
Dynamic recrystallization and texture development during hot deformation of magnesium alloy AZ31
YANG Xu-yue(杨续跃)1, 2, JI Ze-sheng(吉泽升)3, H. MIURA4, T. SAKAI4
1. School of Materials Science and Engineering, Central South University, Changsha 410083, China;
2. Key Laboratory of Nonferrous Metal Materials Science and Engineering, Ministry of Education,
Central South University, Changsha 410083, China;
3. College of Materials Science and Engineering, Harbin University of Science and Technology,
Harbin 150040, China;
4. Department of Mechanical Engineering and Intelligent Systems, UEC Tokyo, Tokyo 182-8585, Japan
Received 10 June 2008; accepted 20 October 2008
Abstract: The dynamic recrystallization(DRX) and texture development, taking place during hot deformation of magnesium alloy AZ31 with a strong wire texture, were studied in compression at 673 K (0.73 Tm). Two kinds of samples were machined parallelly to the extruded and transverse directions of Mg alloy rods. New fine grains are evolved at original grain boundaries corrugated at low strains and develop rapidly in the medium range of strain, finally leading to a roughly full evolution of equiaxial fine grains. Kink bands are evolved at grain boundaries corrugated and also frequently in grain interiors at low strains. The boundary misorientations of kink band increase rapidly with increasing strain and approach a saturation value in high strain. The average size of the regions fragmented by kink band is almost the same as that of new grains evolved in high strain. These characteristics of new grain evolution process are not changed by the orientation of the samples, while the flow behaviors clearly depend on it. It is concluded that new grain evolution can be controlled by a deformation-induced continuous reaction, i.e. continuous dynamic recrystallization(DRX). The latter is discussed by comparing with conventional, i.e. discontinuous DRX.
Key words: magnesium alloy; hot deformation; continuous dynamic recrystallization; texture
1 Introduction
Magnesium(Mg) and its alloys show generally low ductility because of the few slip systems in hexagonal close-packed(HCP) lattice and so are categorized in hard plastic materials. On the other hand, it is known[1-2] that fine grains are relatively easily developed and also several slip systems operate in addition to the basal slip plane under warm and hot deformation. Under such conditions, the plastic workability of Mg alloy can be greatly improved due to fine-grained superplasticity[2-3]. There are, however, few studies on new grain development during hot deformation, i.e. dynamic recrystallization(DRX), in HCP metals and alloys. It has been explained in Mg alloys[4-7] that new fine grain evolution can result from continuous DRX including twinning DRX and rotation DRX at ambient to moderate temperatures and, in contrast, from conventional (i.e. discontinuous) DRX including a nucleation of new grains and their larger-scale growth taking place under hot deformation. The reasons why the DRX mechanisms are changed by deformation conditions and the mechanisms operated remained unclear.
The aim of the present work is to study the DRX behavior of a Mg-Al-Zn alloy at temperature of 673 K (about 0.73 Tm, where Tm is the melting point). The relationships between hot deformation behavior and new grain evolution and between the texture development and its effect on DRX are analyzed in detail, and the mechanisms of DRX operating under hot deformation are discussed.
2 Experimental
A commercial Mg alloy AZ31 tested was provided as a hot-extruded rod with the following chemical composition: Al 2.68%, Zn 0.75%, Mn 0.68%, Cu 0.01%,Si 0.003%, Fe 0.003%, and balance Mg (mass fraction). The Mg alloy rods had a strong preferred orientation with the basal planes lying parallelly to the extrusion direction, as shown in Fig.1. The cylindrical samples of 8 mm in diameter and 12 mm in height were prepared from the rod with the axis aligned along the longitudinal (extrusion) direction and transverse one. Here they are called as the L- and T-directions, respectively. The samples were annealed at 733 K for 7.2 ks and then furnace cooled, leading to the evolution of almost equiaxed grains with an average grain size of about 22 mm.
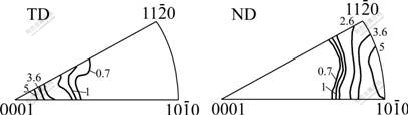
Fig.1 Inverse pole figures for tangential(TD) and normal, i.e. extruded, (ND) direction of AZ31 Mg alloy rod
The compression tests were carried out at constant true strain rates on a testing machine equipped with a water quenching apparatus to freeze instantaneous deformation structures. The samples were deformed at 673 K and mainly at a strain rate of 3×10-3 s-1, followed by water quenching. Each sample was cut along a plane parallel to the compression axis. The surfaces were mechanically polished and electropolished in a solution of nitric acid, glycerol and ethanol with a 1:3:6 volume ratio. The metallographic analysis was carried out using optical microscopy(OM) and scanning electron microscopy(SEM) incorporating an orientation imaging microscopy(OIM) system.
