
Surface modification of spherical LiNi1/3Co1/3Mn1/3O2 with Al2O3 using heterogeneous nucleation process
YANG Zhi(杨 志), LI Xin-hai(李新海), WANG Zhi-xing(王志兴), ZHU Yong-jun(朱勇军)
School of Metallurgical Science and Engineering, Central South University, Changsha 410083, China
Received 15 July 2007; accepted 10 September 2007
Abstract: To improve the cycle stability at high voltage and high charge/discharge rate, spherical LiNi1/3Co1/3Mn1/3O2 was coated with Al2O3 by using heterogeneous nucleation process, and the physical and electrochemical properties were studied. The SEM images show that there is a uniform coating on the modified spherical LiNi1/3Co1/3Mn1/3O2. The electrochemical tests indicate that the properties of LiNi1/3Co1/3Mn1/3O2 coated with 0.5% aluminum oxide are the best. The initial capacities are 150 and 173 mA·h/g at the rate of 1C in the voltage range of 2.7-4.3 V and 2.7-4.6 V, respectively, and the discharge capacities maintain about 99% and 85% after 30 cycles, respectively. While those of the bare LiNi1/3Co1/3Mn1/3O2 are only 90% and 75%, respectively. The CV tests of LiNi1/3Co1/3Mn1/3O2 show that Al2O3-coating can restrain the oxide-reduction peak currents fading during the charge/discharge course.
Key words: Li-ion battery; LiNi1/3Co1/3Mn1/3O2; heterogeneous nucleation; Al2O3-coated
1 Introduction
For its high discharge capacity, thermal stability and low cost, LiNi1/3Co1/3Mn1/3O2 has attracted much attention. While, due to its low tap-density, bad cycling performance at high working voltage and high charge/discharge rate, it can not completely substitute LiCoO2 to become new generation commercial Li-ion battery cathode material[1-3]. LEE et al[4] and YING et al[5] have improved the tap density by sphericizing the materials and the tap density is nearly similar to that of LiCoO2. The bad cycling performance mainly relates to structural instability of material; otherwise, investigators have found that it also concerns with the material salvation in the electrolyte[6-8]. LI et al[7] revealed that interface film that has been formed during the course of active material interaction with electrolyte can be easily destroyed at high working voltage and high rate, and this leads to large capacity loss. By coating the cathode materials to physically isolate and reduce the contacting area in electrolyte, the speed of the interactions between cathode materials and electrolytes is controlled[8-9]. Compared with lattice doping, coating has less nega- tive influence on the electrochemical characteristics of electrode materials in virtue of its proper coating mass and coating only on the surface of the material, and it restrains the interactions obviously. Then, more efforts have been put on cathode materials coating with inert metal oxides, such as B2O3, MgO, ZnO and Al2O3 [10-12]. However, the coating layer has no electro- chemical activation, and thick and compact coating layer would deteriorate the rate capability of electrode materials. Some papers have reported the coating with LiAlO2 and LiMn2O4 that react with electrolyte slightly and have certain electrochemical activation[7,13]. The technology of surface coating by heterogeneous nucleation in the field of inorganic ceramics is very mature and it has been applied to surface modification of other Li-ion battery materials, such as graphite and LiMn2O4[14-17].
In this work, the alkalescency of LiNi1/3Mn1/3- Co1/3O2 and acidity of the Al(NO3)3 in aqueous solution were used to coat Al(OH)3 on the surface of LiNi1/3Mn1/3Co1/3O2 by heterogeneous nucleation. Spherical Ni1/3Co1/3Mn1/3CO3 precursor was obtained by carbonate coprecipitation, and spherical LiNi1/3Mn1/3- Co1/3O2 was synthesized by high-temperature solid reaction. The electrochemical characteristics of final Al2O3 coated LiNi1/3Mn1/3Co1/3O2 were meliorated.
