文章编号:1004-0609(2009)07-1182-07
AZ31镁合金挤出板降温热轧的组织和织构的演变
曲家惠1,岳明凯1,黄 涛2
(1. 沈阳理工大学 装备工程学院,沈阳 110168;
2. 沈阳师范大学 物理科学与技术学院,沈阳 110034)
摘 要:研究AZ31镁合金挤出板坯在降温热轧过程中的组织和织构的演变规律。结果表明:退火前滑移和孪生是主要的变形机制和取向硬化机制;退火后长条晶的滑移和细小等轴晶晶界扩散迁移的共同作用成为主要的变形机制;随着压下量的增大,析出物开始破碎和分散,压下量在70%~80%之间时,基面织构组分的取向密度存在突变最大值,形成硬取向较强的{0001}基面织构,软化退火能大幅减弱硬取向;通过一道67%大压下量和一次软化退火可顺利地将AZ31镁合金轧制成厚0.5 mm的薄板。
关键词:镁合金;轧制;退火;组织;织构
中图分类号:TG 146.22 文献标识码:A
Evolution of microstructure and texture of AZ31 magnesium alloy extrusion sheet by hot rolling with falling temperature
QU Jia-hui1, YUE Ming-kai1, HUANG TaoWANG Fu2
(1. School of Equipment Engineering, Shenyang Ligong University, Shenyang 110168, China;
2. College of Physical Science and Technology, Shenyang Normal University, Shenyang 110034, China)
Abstract: The evolution law of microstructure and texture in extruded sheets of magnesium alloy AZ31 during the hot rolling falling temperature process was studied. The results show that slipping and twinning are the major deforming and orientational hardening mechanism before annealing while the sliding of long grain in combination with the diffusing transfer of fine equiaxed grain boundary becomes a major deforming one after annealing. With increasing the reduction, the precipitation falls to pieces and spreads around. And the basal plane texture component has a maximum mutation value of orientation density with reductions of 70%?80%. So a basal plane texture component {0001} is formed, which has stronger orientation density that can be greatly reduced by softening annealing. A sheet of 0.5 mm in thickness can be made from magnesium alloy AZ31 by one 67% reduction pass and one softening annealing pass.
Key words: magnesium alloy; hot-rolling; annealing; microstructure; texture
