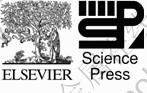
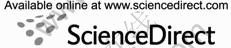
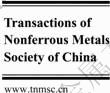
Trans. Nonferrous Met. Soc. China 22(2012) 1540-1548
Effect of heat treatment on microstructures and mechanical properties of sand-cast Mg-4Y-2Nd-1Gd-0.4Zr magnesium alloy
LIU Zhi-jie1, WU Guo-hua1, LIU Wen-cai1, PANG Song1, DING Wen-jiang1,2
1. National Engineering Research Center of Light Alloy Net Forming, School of Materials Science and Engineering, Shanghai Jiao Tong University, Shanghai 200240, China;
2. Key State Laboratory of Metal Matrix Composite, Shanghai Jiao Tong University, Shanghai 200240, China
Received 30 August 2011; accepted 30 September 2011
Abstract: Influence of heat treatment on the microstructures and mechanical properties of sand-cast Mg-4Y-2Nd-1Gd-0.4Zr magnesium alloy was investigated, and the tensile fracture mechanisms of the studied alloys under different conditions were also discussed. The results show that the optimum T4 and T6 heat treatment conditions for the as-cast Mg-4Y-2Nd-1Gd-0.4Zr alloy are 525 ℃, 8 h and (525 ℃, 8 h)+(225 ℃, 16 h), respectively, with regard to the microstructure observation, DSC heating curve and mechanical properties. The hardness, yield strength, ultimate tensile strength and elongation of the Mg-4Y-2Nd-1Gd-0.4Zr alloy treated by optimum T6 heat treatment are HV91, 180 MPa, 297 MPa and 7.4%, respectively. Moreover, the Mg-4Y-2Nd-1Gd-0.4Zr alloys under different heat treatment conditions exhibit different tensile fracture modes.
Key words: Mg-4Y-2Nd-1Gd-0.4Zr alloy; sand-casting; heat treatment; mechanical property
1 Introduction
In recent years, as weight reduction demands for automobile and aircraft body are becoming the world focus, magnesium alloys are becoming one of the key engineering materials due to their low density and high specific strength and stiffness [1-3]. It has been demonstrated that rare earth metals (RE) are the most effective elements to improve the strength properties of magnesium especially [4,5]. The strength of these Mg–RE alloys is achieved essentially via precipitation hardening [6], which is higher than that of conventional Al or Mg alloys. Among them [7,8], the Mg-Y-Nd-Gd serial alloys are recent new developed high strength magnesium alloy, which exhibits higher strength and good heat resisting compared with the other Mg-RE alloy. Some investigations related to the microstructure and mechanical properties of the Mg-Y-Nd-Gd serial alloys produced by metal mould with high cooling rate have been reported [9-13]. With regard to the mechanical properties, the Mg-Y-Nd-Gd serial alloys will have a good prospect in aerospace industry. It should be noted that the aerospace parts are usually produced by sand mould casting with low cooling rate due to its complex structure.
However, up to now, less reports about research on the sand mould casting with a low cooling rate of the Mg-Y-Nd-Gd alloy can be available. The aim of the present study was to investigate the effect of heat treatments on the microstructures and mechanical properties of Mg-4Y-2Nd-1Gd-0.4Zr magnesium alloy produced by sand mould casting with a low cooling rate. Particular emphasis was put on finding out the optimum heat treatment condition.
2 Experimental
The material used in this work was an Mg-4Y-2Nd-1Gd-0.4Zr (mass fraction, %) alloy, which can be produced by sand mould casting. Mg-25Y, Mg-25Nd, Mg-25Gd and Mg-30Zr master alloys were made first by melting high-purity elemental Mg (>99.95%), Y (>99.9%), Nd (>99.9%) and Gd (>99.9%) in a vacuum medium-frequency induction furnace under an argon atmosphere. An alloy ingot was then prepared from high-purity Mg (99.95%), Mg-25Y, Mg-25Nd, Mg-25Gd and Mg-30Zr master alloys in an electric resistance furnace under the mixed atmosphere of CO2 and SF6 with the volume ratio of 100:1, and cast in a sand mould. The real chemical composition was determined to be Mg–3.4Y–1.9Nd–0.9Gd–0.4Zr by an inductively coupled plasma analyzer (Perkin Elmer, Plasma-400).
