超声引线键合过程的信号采集与分析系统
王福亮,刘少华
(中南大学 机电工程学院 现代复杂装备设计与极端制造教育部重点实验室,湖南 长沙,410083)
摘 要:根据超声引线键合实验平台结构,设计PZT(压电陶瓷)驱动信号传感电路,搭建键合力传感系统,集成多普勒振动测试系统,获得键合过程中的换能器驱动电压、电流、劈刀振动和键合压力信号。采用PCI6110数据采集卡,开发基于LabView8.2的采集软件,实现上述4路信号的同步采集、显示、频谱分析和保存。采用小波时频分析方法对电流信号进行分解,发掘电流信号中与键合质量相关联的一些特征。研究结果表明:信号采集系统能高速、同步采集键合过程中的多路信号;电流信号基频的频率、幅值及变化趋势都在一定程度上反映了键合质量;当电流信号频偏离正常值太大、均值太小和变化趋势异常时都表明键合失效。
关键词:信号传感与采集;小波分析;键合质量监测;超声引线键合
中图分类号:TN911.6 文献标志码:A 文章编号:1672-7207(2010)06-2189-06
Signals acquisition and analysis system for ultrasonic
wire bonding process
WANG Fu-liang, LIU Shao-hua
(Key Laboratory of Modern Complex Equipment Design and Extreme Manufacturing, Ministry of Education,
School of Mechanical and Electrical Engineering, Central South University, Changsha 410083, China)
Abstract: According to the ultrasonic wire bonding circuit, sensing circuits were designed to detect the piezoelectric transducer (PZT) driver signal, a bonding force sensing system was constructed, and the laser doppler vibration measure system was used to measure the vibration of tool. Four signals, i.e., driver voltage, current, tool vibration and bonding force during bonding process, were acquired, displayed and saved synchronously with data acquisition card PCI6110, which was programmed by LabView8.2. The current signals were analyzed by using the wavelet time-frequency method. Several characteristics were selected. The results indicate that this system is stable and four signals are acquired effectively at high speed during the bonding process. The frequency, amplitude and change tendency of current signals are related to the bonding quality in a certain extent. The fundamental resonance frequency deviation, very small current and exceptional current changing tendency all mean a failure of bonding.
Key words: signal sensing and acquisition; wavelet analysis; bonding quality monitoring; ultrasonic wire bonding
