaching rate of galena
![]()
1600 r/min, 75 g/L FeCl3·6H2O, 250 g/L NaCl
图 5 反应温度对方铅矿浸出率η的影响
Fig. 5 Effect of temperature on leaching rate
of galena
![]()
1600 r/min, 80 ℃, 40 min, 75 g/L FeCl3·6H2O
图 6 NaCl质量浓度ρ(NaCl)对方铅矿
浸出率η的影响
Fig. 6 Effect of NaCl concentration on
leaching rate of galena
2.2 最佳浸出条件的确定
综合以上实验结果, 可得出如下最佳浸出条件:
a. 液固比为20 m3/t, pH=0.5~1.0;
b. NaCl质量浓度为250 g/L;
c. FeCl3·6H2O质量浓度为75 g/L;
d. 反应温度为80 ℃, 反应时间为40 min;
e. 搅拌强度为1600 r/min。
在上述最佳浸出条件下, 方铅矿精矿的转化率达到97.39%。
2.3 产品的制备、表征及纯度分析
2.3.1 产品的制备和表征
控制合适的转化条件, H2SO4与PbCl2的量比为2, 搅拌速度为700 r/min,在室温下反应30 min,可制得所需的粉末产品。
取该样品进行X衍射分析, 结果如图7所示。 可见, 其峰位和峰强值与JCPDS(36-1461) 卡片上的数值完全吻合,晶胞参数a=0.69575 nm, b=0.84763 nm, c=0.53982 nm, 说明合成得到的产品为正交晶系的PbSO4粉末;衍射峰较锐,表明产品纯度较高, 结晶程度完好。 同时也说明控制合适的反应条件, 可实现PbCl2向PbSO4完全转化。
为进一步了解粉末产品的晶粒尺寸, 可利用谢乐(Scherrer)公式[14]对其进行估算。 其计算公式为:

其中: Dc为产品平均晶粒度; K为Scherrer常数,K=0.94; λ为X射线波长; λ=0.154056 nm; β为由晶粒大小引起的衍射线条变宽时衍射峰的半峰宽; θ为衍射角。经计算, PbSO4粉末材料的平均晶粒度约为32 nm。
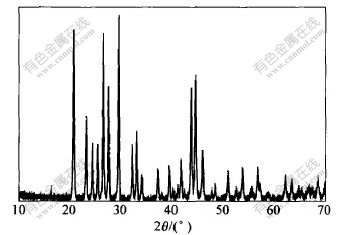
图 7 PbSO4的XRD图谱
Fig. 7 XRD pattern of PbSO4 powders
结合该产品的扫描电镜照片(见图8)发现, 该结果与图8中观测到的晶粒尺寸存在偏差, 这很可能是团聚现象所致。 通过比较不同放大倍数下的扫描电镜图(图8(a)和8(b))可以看出, PbSO4晶粒互相粘连成片状, 表明有团聚现象发生。
![]()
(a) 高倍(×2000); (b)低倍(×500)
图 8 PbSO4的SEM图谱
Fig. 8 SEM images of PbSO4 powders
2.3.2 产品纯度分析
对方铅矿精矿、 PbCl2晶体、 PbSO4粉体进行化学纯度分析比较, 结果如表2所示。 可以看出, PbSO4中的杂质含量低于0.01%, 纯度超过99%, 高于市场上化工企业生产PbSO4的质量标准(98%)[1]。
表 2 产品杂质元素分析结果
Table 2 Contents of individual lead compounds %

3 结 论
a. 浸出工艺最佳条件如下:固液比为20 m3/t,pH=0.5~1.0, 反应温度为80 ℃, NaCl质量浓度为250 g/L, FeCl3·6H2O质量浓度为75 g/L, 转速为1600 r/min, 反应时间为40 min。 在该最佳工艺条件下, 浸出率最高达97.39%。
b. 采用热过滤、 冷却结晶和化学沉淀的方法能达到选择性除杂的目的, 硫酸铅产品的纯度超过99%。 XRD和 SEM分析结果显示, 产品平均晶粒度约为32 nm, 晶粒间相互粘连, 成片状团聚。
c. 利用三步法即浸出-选择性除杂-化学沉淀法将PbS精矿直接转化为PbSO4粉末材料,与传统生产工艺相比, 不但可以简化工艺流程,节约能耗, 降低生产成本, 而且工艺过程中无铅蒸汽和二氧化硫等气体产生,实现了硫酸铅的清洁生产。
参考文献:
[1]司徒杰生. 化工手册(第2版)[M].北京: 化工出版社, 1993:793-795.