In order to obtain the optimum T4 and T6 heat treatment conditions of the studied alloy, the differential scanning calorimetry (DSC, STA 449 F3) was carried out using under-argon atmosphere with a heating rate of 10 K/min. Firstly, specimens were solution treated at 500 ℃, 525 ℃ and 540 ℃ for 6-12 h, and then quenched into water at room temperature. Secondly, after optimizing the solution treatment condition, specimens were isothermally aged at 225 ℃ and 250 ℃ for different time in an oil-bath. The aging response of the specimens was checked by hardness measurement. Vickers hardness testing was carried out using 49 N load and holding time of 20 s. For convenience, the studied alloy was referred to as WNG421.
Specimens for mechanical testing were machined with the load axis parallel to the casting direction of the as-cast alloy. The tensile properties of the WNG421 alloys under different conditions were determined at an initial strain rate of 5×10–4 s–1 using sheet specimens with the nominal dimension of 15 mm in gauge length, 3.6 mm in width and 2 mm in thickness on Zwick/Roell Z020 tensile machine at room temperature. Microstructure of the investigated alloys was observed by optical microscopy (OM). Phase composition and fracture surface after tensile were analyzed by scanning electron microscopy (SEM, Philip-505).
3 Results
3.1 Microstructures
Figure 1 shows the microstructure of the as-cast WNG421 alloy. As seen from Fig. 1, the microstructure of the as-cast alloy consists of equiaxed α-Mg matrix and networks eutectic compounds at the grain boundaries. Its average grain size determined by linear intercept method is 70-80 μm. Based on the experimental results in Ref. [7], the eutectic compounds in the as-cast WNG421 alloy are Mg24Y5.

Fig. 1 Microstructure of as-cast WNG421 alloy
In order to obtain the optimum T6 heat treatment condition of the studied alloy, firstly, we studied the optimum T4 heat treatment condition. The temperature of T4 solution treatment for the WNG421 alloy was determined on the basis of literature data [7], Mg-Y, Mg-Nd and Mg-Gd phase diagrams, and DSC curves. Figure 2 shows the DSC curve of cooling and heating. It can be seen that the peak reaction temperature is about 546.9 ℃. Accordingly, the solution treatment (T4) temperature and time of the specimens were restricted in the range of 500-540 ℃ and 6-12 h respectively, as shown in Table 1.
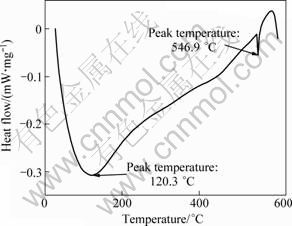
Fig. 2 DSC heating curve of as-cast WNG421 alloy
Table 1 Solution treatment parameters of WNG421 alloy
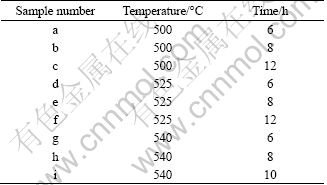
The principle of parameter optimization of T4 solution treatment is that the eutectic phases of the as-cast alloy almost dissolve into the matrix after solution treatment. High temperature and long time for solution treatment should be guaranteed. However, higher solution temperature and time will cause grain growth or overheating, and deteriorate the mechanical properties of the studied alloy.
The microstructural evolution with solution temperature and time is shown in Fig. 3. At 500 ℃ for 6 h, the morphology of the Mg24Y5 phase became thin and its amount decreased (see Fig. 3(a)) compared with that in the as-cast alloy (see Fig. 1). With increasing the solution time at 500 ℃, the Mg24Y5 phase decreases gradually (see Figs. 3(a)-(c)). However, at the temperature for different holding time, the Mg24Y5 phase has not dissolved into the matrix. It is obvious that the solution temperature of 500 ℃ is too low.
