网络首发时间: 2016-07-29 10:51
稀有金属 2017,41(09),1003-1011 DOI:10.13373/j.cnki.cjrm.xy16040601
前驱体合金化方式对粉末冶金泡沫铝孔结构的影响
孙琦 刘彦强 樊建中 魏少华 马自力 郝心想
北京有色金属研究总院国家有色金属复合材料工程技术研究中心
摘 要:
以Al Si11合金为对象, 选取了预合金化的粉末和元素混合粉末作为前驱体的原料, 以Ti H2粉末为发泡剂, 采用粉末冷等静压、真空热除气、热挤压成形等工艺制备前驱体、再次加热发泡成型的方法制备了不同时间状态的一系列泡沫铝试样;对系列试样的孔隙率、孔径及其分布、孔形貌等参数的演变规律进行了对比研究;对孔壁微观组织进行了金相表征。结果表明, 预合金粉前驱体制备的泡沫铝试样的最大孔隙率为72%, 平均孔径为0.593.38 mm, 孔径分布不均匀;气孔演化过程经历了气孔形核、气孔长大和快速合并阶段, 发泡后期出现严重排液现象。元素混合粉前驱体制备的泡沫铝试样的最大孔隙率为84%, 平均孔径为0.581.99 mm, 孔径分布较为均匀;气孔经历了形核、快速合并长大和气孔缓速合并3个阶段。二者相比, 元素混合粉前驱体的可发泡性更好、气孔稳定性更好;结合组织分析可知, 前驱体中AlSi组织特征 (尤其是界面形态) 的差异从本质上决定了合金的熔化和凝固行为, 进而对气孔形核和演化产生了较大的影响。
关键词:
粉末冶金;泡沫铝;孔结构;
中图分类号: TF125.22
作者简介:孙琦 (1990-) , 男, 山东威海人, 硕士研究生, 研究方向:粉末冶金泡沫铝;E-mail:sunqi1254781185@163.com;;刘彦强, 高级工程师;电话:010-60689792;E-mail:lyq9757@163.com;
收稿日期:2016-04-06
基金:国家重点基础研究发展计划项目 (2012CB619606);北京市科技新星计划项目 (Z171100001117067) 资助;
Pore Structure of Aluminum Foam Prepared by Powder Metallurgy with Alloying Method of Precursor
Sun Qi Liu Yanqiang Fan Jianzhong Wei Shaohua Ma Zili Hao Xinxiang
National Engineering & Technology Research Center for Non-Ferrous Metals Composites, Beijing General Research Institute for Nonferrous Metals
Abstract:
By using pre-alloyed powders and mixed elementary powders with composition ratio of Al Si11 as raw material and Ti H2 ( titanium hydride) as blowing agent, series of aluminum foam samples were successfully fabricated with methods of cold isostatic pressing, hot vacuum deaeration, hot extrusion and heating foaming molding. The evolution of porosity, pore size and its distribution, pore morphology parameters were studied, and the metallographic of microstructure of hole wall was characterized. The results showed that the maximum porosity was 72%, the average pore diameter distributed from 0. 