目前,90%以上的微电子封装互连采用热超声引线键合技术实现,对键合质量的检测都采用离线抽样检测。随着键合速度加快(15~20线/s)、焊盘间距缩小(<50 μm),人们期待发展键合质量在线监测技术来提高键合可靠性。由于超声引线键合是一个多变量耦合作用的复杂动态过程[1-3],目前一直没有形成实用的键合质量在线监测方法。Or等[4-5]在超声引线键合换能器中安装压电传感器,获得了键合过程中换能器的振动信号、机械阻抗信号,并以此来判断键合强度。类似地,Michael等[6]在换能器压电堆中嵌入传感器,获得了换能器的振动信号,并据此区分键合(特别是受污染表面的键合)的质量。这些方法虽然可检测出键合是否失效,但嵌入的传感器严重影响了换能器性能,并不具有应用价值。还有一些通过测量引线变形[7-9]和测量换能器的振动[10-13]等来判断键合质量的方法,由于需要增加昂贵的测量设备,也难以应用到实际生产中。基于对超声键合过程的认识,通过检测换能器电信号来判断键合质量的方法不影响换能器的性能,同时不需大幅度增加设备的硬件投入,受到了人们的青 睐。超声键合过程分为3个阶段:首先,引线和焊盘在键合力作用下接触在一起,并产生最初变形;然后,超声能量经变幅杆和劈刀传递到键合面,在接触面周边产生微键合点,初步形成键合强度;最后,超声能量使接触面积增大,微键合点数量增多,并形成超声键合强度[2-4]。在上述过程中,换能器系统阻抗、固有频率随键合界面状态变化而变化,并反映为换能器驱动电压、电流和劈刀振动的变化,且键合强度不同,变化过程也不同。因此,结合键合机理认识,发掘上述变化过程的特征,只要能够找到反映键合强度生成过程的特征,就可以实现键合质量在线检测。针对这个目标,本文作者构建一个用于超声引线键合质量在线监测的四通道高速数据采集系统,实现键合过程电压电流、劈刀振动、键合力信号的同步采集;使用小波时频分析方法提取电流信号的特征,并根据键合强度,获得特定键合条件下电流信号特征与键合强度的关系。
1 键合质量在线监测系统的信号采集
以WS3000型粗铝丝超声引线键合机为实验平台。由于超声键合的超声系统都类似,因此,本文研究也完全可以用于热超声引线键合、热超声倒装键合的研究。
1.1 超声引线键合过程
粗铝丝超声引线键合是指在常温环境下,通过超声振动和劈刀压力的作用,将铝丝焊接到芯片焊盘和基板引脚上,从而将芯片与基板的电路连接在一起的技术[14]。在这个过程中,最重要的超声振动是由换能器系统产生。换能器系统结构如图1所示,它由PZT、变幅杆、劈刀等几部分组成,其工作原理[2]是:带有锁相环的超声发生电路产生超声频率((57±2) kHz)的正弦电信号驱动PZT;PZT将电信号转换成机械振动(压电逆效应);振动经变幅杆和劈刀传输、放大后作用在工作界面上,在键合压力的共同作用下,将穿过劈刀的引线分别焊接在芯片焊盘和基板引脚上,以连接芯片和基板的电路,实现引线键合功能。
在键合过程中,随着键合界面连接强度的逐步形成,引线、劈刀、芯片、基板所组成的界面工况不断改变,体现在:
(1) 使得系统机械特性(共振频率、振型等)发生改变。超声发生电路的锁相环能监测到这种变化,并及时调整电信号的频率,使之与系统频率一致产生谐振,提高超声传递效率。反映在劈刀振动上,表现为振动频率的改变;反映在电路系统上,表现为驱动信号频率的改变。
(2) 系统消耗的功率发生改变,反映在电路系统上,表现为PZT驱动电流和电压幅值发生改变。同时使得系统劈刀、引线和基板之间的阻尼及键合界面微观特性发生改变,反映在劈刀振动上,表现为振动幅值发生改变;反映在结构受力上,表现为键合压力发生改变。
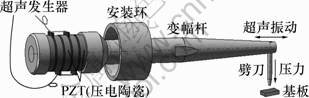
图1 换能器系统结构图
Fig.1 Construction of transducer system
因此,采集并分析键合过程各种信号的变化在一定程度上可了解界面工况和系统特性的变化,并以此判断键合强度的形成。
1.2 键合过程信号传感与采集硬件设计构成
为了提取与键合质量相关的各种信号特征,需要同步采集PZT驱动信号的电压、电流、劈刀振动和压力参数等多路信号。驱动电压为-50~50 V,电流为-1~1 A,振动信号转换为电压后为-10~10 V,压力信号转换为电压后为-5~5 V,它们的频率都为57~ 62 kHz。