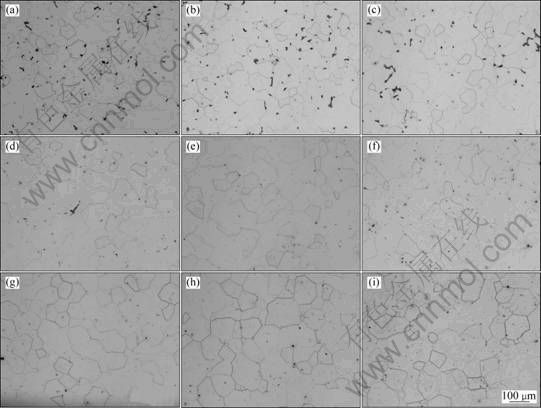
Fig. 3 Microstructures of WNG421 alloys under different solution treatment conditions: (a) 500 ℃, 6 h; (b) 500 ℃, 8 h; (c) 500 ℃, 12 h; (d) 525 ℃, 6 h; (e) 525 ℃, 8 h; (f) 525 ℃, 12 h; (g) 540 ℃, 6 h; (h) 540 ℃, 8 h; (i) 540 ℃, 10 h
As seen from Figs. 3(d)-(i), after solution treatment at 525 ℃ and 540 ℃, almost Mg24Y5 phase disappeared, and some cuboid-shaped particles unevenly distributed in the matrix were found. At 525 ℃ for 8 h, the average grain size is 70-80 μm, which is almost same with the as-cast alloy (see Fig. 3(e)). However, the grain grows with increasing the solution temperature and time, and the average grain size of the WNG421 alloy treated at 525 ℃ for 12 h grew up to 80-90 μm (see Fig. 3(f)). The grain further grew at 540 ℃, and the average grain size even reached 110 μm (see Figs. 3(g)-(h)). Based on the above analysis, the optimum solution treatment condition for the WNG421 alloy is at 525 ℃ for 8 h.
As mentioned above, after solution heat treatment, some cuboid-shaped particles unevenly distributed along grain boundaries and in grain interiors could be found (see Fig. 3). The SEM image of the cuboid-shaped particles is shown in Fig. 4(a). It can be seen that those cuboid-shaped particles contains a dominant proportion of Y (80%) with energy dispersive X-ray (EDX) detector, and small amounts of Nd and Gd, as shown in Fig. 4(b). The composition of the cuboid-shaped particles in sand-cast WNG421 alloy in the present work is different from that in metal mould cast alloy [7]. That is, the particles in metal mould cast WNG421 alloy are Mg41Nd5 and Mg24Y5.
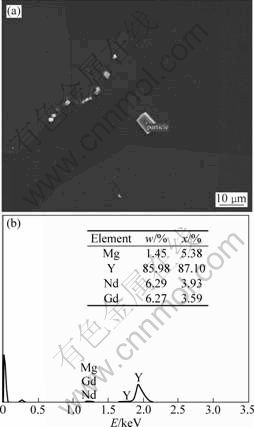
Fig. 4 SEM image (a) and EDX spectrum (b) of cuboid-shaped particles in solution-treated alloy
A small amount of cuboid-shaped particles could be found in the as-cast alloy (see Fig. 5(a)). However, after solution treatment at 500 ℃ for 8 h, the majority of the eutectic compounds in Fig. 1 are dissolved into the matrix and the cuboid-shaped particles increase obviously. Meanwhile, the size of the cuboid-shaped particles also gradually grows (see Fig. 5(b)). At 525 ℃ for 8 h, the eutectic compounds almost dissolve into the matrix, and the cuboid-shaped particles also further increase (see Fig. 5(c)). Therefore, the cuboid-shaped particles probably have two origins. On one hand, initial formation of some particles must take place during casting process of alloy, and solution treatment caused growth of those particles in size. On the other hand, solution heat treatment also causes increase of particles in quantity. Similar cuboid-shaped particles were previously observed in some other Mg-RE alloys [14]. According to the study of cuboid-shaped particles in Mg-5Y-3Nd-Zr-xGd alloy, there are not similar particles in Mg-5Y-3Nd-Zr alloy, while some particles could be found in Mg-5Y-3Nd-Zr-4Gd alloy. Based on the EDX analysis and electron diffraction analysis, Mg5RE phase can be confirmed [14], which is different from cuboid-shaped particles in this work.