2 Experimental
Spherical Ni1/3Co1/3Mn1/3CO3 precursor was prepared by coprecipitation. A mixed metal salt solution of NiSO4, MnSO4 and CoSO4 (cationic molar ratio of Ni?Mn?Co=1?1?1) with a concentration of 2.0 mol/L was pumped into a specially designed continuously stirred reactor, where the stirring speed was maintained at 1 000 r/min. At the same time, 2.0 mol/L Na2CO3 solution and NH3·H2O solution as a chelating agent were also separately pumped into the reactor. The pH of solution was carefully controlled by Na2CO3 solution. The obtained spherical Ni1/3Co1/3Mn1/3CO3 powders were filtered, washed by deionization water, dried at 120℃, and fired at 500 ℃ in air. The fired powders were mixed thoroughly in Li2CO3 with a molar ratio of Li?(Ni+Mn+Co)=1.10?1. Then, the mixed powder was calcined at 900 oC for 12 h to obtain spherical LiNi1/3Co1/3Mn1/3O2 powder.
The Al(NO3)3·9H2O was dissolved to aqueous solution with certain concentration. The pH value was about 2.0. According to the coating mass, 0.5%, 1%, 3% and 5% of the mass of LiNi1/3Co1/3Mn1/3O2, the LiNi1/3Co1/3Mn1/3O2 powders were slowly added into vigorously stirred Al(NO3)3 solution. With different adding masses, the pH value of obtained suspending liquid was from 4.5 to 5. The solution was stirred for 12 h. Then, Al(OH)3 was nucleated on the surface of LiNi1/3Co1/3Mn1/3O2 particles. The pH value was adjusted to 9.0 by NH3·H2O solution in order to make the Al(OH)3 sufficiently grown on the heterophase crystal nucleus to assure the cladding layer more compact. The spherical LiNi1/3Co1/3Mn1/3O2 coated with Al(OH)3 was filtered, washed, dried and heat-treated at 500 ℃ for 10 h to obtain spherical LiNi1/3Co1/3Mn1/3O2 powders coated with Al2O3.
The particle morphology of the powders was observed using a scanning electron microscope (SEM, JSM6301F). The electrochemical characteristics were studied by coin cells and CV tests. The electrode formulation consisted of 80% LiNi1/3Co1/3Mn1/3O2 powders, 10% carbon black and 10% (mass fraction) binder(PVDF). The prepared electrode pellets were dried at 100 ℃ under vacuum for 12 h. The test coin cells (CR2025) were assembled in a dry glove box filled with argon. The separator was a Celguard 2400 microporous polypropylene membrane. The electrolyte was 1 mol/L LiPF6 in EC+DEC (1?1, volume ratio). A lithium metal anode was used in this study. The charge—discharge cycling was galvanostaticly performed at a current of 160 mA/g (about 1 C) with voltage range of 2.70-4.30 V and 2.70-4.60 V at room temperature. The cyclic voltammogram(CV) tests were performed in the voltage range of 2.8-4.6 V (vs Li/Li+) and the scan speed was 0.2 mV/s.
3 Results and discussion
During the process of heterogeneous nucleation, the alkalescency LiNi1/3Co1/3Mn1/3O2 is used to neutralize faintly acid Al(NO3)3 solution to control the pH value. The spherical material is composed of many microcrystals. Comparatively, it is easy to preferentially nucleate and grow on the crystal edges, such as grain boundary and corners, while it is not easy to form on the surface of crystal. When the reaction system is on the condition of heterogeneous nucleation macroscopically and microcosmically, the partial high pH value on the surface of spherical particles will lead to growth of Al(OH)3. Otherwise, Al(OH)3 particles are much inclined to nucleate and grow at the grain boundary.
Fig.1 shows the SEM images of the bare spherical LiNi1/3Mn1/3Co1/3O2 (without Al2O3 coating treatment) and Al2O3-coated spherical LiNi1/3Mn1/3Co1/3O2. Comparing Fig.1(c) with Fig.1(d), we can see that, the surface of LiNi1/3Co1/3Mn1/3O2 coated with Al2O3 looks obscure. Fig.2 reveals that such obscure surface actually has been formed during Al2O3 coating. The contour of crystallites is not distinct, and the surface is obviously covered with mesh-type matters. This shows that the surface is entirely coated by Al2O3 in submicron order of magnitude.
