
Selective separation of copper and cadmium from zinc solutions by low current density electrolysis
YANG Bo(杨 卜), WANG Cheng-yan(王成彦), LI Dun-fang(李敦钫),
YIN Fei(尹 飞), CHEN Yong-qiang(陈永强), WANG Nian-wei(王念卫)
General Research Institute of Mining and Metallurgy, Beijing 100044, China
Received 6 July 2009; accepted 10 January 2010
Abstract: Copper and cadmium ions were selectively separated from zinc sulphate aqueous solution or zinc ammonia/ammonium sulphate aqueous solution by low current density electrolysis. It was shown that the concentration of cadmium ion in zinc sulphate solution decreased from 4.56 g/L to 0.18 g/L in an electrolysis time of 8.5 h, whilst it decreased from 5.16 g/L to lower than 0.005 g/L in zinc ammonia/ammonium sulphate aqueous solution. On the other hand, the deposition rate of copper was so low that it was difficult to separate copper and cadmium ions from the zinc ammonia/ammonium sulphate aqueous solution during electrolysis. But copper ion could be decreased to 0.002 g/L in this solution through solvent extraction by using kerosene diluted LIX984N as extractant. Therefore, it is favorable to recover cadmium ion from the zinc ammonia/ammonium sulphate solution by electrolysis after solvent extraction of copper.
Key words: copper; cadmium; zinc solution; electrolysis
1 Introduction
Cadmium is used in paint, alloy, electroplating and battery. It is extracted from the by-products of zinc metallurgy among which copper-cadmium slag, cadmium-rich dust and spent Ni-Cd batteries are the main raw materials[1-6]. Pure cadmium can be recovered through solvent extraction, electrolysis refining or vacuum distillation[7-15]. The metal elements in copper-cadmium slag are zinc, cadmium, copper and their oxides with a little amount of As, Sb, Fe, Co and Ni. In the industrial treatment process of copper-cadmium slag, sulphuric acid is usually used as leaching agent and MnO2 is added to oxidize iron. The iron, arsenic and antimony ions in the sulphuric acid leaching solution are precipitated through neutralization of lime water. Sponge cadmium is produced by displacement of zinc powder after adjusting the pH value to 3-4. Finally, pure cadmium metal is deposited by electrolysis. The process for cadmium extraction is complicated and also needs a large quantity of zinc powder. Some studies have shown that copper and cadmium could be separated from zinc in sulphate solution by electrodeposition using special equipment[16-17]. Up to now, there is less research report on the separation of copper, cadmium and zinc in ammonia solution.
The obvious advantage of ammonia leaching technology for zinc extraction is that the low grade zinc ores with high impurities can be treated[18-19]. Zinc is dissolved into the ammonia leaching solution while the impurities, such as arsenic, antimony and iron remain in the leached residue. Copper, cadmium, cobalt, nickel and silver are also dissolved[20]. As a result, a large amount of zinc powder is consumed to remove the copper and cadmium ions from the ammonia leaching solution when the ammonia leaching procedure is used to treat copper-cadmium slag. Therefore, new treatment method for the copper and cadmium containing materials should be developed. The present study reveals the results of selective separation of copper and cadmium from zinc solutions by low current density electrolysis.
2 Experimental
2.1 Solution preparation
All chemical reagents, i.e. zinc sulfate, cadmium oxide, copper sulfate, ammonium sulfate, sulphuric acid and ammonia were used in analytical purity. Four kinds of solutions with different concentrations of zinc, copper and cadmium ions were prepared, two of which contained only zinc and cadmium ions in aqueous sulphate solution or ammonia-ammonium sulphate solution while the other two had zinc, cadmium and copper ions in the different solutions, respectively.
Cadmium oxide was dissolved in water by adding concentrated sulphuric acid dropwisely and then zinc sulphate was put into to form zinc-cadmium sulphate solution. Copper sulphate was further dissolved to prepare the zinc-copper-cadmium sulphate solution. Ammonia, ammonium sulphate and zinc sulphate were first dissolved in water to formulate the ammonia solution into which cadmium oxide was added at ambient temperature by stirring. The zinc-cadmium ammonia solution was then filtered. In the same way, the zinc-copper-cadmium ammonia solution was made by dissolving copper sulphate. The concentrations of zinc, copper and cadmium ions in the solutions were 30-55 g/L, 6.0-6.3 g/L and 3.5-7.2 g/L, respectively. The pH value in the sulphate salt solution was adjusted to 6.5 by using 80 g/L NaOH solution. The concentrations of ammonia and ammonium sulphate in the ammonia solution were 15 g/L and 150 g/L, respectively.