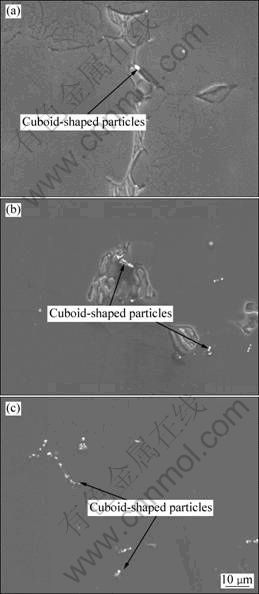
Fig. 5 SEM images of WNG421 alloys under different conditions: (a) As-cast; (b) T4, (500 ℃, 8 h); (c) T4, (525 ℃, 8 h)
3.2 Aging characteristics
Figure 6 shows the aging hardness curves of the solution-treated (at 525 ℃ for 8 h) and isothermally aged at 225 ℃ and 250 ℃ WNG421 alloy. Compared with the as-cast specimen, the hardness is improved by aging treatment. We can see that the hardness of the solution-treated WNG421 alloy depends on the aging time at all aging temperatures. Especially at the aging temperature of 225 ℃, the dependence is more evident, namely, with the increase in the aging time, the hardness first dramatically increases, then slowly decreases. The decrease is a result of over-aging. The gap between two curves increases gradually two hours later. After ageing at 225 ℃ for 16 h, WNG421 alloy gets the peak hardness of HV90.7. While aged at 250 ℃, it needs 12 h to get peak hardness of HV75.4. With regard to the hardness value (see Fig. 6), the aging condition of (225 ℃, 16 h) is taken as the optimum for the solution-treated (at 525 ℃ for 8 h) WNG421 alloy.
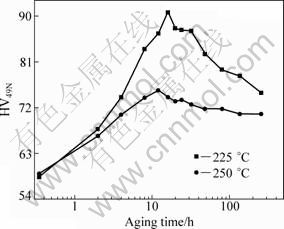
Fig. 6 Aging hardness curves of solution-treated (at 525 ℃ for 8 h) WNG421 alloy at aging temperatures of 225 ℃ and 250 ℃
3.3 Mechanical properties
A comparison of the tensile properties of the WNG421 alloy under different aging conditions is shown in Fig. 7, and the corresponding heat treatment conditions and tensile properties under different aging conditions are listed in Table 2. As seen from Fig. 7, similar to the hardness in Fig. 6, compared with the as-cast alloy, large improvements of the yield strength (YS) and ultimate tensile strength (UTS) are observed from the T6 treated WNG421 alloy, while the elongation (EL) is also slightly increased, which can be explained by the solid solution and precipitation strengthening. Comparatively, precipitation strengthening at 225 ℃ is higher than that at 250 ℃, namely, tensile strength improvement of the tested alloy aging-treated at 225 ℃ is higher than that of the tested alloy aging-treated at 250 ℃. By treatment of (525 ℃, 8 h)+(225 ℃, 16 h), the peak YS and UTS of 180 MPa and 297 MPa of the WNG421 alloy were observed, and the improvement of 40 MPa and 76 MPa compared with the as-cast alloy have been achieved. Hence, (525 ℃, 8 h)+(225 ℃, 16 h) is believed the optimized heat treatment condition.