形变镁合金的发展方向是大批量连续生产高成形性的薄板材,以实现在汽车覆盖件和一些薄壁电子器件外壳上更广泛的应用[1?2]。研究结果表明,生产轧制薄板首先是选择板坯,挤压板坯要优于铸造板坯[3]。塑性较差的六方结构镁合金在轧制时易出现裂纹,尤其是在1 mm以下薄板带的终轧阶段,轧制后期得到的是形变组织[4?5],因此要插入中间再结晶退火以改善成形性,使进一步变形得以进行。镁合金晶粒经过细化后可提高其伸长率和塑性加工性能。利用轧制时发生的动态再结晶可以实现晶粒的有效细化,但较高的终轧温度不利于板型的控制和保持高的表面光洁 度[6];静态再结晶在改善成形性的基础上也可实现晶粒的细化[7],但二者晶粒细化的机理不同,热轧过程中镁合金将形成强{0002}基面织构[7?8]。万玉刚等[9]对温轧AZ31镁合金板材进行退火处理,改善了组织与织构,等轴状的晶粒变得更加细小均匀,{0002}面硬取向有所减弱。织构特征能定量地反映在变形过程中材料微观结构的演变规律,因此,织构分析是研究镁合金塑性变形机制和动态再结晶过程中新晶粒形核机制的有效手段。本文作者研究了挤压板坯多道次降温热轧的组织和织构的演变规律,探寻组织和织构与压下量和软化退火工艺的关系,以便为实际生产提供理论指导。
1 实验
实验材料的化学成分如表1所列。镁合金在东北大学材料电磁过程研究教育部重点实验室制备。热轧板的制备工艺为:将电磁冶炼制备的镁合金铸棒(d 150 mm)热挤压成挤出板(140 mm×4 mm)。热挤压工艺条件为:坯料预热温度400 ℃,挤出筒温度350 ℃,挤出温度400 ℃。在轧辊直径200 mm和宽300 mm的轧机上,挤出板在预热温度400 ℃及轧辊加热温度 150 ℃下,第一道热轧板厚约1.4 mm,直接返回第二道热轧,板厚1 mm;1 mm厚轧板重新在400 ℃下软化退火40 min,同上条件进行第三道热轧,板厚约 0.6 mm,直接返回第四道热轧,板厚0.4 mm。挤出板及其热轧板的实测厚度和压下量如表2所列(第四道热轧取两个不同压下量的样品)。
表1 AZ31镁合金的化学成分
Table 1 Compositions of AZ31 magnesium alloy (mass fraction, %)

表2 挤出板热轧时每道次的厚度和压下量
Table 2 Thickness and reduction in each pass during hot rolling of extruded sheets
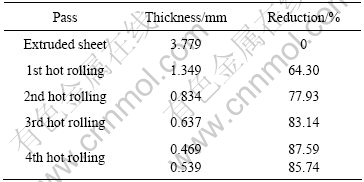
在LeicaDM/T?400型光学显微镜和Philips?G20透射电子显微镜上进行金相显微组织观察。电镜样品的制备方法如下:沿平行于轧制表面取样,研磨至 50 μm左右;在室温真空条件下,利用离子减薄仪从基体一侧单面减薄至穿孔,然后用双枪小角度双面离子减薄去除表面氧化膜。
采用Philip 公司的X’Pert PRD 型织构测量仪进行织构测定,测定时选用Co Kα靶作为入射光源,管电压为35 kV,管电流为40 mA,按反射法测量{10
1}、{10
2}、{11
0}、{10
3} 4张不完整极图,测量范围:α为0?~70?,间隔5?,β为0?~360?,测量步长5?。采用LaboTex3.0定量织构分析软件计算晶粒取向分布函数(ODF),即使用邦厄(Bunge)定义的欧拉角,得出任意取向(φ1, Φ, φ2)的恒φ2(0?~60?)和间隔5?的13个ODF截面图。根据镁晶体的对称性,选取恒φ2为0?和30? 2个ODF截面图进行取向密度f(g)择优分布的分析。
2 结果
2.1 挤出板及其热轧板样品的横截面组织