2.2 Experimental set-up and procedure
Two lead-silver alloy anode plates with an efficient area of 68 cm2 were used as the anode between which a aluminium cathode of 46.1 cm2 was inserted with a interpolar distance of 35 mm. A beaker with 2 000 mL volume as an electrolytic cell was put on a magnetic stirrer (IKA RET basic C) in which the electrolytic solution was agitated. The cathode current density was 50 A/cm2 and a DC regulated power supply (WYK-3010) was employed for current supply. Experimental samples of 20 mL were taken for analysis each time at intervals. Efficiency of electrolytic separation was calculated from the concentrations of the metal ions in the electrolyte solutions.
35% (volume fraction) LIX984N diluted by sulfonated kerosene was used as an extractant to separate copper ion from cadmium ion in the ammonia solution in a 250 mL separatory funnel. 100 mL ammonia solution and 50 mL organic phase were mixed each time at 2?1 (A/O) phase ratio. The ammonia solution and the organic phase were mixed on an electric oscillator with 5 min of contact time and 3 min of standing time. The organic phase was separated and subsequently mixed with water for 3 min. The phase ratio of the washing water to the organic was 1?2 (A/O). The washed organic was then stripped using 25 mL of 200 g/L sulphuric acid in a separatory funnel on an electric oscillator for 8 min and demixed after standing for 5 min.
3 Results and discussion
3.1 Concentration variation of copper and cadmium
All tests were conducted at room temperature with the four types of electrolyte solutions. The results showed that the deposited cadmium was uniform and compact in the Zn-Cd sulphate solution while the pH value of the solution decreased to 1.5. In the Zn-Cu-Cd sulphate solution, the rosy copper was first deposited on the surface of aluminium plate and then the deposited product became grey after a period of electrolysis. The blue colour of copper sulphate became light gradually until transparent at the final electrolysis stage, indicating that almost all the copper ions were removed from the solution. In the Zn-Cd ammonia-ammonium sulphate solution, a loose spongy powder product with black colour was obtained, and can be easily detached from the aluminium cathode during electrolysis. In contrast, although rosy copper appeared first in the Zn-Cu-Cd ammonia-ammonium sulphate solution, the electrolyte solution was still in dark blue colour at the end of 8.5 h of electrolysis. What is more, the electrolytic product was combined closely with the aluminium cathode, resulting in great difficulty in separating the deposited product.
The concentration variations of Zn, Cu and Cd ions before and after electrolysis in the four electrolyte solutions are presented in Table 1. It can be seen that zinc ion concentrations showed almost no change after 8.5 h of electrolysis in different solutions. In Zn2+ and Cd2+ containing solutions, the Cd ion concentration decreased to a low level. Especially, it was only about 0.005 g/L after electrolysis in Zn-Cd ammonia-ammonium sulphate solution. The depositing rates of copper and cadmium were all low from the Zn-Cu-Cd ammonia-ammonium sulphate solution. About 53.7% copper was deposited preferentially from the Zn-Cu-Cd sulphate solution.
Table 1 Concentrations of zinc, copper and cadmium ions before and after electrolysis

As the standard electrode potentials of copper (0.337 V) and cadmium (-0.44 V) are more positive than that of zinc (-0.76 V) and hydrogen over-voltage on cadmium is high, cadmium could be deposited from Zn-Cd sulphate solution. Cadmium can also be co-deposited when the copper ion concentration is low enough, while the concentration of zinc ion keeps unchanged in the solutions after electrolysis. In ammonia solution, Zn, Cu and Cd ions will form complexes with NH3 or OH- anions, and the free ion concentrations of Zn, Cu and Cd will then be reduced, decreasing their electrode potentials:
(1)
There is a great difference among the standard electrode potentials of Zn, Cu and Cd. So, the priority order for electrodeposition of the metals will not change.
The concentrations of Cu and Cd ions as a function of electrolysis time are shown in Figs.1-4. As seen in Fig.1 and Fig.2, cadmium or copper could be removed easily from zinc sulphate solution. Fig.3 shows that the concentration of Cd ion decreased linearly within 4.5 h of electrolysis in Zn-Cd ammonia-ammonium sulphate solution and then its change became gentle. Compared with the electrodeposition rates in zinc sulphate solutions, Fig.4 demonstrates that it was unfavourable for copper or cadmium to be separated effectively from the zinc containing ammonia solution. That is to say, copper and cadmium could not be removed simultaneously by electrolysis from the ammonia solution. The copper ion must be removed before Cd electrodeposition. So, other methods should be developed for copper separation from cadmium from zinc containing ammonia solution.