Fig. 7 Tensile properties of solution-treated WNG421 alloys under different aging treatment conditions at room temperature
3.4 Fractography
Figure 8 shows the optical microstructures of ruptured samples of the WNG421 alloy under different conditions perpendicular to fracture surface, which deformed at room temperature during tensile test. The WNG421 alloy shows different secondary crack morphologies under different conditions. In as-cast alloy, the secondary microcracks are observed along grain boundaries (see Fig. 8(a)), mainly inside the eutectics. Because eutectics are more rigid and brittle than Mg matrix, it is easier for dislocations to be accumulated in the eutectics and cause stress concentration, and initiate micro-cracks during tensile test. Besides, the eutectics with large size and snatchy shape are more likely to initiate micro-cracks due to more serious stress concentration. Twinning is an especially important deformation mechanism for HCP magnesium alloys, in which five independent slip systems that are necessary for arbitrary shape change are not easily activated at room temperature. In this condition, twinning has little relation with the formation of secondary cracks as the secondary cracks all initiate by the break of eutectics. After T4 solution treatment at 525 ℃ for 8 h, the eutectics along grain boundaries disappear, and the secondary cracks mainly locate in grain interiors and twining (see Fig. 8(b)). In this condition, twinning plays an important role in the cracks initiation, and it is easy for cracks to initiate at twining and spread along the twinning. Aged at 225 ℃ for 16 h and 250 ℃ for 12 h, the micro-cracks mainly distribute in grain boundaries (see Figs. 8(c) and (d)). In those conditions (see Figs. 8(b)-(d)), some twinning is also found. It probably has close relation with the secondary cracks. The microcracks probably initiate at the interfaces between twinning and grain boundaries and spread along the twinning boundaries.
Table 2 Tensile properties of solution-treated WNG421 alloy and corresponding aging conditions
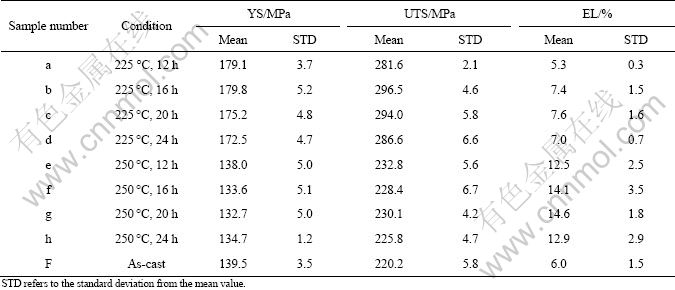
Figure 9 shows the fracture surfaces of tensile specimens of the WNG421 alloy under different conditions. As seen from Fig. 9, the whole fracture surface of alloys inclines to the loading axis and is close to the plane with a maximum shear force. In the as-cast alloy (see Fig. 9(a)), we can see that there are intergranular fracture mechanisms. The fracture planes are cracked along crystal interface of the eutectic structures, which are indicated by the arrow. In addition, the whole failure surface is composed of fractured eutectics and cleavage planes. This indicates that after the microcrack forms inside the eutectics, it progresses along the grain boundaries by connecting with other microcracks or crossing the grains as cleavage fracture. Therefore, the fracture mode of the as-cast alloy is quasi-cleavage. This result is consistent with result of Ref. [13]. When the alloy is subjected to T4 solution heat treatment (see Fig. 9(b)), the fracture surface is mainly composed of cleavage planes that are larger compared with as-cast alloy, and the fracture mode of T4 treated alloy is transgranular cleavage fracture. After peak-aging at 225 ℃ for 16 h, the fracture surface mainly consists of cleavage planes and grain boundaries (see Fig. 9(c)), and shows a transgranular and intergranular mixed fracture. After aging at 250 ℃ for 12 h, the alloy exhibits ductile transgranular fracture features of coarse dimples and tear ridges, which is in accordance with its high elongation of 12.5% (see Fig. 9(d)). Its fracture mode is typical
quasi-cleavage.
The fracture mechanism of the WNG421 alloy under different conditions is schematically illustrated in Fig. 10. In the as-cast alloy, the cracks initiate by the break of eutectics and propagate trans-granularly (see Fig. 10(a)). After solution treatment, due to the disappearance of eutectics, the micro cracks mainly locate at the grain interiors and also travel trans-granularly (see Fig. 10(b)). After peak-aging, the grain interior is strengthened by precipitates compared with the soft grain interior under the as-cast and solution-treated conditions. The cracks start along the grain boundaries and propagate inter-granularly (see Fig. 10(c)).