选用NI公司S系列PCI6110数据采集卡,该卡每个通道采样率可达5 MS/s,可同步采样4路输入模拟信号,分辨率为12 Bit,经扩展的输入范围达-42~ 42 V。
为完成振动等信号的采集,需要设计接口转换电路,把电流、振动等非电压形式的信号转换成电压信号。接口电路如图2所示,在本文研究的粗铝丝引线键合中,PZT驱动电压高于数据采集卡能够承受的最高电压,采用能衰减10倍的BNC探头接入采集卡,衰减后输出电压U2。电流通过9 ?的采样电阻R转换成电压U1。压力信号通过M200B01型石英压力传感器获得。劈刀振动信号使用PSV24002M2 激光多普勒测振仪获得,并从中把分出接入采集卡PCI6110中。
各路实测信号与实际信号的关系如下:电流I=(U1/9)×1 000 mA;电压U=10U2 V;劈刀振动速度v=U4 m/s;键合压力P=8.4U3 N。
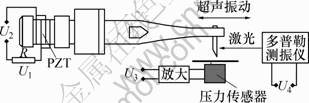
图2 信号采集接线示意图
Fig.2 Sketch map of signal acquisition connection
键合过程信号采集系统主要由键合机、换能器系统、接口转换电路、高速多路数据采集卡、计算机及其软件组成,如图3所示。
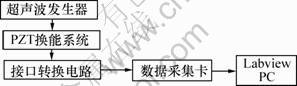
图3 采集系统构成
Fig.3 Components of acquisition system
1.3 采集系统软件总体设计
数据采集系统程序使用LabView8.2编写,软件分为前面板窗口和后流程窗口。前面板窗口完成参数设置和显示数据结果,后流程窗口是对前面板窗口功能的图形化语言的解释。软件前面板设计如图4所示,采集系统程序流程如图5所示。LabView使用图形编程语言,遵循数据流编程,其程序框图和流程图类似。本文使用DAQmx子模块编程,并把需要的参数设置列于前面板。
除了采集功能外,软件还具有采集卡参数设置、采集数据显示、频谱分析结果显示、用户操作响应、数据保存、意外错误处理等辅助功能。系统软件总体设计如图6所示。

图4 LabView数据采集系统前面板
Fig.4 Front board of LabView data acquisition
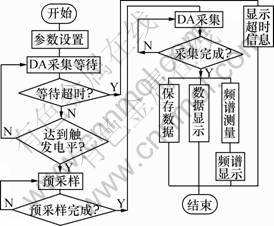
图5 LabView数据采集系统流程图
Fig.5 Flow chart of LabView data acquisition
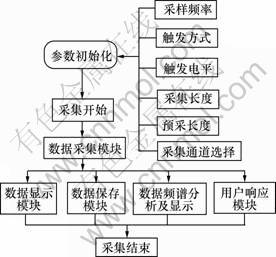
图6 采集系统软件总体设计
Fig.6 Whole design of data acquisition soft
通过设置采样频率等多种参数采集以便不同条件下的键合信号。在通道参数设置中选择需要采集信号的所有通道,可实现多个通道的同步采集。将采集的数据保存到指定文件中。同时,数据和频谱分析结果在前面板中显示,以便判断采集的数据是否符合常规,采集参数设置是否合理,当出现异常时,可及时检查设备和调整采集参数。
2 信号采集实验及结果
实验在WS3000型粗铝丝引线键合机平台上进行。设置一焊键合力为16 N,键合时间为175 ms,键合功率为0.8 W。采集系统使用中间触发方式,触发前预采5 000个采样点,电压信号上升沿作为触发,触发电平为1 V;采样频率设置为1.2 MHz(最高可设置为5 MHz),采样时间为180 ms,即216 000个采样点(键合过程大约为170 ms)。等待时间设置为10 s,即如果10 s内采集系统没有被触发,软件将超时退出。
图7所示为上述采集系统所获得的1组典型键合信号(电流信号、电压信号、压力信号和劈刀振动速度信号)曲线,键合对应的剪切力测试键合强度为7.76 N(由Dage Series 4000拉剪测试机测定,一般剪切力强度在3.92 N以上就已经符合要求)。图中每条曲线都由216 000个采样点绘出,展开后每个超声周期有20多个采样点,足以了解键合过程的每一个细节。
当改变键合时间、键合功率等键合参数时,只需修改采集系统的采样时间、触发电平等。这些参数可以通过试验确定,使采集的数据包含键合过程的全部信息,并尽可能减少冗余信息。