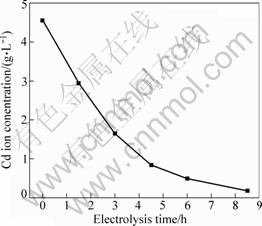
Fig.1 Concentration of Cd ion in Zn-Cd sulphate solution versus electrolysis time

Fig.2 Concentration of Cu and Cd ions in Zn-Cu-Cd sulphate solution versus electrolysis time
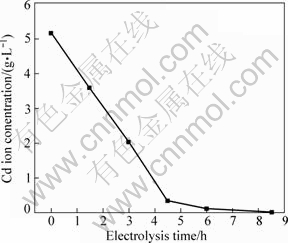
Fig.3 Concentration of Cd ion in Zn-Cd ammonia-ammonium sulphate solution versus electrolysis time

Fig.4 Concentration of Cu and Cd ions in Zn-Cu-Cd ammonia-ammonium sulphate solution versus electrolysis time
3.2 Solvent extraction of copper in ammonia solution
From the above experimental results, it can be seen that the separation of Zn, Cu and Cd was difficult owing to the low deposition rates of Cu and Cd in Zn-Cu-Cd ammonia-ammonium sulphate solution. In contrary, the deposition rate of Cd ion from Zn-Cd ammonia-ammonium sulphate solution was very high. Thus, the separation of Zn and Cd would be favored by preferential removal of Cu from the Zn-Cu-Cd ammonia-ammonium sulphate solution.
35% LIX984N (volume fraction) was used to extract copper from the waste Zn-Cu-Cd ammonia-ammonium sulphate solution with 1.02 g/L Cu2+ and 5.18 g/L Cd2+ after electrolysis. It was shown that the copper ion concentration in the extraction raffinate was only 0.002 g/L after one-stage extraction while the cadmium ion concentration was 5.10 g/L. Namely, the extraction rates of copper and cadmium were 99.8% and 1.54%, respectively. The copper-loaded organic phase was stripped for one time with 200 g/L sulphuric acid. The stripping rate of copper was 99.5% and the cadmium ion concentration was 0.025 g/L in the stripping solution. The results indicate that copper could effectively be separated through solvent extraction from the Zn-Cu-Cd ammonia-ammonium sulphate solution with high zinc and cadmium ion concentrations. Subsequently, cadmium was then deposited by electrolysis from the copper-free ammonia solution, producing a impurity-removed zinc ammonia solution. If necessary, only a small amount of zinc powder is consumed for further purification of the zinc ammonia solution.
4 Conclusions
1) The separation of Zn, Cu, and Cd in solutions was feasible by low current density electrolysis combined with solvent extraction.
2) The electrodeposition rate of cadmium in Zn-Cd sulphate solution was higher than in Zn-Cd ammonia-ammonium sulphate solution.
3) Copper should be removed by solvent extraction before Cd electrodeposition, and a zinc ammonia-ammonium sulphate solution was possibly produced with less than 0.002 g/L Cu2+ and 0.005 g/L Cd2+ for zinc recovery.
References
[1] ZHAO Hong, WANG Tai-xiang, GUO Shu-dong, Extraction technology for copper-cadmium slag in Northwest Smelter [J]. Gansu Metallurgy, 2002(4): 8-10, 32. (in Chinese)
[2] QIAO Ning. Recovery of zinc, copper and cadmium from copper-cadmium slag [J]. Hydrometallurgy of China, 1998, 65(1): 41-42. (in Chinese)
[3] HE Liang-hui, LI Zi-qiang, LI Sheng-zhang, WANG Zu-sen, LI Zheng-shan. Recovery of sponge cadmium from copper-cadmium slag [J]. Inorganic Chemicals Industry, 1991(2): 31-35. (in Chinese)
[4] HUANG Zhuang, TANG Mo-tang, HE Jing. Extracting cadmium from zinc concentrate roasting dust collected by electrostatic precipitator [J]. China Nonferrous Metallurgy, 2005, 34(4): 51-54. (in Chinese)
[5] SAFARZADEH SADEGH M, BAFGHI M S, MORADKHANI D, OJAGHI ILKHCHI M. A review on hydrometallurgical extraction and recovery of cadmium from various resources [J]. Minerals Engineering, 2007, 20(3): 211-220.
