J. Cent. South Univ. Technol. (2007)01-0007-06
DOI: 10.1007/s11771-007-0002-7

Ratio of Fe-Al compound at interface of steel-backed Al-graphite semi-solid bonding plate
ZHANG Peng(张 鹏)1, DU Yun-hui(杜云慧)1, LIU Han-wu(刘汉武)1, ZHANG Jun(张 君)1,
ZENG Da-ben(曾大本)2, BA Li-min(巴立民)3
(1. Department of Mechanical Engineering, Beijing Jiaotong University, Beijing 100044, China;
2. Department of Mechanical Engineering, Tsinghua University, Beijing 100084, China;
3. Anshan Automobile Fittings Factory, Anshan 114014, China)
Abstract: The ratio of Fe-Al compound at the bonding interface of solid steel plate to Al-7graphite slurry was used to characterize the interfacial structure of steel-Al-7graphite semi-solid bonding plate quantitatively. The relationship between the ratio of Fe-Al compound at interface and bonding parameters (such as preheat temperature of steel plate, solid fraction of Al-7graphite slurry and rolling speed) was established by artificial neural networks perfectly. The results show that when the bonding parameters are 516 ℃ for preheat temperature of steel plate, 32.5% for solid fraction of Al-7graphite slurry and 12 mm/s for rolling speed, the reasonable ratio of Fe-Al compound corresponding to the largest interfacial shear strength of bonding plate is obtained to be 70.1%. This reasonable ratio of Fe-Al compound is a quantitative criterion of interfacial embrittlement, namely, when the ratio of Fe-Al compound at interface is larger than 70.1%, interfacial embrittlement will occur.
Key words: bonding interface; ratio of Fe-Al compound at interface; artificial neural network
1 Introduction
Steel backed Al-graphite bonding plate is made up of steel plate and Al-graphite layer. Steel plate has high strength, Al base has perfect thermal conductivity, and graphite has excellent lubricating property. Thus this bonding plate is an ideal material for neotype bearing. Compared with the common steel backed Al base bearing material such as steel-Al-Sn and steel-Al-Pb[1-2], steel-Al-graphite bonding plate has a wider range of usage temperature because the usage temperature of graphite (may be higher than 400 ℃[3]) can be much higher than that of Sn and Pb (usually lower than 150 ℃[4]). Therefore, this steel-Al-graphite bonding plate can also be used for high-temperature bearing and can find a wider application in many fields such as machinery and automobile fields.
For steel backed Al base bonding plate, the interfacial structure which determines the interfacial mechanical property is very important. Fe-Al solid solution and Fe-Al compound are component materials of interface of steel backed Al base bonding plate. When the interface is completely made up of Fe-Al solid solution (for example, the interface of solid steel plate to solid Al base plate), interfacial mechanical property is generally lower, usually only about 40 MPa[5]. When the interface is mainly made up of Fe-Al compound (for example, the interface of solid steel plate to Al base liquid), the interface becomes brittle, and the interfacial mechanical property is not very high, usually about 60 MPa[6]. When the interface is made up of Fe-Al compound and Fe-Al solid solution (for example, the interface of solid steel plate to Al base slurry), the interfacial mechanical property can be improved a lot[7]. Therefore, it is very important to determine the interfacial structure of the steel backed Al base bonding plate quantitatively.
In this study, the interfacial structure of steel-Al- 7graphite semi-solid bonding plate was investigated quantitatively using ratio of Fe-Al compound at interface. The relationship between ratio of Fe-Al compound at interface and bonding parameters (such as preheat temperature of steel plate, solid fraction of Al-7graphite slurry and rolling speed) was established by artificial neural networks, and the reasonable interfacial structure was determined.
2 Experimental
The materials used in this experiment were 1.2 mm-
thick 08Al steel plate and Al-7graphite (mass fraction) alloy which contains 1.5%Si.
The experimental procedures were as follows.
1) Treating the steel plate surface: Firstly defatting and descaling the surface to get fresh surface. Secondly immersing the surface in the aqueous solution of flux (K2ZrF6). The mass fraction of the solution was 7%. The temperature of the solution was 90 ℃. The immersing time was 1 min. These conditions could form a 10 μm-thick flux layer on the surface of steel plate. This flux layer could prevent the fresh surface from oxidizing. Thirdly stoving the steel plate at 200 ℃ for 1 min in order to remove water in the flux layer.