4 Discussion
The eutectic temperature (546.9 ℃) of the sand-cast WNG421 alloy was detected as the temperature of the first endothermic peak was obtained in the DSC trace. Comparatively, the average grain size of the sand-cast alloy in the present work is 70-80 μm, and obviously larger than the metal-cast alloy (60-70 μm) in Ref. [7], which can be explained by the low cooling rate during sand-casting process. However, the optimal solution conditions of the two alloys are both at 525 ℃ for 8 h with regard to the DSC heating curve and microstructure evolution. After solution treatment, the eutectic Mg24Y5 phase dissolved into the matrix, and induced slight solid solution strengthening in the solution treated WNG421 alloy.

Fig. 8 Optical images of longitudinal section of fracture surfaces of WNG421 alloy under different conditions: (a) As-cast; (b) T4, (525 ℃, 8 h); (c) T6, (525 ℃, 8 h)+(225 ℃, 16 h); (d) T6, (525 ℃, 8 h)+(250 ℃, 12 h)
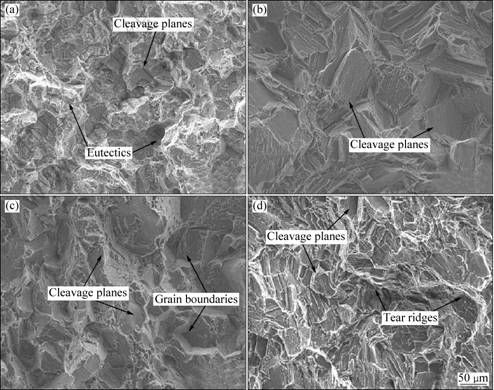
Fig. 9 Typical SEM images showing fracture surfaces of tensile tested alloys: (a) As-cast; (b) T4, (525 ℃, 8 h); (c) T6, (525 ℃, 8 h)+(225 ℃×16 h); (d) T6, (525 ℃, 8 h)+(250 ℃, 12 h)
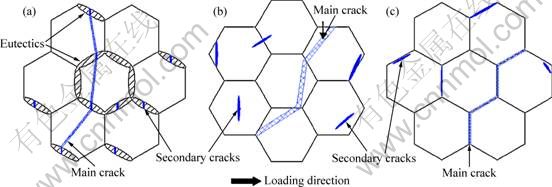
Fig. 10 Schematic diagrams showing secondary crack location and propagation of main crack of WNG421 alloy under different conditions: (a) As-cast alloy; (b) Solution-treated alloy; (c) Peak-aged alloy [7]
For magnesium alloy with HCP crystal structure, the precipitation hardening induced by aging treatment is an important strengthening mode on the tensile properties. The optimization of aging temperature and time depends on research of precipitation mechanism. The decomposition of α-Mg supersaturated solid solution (S.S.S.S) in Mg-Y-Nd-RE alloy has been studied well by NIE and MUDDLE [6] and ANTION et al [15]. With the increase in aging time, the precipitation sequence consists of the following steps: S.S.S.S.(CPH)→ β″(DO19) →β′(CBCO)→β1(FCC)→β (FCC). Metastable β″ and β′ phases coexist in the matrix at the under-aging stage. At the peak-aging stage, β′ precipitates form at the beginning of the steep hardness increase and then grow into prismatic plates that contribute to the hardness maximum. At the over-aging stage, the β phase appears via an in situ transformation from the decomposed β1 phase, and both of them grow in a direction that is different from the direction of the previous β′ phase growth [6,15,16]. Comparatively, the strengthening effect of the β′ phase on mechanical properties at the peak-aging stage is higher than that of β or β1 phase at the under-aging and over-aging stages. Therefore, compared with the solution treated WNG421 alloy, it is believed that the improvement of tensile strength for aging-treated alloy is mainly contributed to precipitation hardening of β′ phase [17]. The change of hardness, mechanical properties and crack ignition of different aging treatments are mainly associated with different precipitates in kind, shape, distribution, volume fraction, and number density. According to Refs. [6,18], after aging at 250 ℃ for 48 h, the β′ is wholly replaced by β1 and β. Due to the differences of precipitates in kind, shape, and distribution, the long aging time at 250 ℃ probably leads to weaker precipitation hardening effect. Compared with the alloy peak-aged at the 250 ℃, the alloy peak-aged at 225 ℃ probably possesses finer and higher density β′ phases, which will induce higher precipitation hardening effect on the tensile properties. This work is now under study and will be reported in due course.