[6] SAFARZADEH SADEGH M, MORADKHANI D, OJAGHI-ILKHCHI M. Kinetics of sulfuric acid leaching of cadmium from Cd-Ni zinc plant residues [J]. Journal of Hazardous Materials, 2009, 163(2/3): 880-890.
[7] SHIRAISHI T, TAMADA M, SAITO K, SUGO T. Recovery of cadmium from waste of scallop processing with amidoxime adsorbent synthesized by graft-polymerization [J]. Radiation Physics and Chemistry, 2003, 66(1): 43-47.
[8] ZHU Jian-xin, LI Jin-hui, NIE Yong-feng. Recovery of cadmium by high-temperature vaccum evaporation from Ni-Cd batteries [J]. Trans Nonferrous Met Soc China, 2003, 13(2): 254-257.
[9] NOGUEIRA C A, MARGARIDO F. Leaching behaviour of electrode materials of spent nickel-cadmium batteries in sulphuric acid media [J]. Hydrometallurgy, 2004, 72(1/2): 111-118.
[10] WANG Fei, WANG Lian-jun, LI Jian-sheng, SUN Xiu-yun, HAN Wei-qing. Adsorption behavior and mechanism of cadmium on strong-acid cation exchange resin [J]. Trans Nonferrous Met Soc China, 2009, 19(3): 740-744.
[11] GOUVEA LIGIANE R, MORAIS CARLOS A. Recovery of zinc and cadmium from industrial waste by leaching/cementation [J]. Minerals Engineering, 2007, 20(9): 956-958.
[12] LIU Yun-guo, FAN Ting, ZENG Guang-ming, LI Xin, TONG Qing, YE Fei, ZHOU Ming, XU Wei-hua, HUANG Yu-e. Removal of cadmium and zinc ions from aqueous solution by living Aspergillus niger [J]. Trans Nonferrous Met Soc China, 2006, 16(3): 681-686.
[13] CA?IZARES P, P?REZ A, CAMARILLO R, MAZARRO R. Simultaneous recovery of cadmium and lead from aqueous effluents by a semi-continuous laboratory-scale polymer enhanced ultrafiltration process [J]. Journal of Membrane Science, 2008, 320(1/2): 520-527.
[14] RAMACHANDRA R B, NEELA P D, RAJESH K J. Solvent extraction of cadmium(Ⅱ) from sulphate solutions using TOPS 99, PC 88A, Cyanex 272 and their mixtures [J]. Hydrometallurgy, 2004, 74(3-4):277-283.
[15] KUMAR V, KUMAR M, JHA M K, JEONG J, LEE J C. Solvent extraction of cadmium from sulfate solution with di-(2-ethylhexyl) phosphoric acid diluted in kerosene [J]. Hydrometallurgy, 2009, 96(3): 30-234.
[16] ZHAO Zun-sheng, YAO Feng-yi, SONG Le-shan. Preparation of pure zinc sulphate by pulse current electrolysis [J]. Chemical Industry and Engineering, 1988(3): 20-22, 6. (in Chinese)
[17] SUN Xiao-hua, YIN Fu-tang. Recovery of metal values from copper-cadmium slag via fluidized bed electrode [J]. Environmental Protection of Chemical Industry, 1989(1): 14-17. (in Chinese)
[18] TANG Mo-tang, LU Jun-le, YUAN Yan-shen, YAN De-sheng, HE Qing-pu. On the ammoniation-complex equilibria in the system of Zn(Ⅱ)-NH3-(NH4)2SO4-H2O [J]. Journal of Central South University of Technology (Natural Science), 1994, 25(6): 701-705. (in Chinese)
[19] ZHANG Bao-ping, TANG Mo-tang. Leaching zinc oxide ores in the system of NH4Cl-NH3-H2O [J]. Journal of Central South University of Technology (Natural Science), 2001, 32(5): 483-486. (in Chinese)
[20] ZHANG Bao-ping, TANG Mo-tang, YANG Sheng-hai. Treating zinc oxide ores using ammonia-ammonium chloride to produce electrolysis zinc [J]. Journal of Central South University of Technology (Natural Science), 2003, 34(6): 619-623. (in Chinese)
Foundation item: Projects(50774014, 50734005) supported by the National Natural Science Foundation of China; Project(2008AA03Z514) supported by the National High-tech Research and Development Program of China
Corresponding author: WANG Cheng-yan; Tel: +86-10-88399551; Fax: +86-10-88377374; E-mail: wchy3207@sina.com
DOI: 10.1016/S1003-6326(09)60174-6
(Edited by YANG Bing)