图1所示为AZ31镁合金原始挤出板及其各道次热轧板的金相组织(水平方向为挤出和轧制方向)。图1(a)所示为原始挤压板的组织,可以看出是大的再结晶等轴晶粒。图1(b)所示为压下量为64.30%的一道热轧板的组织,由于压下量较大,在晶内滑移的作用下,晶粒显著拉长,晶界变得模糊不清。在压下量为77.93%的连续二道热轧时(见图1(c)),随压下量增加,粗大的晶粒在轧挤压力作用下,在垂直于压力方向被压扁,进而发生弯曲,破碎成细的晶粒;同时发生晶粒间的相对转动,带动已破碎的第二相发生滑移和变形,呈离散状分布;在平行流线上分布着大量细小、致密的等轴晶粒,可见轧制形变组织已发生再结晶,虽然出现再结晶组织,但孪晶组织仍占绝大部分。在对二道热轧板软化退火后,进行压下量为83.14%的三道热轧,如图1(d)所示,再结晶组织大量增加,原晶粒的晶界处和晶内形成无畸变的新晶粒,看不到孪晶组织。连续进行四道热轧,压下量分别为85.74%和87.59%,如图1(e)和1(f)所示,随着压下量的进一步增加,几乎全为再结晶组织,晶粒细小,但变形仍不均匀。
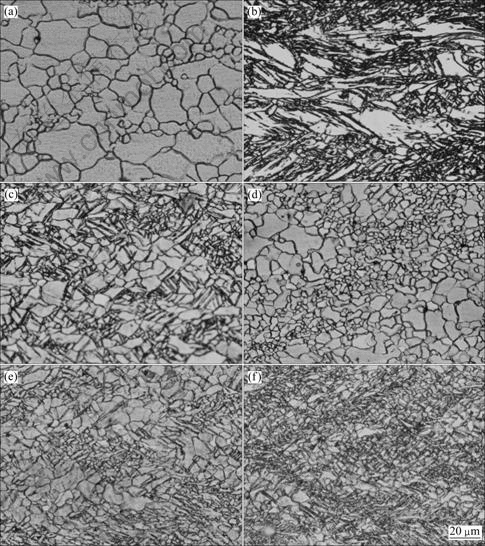
图1 挤出板和不同道次压下量的热轧板的金相组织
Fig.1 Microstructures of AZ31 extruded sheet and hot-rolling sheets with different reductions in passes: (a) Extruded sheet; (b) 64.30% in 1st pass; (c) 77.93% in 2nd pass; (d) 84.07% in 3rd pass; (e) 85.74% in 4th pass; (f) 87.59% in 4th pass
2.2 挤出板及其热轧板样品的微观组织
图2所示为不同道次压下量的热轧板的TEM像。由图2(a)可以看出,在变形初始阶段,发生了大量的孪生变形,在条状孪晶内有很高的位错密度,这说明孪生是在严重的位错塞积后发生的,同时孪生诱发动态再结晶,晶粒A和B的电子衍射花样分析晶带轴均为<001>。图2(b)所示为软化退火后的四道热轧板的TEM像,变形后的组织中再结晶核心长大为均匀细小的再结晶等轴晶粒,这些再结晶小晶粒的内部几乎没有位错和孪晶的存在。图3所示为不同道次压下量的热轧板析出物的TEM像。由图3可以看出,压下量小时可析出完整的棒状析出物,随着压下量的增大,析出物开始破碎和分散。通常由α-Mg与β-Mg17Al12组成共晶体,大部分元素Mn则与Al 形成AlMn析出相弥散分布于共晶体内。图3所示的析出物随压下量的增加而变化的原因和影响还需进一步研究。
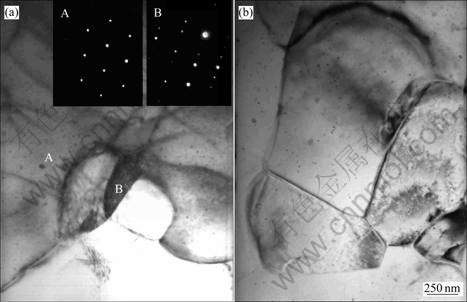
图2 不同道次压下量的热轧板的TEM像
Fig.2 TEM images of hot-rolling sheets with different reductions in passes: (a) 64.30% in 1st pass; (b) 87.59% in 4th pass
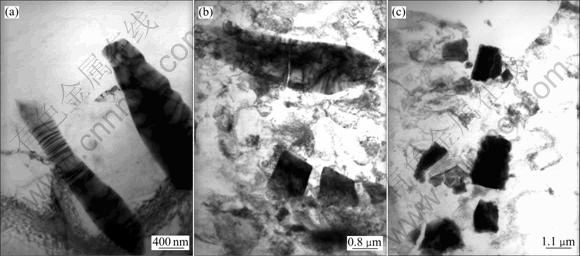
图3 不同道次压下量的热轧板析出物的TEM像
Fig.3 TEM images of precipitation of hot-rolling sheets with different reductions in passes: (a) 64.30% in 1st pass; (b) 77.93% in 2nd pass; (c) 87.59% in 4th pass
2.3 挤出板在不同形变量下热轧的织构变化
本实验测得压下量分别为0%、64.30%、77.93%、83.14%、85.74%和87.59%时的恒φ2—ODF截面图,如图4(a)~(f)所示。在不同压下量下,AZ31镁合金热轧板的ODF恒φ2系列截面图反映了AZ31挤出板的宏观织构随不同道次热轧压下量的增加而变化的规律。在热轧变形过程中,随着热轧压下量的增加,原始镁合金挤出板中不同初始织构组分均有不同程度的变化。当一道热轧压下量为64.30%时,初始织构向(80?,15?,0?)聚集增强,其取向密度由9.57增至11。当二道热轧压下量为77.93%时,热轧板中形成了很强的基面织构(0?,5?,0?)和(90?,0?,30?),取向密度分别为28.77和25.19;而初始织构组分(80?,15?,0?)减弱,其取向密度由9.57减弱至4.59。当二道热轧板经软化退火后进行三道和四道连续热轧时,二道热轧板的强织构被弱化,织构向软取向(80?,15?,0?)聚集缓慢增强。四道热轧压下量为87.59%时,织构组分有(0?,0?,0?)、(30?,0?,0?)、(80?,15?,0?)和(0?,5?,30?),对应取向密度分别为8.08、7.81、10.40和8.68。