3 Results and discussion
3.1 Flow behaviors and texture development
The true stress—true strain (s—e) curves at 673 K are represented in Fig.2. The flow curves for the L-direction are shown by solid line and those for the T-direction by dashed line. The flow curve for the L-direction shows a rapid hardening, a single peak in relatively low strain and then a strain softening, followed by a stead state flow in high strain. It is interesting to note that the peak flow stress and the magnitude of strain softening increase clearly with increasing strain rate, while the peak strain where the peak stress appears scarcely changes. In contrast, the flow curve for the T-direction shows no appreciable work softening but only a steady state flow. This suggests that hot deformation of the T-direction Mg alloy can be controlled mainly by dynamic recovery.
The initial strong texture (Fig.1) is clearly changed by compression in the L-direction, but scarcely in the T-direction, as shown in Fig.3. Here instead of presenting the data as inverse pole figures, relative intensity of the texture orientations measured in the OIM data is plotted against j, the angle between the compression axis and the basal plane. Such plots are similar to those used by ION et al[4]. The initial texture of the L-direction sample is reoriented gradually by compression. Namely, the alignment of the basal planes initially parallel to the compression axis is rotated gradually by compression and approaches perpendicular to the compression axis in high strain. In contrast, it can be seen that the initial texture in the T-direction sample scarcely changes and the relative intensity increases with increasing strain.
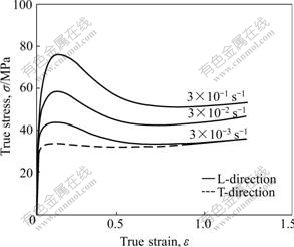
Fig.2 True stress—true strain curves under various strain rates at 673 K
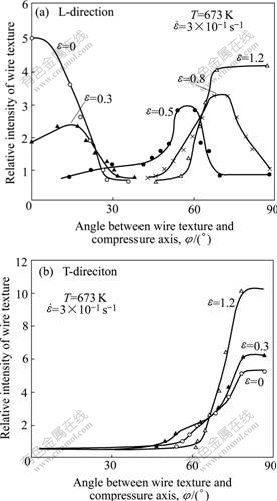
Fig.3 Changes in distribution of wire texture, with basal planes lying parallelly to the extruded direction, in compression at 673 K
It is quite possible, therefore, that work softening in the L-direction sample does not result from new grain development, but rather from a change in the basal plane from the hard slip directions to the soft or stable ones, that is the geometrical softening. It is also well understood why an appreciable work softening does not take place in the T-direction sample because of no clear change in the texture. By the way, it can be seen in Fig.2 that the s—e curves for the L- and T-directions show roughly the same flow stresses in moderate strain above 0.5 and a small work hardening in high strain. This may be because the basal slip planes become more lying perpendicular to the compression axis, as can be seen in Fig.3(b), that is the geometrical hardening.
3.2 Microstructural development during hot defor- mation
The microstructures developed during hot deformation are described here mainly for the results obtained from the L-direction sample. Surface morphology of the sample, deformed to 0.06 at 673 K and at 3×10-3 s-1, is shown in Fig.4. It can be seen that fine slip bands are developed in grain interiors roughly parallel to the compression axis (i.e. the basal planes), grain boundary migration takes place locally in limited distance and some of the boundaries are corrugated. It is remarkable to note here that there are several deformation bands (kink bands)[8-9] evolved and they are traversed and/or intersect in some grain interiors even at e=0.06. Grain boundary sliding and grain rotation boundaries serrated and deformation bands (kink bands) accompanying with fine slip bands in grain interiors) taking place were confirmed by slipping off and rotation of scratched marker lines[10] as well as the appearance of grain boundaries themselves.