Fig.3(a) shows the initial discharge curves of the materials in the voltage range of 2.7-4.3 V and at the rate of 1C. The LiNi1/3Mn1/3Co1/3O2 without any treatment shows the most high initial discharge capacity, 158 mA?h/g. The material coated with 5% Al2O3 shows most low capacity, only 141 mA?h/g. The initial discharge capacity of LiNi1/3Mn1/3Co1/3O2 only treated in water is 146 mA?h/g. With the coating content of 0.5%, 1.0% and 3.0%, the materials show minor difference of the capacity, 149, 150 and 151 mA?h/g, respectively. In the voltage of 2.7-4.6 V (Fig.3(b)), the material with coating content of 0.5% shows the highest capacity, 173 mA?h/g. The capacity of LiNi1/3Mn1/3Co1/3O2 without any treatment shows a bit lower capacity, 170 mA?h/g. The capacity of material coated with 5.0% Al2O3 is the lowest (156 mA?h/g). It can be deduced that the appropriate Al2O3 coating treatment can improve the discharge capacity at high working voltage. While too much coating content will exert bad influence on the discharge capacity. It mainly concerns with the inert electrochemical activity of Al2O3.
Fig.4 shows the cycling performance of materials at the rate of 1C. The coated materials exhibit good cycle stability no matter that the upper cut-off potential is 4.3 or 4.6 V. In comparison, the uncoated LiNi1/3Mn1/3-Co1/3O2 shows a poor cycle stability during cycling. Fig.4(a) reveals that in 2.7-4.3 voltage range, after 30 cycles, the capacity of LiNi1/3Mn1/3Co1/3O2 with coating keeps up to 95%, while that of LiNi1/3Mn1/3Co1/3O2 without any treatment is only 90% and that of LiNi1/3Mn1/3Co1/3O2 only treated in water is 92%. The LiNi1/3Mn1/3Co1/3O2 with 0.5% coating content shows the best cycling performance and the capacity maintains as high as 99%. In the voltage range of 2.7-4.6 V, at 1C discharge rate, the cycle performances of coated materials are all better than those of material without coating. After 30 cycles, the capacity of LiNi1/3Mn1/3Co1/3O2 with 0.5% Al2O3 maintains 85%, while that of LiNi1/3Mn1/3Co1/3O2 without Al2O3 coating is only 75%. However, excessive amount of coating will have a harmful effect on discharge capacity. So, we can draw a conclusion from Fig.3 and Fig.4 that when the coating content is 0.5%, the performance of material is comparatively the best.
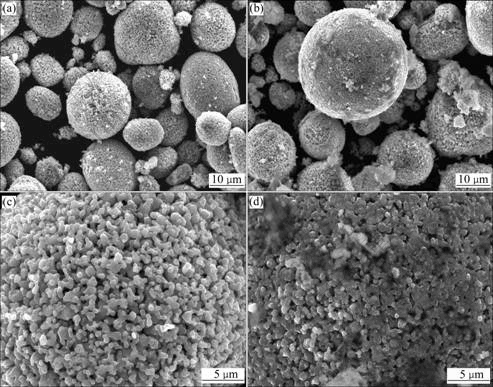
Fig.1 SEM images of bare LiNi1/3Mn1/3Co1/3O2 and Al2O3-coated LiNi1/3Mn1/3Co1/3O2: (a) and (b) Bare LiNi1/3Mn1/3Co1/3O2; (b) and (d) Al2O3-coated LiNi1/3Mn1/3Co1/3O2
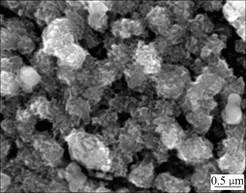
Fig.2 SEM image of LiNi1/3Mn1/3Co1/3O2 with Al2O3 dosage of 3%
Fig.5 shows CVs of LiNi1/3Mn1/3Co1/3O2 and LiNi1/3Mn1/3Co1/3O2 coated with Al2O3. As it can be seen that the materials have two oxidation/reduction peaks in the voltage range of 2.8-4.8 V. The oxidizing peak of Ni2+/4+ appears in the voltage range of 3.9-4.1 V, and reductive peak appears in the voltage range of 3.5-3.7 V. The oxidation/reduction peaks of Co3+/4+ are in the voltage range of 4.5-4.7 V. Fig.5(a) shows that at the scan rate of 0.2 mV/s, oxidation/reduction peaks show a bit excursion, while the peak current of oxidizing peaks shows little difference. The bare LiNi1/3Mn1/3Co1/3O2 shows the highest oxidant peak current