从图7可见:键合过程中电压电流信号、键合压力信号和劈刀振动速度信号都随时间有明显的变化。图7(a)表明:电流信号在超声启动后迅速上升,大约在10 ms时出现1个波峰,随后信号幅值逐渐减小并趋于稳定,平稳阶段的电流约为10 mA。图7(b)表明:电压信号在启动后开始下降,大约在10 ms时出现1个波谷,随后逐渐增大并趋于稳定,平稳时电压约为50 V。图7(c)所示为超声启动至一焊键合结束时的压力信号,均值约为13 N。压力信号均值主要与键合力设定有关,幅值主要与劈刀振动有关。图7(d)为劈刀振动速度信号,其变化主要与加载在压电换能器上的超声功率有关,同时受键合界面状态的影响。
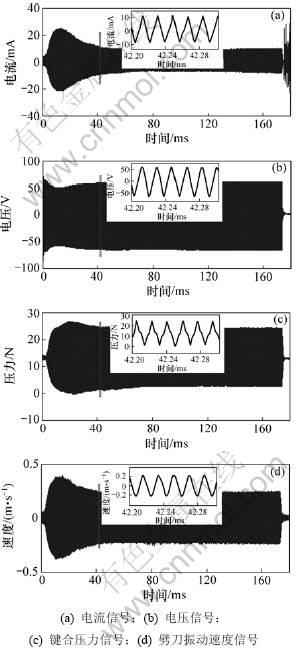
图7 超声引线键合过程中的电压、电流、压力、劈刀振动速度信号
Fig.7 Voltage, current, pressure ant ool vibration of ultrasonic wire bonding
3 电流信号特征提取及其与键合强度的关系
采用上述采集软件获得了大量超声引线键合过程的电流、电压、振动、压力等信号,这些信号包含了反映键合强度生成过程的特征。提取并识别这些特征,就有可能形成键合强度的在线判断方法。
电流信号包含了很多的频率信息,而其中对键合起主要作用的是与系统谐振频率相关的信息。电流信号中的基频和各倍频信号集中了原信号绝大多数能量,因此,本文主要对电流信号基频和倍频信号进行分析,提取与键合质量有关的特征值。本文使用Matlab软件,采用小波分析方法对电流信号进行分析。
由于换能器的固有频率为57 kHz,因此,电流信号中基频信号在57 kHz附近,其他倍频信号频率近似为57 kHz的整数倍。为了得到电流信号的基频、倍频相关特征,首先采用db40小波基[15],利用正交小波包分解对电流信号进行处理,对分解后的第8层信号进行分析,找出包含各倍频信号的频率段,然后,计算各频率段信号的有效值,计算公式为:
, i=0, 1, …, S/200
图8所示是采用上述小波分析方法获得的电流信号主要频率段有效值曲线。由图8可以提取如下电流信号特征:
(1) 基频、倍频、三倍频、四倍频信号有效值8.5~34 ms内的方差和平均值。
(2) 基频8.5~204 ms的电流平均值、峰值以及峰值点对应时间,85~102 ms段和187.1~204 ms段的电流均值及方差。
(3) 基频f。

图8 电流信号主要频率段有效值曲线
Fig.8 Effective value curves of main harmonic signals
上述特征的提取方法及其与键合强度之间的关联规律为:
(1) 电流信号的基频段有效平均值A,计算方 法为:
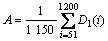
其中:D1为基频段信号有效值。若该特征值过小,则键合强度较差。不同键合条件下的阈值可由实验确定。
(2) 信号的有效值变化趋势特征值d。该特征是取基频有效值曲线中间段与结束段的电流均值之差,它反映了电流信号的变化速度,计算方法为:
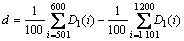
其中:D1为电流信号基频段有效值。实验结果表明:若特征值d很小,即基频段在后半段下降幅度过小或者没有下降甚至上升,则键合强度较差。
并不是所有失效键合信号的后半段就一定衰减慢,但是,信号后半段衰减慢的键合必然失效。因此,在监测系统中若发现信号后半段衰减很慢,则可肯定键合失效。
(3) 电流信号基频f,即键合系统的谐振频率f。如果该频率大于70 kHz或者低于45 kHz(即偏离换能器固有频率,约57 kHz),则说明换能器系统频率跟踪出错,从而键合失败。
4 结论
(1) 根据超声引线键合实验平台的结构,搭建了采集键合过程中PZT驱动电压信号、电流信号、劈刀振动信号和键合力信号的传感电路。
(2) 基于NI公司的高速数据采集卡PCI6110,LabView开发了超声引线键合信号采集系统,实现了键合过程中上述信号的实时采集、数据传输、波形显示,以及信号的频谱分析和处理。该系统具有5 MHz的采样率,可获得键合信号的微小变化细节。
(3) 使用Matlab软件,采用小波分析方法对电流信号进行分析,找到了几个与键合质量有关的特征:若键合过程中电流信号基频偏离正常值,或基频段有效平均值很小,或基频段信号有效值变化趋势异常,都将导致键合失效。
参考文献:
[1] 王福亮, 李军辉, 韩雷, 等. 超声波在引线键合机变幅杆中的传递规律[J]. 中南大学学报: 自然科学版, 2005, 36(6): 1017-1020.