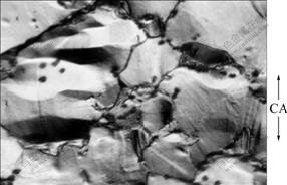
Fig. 4 Surface morphology of AZ31 alloy deformed to e=0.06 at 673 K and 3×10-3 s-1 (Development of local migration of grain
A typical OIM micrograph for the sample deformed to e=0.15 is shown in Fig.5. High-angle boundaries with misorientations more than 15? are delineated by thick- black lines, while low-angle boundaries in the range of 4?-15? by thin-black lines and those in the range of 2?- 4? by white lines. It can be seen in Fig.5 that fine grains with an average size of 10.3 mm are partly evolved along grain boundaries, and new boundaries with low to medium angle misorientations are also evolved in some grain interiors and some of them intersect with each other. These new boundaries correspond exactly to those of the kink bands, as confirmed also in Fig.6. These are considered to be similar to the transition bands or microbands[9]. It is interesting to note that several initial grains are fragmented by the formation of such kink bands and the crystal orientation of each region fragmented is slightly changed even in a grain interior.
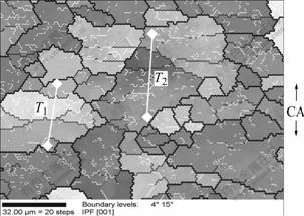
Fig.5 Typical OIM map of AZ31 alloy deformed to strain of 0.15 at 673 K and 3×10-3 s-1 (Thin white lines correspond to boundaries of misorientation >2?, thin black line to >4? and thick black lines to >15?, respectively)
The point-to-point misorientation(θ) defines a relative difference of crystal orientation between two adjacent scan points (0.4 mm), and the cumulative misorientation (Sθ) the one between the first scan point near a grain boundary and a point-n in another one in the opposite side. They were measured along the lines T1 and T2 indicated in Fig.5. Fig.6 shows the results for the θ shown by dotted line and for the Sθ by a mark () measured along the lines T1 and T2. It can be seen that the θ changes discontinuously and the maximum of θ exceeds 5? at several local places, while it ranges from 2? to 3? in the other ones. The Sq changes discontinuously at the same local places. These places correspond exactly to the boundaries of each kink band.
Microstructure development in the L-direction sample was described in details elsewhere[10], and so the main results are summarized here as follows. New fine grains are partly evolved near the boundaries around the peak strain, ep=0.12, and frequently develop in colony along most grain boundaries, as shown in Fig.5. With further straining to a steady state flow, there are equiaxed new grains developed homogeneously and almost fully in the whole area. Such a close relationship between the flow behavior and the development process of new grain structure is roughly similar to that in conventional DRX in cubic metals [11-13]. The average grain size in the new grained regions(Drex) is scarcely changed by hot deformation and does not depend on the orientation of the Mg alloy. It is also interesting to note that the average size fragmented by kink band at low strains is roughly the same as that of Drex evolved at high strains. This suggests that each fragmented region surrounded by low to medium angle boundaries may transform in-situ to a grain with high angle boundaries and also scarcely grow during deformation.
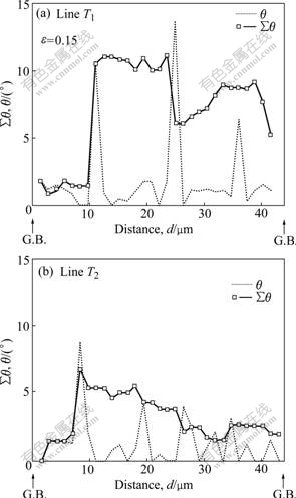
Fig.6 Point-to-point misorientations θ (dotted line) and cumulative misorientations Sθ () measured along lines T1(a) and T2(b) marked in Fig.5
Changes in the average misorientation (θav) and the volume fraction of a new grain structure (Xrex) with hot deformation are depicted in Fig.7. Both the θav and Xrex start to increase around the peak strain (ep=0.12) and rapidly rise during work softening, finally approach saturation values at high strains of above 0.5. Such behaviors of θav and Xrex are considered to correspond to the shape of flow curve, namely, a stress peak at ep=0.12 and then a work softening, followed by a steady state flow at high strains. It can be seen in Fig.7 that the θav and Xrex do not depend on the orientation of Mg alloy, i.e. the L- or T-direction. It is also interesting to note in Fig.7(b) that even under a steady state flow the new grain structure is not fully developed. Such a result has not been reported in conventional DRX of cubic metals [11-13].