59 to 3. 38 mm, and pore size distribution was not uniform.For the aluminum foam sample prepared by pre-alloyed powders precursor, the evolution process of precursor went through three stages:pores nucleation, pores growth and pores rapid consolidation, and serious drainage phenomenon happened at late stage. For the aluminum foam sample prepared by mixed elementary powders precursor, the maximum porosity was 84%, the average pore diameter distributed from 0. 58 to 1. 99 mm, pore size distribution was relatively uniform and the evolution process went through pores nucleation, pores rapid growth with consolidation and slow consolidation of pores. Compared with pre-alloyed powders, aluminum foam prepared by mixed elementary powder had higher porosity, smaller pores diameter, more uniform pores and more stable porosity. Combined with microstructure analysis, it could be concluded that the alloy melting and solidification behavior was essentially decided by organization characteristics of Al-Si precursor ( especially the interface morphology) , and thus nucleation and evolution of bubble were affected.
Keyword:
powder metallurgy; aluminum foam; pore structure;
Received: 2016-04-06
泡沫铝是采用专用造孔技术在铝合金内部引入规则孔隙, 制备形成的一类具有多孔结构的功能-结构一体化的超轻铝合金。泡沫铝具有许多优异的性能, 如密度小、耐热、隔音降噪、抗冲击、耐腐蚀和电磁屏蔽特性, 因此在高端装备、冶金、建筑、交通运输装备、电子器械、通讯设备等方面有着广泛的应用前景[1]。目前国内外已报道了泡沫铝的多种制备技术, 主要包括直接吹气法、熔体发泡法和粉末冶金法[2], 其中, 以吹气法和熔体发泡法所代表的熔体技术在孔结构均匀度控制和大尺寸泡沫铝块材制备方面已取得了较大的进展[3,4,5], 具备一定技术优势。