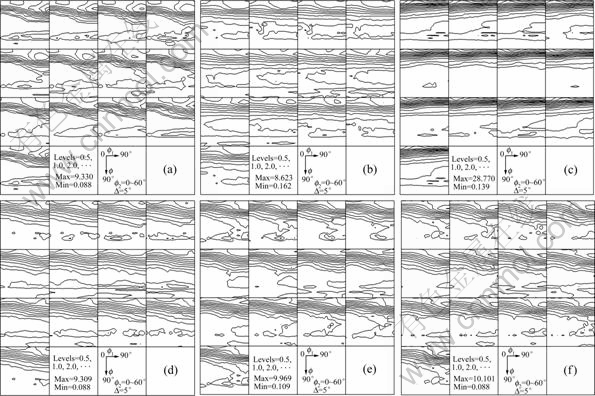
图4 AZ31挤出板和不同道次压下量的热轧板的恒φ2—ODF截面图
Fig.4 Constant φ2—ODF sections of AZ31 extruded sheet and hot-rolling sheets with different reductions in passes by hot-rolling: (a) Extruded sheet; (b) 64.30% in 1st pass; (c) 77.93% in 2nd pass; (d) 84.07% in 3rd pass; (e) 85.74% in 4th pass; (f) 87.59% in 4th pass
3 讨论
3.1 位错、孪生与动态再结晶
镁合金热轧板材的组织主要由长条晶、孪晶、切变带等变形组织及细小的动态再结晶晶粒组成。热轧过程中,温度、变形量、变形速率等因素将会影响组织形态与再结晶的发生[10?14]。图1可知,切变带和动态再结晶是其主要的细化机制。这与陈彬等[15]在研究300和400 ℃下大压下量高温轧制AZ31镁合金时得到的结果不同。在本实验大形变量降温热轧变形过程中,镁合金组织同时产生动态再结晶、变形孪晶和切变带,在变形过程中三者发生相互转化。
降温轧制开始阶段由于温度较高,首道轧制具有较大的压下量,因而组织中主要发生动态再结晶和剪切带变形,生成了大量等轴小晶粒,尺寸约2~3 μm,随着轧制温度的下降,动态再结晶组织成分开始减少,孪晶及切变带开始增多。因为切变带能起到细化组织的作用[4],所以切变带内含有大量细小(亚)晶粒,其尺寸不到1 μm。这些组织在退火后可长大为较均匀的细小再结晶组织,再进行轧制又能形成扩展的切变带。在轧制温度区间的上限,挤出板首道大压下量热轧形成长条晶粒,说明在此温度下这些晶粒内有足够的独立滑移系,可以均匀变形;在温度区间的下限,连续二道热轧形成大角晶界形变组织,滑移变得困难,而孪生往往在滑移困难时出现,通过孪生系统的运动以补充滑移系统的不足。孪生在密排六方(hcp)晶体低温塑性变形中的重要性愈来愈引起广泛注意,其对塑性、加工硬化和断裂过程有重要影响。因此,对hcp晶体
中孪晶的产生以及交互作用的研究是近几年来的一个热点。hcp晶体真正意义上的孪生变形依赖于滑移与孪生的协调进行,并最终受制于孪生[16]。已滑移的孪晶区域和剩下的基体晶粒有着不同的晶体取向,也可以把这一过程看作产生了新晶粒。随着孪晶在基体晶粒中的成核和成长又增加了界面能,造成局部应力集中,同时可见形变过程形成含大量细小亚晶粒的扩展的切变带。连续两道降温热轧后实施软化退火,通过静态再结晶削弱基面织构并消除切变带形成细晶,防止切变带裂纹。图2表明这些再结晶核心在晶界扩散和晶界迁移的作用下长大为再结晶小晶粒,这些再结晶小晶粒的内部几乎没有位错的存在。所以,软化退火前后的变形机制是不同的。多道次降温轧制加一次软化退火的薄板轧制工艺,即第一道轧制温度较高,采用大压下量降低板材厚度;随板材温度下降,再采用较小的压下量,及通过软化退火形成静态再结晶和回复细化组织。研究结果表明,通过该轧制方法可以制成厚0.4 mm的薄板,且平均晶粒尺寸可达到5 μm,具有抑制晶粒长大的优点。
3.2 挤出板多道次热轧的宏观织构的演变
图5和图6所示为不同压下量的宏观基面织构和强点织构的变化。由图5可以看出,随着压下量的加大,基面织构取向的晶粒间主要是0~30?<0001>的取向关系。由图6可以看出,非基面织构组分和基面织构组分之间发生转换,压下量在70%~80%之间时,基面织构组分的取向密度存在突变最大值,镁合金在这种条件下形成了硬取向较强的{0001}基面织构,取向硬化使塑性变差给后续变形带来不利,在这种情况下应实施软化退火。退火处理后,随着回复、再结晶等过程的发生,等轴状的晶粒变得更加细小均匀,织构中{0001}面硬取向经软化退火后减弱,而织构中软取向织构组分(80?,15?,0?)的取向密度有所增强,明显提高了温轧AZ31镁板的塑性。因此对镁合金织构的控制具有十分重要的意义。