and reductive peak current is comparatively small. Fig.5(b) shows that during the second cycle, the polarization is small, and the area of the oxidant peaks is almost consistent with that of the reductive peaks. This reveals that the material reversibility is perfect. From Figs.5(a) and (b), we can see that during the first and second cycles, the oxidation/reduction peak current of LiNi1/3Mn1/3Co1/3O2 with Al2O3 coating is increased, while bare LiNi1/3Mn1/3Co1/3O2 peak current decreases much. During the second cycle, the reductive peak currents of

Fig.3 Discharge curves of bare LiNi1/3Mn1/3Co1/3O2 and Al2O3-coated LiNi1/3Mn1/3Co1/3O2: (a) 2.7-4.3 V; (b) 2.7-4.6 V; 1 LiNi1/3- Co1/3Mn1/3O2; 2 LiNi1/3Co1/3Mn1/3O2 treated in water; 3 Coated with 0.5% Al2O3; 4 Coated with 1.0% Al2O3; 5 Coated with 3.0% Al2O3; 6 Coated with 5.0% Al2O3
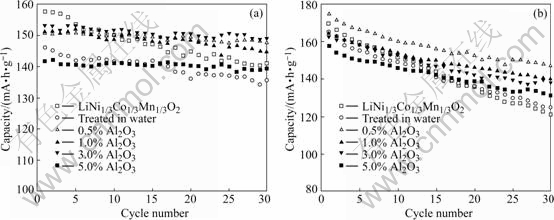
Fig.4 Cycling performances of bare LiNi1/3Mn1/3Co1/3O2 and Al2O3-coated LiNi1/3Mn1/3Co1/3O2 at 1C rate: (a) 2.7-4.3 V; (b) 2.7-4.6 V
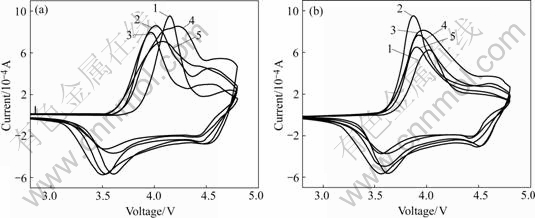
Fig.5 CVs of bare LiNi1/3Mn1/3Co1/3O2 and Al2O3-coated LiNi1/3Mn1/3Co1/3O2 at scan rate of 0.2 mV/s: (a) First cycle; (b) Second cycle; 1 Bare LiNi1/3Co1/3Mn1/3O2; 2 Coated with 0.5% Al2O3; 3 Coated with 1.0% Al2O3; 4 Coated with 3.0% Al2O3; 5 Coated with 3.1% Al2O3
LiNi1/3Mn1/3Co1/3O2 coating with Al2O3 are larger than that of bare LiNi1/3Mn1/3Co1/3O2. Otherwise, with the increase of Al2O3 coating content, the peak currents of oxidation/reduction decrease, which shows that Al2O3 coating can improve the reversibility of materials, while too much coating will deteriorate the reversibility to some degree.
4 Conclusions
1) Heterogeneous nucleation process is applied to Al2O3 coating on the surface of spherical LiNi1/3Co1/3- Mn1/3O2 and a uniform coating layer can be obtained.
2) The cycling performance of spherical LiNi1/3Co1/3Mn1/3O2 is improved in the voltage range of 2.7-4.3 V and 2.7-4.6 V at 1C rate by coating. When the coating content is 0.5%, it shows the best result after 30 cycles. The capacities of the materials maintain about 99% and 85%, and the initial discharge capacity is as high as 173 mA?h/g, which is higher than that of LiNi1/3Mn1/3Co1/3O2 without coating. While, too much coating will deteriorate the performances.
3) The tests of CVs testify that proper Al2O3 coating will meliorate the electrochemical reversibility of spherical LiNi1/3Co1/3Mn1/3O2. Hence, proper Al2O3 coating will helpful to structural stability of LiNi1/3Co1/3Mn1/3O2 and improving the electrochemical characteristics at high working voltage and high charge/discharge rate.
References
[1] YABUUCHI N, OHZUKU T. Electrochemical behaviors of LiCo1/3Ni1/3Mn1/3O2 in lithium batteries at elevated temperatures [J]. Journal of Power Sources, 2005, 146(1/2): 636-639.
[2] LIU Yong-xin, MA Xiao-hua, QIU Wei-li, PU Yuan, HE Xiang-min. Research progress in cathode material LiNi1/3Co1/3Mn1/3O2 for Li-ion battery [J]. Chinese Journal of Battery Bimonthly, 2005, 35(5): 398-400. (in Chinese)
[3] LI De-cheng, TAKAHISA M, ZHANG Lian-qi, MASAKI Y, HIDEYUKI N. Effect of synthesis method on the electrochemical performance of LiCo1/3Ni1/3Mn1/3O2 [J]. Journal of Power Sources, 2004, 132(1): 150-155.