并已在泡沫铝的熔体技术基础上开展了复合构件制备成型探索研究工作, 如采用二次粘合或焊接方法制备复合板材[6]。粉末冶金发泡法工艺具有材料成分可以灵活设计的优势, 为材料性能优化提供了较大的空间;该工艺将前驱体制备和发泡分离开来, 这为复合构件的预成型提供了可能性。自20世纪90年代开始, 德国Fraunhofer应用材料研究所率先对泡沫铝的粉末冶金发泡制备方法进行了一系列工艺研究, 围绕粉末冶金泡沫铝的孔结构控制和性能优化开展了较为细致的研究[7,8,9,10], 已经能够制备出三明治复合板和复杂构件, 并在汽车领域得到推广和初步应用[11]。随着粉末冶金工艺在材料设计、构件成型和净终成型等方面的综合优势的逐步体现[12], 该工艺受到越来越多研究机构的重视。自2000年以后, 国内东南大学、东北大学、太原科技大学和昆明理工大学等高校也对粉末冶金制备泡沫铝开展了探索研究, 并在制备工艺和泡沫铝孔结构演化等方面取得了一定的进展[13,14,15,16]。分析表明, 粉末冶金前驱体的品质是决定泡沫铝孔结构和性能的关键控制因素之一[17];而前驱体的组织结构特征与孔结构的相关关系研究还较少, 其内在控制规律还不明确。因此, 必须围绕前驱体的组分和制备工艺开展深入研究, 合理调控材料的物理化学性质, 从根本上控制气孔的稳定性, 改善工艺重复性, 提高一致性。
为了深入探索粉末原料合金化状态对发泡特性的影响规律, 本文以常用的Al-Si合金为对象, 选取了两种典型的粉末原料作为前驱体的原材料:预合金化的粉末和元素混合粉末 (未合金化) ;利用粉末冷等静压和热挤压成形的方法制备前驱体, 加热发泡制备泡沫铝。通过对不同阶段泡沫铝气孔结构的观察分析, 研究了发泡过程中气孔的演化过程, 并分析了气孔结构的影响因素。
1 实验
1.1 材料制备
本文分别采用了合金成分为Al Si11的预合金粉末和元素混合粉末 (分别简称为合金粉和元素粉) , 合金粉为气雾化制得的Al Si11粉末, 平均粒度为45μm, 元素粉是采用平均粒度为20μm的气雾化纯铝粉 (纯度99.7%) 和粒度为5μm的纯硅粉直接混合制得。两种样品编号分别为样品1和样品2。分别将两种粉末与0.5%~1.0% (质量分数) 的氢化钛粉末 (Ti H2, 粒度45μm) 进行机械混合, 混合时长20 h;将混合粉末冷压成型, 再经真空热除气和热挤压制备出致密的前驱体。前驱体切割加工得到30 mm×30 mm×8 mm的样品, 将前驱体放置于预加热后的钢模具中加热发泡, 发泡温度为660~700℃。
发泡结束后迅速冷却获得泡沫铝样品。对发泡的前驱体进行切割, 将截面照片进行二值化处理后, 运用imageproplus软件对气孔进行统计分析。本文中的孔径数据是由二维平面孔统计得到, 不能严格代表所测样品的真实孔径, 但可作为代表孔径的重要指标, 半定量对比评价孔结构。
采用ZEISS的Axiovert200MAT光学显微镜 (OM) 表征前驱体和泡沫铝孔壁的金相组织, 采用扫描电子显微镜 (SEM, 型号:JSM-6510) 对前驱体的微观组织进行观察。采用差热扫描量热法热分析 (DSC:NETZSCH SAT 409 PC) 对样品进行热分析, 升温速率为5 K·s-1。
1.2 孔结构表征
公式 (1) 为孔隙率计算公式。

式中, P为孔隙率 (%) , V为材料的绝对密实体积 (cm3) , V表观为试样表观体积 (cm3) 。
样品的孔径是采用imageproplus软件对低倍等比例照片进行采集和测算, 平均孔径为横截面上所有气孔孔径的平均值。式 (2) 为孔径标准差的计算公式。

式中, σ为孔径标准差, N为孔数, xi为孔径值 (mm) , μ为所有测得气孔的平均孔径 (mm) 。