2) Preparing Al-7graphite slurry: Electromagnetic- mechanical stirring technique was used to prepare Al-7graphite slurry[8]. The precision of solid fraction of Al-7graphite slurry was ±1%.
3) Conducting steel-Al-7graphite semi-solid bond- ing: The experimental equipment is shown in Fig.1. The length of pour mouth was 200 mm. The diameter of roller was 320 mm. The precision of temperature was ±1 ℃. The precision of rolling speed was ±0.1 mm/s. And the thickness of bonding plate was 2.5 mm.
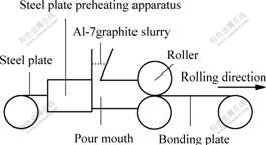
Fig.1 Schematic diagram of steel-Al-7graphite semi-solid bonding process
4) Cutting up the bonding plate into testing samples for SEM experiment using linear cutting method. The sample was a block of 10 mm×10 mm×2.5 mm. One side of this sample must be carefully ground, polished, eroded, cleaned and dried. The content of etching liquid was 0.5% HF, 1.5% HCl, 2.5% HNO3 and 95.5% H2O.
5) Conducting SEM experiment to observe the interfacial structure.
3 Results and discussion
3.1 Relationship between ratio of Fe-Al compound and bonding parameters
The bonding interface of solid steel plate to Al-7graphite slurry is made up of Fe-Al compound and Fe-Al solid solution alternatively[9]. According to the periodic structural characteristic, one period can be used to determine the interfacial structure of steel-Al- 7graphite semi-solid bonding plate quantitatively. L1/L is named as the ratio of Fe-Al compound at interface(see Fig.2), L1 is the length of Fe-Al compound in one period, L is the length of one period, namely, the sum of L1 and L2 (the length of Fe-Al solid solution in one period).
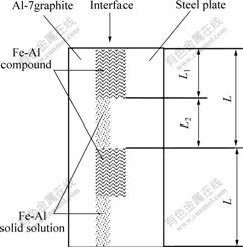
Fig.2 Interface of steel-Al-7graphite semi-solid bonding plate
It is well known that the formation of interface of steel backed Al base bonding plate is the result of diffusion of Al atoms to steel substrate and reaction with Fe atoms[10]. Therefore, the bonding parameters, which can influence the diffusion and reaction of Al atoms in bonding, have important effects on the interfacial structure of steel backed Al base bonding plate.
In steel-Al-7graphite semi-solid bonding, the bond- ing parameters such as the preheat temperature of steel plate, solid fraction of Al-7graphite slurry and rolling speed have some influences on ratio of Fe-Al compound at interface. There exists a complicated nonlinear relationship between the bonding parameters and the ratio of Fe-Al compound at interface. This relationship is rather difficult to or can not to be determined by conventional regression method.
Artificial neural network(ANN) has been widely used to realize modeling, estimation, prediction, diag- nosis and adaptive control in complex nonlinear system[11-17]. The back-propagation(BP) network is a multilayer feedforward and full-connected neural network. It has strong associative memory and generaliz- ation capabilities, and it can approximate any nonlinear continuous function with an arbitrary precision. Therefore artificial neural networks can be used to establish the relationship between bonding parameters and ratio of Fe-Al compound at interface in steel-Al-7graphite semi-solid bonding.
A 3-layered feed-forward neural network system with 3 neurons in the input layer, 2 in the hidden layer and 1 in the output layer was used in this study (see Fig.3). Layer Ⅰ is the input layer which uses linear elements Z1, Z2 and Z3 to represent the preheat temperature of steel plate, solid fraction of Al-7graphite slurry and rolling speed, respectively. Layer Ⅱ is the hidden layer which uses nonlinear elements. The input of element j is Nj which is the sum of the outputs of layer Ⅰ after timing weight respectively, and the output of element j is Yj which is the result of the nonlinear function of Nj named as f(x). Layer Ⅲ is the output layer which uses only one nonlinear element whose input N is the sum of the outputs of layer Ⅱ (Yj) after timing weight respectively, and the output, also the output of ANN, is the ratio of Fe-Al compound at interface (H) which is the result of the nonlinear function of N named as f(x). Vji is the connection weight between the input layer and the hidden layer, and Wj is the weight between the hidden layer and the output layer.

Fig.3 Back-propagation structure of ANN
The learning algorithm could be summarized as follows.
1) Selecting the learning rate h=0.1, momentum coefficient a=0.1 and Z4=Y3=-1.
2) Taking a group of random numbers within (-0.5, 0.5) as the initial values of Vji and Wj.
