
Dependence of phase selection on cooling rates in as-cast Al-Si-Mg alloys
HE Zhi(何 志)1, ZHANG Rui-jie(张瑞杰)2, LIU Yong-qin(刘永勤)1, JIE Wan-qi(介万奇)1
1. College of Materials Science and Engineering, Northwestern Polytechnical University, Xi’an 710072, China;
2. Department of Mechanical Engineering, Tsinghua University, Beijing 100084, China
Received 28 July 2006; accepted 15 September 2006
Abstract: The effect of cooling rate on the solidification process of Al-2.06%Si-1.58%Mg was numerically and experimentally investigated. The solidification paths and the phase precipitation sequence were predicted based on the solute transportation analysis in the solidification process by coupling the thermodynamic calculation. Due to the different solute diffusion speeds, the solidification paths can be largely influenced by the cooling rates. Different phase precipitation sequences can be obtained through calculation under different cooling rates. And the later experiments have also proved this phenomenon. In the researched Al-2.06%Si-1.58%Mg alloy, the solidification sequences are α(Al)→α(Al)+Si→α(Al)+Mg2Si+Si under low cooling rate and α(Al)→α(Al)+Mg2Si→α(Al)+Mg2Si+Si under high cooling rate, respectively. The experimental results confirm the calculation predications.
Key words: Al-Si-Mg alloys; cooling rate; solute transportation; phase selection
1 Introduction
Cast aluminum-silicon alloys have widespread applications, especially in the aerospace and automotive industries. These foundry alloys have an excellent combination of castability and mechanical properties, as well as good corrosion resistance and weldability[1-3].
The solidification simulation for binary alloys usually commences with the assumption of the constant equilibrium partition coefficient[4,5]. In multi- component alloys, invariable binary data of the corresponding binary sub-system are usually simply adopted. The multi-component and multi-phase alloys are the most popular engineering materials, where one phase acts as the matrix and the others serve as the reinforcing elements. This kind of microstructure can be obtained directly through solidification method. Therefore, it is of vital importance to guide the solidi- fication process in the way favorable to controlling the species, volume fraction, morphologies and sizes of the reinforcement phases[6].
Recently, the more accurate phase diagram can be obtained through the CALPHAD method[7,8]. By coupling the CALPHAD method with the classical solidification models, it is possible to predict the solidification process in details.
In our recent researches, the solidification of Al-Si-Mg alloy is studied with the stresses on the effect of cooling rate on the formation of the reinforcing phases, Si and Mg2Si. The formation order of Si and Mg2Si is not only mainly dependent on the concentrations of Si and Mg [9,10], but also influenced by the cooling rates. By changing the cooling rate, the formation order as well as the volume fractions of Si and Mg2Si phases during the solidification can be changed due to the solute redistribution and the different of diffusion coefficients.
In this paper, the solute partition behavior and its influence on the solidification process of multi- component alloys were studied in detail based on the CALPHAD technology. By comparing the results of this simple solution with the experimental results, it was shown that this simple model is satisfactory for the prediction of solidification path of Al-Si-Mg alloys during solidification process. The detail regulation was confirmed by both numerical modeling results and experimental results.
2 Predication of solidification path
The following assumptions were adopted for the analysis of the solute redistribution during the solidification of Al-Si-Mg alloy:
1) The diffusion in the solidified primary phase (α-phase) is ignored, and that in liquid is a pure diffusion without convection;
2) The local thermodynamic equilibrium at the growth interface is reached during the whole solidification process;
3) The primary α-phase keeps sphere during growth.
In the present model, the grain is also assumed to be at uniform temperature and thus the heat balance for the grain can be written as[4]
(1)
where
is the cooling rate just before solidification. L is the volumetric heat of solidification and cp is the volumetric specific heat capacity. R0 is the equivalent radius of the grains, and Rs is the equivalent radius of the solidified primary phase.
and R0 can be determined through experiments.
Therefore, the Fick’s diffusion equation for each element can be written as
i= Si, Mg (2)
The boundary condition of
(3)
and solute conservation condition of
(4)
where Di is the diffusion coefficient of element i in liquid phase, and wl,i, wS,i and w0,i are the contents of element i of liquid, solid and average in mass fraction respectively.
The dependence of the solidification temperature, i.e. the liquidus temperature, on the solute concentration of
TL=T(wSi, wMg) (5)
will be calculated based on Thermo-Calc method[8,11]. The artificial alloy Al-2.06%Si-1.58%Mg was taken as example in calculation. By choosing different cooling rates of 0.3, 6.0 and 200 ℃/s, which correspond to the furnace cooling, air cooling and water cooling in the following experiments, the solidification paths were predicated.
The parameters of Al-Si-Mg alloys used in calculations are listed in Table 1[10].
The calculated solidification paths for different cooling rates are shown in Fig.1. It can be seen that at small cooling rate of 0.3 ℃/s, the content variation of the solidified primary phase follows path 1. It means that α(Al)+Si eutectic will appear before the ternary eutectic of α(Al)+Mg2Si+Si. So the solidification process is α(Al)→α(Al)+Si→α(Al)+Mg2Si+Si. But, at a high cooling rate, such as 6.0°C/s or 200°C/s, paths 2 and 3 will be followed. The solidification order will be α(Al)→α(Al)+ Mg2Si→α(Al)+Mg2Si+Si.