[4] LEE M H, KANG Y J, MYUNG S T, SUN Y K. Synthetic optimization of Li[Ni1/3Co1/3Mn1/3]O2 via co-precipitation [J]. Electrochimica Acta, 2004, 50(4): 939-948.
[5] YING Jie-rong, GAO Jian, JIANG Chang-yin. Research and development of preparing cathode spherical materials for lithium ion batteries by controlled crystallization method [J]. Journal of Inorganic Materials, 2006, 21(2): 291-291. (in Chinese)
[6] ZHAO Fang-hui, YING Jie-rong, HE Xiang-ming, WANG Chun-rong, JIANG Chang-yin.. Surface modification and characterization of LiNi0.8Co0.2O2 coated with MgO [J]. Chinese Journal of Power Sources, 2003, 27(1): 14-16. (in Chinese)
[7] LI De-cheng, KATO Y, KOBAYAKAWA K, NOGUCHI H, SATO Y. Preparation and electrochemical characteristics of LiNi1/3Mn1/3Co1/3O2 coated with metal oxides coating [J]. Journal of Power Sources, 2006, 160(2): 1342-1348.
[8] WANG Zhi-xing, XING Zhi-Jun, LI Xin-hai, GUO Hua-jun, PENG Wen-jie. Study on Al2O3-modified LiMn2O4 Prepared by Heterogeneous Nucleation [J]. Acta Phsic Chem Sin, 2004, 20(8): 790-794. (in Chinese)
[9] YING Ji-rong, WAN Chun-rong, JIANG Chang-yin. Surface modification and characterization of LiNi0.8Co0.2O2 [J]. Journal of Tsinghua University (Natural Science Edition), 2001, 41(6): 78-80. (in Chinese)
[10] SUN Y K, HONG K J, PRAKASH J, AMINE K. Electrochemical performance of nano-sized ZnO-coated spinal LiNi0.5Mn1.5O4 as 5 V materials at elevated temperatures [J]. Electrochemistry Communications, 2002, 4(4): 344-348.
[11] ZHANG Z R, LIU H S, GONG Z L, YANG Y. Electrochemical performance and spectroscopic characterization of TiO2-coated LiNi0.8Co0.2O2 cathode materials [J]. Journal of Power Sources, 2004,129(1): 101-106.
[12] LIU Han-san, ZHANG Zhong-ru, GONG Zheng-liang, YANG Yong. A comparative study of LiNi0.8Co0.2O2 cathode materials modified by lattice-doping and surface-coating [J]. Solid State Ionics, 2004, 166(2): 317-325.
[13] JAEPHIL C. Direct micron-sized LiMn2O4 particle coating on LiCoO2 cathode material using surfactant [J]. Solid State Ionics, 2003, 160(1): 241-245.
[14] JIAN Guo, LI Fang-Jiao, HUA Tang-Yuan, HAI Xia-li, MING Zhang, YONG Mei-wang. Effect of synthesis condition on the structural and electrochemical properties of Li[Ni1/3Mn1/3Co1/3]O2 prepared by the metal acetates decomposition method [J]. Electrochimica Acta, 2006, 51 (18): 3731-3735.
[15] GUAN Yi, CHENG Lin-yan, ZHANG Jin-yuan. Application of heterogeneous deposition in particle coating [J]. Materials Review, 2006, 20(7): 88-90. (in Chinese)
[16] ZOU Ling-li, WU Yun-yun, LIANG Yong-he. Study on heterocoagulation applied to graphite treatment [J]. Journal of Wuhan University of Science and Technology, 2001, 24(2): 342-344. (in Chinese)
[17] LI Zhen-jiang, YAO Pei-zhen, ZHANG Can-ying, HOU Yao-yong. Surface coating with heterogeneous nucleation of Si3N4 powder and its rheological property [J]. Journal of the Chinese Ceramic Society, 1999, 27(5): 562-568. (in Chinese)
(Edited by YANG Bing)
Corresponding author: YANG Zhi; Tel: +86-731-8836633; E-mail: hml-yz-1978@163.com