3) Computing the outputs of all neurons layer by layer, starting with the input layer as follows.
(1)
Yj=f(netj) (2)
(3)
H=f(net) (4)
f(x)=(1-e-x)/(1+ex) (5)
Vj4 and W3 offer thresholds for the neurons in the hidden layer and output layer because the output value of Z4 and Y3 are constant and equal to -1.
4) Computing system error as follows:
(6)
where P represents the total number of patterns, Hn are the ANN outputs and Dn the desired outputs.
5) If E is small enough or learning iteration is big enough, stopping learning.
6) Computing learning errors for all neurons layer by layer
δH=(D-H)f′(net) (7)
δj=WjδHf′(netj), j=1, 2 (8)
7) Updating weights along negative gradient of E
Wj(t+1)=Wj(t)+ηδHYj+α[Wj(t)-Wj(t-1)] (9)
Vji(t+1)=Vji(t)+ηδjZi+α[Vji(t)-Vji(t-1)] (10)
8) Repeating by going to step 3).
Randomly select 19 samples to train the ANN and the tested 5 samples to verify the generalization capabil- ity of the ANN. After 61 000 iterations, the outputs H of the ANN are close enough to the desired outputs D, not only for training samples but also for testing samples. The results are shown in Table 1. The maximum of relative error is 4.1%. This fact shows that the ANN is good enough.
3.2 Determination of reasonable ratio of Fe-Al com- pound at interface
The reasonable ratio of Fe-Al compound at interface is corresponding to the largest interfacial mechanical property. In the study on mechanical property of steel- Al-7graphite semi-solid bonding, the bonding parameters for the largest interfacial shear strength are obtained as 516 ℃ for preheat temperature of steel plate, 32.5% for solid fraction of Al-7graphite slurry and 12 mm/s for rolling speed. From these bonding parameters, the reasonable ratio of Fe-Al compound at interface is determined to be 70.1% using the relationship established by the artificial neural network.
3.3 Discussion
For Al-7graphite slurry, the primary solid particles distribute in liquid uniformly. In process of steel-Al- 7graphite semi-solid bonding, the primary solid particles and liquid in the uniform slurry contact with steel plate in some proportion respectively. The diffusion and reaction between Al-7graphite slurry and steel plate generate after the removal of flux layer from the surface of steel plate. Because Si content in Al-7graphite slurry is far lower than that of realizing the diffusion and reaction in steel substrate 2.5% (mass fraction)[18], the diffusion between Al-7graphite slurry and steel plate is mainly that of Al atoms in Al-7graphite slurry to steel substrate. The diffusion of Al atoms in steel substrate can be determined by FICK’s law as
Table 1 Results of ANN training and predication points
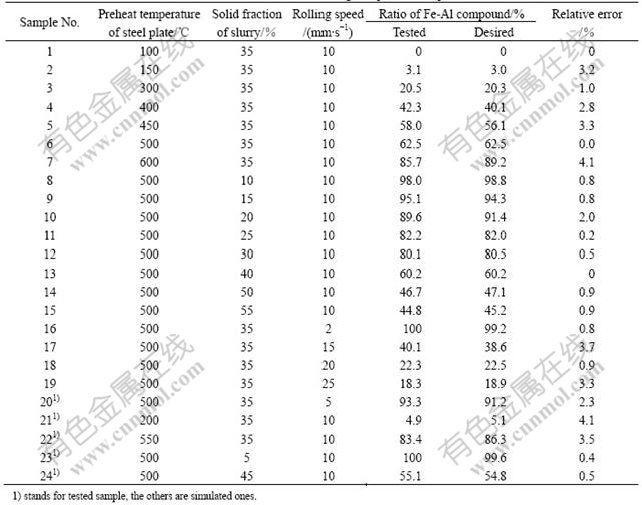
(11)
where C is the diffusion concentration of Al atoms in steel substrate, t is diffusion time, D is diffusion coefficient, x is diffusion distance. In this study, when t=0, C≈0 for x=0 and when x=0, C≈100% for t>0. Therefore, the analytic solution for Eqn.(11) is
, x≥0 (12)
The diffusion coefficient of liquid Al atom is greater because it has more energy[19-20]. Thus the diffusion concentration of Al atoms in steel substrate is higher in the contact region of steel plate and liquid. The reactions of Al atoms with Fe atoms could take place as follows:
Fe+3Al=FeAl3 (13)
Fe3C+9Al=3FeAl3+C (14)
2Fe+5Al=Fe2Al5 (15)
2Fe3C+15Al=3Fe2Al5+2C (16)
Thus Fe-Al compounds form. However, the diffusion coefficient of solid Al atom is smaller for it has less energy. Furthermore, the contact of primary solid particles with steel plate is not as compact as that of liquid with steel plate. Very limited diffusion of Al atoms occurs in steel substrate after the removal of flux layer from the surface of steel plate. Only Fe-Al solid solution forms at this ultra-small diffusion concentration of Al atoms in the contact region of steel plate and primary solid particles. Therefore, the periodic interface of steel-Al-7graphite semi-solid bonding plate is usually made up of Fe-Al compound and Fe-Al solid solution alternatively.