单个孔的圆形度 (e) 是通过imageproplus软件方法测算得到, 平均圆形度为截面所有孔的圆形度的平均值。式 (3) 为圆形度计算公式。

式中, L为图形周长 (mm) , A为图形面积 (mm2) , e代表圆形度值, 如果孔形为标准圆形, 则e=1, 孔形与标准圆差异越大, e值越大。
2 结果与讨论
2.1 前驱体的组织结构
图1为前驱体的OM照片和SEM背散射照片, 可以看出制备的两种前驱体材料均没有明显的缺陷和孔洞, 前驱体用排水法测得的相对致密度均达到100%。相比而言, 样品1所用合金粉由气雾化直接制备得到, 其中的硅颗粒为快速凝固得到, 颗粒更为细小、分布更加均匀。而样品2中的硅颗粒尺寸较大, 由于直接混粉后分布不太均匀, 经热挤压成形了颗粒沿挤压方向条带状分布的特征组织。由图1 (c) 和 (d) 中可以看到, 两种样品中的氢化钛颗粒分布较为均匀, 其在两种前驱体中的分布并未发现明显的差异。
对两样品的前驱体进行DSC热分析, 结果如图2所示。两种前驱体的熔化过程基本一致, 吸热峰十分尖锐狭窄。样品1吸热峰起始点、峰值和终止点分别为581, 592, 595℃, 峰宽14℃。样品2吸热峰起始点、峰值和终止点分别为584, 593, 598℃, 峰宽为15℃。样品2峰位向高温方向略为偏移, 峰宽相差小于1℃, 两种不同合金化方式的样品的热力学特征基本一致。
2.2 宏观形貌及孔结构分析
图3和4分别为样品1前驱体和样品2前驱体不同发泡时长的泡沫铝宏观形貌照片。从图3, 4中可以看出, 样品1发泡时间小于150 s时, 气孔较小、孔形状为饼状。随着发泡时间延长, 165 s之后气孔从下到上开始迅速生长, 孔形逐渐接近圆形。195 s时气孔分布最为均匀。195 s之后孔持续长大, 样品顶部孔出现明显的坍塌和氧化, 孔壁破裂, 并伴随着明显的排液现象, 形成底部无泡层。样品2发泡时间小于150 s时, 气孔也很小且形状不规则。但随着发泡时间延长, 样品持续发泡膨胀, 孔径和气孔布逐渐均匀化, 在195 s以后, 孔径没有发生迅速增大, 增速放缓, 孔型接近圆形。对比发现, 样品1和2的发泡过程都经历了气孔形核、长大和合并等过程, 这与Banhart等的研究结果类似[18]。两种样品相比, 样品2的气孔数目多且均匀。
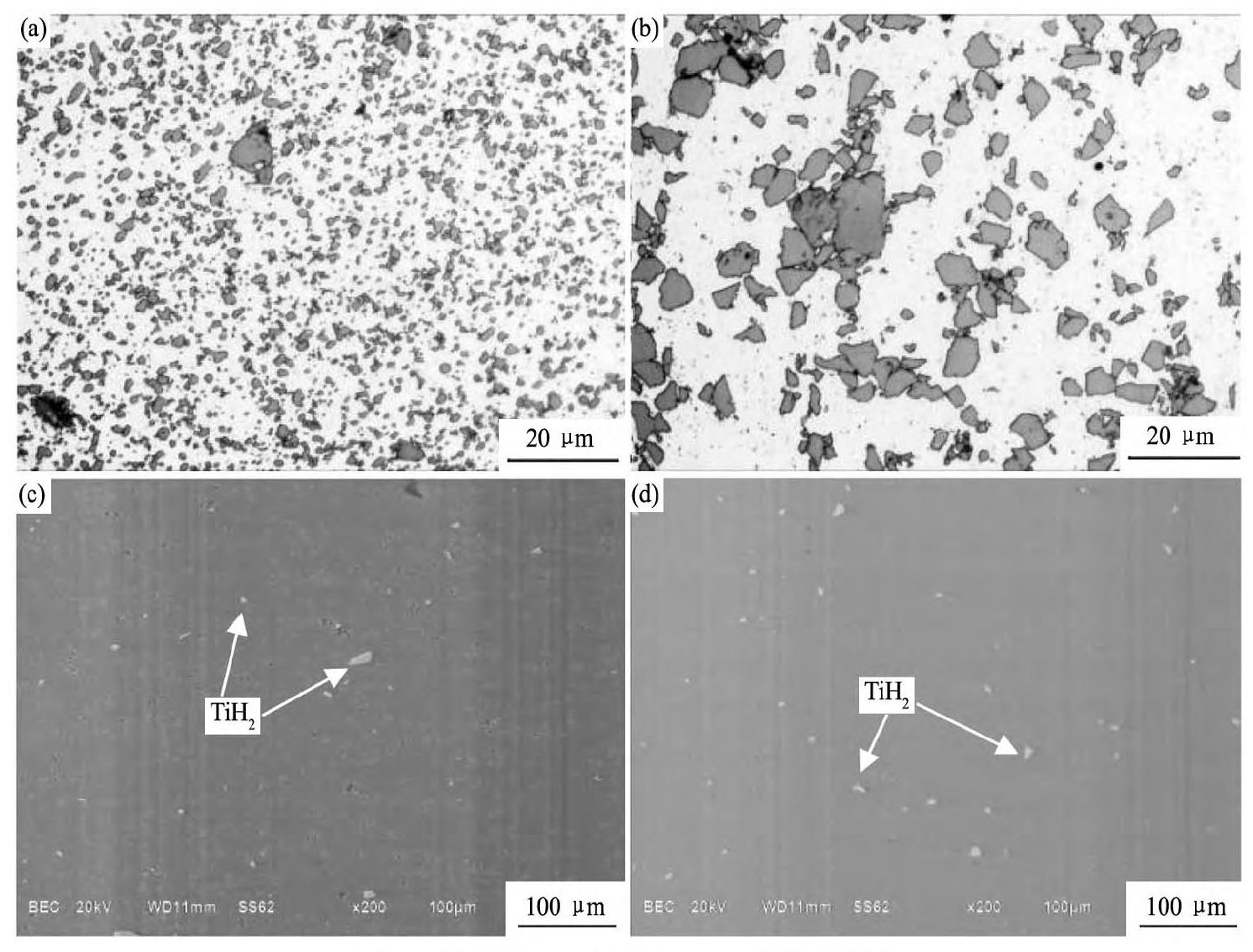
图1 前驱体OM照片和SEM背散射照片Fig.1 OM and SEM back scattered images of precursor
(a) OM image of Sample 1 precursor; (b) OM image of Sample 2 precursor; (c) Back scattered image of Sample 1 precursor; (d) Back scattered image of Sample 2 precursor
发泡过程各阶段的孔隙率、平均孔径、平均圆形度随发泡时间变化如图5所示。图6和7分别为样品1和2不同发泡时间的孔径分布直方图。从孔结构数据随发泡时间的变化可看出, 样品1发泡过程分为3个阶段, 第一阶段为快速膨胀阶段 (130~150 s) , 样品的孔隙率快速增加, 平均孔径较小, 圆形度值较高 (孔不圆) 。结合图3的孔形貌分析可知, 该阶段为气孔形核过程, 主要发生孔数量的变化。第二阶段为气孔长大阶段 (150~195 s) , 样品膨胀速率减慢, 孔隙率缓慢增加, 平均孔径持续增加, 孔的平均圆度降低至1.2, 结合图3的孔形貌和图6的孔径分布分析可知, 该阶段为气孔的长大过程, 主要发生孔径增大和圆形度改善的变化。第三阶段为泡沫坍塌阶段 (195~240 s) , 样品孔隙率开始下降, 平均孔径及孔径标准差迅速增加, 圆形度迅速增大。结合图3的孔形貌分析可知, 该阶段为气孔合并破裂、泡沫坍塌的过程, 在平均孔径和孔型方面发生了显著变化。从图6中也可看到, 在加热发泡240 s之后, 气孔数变得极少, 且孔径分布并无明显规律。