5 Conclusions
1) The microstructure of the sand-cast Mg-4Y-2Nd-1Gd-0.4Zr alloy mainly consists of α-Mg and eutectic compounds. After solution treatment, the eutectic compounds are almost dissolved into the matrix. Based on the microstructure evolution, the optimum solution treatment condition is at 525 ℃ for 8 h.
2) The Mg-4Y-2Nd-1Gd-0.4Zr alloy exhibits considerable precipitation hardening. Aged at 225 ℃ and 250 ℃, the tested alloys reach the peak hardness at 16 h and 12 h, respectively. The elongation of alloy aged at 250 ℃ is better than that of alloy aged at 225 ℃, while the strength of the latter is higher than that of the former obviously. With regards to the tensile properties and hardness, the optimum T6 heat treatment condition is (525 ℃, 8 h)+(225 ℃, 16 h), the corresponding yield strength, ultimate tensile strength, elongation and hardness are 180 MPa, 297 MPa, 7.4% and HV91, respectively.
3) The Mg-4Y-2Nd-1Gd-0.4Zr alloy under different conditions shows different fracture modes. The fracture modes for the as-cast, T4 solution treated, peak-aged of 225 ℃, and peak-aged of 250 ℃ alloys are intergranular quasi-cleavage, transgranular cleavage, mixed transgranular and intergranular fracture, and typical quasi-cleavage, respectively.
References
[1] MORDIKE B L, EBERT T. Magnesium properties-application- potential [J]. Materials Science Engineering A, 2001, 302(1): 37-45.
[2] WANG Ying-xin, GUAN Shao-kang, ZENG Xiao-qin, DING Wen-jiang. Effects of RE on the microstructure and mechanical properties of Mg-8Zn-4Al magnesium alloy [J]. Materials Science and Engineering A, 2006, 416(1-2): 109-118.
[3] LIU Wen-cai, DONG Jie, ZHANG Ping, YAO Zhen-yi, ZHAI Chun-quan, DING Wen-jiang. High cycle fatigue behavior of as-extruded ZK60 magnesium alloy [J]. Journal of Materials Science, 2009, 44(11): 2916–-2924.
[4] YU Kun, LI Wen-xian, WANG Ri-chu, MA Zheng-qing. Research, development and application of wrought magnesium alloys [J]. The Chinese Journal of Nonferrous Metals, 2003, 13(2): 277-287. (in Chinese)
[5] LIU Wen-cai, DONG Jie, ZHANG Ping, JIN Li, PENG Tao, ZHAI Chun-quan, DING Wen-jiang. Fatigue behavior of hot-extruded Mg-10Gd-3Y magnesium alloy [J]. Journal of Materials Research, 2010, 25(4): 773-783.
[6] NIE Jian-feng, MUDDLE B C. Precipitation in magnesium alloy WE54 during isothermal aging at 250 ℃ [J]. Scripta Materialia, 1999, 40(10): 1089-1094.
[7] FU Peng-huai, PENG Li-ming, JIANG Hai-yan, ZHANG Zheng-yan, ZHAI Chun-quan. Fracture behavior and mechanical properties of Mg-4Y-2Nd-1Gd-0.4Zr (wt. %) alloy at room temperature [J]. Materials Science and Engineering A, 2008, 486(1-2): 572-579.
[8] AVEDESIAN M M, BAKER H. Magnesium and magnesium alloys [M]. Ohio: The Material Information Society, 1999.
[9] WILSON R, BETTLES C J, MUDDLE B C, NIE Jian-feng. Precipitation hardening in Mg-3%Nd-(Zn) casting alloys [J]. Materials Science Forum, 2003, 419-422: 267-272.
[10] ROKHLIN L L. Magnesium alloys containing rare earth metals [M]. London: Taylor and Francis, 2003.