For steel-Al-7graphite semi-solid bonding, under the conditions of low preheat temperature of steel plate, large solid fraction of Al-7graphite slurry and high rolling speed, the diffusion and reaction of Al atoms are restricted. Fe-Al solid solution forms at the interface greatly. Only very little Fe-Al compound forms. So the ratio of Fe-Al compound at interface is rather smaller.
Fig.4 shows the typical interface of steel-Al- 7graphite semi-solid bonding plate with small ratio of Fe-Al compound at interface. The right side is 08Al steel plate. The left side is Al-7graphite layer. Regions 1 and 3 are Fe-Al compounds. Region 2 is Fe-Al solid solution. It can be seen that rather a few of Fe-Al compound forms at the interface.
With increasing preheat temperature of steel plate and decreasing solid fraction of Al-7graphite slurry and rolling speed, the diffusion and reaction of Al atoms increase gradually. More and more Fe-Al compounds form at the interface, and thus the ratio of Fe-Al compound at interface becomes larger and larger. When the diffusion of Al atoms generates sufficiently, the reaction of Al atoms with Fe atoms will take place at the whole interface. A continuous layer of Fe-Al compound forms and the ratio of Fe-Al compound at interface reaches 100% (see Fig.5).
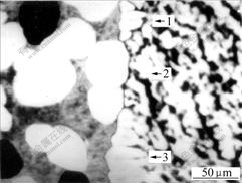
Fig.4 SEM image of interface with small ratio of Fe-Al compound
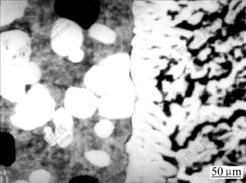
Fig.5 SEM image of interface with 100% ratio of Fe-Al compound
At the interface, Fe-Al solid solution forms by weaker bonding, and Fe-Al compound forms by stronger metallurgic bonding. When the ratio of Fe-Al compound at interface is smaller, too more Fe-Al solid solution at the interface results in the lower interfacial mechanical property directly. So this interfacial structure with too little Fe-Al compound is not good. However, when the ratio of Fe-Al compound at interface is too larger, too more Fe-Al compound will result in the interfacial embrittlement, and the interfacial mechanical property is also poor. When the ratio of Fe-Al compound at interface is 70.1%, Fe-Al compound at interface not only keeps the strong metallurgic bonding, but also avoids the interfacial embrittlement. Thus the interfacial mechanical property is the best and this interfacial structure is very reasonable. Therefore, 70.1% is a quantitative criterion of interfacial embrittlement, namely, when the ratio of Fe-Al compound is larger than 70.1%, the interfacial embrittlement will occur and the interfacial mechanical property will deteriorate. Fig.6 shows the typical reasonable interface of steel-Al-7graphite semi-solid bonding plate. The right side is 08Al steel plate. The left side is Al-7graphite layer. Regions 1 and 3 are Fe-Al compounds, and region 2 is Fe-Al solid solution.
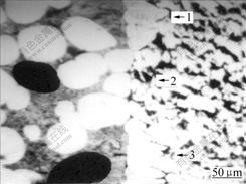
Fig.6 SEM image of interface with reasonable ratio of Fe-Al compound
4 Conclusions
1) The relationship between the ratio of Fe-Al compound at interface and bonding parameters (preheat temperature of steel plate, solid fraction of Al-7graphite slurry and rolling speed) in steel-Al-7graphite semi-solid bonding is established by artificial neural networks perfectly.
2) When the bonding parameters are 516 ℃ for preheat temperature of steel plate, 32.5% for solid fraction of Al-7graphite slurry and 12 mm/s for rolling speed, the reasonable ratio of Fe-Al compound at interface is 70.1%, which is corresponding to the highest interfacial mechanical property.