图5 AZ31挤出板和不同道次压下量的热轧板的基面织构组分的取向密度
Fig.5 Orientational density of basal plane textures (φ1, 0?, 0?) of AZ31 extruded sheet and hot-rolling sheets with different reductions in passes

图6 AZ31挤出板和不同道次压下量的热轧板的强点织构组分的取向密度
Fig.6 Orientational density of strength point textures of AZ31 extruded sheet and hot-rolling sheets with different reductions in passes
挤出板预热后连续一、二道降温热轧,以及软化退火后再进行三、四道降温热轧的织构演变表明,退火前后织构不同,形变机制也有差异。虽然新晶粒的取向都逐渐转向基面织构取向附近,但并非完全相同,说明动态再结晶时形变机制是不同的,宏观织构是粗大长条形变晶粒和细小的再结晶等轴晶共同作用的结果。
大角度等轴晶的变形,说明在长条晶粒内部发生均匀变形,有足够的独立滑移系,此时基面取向的晶粒对于棱面滑移有高的取向因子(或Schmid因子)。又因高温下棱面滑移的临界分切应力已下降到与基面滑移对应到的临界分切应力相近的数量级,因而可以推断,长条变形晶粒良好的塑变能力是棱面滑移造成。形变长条晶粒都是基面取向晶粒,也有一些为转动的基面取向,而细小等轴的再结晶晶粒的取向主要为基面取向。可以推断,形变时亚晶粒取向必须偏转到与基面取向的形变晶粒成大角度或大取向差时才能构成真正的再结晶新晶粒,它们只能具有转动的基面取向。随着轧制道次的增多和板材厚度的减薄,一部分再结晶晶粒因形变逐渐转到基面取向,同时有产生一些转动的基面取向新晶粒,所以宏观织构不变或逐渐增强。正由于形变机制的作用,新晶粒总趋向于处于在基面织构取向,而不是轻易地转到其它取向。
4 结论
1) 采用挤出板坯在预热温度400 ℃及轧辊加热温度150 ℃下,连续一、二道降温热轧,以及软化退火后再进行三、四道降温热轧,可顺利地将AZ31镁合金轧制成厚0.5 mm的薄板。该工艺具有一道67%大压下量和一次软化退火的特点,大大提高了轧制效率。
2) 退火前滑移和孪生是主要的变形机制和硬化机制;退火后长条晶的滑移和细小的再结晶等轴晶晶界扩散迁移的共同作用成为主要的变形机制。软化退火前后具有不同初始取向的样品形成类似的基面织构,但新晶粒取向的择优过程并不完全相同。
3) 压下量在70%~80%之间时,基面织构组分的取向密度存在突变最大值,形成了硬取向较强的 {0001}基面织构。在这种情况下实施软化退火,织构中{0001}面硬取向大幅减弱,而织构中软取向织构组分(80?,15?,0?)的取向密度有所增强,明显提高了温轧AZ31镁合金板的塑性。
4) 压下量小时析出完整的棒状析出物,随着变形量的增加,析出物开始破碎和分散。
REFERENCES
[1] DOEGE E, DRODER K. Sheet metal forming of magnesium wrought alloys formability and process technology[J]. J Mater Proc Technol, 2001, 115: 14?19.
[2] OGAWA N, SHIOMI M, OSAKADA K. Forming limit of magnesium alloy at elevated temperature for precision forging[J]. Int J Mach Tools and Manuf, 2002, 42: 607?614.