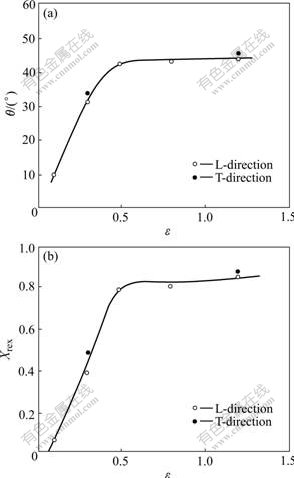
Fig.7 Strain dependence of average misorientation of dislocation boundaries including kink bands, θav (a), and volume fraction dynamically recrystallized, Xrex (b), of AZ31 alloy deformed at 673 K and 3×10-3 s-1
It is proved by the experimental results described above that the high temperature flow behavior of Mg alloy AZ31 is closely related to the new grain formation due to the operation of DRX, and the interrelationship between them as well as their characteristics is roughly similar to that of conventional DRX behaviors appearing in cubic metals[11-13]. Namely, the initial grain boundaries are frequently corrugated around the peak strain and some boundaries with medium angle misorientations are evolved in regions near the initial grain boundaries corrugated, finally leading to the formation of new grains in grain interiors. Some results in the Mg alloy are, however, not the same as those of conventional DRX taking place in cubic metals. For example, deformation bands (kink bands) are easily formed in grain interiors even at a low strain of 0.06 and some initial grains are fragmented by the boundaries of kink bands. Also a new grain structure is not fully evolved even under steady state flow in high strain. It should be also noted that the peak strain of Mg alloy scarcely changes with strain rate (Fig.2), while that of cubic metals sensitively depends on it.
3.3 Mechanism of DRX in Mg alloy
The mechanism of new grain evolution taking place in Mg alloy is discussed here based on the present experimental results. During hot deformation of Mg alloy, some initial grain boundaries migrate locally and in a limited distance and also are frequently corrugated at relatively low strains. Kink bands are concurrently formed to cross some grain interiors perhaps in the regions of corrugated grain boundaries[10]. Kink bands can be developed in low strain as keeping grain compatibity requirements, perhaps because Mg alloy has a few slip system. The misorientation and number of the boundaries of kink band rapidly rise with further deformation (Fig.7) and finally the regions fragmented by kink bands are bounded by high angle boundaries in high strain, resulting in in-situ evolution of new grains assisted by dynamic recovery and also grain boundary sliding[10]. It should be added that the average size of the regions fragmented is roughly the same as the stable DRX grain size. Namely, there are quite few extra places for long distance growth of each DRX grain. It is concluded, therefore, that the dynamic formation of new grains in Mg alloy can result from a series of deformation-induced continuous reaction, which is essentially similar to continuous DRX. Some previous studies[4-7] on the DRX of Mg alloy have concluded that new grain development can result from conventional (discontinuous) DRX. As explained in the description above, this may be due to the formation process of new grains and the flow behaviors of Mg alloy, and most of their interrelationship are apparently similar to those for DRX behaviors of many cubic metals.
Restoration mechanism operated in continuous DRX is principally dynamic recovery[9,14]. The s—e curve controlled by dynamic recovery shows generally no work softening and only a steady state flow in high strain. This is confirmed by the s—e curve of the T-direction sample (Fig.2). Fig.8 shows the strain dependence of room temperature hardness for the L- and T-direction samples deformed to various strains at 673 K and 3×10-3 s-1, followed by water quenching. The hardness(HV) increases with increasing strain at e<0.5 irrespective of the orientation and then approaches a constant value in high strain. This relationship between HV and e is roughly similar to those for the θav—e and Xrex—e in Fig.7. This suggests that increasing in HV due to hot deformation can not result from work hardening or softening, but also a fine grain development due to continuous DRX, that is, the Hall-Petch hardening[15].
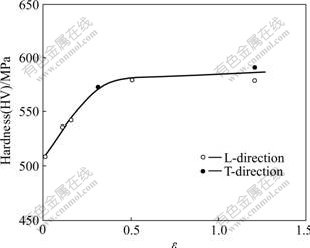
Fig.8 Strain dependence of room temperature hardness for AZ31 alloy deformed to various strains at 673 K and at 3×10-3 s-1, followed by water quenching
4 Conclusions
The dynamic recrystallization(DRX) and texture development taking place during deformation of Mg alloy AZ31 with a strong wire texture were studied in compression at 673 K (0.73 Tm). The main results obtained are summarized as follows.