WU Fu-liang, LI Jun-hui, HAN Lei, et al. A PZT driver signal acquisition and analysis system for ultra sonic wire bonding[J]. Journal of Central South University: Science and Technology, 2005, 36(6): 1017-1020.
[2] 王福亮, 李军辉, 韩雷, 等. 热超声倒装键合界面的运动传递过程[J]. 机械工程学报, 2008, 44(2): 68-73.
WU Fu-liang, LI Jun-hui, HAN Lei, et al, Vibration transfer process at thermosonic flip chip bond interface[J]. Chinese Journal of Mechanical Engineering, 2008, 44(2): 68-73.
[3] 王福亮, 韩雷, 钟掘. 超声功率对引线线键合强度的影响[J]. 机械工程学报, 2007, 43(3): 107-111.
WU Fu-liang, HAN Lei, ZHONG Jue. Effect of ultrasonic power on the wire bonding strength[J]. Chinese Journal of Mechanical Engineering, 2007, 43(3): 107-111.
[4] Or S W, Chan H L W, Lo V C, et al. Ultrasonic wire bond quality monitoring using piezoelectric sensor[J]. Sens Actuators A, 1998, 65: 69-75.
[5] Uthe P M, Bamburak P S. Ultrasonic wire bonding quality monitor and method: USA, 4815001[P]. 1989.
[6] Michael B, J?rg W. Bond process monitoring via self-sensing piezoelectric transducers[C]//Frequency Control Symposium and Exposition, Proceedings of the 2004 IEEE International. Montreal, Canada, 2004: 125-129.
[7] Goebel B, Ziemann A. Quality control for wire bonding: United States, 4984730[P]. 1991.
[8] Farhad F. Wire bonding ultrasonic control system responsive to wire deformation: USA, 5314105[P]. 1994.
[9] Hight M J, Winkle R V, Dale J R. Ultrasonic bonding apparatus: USA, 4040885[P]. 1977.
[10] Pufall R. Automatic process control of wire bonding[C]// Proceedings of 43rd Electronic Components and Technology Conference. Orlando, USA, 1993: 159-162.
[11] Raben K U. ?berwachung von bondparametern w?hrend des bondvorganges: European patent, 4854494[P]. 1989.
[12] Zschimmer G. Ultraschall-sonotrode: German, 2946154A1[P]. 1979.
[13] Gibson O E, Gleeson W J, Burkholder L D, et al. Bond signature analyzer: USA, 4998664[P]. 1989.
[14] Chiu S S, Chan H L W, Or S W, et al. Effect of electrode pattern on the outputs of piezosensors for wire bonding process control[J]. Materials Science and Engineering, 2003, B99(12): 121-126.
[15] 高成, 董长虹, 郭磊, 等. Matlab小波分析与应用[M]. 2版, 北京: 国防工业出版社, 2007: 18-28.
GAO Cheng, DONG Chang-hong, GUO Lei, et al. Matlab wavelet analysis and application[M]. 2nd ed. Beijing: Defense Industry Press, 2007: 18-28.
(编辑 陈灿华)
收稿日期:2009-12-15;修回日期:2010-03-21
基金项目:国家重点基础研究计划(“973”计划)项目(2009CB724203);国家自然科学基金青年基金资助项目(50705098)
通信作者:王福亮(1979-),男,湖南宜章人,副教授,从事微电子封装技术与装备研究;电话:13975145436;E-mail: csuwfl@sohu.com