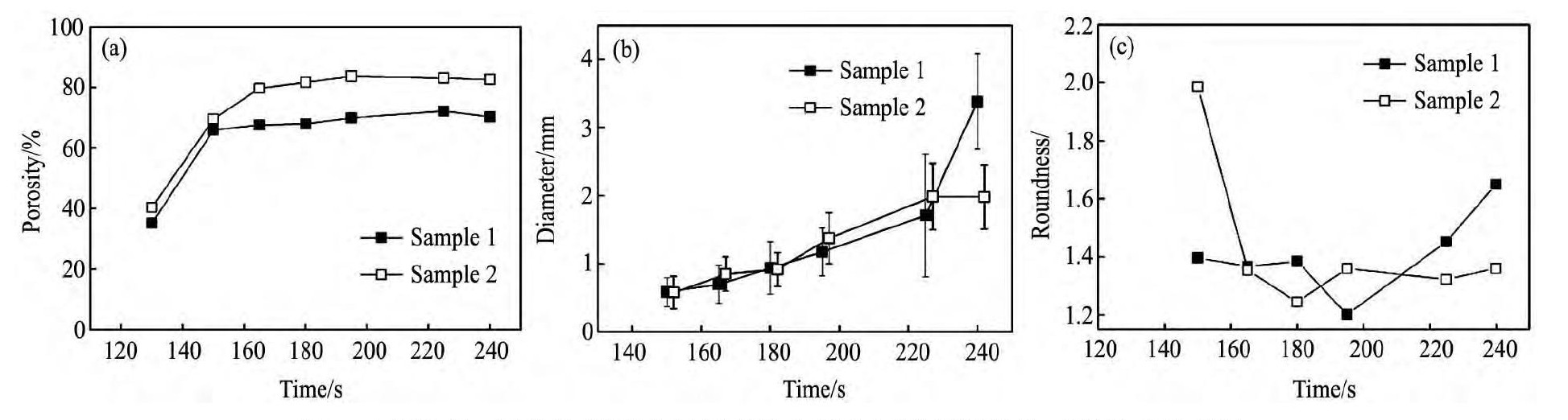
图5 孔隙率、平均孔径及孔径标准差和平均圆形度随发泡时长的变化规律Fig.5 Change rule as foaming time of two samples:porosity (a) , average pore diameter and pore diameter standard deviation (b) and average degree of circular (c)
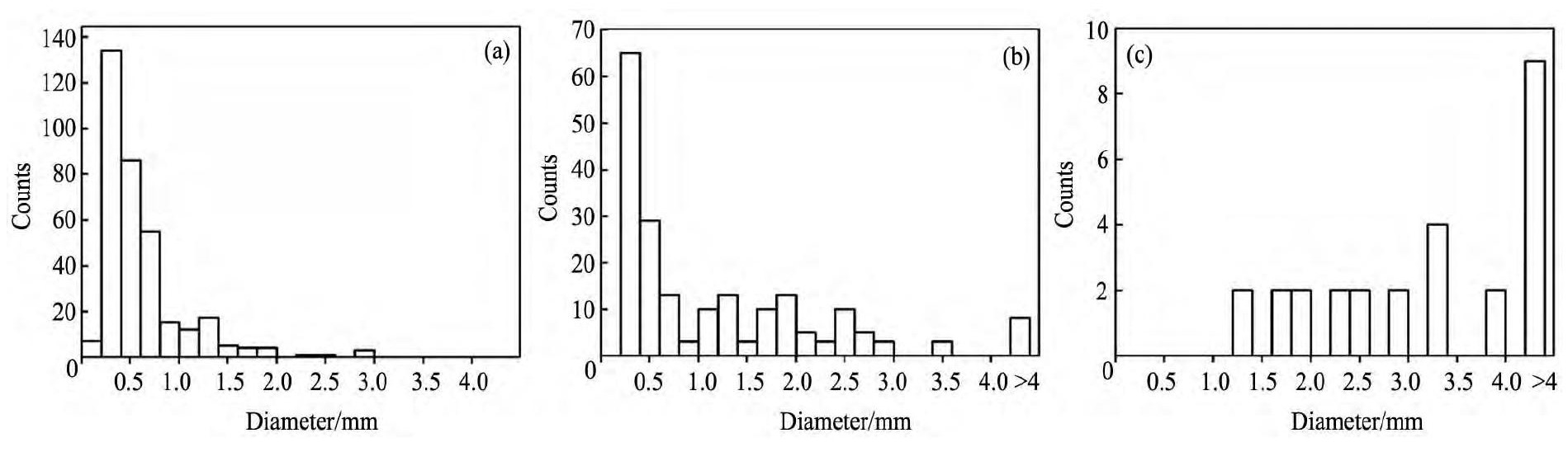
图6 样品1前驱体不同发泡时间泡沫铝样品的孔径分布直方图Fig.6 Pore size distribution histogram of aluminum foam for Sample 1 precursor
(a) 150 s; (b) 195 s; (c) 204 s
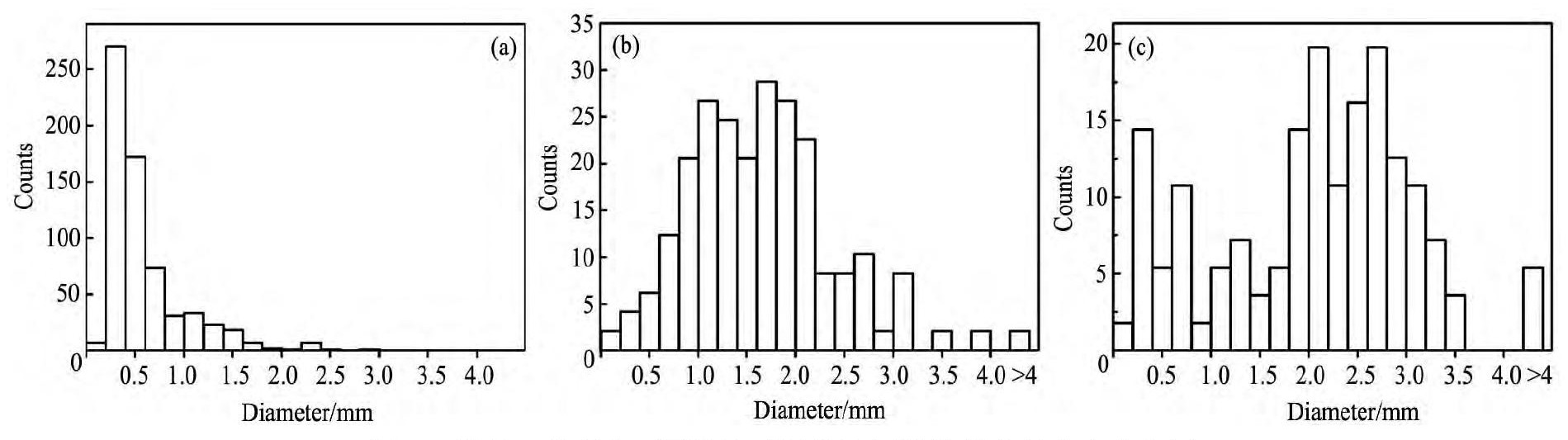
图7 样品2前驱体不同发泡时间泡沫铝样品的孔径分布直方图Fig.7 Pore size distribution histogram of aluminum foam for Sample 2 precursor
(a) 150 s; (b) 195 s; (c) 204 s
样品2气孔演化也呈现出3个阶段。第一阶段为快速膨胀阶段 (130~165 s) , 样品的孔隙率迅速增加, 平均孔径缓慢增长, 平均圆形度迅速降低 (变圆) 。结合图4分析可知, 该阶段为气孔形核过程, 主要发生孔数和孔径变化。第二阶段为气孔长大合并阶段 (165~195 s) , 样品膨胀速率减慢, 孔隙率缓慢增加, 平均孔径持续增加, 孔的平均圆形度先减少后增加, 该阶段为气孔的长大合并过程, 主要发生孔径和圆形度变化。到195 s时, 孔数急剧下降, 孔径分布已经呈现出正态分布 (图7) 。第三阶段为气孔缓慢合并过程, 样品孔隙率基本保持不变, 平均孔径缓慢增大, 平均圆形度变化不大。对照图7中的195和240 s的孔径分布状态, 可以发现, 在这一阶段, 孔径分布总体趋势变化不大, 只是正态分布的峰值向大孔径方向移动。此阶段为气孔的稳定阶段, 孔结构变化微小, 气孔趋于相对稳定。
对比样品1和2的孔结构数据可知, 两种样品发泡过程存在以下重要差别: (1) 样品2的孔隙率明显高于样品1, 样品2孔隙率最高可达84%, 而样品1孔隙率最高为72%。 (2) 样品2在195 s之后平均孔径、孔径标准差和平均圆形度变化缓慢, 孔结构趋于稳定, 而样品1在195 s之后, 平均孔径、孔径标准差和平均圆形度发生剧烈变化, 气孔快速演化并塌陷破坏, 孔结构很不稳定。
2.3 气孔演化理论分析
总结上述气孔结构分析数据可知:与合金粉相比而言, 元素粉前驱体制备的泡沫铝样品的孔隙率高、平均孔径更加均匀、孔径分布范围窄、气孔圆形度好, 在发泡过程中表现出更好的稳定性。下面就两种样品在气孔演化过程中的不同进行分析。
发泡过程的第一步首先是气孔形核, 即Ti H2颗粒受热分解释放出的氢在铝合金熔体中的某些高能量质点附近累积并通过非均匀形核形成小气孔[19]。图8为两种样品不同发泡时间的孔壁显微组织照片。发泡时间150 s时, 两样品均未完全熔化, 前驱体中的硅颗粒仍普遍存在。气孔形核临界压强为[20]
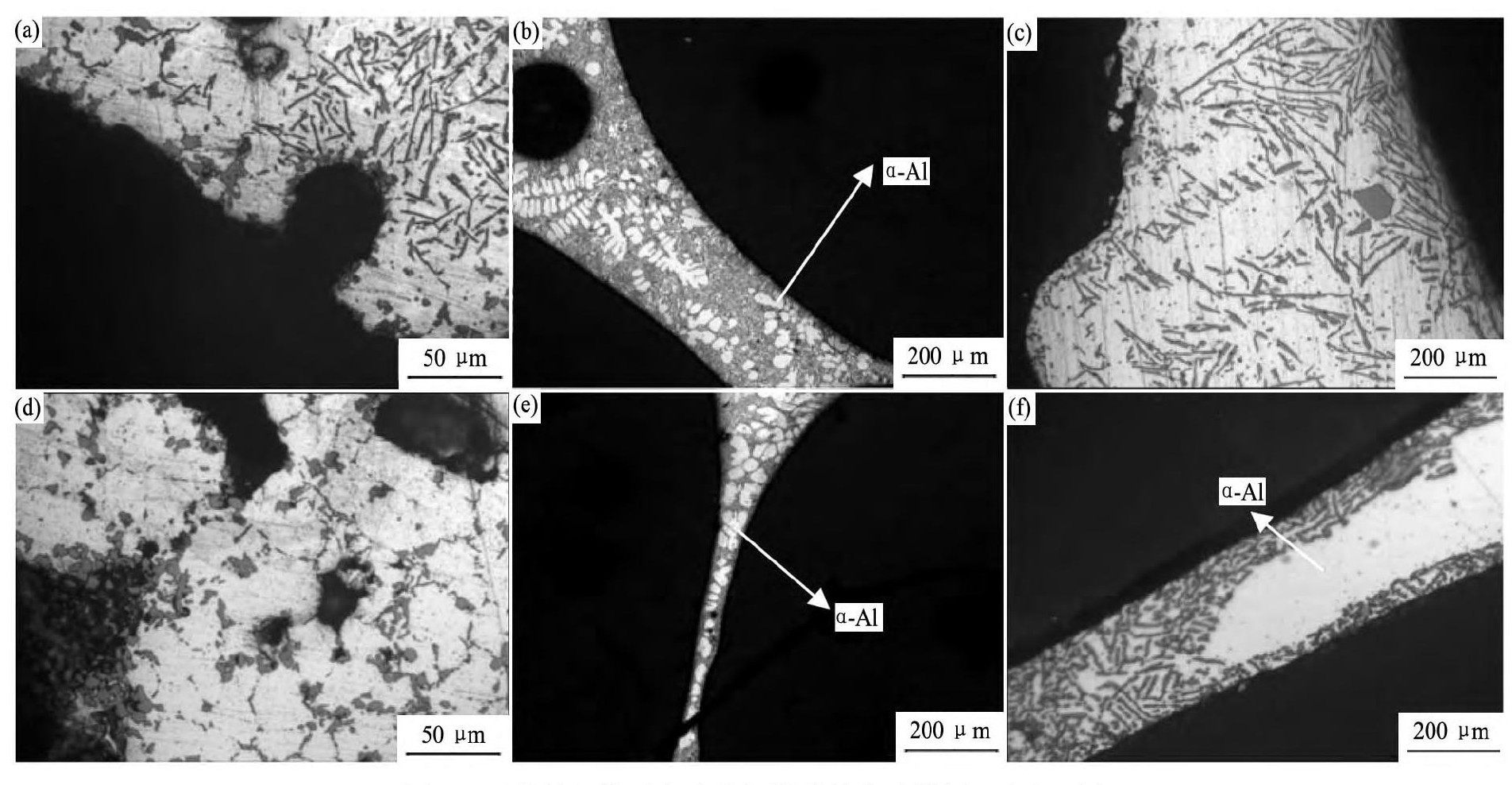