Table 1 Values used for solidification calculation
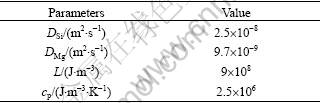
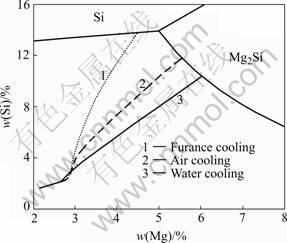
Fig.1 Solidification paths at different cooling rates predicted by theoretical calculation
3 Experimental investigations
3.1 Experiment process
To confirm the above numerical predications, the solidification experiments were guided using the same alloy of Al-2.06%Si-1.58%Mg. The alloy was prepared from the 99.99%Al, Al-12.47%Si and Al-49%Mg alloys with appropriate proportion in a graphite crucible in an electrical resistance furnace. And the alloys were cast into d8 mm?120 mm samples at 720 ℃, then the alloy samples were held in graphite crucible with inner diameter of 9 mm. After the re-melting and superheating, the samples were cooled down in furnace, air and water respectively. After polished, the samples were corroded by 0.5% HF aqueous solution. The microstructures of the samples were observed under optical microscope and the influence of cooling rates on solidification paths was analyzed.
3.2 Experiment results
The measured cooling rates are 0.3, 6.0 and 200 ℃/s respectively, which are coincident to the calculation parameters. The microstructures are shown in Fig.2. It is shown that, for the cooling rate of 0.3 ℃/s, Si and α(Al)+Si+Mg2Si phases are obtained, which shows the solidification order of α(Al)→α(Al)+Si →α(Al)+ Mg2Si+Si, while for the cooling rates of 6.0 ℃/s and 200℃/s, Mg2Si and α(Al)+Si+Mg2Si phases are obtained, which shows the solidification order of α(Al)→α(Al)+ Mg2Si→α(Al)+Mg2Si+Si. The experimental results confirm the calculation predications.
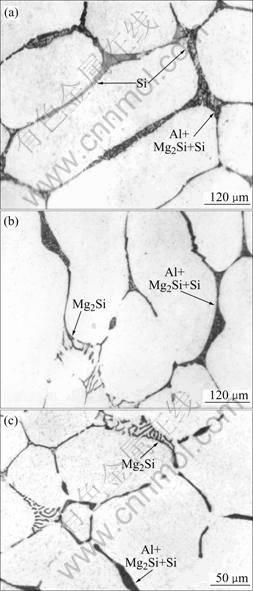
Fig.2 Microstructures of Al-2.06%Si-1.58%Mg alloy obtained with different cooling rates: (a) 0.3 ℃/s; (b) 6.0 ℃/s; (c) 200 ℃/s
4 Analyses
The diffusion coefficient of Si is slower than that of Mg in solid phase, but larger in liquid phase. If the cooling rate is small, the solidification process will need much more time. Mg element will diffuse much more into solid phase than Si. On the other hand, Si element will diffuse into the liquid much more under small cooling rate. The Si content in liquid phase will increase relatively. Thus, the solidification path will move to α(Al)+Si eutectic with the decrease of cooling rate.
5 Conclusions
The phase selection of Al-Si-Mg alloys can be controlled through changing the cooling rate as well as the contents. It is proved through both calculation and experiments that different phase precipitation sequences are available under different cooling rates. In the researched Al-2.06%Si-1.58%Mg alloy, the solidification sequences are α(Al)→α(Al)+Si→a(Al)+ Mg2Si+Si under low cooling rate and α(Al)→α(Al)+ Mg2Si→α(Al)+Mg2Si+Si under high cooling rate, respectively.
References
[1] SHIVKUMAR S, WANG L, APELIAN D. Molten metal processing of advanced cast aluminum alloys [J]. JOM, 1991, 26-32.
[2] WANG P, LIAUH Y, LEE S, LIN J. Effect of Be addition on microstructures and mechanical properties of B319 alloys [J]. Mater Chem Phys, 1998, 195-202.
[3] DJURDJEVIC M, STOCKWELL T, SOKOLOWSKI J. The effect of strontium on the microstructure of the aluminum-copper eutectics in the 319 aluminum alloy [J]. Int J Cast Met, 1999, 67-73.
[4] RAPPAZ M, BOETTINGER W J. On dendritic solidification of multicomponent alloys with unequal liquid diffusion coefficients [J]. Acta Mater, 1999, 47: 3205-3219.
[5] MEHRABIAN R, FLEMINGS M C. Macrosegregation in ternary alloys [J]. Metallurgical Transactions A, 1970, 1: 455-464.
[6] FEI W D, KANG S B. Effects of cooling rate on solidification process in Al-Mg-Si alloy [J]. J Mater Sci Letters, 1995, 14: 1495-1497.
[7] ANSARA I. Comparison of methods for thermodynamic calculation of phase diagram [J]. International Metals Reviews, 1979, 1: 20-51.
[8] SAUNDERS N, MIODOWNIK A P. Calphad: A Comprehensive Guide [M]. Oxford: Pergamon Press, 1998: 299-402.
[9] WU Q, SUN F, SUN Q J, JIANG S F. Solidification process of Al-Mg-Si alloys [J]. The Chinese Journal of Nonferrous Metals, 2000, 10(3): 688-692. (in Chinese)
[10] ZHANG R J, WANG X Y, JIE W Q. Solute partition behavior and its influences on solidification process of Al-Si-Mg alloys [J]. The Chinese Journal of Nonferrous Metals, 2003, 13: 1483-1487. (in Chinese)
[11] ANDERSSON J O, HELANDER T, H?GLUND L. Thermo-Calc and Dictra, computational tools for materials science [J]. Calphad, 2002, 26: 273-311.
(Edited by HE Xue-feng)
Foundation item: Project (2006CB605202) supported by the Hi-tech Research and Development Program of China
Corresponding author: HE Zhi; Tel: +86-29-88460275; E-mail: hzzhi_1978@163.com