3) The ratio of Fe-Al compound at interface should not be larger than 70.1%. This value is a quantitative criterion of interfacial embrittlement. When ratio of Fe-Al compound at interface is larger than 70.1%, the interfacial embrittlement will occur.
References
[1] ZHANG Peng, DU Yun-hui. Study on steel-mushy Al-20Sn alloy bonding[J]. J Mater Sci Technol, 2000, 17(2): 224-227.
[2] ZHANG Peng, DU Yun-hui. Modeling and optimizing of steel and mushy Al-28Pb alloy bonding[J]. Trans Nonferrous Met Soc China, 2001, 11(2): 239-243.
[3] LI Shi-xian. Graphite[M]. Beijing: Chemistry Industry Press, 1991.(in Chinese)
[4] KENNETH B. Metal Base Composite Material[M]. Beijing: National Defense Industry Press, 1982: 45-68.
[5] QIN Hua, QI Fei-peng. Development of technique of hot-dip aluminizing for iron and steel parts[J]. Mater Mech Eng, 1995, 19(1): 32-35.(in Chinese)
[6] ZHANG Peng, DU Yun-hui. Interface of solid steel and liquid aluminum under nonequilibrium diffusion[J]. Trans Nonferrous Met Soc China, 2000, 10(3): 389-392.
[7] ZHANG Peng, DU Yun-hui. Relationship between solid fraction of slurry and property of steel/mushy Al-20Sn semi-solid bonding[J]. Trans Nonferrous Met Soc China, 2002, 12(5): 914-917.
[8] ZHANG Peng, DU Yin-hui. Study on semi-solid processing of Al-7graphite composite[J]. J Uni Sci Technol Beijing, 2001, 8(3): 203-206.
[9] ZHANG Peng, DU Yin-hui. Study on bonding of steel-mushy Al-7graphite[J]. J Uni Sci Technol Beijing, 2001, 8(4): 283-286.
[10] QIAN Wei-jiang, GU Wen-gui. Inhibitory action of Si on growth of interfacial compound layer during hot-dip aluminizing[J]. Acta Metallurgica Sinica, 1994, 30(9): 404-407. (in Chinese)
[11] HOPFIELD D. Diagonal recurrent neural networks for dynamics control[J]. J Proc Nat Acad Sci USA, 1982, 79: 2554-2561.
[12] ZHANG Peng, DU Yun-hui. Study on modeling and optimizing of deformed steel bars hot rolling[J]. J Uni Sci Technol Beijing, 1999, 6(4): 338-341.
[13] PSALTISAND D, SIDERIS A. Multilayered neural network controller[J]. IEEE Control Syst Mag, 1988, 8(2): 17-26.
[14] SONG R, ZHANG Q. The application of artificial neural networks to the investigation of aging dynamics in 7175 aluminum alloys[J]. Mater Sci Eng, 1995, 3(1): 39-44.
[15] ZHANG Peng, DU Yun-hui. Artificial neural networks in steel-mushy aluminum pressing bonding[J]. Trans Nonferrous Met Soc China, 2000, 10(2): 213-216.
[16] ZHANG Peng, DU Yun-hui. Mechanical relationship in steel-aluminum solid to liquid bonding[J]. Trans Nonferrous Met Soc China, 2003, 13(4): 785-789.
[17] ZHANG Peng, DU Yun-hui. Interfacial structure of steel-Al-28Pb bonding plate with semisolid rolling-casting method[J]. Trans Nonferrous Met Soc China, 2004, 14(2): 325-329.
[18] NETA T. Structure analysis of hot impregnated Al-Si coating[J]. Met Surface Technol, 1982, 33(6): 537-540.
[19] FANG Jun-xin. Solid Physics[M]. Shanghai: Shanghai Science and Technology Press, 1980: 170. (in Chinese)
[20] ZHANG Peng, DU Yun-hui. Relationship between interfacial structure and property of steel-mushy Al-28Pb bonding plate[J]. J Cent South Univ Technol, 2006, 13(1): 12-16.
(Edited by CHEN Wei-ping)
Foundation item: Project(50054) supported by the Program for New Century Excellent Talents in University; project(20060004020) supported by the Research Fund for the Doctoral Program of Higher Education; project(3062017) supported by the Natural Science Foundation of Beijing, China; project(2004SZ007) supported by the Foundation of Beijing Jiaotong University
Received date: 2006-05-08; Accepted date: 2006-07-09
Corresponding author: ZHANG Peng, Professor, PhD; Tel: +86-10-51682226; E-mail: zhangp9@263.net