图8 两种前驱体对应泡沫铝样品的孔壁横剖面金相照片Fig.8 Transverse section OM images of hole wall of two kinds of aluminum foam sample
(a~c) Corresponding to foaming time at 150 s, 195 s and 240 s for Sample 1; (d~f) Corresponding to foaming time at 150, 195 and240 s for Sample 2

式中, p为形核临界压强 (Pa) , p大气为大气压强 (Pa) , ρ为前驱体密度 (kg·m-3) , g为重力加速度 (m·s-2) , h为气泡上方高度 (m) , σ为表面能 (N·m-1) , r为气孔半径 (m) 。
两种样品的形核数目存在差异 (图3, 4) , 是铝硅界面不同导致的。样品2由于硅颗粒与铝基体的界面存在氧化物夹杂 (粉末冶金工艺固有特征) , 铝硅界面能较高, 为气孔形核提供了条件。所以元素粉的形核率明显高于合金粉, 发泡全程孔数量更多。
气孔的长大本质上是在熔体中的过饱和氢气向气孔中继续迁移的过程。在气孔独立长大过程中, 泡沫铝气孔长大速率与氢化钛分解速率成正比[20],

式中, d V/dt为气孔长大速率 (m3·s-1) , R为气体常数 (J·K-1·mol-1) , T为温度 (K) , p为气孔压强 (Pa) , dn/dt为发泡剂分解速率 (mol·s-1) 。这一阶段 (165~195 s) , 由于两种样品的发泡剂状态和温度环境相同, 所以其气孔孔径增长速率基本接近, 见图5 (b) 。但从图3和4中对比可以看出, 两者的气孔长大方式略有不同, 样品1气孔在长大过程中很不均匀, 样品2则较为均匀, 可能的原因是两者形核压强不同, 从而导致在熔化期间气孔的膨胀方式有所不同。
随着发泡的进行, 195 s时, 两样品孔壁已经发生大面积熔化, 如图8 (b, e) 所示, 金相中主要包含了Al-Si共晶和α-Al, 不同的是, 样品1中的α-Al呈现典型枝晶特征, 样品2的铝相较为粗大。此时两种样品中已经形成较薄的孔壁, 气孔之间相互接触和挤压, 形成典型的布拉德边界, 气孔演化至合并阶段。这一阶段, 两样品有着显著的不同, 合金粉泡沫铝气孔迅速合并, 而元素粉泡沫铝气孔则表现出一定的稳定性。
孔壁在减薄过程中, 由于孔壁和布拉德边界处的曲率不同, 导致了形成了一定的压强差, 从而使孔壁中熔体向布拉德边界处移动。根据Reynolds方程[21], 减薄速率为

式中, v为孔壁减薄速率 (m·s-1) , x为孔壁厚度 (m) , σ为表面张力 (N·m-1) , η为熔体黏度 (Pa·s) , r1为曲率半径 (m) , r2为圆盘半径 (m) 。
另一方面, 泡沫铝在气孔演化过程中, 受到重力的作用, 液体下排, 孔壁减薄。这一过程受熔体粘度的影响, 熔体粘度越大排液速度越慢[13]。孔壁的减薄是在重力和毛细作用力共同作用下进行的。熔体表面张力越大、黏度越小、气孔破裂消亡的倾向越大, 反之亦然[20,22]。
两种样品在气孔合并期间表现的不同受孔壁减薄速率的影响。图8 (c, f) 为两种样品在发泡240 s时孔壁金相照片, 从图8中可以看出, 在相同的加热和冷却条件下, 两种样品的孔壁金相组织并不相同。合金粉前驱体由于铝硅分布均匀, 熔化迅速, 凝固后的孔壁中铝硅共晶相分布均匀。而元素粉前驱体, 铝硅分布相对不均匀, 熔化较慢, 仍可能存在少量未完全熔化的固态颗粒。因此, 合金粉泡沫铝在气孔生长合并阶段, 熔体黏度较小, 流动性较强。其孔壁减薄速率较快, 孔壁快速变薄直至破裂、气孔合并。元素粉前驱体由于熔体中含有部分未完全熔化的固态颗粒 (包括氧化夹杂物) , 一定程度上增大了熔体黏度, 阻碍了孔壁中熔体的流动。孔壁变薄的速率相对较慢, 孔结构变化很小, 将孔壁维持在一定的厚度水平, 增加孔壁稳定性。