1) The flow curve of the L-direction sample shows a rapid hardening, a stress peak at relatively low strain and then a strain softening, followed by a steady state flow in high strain, while that of the T-direction sample shows a rapid hardening followed by a steady state flow in high strain.
2) Work softening taking place in the L-direction sample does not result from new grain formation, but rather from a change in the basal plane from the hard slip directions to the soft or stable ones, that is the geometrical softening.
3) Kink bands are evolved at grain boundaries corrugated and also frequently in grain interiors even at low strains. The misorientation of the boundaries of kink band increases rapidly with increasing strain and approaches a saturation value at high strains. Such behaviors do not depend on the sample orientation.
4) The average size of new grains evolved scarcely changes during deformation and does not depend on the orientation. The grain size is roughly the same as that of the regions fragmented by kink band evolved in low strain.
5) New grain evolution can be controlled by a series of deformation-induced continuous reaction, i.e. continuous dynamic recrystallization (DRX).
References
[1] CHINO Y, MABUCHI M. Plastic-forming processes for magnesium alloy [J]. Japan Inst of Light Metals, 2001, 51(5): 498-502.
[2] XING J, YANG X, MIUNA H, SAKAI T. Supereplasticity of magnesium alloy AZ31 processed by severe plastic deformation [J]. Mater Trans, 2007, 48(6): 1406-1411.
[3] WATANABE H, FUKUSUMI M. Mechanical properties and texture of a superplastically deformed AZ31 magnesium alloy [J]. Mater Sci Eng A, 2008, 477(3): 153-161.
[4] ION S E, HUMPHREYS F J, WHITE S H. Dynamic recrystallization and the development of microstructure during high temperature deformation of magnesium [J]. Acta Metall, 1982, 30(10): 1909- 1919.
[5] KAIBYSHEV R, SITDIKOV O. On bulging mechanism of dynamic recrystallization [C]// MCNELLEY T D. Recrystallization and Related Phenomena (ReX’96). Monterey: MIAS, 1997: 287-294.
[6] GALIYEV A, KAIBYSHEV R, GOTTSTEIN G. Correlation of plastic deformation and dynamic recrystallization in magnesium alloy ZK60 [J]. Acta Mater, 2001, 49(4): 1199-1207.
[7] SITDIKOV O, KAIBYSHEV K, SAKAI T. Dynamic recrystallization based on twinning in coarse-grained magenisium [J]. Materials Science Forum, 2003, 419/422(1): 521-526.
[8] HIGASHIDA K, TAKAMURA J, NARITA N. The formation of deformation bands in fcc crystals [J]. Mater Sci Eng, 1986, 81(8): 239-258.
[9] HUMPHREYS F J, HATHERLY M. Recrystallization and related annealing phenomena [M]. Oxford: Pergamon, 1995.
[10] YANG X, MIUNA H, SAKAI T. Dynamic evolution of new grains in magnesium alloy AZ31 during hot deformation [J]. Mater Trans, 2003, 44(1): 197-203.
[11] SAKAI T, JONAS J J. Dynamic recrystallization: Mechanical microstructural consideration [J]. Acta Metall, 1984, 32(2): 189-209.
[12] SAKAI T. Microstructural development under dynamic recrystallization of polycrystalline materials [C]// YUE S, ESSADIQI E. Thermomechanical Processing of Steels (J. J. Jonas Symposium). Montreal: TMS-CIM, 2000: 47-62.
[13] WUSATOWSKA-SARNEK A M, MIURA H, SAKAI T. Nucleation and microtexture development under dynamic recrystallization of copper [J]. Mater Sci Eng A, 2002, 323(2): 177-186.
[14] SAKAI T, JONAS J J. Plastic deformation: Role of recovery and recrystallization [C]// BUSCHOW K H J, et al. Encyclopedia of Materials: Science and Technology. Oxford: Elsevier, 2001: 7079-7084.
[15] KOIKE J. Strength and ductility of mg alloys [C]// HANAD S, et al. Advanced Materials and Processing (PRICM4). Japan Inst Metals, 2001: 1179-1182.
Corresponding author: YANG Xu-yue, Tel: +86-731-8830136; E-mail: yangxuyue@mail.csu.edu.cn
DOI: 10.1016/S1003-6326(08)60228-9
(Edited by YUAN Sai-qian)