[3] 张青来, 卢 晨, 朱燕萍, 丁文江, 贺继泓. 轧制方式对AZ31镁合金薄板组织和性能的影响[J]. 中国有色金属学报, 2004, 14(3): 391?397.
ZHANG Qing-lai, LU Chen, ZHU Yan-ping, DING Wen-jiang, HE Ji-hong. Effect of rolling method on microstructure and properties AZ31 magnesium alloy thin sheet[J]. The Chinese Journal of Noferrous Metals, 2004, 14(3): 391?397.
[4] YANG P, MAO W M, REN X P, TANG Q B. On the shear bands in magnesium alloy AZ31[J]. Trans Nonferrous Met Soc China, 2004, 14(5): 851?857.
[5] 余 琨, 黎文献. Mg-Al-Zn系变形镁合金轧制及热处理后的组织和性能[J]. 金属热处理, 2002, 27(5): 8?11.
YU Kun, LI Wen-xian. Microstructures and properties of Mg-Al-Zn wrought alloys in as-rolling and annealing states[J]. Metal Heat Treatment, 2002, 27(5): 8?11.
[6] STYCZYNSKI A, HARTIG C, BOHLEN J, LETZIG D. Cold rolling textures in AZ31 wrought magnesium alloy[J]. Scripta Mater, 2004, 50: 943?947.
[7] MYAGCHILOV S, DAWSON P R. Evolution of texture in aggregates of crystals exhibiting both slip and twinning[J]. Modelling and Simulation in Materials Science and Engineering, 1999, 21(7): 975?1004.
[8] PRADO M T, VAUJE J A, RUANO O A. Effect of sheet thickness on the microstructure evolution of an Mg alloy during large strain hot rolling[J]. Scripta Materialia, 2004, 50: 667?671.
[9] 万玉刚, 吕保义, 康永林, 王朝辉, 蔡庆伍, 张济山. 退火工艺对温轧AZ31板组织、织构及性能的影响[J]. 稀有金属, 2007, 31(4): 412?415.
WAN Yu-gang, L? Bao-yi, KANG Yong-lin, WANG Zhao-hui, CAI Qing-wu, ZHANG Ji-shan. Effects of annealing technique on microstructure, texture and mechanical properties of warm-rolling AZ31 sheet[J]. Chinese Journal of Rare Metals, 2007, 31(4): 412?415.
[10] YU K, LI W X. Plastic deformation behaviors of a Mg-Ce-Zn-Zr alloy[J]. Scripta Mater, 2003, 41: 1319?1323.
[11] TAN J C, TAN M J. Dynamic continuous recrysta11ization characteristics in two stage deformation of Mg-3AI-1Zn alloy sheet[J]. Mater Sci Eng A, 2003, 339: 124?132.
[12] PEREZ-PRADO M T, VALLE J A, RUANO O A. Achieving high strength in commercial Mg cast alloys through large strain rolling[J]. Materials Letters, 2005, 59(26): 3299?3303.
[13] POLIAK E I, JONAS J J. A one-parameter approach to determining the critica1 conditions for the initiation of dynamic recrystallization[J]. Acta Mater, 1996. 41: 127?136.
[14] 张凯锋, 尹德良, 韩文波. 热轧AZ31镁合金温变形中的微观组织演变[J]. 航空学报, 2005, 26(4): 505?509.
ZHANG Kai-feng, YIN De-liang, HAN Wen-bo. Microstructure evolution in warm deformation of hot-rolled AZ31 Mg alloy[J]. Acta Aeronautica Et Astronautica Sinica, 2005, 26(4): 505?509.
[15] 陈 彬, 林栋樑, 曾小勤, 卢 晨. AZ3 1镁合金大压下率轧制的研究[J]. 锻压技术, 2006, 31(3): 1?3.
CHEN Bin, LIN Dong-liang, ZENG Xiao-qin, LU Chen. Research on heavy reduction rate rolling of AZ31 magnesium alloy[J]. Forging & Stamping Technology, 2006, 31(3): 1?3.
[16] BROOKS C R. Heat Treatment structure and properties of nonferrous alloys[M]. OH: Metals Park, 1982: 324?360.
基金项目:辽宁省教育厅科学技术研究资助项目(2008T184)
收稿日期:2008-09-02;修订日期:2009-04-10
通讯作者:曲家惠,副教授,博士;电话:024-24681918;E-mail: qjh915@163.com
(编辑 李向群)