2.4 讨论
综上所述, 在维持材料成分不变的情况下, 通过调整粉末合金化方式、改变前驱体内部显微组织结构特征, 便可以明显改变前驱体发泡时的气孔形核与长大合并的规律, 控制泡沫铝孔结构质量, 以及发泡过程的稳定性。与Alulight Company提供的前驱体所制备的泡沫铝[17]直观对比, 该制备工艺制得的泡沫铝, 平均孔径较小, 孔径分布较为集中。这是由于以往制备的泡沫铝, 多采用粉末直接压制或烧结成形后发泡的工艺方法, 获得前驱体中界面氧化物夹杂多、结合力差, 在加热熔化发泡时由于界面质量不均匀而造成材料内部形核不均匀的问题, 进而导致孔结构的严重不均匀, 这与Jiménez C的研究相吻合[9]。本文研究中采用了真空热除气和热挤压的方式对前驱体进行固结致密化处理;通过真空除气可以最大程度去除铝粉表面吸附的气体、减少界面夹杂, 通过热挤压过程施加的三向压应力产生的剪切变形可以促进形成高强度的Al-Si冶金界面 (尤其针对元素粉) 。本文得到的结果有助于加深对粉末冶金发泡机理的理解以及对孔结构控制工艺方法的掌握;关于前驱体组分和制备工艺对泡沫铝孔结构的半量化控制还有待于进一步的系统研究。
3 结论
以合金粉末和元素粉末为原料, 运用冷压、真空热除气和热挤压工艺制备的前驱体致密度高, 具有良好的可发泡性能。合金粉前驱体制备的泡沫铝的孔隙率最高为72%, 孔径范围为0.59~3.38 mm, 孔径分布不均匀, 排液明显。元素粉前驱体制备的泡沫铝的孔隙率最高为84%, 孔径0.58~1.99 mm, 孔径分布较为均匀, 排液不明显。二者相比, 元素粉制备的泡沫铝, 孔隙率高、孔径分布均匀, 发泡过程稳定。二者的发泡过程有较大区别, 合金粉前驱体发泡过程经历了气孔形核、气孔长大和气孔迅速合并过程, 而元素粉前驱体则经历了气孔形核、气孔迅速合并长大和气孔缓慢合并的过程。产生这种差异的本质原因在于, 两种组分样品的前驱体中硅颗粒的尺寸、分布以及铝-硅界面状态不同;这种差异直接影响了前驱体发泡过程中气孔的形核数量、气孔生长方式以及气孔演化的稳定性。总之, 对前驱体显微组织特征的控制是调控泡沫Al-Si合金 (乃至其他铝基泡沫) 发泡过程以及控制最终孔结构的有效措施。
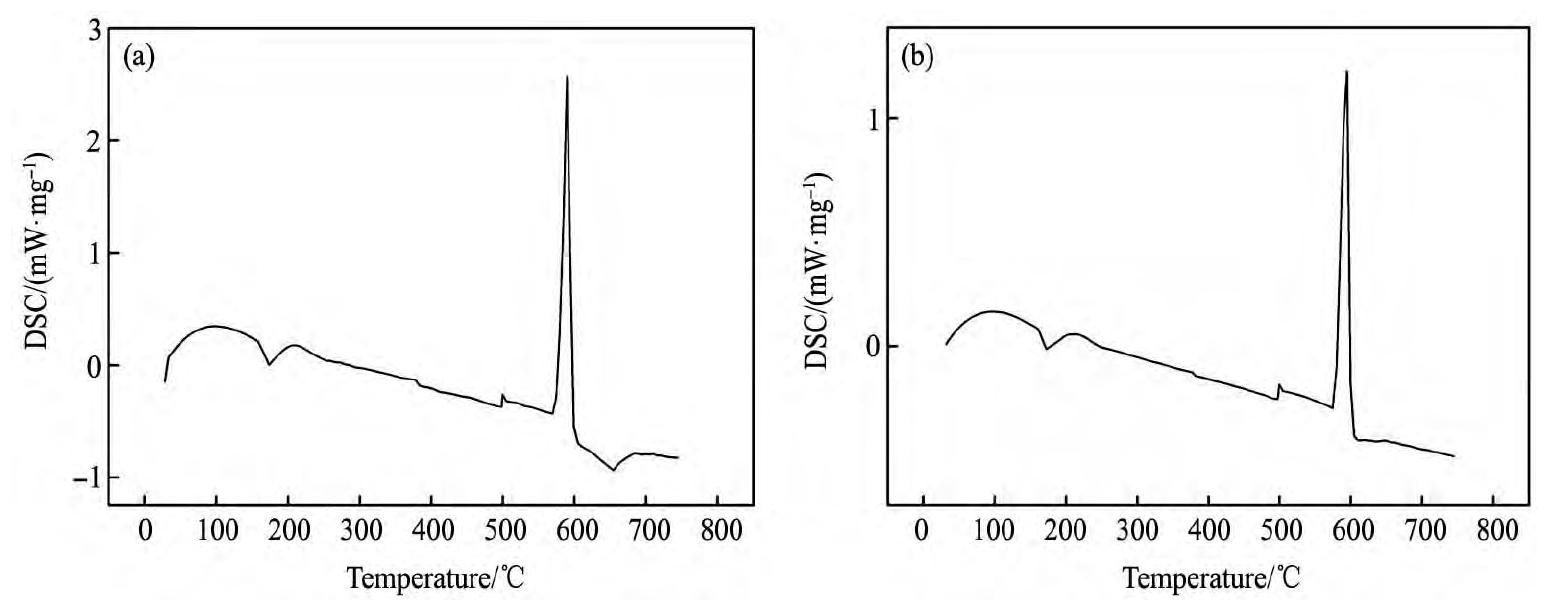
图2 样品1和样品2前驱体的DSC热分析曲线Fig.2 DSC curves of precursor Sample 1 precursor (a) and Sample 2 precursor (b)
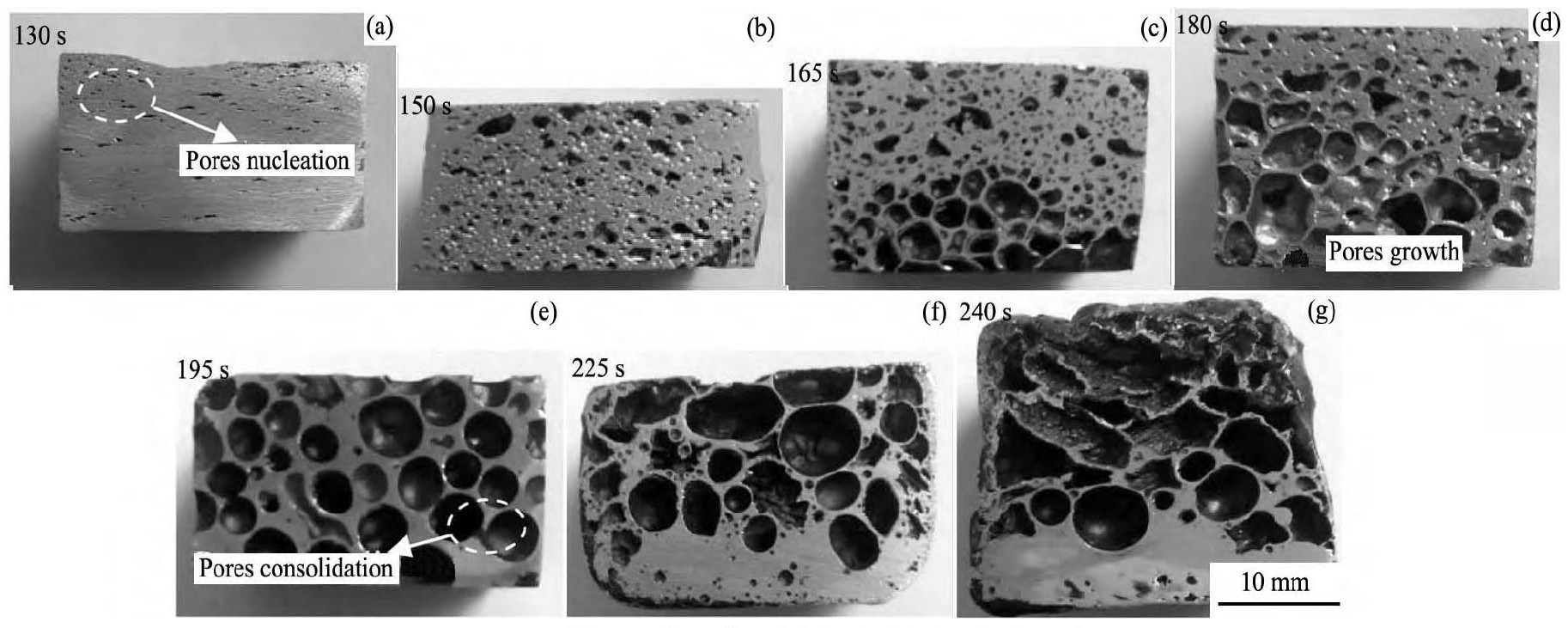
图3 样品1前驱体不同发泡时长的泡沫照片Fig.3 Photos of Sample 1 aluminum foam samples at different foaming time
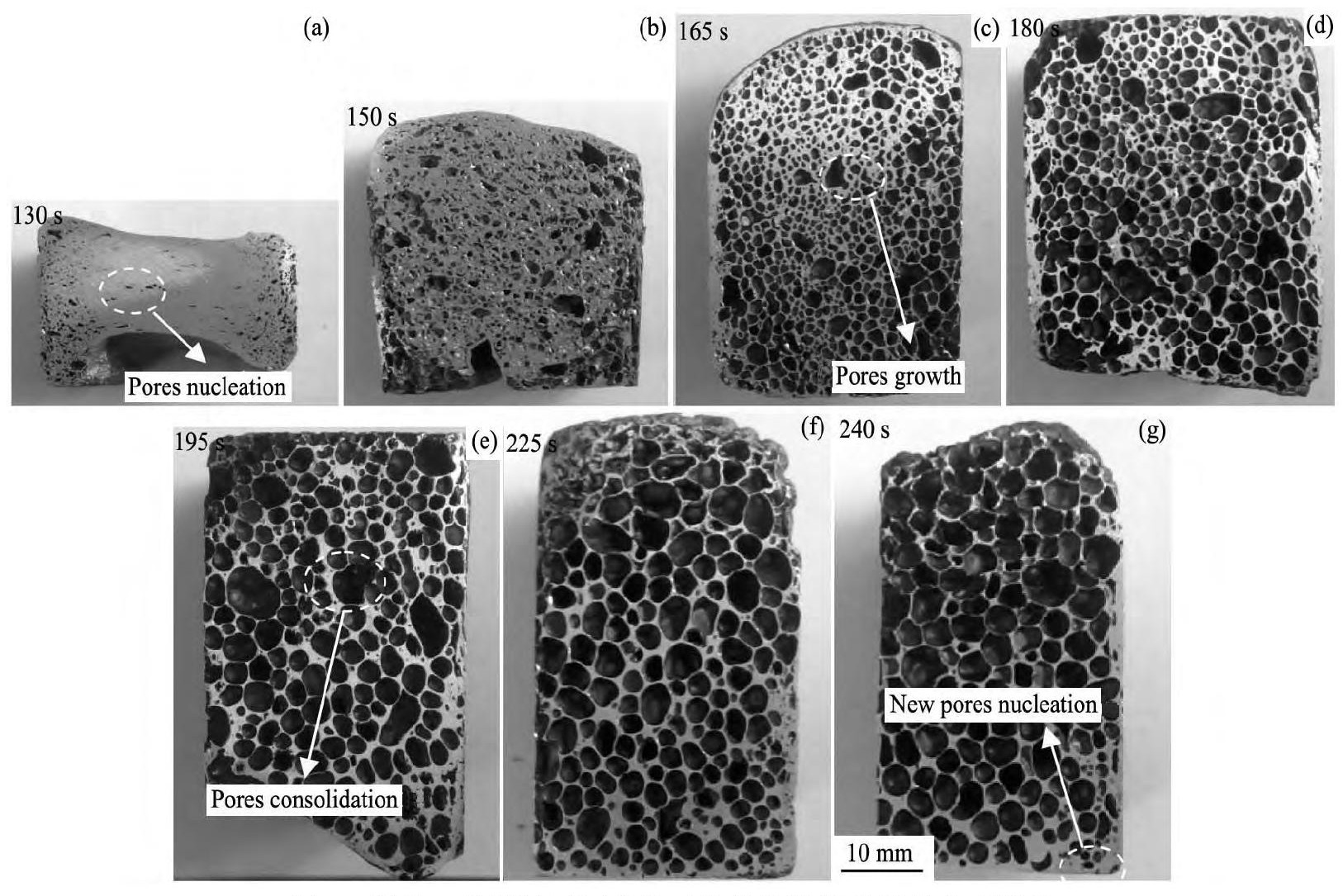
图4 样品2前驱体不同发泡时长的泡沫铝样品的宏观形貌Fig.4 Photos of Sample 2 aluminum foam samples at different foaming time
参考文献
[1] Wang Z T, Zhang R.Performance of foam aluminum and its production technology[J].Light Alloy Fabrication Technology, 2011, 39 (10) :10. (王祝堂, 张睿.泡沫铝性能及制备技术[J].轻合金加工技术, 2011, 39 (10) :10.)