[11] HE Shang-ming, ZENG Xiao-qin, PENG Li-ming, GAO Xiang, NIE Jian-feng, DING Wen-jiang. Precipitation in a Mg–10Gd–3Y–0.4Zr (wt. %) alloy during isothermal aging at 250 ℃ [J]. Journal of Alloys and Compounds, 2006, 421(1-2): 309-313.
[12] ZHENG Kai-yun, DONG Jie, ZENG Xiao-qin, DING Wen-jiang. Precipitation and its effect on the mechanical properties of a cast Mg-Gd-Nd-Zr alloy [J]. Materials Science and Engineering A, 2008, 489(1-2): 44-54.
[13] LIU Wen-cai, DONG Jie, SONG Xu, BELNOUE J P, HOFMANN F, DING Wen-jiang, KORSUNSKY A M. Effect of microstructures and texture development on tensile properties of Mg-10Gd-3Y alloy [J]. Materials Science and Engineering A, 2011, 528(6): 2250-2258.
[14] WANG Li-dong, XING Cheng-yao, HOU Xiu-li, WU Yao-ming, SUN Jian-fei, WANG Li-ming. Microstructures and mechanical properties of as-cast Mg-5Y-3Nd-Zr-xGd(x=0, 2, and 4 wt.% alloys [J]. Materials Science and Engineering A, 2010, 527: 1891-1895.
[15] ANTION C, DONNADIEU P, PERRARD F, DESCHAMPS A, TASSIN C, PISCH A. Hardening precipitation in a Mg-4Y-3RE alloy [J]. Acta Materialia, 2003, 51(18): 5335-5348.
[16] MENGUCCI P, BARUCCA G, RIONTINO G, LUSSANA D, MASSAZZA M, FERRAGUT R, HASSAN A E. Structure evolution of a WE43 Mg alloy submitted to different thermal treatments [J]. Materials Science and Engineering A, 2008, 479: 37-44.
[17] GAO Xiang, HE Shang-ming, ZENG Xiao-qing, PENG Li-ming, DING Wen-jiang, NIE Jian-feng. Microstructure evolution in a Mg-15Gd-0.5Zr(wt.%) alloy during isothermal aging at 250 ℃ [J]. Journal of Alloys and Compounds, 2006, 421: 309-313.
[18] NIE Jun-feng, MUDDLE B C. Characterisation of strengthening precipitate phase in a Mg-Y-Nd alloy [J]. Acta Materialia, 2000, 48: 1691-1703.
热处理对砂型铸造Mg-4Y-2Nd-1Gd-0.4Zr镁合金显微组织和力学性能的影响
刘志杰1,吴国华1,刘文才1,庞 松1,丁文江1,2
1. 上海交通大学 轻合金精密成型国家工程研究中心,上海 200240;
2. 上海交通大学 金属基复合材料国家重点实验室,上海 200240
摘 要:研究热处理工艺对砂型铸造Mg-4Y-2Nd-1Gd-0.4Zr镁合金显微组织和力学性能的影响,分析不同热处理条件下合金的断裂机制,获得最佳热处理工艺。结果表明:Mg–4Y–2Nd–1Gd–0.4Zr合金的最佳T4和T6热处理工艺分别为525 ℃,8 h 和(525 ℃,8 h)+(225 ℃,16 h)。在最佳T6热处理条件下,Mg-4Y-2Nd-1Gd-0.4Zr合金的硬度、屈服强度、抗拉强度和伸长率分别为HV91、180 MPa、297 MPa和7.4%。此外,不同状态的Mg-4Y-2Nd-1Gd-0.4Zr镁合金也显示出不同的拉伸断裂方式。
关键词:Mg-4Y-2Nd-1Gd-0.4Zr;砂型铸造;热处理;力学性能
(Edited by YANG Hua)
Foundation item: Project (0502) supported by the Aerospace Science and Technology Innovation Fund of China Aerospace Science and Technology Corporation; Project (2007CB613701) supported by the National Basic Research Program of China; Project (2009AA033501) supported by the National High-tech Research and Development Program of China
Corresponding author: WU Guo-hua; Tel: +86-21-54742630; E-mail: ghwu@sjtu.edu.cn
DOI: 10.1016/S1003-6326(11)61353-8