SITU Jie-sheng. Handbook of chemical products(2nd ed)[M]. Beijing: Chemical Technology Press,1993:793-795.
[2]赵乃良, 时蕊.硫酸铅产品质量影响因素的研究[J]. 黑龙江科技学院学报, 2001,11(3): 20-25.
ZHAO Nai-liang, SHI Rui. Research on the factors affecting the quality of lead sulphate[J]. Journal of Heilongjiang Institute of Science and Technology, 2001,11(3):20-25.
[3]索因,乔治.硫化矿冶炼的进展(第2卷)[M].包晓波, 邓文基,译.北京: 冶金工业出版社, 1991:118-132.
Sohn Y, George B. Advance in sulfide smelting(2nd ed)[M]. BAO Xiao-bo, DENG Wen-ji, translate. Beijing: Metallurgy Industry Press, 1991:118-132.
[4]《铅锌冶金学》编委会. 铅、 锌冶金学[M].北京: 科学出版社, 2003:178-210.
Editorial Committee of Metallurgy of Lead and Zinc. Metallurgy of lead and zinc[M]. Beijing: Science Press, 2003: 178-210.
[5]Kobayashi M. A critical review of the ferric chloride leaching of galena[J]. Can Metall Q, 1990, 29(3): 201-211.
[6]Alan A. The ferric fluosilicate leaching of lead concentrates[J]. Met Trans B, 1994, 25(5): 473.
[7]Dutrzac J E, Chen T T. The leaching of galena in ferric sulphate media[J]. Metallurgical and Materials Tan(B), 1995, 26: 219-227.
[8]Mark P. Model for the ferric chloride leaching of galena[J]. Metallurgical and Materials Transactions B, 1998, 29: 953-959.
[9]Luengos M A, Ambrosio E, Bohe A E, et al. Thermal behaviour of galena ore in the chloride atmosphere[J]. Journal of Thermal Analysis and Calorimetry, 2000, 59: 775-789.
[10]ZHANG Ying-jie,YANG Xian-wan,DENG Lun-hao, et al. Leaching mechanism of sulfide ores in slurry electrolysis[J]. Trans Nonferrous Met Soc China, 2000, 10(1): 105-108.
[11]GONG Ya-jun, CHEN Jia-yong. Kinetics of conversion of galena into lead carbonate in ammonium carbonate solution in the presence of cupric ion[J]. Hydrometallurgy, 1993, 33: 177-195.
[12]Breza M, Manova A. Study on the structure of lead(Ⅱ) complexes in aqueous solution[J].Polyhedron,1999, 18: 2085.
[13]黄惠忠. 纳米材料分析[M].北京: 化学工业出版社, 2003.
HUANG Hui-zhong. Analysis of nanometer materials[M]. Beijing: Chemistry Industry Press, 2003.
[14]Balaz P, Boldizarova E, Godocikova E, et al. Mechanochemical route for sulphide nanoparticles preparation[J]. Materials Letters, 2003, 57: 1585-1589.
收稿日期:2004 -06 -25
基金项目:国家自然科学基金资助项目(50204013)
作者简介:覃文庆(1969-), 男, 湖南宁乡人,教授,博士, 从事浮选电化学、生物提取的研究
论文联系人: 覃文庆,男,教授,博士; 电话: 0731-8879815(O)