[2] Xu F S, Li Q, Du J C.Foam aluminum producing technology and market both at home and abroad[J].Light Alloy Fabrication Technology, 2012, (10) :19. (胥福顺, 李全, 杜吉灿.泡沫铝制备技术及国内外市场综述[J].轻合金加工技术, 2012, (10) :19.)
[3] Liu X N, Li Y X, Chen X, Fan X L.Effect of Ca on particulate dispersion and foam stability in gas injection foaming process[J].Chinese Journal of Nonferrous Metals, 2011, 21 (2) :392. (刘兴男, 李言祥, 陈祥, 范雪柳.吹气发泡工艺中Ca对颗粒分散和泡沫稳定性的影响[J].中国有色金属学报, 2011, 21 (2) :392.)
[4] Wang X M, Yang G J, Yao G C.Improving on the technology producing closed-cell aluminum foam and discussion about key problems[J].Light Alloy Fabrication Technology, 2006, 34 (12) :46. (王兴明, 杨国俊, 姚广春.泡沫铝制备工艺的改进及关键问题探讨[J].轻合金加工技术, 2006, 34 (12) :46.)
[5] Huang L, Yang D H, Wang H, Lv Z P, Ye F.Compression and energy absorption properties of cellular Al-0.16 Sc alloy foam after isothermal aging[J].Materials for Mechanical Engineering, 2013, 37 (8) :36. (黄粒, 杨东辉, 王辉, 吕昭平, 叶丰.泡沫Al-0.16 Sc合金等温时效后的压缩及能量吸收性能[J].机械工程材料, 2013, 37 (8) :36.)
[6] Yu C C.Preparation and Reliability Evalution of the Aluminum Foam Sandwich[D].Harbin:Harbin Institute of Technology, 2012.11. (于冲冲.泡沫铝夹芯三明治结构制备及可靠性评价[D].哈尔滨:哈尔滨工业大学, 2012.11.)
[7] Matijasevic L B, Banhart J, Fiechter S, Gorke O, Wanderka N.Modification of titanium hydride for improved aluminium foam manufacture[J].Acta Materialia, 2006, 54 (7) :1887.
[8] Matijasevic B, Banhart J.Improvement of aluminium foam technology by tailoring of blowing agent[J].Scripta Materialia, 2006, 54 (4) :503.
[9] Jiménez C, Garcia M F, Mukherjee M, Goerkec O, Banhart J.Improvement of aluminium foaming by powder consolidation under vacuum[J].Scripta Materialia, 2009, 61 (5) :552.
[10] García M F, Jiménez C, Mukherjee M, Holm P, Weised J, Banhart J.Experiments on metallic foams under gravity and microgravity[J].Colloids&Surfaces A Physicochemical&Engineering Aspects, 2009, 344 (1-3) :101.
[11] Wang G, Yang H X, Jiao M W, Wei Y S, Li H, Gong Z F.Development and application of aluminum foam material in automobiles[J].Chinese Journal of RareMetals, 2015, 39 (7) :660. (王刚, 杨红新, 焦孟旺, 魏元生, 李贺, 贡泽飞.泡沫铝在汽车上的开发应用[J].稀有金属, 2015, 39 (7) :660.)
[12] Lefebvre, L P, Banhart J, Dunand D C.Porous metals and metallic foams:current status and recent developments[J].Advanced Engineering Materials, 2008, 10 (9) :775.
[13] Zhu Y G, Chen F, Liang X J, He D P.Evolution of pore morphology and cell wall microstructure of aluminum foam during powder metallurgical foaming[J].Chinese Journal of Nonferrous Metals, 2004, 14 (7) :1006. (朱勇刚, 陈锋, 梁晓军, 何德坪.粉末冶金发泡时泡沫铝孔结构及泡壁的微观组织演变[J].中国有色金属学报, 2004, 14 (7) :1006.)
[14] Wang L, Yao G C, Ma J, Hua Z S.Effects of compaction methods on cell structures of closed-cell aluminum foams[J].Journal of Northeastern University, 2010, 31 (3) :406. (王磊, 姚广春, 马佳, 华中胜.压制方式对闭孔泡沫铝泡孔结构的影响[J].东北大学学报:自然科学版, 2010, 31 (3) :406.)
[15] Wang L C, Zeng S Y, Wang F, You X H.Effects of PCM methods on foaming behavior of Al-Ti H2precursor[J].Chinese Journal of Nonferrous Metals, 2007, 17 (7) :1135. (王录才, 曾松岩, 王芳, 游晓红.预制体制备方式对PCM法泡沫铝发泡行为的影响[J].中国有色金属学报, 2007, 17 (7) :1135.)
[16] Zuo X Q, Sun J L.Review on foam metal manufacture techniques[J].Journal of Materials Science&Engineering, 2004, 22 (3) :452. (左孝青, 孙加林.泡沫金属制备技术研究进展[J].材料科学与工程学报, 2004, 22 (3) :452.)
[17] Lázaro J, Rmer O, Solórzano E, Moreno F G, Pérez MR, Banhart J.Heat treatment of aluminium foam precursors:effects on foam expansion and final cellular structure[J].Procedia Materials Science, 2013, 4:28.
[18] Duarte I, Banhart J.A study of aluminium foam formation—kinetics and microstructure[J].Acta Materialia, 2000, 48 (9) :2349.
[19] Rack A, Helwig H M, Bütow A, Rueda A, Matijasevic L B, Helfen L, Goebbels J, Banhart J.Early pore formation in aluminium foams studied by synchrotron-based microtomography and 3-D image analysis[J].Acta Materialia, 2009, 57 (16) :4809.
[20] Guo Z Q, Yao G C, Yu H J, Li H B.Evolution of pore morphology in foam aluminium[J].The Chinese Journal of Process Engineering, 2006, 6 (6) :978. (郭志强, 姚广春, 尉海军, 李红斌.泡沫铝材的泡体演化过程[J].过程工程学报, 2006, 6 (6) :978.)
[21] Bhakta A, Ruckenstein E.Decay of standing foams:drainage, coalescence and collapse[J].Advances in Colloid&Interface Science, 1997, 70 (1) :1.
[22] Wübben T, Stanzick H, Banhart J, Odenbach S.Stability of metallic foams studied under microgravity[J].Journal of Physics Condensed Matter, 2003, 15 (1) :S427.